塑料圆盒模具设计说明书Word文档下载推荐.docx
《塑料圆盒模具设计说明书Word文档下载推荐.docx》由会员分享,可在线阅读,更多相关《塑料圆盒模具设计说明书Word文档下载推荐.docx(27页珍藏版)》请在冰豆网上搜索。
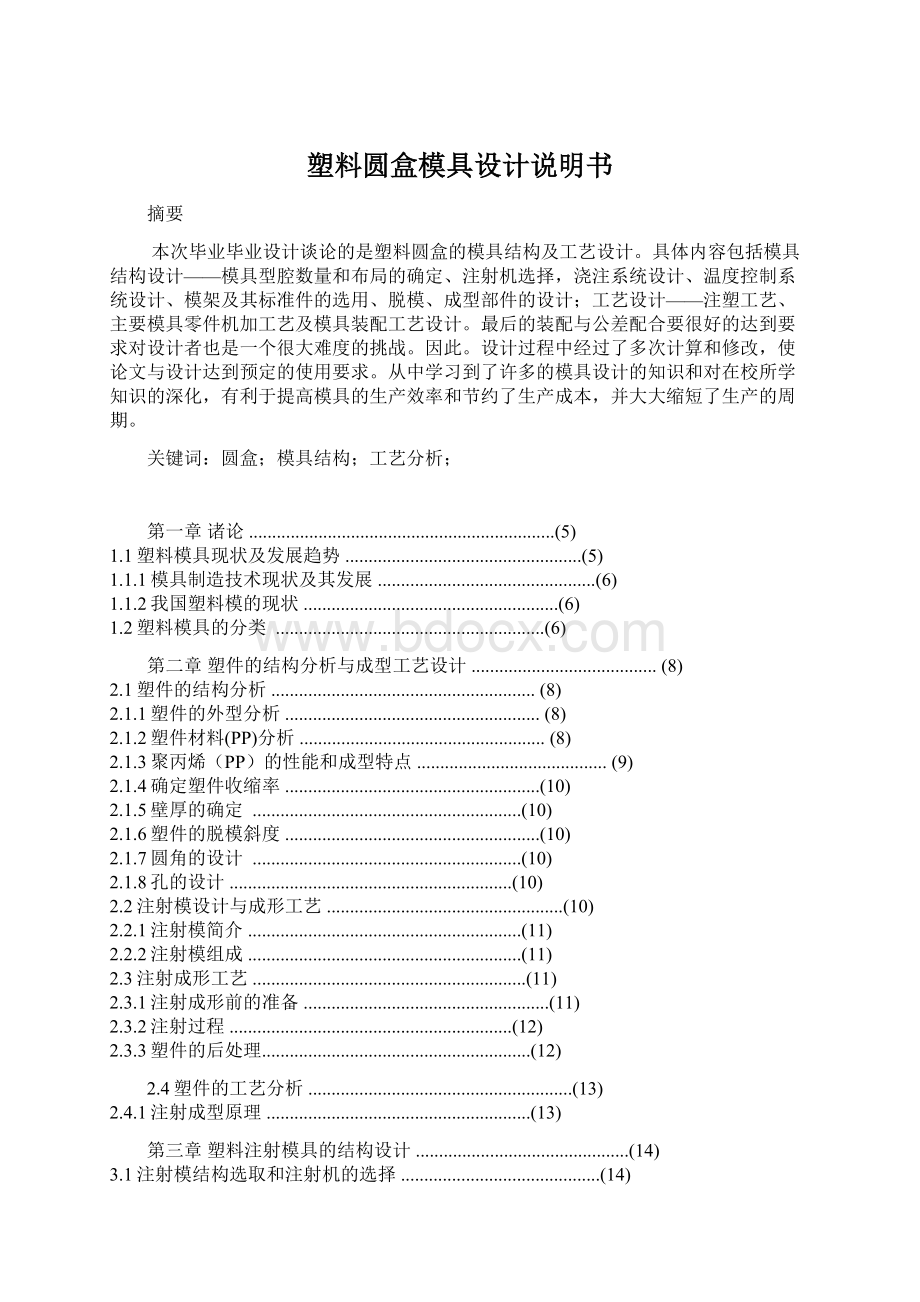
2.1.4确定塑件收缩率.......................................................(10)
2.1.5壁厚的确定..........................................................(10)
2.1.6塑件的脱模斜度.......................................................(10)
2.1.7圆角的设计..........................................................(10)
2.1.8孔的设计.............................................................(10)
2.2注射模设计与成形工艺...................................................(10)
2.2.1注射模简介...........................................................(11)
2.2.2注射模组成...........................................................(11)
2.3注射成形工艺...........................................................(11)
2.3.1注射成形前的准备.....................................................(11)
2.3.2注射过程.............................................................(12)
2.3.3塑件的后处理..........................................................(12)
2.4塑件的工艺分析.........................................................(13)
2.4.1注射成型原理.........................................................(13)
第三章塑料注射模具的结构设计..............................................(14)
3.1注射模结构选取和注射机的选择...........................................(14)
3.1.1型腔数目的确定.......................................................(14)
3.1.2分型面的设计.........................................................(14)
3.1.3型腔的配置...........................................................(15)
3.2注射机的选择...........................................................(15)
3.2.1注射量的计算.........................................................(15)
3.2.2浇注系统凝料体积的初步计算...........................................(16)
3.2.3选择注射机...........................................................(16)
