年产300吨硫酸链霉素生产线课程设计文档格式.docx
《年产300吨硫酸链霉素生产线课程设计文档格式.docx》由会员分享,可在线阅读,更多相关《年产300吨硫酸链霉素生产线课程设计文档格式.docx(16页珍藏版)》请在冰豆网上搜索。
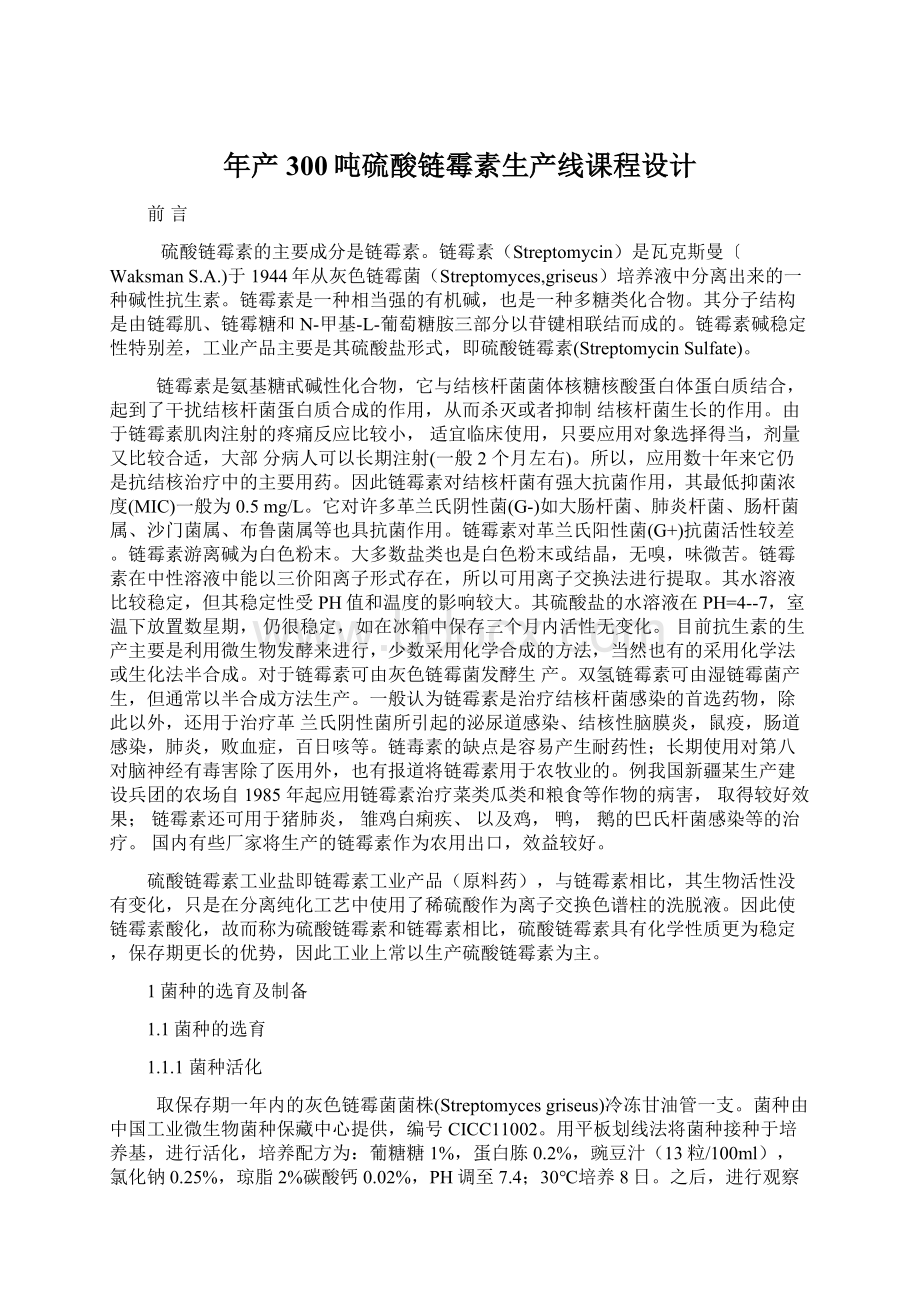
用平板划线法将菌种接种于培养基,进行活化,培养配方为:
葡糖糖1%,蛋白胨0.2%,豌豆汁(13粒/100ml),氯化钠0.25%,琼脂2%碳酸钙0.02%,PH调至7.4;
30℃培养8日。
之后,进行观察:
首先观察培养基内菌落菌落是否为为白色丰满的梅花形和馒头形,背面为淡棕色色素菌落;
之后,取少量进行涂片,简单染色后观察细胞形态状况,排除形态异常菌落,于斜面固体培养基内传代作为种子使用,传代培养基成分与活化培养基成分相同。
1.1.2孢子生产
取上一步活化菌种斜面一支,进行种子子培养。
产种子培养基成分为:
酵母浸膏2%,七水合硫酸镁0.05%,磷酸氢二甲0.05%,葡萄糖1%,氯化钠0.5%,PH调至7.8。
培养基灭菌后,于超净台内接种,接种孢子的浓度按2.5%接入100ml培养基,30℃、200rpm震荡培养48小时。
1.1.3摇瓶发酵
将种子按照6%浓度分别接种于5个三角瓶中的生产培养基中进行发酵实验。
培养基成分为:
黄豆饼粉5%,玉米淀粉4%,硫酸铵0.6%,磷酸氢二钾1%。
30℃、200rpm震荡培养48小时,之后降温至28℃,继续震荡培养96小时。
1.2HPLC法检测发酵产物含量
分别从5个三角瓶中各取100μl发酵液,过0.45μm孔径膜除去杂质,4摄氏度保存备用。
之后,称取0.05g标品,置于50ml容量瓶中,加0.1mol/L氢氧化钠10ml,60摄氏度水浴40min。
之后,各加入1%硫酸铁铵0.5ml使之与发酵液中的产物络合,之后超纯水定容,过0.45μm膜除去杂质。
色谱柱:
选用SymmetryshieldTMRP18C18柱(5μm,3.9mm×
150mm)色谱柱,流动相:
乙腈-庚磺酸钠溶液(1.0g庚磺酸钠溶于500mL水,体积比20∶80),流量:
0.5mL/min,柱温:
30C检测波长330nm,进样体积:
5.0μL,保留时间:
2.477min。
在上述操作条件下,待仪器基线稳定在1.0×
10-3AU范围内变化后,连续数针标准溶液进样,当相邻两针的峰面积变化小于1.5%时,进样顺序为:
标准溶液、试样溶液
(1)、试样溶液
(2)、试样溶液(3)、试样溶液(4)、试样溶液(5)、标准溶液的顺序进样进行分离和测定。
待出峰后计算链霉素含量,并确定单位量灰链霉菌的链霉素产量。
若产量达到足够要求,则对菌种进行保存并进行下一步。
1.3菌种的保藏
短期保存:
取之前活化菌种适量接种于固体斜面培养基上,30℃培养48小时,之后缓慢注入50%灭菌甘油水溶液。
