锻压设备及锻工的安全技术.docx
《锻压设备及锻工的安全技术.docx》由会员分享,可在线阅读,更多相关《锻压设备及锻工的安全技术.docx(12页珍藏版)》请在冰豆网上搜索。
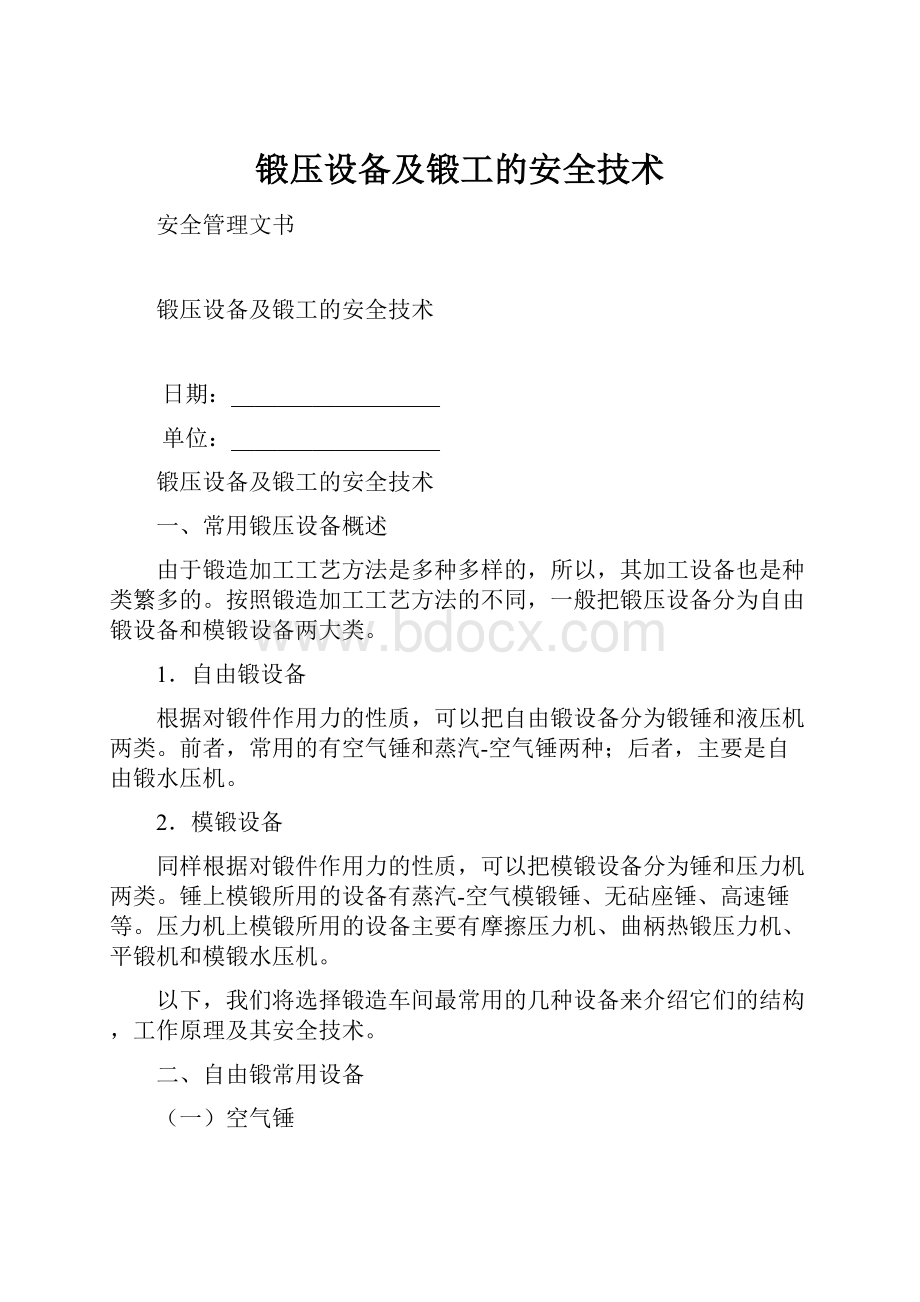
锻压设备及锻工的安全技术
安全管理文书
锻压设备及锻工的安全技术
日期:
__________________
单位:
__________________
锻压设备及锻工的安全技术
一、常用锻压设备概述
由于锻造加工工艺方法是多种多样的,所以,其加工设备也是种类繁多的。
按照锻造加工工艺方法的不同,一般把锻压设备分为自由锻设备和模锻设备两大类。
1.自由锻设备
根据对锻件作用力的性质,可以把自由锻设备分为锻锤和液压机两类。
前者,常用的有空气锤和蒸汽-空气锤两种;后者,主要是自由锻水压机。
2.模锻设备
同样根据对锻件作用力的性质,可以把模锻设备分为锤和压力机两类。
锤上模锻所用的设备有蒸汽-空气模锻锤、无砧座锤、高速锤等。
压力机上模锻所用的设备主要有摩擦压力机、曲柄热锻压力机、平锻机和模锻水压机。
以下,我们将选择锻造车间最常用的几种设备来介绍它们的结构,工作原理及其安全技术。
二、自由锻常用设备
(一)空气锤
空气锤是应用很广泛的一种自由锻造设备,它可以用于各种自由锻造工序。
也可用作胎模,在某些缺乏模锻设备的工厂里,还有用它来进行模锻的。
空气锤的打击能量(或吨位)以它落下部分的重量表示。
如落下部分的重量是4000N,则称该锤为400kg空气锤。
最常用的空气锤,落下部分的重量在1000~7500N之间,大于7500N的空气锤,一般被蒸汽-空气锤代替。
空气锤是靠电力驱动机构的作用,利用本身产生的压缩空气,推动落下部分动作,同蒸汽-空气锤比较,它的安装费用低,适合于小厂、修配厂使用,也适合小型锻件的生产。
其工作原理如图1所示。
开动电动机后,带动曲轴连杆机构1旋转,而使压缩气缸3内的活塞2作上下直线运动,当向下时,压缩气缸下部的空气被压缩,经过下阀室8内的旋阀进入工作气缸5的下部空间。
这时,工作气缸的上部空间缺气。
作用在工作活塞6下面的空气压力,使落下部分向上运动。
当压缩气缸的活塞2向上时,压缩气缸的上部气被压缩,并经过上阀室4内的上旋阀进入工作气缸的上部空间,工作气缸下部空间缺气。
作用在工作活塞上面的空气压力和活塞本身重量的共同作用,使落下部分向下,打击放在下砧7上的金属。
通过关闭或改变气道通路的大小,就能使锤头得到连打、单打、上悬和下压等不同的动作。
(二)蒸汽-空气锤
蒸汽-空气锤是利用蒸汽或压缩空气带动锤头工作的,常用的双柱拱式蒸汽锤的构造如图3所示。
其主要组成部分有工作汽缸1,落下部分2(活塞、锤杆、锤头和上抵铁),带导轨的左右机架3,带下抵铁的砧座4和操纵手柄5等。
