轴承端盖冲压模具的方案设计书Word下载.docx
《轴承端盖冲压模具的方案设计书Word下载.docx》由会员分享,可在线阅读,更多相关《轴承端盖冲压模具的方案设计书Word下载.docx(20页珍藏版)》请在冰豆网上搜索。
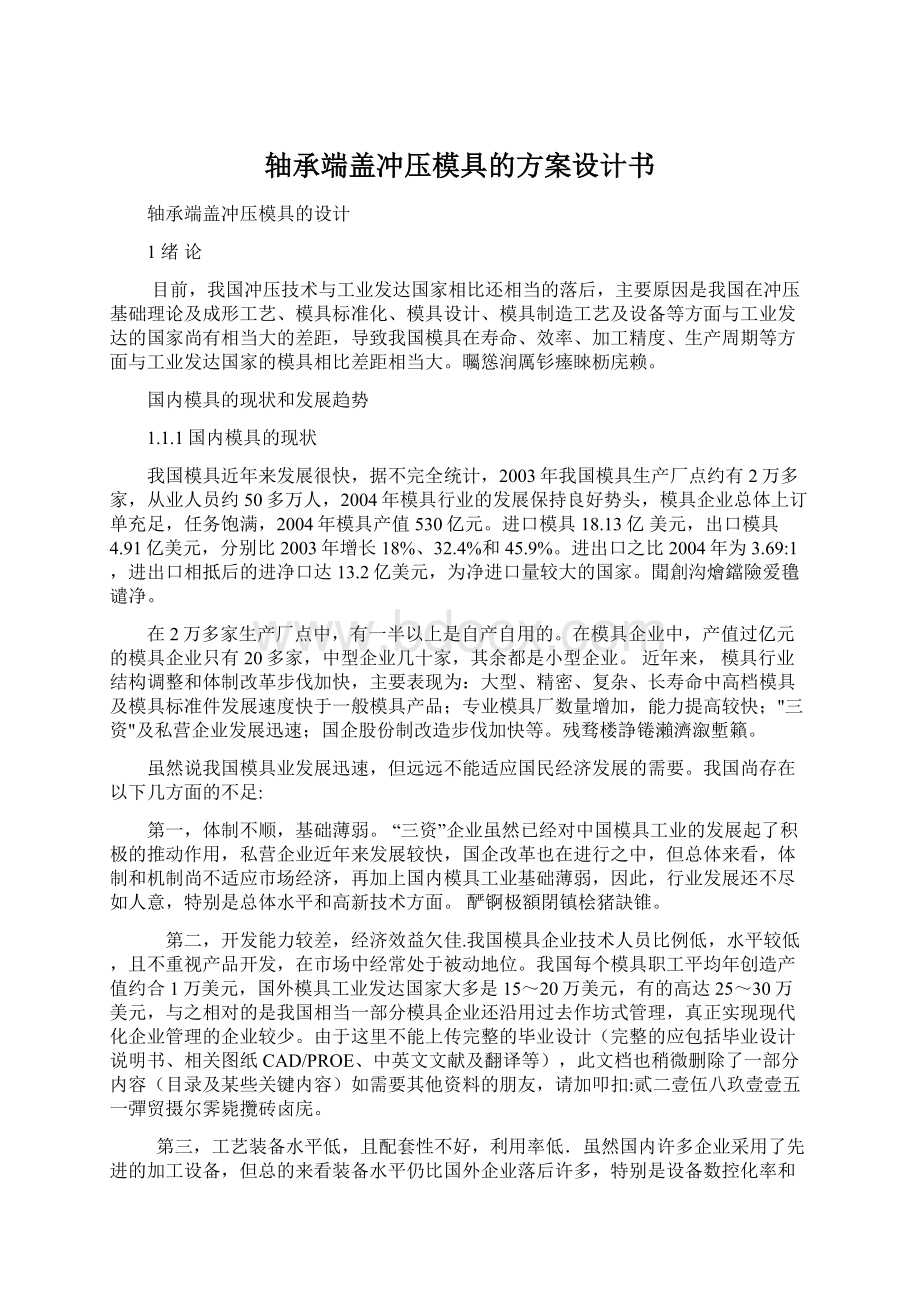
第四,专业化、标准化、商品化的程度低、协作差.由于长期以来受“大而全”“小而全”影响,许多模具企业观念落后,模具企业专业化生产水平低,专业化分工不细,商品化程度也低。
目前国内每年生产的模具,商品模具只占45%左右,其馀为自产自用。
模具企业之间协作不好,难以完成较大规模的模具成套任务,与国际水平相比要落后许多。
模具标准化水平低,标准件使用覆盖率低也对模具质量、成本有较大影响,对模具制造周期影响尤甚。
厦礴恳蹒骈時盡继價骚。
第五,模具材料及模具相关技术落后.模具材料性能、质量和品种往往会影响模具质量、寿命及成本,国产模具钢与国外进口钢相比,无论是质量还是品种规格,都有较大差距。
塑料、板材、设备等性能差,也直接影响模具水平的提高。
茕桢广鳓鯡选块网羈泪。
1.1.2 国内模具的发展趋势
巨大的市场需求将推动中国模具的工业调整发展。
虽然我国的模具工业和技术在过去的十多年得到了快速发展,但与国外工业发达国家相比仍存在较大差距,尚不能完全满足国民经济高速发展的需求。
未来的十年,中国模具工业和技术的主要发展方向包括以下几方面:
鹅娅尽損鹌惨歷茏鴛賴。
1)模具日趋大型化;
2)在模具设计制造中广泛应用CAD/CAE/CAM技术;
3)模具扫描及数字化系统;
4)在塑料模具中推广应用热流道技术、气辅注射成型和高压注射成型技术;
5)提高模具标准化水平和模具标准件的使用率;
6)发展优质模具材料和先进的表面处理技术;
