杠杆CA1340自动车床加工工艺规程及夹具设计Word文档格式.docx
《杠杆CA1340自动车床加工工艺规程及夹具设计Word文档格式.docx》由会员分享,可在线阅读,更多相关《杠杆CA1340自动车床加工工艺规程及夹具设计Word文档格式.docx(33页珍藏版)》请在冰豆网上搜索。
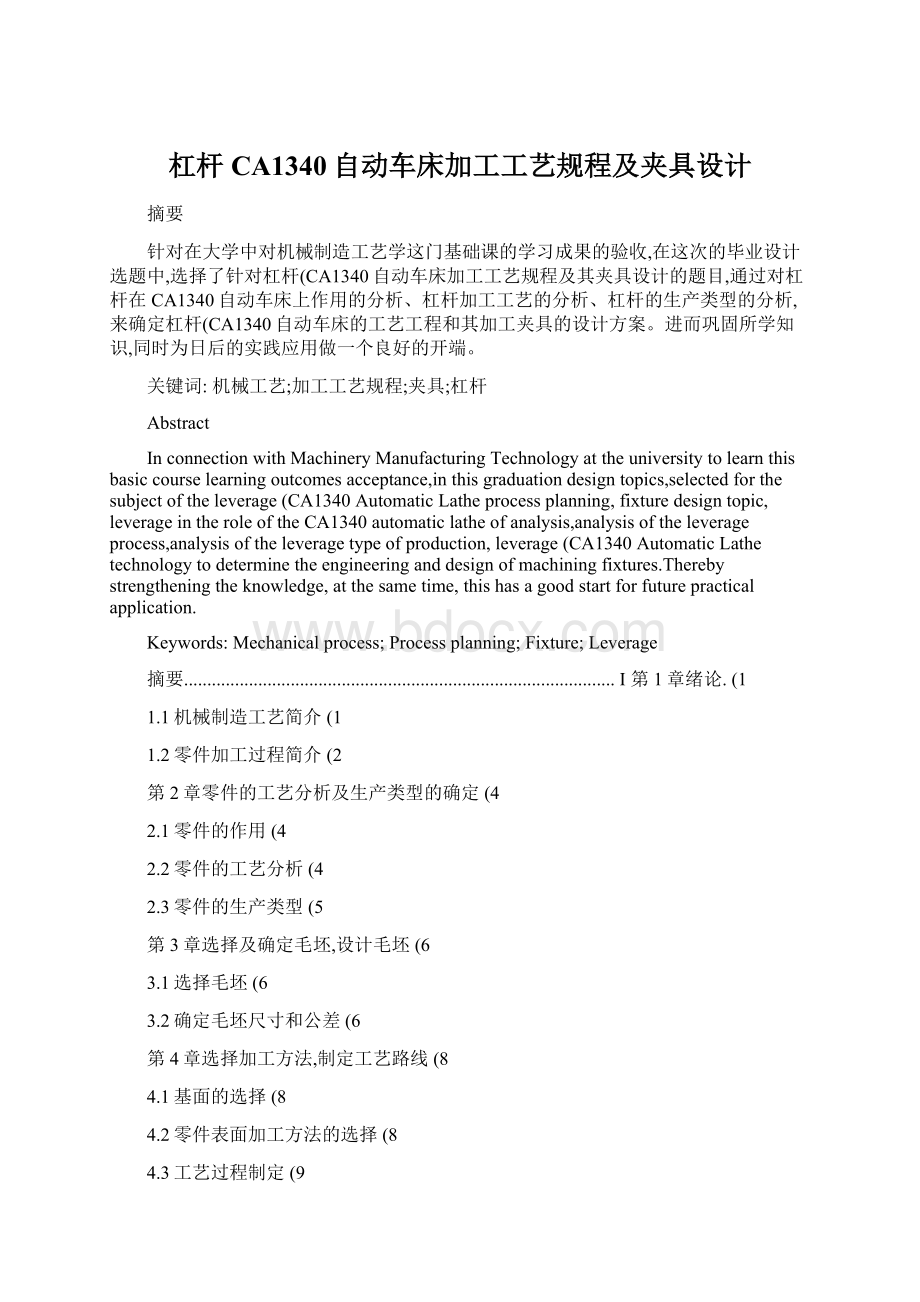
第4章选择加工方法,制定工艺路线(8
4.1基面的选择(8
4.2零件表面加工方法的选择(8
4.3工艺过程制定(9
第5章工序设计(11
5.1选择机床(11
5.2选择夹具(11
5.3根据不同工序选择刀具(12
5.4选择量具(13
5.5确定工序尺寸(15
第6章确定切削用量及基本时间(19
第7章夹具设计(36
7.1设计钻Φ4MM的油孔及锪Φ8MM圆锥沉头孔专用夹具(36
7.1.1定位方案(36
7.1.2装夹设计要求(37
7.1.3切削力和夹紧力的计算(37
7.1.4导向元件(38
7.1.5夹具与机床连接元件(38
7.1.6装夹说明(38
7.1.7夹具特点(39
7.2设计零件底槽的专用夹具(39
7.2.1定位方案(39
7.2.2装夹设计要求(39
7.2.3切削力及夹紧力的计算(40
7.2.4夹具设计及操作的简要说明(40
结论(41
致谢(42
参考文献(43
第1章绪论
1.1机械制造工艺简介
机械制造业是国民经济的支柱产业,是国家创造力、竞争力和综合国力的重要体现。
机械制造工艺是将各种原材料、半成品加工成产品的方法和过程。
它是应先进工业和科学技术的发展需求而发展起来的。
现代工业科学技术的发展又为制造业技术提供了近一步发展的技术支持,如新材料的使用、计算机技术、微电子技术、控制理论与技术、信息处理技术、测试技术、人工智能理论与技术的发展与应用都促进了制作工艺技术的发展。
现代机械制造中较多的采用了数控机床、机器人、柔性制造的单元和系统等高技术的集成,来满足产品个性化和多样化的要求[1]。
但是传统的机械制造工艺在机械制造中也是不可或缺的。
它虽已经慢慢的被新的科学技术所代替,但是新的科学技术的发展和创新是离不开传统机械制造工艺的基础的。
传统的机械制造工艺一般是指:
热加工和冷加工两种,主要热加工有铸造,锻打,焊接,热处理等;
冷加工一般是指车、铣、刨、磨、钳、拉、镗等。
机械制造工艺就是在这些加工工艺的基础上一步一步的演变过来的,从传统的车床到现在的自动化数控车床,从过去的人工装夹到现在的全自动智能机械,从过去的生产质量低效率低到现在的高产高效,这一系列的进步,都是在传统工艺的成熟发展下开展的[2]。
机械制造工艺的发展,离不开市场要求的牵引和科技发展的推动。
在市场需求不断变化的驱动下,机械制造业的生产规模沿着“小批量—少品种大批量—多品种变批量”的方向发展;