蒸汽-空气锤的工作原理如图3左上方局部放大图所示,当滑阀6在图示位置时,沿进气管7的新蒸汽进入滑阀汽缸8,并从滑阀的外面绕过而进入工作汽缸活塞9的上部空间,使活塞9,锤杆10和锤头向下运动进行锤击。
这时原先在工作汽缸1下部空间的废汽则进入滑阀汽缸并通过滑阀中间的孔,顺着排气管11排出。
当滑阀6移至下在位置时,则新蒸汽进入工作汽缸活塞的下部空间,并给予活塞压力,使锤头上升。
先前进入工作汽缸上部的废汽就直接经排气管11排出。
蒸汽-空气锤用4~9×101325Pa的蒸汽或压缩空气来推动活塞,使之以6~8m/s的速度向下运动。
故落下部分能量可显著增大,锤击功能可大为提高。
但必须有一套辅助设备,如蒸汽锅炉或空气压缩机等,但此空气锤复杂。
蒸汽-空气锤的吨位一般为0.5~5t。
3t以下常见的是悬臂式机架,而5t锤则通常是桥式结构。
蒸汽-空气锤适合锻造中型或较大的锻件。
(三)水压机
1.水压机的工作原理
水压的工作原理是根据帕斯卡液体静压定律而来的。
即:
加在密封容器内的液体的压强(单位面积上的压力)能够按照它原来的大小向液体各个方向传递。
根据这一原理,如图4所示,在连通的容器中的柱塞D<sub>1<sub>和D<sub>2<sub>所受到的压力和它们的端面面积成正比。
因此在小柱塞上作用一个小的力P<sub>1<sub>,则大柱塞上就产生一个增大的力P<sub>2<sub>。
这力所增大的倍数,就等于大柱塞端面面积比小柱塞端面面积所增大的倍数,这一关系可以用以下方程式来表示:
(1)
或
(2)
式中P<sub>1<sub>、F<sub>1<sub>、D<sub>1<sub>——作用在小柱塞上的力以及小柱塞的横截面积和直径。
P<sub>2<sub>、F<sub>2<sub>、D<sub>2<sub>——大柱塞所产生的力以及大柱塞的横截面积和直径。
水压机就是根据这个原理制造的。
图5可以形象地说明水压机的工作原理:
泵室2和水压机工作缸4通过管道3连接成密闭的连通容器。
当水泵起动后,作用在水泵柱塞1(相当于小柱塞)上的力P<sub>1<sub>,通过管道3在工作柱塞5(相当于大柱塞),产生出增大了的力P<sub>2<sub>,再借助于上砧6,将其压力作用在置于下砧8的坯料7上,使之变形。
图5(略)水压机的工作原理
1―水泵柱塞2―泵室3―管道4―水压机的工作缸5―工作柱塞6―上砧7―坯料8―下砧
2.水压机本体的构造和工作过程
水压机的构造如图6所示。
工作时高压水(200×101325Pa左右)沿管13进入安装在上横梁3上的工作缸1内,并压
在柱塞2上使其下降。
这时与柱塞固定在一起的活动横梁4也沿着立柱5随同下降。
活动横梁的下端装有上抵铁11,下降时便对置于下抵铁12上的锻件施加压力。
下抵铁固定在下横梁6上。
图6(略)水压机
1―工作缸2―柱塞3―上横梁4―活动横梁5―立柱6―下横梁7―回程缸8―小柱塞9―小横梁10―拉杆11―上抵铁12―下抵铁13、14―高压水管