7)模具的精度将越来越高;
8)模具研磨抛光将自动化、智能化;
9)研究和应用模具的高速测量技术与逆向工程;
10)开发新的成形工艺和模具。
1.2 国外模具的现状和发展趋势
模具是工业生产关键的工艺装备,在电子、建材、汽车、电机、电器、仪器仪表、家电和通讯器材等产品中,60%-80%的零部件都要依靠模具成型。
用模具生产制作表现出的高效率、低成本、高精度、高一致性和清洁环保的特性,是其他加工制造方法所无法替代的。
模具生产技术水平的高低,已成为衡量一个国家制造业水平高低的重要标志,并在很大程度上决定着产品的质量、效益和新产品的开发能力。
近几年,全球模具市场呈现供不应求的局面,世界模具市场年交易总额为600~650亿美元左右。
美国、日本、法国、瑞士等国家年出口模具量约占本国模具年总产值的三分之一。
籟丛妈羥为贍偾蛏练淨。
国外模具总量中,大型、精密、复杂、长寿命模具的比例占到50%以上;
国外模具企业的组织形式是"
大而专"
、"
大而精"
。
2004年中国模协在德国访问时,从德国工、模具行业组织--德国机械制造商联合会(VDMA)工模具协会了解到,德国有模具企业约5000家。
2003年德国模具产值达48亿欧元。
其中(VDMA)会员模具企业有90家,这90家骨干模具企业的产值就占德国模具产值的90%,可见其规模效益。
預頌圣鉉儐歲龈讶骅籴。
随着时代的进步和技术的发展,国外的一些掌握和能运用新技术的人才如模具结构设计、模具工艺设计、高级钳工及企业管理人才,他们的技术水平比较高.故人均产值也较高.我国每个职工平均每年创造模具产值约合1万美元左右,而国外模具工业发达国家大多15~20万美元,有的达到25~30万美元。
渗釤呛俨匀谔鱉调硯錦。
国外先进国家模具标准件使用覆盖率达70%以上,而我国才达到45%.
