75000分段制造施Word下载.docx
《75000分段制造施Word下载.docx》由会员分享,可在线阅读,更多相关《75000分段制造施Word下载.docx(25页珍藏版)》请在冰豆网上搜索。
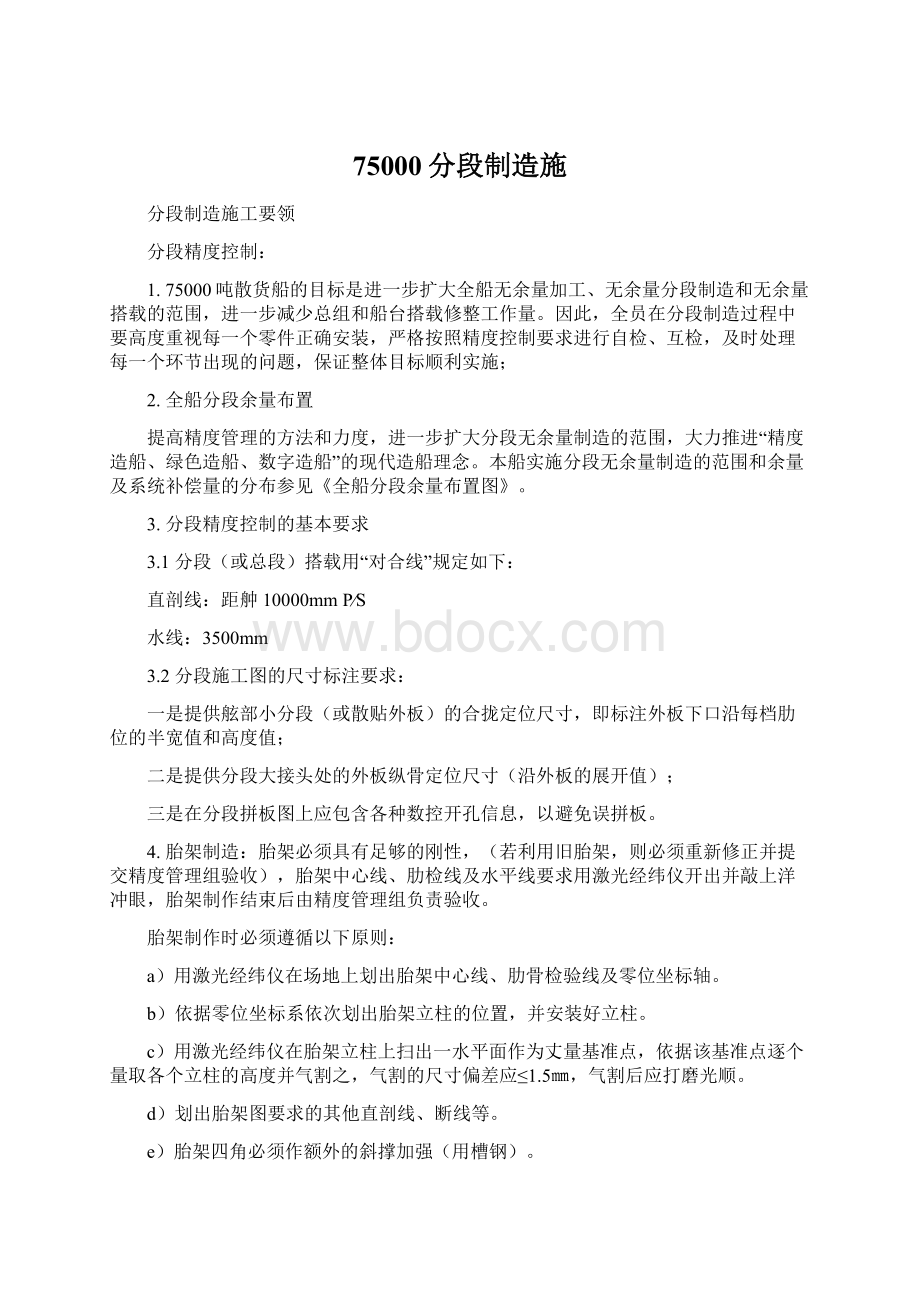
h)胎架完工后必须提交厂检验科验收。
i)胎架在使用的过程中意外被损坏,要求立即停止施工,对胎架进行修复后才能继续施工。
5.大拼板部件的精度控制
主要指一些外板、内壳板等在流水线上进行拼板及安装纵骨的安装作业。
a)原则上以零件两端的100㎜检验线作为拼板依据,同时必须检验周界尺寸、直线度、拼板对角线及周界的坡口朝向,装配结束后由精度管理组进行验收。
b)在拼板划线之前,必须对拼板进行平整度测量并矫正。
c)划线采用专用钢带划制,并由精度管理组负责对划线进行验收。
d)纵骨安装时采用专用工装件来保证其安装精度,尤其确保纵骨在正肋位处的垂直度,要求纵骨与安装位置线的偏差≤0.5㎜,纵骨安装的垂直度偏差≤0.5㎜。
e)用专用检验样尺对安装后的大拼板部件进行平整度检验,对超差部分进行矫正,直至符精度要求为止。
f)对大拼板部件进行必要的吊运加强,并用专用吊排起吊移位。
g)部件由内场运至外场时必须采用单件运输,不得多件叠堆在平板车上运输。
6.胎架散铺板的精度控制
胎架散铺板包括平面胎架铺板和曲面胎架铺板两种。
a)在平面胎架上铺板时,用挂锤线法使铺板的周界线与胎架上的位置线一一对应,对K行板定位时必须对准中心线,板与胎架保持密贴,不吻合度≤2.5㎜。
b)在曲面胎架上铺板时,除了满足上述要求外,还必须要求每列板的板缝位置与胎架上的相应位置线一一对应,确保板缝不错位。
c)铺板装配结束后,用专用工装器具对铺板进行固定来防止焊接变形。
d)铺板焊接结束后,用激光经纬仪(或挂锤线法)把胎架中心线、肋骨检验线等驳至铺板上,并在线的两端敲上洋冲眼,作为结构划线的基准线。
e)平面铺板的结构线划线采用专用钢带来划制;
曲面铺板的结构划线使用计量合格的钢圈尺来划制,线的宽度应≤0.5㎜。
f)划线作业结束后必须提交给精度管理组进行划线验收。
7.分段大组装阶段的精度控制
a)纵骨上胎架吊装定位必须对准位置线、垂直度偏差≤0.5㎜,用带水平仪的三角尺靠样检验。
b)肋板、纵桁板等部件的吊装定位须用水平尺或荡锤线的方法靠样检验。
c)肘板等小零件的安装必须注意安装节点的准确性。
d)舷侧小分段的吊装定位必须对每档肋位处的定位半宽、高度进行逐个测量,定位尺寸由设计所提供。
e)在片状小分段翻身上胎架合拢之前,由精度管理组对胎架面上的纵骨开档尺寸、垂直度进行逐个测量(仅测量与肋板相交处的纵骨开档尺寸及垂直度),再把测量数据与片段肋板上的对应纵骨开档相对照,对偏差大于2㎜的部位要求返修,使其满足片段吊装合拢的精度需要。
f)在首个分段制造时,要求对其“片状小分段”、“大拼板+纵骨”部件的焊接变形、焊接收缩量进行跟踪测量,记录测量数据,供后续分段制造时参考。
g)线型复杂、纵骨扭曲的分段,设计二所考虑在适当位置设置假隔舱。
8精度管理组对分段制造全过程实行精度监控,并对以下施工工序进行测量:
(测量记录存档)
8.1分段铺板划线测量:
中心线、肋检线,结构线、余量线及对合线等。
8.2大拼板装配尺寸测量—→上分段盖贴定位尺寸测量。
8.3舷部小分段(或散贴外板)与基面分段合拢尺寸测量。
8.4分段大接头处精度控制,分段完工测量(采用立体图、表格结合形式)。
8.5完工分段的中心线、肋检线、对合线必须敲上洋冲眼。
9.分段完工要求:
9.1完工分段应明显标出中心线、肋骨检验线、半宽检验线。
9.2完工分段须带船台散装件,装上快速搭载眼板。
9.4完工分段不准留有未切割的余量。
9.5完工分段的自由边波浪变形必须实施火工校正。
9.6所有的预舾装件安装完整。
9.7分段提交前,作好自检、互检和专检工作,确保一次交验成功。
10.分段施工图在工艺设计中的一些注意事项
10.1施工图中各种安装节点的形式必须表注清楚;
角焊缝的焊脚高度必须注明且无遗漏。
10.2提供片段吊环设置方案,分段吊环的设置应与其他专业室能充分协调好,以避开各种管子、机座等预舾装件,同时尽可能考虑到与总段吊环的兼用性。
10.3凡在内场制造的分段应提供两台行车抬吊用吊环。
10.4分段总组件及船台散装件原则上要求用马板固定在分段上(规格超大者除外),施工图上应注明定位焊等字样。
10.5船台临时工艺孔的布置必须考虑焊工皮带的长度限制、在舱内进行CO2焊接时的通风要求、分段搭载顺序等实际因素,做到方便施工、确保安全。
分段建造方法
一、货舱区域
1.双层底分段
,两个小片段分别以内底板或外板为基面在平面分段流水线上制造,完工后以外底板为基面在外场进行合拢。
外板和内底板均采用FCB法进行拼板,自动角焊角进行纵骨装焊。
(a)内底板在流水线拼板、定位—→内底板拼板焊接、修补—→在内底板上划构架安装线—→装配内底纵骨—→纵骨与内底板焊接、修补—→安装肋板、纵桁和其它构架与零件—→肋板、纵桁、其它构架和零件与内底板之间进行焊接—→预舾装;
(b)外板在流水线上拼板、定位—→外板拼板焊接、修补—→在外板上划构架安装线—→外板纵骨安装—→纵骨焊接、修补—→外场
(c)外场以外板为基面,外板片段为合拢基准片段,内底板片段翻身合拢—→定位焊接—→其它小零件安装—→焊接—→完工测量—→提交船东、船检验收—→正态上门架喷砂涂装。
(a):
保证拼板尺寸的正确,尤其是焊接前对对角线进行测量,保证满足公差要求;
(b):
保证纵骨安装的垂直度和距舯尺寸,最好划线时在拼板上标明;
(c):
分段完工后,进行完工测量,保证各尺寸满足分段制造公差要求;
并按照如下要求进行划线和作好标记,尤其保证洋冲标记反驳在内底板上表面,为船台总组搭载提供参考标准;
(d):
请精度管理组作好焊接收缩量的统计和完工测量记录,在船台总组搭载前提供给船台划线组参考。
2.舷侧分段
3.舷侧分段
,采用活络胎架制造。
4.顶边分段
建造方式:
分段分成3个片状小分段:
甲板片段1、外板片段2和斜旁板片段3,外板片段2以外板为基面在平面分段流水线上制造,甲板片段1以甲板为基面在平面分段流水线上制造,斜旁板片段3以斜旁板为基面在平面分段流水线上制造,完工后在外场平面胎架以斜旁板为基面进行合拢。