活动横梁的回升由回程缸7来完成,这时工作缸排水,而高压水沿管14进入回程缸7,并推动小柱塞8使其上升。
同时通过小横梁9,拉杆10带动活动横梁也随着上升,这样就完成了水压机的一个工作过程。
因此,通过对操纵手柄的控制,就可以使水压机得到预压、施压、回程(提升)、上悬(停止)等四种动作。
各种形式的自由锻水压机的结构主要构成部分都大致如此,其工作过程则是完全一致的。
所不同的是,一些主要构件(如机架、工作缸和回程缸等)的结构、位置和数量上有所差异。
例如:
机架有四柱式、双柱式、也有单臂式;工作缸有单缸、双缸、三缸和多缸之分。
3.水压机的工作特点和用途
水压机的优点在于它以压力(上抵铁速度约0.1~0.3m/s)代替锻锤的冲击力(锤头速度可达6~8m/s,从而避免了对地基及建筑物的震动,而且工作条件较好和安全。
其次,金属在水压机上比在锤上锻造容易达到较大的锻透深度,可获得整个截面是细晶粒组织的锻件。
水压机的缺点是设备庞大,并需一套供水系统和操纵系统,造价较高。
水压机的吨位一般常用的是500~50000t。
水压机主要用于自由锻造(横锻水压机与自由锻水压机在结构上稍有不同,但工作原理则完全一致)。
它是锻制大型锻件的基本设备,代替了5t以上的锻锤。
三、模锻常用设备
(一)蒸汽-空气模锻锤
蒸汽-空气模锻是普遍使用的一种模锻设备。
它的工作原理和蒸汽-空气自由锻锤基本相似。
结构上的主要区别是:
模锻锤的锤身是直接安放在砧座上的,用带弹簧的螺栓来固定。
调整锻模时,锤身可沿砧座平移,锤身装有长而可调节的导轨,锤的砧座较重(是落下部分重量的20~25倍)。
这些都为了保证模锻锤工作时,上下模尽可能减小错移,以提高模锻件的精度。
上下模用斜楔和键块分别紧固在锤头和模座上。
模锻锤一般都由模锻工通过脚踏板直接操纵,不需要司锤工。
蒸汽-空气锤的工作过程是:
锤头上下摇动(代替自由锻锤的悬空)、单次锻击、调节的连续锻击,其操纵机构如图7所示。
1.锤头上下摇动
此时锤头仅在导轨的上部作上下往复运动,上升时达到最高位置,下降时上锻模并不接触下锻模,而是形成高度为200~500mm的下行程不足量,这个量随锻锤的尺寸而定。
这时脚踏板1处在自由状态,手柄2放在下部位置,节气阀8稍微打开,蒸汽经滑阀15和下气道20进入活塞14的下面,推动活塞和锤头18一起上升,这时锤头的斜面压迫马刀形杠杆长臂17,使滑阀向上,蒸汽又经上汽道21进入活塞的上面,使锤面向下。
这时马刀形杠杆长臂不再受压,滑阀由于自重作用而下降,蒸汽又改由下气道进入活塞的下在,使锤头向上。
如此重复,便产生锤头的上下摇动。
此时便可在锻模中移动锻件,并短时间地等待加热坯料。
采用摇动循环的目的是为了增加打击次数和提高打击能量。
2.单次锻击
单次锻击是在锤头上下摇动的基础上进行的。
当锤头上升到近于行程上顶点时,踩下脚踏板,使节气阀完全打开,并使滑阀向上,蒸汽通过上汽道进入活塞的上面,锤头便向下打击。
