注塑不良产生原因及解决方法Word格式文档下载.docx
《注塑不良产生原因及解决方法Word格式文档下载.docx》由会员分享,可在线阅读,更多相关《注塑不良产生原因及解决方法Word格式文档下载.docx(15页珍藏版)》请在冰豆网上搜索。
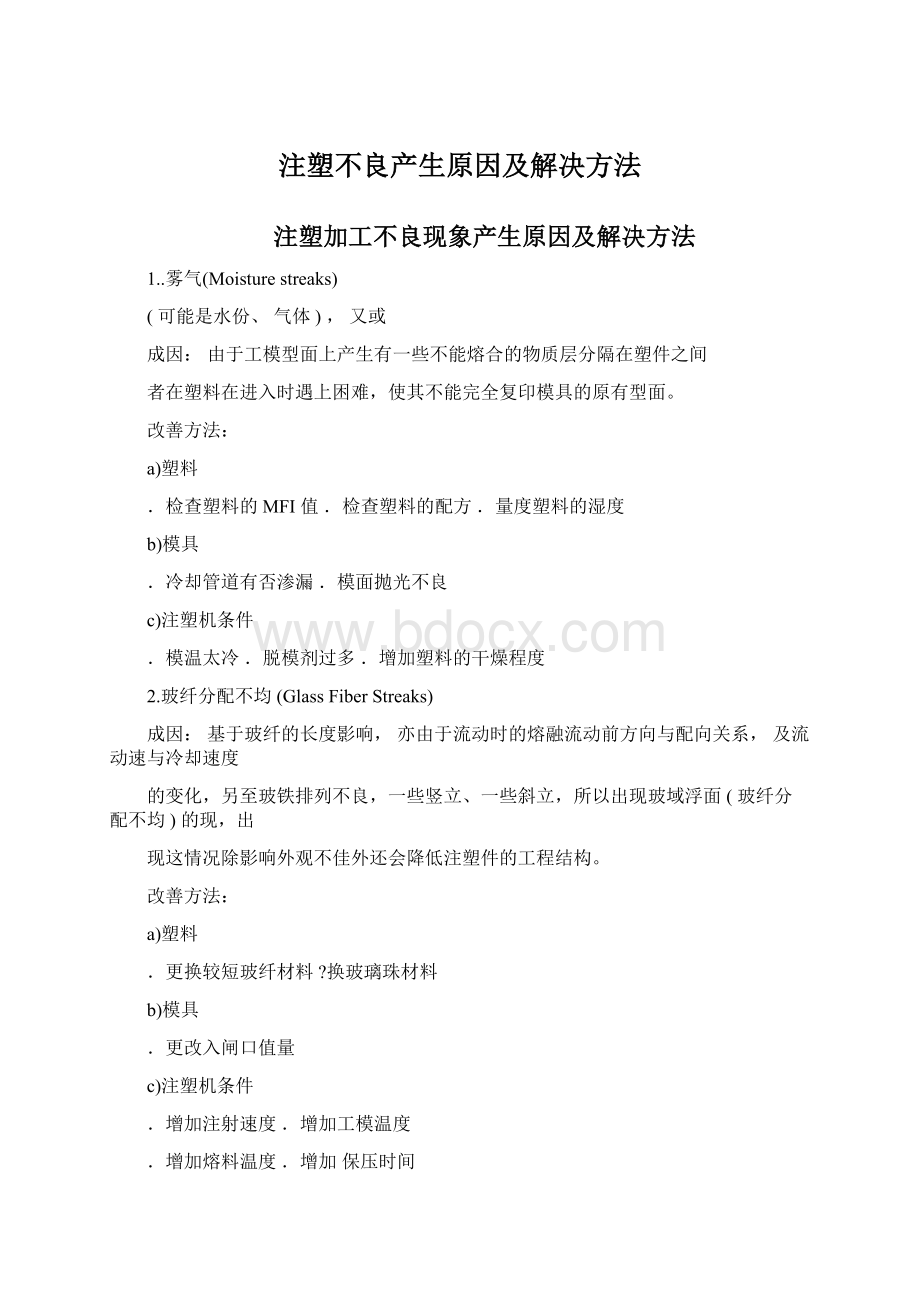
.减低注塑速度.减低锁模压力
.减低注塑温度
4.银丝纹(SliverMarks)
成因:
这种情况是由于模具内有大量水气、又或者注料筒内的热熔塑料有大量被气化的水份、亦
有可能是由添加剂的化学反应引致的气/水份,在注塑过程中一起被注入型腔,并被压至放射形
成银丝纹态状。
.塑料存放失当
.冷却管道有否渗漏.避免过于尖角设计
.减少雕刻深度
.增加干燥温度.增加干燥时间
.增加背压力.减少倒索
.减低注射速度
.检查射值的密封程度.检查/更换颜料等添加剂
5.结合线(WeldLine)
注塑件由于在流入的过程中遇上不良的夹合所以产生结合线,在流动的过程中亦会产生类
同的另一种情况(熔合线MeldLine)。
两者大致产生的原困亦相同无论是塑件设计不良或是注塑
条件欠佳而最重要的由于汇合流峰时产生=或>
10度的温度降。
.更换较高的流动等级
.避免设计厚薄突变.闸口不应设立于薄位处.检查排气道有否闭塞
.增加模具的表面处理.门口迁位(目的将结合线迁位)
.增加工模温度.增加注射速度
.增加熔胶温度.增加保压压力
6.水波纹(WaterWaveEffect)
原因:
注塑件由于在流入的过程中遇上不良的冷却条件、注塑速度过低、或熔料温度过低所以产
生水波纹现像。
另致是塑料一边进入一边急速冷却,不能顺利移动将塑料压向模壁,而塑料进入
是幅射形态推进,经冷却后的表面使形成像水波纹/手指模纹。
.增大闸口直径.增大流道直径
.增加注塑速度.增加温塑压力(第一段).增加塑料熔胶温度.增加模具温度
注:
应用模具温度控制机及切记加上模具隔热板。
7.黑点(DarkSpots)
注塑件出现黑点现像,整体原因都是由不洁所做成。
而不洁的来原亦非常广泛,有关的来
原如注塑操作控制、模具不洁及磨损、注塑机料筒不洁及磨损、原材料污染/翻磨料污染等。
.检查/更换原材料.检查/更换翻磨料.检查/更换添加剂
.检查/优化模具流道死区.检查模具清洁.更换磨损模具配件.检查/清洁热咀系统
.减低熔料温度.调整洽当热咀温度
.调整洽当余料量.清洗注塑机料筒
.检查注机料筒、螺杆、止回阀磨损
8.顶出印(VisibleEjectorMarks)
注塑件出现顶出印现像,成因都是由于脱模困难所做成。
而做成脱模困难的原因基本上有
两种情况,一种是塑件在模具被推时固化不足,另一种情况是模具设计/制作不良而产生。
.更换有高脱模效能添加剂等级材料
.检查冷却管道杨顺/校率.增加冷却管道.增加模具下模光滑.增加模具出模斜度
.检查/增加模具排气道
.优化顶出系统
.减低保压压力.减低保压时间