3.2.4注射机的相关参数的校核...............................................(17)
3.3浇注系统的设计.........................................................(17)
3.3.1浇注系统的简介.......................................................(17)
3.3.2浇注系统的分类及组成.................................................(17)
3.3.3浇注系统设计的原则...................................................(18)
3.3.4主流道的设计.........................................................(18)
3.4推出机构设计...........................................................(19)
3.5脱模机构的设计原则与选用...............................................(19)
3.6合模导向机构设计.......................................................(20)
3.7导柱导向机构的设计.....................................................(20)
3.8排溢系统的设计.........................................................(21)
3.9成型零件的结构设计及计算................................................(21)
3.9.1成型零件的结构设计....................................................(22)
3.9.2成型零件钢材的选用...................................................(24)
3.9.3成型零件工作尺寸的计算................................................(26)
3.9.4模具型腔侧壁和底板厚度的计算..........................................(26)
3.10支撑零部件的设计......................................................(27)
第四章塑料注射模其它设计..................................................(28)
4.1选标准模架.............................................................(28)
4.2成型零件材料选用........................................................(28)
4.3注射模钢种的选用.......................................................(29)
4.4最大注射压力的校核.....................................................(29)
4.5最大注塑量的校核.......................................................(29)
4.6模具与注塑机安装部分相关尺寸校核.......................................(30)
4.7开模行程校核...........................................................(30)