用量可超出斜面1cm即可,之后将斜面置于4℃冰箱进行保存。
单支保存期不超过一年。
长期保存:
取经过2%盐酸刷洗,超纯水清洗并高温灭菌的安瓿瓶1支,瓶内加灭菌脱脂牛奶2ml。
之后,接种环刮取活化好并进入稳定期的菌种细胞若干,并将其转移至牛奶中,充分溶解。
溶解后,置于-80℃冰箱预冷2小时。
待溶液冷冻后,将安瓿瓶转移至冻干机冻干。
当安瓿瓶中冰块完全冻干后,瓶内抽真空并封口。
2培养基设计及灭菌
2.1培养基类型及其功能
微生物大规模发酵设计主要用到孢子、种子、生产培养基以上三种类型。
孢子培养基配置得目的主要是活化保藏菌种,并给菌体繁殖孢子提供条件,常采用固体培养基,对这类培养基的要求主要是可使菌体快速生长,并产生大量优质孢子,且无致变异物质。
种子培养基主要为孢子出芽、生长、大量繁殖菌丝提供营养物质。
并使菌丝生长情况良好,可产生大量种子。
酵培养基是供菌体发芽、生长、繁殖、合成产物使用。
要求是既能够使种子接种后能迅速生长,可使其达到一定的菌丝浓度,又可以迅速合成产物。
2.2培养基的成分
培养基主要成分为水、碳源、氮源、无机盐及微量元素、生长因子、促进剂和抑制剂等几大部分组成。
不同的微生物对碳源、氮源及微量元素、生长因子所需含量不同。
且相同微生物不同生长时期所需物资也有所不同。
故,在工艺设计过程中需考虑培养基中各种物质在不同时期所占比例。
2.2.1碳源
碳源主要为微生物提供生长繁殖及其他生命活动所需的能量,为合成菌体和发酵产物提供必须的碳成分。
常用的碳源有糖类、油脂、有机酸、低碳酸及轻链烷烃。
通过查阅已有文献资料,本设计采用玉米淀粉作为碳源。
2.2.2氮源
氮源主要用于构成菌体细胞的细胞质、蛋白质和其他含氮代谢产物.分为有机氮源和无机氮源。
常用有机氮源有花生饼粉、豆饼粉、棉籽饼粉、玉米蛋白粉、蛋白胨、酵母抽提物等。
常用无机氮源有铵盐、硝酸盐、氨水。
相比较有机氮源来说,微生物细胞对无机氮源的吸收效率要由于有机氮源。
根据以往文献资料[2],并结合实验比较花生饼粉、豆饼粉、棉籽饼粉、玉米蛋白粉和铵盐、硝酸盐、氨水几种物质作为氮源时链霉素的产量。
本设计选用的碳源分长效碳源和速效碳源,长效碳源为黄豆饼粉,速效碳源为硫酸铵
2.2.3水
水是所有培养基的主要构成成分,也是微生物机体的重要组成成分。
为避免水质影响,故选用自来水为水源,经过净水机纯化处理引入发酵罐作为生产用水。
2.2.4无机盐及微量元素
微生物生长所需的无机盐多种多样,其中最为关键的是钠盐、钾盐。
本设计选用磷酸氢二甲和氯化钠作为钾盐和钠盐。
2.2.5其他
经查阅文献及实验筛选。
本设计中,培养基内将在发酵100小时时添加1%巴比妥酸衍生物及钙离子。
2.3培养基优化
虽然培养基成分确定,但需要调整不同物质浓度达到适宜浓度。
适宜浓度培养基应具备利用率高、转化率高的特点。
转化率分理论转化率和实际转化率。