.优化转压点.减低模具温度
.优化顶出速度
.增加冷却时间
注:
应用模具温度控制机切记加上模具隅热板。
9.变形(DeformationDuringDemolding)
注塑件出现变形现像,成因在几类环境下都会产生一种是于脱模时/脱模后立即出现、第二
种是于脱模后一段时间才出现。
第一种情况是由于固化条件不良/模具设计不良而做成的变形,
另一种注塑件变形是在注塑过程上提供了不良注压条件所致。
.更换强度较高/纤维增强的塑料品种.更换有高脱模效能添加剂等级材科
.检查冷却管道畅顺/校率.增加冷却管道.增加模具下模光滑
.增加模具出模斜度.检查/增加模具排气道.优化顶出系统.增加模具强度
.增加模塑件肋骨
注塑机条件
.减低保压压力.减低保压时间优化转压点.减低模具温度
.优化顶出速度,增加冷却时间
另一种是"
收缩率过大产生的变形。
就相对要增加温塑压力及注塑时间。
10.填充不足(ShortFiIling)
注塑件出现填充不足现像,成因在两类环境下都会产生,一种是属于不良的注塑加工操作
因素产生,另一种属于注塑件设计不良导致。
注塑加工因素产生的缺陷多数由于注塑过程中塑
料从闸口至填充完成前遇上过大的温度降及压力降影响。
注塑件设计不良导致的缺陷,多数由于
闸口开设不良/太远、厚薄不均、整体胶位过薄、特殊设计限制、排气不良等。
.优化闸口开设位置.优化塑件壁厚.优化特殊设计.检查/增加模具排气道
.增加模塑件辅助支流(subFlow)
.增加注塑容量.增加注塑熔融温度
.增加注塑压/保压压力.增加注塑速度
.增加注塑时间.增加模具温度.减低锁模压力.使用特殊注塑机种
11..冷料流痕(ColdSlug)
注塑件出现冷料流痕现像,成因是当熔融塑料通过在闸口或射咀时提早轻微固化,而与后
段熔融塑料一拼进入型腔时所产生。
情况严重有如非深刻的结合线差不多。
.增加/优化冷料井
.增加/优化射咀温度.改用细孔射咀.减少倒索.使用闭咀系统
12..进浇口点不良(DullSpotsNearTheSpure)
注塑件出现进浇口点不良现像,实际是高剪切应力裂化情况,而多出现在潜水式闸口和黏
度较高的塑料件身上。
成因是当高黏度熔融塑料通过在极细的开口时,要高速、高压才能通过,
所以便会在入闸口附近产生过荷裂化缺陷。
.更换较高的流动等级塑料.使用改善流动添加剂
.增加模具闸口直径.增加模具流道闸口光洁度
.更改闸口位置
.减低注塑速度.级段优化调整注塑速度(S-F)
.增加注塑熔融温度.增加模具温度
.使用特殊注塑机种
13.喷射痕(Jetting)
注塑件出现喷射痕(蛇仔纹)不良现像,成因是注塑机对该塑料的塑化量不足,或该塑料在
未完全熔融的状态下,通过闸口与后段熔融塑料一拼进入型腔时所产生的情况。
.增加模具闸口宜径.更改闸口位量
.增加障碍在闸口前
.减低注塑速度.级段优化调整注塑速度(s-F)
.检查/增加注塑熔融温度
.增加模具温度.增加背压压力