根据脚踏板压下高度的不同,就能得到不同力量的打击。
假如在打击后继续压住脚踏板,那么锤头将保持不动;当松开脚踏板时,锤头又进行上下摇动。
3.调节的连续锻击
连续锻击不能自动进行。
必须不断地调节操纵机构,即松开脚踏板,在锤头上升到近于行程上顶点时,马上再踩下脚踏板,这样连续地踩下和松开脚踏板,使两次锻击之间不插入上下摇动循环,使得到调节的连续锻击。
蒸汽-空气模锻锤的能力也以落下部分的重量(质量)来表示,有0.5~30t,国内常用的是1~16t。
(二)摩擦压力机
摩擦压力机是习惯叫法。
按其作用力的性质。
它应该是属于锻锤一类设备。
因为,象锤一样,摩擦压力机的滑块(相当于锤点)靠向下运动的速度取得动能,然后转换成打击的能量,摩擦压力机的打击能量是以行程终了所产生的压力来表示的。
螺母2固定在机架上(图中未画出),螺杆1通过螺母2可以作上下传动。
螺杆上端固定着飞轮3,下端用轴承与滑块7相连。
主轴9上装有一对摩擦盘,由电动机带动主轴与摩擦盘一起旋转。
用操纵杆可使主轴沿轴向作一些移动,这样就可使这一个或另一个摩擦盘与飞轮的边缘靠紧产生摩擦力而带动飞轮旋转,螺杆也随飞轮作不同方向的转动,滑块则随之进行上下运动。
摩擦压力机上的模锻主要是靠飞轮,螺杆及滑块向下运动时所积蓄的能量来实现的。
常用摩擦压力机的吨位为160~1000t。
(三)曲柄热模锻压力
曲柄热模锻压力机是一种比较先进的模锻设备,常用于大批大量生产的流水线中。
1―滑块2―连杆3―曲轴4―制动器5―离合器6―人字齿轮7―小齿轮8―传动轴9―飞轮10―皮带轮11―电动机12―工作台
由电动机11经皮带轮10,9的传动来带动中间传动轴8,经齿轮7,6和离合器5带动曲轴-连杆(3-2)机构,推动滑块,沿导轨作业上下直线运动。
大齿轮6在主轴(曲轴)3上可以自由转动,它们之间可以通过摩擦离合器5的作用连成一体;制动器4用来使用曲轴停止转动并防止在离合器脱开后滑块的自由滑行。
工作台12可以利用斜楔来调节高低。
热模锻压力机有三个工作过程:
1.单头全冲程
按下按钮(或脚踏板)后,滑块由上死点经下死点再回到上死点。
进行第二次行程时动作再重复一次。
2.自动全冲程
按下按钮(或脚踏板)后,滑块即连续地重复单次全冲程,直到松开按钮(或脚踏板)为上,此时滑块又回到上死点位置。
3.寸动(调整)冲程
按下按钮(或脚踏板),滑块即在导轨中作短距离的移动,行程的大小视按下时间的久暂而定(用于模具的调整)。
(四)平锻机
平锻机的主要结构与曲柄压力机相同。
只因滑块是作水平方向运动,故称平锻机。
图10为目前常采用的平锻机传动简图。
电动机2通过皮带3将运动传给皮带轮1,皮带轮带有离合器5并装在传动轴4上,传动轴的另一端有齿轮6,可将运动传至曲轴7上。
曲轴通过连杆与主滑块8相连,另外通过一对凸轮10与副滑块相连,后者通过连杆系统11与活动模12相连。