在科技发展和机械制造技术本身的不断完善下,机械制造业的资源配置沿着“劳动密集—设备密集—信息密集—知识密集—智能密集”的方向发展。
与之相适应,机械制造技术的生产方式沿着“手工—机械化—单机自动化—刚性流水自动化—柔性自动化—智能自动化”的方向发展;
加工方法也日趋增多和完善,在传统制造技术不断完善的同时,一些新的制造技术不断地涌现和被采用,机械加工所能表达到的精度也从本世纪初的0.1mm向目前的纳米级发展[3]。
1.2零件加工过程简介
零件在工艺规程制定之后,就要按工艺规程顺序进行加工。
加工中除了需要机床、刀具、量具之外,成批生产时还需要机床夹具。
夹具是机床和工件之间的连接装置,使工件相对于机床或者刀具获得正确的位置。
机床夹具的好坏直接影响工件加工表面的位置精度和生产率;
机床夹具按使用范围分为:
通用夹具、专业夹具、可调整夹具和成组夹具、组合夹具和随行夹具等;
近年来,数控机床、加工中心、成组技术、柔性制造系统等新加工技术的应用对机床夹具也提出了新的要求:
要能装夹一组具有相似特征的工件、能适用于精密加工的高精度机床和各种现代化的制造技术的新型机床以及采用以液压站等为动力的高效夹紧装置。
零件生产过程是指从原材料(或半成品制成产品的全部过程。
对机器生产而言包括原材料的运输和保存,生产的准备,毛坯的制造,零件的加工和热处理,产品的装配、及调剂,油漆和包装等内容。
生产过程的内容十分广泛,现代企业用系统工程学的原理和方法组织生产和指导生产,将生产过程看成是一个具有输入和输出的生产系统。
能使企业的管理科学化,使企业更具应变力和竞争力。
其中。
零件的生产过程中以零件的加工为重点部分,这一部分的设计,关系着整个零件在生产过程中的成败,要想生产出合理、经济、使用,同时合格优秀的产品,加工工艺流程的设计是非常重要的[4]。
机器的生产过程中,改变生产对象的形状、尺寸、相对位置和性质等使其成为成品或半成品的过程称为工艺过程。
将铸、锻件毛坯或钢材经机械加工方法,改变它们的形状、尺寸、表面质量,使其成为合格零件的过程,称为机械加工工艺过程。
在热处理车间,对机器零件的半成品通过各种热处理方法,直接改变它
们的材料性质的过程,称为热处理工艺过程。
最后,将合格的机器零件和外购件、标准件装配成组件、部件和机器的过程,则称为装配工艺过程。
无论是哪一种工艺过程,都是按一定顺序逐步进行的——加工工艺流程。
为了便于组织生产,合理使用设备和劳力,以保证产品质量和提高生产效率,任何一种工艺过程又可划分为一系列工序[5]。
第2章零件的工艺分析及生产类型的确定
2.1零件的作用
题目所给的零件是CA1340自动车床上的杠杆(见图,它位于自动车床的自动机构中,与灵活器配合使用,起制动的作用。
图2-1CA1340自动车床的杠杆零件图
2.2零件的工艺分析
杠杆共有三组加工表面,它们之间有一定的位置要求,现分述如下:
1.以Φ6H7孔为中心的加工表面
这一组加工表面包括:
两个Φ6H7的孔,粗糙度为Ra1.6;