4.8脱模力的计算...........................................................(30)
4.9模具冷却系统的设计....................................................(31)
4.9.1冷却装置的设计原则..................................................(31)
4.9.2冷却装置的选用......................................................(31)
第五章模具安装和试模.......................................................(32)
结语........................................................................(34)
参考文献....................................................................(35)
第一章绪论
1.1塑料模具现状及发展趋势
1.1.1模具制造技术现状及其发展
(一)现状
模具的特点决定了模具工业的快速发展,模具制造水平是衡量一个国家机械制造业水平的重要标志。
我国已经具备制造大型、精密、复杂、长寿命模具的能力。
如:
硬质合金多工位级进模,步距精度<
0.005mm,成型表面粗糙度达0.4-0.1um,镶件的重复定位精度<
0.005mm,互换性好,模具寿命达1亿冲次,具有自动冲切、叠压、铆合、扭角、计数分组和安全保护功能。
又如:
大型的塑料模,重达10吨以上,尺寸精度为0.01mm,型腔Ra=0.1um,模具寿命达30万次以上。
达到国际同类模具产品的技术水平。
(二)发展状况
(1)制造设备水平的提高促进模具制造技术的发展
先进的模具加工设备拓展了机械加工模具的范围,提高了加工精度,降低了表面粗糙度,大大提高了生产效率。
数控仿形铣床、加工中心、精密坐标磨床、数控坐标磨床、数控电火花成形机、慢走丝线切割、精密电加工机床、坐标测量机、挤压研磨机、激光快速成形机等。
(2)模具新材料的应用促进模具制造技术的发展
模具材料是影响模具寿命、质量、生产效率和生产成本的重要因素,目前我国模具寿命仅为发达国家的1/5-1/3,而其中材料和热处理原因占60%以上。
随着新型优质模具钢的不断开发(如:
65Nb、LD1、HM1、GR等)以及热处理工艺和表面强化处理工艺的进一步的完善和发展,(如:
组织预处理、高淬低回、低淬低回、低温快速退火等热处理工艺以及化学热处理、气相沉积、渗金属、电火花强化等新工艺、新技术)。
都将极大地促进和提高模具制造技术的快速发展。
(3)模具标准化程度的提高刺进模具制造技术的发展
模具的标准化程度是模具技术发展的重要标志,目前我国的标准化程度约为30%,而发达国家为70-80%,标准化促进了模具的商品化,商品化推动了模具生产的专业化。
从而提高模具制造质量,缩短制造周期,降低制造成本,也促进新材料、新技术的应用。
(4)模具现代设计和制造技术促进了模具制造技术的发展
CAD/CAM/CAE技术的发展,使模具设计与制造向着数学化方向发展,尤其在成形零件方面软件(如:
UG、Pro/E)的广泛应用,实现了模具设计与制造的一体化,极大的提高了模具制造技术和制造水平,也是未来模具制造技术的主要发展方向。
(三)发展趋势
社会快速发展,产品不断增多,更新换代加快,模具质量和生产期尤为重要,从而决定了模具制造技术的发展趋势:
(1)粗加工向高速加工发展
(2)成形表面的加工想精密、自动化方向发展
(3)光整加工向自动化方向发展
(4)反响制造工程制模技术的发展
(5)模具CAD/CAM/CAE技术将有更快的发展
从模具结构设计——模具工作状态的模拟——自动加工程序的生成——自动化加工、自动检测。
实现设计到制造的一体化是模具制造业发展的必然趋势。
1.1.2我国塑料模的现状
模具作为提高生产率,减少材料和消耗,降低产品成本,提高质量和市场竞争力的重要手段,已越来越受到各工业部门的重视。
