唐平推钢式连续热炉.docx
《唐平推钢式连续热炉.docx》由会员分享,可在线阅读,更多相关《唐平推钢式连续热炉.docx(24页珍藏版)》请在冰豆网上搜索。
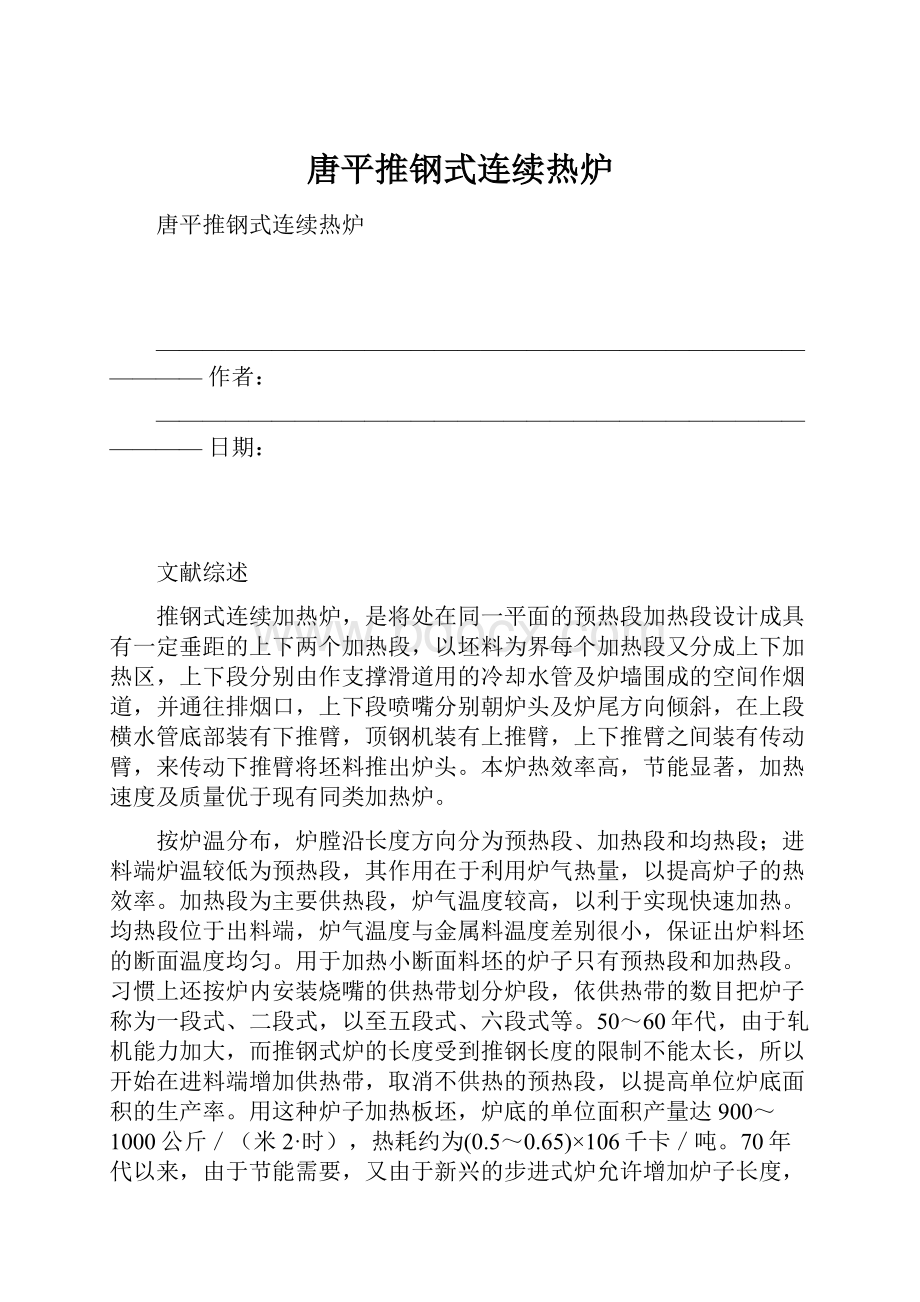
唐平推钢式连续热炉
唐平推钢式连续热炉
————————————————————————————————作者:
————————————————————————————————日期:
文献综述
推钢式连续加热炉,是将处在同一平面的预热段加热段设计成具有一定垂距的上下两个加热段,以坯料为界每个加热段又分成上下加热区,上下段分别由作支撑滑道用的冷却水管及炉墙围成的空间作烟道,并通往排烟口,上下段喷嘴分别朝炉头及炉尾方向倾斜,在上段横水管底部装有下推臂,顶钢机装有上推臂,上下推臂之间装有传动臂,来传动下推臂将坯料推出炉头。
本炉热效率高,节能显著,加热速度及质量优于现有同类加热炉。
按炉温分布,炉膛沿长度方向分为预热段、加热段和均热段;进料端炉温较低为预热段,其作用在于利用炉气热量,以提高炉子的热效率。
加热段为主要供热段,炉气温度较高,以利于实现快速加热。
均热段位于出料端,炉气温度与金属料温度差别很小,保证出炉料坯的断面温度均匀。
用于加热小断面料坯的炉子只有预热段和加热段。
习惯上还按炉内安装烧嘴的供热带划分炉段,依供热带的数目把炉子称为一段式、二段式,以至五段式、六段式等。
50~60年代,由于轧机能力加大,而推钢式炉的长度受到推钢长度的限制不能太长,所以开始在进料端增加供热带,取消不供热的预热段,以提高单位炉底面积的生产率。
用这种炉子加热板坯,炉底的单位面积产量达900~1000公斤/(米2·时),热耗约为(0.5~0.65)×106千卡/吨。
70年代以来,由于节能需要,又由于新兴的步进式炉允许增加炉子长度,所以又增设不供热的预热段,最佳的炉底单位面积产量在600~650公斤/(米2·时),热耗约为(0.3~0.5)×106千卡/吨。
连续加热炉通常使用气体燃料、重油或粉煤,有的烧块煤。
为了有效地利用废气热量,在烟道内安装预热空气和煤气的换热器,或安装余热锅炉。
工业炉的基本类型
工业炉按供热方式分为两类:
一类是火焰炉(或称燃料炉),用固体、液体或气体燃料在炉内的燃烧热量对工件进行加热;第二类是电炉,在炉内将电能转化为热量进行加热。
大型台车式炉火焰炉的燃料来源广,价格低,便于因地制宜采取不同的结构,有利于降低生产费用,但火焰炉难于实现精确控制,对环境污染严重,热效率较低。
电炉的特点是炉温均匀和便于实现自动控制,加热质量好。
按能量转换方式,电炉又可分为电阻炉、感应炉和电弧炉。
工业炉按热工制度又可分为两类:
一类是间断式炉又称周期式炉,其特点是炉子间断生产,在每一加热周期内炉温是变化的,如室式炉、台车式炉、井式炉等;第二类是连续式炉,其特点是炉子连续生产,炉膛内划分温度区段。