1.3 拉深模具设计与制造方面
1.3.1拉深模具设计的设计思路
拉深是冲压基本工序之一,它是利用拉深模在压力机作用下,将平板坯料或空心工序件制成开口空心零件的加工方法。
它不仅可以加工旋转体零件,还可以加工盒形零件及其他形状复杂的薄壁零件,但是,加工出来的制件的精度都很底。
一般情况下,拉深件的尺寸精度应在IT13级以下,不宜高于IT11级。
铙誅卧泻噦圣骋贶頂廡。
只有加强拉深变形基础理论的研究,才能提供更加准确、实用、方便的计算方法,才能正确地确定拉深工艺参数和模具工作部分的几何形状与尺寸,解决拉深变形中出现的各种实际问题,从而,进一步提高制件质量。
擁締凤袜备訊顎轮烂蔷。
圆筒件是最典型的拉深件,其工作过程很简单就一个拉深,为了保证制件的顺利加工和顺利取件,模具必须有足够高度。
要改变模具的高度,只有从改变导柱和导套的高度。
导柱和导套的高度可根据拉深凸模与拉深凹模工作配合长度决定.设计时可能高度出现误差,应当边试冲边修改高度。
贓熱俣阃歲匱阊邺镓騷。
1.3.2深圆筒拉深模具设计的进度
1.了解目前国内外冲压模具的发展现状,所用时间20天;
2.确定加工方案,所用时间5天;
3.模具的设计,所用时间30天;
4.模具的调试.所用时间5天.
2转子轴承盖冲压工艺的分析
2.1拉深件工艺分析
原始资料:
如图所示
材料:
08
厚度:
2mm
此工件为带有凸缘圆筒形工件,而且拉深的结构是台阶形状的结构,拉深的筒臂有一定的倾斜角度是45°
在拉深件的底部有一个直径13的孔,在零件的外形上有两个耳朵,并且耳朵上有两个直径4的孔,要求有一定的外形尺寸要求,没有厚度不变的要求。
此工件的拉深部分形状满足拉深的工艺要求,可采用拉深工序加工。
而对于零件孔与外形结构和材料的性质都满足冲裁工艺的要求,所以零件的空结构与外形结构分别采用冲孔与落料的冲压工序完成。
由于本零件需要经过拉深,冲孔落料工序方可成形。
首先应当对此零件进行冲裁和拉深的工艺性分析,冲裁工艺性是指冲裁件对冲裁工艺的适应性,所谓冲裁工艺性好是指能用普通的冲裁方法,在模具寿命和生产率较高,成本较低的条件下得到质量合格的冲裁件。
因此,冲裁件的结构形状,尺寸大小,精度等级,材料及厚度应当符合冲裁工艺性要求。
冲裁件的结构工艺性要求是冲裁件的形状应力求简单,对称,有利于材料的合理利用。
冲裁件的内形及外形的转角处要尽量避免尖角,应当用圆弧过渡,同时也应当尽量避免冲裁件上有过长的凸出悬臂和凹槽,如果有的话悬臂和凹槽的宽度也不宜过小,另外为了避免工件变形和保证模具的强度,孔边距和孔间距不能过小。
在拉深件上冲孔时,孔边与直壁之间应保持一定的距离,以避免冲孔时凸模受水平推力而折断,冲孔时因受凸模强度的限制,孔的尺寸不应太小,否则凸模易折断或压弯。
d≥1.5t。
冲裁件的尺寸精度和表面粗糙度也有一定的要求,一般冲裁件的精度可以分为精密精度和经济精度。
精密级是指冲压工艺在技术上所允许的最高精度,而经济精度是指模具达到最大许可磨损时,其所完成的冲压加工在技术上可以实现而在经济上又最合理的精度,既是所谓经济精度。
为了降低冲压成本,获得最佳的技术经济效果,在不影响冲裁件的使用要求的前提下,应尽量采用经济精度。
在实际生产中冲裁件的经济精度等级不高于IT11级。
冲裁件的基准应尽可能与其冲压时定位基准重合。
拉深件的工艺性要求拉深件的尺寸精度应在IT13级以下,不宜高于IT11级。