随诊工业技术不断向前发展,要求模具在更苛刻、更高速度的工作条件下,对模具的精度越来越高,使用寿命越来越长。
为了满足这些要求,国内外都在模具材料的研究和开发上作了巨大的努力,也在这方面取得了不少成果。
近年来,中国塑料模具发展速度相当快。
目前,塑料模具在整个模具行业中所占比重约为30%。
随着中国汽车、家电、电子通讯、各种建材迅速发展,预计在未来模具市场中,塑料模具占模具总量的比例仍将逐步提高,且发展速度将快于其他模具。
专家指出,面对国外先进技术与高质量制品的挑战,中国塑膜企业不近要加快产业集群化,发挥规模效应,还要注重模具产业链的全段研发、人才建设和产品链后端的检测以及信息服务,尽快缩短技术、管理、工装水平与国际水准的差距。
这是塑料模具企业在发展中必须解决的重要问题。
1.2塑料模具的分类
塑料模具的分类方法很多,按照塑料制件的成型方法不同可以分为一下几类。
(1)注射模注射模又称为注塑模。
塑料注射成型是在金属压铸成型原理的基础上发展起来的。
(2)压缩模压缩模又称压缩模。
压缩成型是塑件成型方法中较早采用的一种方法。
(3)压住模压住模又称传递模。
压住模的加料室与型腔是通过浇注系统连接起来的,通过压柱或柱塞将加料室内受热塑化熔融的加固性塑料经浇注系统压入被加热的闭合型腔,最后固化定型。
(4)挤出模挤出模常称为挤出机头。
挤出成型是利用挤出机料筒内的螺杆旋转加压的方式,连续地将塑化好的呈熔融状态的物料从筒中挤出。
(5)气动成型模气动成型模是利用气体作为动力成型塑料制件的模具。
除了上述的几类常用的塑料成型模具外,还有泡沫塑料成型模、浇注成型模、滚塑(包括搪塑)成型模、压延成型模、拉丝成型模以及聚四氟乙烯冷压成型模等。
第二章塑件的结构分析与成型工艺设计
2.1塑料的结构分析
2.2.1塑料的外型分析
塑件如图2.1所示
图2.1塑件图
塑料是塑料圆盒的主视图。
塑料结构比较简单,高度较高,所以采用一模一腔,塑件制件表面无明显痕迹。
材料要求为PP,生产批量为大批量,塑件公差按模具设计要求进行转换。
2.1.2塑件材料(PP)分析
选材在设计过程中是个关键步骤,对于指定部件的材料,最主要的是考虑部件的功能和决定部件功能的有关材料性能,同事还要考虑诸如部件的特点和禁忌、使用使的外界条件、临界条件、使用寿命和使用方式、维修方法、制品尺寸和尺寸精度、成形加工工艺、生产数量、生产速度、成本、原料来源和经济效益等等。
从圆盒的结构性能和用途及成型等各方面考虑,它需要的材料耐话品性良好。
且流动性好,易于加工成型,染色性好,无毒无臭,聚丙烯正好符合性能方面的要求,因此,选用聚丙烯(PP)。
2.1.3聚丙烯(PP)的性能和成型特点
(一)基本特性
PP即聚丙烯是结晶性塑料;
聚丙烯无味、无色、无毒。
外观似聚乙烯,但比聚乙烯更透明、更轻。
密度仅为0.88~0.91g/cm3。
它不吸水、光泽好、易着色。
聚丙烯的屈服强度、抗拉强度、抗压强度和硬度及弹性比聚乙烯好。
定向拉伸后的聚丙烯可制作铰链,其具有特别高的抗弯曲疲劳强度,如用聚丙烯注射成型的一体铰链(盖和本体合一的容器),经过7x10七次方次开闭弯折未产生损坏和断裂现象。
聚丙烯的熔点为164~170摄氏度,其耐热性好,能在100摄氏度以上的温度下进行消毒灭菌。
聚丙烯耐低温的使用温度可达-15摄氏度,在低于-35摄氏度时会脆裂。
聚丙烯的高频绝缘性能好,而且由于其不吸水,绝缘性能不受湿度的影响。
聚丙烯在氧、热、光的作用下极易洁聚、老化,所欲必须加入防老化剂。
PP塑料的主要技术指标如下表2.1
表2.1PP塑料的主要技术指标
密度(克/立方厘米)0.88-0.91
收缩率(%)1.0-3.0
熔点(摄氏度)164-170
热变形温度(摄氏度)105-116
拉伸弹性模量(MPa)1.1-1.6x10的三次方
弯曲强度(MPa)42-67
硬度HBHR95-105
体积电阻率(欧姆.厘米)>
10的16次方
击穿电压(千伏/毫米)20-26
(二)主要用途
聚丙烯可用于制造各种机械零件,如法兰、接头、泵叶轮、汽车零件和自行车零件;
可作水、蒸汽、各种酸碱等的输送管道,化工容器和其他设备的衬里、表面涂层;