在加热过程中每一区段的温度是不变的,工件由低温的预热区逐步进入高温的加热区,如连续式加热炉和热处理炉、环形炉、步进式炉、振底式炉等。
火焰炉结构
在冶金.化工.机械制造等工业部门中,以燃料燃烧的火焰为热源的各种工业炉统称为火焰炉。
火焰炉广泛应用于物料(工件)的焙烧.干燥.熔化,熔炼加热和热处理等生产环节。
火焰炉得到广泛应用的原因有以下几点:
1:
火焰炉所采用的燃料有较大的灵活性,可以根据燃料的种类和规格建造各种不同型式和构造的炉子、,以满足生产的需求。
2:
燃料的供应一般比较充足,价格也比较低。
3:
火焰炉对于被处理物料(工件)的形状大小。
规格等的限制较少,大到几百吨的金属锭,小到细颗粒,都可以在火焰炉中进行热工处理。
4:
火焰炉工作温度的范围比较大,可以满足不同工作温度的需求。
5:
火焰炉通常是直接加热式,但如果有特殊要求,也可以进行间接加热。
正是以上的几点,使的火焰炉的到广泛的应用。
火焰炉一般由炉子热工工艺系统、装出料系统、热工检测及自动控制系统等
三个系统互相配合,使炉子正常运转。
炉子的热工工艺系统是火焰炉最基本的组成部分。
包括炉子的工作室(炉膛)、供热系统(油泵、管道、燃烧装置等)、排烟系统(烟道、烟闸、换热器、余热锅炉、烟囱、排烟机等)及冷却系统等。
参见图1—1。
工作室是炉子的核心。
主要的热工及工艺过程都在工作室内完成。
炉子其他各部分的任务是为工作室内所进行的热工工艺过程提供有利条件。
装出科系统和热工检测及自动控制系统,是现代化火焰炉不可缺少的两个工作系统。
前者包括炉前炉后的装出料机械和炉内的运料机械,后者包括热工参数的检测仪表、显示仪表记录仪表、自动控制仪表或计算机以及执行机构等。
在炉子上配备这两个系统,可以实现产的自动化操作,从而提高炉子的生产指标。
下面仅对热工工艺系统中的主要组成部分加以介绍。
火焰炉的组成
炉膛(工作室):
炉膛一般是由炉墙、炉顶和炉底构成的一个近乎六面体的空间。
因工艺和用途的不同,炉膛形状是各式各样的。
大多数炉膛是在高温下工作,经受炉气、炉尘和炉渣的侵蚀和冲刷。
因此,要求构成炉墙、炉顶和炉底等所用的材料、结构型式的尺寸等,都必须适应这一特点,以保证炉子的正常工作。
炉墙:
炉子四周的围墙称为炉墙。
加热炉都采用直立的炉墙,分为侧墙和端墙。
为保证炉墙结构的稳定性,炉墙必须有一定的厚度,并应随炉子尺寸增大和炉膛温度的升高而增厚。
为减少散热和蓄热损失,炉墙应设有绝热层。
侧墙的厚度一般为2—2.5块砖厚(464。
580mm),其中起稳定作用的主墙用粘土砖砌筑,厚度为1.5—2块砖厚,其余部分为绝热材料,构成复合炉墙。
用耐火浇注料或耐火可塑料等制作的炉墙.主墙厚度一般为250一300mm。
端墙厚度应视烧嘴孔道尺寸而定,一般为2.5—4块砖厚。
为提高炉子强度和气密性,炉培外面包以4—10mm厚的钢板。
炉墙的经济厚度,应根据砌休的材料费和蓄热散热损失引起的燃料费进行优化计算确定。
炉墙上常设有炉门、窥视孔、烧嘴孔以及热工参数检测孔等孔洞。