外板、甲板、斜旁板均采用FCB法进行拼板,自动角焊角进行纵骨装焊。
4.1甲板片段1
,平面分段流水线制造。
4.2外板片段2
,纵骨装焊,肋板装焊。
,斜旁板带纵骨合拢装焊—→预舾装—→预密性(装配详细流程见下图)—→完工测量
特别注明:
因CS11P/S、HS17P/S、HS18P/S、HS19P/S分段的外板局部有线型,其外板片段2须在活络胎架上制造,由设计所提供电算胎架数据。
4.3斜旁板片段3
,按照精度控制要求施工,完工测量;
后以斜旁板为基面侧态上门架喷砂涂装。
片段制造时保证肋板的定位尺寸和垂直度,再就是片段的整体外形尺寸满足精度控制图的要求,从而保证最终片段合拢时顺利施工,并且满足分段制造的整体精度要求。
4-1顶边水分段
4-,散贴外板。
4-
4-,预装验收—→提交船东、船检验收—→以斜旁板为基面侧态上门架喷砂涂装
5.底边水分段
分段分成2个片状小分段:
外板片段1和底板片段2,外板片段1以外板为基面在平面胎架上制造,底板片段2以船底外板为基面在平面分段流水线上制造,完工后在外场平面胎架以斜旁板为基面进行合拢。
5.1外板片段1
,平面胎架上制造。
5.2底板片段2
5.3片段合拢:
以斜旁板为基面进行合拢(详细流程见下图),按照精度控制要求施工,完工后测量;
后以船底外板为基面正态上门架喷砂涂装。
尤其注意折角板和舭部转圆板的精度控制,装配时采用样板,详细要求参照精度控制图表。
(e):
并按照如下要求进行划线和作好标记,尤其保证洋冲标记反驳在内底板上表面及斜旁板上表面,为船台总组搭载提供参考标准;
6.底边水分段
,散贴外板。
,预装验收—→提交船东、船检验收—→侧态上门架喷砂涂装
保证分段大接头处的横剖面的外板线型,满足精度要求;
保证肋板和舷侧肋骨小T排的安装角度满足精度要求(样台提供安装角度样板);
7.横隔舱分段
,再以槽形后舱壁平面为基面进行卧造,其中P/S槽形舱壁分段进入舷侧C型总组,中部槽形舱壁分段与中部下墩脚分段进行总组后再吊离胎架。
下墩分段分别以下墩垂直板为基面进行制造。
,预装验收—→提交船东、船检验收
槽形舱壁板部装件制造—→上胎架铺板、定位—→构架、部件装焊—→管系和铁舾件预舾装—→与下墩分段总组—→吊环及加强、工装件装焊—→翻身施焊—→另一面管系和铁舾件预舾装—→完工测量—→结构性验收,预装验收—→提交船东、船检验收—→翻身卧态上门架—→涂装
内场部装槽形板拼板时使用检验样板
槽形舱壁分段与下墩合拢时使用检验样板
下墩分段下口尺寸要保证,另须做适当加强
8.甲板分段
,预装验收—→提交船东、船检验收—→反态上门架喷砂涂装
9.舱口围分段
,分别以舱口围壁内表面为基面制造,最后合拢后上船台。
注意油马达基座面板与舱口围面板的相对高度控制比理论值大约10mm,以便于船台搭载
二、机舱区域
10.机舱区域双层底分段
EB01:
内底板铺板焊接—→构架划线—→构架、部件装焊—→管系,铁舾件预舾装—→外板盖板施焊—→吊环及加强、工装件安装—→分段翻身施焊—→预装—→完工测量—→结构性验收,预装验收—→与ES41P/S分段总组—→涂装—→盆舾装
EB02/EB03:
主机面板加工—→主机座结构部件组装—→内底板铺板—→内底板定位,划线、构架部件装焊—→管系和铁舾件预舾装—→外板盖板施焊—→吊环及加强、工装件安装—→分段翻身施焊—→完工测量—→结构性验收,预装验收—→涂装
其中EB03分段完工后与ES43P/S和ET42分段进行总组后,正态上门架,进涂装车间涂装,再进行盆舾装。
EB01~EB03所有板材和型材均无余量加工制造,分段胎架制造时要加放适当的反变形1.5‰(机座面板除外),并且外板散贴时注意大接头处的曲面线型控制,关键点必须保证在精度控制图要求的公差范围内;
EB03与ES43P/S和ET42,EB03与ES41P/S总组注意大接头处的曲面线型控制,关键点必须保证在精度控制图要求的公差范围内;
11.机舱区域分段
11.1分段
,预装验收—→ES41P/S与EB01总组,ES43P/S与EB03和ET42总组—→上门架涂装—→盆舾装
曲面胎架必须提交精度管理组合格后,才可使用,分段制造时注意大接头处的曲面线型控制。
ES43P/S与EB03和ET42,ES41P/S与EB03总组时,保证大接头处的曲面线型控制关键点在精度控制图要求的公差范围内;
11.2分段ET42
,预装验收—→与ES43P/S和EB03总组—→上门架涂装—→盆舾装
12.机舱区域半立体分段
,舷部小分段侧造,完工后大组装
舷部小分段:
曲面胎架制造验收—→外板铺板焊接—→构架划线—→构架、部件装焊—→预舾装—→吊环及加强、工装件安装—→完工测量
甲板拼板焊接、部件制造—→上胎架铺板、定位、划线—→划线验收—→构架、部件装焊—→预舾装—→舷部小分段合拢—→吊环及加强、工装件安装—→完工测量—→结构性验收,预装验收—→提交船东、船检验收—→反态上门架喷砂涂装
曲面胎架必须提交精度管理组合格后,才可使用;
舷部小片段合拢时注意大接头处的曲面线型控制,具体要求按精度控制图执行。
13.艉部立体分段AB02
,艉尖舱小片段以10000mm平台为基面反造,后两片段以FR11横壁为基面合拢。
艉轴小片段:
艉轴壳和轴管垂直装焊—→曲面胎架制造验收—→艉轴壳轴管定位—→左侧外板铺板焊接—→构架划线—→构架、部件装焊—→外板盖板—→吊环安装—→吊离胎架—→合拢
艉尖舱小片段:
平台板铺板划线—→构架、部件装焊—→预舾装—→外板散贴装焊—→吊环安装—→吊离胎架
艉尖舱小片段与艉轴小分段合拢—→加强、工装件安装—→完工测量,划线敲洋冲—→结构性验收,预装验收—→泵气密性,预密性—→轴系预搪孔—→侧态上门架喷砂涂装
FR11横舱壁板与胎板的吻合度≤2.5㎜,另分段制造时注意大接头FR11+250处的曲面线型控制,要满足精度控制图表中的要求。
尾轴小片段制造和总组时要保证轴中心线与基线的平行,偏差≤3㎜。
轴管与FR11舱壁的前后偏差≤3㎜;
定位结束后由精度管理组负责验收。
制定专门的焊接施工工艺,严格控制焊接变形。
艉尖舱小片段与艉轴小分段合拢焊接过程中,由精度管理组负责对SF焊接变形进行全程检测,并及时把测量信息反馈给焊工来改进焊接方法,进一步控制焊接变形
14.艉部立体分段
,RH分段与其总组。