理论转化率可由反应方程式物料衡算求得。
实际转化率则需要实验确定。
本设计采取单因素实验选择最优成分,正交实验选取最佳浓度及组合。
首先进行单因素实验,筛选合适碳源、氮源。
复合碳源在淀粉、麦芽糖、蔗糖、甘油之间选择,复合氮源在花生饼粉、豆饼粉、棉籽饼粉、玉米蛋白粉、青霉菌菌丝水浸提物和黄豆粉抽提物之间进行筛选。
最后,多因素实验,并计算K、R值。
最终选择玉米淀粉和黄豆饼粉作为主要的碳源和氮源。
3灭菌
3.1培养基灭菌
本实验采取湿热蒸汽灭菌,条件为121℃、大气压0.1MPa进行。
灭菌时间由
经验公式
计算求得灭菌时间。
公式中:
τ为灭菌时间
N为经过τ时间灭菌后微生物数量,
N0为培养基灭菌前微生物数量,通常通过实验计数求得。
3.2空气灭菌
3.2.1过滤除菌流程及设备
由于采用AtlasCopcp成套服务方案,故本设计空气净化流程如下:
采风塔→OSS空气净化器→空气压缩机→冷却器→空气储罐→油水分离器→空气换热器
设备如下:
1.采风塔:
考虑到太原地区风向流动问题,采风塔选址位于厂区西北侧,远离下风处,高20m,气流8m/S
2.空气压缩机:
选用AtlasCopcp公司ZH+型离心式无油空气压缩机,流量1200L/s-4800L/s。
3.空气净化器:
选用AtlasCopcp公司OSS空气净化分离器。
该分离器对2μm左右颗粒分离效率可达到75%,且耐蒸汽灭菌。
4.空气冷却器;
压缩后空压机出口温度约为120℃,故添加列管式热交换器。
换
热面积由公式计算求得
考虑热损失,实际换热面积为理论换热面积的120%。
5.空气储罐:
储量由公式VR=0.1×
V1V1为空气压缩机每分钟排气量。
计算后,决定选用AtlasCopcp公司2000m3储气罐两个。
罐体高径比为2.5。
储罐适用温度范围为-40℃-40℃。
7.油水分离器:
考虑到空气中存在一定数量的油状液滴,OSS过滤器主要分离固体物质。
因此在此加入AtlasCopcp公司OSC油水分离器,以除去油状液滴,可耐高压蒸汽灭菌。
根据供货商提供数据,本设计选用QSC-2400型油水分离器。
设备-40℃-40℃。
8.空气换热器:
考虑山西地区冬夏气温差异较大。
不同时期所需的空气温度,故选用AtlasCopcp公司1600-CMF空气干燥热交换器。
交换器腔体内通过过滤空气,腔体外通过电加热/冷却剂降温。
夏季可降低空气温度,冬季可提高空气温度。
由于发酵生产需要高洁净度空气,因此在生产前应向供气管路中通入足量高压蒸汽进行灭菌。
考虑设备具有较高耐受能力,故蒸汽压力选择在0.2—0.4MPa之间,灭菌时间为45min。
3.2.2无菌空气检查
为保障通入罐体内的空气为无菌空气,故需要对空气进行检查。
为简化工作流程,减少工作量。
本设计采用撞击式空气微生物采样器对净化空气中的微生物数量进行计数。
3.3发酵罐灭菌