为防止砌体破坏,炉墙应尽量避免直接承受附加负荷,炉门、冷却水管等构件应设置在钢结构上。
加热炉炉门尺寸已标准化,尺寸可由有关手册中查得。
侧墙上还必须设有供检修用人孔假门。
炉顶:
炉顶是炉膛组成中的薄弱环节。
炉顶是否牢固可靠,对炉子工作有重大影响。
尤其在熔炼炉(如平炉.玻璃炉)中,往往因受炉顶温度的限制而妨碍炉子生产率的提高,由于炉顶的损坏而降低炉子的作业效率。
固在炉子设计时对炉顶的可靠性必须给予足够的重视。
炉项按其结构型式分为拱顶和吊项两种。
拱顶可用楔形砖砌筑或不定形耐火材料捣制而成,结构参见图1—3。
拱顶的拱角可变化在60度到180度之间,通常采用的有60度、90度、120度和180度拱顶。
60度拱顶的R等于炉子跨度B,拱顶矢高A=o.1345,称为标准拱顶。
拱顶的质量W作用于拱角砖上,承受在两侧护路上,水平分力F通过拱角梁由钢结构承受。
吊顶是由一些特制的异形砖组成的,异形砖用金属吊杆单独地或成组地吊在护子钢结构上。
吊顶的结构型式很多,图1—4是常见的几种吊顶结构。
图中(6)是槽砖吊挂结构,这种吊砖结构和砌筑都比较简单,更换也方便。
为避免挂砖的工字钢温度过高,砖的上表面不允许敷设绝热层,因此萨顶散热量较大。
图中(6);(f)是颈吊式吊挂结构,这种结构的每一块吊砖都有一个夹钩和一个吊杆。
由于金属夹钩在砌体外面,故可以在砖的部分表面敷设绝热层,炉顶散热损失较小。
但这种结构只适用于吊挂水平的及倾斜度不大的炉顶,较大倾斜度及转弯处须做特殊处理。
图中(墨)是齿槽式吊挂结构,它的优点是砖与砖之间互相咬合,气密性好,个别砖块即使断裂也不致掉落,缺点是砖形复杂,公差要求严格,砌筑难度大。
这种结构的炉顶砖上面也不宜敷设绝热层。
炉底:
炉底的工作条件是非常恶劣的。
它不仅要承受被处理物料的机械负荷、碰撞与摩擦等作用,有时还要受到被处理物料的化学侵蚀及熔体的渗透等。
炉底结构型式和所用材料,决定于工艺过程和炉内的工作温度及化学反应的性质。
加热炉的炉底结构型式基本有两种:
①固定式炉底一—被处理的炉料推钢机推动在炉底上移动。
为了避免物料与炉底耐火材料直按摩擦而损坏炉底与金属表面.有些情况下用砂封的移动式炉底,在炉底上装有金属滑轨或水冷管滑道。
②移动式炉底——机械化的活动炉底带动炉内物料一道移动,属于这种类型的炉子很多,其中主要有步进式加热炉、转底式加热炉、分室式加热炉、辊底式加热炉和链式加热炉等。
这种炉底因为需要设置复杂的炉底机械装置,构造比固定式炉底复杂。
炉子基础和钢结构:
修建炉子时必须打好炉子基础。
炉子基础一方面要承受整个炉子的质量不致下沉或倒场;另一方面还要防止炉底受潮或遭受地下水的侵袭,保证炉于正常工作。
根据炉子的大小和土质的好坏,炉子基础可采用不同材料和结构来砌筑。
小炉子可用红砖或块石砌筑,绝大多数大中型炉子都采用混凝土或钢筋混凝土修建,因为它既结实又抗潮。
在设计和修筑炉子基础时应注意以下几点:
(1)混凝土任何部分的温度都不允许超过300℃,否则混凝土就会变质而压坏。