平台板铺板划线—→构架、部件装焊—→预舾装—→外板散贴装焊—→与RH分段总组—→剩余外板和纵桁装焊—→吊环安装—→完工测量,划线敲洋冲—→结构性验收,预装验收—→泵气密性,预密性—→反态上门架—→涂装
RH与AB01的定位合拢主要控制舵杆中心线的垂直度、与AB01“FR0”号位的重合度及上、下舵承距舵机平台的高度;
由精度管理组对定位尺寸进行验收。
在焊接之前必须根据施工图的要求做好必要的加强。
在RH与AB01的合拢焊接过程中,由精度管理组负责对RH焊接变形进行全程检测,并及时把测量信息反馈给焊工来改进焊接方法,进一步控制焊接变形。
三、艏部区域
15.艏部底部分段
内底板铺板划线—→构架、部件装焊—→预舾装—→外板散贴装焊—→吊环安装—→完工测量,划线敲洋冲—→翻身装焊—→结构性验收,预装验收—→正态上门架—→涂装
尤其注意控制艉端内底板和船底外板的相对高度,必须保证在精度控制图要求的范围内。
16.艏部半立体分段
,舷侧小片段侧造,完工后合拢
,舷侧曲面胎架
平台板/甲板铺板划线—→构架、部件装焊—→预舾装—→舷侧小片段合拢—→吊环安装—→完工测量,划线敲洋冲—→结构性验收,预装验收—→反态上门架—→涂装
17.球艏分段
,预装验收—→提交船东、船检验收—→反态上门架—→涂装
18.球艏分段
19.球艏分段
,预装验收—→提交船东、船检验收—→正态上门架—→涂装
20.球艏分段
,两舷部分总组时以艏楼甲板为基面正态散装
,划线—→构架、部件定位—→构架、部件装焊—→外板散贴装焊—→吊环及加强、工装件安装
四、上层建筑、甲板舱室分段
,分段分四片在胎架上总组。
其余分段均以甲板为基面在平面胎架上反造。
21.1.4施工提示:
a)施工图上应注明湿房间的位置,以方便电焊作业。
b)分段围壁下口的临时加强应设置在内侧,以确保外围壁的美观。
c)烟囱内的预舾件较多,各专业室必须协调好,编入分段托盘表,防止漏装。
d)分段PD11C、PD11PS完工后需先行总组后再进行打磨涂装。
a)胎架上铺板以肋骨或中心线为基准,分别用激光经纬仪开出角尺线,并测量铺板的长度、宽度、对角线是否符合型值尺寸;
用压铁、火工等办法使铺板与胎架的吻合度≤2.5㎜。
b)以肋检线或中心线为基准线,分别向两侧划线,从而减少积累误差。
c)围壁板以上口为准足,余量或加放值放在下口;
并从上口向下在光面划一根2米的检验线,围壁板与甲板定位时,采用荡锤线或水平尺的方法取两端及中间三点进行测量确保其安装垂直度,并用斜撑加强,防止焊接变形。
d)门窗高度尺寸,是指下层甲板至门窗中心线的理论尺寸,在划线时必须换算成从上层甲板至门窗中心的尺寸。
e)气割余量时必须增划一条100㎜气割检验线。
75000散货轮分段预密性
为进一步推动分段预密性工作,根据75000散货轮结构设计特点、焊接方法和分段预密性使用的方法,我们对75000散货轮分段预密性制定了初步方案,具体如下:
1.分段预密性采用的一般方法:
1.1角焊缝泵气试验法
1.1.1原理
对于非溶透的角焊缝,采取合适的补板形式,如果整条焊逢无裂缝,则空气可以在两边角焊逢内流动,因此在焊逢一端输送压缩空气,另一端连通压力表可以查看焊缝是否有裂纹。