14.表面起层(FlakingOfTheSurfaceLayer)
注塑件出现表面起层的不良现像,成因是该注塑件的塑料配方在成形后产生不完全熔合
或该塑料配方内(包括添加剂)在成形后产生排斥分裂现像。
.检查/更换塑料混合配方.检查/更换塑料添加剂混合配方
.检查塑料干燥条件.检查/优化螺杆旋转速度.检查塑料塑化程度.减低注射速度
.减低熔料温度.增加模具温度
15.浮泡(EntrappedAir)
注塑件出现浮泡的不良现像,成因是该注塑件在熔料过程中混入大量空气,或在使用过度
的倒索功能时抽入大量空气,并且在注塑过程一拼注入模具型腔内,而该塑料配方属透明等级,
更易看见此现像。
.检查塑料粒状是否太大
.减少倒索功能.增加背压
.减低螺杆旋转速度.检查熔料系统是否正常操作
16.过热变色(BurntStreaks)
注塑件出现过热变色的不良现像,成因有多方面若聚合物受热过度,分子链便会产生分裂,
并且会热降解或燃烧,这时便会出现可见过热变色现像。
有时只见一些黄色的色变亦显示已经出
现轻微热降解,热降解不单由聚合物的燃烧引致,聚合物内的袖剂也是导因。
处理燃烧缺陷一定
要知道在甚么地方出现:
若熔体在清机时没有出现啡、黄,黑的色变,说明熔体在离开炉嘴后始发生燃烧,应该检
查主径、流道、入水位和模具设计或校正、注、速度、压力等。
若清机时发现咖啡条纹或色变,证明降解在炮筒、炉嘴内发生。
若同时见到咖啡条纹和银色条纹,便应怀疑是否水分方面出了问题若位置固定而部件成品
的构型一样,燃烧便是源于检查阀门或炉嘴尽头。
若色变分散,降解便是在炮筒、螺杆(进料口侧)发生。
.检查,更换塑料添加剂混合配方.减小翻磨料比例
.优化模塑件尖角.增加流道/闸口直径.优化模塑件壁厚.检查排气通道
.检查热流道系统
.减低注塑容量.减低注塑熔融温度.减低螺杆旋转速度.减低背压级段优化注塑速度
(s-F)
.检查熔料系统是否正常操作
.减低总周期
.检查干燥系统清洁.检查注塑系统是否正常
.使用洽配注塑机种
17.龟裂(StressCrack)
注塑件出现龟裂的不良现像成因是该注塑件的塑料在注塑过程中受着过大的剪切应
力加工而老化出现时就是它的龟裂过程开始塑料在注塑过程中受剪切应力破坏的过程,是
指塑料在加热不足、流动不佳的情况下,强行将它用较大的压力推入型腔内的注塑行为,份
子过度拉长,当老化来临时它使容易断裂会产生龟裂纹,透明塑件更容易看见此现像。
.增加流道/间口直径.优化模塑件壁厚
.级段优化注塑压力.延迟转换保压压力
.减低保压压力.减低注塑速度
.增加注塑温度(无定形料).增加模具温度(无定形料).增加冷却时间(无定形料)
.减低注塑温度(结晶形料).减低模具温度(结晶形料).减低冷却时间(结晶形料)
18.缩水痕(SinkMarkS)
注塑件出现缩水痕的不良现像,成因有多方面,例如:
不洽当选择塑料特性、不良
塑件设计、和较差的注塑条件等都会导致有缩水痕出现。
将上述各项缩水痕的成因来源分