因此当炉底直接建筑在混凝土上时,要在炉底与混凝土之间用绝热材料隔开,对于温度较高的炉子,要把炉底架空起来,靠空气冷却基础。
(2)炉子基础必须是整块的,不允许有断裂现象。
炉子基础要与其他基础(如辅助设备、二房、烟囱等基础)分开,以避免由于基础受力不同而引起不均匀下沉,使基础开裂或设备倾
(3)基础的底部应在地基的冻土线以下,以免因天气寒冷使基础遭道到破坏。
(4)炉子基础应尽可能地建于地下水面以上,以免由于地下水的侵入而损坏基础的强度。
炉子个别部分(如烟道。
换热器等)必须建在地下水面以下时,一定要有防水沟或防水层等严密的防水措施。
炉子钢结构一般是由钢柱、横梁、拉杆、拱角梁等组成的钢架。
其作用是:
(1)加固炉子砌体,承受炉子拱顶的水平分力或者炉子吊顶的全部重量,并把它们的作用力传到炉子基础上。
(2)钢结构也是炉子的骨架,在其上可以安置炉门框、炉门、烧嘴和冷却水管等各种炉子部件,井承受这些部件的重量。
(3)可抵抗砌体的高温膨胀,使炉子受热后不发生变形。
为使钢架形成整体而把炉子夹固起来,各个独立的钢件之间必须互相连接起来,除有特殊要求采用活动连接外.一般都采用焊接结构。
钢铁下端大都固定在炉子基础上。
由于钢架是固定死的,故各部分砌体均需留有膨胀缝,以免受热后钢架变形。
钢结构所用材料通常有槽钢、工字钢、角钢、圆钢、钢轨和钢板等。
为使钢结构工作可靠,又能节约钢材,各种钢件的尺寸和规格的选用都应通过计算,并参照实际使用资料来确定。
此外,炉子的平台、栏杆及扶梯等,也都用于钢结构的范围,应根据炉子的具体情况来设置。
两段式连续加热炉
按炉温制度分为加热期和预热期,炉膛也相应的分为加热段和预热段。
加热薄料坯的小炉子也有单面加热的,一般多为两面加热。
烧煤时设有端部的燃烧室,。
称为炉头,下加热的燃烧室设在两侧,成为腰炉。
具有两面加热的两段式连续加热炉,其燃料的分配比例上加热大约是30%到40%,下加热大约是60%到70%。
以为下面的炉气要上浮,部分气体有两侧的空隙上来,使下部的热量供应不足;其次钢坯下面的冷却水要带走大量的热量,这部分热几乎都要有下面加热来供给;此外,钢坯与水管接触的地方要产生黑印,若下加热能力不足,则黑印回更加严重,而到了实体段时,只有上表面能够加热。
因而需要给下加热燃料多供给些。
三段式连续加热炉
三段式连续加热炉在加热制度上采用预热期.加热期.和均热期的三段温度制度。
在炉子的结构上也相应的分为预热段.加热段和均热段。
一般有三个供热点,及上加热.下加热和均热段供热。
断面尺寸较大的钢料和合金钢料的加热,多采用三段式炉温制度的三段式连续加热炉。
三段式加热炉炉型的变化很多,但在结构上仍有一些共同的基本点。
炉顶轮廓曲线变化是很大的,它大致与炉温曲线相一致,及炉温高的区域炉顶也高,炉温低的区域,其炉顶也相应的压低。
在加热段与预热段之间,有一个比较明显的过渡,炉顶向预热段压下。