另外拉深件的形状应尽量简单对称,尽可能一次拉深成形。
需多次拉深的零件,在保证必要的表面质量前提下,应当允许内,外表面存在拉深过程中可能产生的痕迹,在保证装配的要求的前提下,应允许拉深件侧壁有一定的斜度,拉深件的底或凸缘上的孔边到侧壁的距离应满足:
a≥R+0.5t,拉深件的底与壁,凸缘与壁,矩形件四角的圆角半径应满足:
rd≥t,R≥2t,r≥3t。
否则应增加整形工序。
拉深件的尺寸标注,应注明保证外形尺寸还是内形尺寸,不能同时标注内外形尺寸。
带台阶的拉深件,其高度方向的尺寸标注一般应以低部为基准,若以上部为基准,高度尺寸不易保证。
坛摶乡囂忏蒌鍥铃氈淚。
此零件精度要求一般,没有配合要求,材料为08此材料使用普遍容易在市场上购得,也满足冲压工艺性要求,有上分析知道此零件结构对称简单,结构满足冲压工艺性要求,也满足拉深工艺性要求,工件底部圆角半径R1,由于没有公差等级标注,所以可以按未标公差等级处理。
满足拉深工序对工件公差等级的要求。
蜡變黲癟報伥铉锚鈰赘。
2.2拉深和冲压工艺计算和工艺方案
拉深件的工艺计算是拉深工艺设计中的一个环节,本制件的工艺计算属于简单
的。
其主要的内容包括计算毛坯直径、决定拉深次数及确定工序件的尺寸等。
为了避免设计拉深模时出现尺寸错误,可以画出圆筒形拉深件的工序图。
買鲷鴯譖昙膚遙闫撷凄。
2.2.1冲压和拉深工艺方案的确定
根据制件的工艺分析,知道制件是个简单的圆筒形拉深件。
所以它的工序有一个:
拉深。
同时此工件有有三个孔,因此,本制件的工艺方案就是:
拉深再冲孔和落料三个基本的工序。
可以有以下三个工艺方案:
綾镝鯛駕櫬鹕踪韦辚糴。
方案一:
先拉深,后冲孔最后落料。
采用单工序模生产。
方案二:
拉深—冲孔—落料复合冲压。
采用复合模生产。
方案三:
拉深—冲孔—落料级进进行冲压。
采用级进模生产。
方案一模具结构简单,但是需要三道工序三副模具,成本高而生产效率低,难以满足批量生产和低成本生产。
方案而只需一副模具,工件的精度及生产效率都较高但是工件的最小壁厚1.9mm小于凸,凹模许用最小壁厚3.2mm,模具强度较差,制造难度大,并且冲压后成品留在模具上,在清理,模具上的物料时会影响冲压速度,操作不方便。
方案三:
也只需要一副模具生产效率高,操作方便,工件精度也能满足要求。
通过对上述三种方案的分析比较,该工件的冲压生产采用方案三为佳。
驅踬髏彦浃绥譎饴憂锦。
2.2.2计算毛坯尺寸
根据表面积相等原则,用解读法求该零件的拉深部分毛坯直径D。
可按下面的公式计算:
A=∏r×
r=3.14×
[(4.2×
0.412)+27.5]×
0.412)+27.5]
A=2682.87mm
A—拉深毛坯的面积
2.2.3确定是否用压边圈
为了解决拉深过程中的起皱问题,在实际生产中的主要方法是在模具结构上采用压料装置。
常用的压料装置分为刚性压料装置和弹性压料装置两种。
是否采用压料装置看是否在拉深过程中可能放生起皱。
实际生产中可以通过查表来判断拉深过程中是否会起皱和采用压料装置。
通过相对厚度的判断,查《冲压模具设计与制造》高等教育出版社刘建超张宝忠编表4.4.4得第一次拉深(t/D)×
100>2的可以不用压料装置,2/[(4.2×
0.412)×
2+20]=2/23.46=8.52mm远远的大于2mm所以不需要采用压边圈。
猫虿驢绘燈鮒诛髅貺庑。