1―皮带轮2―电动机3―皮带4―传动轴5―离合器6―齿轮7―曲轴8―主滑块9―凸模10―凸轮11―杠杆12―副滑块和活动模13―固定模14―挡料板15―坯料
运动传至曲轴后,随着曲轴的转动,主滑块8带着凸模9做前后往复运动。
同时凸轮10运动使副滑块前后运动并驱使活塞模12左右运动。
挡料板14通过辊子与主滑块上的轨道相连,当主滑块向前运动(工作前程)时,轨道斜面迫使辊子上升,并使档料板绕其轴线转动,挡料板的末端便移至一边,给凸模让出路来。
根据固定模和活动模分模面所呈的位置,平锻机有水平分模和垂直分模两种。
图9所示为垂直分模的平锻机。
平锻机的吨位以凸模最大压力来表示,一般是50~350t。
可加工φ=25~230mm的棒料。
以上我们介绍了自由锻和模锻共七种设备(即空气锤、蒸汽-空气自由锻、水压机、蒸汽-空气模锻锤、摩擦压力机、曲柄热模锻压力机和平锻机),就它们的结构原理和工作特点作了简要说明。
这几种设备在国内锻压生产中是使用得最普遍的。
因此,也是我们从事安全技术工作所必须熟悉的。
其实锻压充备种类繁多,型号、规格复杂,而特种锻造设备更是不胜枚举。
限于篇幅,不能一一介绍。
重要的是,我们应该举一反三,通过比较,从各种锻压设备的共性中,找出它们之间安全技术工作应该共同关心的问题来。
四、使用锻锤和水压机的安全技术
(一)使用锻锤的安全技术
在使用空气锤和蒸汽-空气自由锻锤时,常见的工伤事故,可归纳如下:
1.下料时发生的事故
首先是材料在切割时飞出伤人。
产生的原因主要是毛坯放置的位置不当,或者由于打击轻重不适宜。
其次是在切较长的料时,锻工用手拿着毛坯的一端,由于放得不平持击时引起震动,而将锻工的手腕震伤。
有时司锤工或锻工没有配合好,在锻工未钳牢工件前司锤工即把锤头提起,使切好的毛坯从砧面上掉下来,打伤锻工。
另外是剁刀没有垂直地放在坯料上,在锤击时向一旁滑射出去而伤及周围的人。
2.拔长时发生的事故
坯料拔长,由于金属变形流动的特点,很难避免其轴向弯曲(坯料从端部送进,拔长时,总是沿轴向向上翘),这样给继续送进带来了困难,在锻打中,一不小心,就容易把手震伤。
3.镦粗时发生事故
坯料镦粗时,随着坯料截面积的迅速增大并呈鼓形,使钳子不容易钳住。
尤其在镦粗后进行滚圆时,工作易滑落,造成工伤事故。
4.冲孔时发生的事故
冲孔时,为了便于冲头从冲孔坯料中取出,常在坯料预冲的盲孔里放上一点煤屑,冲孔过程中即借助于煤屑在红热的坯料中燃烧产生的煤气把冲头爆出。
冲头的突然爆出和未燃尽的煤屑飞溅会伤及周围的工人。
5.弯曲时发生的事故
在锤上用胎模弯曲时,需持别小心,因为锻锤的动作不容易控制得很平稳。
往往使变形速度很快,这时司机和掌钳工要是没配合好的话,锻工很可能被弯曲零件碰伤。
6.崩伤
加热好金属的表面总有一层氧化铁皮,在锻造过程中,这些氧化铁皮一面不断地剥落,同时不断产生新的氧化铁皮。
氧化铁皮即轻又硬,因此在锤击时容易飞出伤人。
曾发生过崩瞎工人眼睛的严重事故。
7.使用胎模时发生的事故