这是为了避免加热段高温区域有许多热量向预热段的低温区域辐射,加热段是主要燃烧区域,空间比较大,有利于辐射传热:
预热段是余热利用的区域,压低炉顶缩小空间,有利于强对流换热。
但是也有的炉子着眼于强化加热,使加热段相对的延长,加热段与预热段的界限也不在十分的明显。
下面是二段式和三段式加热炉炉温---时间表比较,图(a)是二段式,图(b)
为三段式。
燃烧系统及其控制
烧嘴及其分布
加热钢锭用推钢式加热炉多采用平焰烧嘴,其火焰呈圆盘形,辐射能力强,加热速度快,火焰直径800-1000mm,厚度50150mm,对降低炉膛高度有利。
烧嘴分布有矩形排列(a)和交错排列(b)两种形式,如图4所示。
图4中,在炉膛尺寸和烧嘴总功率一致的前提下,由于烧嘴火焰呈圆盘形,(b)种排列烧嘴间的死角较(a)小,且两排烧嘴在钢锭运行方向上的位置互补,有利于避免因烧嘴间隔过大而造成钢锭表面黑线的产生。
炉子加热段烧嘴配置的功率要大,数量要多,炉膛温度相对较高,使钢锭快速加热到设定温度。
而均热段烧嘴配置的功率应相对较小,炉膛温度相对较低,使钢锭由表及里温度趋于均匀。
燃烧控制技术
烧嘴及其燃烧控制是步进炉的核心技术之一,手动控制已被自动控制方式所取代。
目前大规格钢锭推钢式加热炉可选用的燃烧自控方式通常有:
(1)空燃比例连续控制系统,该系统主要由烧嘴、燃烧控制器、空气/燃气比例阀、空气/燃气电动蝶阀、空气/燃气流量计、热电偶、气体分析装置、PLC等组成。
工作原理是由热电偶或气体分析装置检测出来的数据传送到PLC与其设定值进行比较,偏差值按比例积分、微分运算输出4-20mA的电信号分别对空气/燃气比例阀和空气/燃气电动蝶阀的开度进行调节,从而达到控制空气/燃气比例和炉内温度之目的。
(2)双交叉限幅控制系统,该系统主要由烧嘴、燃烧控制器、空气/燃气流量阀、空气/燃气流量计、热电偶等组成。
工作原理是:
通过一个温度传感器热电偶把测量的温度变成一个电信号,该信号表示测量点的实际温度,该测量点的温度期望给定值是由预存贮在上位机中的工艺曲线自动给定的。
根据这两个温度值偏差的大小,PLC自动校准燃气/空气流量阀的开度。
该阀通过电动执行机构定位。
空气/燃料比控制,借助于孔板和差压变送器来测量空气流量,燃气的流量是借助于一台安装在燃气支管上的质量流量计来测量,使精确的温度控制得以实现。
(3)数字化脉冲控制系统,该设计的前提思路是:
某种形式分布的烧嘴,在额定的燃气压力、热值条件下,单位时间内喷出热
气流的总热烙是一个定值,根据锭坯在炉内的具体分布情况和加热要求(已输PLC),对各烧嘴的燃烧工况进行合理组合,就会获得满意的炉内温度场的分布,从而保证了锭坯的加热质量。
数字化脉冲控制的工作原理(图5)是在一段时间内燃气总量不变的情况下,根据预调好的空气/燃气比,按时序分配的结果,对各烧嘴的燃烧功率进行大小火控制,实现炉内各区的供热量与负荷的合理配置。
(4)其他控制技术①助燃空气温度一流量控制。
推钢炉开炉或炉内工况变化时,由热交换器加热的助燃空气温度是不稳定的。