尺寸为20mm且与两个孔Φ6H7相垂直的四个平面,粗糙度为Ra6.3。
其中,主要加工表面为两个Φ6H7的孔。
2.以Φ20H7孔为中心的加工表面
一个Φ20H7的孔及其倒角,粗糙度为Ra1.6;
两个与Φ20H7孔垂直的平面,粗糙度为Ra3.2;
一个中心轴线与Φ20H7孔中心轴线平行且相距8mm的圆弧油槽;
还有一个与Φ20H7孔垂直的油孔Φ4,并锪沉头孔。
其中,Φ20H7孔及两端面为主要加工面。
3.以Φ8H7孔为中心的加工表面
两个Φ8H7的孔,Ra1.6;
一个槽和一个M4mm的螺纹孔。
其中,主要加工表面为Φ8H7孔。
这三组加工表面之间有一定的位置要求,主要是:
(1Φ6H7孔与Φ20H7孔具有平行度,公差为0.06mm。
(2Φ8H7孔与Φ6H7孔具有平行度,公差为0.08mm。
由以上分析可知,对于这三组加工表面而言,可以先加工一面一孔,以它们为精准加工其它表面,并且可以保证加工面之间的位置精度要求。
另外,该零件结构简单,工艺性好[5]。
2.3零件的生产类型
原始资料:
该零件图样,Q=30000件/年,n=1件/台,每日一班。
依据设计的题目每年3万件,零件是CA1340自动车床上的杠杆,质量为12kg,由文献[1,89-90]可知,其属轻型零件,生产类型为大批生产。
第3章选择及确定毛坯,设计毛坯3.1选择毛坯
零件的材料为球墨铸铁QT45-5。
考虑到零件结构简单,工艺性好,在工作过程中受力不大及没有经常承受交变载荷,因此,应该选用铸件。
由于零件年产量为30000件,以达到大批生产的水平,而且零件的轮廓尺寸不大,重量在12kg以下,故可采用机械造型中的金属模铸造[6]。
3.2确定毛坯尺寸和公差
由文献[3,5-1]可知,该零件为球墨铸铁QT45-5,金属型铸造,得公差等级CT为8-10。
查表5-3,取CT为9,查得铸件各尺寸公差为1.6-3.2mm。
分析本零件,除两个Φ8H7的孔和一个Φ20H7的孔以及两个Φ6H7的孔的Ra=1.6μm,其余各表面Ra≥1.6μ,因此这些面的毛坯尺寸只需将零件的尺寸加上查得的余量和公差即可(由于有的表面只需粗加工,这时可取表中的较小值。
当要粗加工和半精加工时,可取大值。
单边加工时:
/2
RFRMACT
=++(3-1双侧加工或外圆面时:
2/2
RRFRMACT
==++(3-2内腔加工时:
-2-/2
=(3-3式中R—毛坯尺寸
F—基本尺寸
RMA—机械加工余量
CT—公差等级
根据铸件的公差等级及要求加工余量,由文献[3]得知:
1.对于加工Φ20H7两端面时,根据铸件的公差等级及要求加工余量分别由文献[3,5-3],由于零件基本尺寸为80所以毛坯单边加工
余量为Z=3mm。
2.Φ6二孔外端面的加工余量,由文献[3,5-3,5-4]可知,取毛坯的单边加工余量Z=3.5mm,铸件尺寸精度等级为5,固偏差为±
0.5。