锻工车间的产品或工具常处在高温状态下,有时看上去是黑色,但实际上温度可能达到几XX,如用手去摸就会造成烫伤事故。
没有经过预热的胎模由于受热不均,在锻造过程中容易发生破裂现象。
这时破裂的胎模碎块,很可能飞出伤人。
8.操作姿势不正确引起的事故
有些工人在锻造时把钳子低住肚子,由于在锤击时产生的水平分力,可能会把肚子碰伤,造成重伤。
9.工具选择不当
如钳口不适于所钳的锻件,在锻造过程中发生脱落现象,而夹伤手指或震伤手腕。
10.锤杆断裂
锤杆容易损伤,对3t以下的锻锤,锤杆往往是锤杆与锤头连续的地方损坏。
由于事先不容易发现锤杆
是否已产生裂纹,所以无法避免它的突然断裂。
锤杆断理解的根本原因是偏心锻造,即锻件没有放在砧子的中心而进行锻造造成的。
针对以上情况,应该采取以下技术安全措施:
1.在下料时应在被切毛坯可能飞出的方向加防护挡板,而在防护挡板之内不准有人。
当切割的毛坯短小时,最好在胎模中进行(如图11)这样也可以防止毛坯在切割时飞出伤人。
为了防止切割长料时把手震伤,可以采用带弹簧的小车(如图12),这种小车可以在临时铺设的轻便铁轨上前后移动,工人在操作时不必用手直接把住毛坯的一端,只要推动小车就行了。
当然,如果锻锤上配备有操作机或吊车就更方便了。
不过要注意,被切的坯料一定要在砧面上放平,才能进行切料。
剁刀的刀口必须保持平直,不许有翻卷现象,否则,切料时翻卷部分会变成碎片飞出伤人。
不在胎模中切料时,最后几下要特别小心,力量用得过猛,也容易使毛坯飞出伤人。
下料时要使剁刀垂直对准切口,如剁刀放置歪斜或没有对准切口,都可能因此震伤或打伤工人,或损坏设备。
2.为了使拔长时毛坯不致产生严重的轴向弯曲现象,上下砧面的宽度应该保持一致,并在拔长过程中随时注意校直。
更重要的是,在逆进过程中,要随时注意把坯料摆平在砧面上,以免震伤操作者的手腕,或震坏操作机及操作工具。
3.为了防止镦粗时,抱钳钳不紧锻件,最好在抱钳钳柄上装一链子,这样在起员时可以用起重的力量把锻件夹紧。
4.为了使冲头容易从冲孔中取出,冲孔前可以冲孔的位置上放一些煤屑,但锤击二三下后,应立即把冲头取出,以便放走煤屑燃烧时产生的气体。
使用细长冲头时,必须仔细检果有无裂纹,以免在锤击时突然折断。
5.弯曲件的变形相当大,所以在锻锤上进行弯曲是不够安全的,最好采用专用的弯曲压机。
对不得不在锤上弯曲的锻件,要借助于胎模装置,操作机或锻造行车的协调配合。
6.为了防止氧化铁皮崩山伤人,一方面工人在操作时应该穿戴好工作服和防护用具;另一方面必须随时清除掉落在砧面上的氧化铁皮。
清除的方法,可以采用压缩空气喷嘴,既可以固定在锻锤上的某个位置,也可以由工人用手拿着进行吹扫。
7.在使用胎模时,千万不要手去搬胎模,因为胎模带有几XX的高温、容易把手烫伤,为了使胎模便于搬运,必须在模上装置手把。
胎模在使用前,应预热到100~200℃,以免局部骤然受热时,因膨胀不均而破裂。