当炉压不变时,温度升高,导致相同流量时空气质量的减少,使得烧嘴前的实际空气/燃气比下降;反之亦然。
为确保烧嘴能合理燃烧,PLC应输人助燃空气量随温度变化的逻辑程序,用实测的热空气温度信号对其进行流量补偿。
②烧嘴燃烧安全控制系统。
高水平的烧嘴燃烧安全控制系统是炉子安全生产的重要保证,包括点火前的安全吹扫、点火程序控制、燃烧火焰的自动检测和燃气快速切断阀,不仅要求系统设计可靠,而且要求构成系统的每个部件的质量要极为可靠。
燃烧设备的爆炸事故大多为烧嘴点火时引起的。
每次烧嘴点火前应启动氮气(也有用空气的)吹扫系统,对燃气管道吹扫一定时间,耗气量约为管道容积的3-5倍,以清除烧嘴前燃气管道内残留的可燃性混合气体,然后再将空气管道至烧嘴间阀门开启至最大位置,启动炉膛空气吹扫系统,用助燃风机对炉膛进行吹扫。
③自动点火安全控制。
工作原理是:
吹扫结束时,阀门回到最小开度,燃气电磁阀打开,同时点火变压器通过烧嘴上的点火电极高压放电,将燃气点燃,然后进人火焰检测程序。
火焰稳定后,经烧嘴上的监测电极反馈给自动点火控制器一个5-30mA的信号,自动点火控制器接受到信号后,各阀门逐渐进人工作开度。
若烧嘴没有形成稳定火焰或熄火时,自动点火控制器不能接受到监测信号,此时进人故障状态,输出一个故障信号,自动点火控制器自动切断燃气电磁阀。
自动点火控制器可按设定程序或在手动复位后才能进行第二次点火程序。
火焰监测器分为离子式、紫外线式和光敏元件等
排烟系统
排烟系统要求一是能克服烟道阻力,顺利地将烟气排空;二是精确控制炉膛压力;三是采用热交换器,最大程度地回收烟气热量以预热助燃空气。
排烟系统主要由保温烟道、换热器、烟道闸门、排烟风机(强制排烟时)和烟囱等组成。
烟道
一般烟道常常埋在地下,这样对车间布置方便,但如地下水位较高时也可把烟道放在地上。
埋设在地下的烟道结构如图l—9所不,埋设深度一般都布置离地面至少300mm以下。
对于穿过有动载荷(如车辆通过)的地段,穿过料场或成品库以及汽锤等振动较大的操作区域的烟道,应该用混凝土框把烟道包起来。
处于地下水位以下的烟道应设有可靠的防水措施.通常是包以混凝土框,并在混凝土外面包以钢板。
必要时须在烟道附近设置深水井,并用水泵抽水。
烟道布置要尽量缩短长度和减少烟气流动阻力损失,要与厂房柱基、设备基础和电缆等保持一定的距离,以免它们受烟道温度的影响。
当烟道内设有余热回收装置时,一般要设置分烟道和相应的烟道闸板。
为了控制排烟量以调节沪膛压力,烟道上必须设置烟道闸板。
当烟气温度低于400一600℃时,闸板可用灰口铸铁件或铸钢件制作;当温度高于600一700℃时,应采用水冷闸板、空冷闸板、衬砖闸板或耐热合金钢制造的闸板。
烟囱
烟囱是通常用的一种排烟装置。
烟囱结构有砖烟囱、钢筋混凝土烟囱(内衬砖)和金属烟囱(有的衬砖省的不衬砖)。
烟囱高度低于60一70m时,砖烟囱比钢筋混凝土烟囱造价低,但砖烟囱砌筑比较因难(不便于机械化施工),而且寿命也不如钢筋混凝土烟囱。