1.1.2操作程序:
A.焊接前,将连接板固定在焊缝焊缝两端,并在连接板外侧开好止流孔;
B.用适当的焊接工艺进行角焊缝进行焊接,并修补缺陷,同时堵死止流孔;
C.检查焊缝外观质量符合要求后,在角焊缝两端连接板上分别安装压缩空气接头球阀和压力表;
D.开启球阀,将压力至少为0.2kg/cm²
压缩空气通过接头注入角焊缝根部间隙;
E.当压力表超过0.2kg/cm²
,关闭球阀,保持15分钟,检查压力表是否下降;
如果压力表在15分钟内有明显下降,则检查接头或焊缝是否渗漏,寻找压力下降原因;
F.如果压力没有下降,在角焊缝表面涂肥皂水,并观察焊缝表面是否有气泡。
如果没有气泡,则表明该焊缝合格;
如果有气泡,则表明该焊缝出现渗漏,要求作好记号并及时修补,修补长度大于50mm;
缺陷修补后使用真空密性罩重新做试验;
G.试验完工后,及时做好记录,并提交船东认可,再根据焊接要求将连接板上的孔焊死,根据油漆规范要求补底漆;
F.对于连接板外侧无法使用角焊缝泵气密性试验的两端,采用真空密性罩抽真空进行密性试验。
1.1.3能做角焊缝泵气试验水密肋板采用的补板形式
A.
B.
C.
D.
E.
1.2真空密性检查法
1.2.1方法:
用合适的空气排出设备从它内部排出空气,形成一定的真空度,使焊缝两表面形成压力差,来检查焊缝渗漏情况。
试验采用一种叫做真空罩的专门装置。
,例如肥皂水溶液进行。
此时真空罩承受不少于0.2bar(0.2kgf/cm2)的空气压力,渗漏检查可以通过观察在焊缝上肥皂液进行。
1.3着色检查法
1.3.1方法:
喷着色剂检查焊缝表面缺陷的试验方法。
1.3.2焊接完工后,所有需要进行着色试验的焊缝经船东船检认可后方可进行着色试验。
1.4泵气试验法
1.4.1原理:
将舱室内压力增大,形成舱室内外压力差,从而检查焊缝是否渗漏。
1.4.2操作程序
A.首先进行密闭性检查和所有焊缝根部清理,要求对整个舱室完全密闭;
B.安装好泵气装置,先将舱内压力升到0.2kg/cm²
,然后逐渐减低到0.15kg/cm²
的压力保持到试验结束;
C.在焊缝上涂肥皂水检查渗漏情况;
D.如果出现渗漏,要求作好记号并及时修补;
如果没有渗漏,提交船东认可;
E.试验完工后,及时做好记录,并可以根据油漆规范要求补底漆;
1.4.3使用部位:
各种舱室和箱柜。
2.分段需要做预密性的部位和采取的方法:
1.货舱区分段预密性的位置和方法如下图:
2.其它区域预密性原则如下:
A全熔焊不做角焊缝密性试验;
B在单独分段出现密闭舱室时直接采用泵气试验法做密性试验;
C角焊缝密性以角焊缝泵气试验法为主,真空试验和染色试验为辅做密性;
D散贴外板的纵骨上开有通焊孔的角焊缝不做预密性,待总组或船台/坞整个舱室密闭后整体使用泵气做密性;
3.其它说明;
3.1补板在肋板与外板、内底板等角焊接之前安装,补板处肋板与外板、内底板等不许焊接,如图所示:
3.2肋板(包括补板)与外板、内底板等角接是原则上无间隙装配,最大间隙不得超过2mm;
3.3所有的补板严格按照图纸形式,使用自动切割机切割而成,不得私自使用手工下料或使用不符合规范的补板。
3.475000散货轮分段需