锻造中,如必须把上下胎模合起来时,应在胎模上设置定位或导向装置,以免锤击时滑落。
8.在操作中,锻工应保持正确的姿势,通常钳子应放在身子的左面,右手在前,左手在后。
下砧面离地面高度最好在700mm左右,这时锻工在观察锻件变形时比较方便。
过低的砧面往往使锻工不得不把锻件的一端抬起来。
这样很容易由于一时的疏忽而把锻件打飞,震伤手臂。
9.选择适当的钳子是保证把锻件夹紧的主要措施之一。
自由锻的每个生产班组应具有一套各种基本外形的钳子和工具胎模。
10.锤杆断裂主要原因是偏心锻造,另外由于锤杆和锤头接触不良,因而使打击力集中在锤杆和锤头接触的地方,这样也会加速锤杆的断裂。
为了改善锤杆3(见图13)和锤头4的接触面,锤杆的下端有1:
25~1:
12的锥度,插入锤头中的钢套5和铜套6中,因为铜的硬度较小,所以在几次打击后便把锤杆和锤头间的空隙满了。
锤头的下部开有燕尾槽和键槽,用钭楔和键块将上砧固定在锤头上。
锻锤在使用过程中,必须注意保护不受突然事故的损坏。
除了上面说到的,采取措施防止锤杆断裂外,同时,必须防止因操作不慎损坏了活塞和气缸。
活塞向下运动的最低点是当上砧空击碰到下砧的时候,这时的活塞9(见图3)或1(见图13)不能把工作气缸的下部进气通道封死,或更有甚者,出现活塞底面与工作气缸的底部相互打坏。
为此,必须通过控制上、下砧的高度来保证不致发生这种情况。
即应规定出上下砧的最小总高来保证当活塞处于最低位置时的正常状态。
这点是需要设备管理人员高度重视的。
为了保证工作气缸顶部不至因为活塞冲顶而损坏,应该在锻锤工作气缸的上方装上缓冲器。
常用的弹簧式缓冲器和空气式缓冲器两种形式。
图14所示为弹簧式缓冲器,在气缸上端装有反击中心杆的活塞向上碰到弹簧的中心杆,弹簧开始压缩而发生缓冲作用。
空气式缓冲器的构造如图15所示。
其工作原理是:
通常缓冲器活塞2位于缓冲器气缸1的下部,当工作活塞冲顶时,缓冲气缸中的空气即被压缩,部分空气可能从缝隙中跑出来;当工作活塞下落时,由于缓冲器活塞2本身的重量和原来空气被压缩后的压缩力,使缓冲活塞2下降到原来的位置,这时不足的空气从气孔4中进入缓冲器气缸1中。
(二)使用水压机的安全技术
水压机传递能量的工作介质是高压液体。
工作中机架需要承受很高的压力,而且所锻造的锻件多为大件,设备长期处在高温的烘烤下,加上这种设备和装置造价昂贵,这在设备的使用维修和安全生产方面向操作者提出了特殊的要求。
1.对水压机的使用和维修的要求
(1)全部水压装置都应置于温度为0℃以上的车间内,若车间温度有可能低于0℃时,应把水压装置中的水全部放出去。
在冬天,水压装置暂停工作时,必须对缸体和导管保暖,防冷防冻。
(2)水压装置中所用的工作介质应该选用乳化水,以防管道、缸体等生锈或形成沉垢。
安全管理文书
整理范文,仅供参考!
日期:
__________________
单位:
__________________