所以,小烟囱常用砖烟囱,45m高以上的烟囱一般采用钢筋混凝土烟囱。
烟囱必须有独立的基础,不能与烟道基础相连,以免烟囱下沉时烟道基础断裂。
烟囱底部应设人孔烈备烘烤烟囱、扒灰和修理内衬之用。
金属烟囱一般用5—10mm厚钢板焊成,其寿命低,但修建快,造价低,在小炉子上时常采用。
当温度较高时,内部须衬以耐火材料。
排烟方式
分为自然排烟和强制排烟两种。
当烟道阻力<500600Pa时,推荐自然排烟方式,该方式无动力消耗,运行成本低,但随烟囱高度的增加,建筑费用将激增。
烟道阻力较大时,应采用强制排烟方式。
又分为引风机排烟和引射风机排烟。
前者采用的是高温风机,开炉时因烟气温度低风机负荷较大,炉子正常工作时又因为高温烟气的自身抽力使风机负荷下降,因此引风机应变频控制,此方案虽然有烟囱高度小的优点,但因排烟温度高,风机易损坏而会造成停炉事故;后者为普通风机,但排烟效率低,功率应相对较大,有能量转换损失也可用变频控制。
换热器及其保护
目前常用的换热器有热管式、带翅片管式、麻花管式和喷流幅射式等类型。
其中热管式换热器的换热效率较贵;喷流幅射式换热器烟气人口温度要求》800℃;其他两种价格适中,但体积相对较大。
换热器除了具有良好的换热性能外,使用寿命也是其重要的质量指标。
换热器长期在高温状态下工作,其焊缝会产生热脆性而烧裂,在烟气人口处的材质可选1Crl8Ni9Ti,1Crl8Ni9和1Crl3等,应装设膨胀节,防止因热胀冷缩而使换热器体开裂。
换热器的工作环境也是换热器寿命的重要保证。
若使用不当,再好的换热器短时期内就可能损坏,因此在系统中必须有保护措施:
一是换热器烟气人口温度控制,即烟气稀释法,在换热器人口前烟道上增加一个冷却用空气阀门(冷空气可来自引风机);二是空气预热温度控制,即热风放散法,当助燃空气温度过高时,增大空气流量以降低空气温度,且打开热风管道的放散阀,将多余的热空气排人大气。
炉膛压力控制
炉膛压力不允许在负压状态下操作,以防冷空气进人炉内,破坏炉内气氛和影响加热质量,一般炉底处为1030Pa微正压。
当因炉门开启等原因造成炉压波动时,炉压的控制有两种方法可选:
一是通过烟道闸门的开大或关小达到控制炉压之目的;二是对引风机进行变频控制,通过控制排烟量来达到控制炉压。
工业炉的节能
对一个节能的加热炉的基本要求是:
有较高的炉底(或炉膛)有效利用率,在此面积(或炉膛)上有均匀的温度场,有较高的装载量;炉内加热元件(或装置)、炉气、炉膛对工件有良好的传热效果,可缩短工件加热时间;较好的保温能力和较少的热损失,有较高的热效率。
以上各要求须通过合理地设计炉型、炉衬、加热元件(或装置)等来实现。
工业炉节能的几个措施
(1)炉衬
炉衬在保证炉子的结构强度和耐热度的前提下,应尽量提高保温能力和减少储蓄热。
单纯依靠增加炉衬厚度来降低炉外壁温度是不合适的,因为这样做不仅会增加炉衬储蓄热和成本,还相应地减少了炉底面积(炉膛)的有效利用率。