2.2.4拉深次数的确定
拉深系数m=d/D=[(39+7.4+39)/2]/[46.4+(4.2×
0.412+2)]
=0.863
采用查表法。
根据和工件相对高度,查《冲压模具设计与制造》高等教育出版社刘建超张宝忠编表4.4.2得第一次极限拉深系数0.5。
由于0.863>0.5可以一次拉深成形。
锹籁饗迳琐筆襖鸥娅薔。
拉深相对厚度t/D=2/49.44=0.04
采用查表法。
根据和工件相对高度,查《冲压模具设计与制造》高等教育出版社刘建超张宝忠编表4.4.3得第一次拉深相对拉深高度0.94~0.77。
可以通过一次拉深成形。
所以通过上边的分析确定拉深部分可以通过一次拉深成形。
構氽頑黉碩饨荠龈话骛。
2.2.5冲压排样设计
冲压件在条料和带料或板料上的布置方法叫排样。
合理的排样是提高材料利用率和降低成本,保证冲压件质量及模具寿命的有效措施。
冲压所产生的废料可以分为两类:
一类是结构废料,是有冲压件的形状结构特点产生;
另一类是有冲压件之间和冲压件与条料侧边之间的搭边,以及料头,料尾和边余料而产生的工艺性废料。
要提高材料利用率,主要从减少工艺废料着手,可以通过设计合理的排样方案,选择合适的板料规格和合理的裁板法。
排样方法分为三种:
1有废料排样2少废料排样3无废料排样本零件由于考虑到其结构的特点采用单排斜排倾斜45°
为了提高零件精度和模具寿命,采用有废料排样,但是材料利用率低輒峄陽檉簖疖網儂號泶。
塔边的确定,排样时冲压件之间的以及冲压件与条料侧边之间留下的工艺性废料叫搭边。
搭边的作用一是补偿定位误差和剪板误差,确保冲出合格的零件;
二增加条料刚度,方便条料送进,提高劳动生产率;
同时,搭边还可以避免冲压时条料边缘的毛刺被拉入模具间隙,从而提高模具寿命。
通过查《冲压模具设计与制造》高等教育出版社刘建超张宝忠编表2.5.2最小搭边值工件到边a1=1.5mm,侧边a=1.8mm。
工件间a2=2。
通过分析计算条料的宽度取62mm,步距60mm。
条料排样图如图所示尧侧閆繭絳闕绚勵蜆贅。
材料的利用率,冲压件的实际面积与所用板料的面积之比的百分比叫材料的利用率,它是衡量合理利用材料的经济性指标。
一个步距内的利用率η为识饒鎂錕缢灩筧嚌俨淒。
η=A/Bs×
100%=70.08%
A—一个步距内冲压件的实际面积;
B—条料宽度62.06mm;
s—步距60mm;
2.2.6选取凸模与凹模的圆角半径
考虑到实际采用的拉深系数均接近其极限值,故首次拉深凹模圆角半径应大些,本零件只有一次拉深凹模圆角半径可按下公式计算;
凍鈹鋨劳臘锴痫婦胫籴。
rA1=0.8(D-d)t=1
rA1—凹模圆角半径;
D—坯料直径;
d—凹模内经;
t—板料厚度;
凸模圆角半径确定第一次拉深可取:
rT1=(0.7~1.0)rA1=1.0mm
2.2.7画出拉深工序图
画出各次拉深件的简图,便于设计各次拉深模,可避免设计拉深模时,将重要尺寸搞错。
如果拉深次数较少,也不用画出工序图。
由于本零件拉深次数少简图可以省去;
恥諤銪灭萦欢煬鞏鹜錦。
2.3压力、压力中心计算及压力机的选用
2.3.1冲压和拉深力的计算
由于不用压撩圈拉深所以拉深力
F=1.25∏(D-d1)tσb
=56.486σb
F—拉深力;
σb—拉深件材料的抗拉强度;
由于在实际生产中,深拉深所需要的拉深力较大些,所以在选取压力机的公称压力时,由于是浅拉深可按下面的公式计算:
鯊腎鑰诎褳鉀沩懼統庫。
Fg≥(1.6~1.8)2F=101.67σb
冲压力F=KLtTb
F—冲压力;
L—冲压周边长度;
t—材料的厚度
Tb—材料抗剪强度;
K—系数。
或F≈Ltσb
σb—材料08钢的抗拉强度。
F孔=134.4σb
F落料=373.8σb
F总=609.8σb
2.3.2压力中心确定
建立坐标系如图所示
Y0=0
X0=F1X1+F2X2+……+FNXN/(F1+F2+……+FN)=78.09mm
2.3.3压力机的选用
压力机的工作行程需要考虑工件的成形和方便取件,因此,工作行程
根据拉深力的计算结果和工件的高度,选择压力机:
J23-25
3模具的结构设计
3.1模具工作部分的计算
3.1.1拉深模的间隙
深间隙对拉深过程有较大的影响。
它不仅影响拉深件的质量与尺寸精度,而且影响拉深模的寿命以及拉深是否能够顺利进行。
因此,应该综合考虑各种影响因素,选取适当的拉深间隙值,既可保证工件的要求,又能使拉深顺利进行。
硕癘鄴颃诌攆檸攜驤蔹。
本模具的拉深间隙查表得出:
Z1/2=1.1t=1.1mm
3.1.2凸凹模工作部分的尺寸和公差
1.拉深凸.凹模尺寸及公差
由于工件底部尺寸φ20和φ39.R1均为过渡尺寸要求不高,为简单方便,直接按工件尺寸作拉深凸,凹模该处的尺寸。
阌擻輳嬪諫迁择楨秘騖。
d凸1=Φ20
d凸2=Φ19
d凸3=Φ39
mmd凸4=Φ46.2
0mm
dA1=Φ22.2
dA2=Φ31.2
mm
dA3=Φ31.2
mmdA4=Φ48.4
Z=2.1mm
2.冲孔凸,凹模尺寸及公差要求1.冲Φ4.20-0.1mm的孔查表2.3.3冲模初使双面间隙值Zmin=0.246mmZmax=0.36mm采用分别加工法.磨损系数取x=0.75.氬嚕躑竄贸恳彈瀘颔澩。
dT=(dmin+x×
△)0-δT=(Φ4.1+0.75×
0.1)0-δT=Φ4.175
mm
dA=(dT+Zmin)+δA0=Φ4.421
冲Φ13+0.20mm的孔
△)0-δT=(13+0.75×
0.2)0-δT=Φ13.15
dA=(dT+Zmin)+δA0=Φ13.396
δT+δA=0.74mm≤Zmax-Zmin=0.74mm
3.落料部分模具尺寸
DA=(Dmax-x×
△)+δA0=(Φ8-0.75×
0.1)=+0.0440=Φ7.925
DT=(DT-Zmin)0-δA=Φ13.396
△)+δA0=(52-0.75×
0.62)+δA0=Φ51.535
DT=(DT-Zmin)0-δA=Φ51.289
4孔心距Ld=L+1/8Δ=62±
1/8×
2=62±
0.25mm
3.1.4选用模架、确定闭合高度及总体尺寸
1.模具类型的选择
有冲压的工艺性分析知道本模具采用级进冲压,所以模具类型为级进模.
2.定位方式的选择
因为该模具采用的是条料,控制条料的送进方向采用导料板,无侧压装置.控制条料的送进步距采用初使挡料销,导正销精定距.而第一件的冲压位置因为条料有余量可以靠目测定距.釷鹆資贏車贖孙滅獅赘。
3.卸料出件方式的选择
因为工件料厚2mm相对较薄,卸料力也较小故,可以采用弹性卸料,因为是级进模采用下出件的方式比较便于操作与提高生产效率.怂阐譜鯪迳導嘯畫長凉。
4.导向方式的选择
为提高模具寿命和工件质量和精度,方便安装调试级进模采用中间导柱滑动导向方式.