析后,总结了以下几点:
塑料固化太慢、有效保压时间不足、有效保压太低及保压传送不良。
.检查塑料粒状条件.更改低收缩等级材料.添加发泡剂
.检查模具排气线.检查模具主流径与门口尺寸.改善模具壁厚
.改善模具壁厚与肋骨位之间厚度比率.增加模具冷却管道
.增加储科量.检查注塑机螺杆止回阀
.检查/移除进料口积聚的材料
(+).优化保体压力(+)
(-).改变料温(-)
改变注塑速率(-).优化保压时间(+).优化保压压力(+).改变模温(+)
(+).改优注塑速率(+)
19.真空气泡(DensityBubble)
注塑件出现真空气泡的不良现像,成因主要是该注塑件的塑料在注塑过程中得不到
充份密度填充所致。
塑件得不到充份密度的填充原因,大多数与塑料的类别(结晶形/无定
形)、流道闸口过早停止进入塑料或塑件设计不良有关。
.检查塑料的类别(结晶形/无定形).更换低气泡量塑料(PP)
.检查,增加模具排气道.减短模具主径及流道
.增加闸口尺寸.减低模具壁厚
.优化模具壁厚薄之间相差比率
.增加注塑总容量.优化注塑余量.级段优化注塑压力.增加保压压力
.增加注塑速度.增加注塑温度
.增加模具温度.增加注塑时间
20.披锋(FIash)
注塑件出现披风的不良现像,成因主要是该注塑件在注塑过程中得到过份塑料填充所
致。
塑件过份填充原因,大多数与塑料的等级(流动指数MFI)、塑件设计不良、工模损坏,
或注塑机种,注塑机效能与调整有关。
.更换较低的流动等级材料
.检查模具损坏.优化模具壁厚薄之间相差比率
.检查/增强模具结构及强度
.级段优化注塑压力.减低注塑压力
.优化保压压力转换位置.减低保压压力
.减低注塑速度.减低保压时间
.减低注塑温度.减低模具温度.增加锁模压力
.更换锁模力较大机种
21.擦伤印(ScratchMarks)
注塑件出现擦伤印的不良现像,成因主要是该注塑件在注塑完成后脱模过程中与模
具的壁面和边角间产生过份磨擦所致。
塑件产生过份磨擦原因,大多数与塑件脱模斜度不
足、工模结构强度不足、工模损坏,或注塑机效能与注塑参数调整有关。
.检查模具上模夹线损坏.增加模具上模光滑度
.增加模具出模斜度
.检查/增强模具结构及强度.检查/增加上模模具排气道.检查冷却管道畅顺/校率
.增加上模冷却管道
.减低注塑温度.减低模具温度.减低模具开启首段速度
01.填充不足
1.注射压力不足提高注射压力
2.充填速度慢提高注射速度
3.树脂温度低提高机筒温度
4.排气不好气体滞存在未充填部加排气孔(长2-4mm,深0.015-0.02mm)
5.浇口过小扩大浇口尺寸或缩短浇口流道的距离
⑥防逆流阀与机桶的间隙过大检查阀的磨损
02.表面状态不好,无光泽
6.成型品密度不足增加剂量,提高注射压力
7.充填速度慢提高机桶速度
8.模具温度低提高注射速度,提高模具温度(<
140℃)
9.排气不好充分排气
03.凹陷及空巢
1.成型品密度不足增加剂量,提高注射压力,延长注射时间