可制造盖和本体合一的箱壳,各种绝缘零件,并用于医药工业中。
(三)成型特点
聚丙烯成型收缩范围大,易发生缩孔、痕凹及变形;
聚丙烯热容量大,注射成型模具必须设计能充分进行冷却的冷却回路;
聚丙烯成型的适宜模温为80摄氏度左右,不可低于50摄氏度,否则会造成成型塑件表面光泽差或产生熔接痕等缺陷,且温度过高会产生翘曲现象。
2.1.4确定塑件收缩率
模具型腔和型芯的加工尺寸除了计算基本尺寸之外,还有一个加工公差的问题。
按照惯例,模具的加工公差为塑料公差的1/4。
但由于塑料收缩率范围和稳定性各有差异,首先必须合理化确定不同塑料所成形塑件的尺寸公差。
PP的收缩率为1%-3%,在设计本产品时,结合产品的结构工艺特点和材料的特性,在本设计中,零件中,零件的收缩率为2%。
2.1.5壁厚的确定
塑件壁厚对成形工业的影响很大,合理的去顶塑件的壁厚是很重要的。
塑件的壁厚首先决定于塑件的使用要求,壁厚过小,成型时流动阻力大,大型复杂塑件难以充满型腔。
设计要求本产品的壁厚设置为2.0mm,是根据零件的工作要求、摆放位置和化学和流动特性确定。
2.1.6塑件的脱模斜度
根据产品的外型,结合的工作条件、工艺特点,为提高产品的生产效率和表质量,脱模斜度设置为3°
2.1.7圆角的设计
在塑件的设计过程中,为了避免应力集中,提高塑件的强度,改善熔体的流动情况和便于脱模,在塑件各内外表面的转角连接处,均应采用圆弧过渡。
此外,有了圆角,模具在淬火或使用时不致应力集中而开裂。
一般内外圆弧半径R1均为壁厚1的1.5至2.5倍。
2.1.8孔的设计
在设计塑件中孔的位置时,应不致影响到塑件的强度,并应尽量不增加模具制造的复杂性。
此塑件上没有成型孔,所以不用考虑设计孔的要求。
2.2注射模设计与成形工艺
2.2.1注射模简介
塑料注射成型所用的模具称为注射成形模具,简称注射模。
塑料的注射成形过程是借助注射剂内的螺杆或柱塞的推力,将已塑化的塑料熔体以一定得压力和速率注射到闭合的模具型腔内,经冷却、固化。
定型后开模面获得制品。
2.2.1注射模组成
注射模由动模和定模两部分组成。
动模安装在注射机的移动工作台上,定模安装在注射机的固定工作台面上。
动模和定模闭合后已塑化的塑料通过浇注系统注入到模具型腔中冷却、固化和定型。
通常要求注射模分开后,制品滞留在动模一侧,由设置在动模内的脱模机构将制品从模内推出。
(1)成形零部件:
指构成模具型腔、直接与塑料熔体想接触并成形制品的模具零件或部件。
(2)浇注系统
(3)导向和定位机构
(4)脱模机构
(5)侧向分型抽芯机构
(6)温度调节系统
(7)排气系统
2.3注射模设计与成形工艺
包括成形前的准备、注射过程和制品的后处理。
2.3.1注射成形前的准备
(一)原料的检验和预处理
根据塑料工艺性能要求,检验其各种性能指标,如含水量等。
对于该塑件材料PP,查本节参考文献得聚丙烯PP吸水率<
0.03%,允许水含量为0.05%-0.20%。
由于该塑料不易吸水,估可以不进行干燥处理。
(二)料筒的清洗
在注射成型过程中,当改变产品、更换原料及颜色时均需清洗料筒。
通过,柱塞式料筒可拆卸清洗,而螺杆式料筒可采用对空注射法清洗。
2.3.2注射过程
注射的过程包括:
加料、塑化、注射、保压、冷却、脱模。
但就塑料注射成型中的实质变化来说,分为塑料的塑化、熔体充满型腔和冷却定型三大过程。
(一)加料
由注射机的料斗落入一定量的塑料,以保证操作稳定、塑料塑化均匀,最终获得良好的塑件。
通常其加料量由注射机计量装置来控制.
(二)塑化
塑化是指塑料在料筒内经加热达到熔融流动状态,并具有良好可塑性的全过程就生产的工艺而论,对这一过程的总要求是:
在规定时间内提供足够数量的熔融塑料,塑料熔体在进入型腔之前要充分塑化,既要达到规定的成型温度,又要使塑化料各处的温度尽量均匀一致,还要使分解物的含量达到最小值。
这些要求与塑料的特性、工艺条件的控制及注射机塑化装置的结构等密切相关。
(三)注射
注射机用柱塞或螺杆推动具有流动性和温度均匀的塑料熔体,从料筒中经过喷嘴、浇注系统,直至压入模腔。
(四)保压
保压是自注射结束到柱塞或螺杆开始后移的这段过程,即压实工序。
保压的目的一方面是防止注射压力杰出