3.Φ6二孔加工余量,两内孔精度要求为IT7级,由文献[3,5-3,5-4]可知,确定工序尺寸及余量为Z=0.2mm。
4.Φ8孔的加工余量,孔的精度要求为IT7,由文献[3,5-3,5-4]可知,确定工序尺寸及余量为Z=0.2mm。
5.Φ20孔的加工余量,孔的精度要求为IT7,由文献[3,5-3,5-4]可知,确定工序尺寸及余量为Z=2mm。
6.槽的加工余量,由文献[3,5-3]可知,确定工序尺寸及余量为Z=2mm。
综上所述确定毛坯尺寸如下表3-1:
表3-1杠杆毛坯尺寸(铸件
第4章选择加工方法,制定工艺路线4.1基面的选择
基面的选择是工艺规程设计中的重要工作之一。
基面选择得正确与合理,可以使加工质量得到保证,生产率得以提高。
否则,加工工艺过程中会问题百出,更有甚者,还会造成零件大批报废,使生产无法正常进行。
(1精基准的选择
主要原则有:
①基准重合原则;
②基准统一原则;
③自为基准原则;
④互为基准原则[7]。
对本零件而言,是以Φ20H7的孔为设计基准的,所以选Φ20H7的孔为加工的精基准(符合基准重合原则。
(2粗基准的选择
选择粗基准主要是选择第一道机械加工工序的定位基准,以便为后续的工序提供精基准。
选择粗基准的出发点是:
一要考虑如何分配各加工表面的余量;
二要考虑怎样保证不加工面与加工面间的尺寸及相互位置要求。
这两个要求常常是不能兼顾的,但对于一般的轴类零件来说,以外圆作为粗基准是完全合理的[7]。
零件中Φ32mm的外圆表面为不需要加工的表面,而且为了能够保证Φ32mm的外圆表面与Φ20H7的孔的位置关系,主要是同轴度,所以综合各种因素我们选择Φ32mm的外圆作为粗基准。
4.2零件表面加工方法的选择
本零件的加工面有外圆端面、内孔、槽等,材料为球墨铸铁,以公差等级和表面粗糙度要求,由文献[4,56-98]可知其加工方法可如下:
(1加工Φ20H7两端面
由文献[4,66-67]查得其精度为IT11虽不高,但其表面粗糙度为3.2um,所以需要粗铣、半精铣、精铣。
(2加工Φ6二孔孔外端面
因为未注公差等级,根据[4,56-98]查得公差为IT11,表面粗糙度为6.3μm,所以可以先粗铣再半精铣就可。
(3加工Φ6二孔
因为其精度等级较高为7级且表面粗糙度也为1.6,所以总体要求高,可以粗铰、精铰。
(4加工Φ8孔
因为其精度等级较高为7级且表面粗糙度也为1.6,所以总体要求高,可以粗铣、精铰。
(5加工Φ20孔
(6槽的加工
其表面粗糙度为6.3μm,未注公差等级,根据[4,56-98]查得公差为IT11~IT12,所以可以粗铣、半精铣。
4.3工艺过程制定
制定工艺流程的出发点,应该是使零件的几何形状、尺寸精度及位置精度等技术要求能得到合理的保证。
在生产纲领已确定为大批生产的条件下,可以考虑采用万能性机床配以专用夹具,并尽量使工作集中来提高生产率。
除此以外,还应当考虑经济效率,以便使生产成本尽量下降。
工艺流程:
工序1去应力退火;
工序2粗铣、半精铣、精铣Φ20H7孔的左端面。
以Φ32外圆柱面和一个未加工面为粗基准,选用X61W型万能升降台铣床并加专用夹具;
工序3粗铣、半精铣、精铣Φ20H7孔的右端面。
以Φ32外圆
柱面和一个未加工面为粗基准,选用X61W型万能升降台铣床并加专用夹具;
工序4钻R3mm圆弧油槽,扩Φ20H7孔。
以Φ20H7孔的一个端面和Φ32外圆柱面为基准,选用Z525型立式钻床和专用夹具;
工序5粗铰、精铰Φ20H7孔,锪Φ20H7孔倒角。
以Φ20H7孔的一个端面和Φ32mm外圆柱面为基准,选用Z525型立式钻床和专用夹具;
工序6粗铣Φ6H7孔的四个端面。
以Φ20H7孔的一个端面和Φ20H7孔为基准,选用X61W型万能升降台铣床和专用夹具;
工序7半精铣Φ6H7孔的四个端面。
工序8钻、粗铰、精铰Φ6H7两孔。
以Φ20H7孔的一个端面和Φ20H7孔为基准,选用Z5125型立式钻床和专用夹具;
工序9钻、粗铰、精铰Φ8H7两孔。
以Φ20H7孔的一个端面和Φ20H7孔为基准,选用Z525型立式钻床和设计夹具;
工序10钻Φ4油孔、锪Φ8圆锥沉头孔。
以Φ8H7孔的一个端面和Φ20H7孔为基准,Φ20H7孔辅助定位,选用Z525型立式钻床和专用夹具;
工序11钻M4螺纹底孔、攻M4螺纹孔。
以Φ20H7孔的一个端面和Φ20H7孔为基准,Φ6H7孔辅助定位,选用Z525型立式钻床和专用夹具;
工序12粗铣。
以Φ20H7孔的一个端面和Φ20H7孔为基准,Φ6H7孔辅助定位,选用X61W型万能升降台铣床和设计夹具;
工序13半精铣槽。
工序14去毛刺;
工序15清洗;
工序16终检。
第5章工序设计
5.1选择机床
工序2,3:
粗铣,半精铣,精铣Φ20H7孔的两端面。
选用机床:
X61W万能升降台铣床。
工序4:
钻R3mm圆弧油槽,扩Φ20H7孔.选用Z525立式钻床。
工序5:
粗铰、精铰Φ20H7孔,锪Φ20H7孔两端倒角1×
45°
。
选用Z525立式钻床。
工序6,7:
粗铣,半精铣,精铣Φ6H7孔的四个端面。
选用机床:
X61W万能升降台铣床。
工序8:
钻、粗铰、精铰Φ6H7两孔。
选用Z525立式钻床
工序9:
钻、粗铰、精铰Φ8H7孔。
选用Z525立式钻床。
工序10:
钻Φ4油孔,锪Φ8圆锥沉头孔。
工序11:
钻M4mm螺纹底孔,攻M4mm螺纹孔。
工序12,13:
粗铣,半精铣槽。
5.2选择夹具
粗铣,半精铣,精铣Φ20H7孔的两端面。
选用专用夹具。
钻R3mm圆弧油槽,扩Φ20H7孔.选用专用夹具。
粗铣,半精铣,精铣Φ6H7孔的四个端面。
选用专用夹具。
钻、粗铰、精铰Φ8H7孔。
钻Φ4油孔,锪Φ8圆锥沉头孔。
选用设计夹具。
工序12,13:
5.3根据不同工序选择刀具
1.工序2,3中由于零件材料为球墨铸铁QT45-5,在粗铣时要求的精度等不高,且是大批量生产,那么就要提高生产