2.树脂产生气体过多实施充分的事前烘料(140-160℃,1-2hr)
3.壁过厚最厚为6mm
4.热收缩大降低机桶及模具的温度
04.内部裂纹
1.成型品冷却过快提高模具温度,成型品取出后慢慢冷却
2.产生残留应力降低注射压力,提高模具温度,降低冲填速度
3.壁过厚降低壁厚并均匀化
05.翘曲
1.成型品冷却不均匀调整模具温度的平衡
2.成型品壁厚不均匀使制品的壁厚均匀化
3.填充过度减少剂量,降低注射压力
4.注射速度过快降低注射速度
06.接合部强度不足
1.模槽部压力不足或模具温度过低提高树脂及模具的温度,提高充填速度,提高注射压力,
增加供料
2.模槽内空气滞留设排气孔或成型品外侧树脂溢流区
3.浇口位置不当更改浇口位置避开接合线发生在复合的部位
07.烧焦
1.气体滞留加排气孔
2.树脂温度过高降低机筒温度及充填速度
08.成型品在高温使用时尺寸稳定性差,刚性不足
1.树脂的结晶化不足提高模具温度、对成型品进行退火处理
09.顶模困难
2.脱模锥度不足加大脱模锥度、使用脱模剂
3.成型品残留在模心面模槽侧面锥度过小要加大、模槽研磨、稍切掉模心面底部
10.顶出部成型品破损及顶出不良
1.脱模鞘位置不适或脱模鞘的直径过小使脱模鞘作用平衡
2.成型品冷却不充分增加脱模鞘的直径、增加成型周期、降低模具温度、扩大脱模锥度
11.流道脱落困难
1.浇口护套不光滑将浇口护套研磨光滑
2.流道锥度不足增大流道的锥度
3.流道与喷嘴尺寸不当调整流道与喷嘴的尺寸
12.喷嘴溢流多
1.树脂含水量多充分进行事前烘料(140-160,2hr)
2.树脂产生的气体过多降低喷嘴及机筒温度、使用溢流防止阀
13.成品表面出现黑点
①.冷胶跑进成品内扩大冷胶井、提高喷嘴温度
14.飞边
1.模具锁模力不足提高锁模力
2.模具变形修理模具
3.物料流动速率过高选用流动性较低的料
4.注塑压力等工艺不当调整注射压力等工艺
15.熔接痕
1.注塑工艺设置不当提高料温、模温,调整注塑速度和压力
2.排气不良提高注塑压力,增设或扩张排气通道
3.腔内有异物清理模腔表面
4.物料流动性不足选用流动性较高的料
16.成型收缩大或有缩孔凹痕
1.注塑量不足,模腔填充不够增加注塑量
2.浇口尺寸太小,无法补料加大浇口尺寸
3.注射压力不足,物料进入量不够提高注射压力及保压压力
4
降低料筒温度及模具温度
修改设计
提高模具光洁度及清洁表面
充分干燥原料
.料温或模具温度过高
5.模具或制件设计不合理17.表面粗糙浮纤①.模具表面粗糙或结垢②.原料中有易挥发性物质
6.排气不良增设排气通道
7.模具温度过低提高模具温度
8.注塑工艺设置不当调整注射速度、压力和延长保压时间等
18.厚壁制件开裂
1.内应力过大调整成型工艺和后处理工艺
2.模具温度和注塑温度设置不当合理调整模温和注塑温度
3.润滑剂、脱模剂使用不当减少脱模剂用量
4.嵌件位置设置不当或未预热优化设计并对嵌件预热
5.材料选择牌号不对选择适用于厚壁成型的料