5主要工作零件结构设计
凹模的外形选用板形的。
冲孔和落料部分的刃口选用平刃,此种刃口强度高,修模后刃口尺寸不变,为了便于卸料可以将谚辞調担鈧谄动禪泻類。
凹模厚度H=Kb=0.35×
70=25mm
壁厚C=(1.5~2)H=20mm
结构如图所示
凸模的结构形式及其固定方式
由于冲件的结构和尺寸不同,所以冲压模的凸模的加工以及装配工艺的实际条件也不同,所以在实际生产中使用的凸模结构方式也很多。
其截面形状有圆形和非圆形的。
本模具的凸模结构考虑到零件的结构与尺寸采用圆形的凸模,由于冲的孔的尺寸比较小所以为了增加模具的强度与刚度采用台阶式的截面形状为圆形的凸模,此种凸模装配修模方便,其工作部分的尺寸有计算而得,与凸模固定板配合的部分按过度配合(H7/m6)制造。
最大直径的作用是形成台肩,以便固定,保证工作时凸模不被拉出。
嘰觐詿缧铴嗫偽純铪锩。
A凸模长度计算
凸模长度尺寸应根据模具的具体结构,并考虑修模,固定与卸料板之间的距离,安装等的需要来确定。
当采用弹性卸料板时,其凸模长度按下式计算:
L=h1+h2+t+h=75
L—凸模的长度〔mm〕
h1—凸模固定板的厚度〔mm〕
h2—卸料板的厚度〔mm〕
t—材料的厚度〔mm〕
h—增加长度。
它包括凸模的修模量.凸模进入凹模的厚度〔0.5—1mm〕.凸模固定板与卸料板之间的安全距离等一般取10—20mm。
本模具的凸模取10mm。
熒绐譏钲鏌觶鷹緇機库。
3.2模具零件的结构设计
3.2.1拉深凹模
内、外形尺寸和厚度已由前面的计算确定;
拉深凹模需要有四个螺钉与下模座固定,还需要两个与下模座同时加工的销钉孔。
鶼渍螻偉阅劍鲰腎邏蘞。
3.2.2拉深凸模
拉深凸模的外形尺寸〔工作尺寸〕由前面的计算确定。
拉深凸模上一般开有出气孔,这样会使卸件容易些,否则凸模与工件由于真空状态而无法卸件。
查表,本凸模出气孔的直径为φ8mm纣忧蔣氳頑莶驅藥悯骛。
3.2.3卸料板
一般与卸料杆螺钉与橡胶联合使用,属于弹性卸件装置,靠橡胶的弹性势能把拉深工件卸下来。
图3-1卸料板
3.2.5导柱、导套
对于生产批量大、要求模具寿命高的模具,一般采用导柱、导套来保证上、下模的导向精度。
导柱、导套在模具中主要起导向作用。
导柱与导套之间采用间隙配合。
根据冲压工序性质、冲压的精度及材料厚度等的不同,其配合间隙也稍微不同。
因为本制件的厚度为2mm,所以采用H7/f7。
颖刍莖蛺饽亿顿裊赔泷。
导柱:
32×
300、35×
300;
导套:
115×
45、35×
50
3.3模具总装图
由以上设计,可得到模具的总装图,其工作过程是:
模具在工作时,将前一道工序拉深后所得的半成品坯件套在凹模槽。
凹模装在下模,凸模装在上模。
待凸模随上模下降时,首先卸料板将坯件压住,拉深凸模向下推,拉深凸模通过卸料板,而将坯料上端一部分材料压入凹模内,使坯件在凸、凹模作用下,产生塑性变形以后在经过冲孔凸模和落料凸模的作用下而制成所要求的零件。
濫驂膽閉驟羥闈詔寢賻。
当凹模随上模回升时,零件制品从落料孔