而实行炉衬纤维化和轻质化,则有很大的节能效果。
耐火纤维也称陶瓷纤维,它具有耐高温、热导率低、密度小、蓄热量少、抗热震性能好等特点,耐火纤维炉衬可以采用叠铺或用预制块安装,也可用耐火纤维喷涂。
罩式退火炉在炉衬上采用硅酸铝针刺毯保温材料,取得了良好的节能效果,能耗比轻质砖炉衬降低40%,大大减轻了炉架的负荷。
(2)炉膛结构及强化热交换
使炉膛形成一个热交换的系统,在加热元件、炉衬和工件三者之间进行热交换。
提高炉膛热交换常有如下措施:
首先采用合理的炉膛空间。
由于集箱加热退火长度在9m以下,采用罩式炉,其加热元件均匀分布在炉膛内壁,确保炉膛均匀传热;若集箱长度在6m以下,则只采用两个边炉罩组合,灵活运用,有效利用炉膛空间,提高了热效率。
其次在不增大炉膛空间容积的前提下,加大炉内壁的面积,以增大热交换面积,如采用波纹形的炉顶。
第三,可采用圆形炉膛,替代箱形炉膛,可强化炉膛对工件均匀传热的效果,并减少炉壁散热量。
第四,炉膛内安设风扇,以加强炉内对流传热。
特别是小型加热炉,高速气流可破坏停滞在工件表面阻碍传热和界面反应的炉气边界底层,起到缩短加热时间和加快提高工件温度的作用。
第五,炉膛密封,包括炉膛内各引出构件、炉壳、炉门等处的密封。
炉子密封影响气氛控制、工件品质和能耗。
当炉内有96Pa负压时,通过3cm2的孔洞将会吸进10m3/h冷空气,炉门开启0.2mm2,热能消耗会增加15%。
因此注意炉膛、炉壳、炉门等处的密封有利于节能。
(3)加热元件布置
对于电炉,加热元件的布置对节能有一定影响,在炉膛内均匀布置可形成温度均匀的有效加热空间。
本公司在边炉罩与中炉罩的衔接处仍安装了加热元件,可改善炉体结合区温度偏低的现象。
也可采用辐射管加热元件有利于炉温均匀和节能。
燃料炉的节能
燃料炉与电加热炉比较,主要不同点是其热源是依靠燃料燃烧和产生燃烧气体。
因此,其节能除具备电加热炉节能的基本要点外,主要是燃料燃烧和炉内气流合理组织等。
(1)油燃烧装置(或称喷嘴、燃烧器)
油的燃烧程度主要取决于油的雾化程度,一般认为雾化颗粒小于50μ的占85%以上最为理想,油的雾化效果决定于喷嘴结构和油的粘度。
油雾化的机理有:
压力雾化、气动雾化和发泡雾化。
依此制造了各种类型的喷嘴。
压力雾化的喷嘴是最常用的形式。
压力喷射雾化式的油压比例调节喷嘴(F型喷嘴),以油压为调风的动力,调节时自动地随之调风,自动地实现油风比例的调节。
本公司采用F型喷嘴替代R型喷嘴可显著节能。
气动雾化利用具有一定压力的雾化剂与燃油之间的相互作用把油雾化。
用这种机理制造的ZBF型转杯式燃油器,利用高速度旋转的转杯的离心力,使燃油雾化。
用它来代替压缩空气压力雾化的高压喷嘴,燃烧更为安全,可显著节油。
发泡雾化燃烧器适用于粘度较大的重油和渣油燃烧,其节油率可达6%以上。
(2)燃气燃烧装置(或称喷嘴、燃烧器)
对于气体燃料燃烧,当燃料与空气混合比例合适时,着火后可瞬间燃尽。
优良的气体烧嘴,能自动调节