发酵罐可采取空罐灭菌和实罐灭菌。
本设计采取空罐灭菌法对发酵罐及附属管道设备进行灭菌。
工作流程是:
首先,关闭阀门,蒸汽由上部进入,压力维持在4—5kg/m2,温度维持160℃。
对管道及罐体内部进行冲刷
当罐体内温度>
80℃后,减小蒸汽供应量,继续向罐体内通入蒸汽,维持气温121℃,0.2MPa,时间30min。
减小通气量后,继续观察罐体内温度值,当罐体内温度达到118℃后,计时30min。
计时结束后,关闭蒸汽阀,向罐体内通入无菌空气,使罐内维持正压,并在罐外通冷却水冷却罐内温度至55℃以下。
4.种子扩大培养
本设计采取三级种子罐工艺流程,设流程如下:
孢子→锥形瓶→种子罐→种子罐→发酵罐。
首先进行种子的活化培养,之后进行初步扩增,然后进入种子罐,再次扩增两次。
4.1实验室种子制备
取之前保存的石蜡油斜面两支,在超净台内分别取少量菌种接种于孢子培养基平板上。
养配方为:
葡糖糖1%,蛋白胨0.2%,豌豆汁(13粒/100ml),氯化钠0.25%,琼脂2%
平板活化后,即可进行摇瓶扩大培养,以获得足量菌丝体作为种子。
液体培养基配方为:
取上一步活化菌种斜面一支,进行种子子培养。
产种子培养基为:
酵母浸膏2%,七水合硫酸铵0.05%,磷酸氢二甲0.05%,葡萄糖1%,氯化钠0.5%,PH调至7.8。
孢子浓度按2.5%接入100ml培养基,30℃、200rpm震荡培养48小时,光照充足。
4.2生产车间种子扩大培养
一级种子罐扩大培养:
取一瓶活化情况较好的菌丝体,用压差接种法接种于种子罐进行扩大培养。
在30℃条件下培养24小时,之后进行二级种子罐的扩增。
要求供氧良好,搅拌转速为350rpm。
二级种子罐扩增:
将一级种子罐内细胞以压差法移入二级种子罐,接种量按6%进行接种。
接种完成后,30摄氏度培养24小时,使细胞进入对数生长期。
发酵罐生产培养。
将经过二级种子罐扩增的细胞移入三级种子罐,接种量控制在10%左右。
首先,于30摄氏度培养48小时,使细胞进行大量繁殖。
之后,降温至28摄氏度,培养96小时,转入产物合成阶段。
生产培养基配方为:
另外,在发酵进入到产物合成阶段时,补料内添加1%巴比妥衍生物。
5发酵过程参数控制
5.1发酵过程补料控制
根据参考文献和已有生产经验,本设计采用分批补料发酵工艺。
由于链霉菌发酵周期为48小时(生长期)+96小时(产物合成期),所以补料时期选在生长期后期开始进行补料。
一个批次共补料类次。
分别是:
补全料:
一个发酵周期约补3次。
每吨发酵液约补370L全料。
从发酵20小时开始补全料,至30小时时结束。
根据发酵液还原糖含量水平控制具体补全料体积及时间。
补稀料:
一个发酵周期补2次左右。
每吨发酵液约补200L稀料。
自发酵40小时后开始补稀料,根据发酵液还原糖含量水平控制,保持还原糖浓度大于等于2.6g/100ml。
补氨水:
自发酵33小时开始补氨水,每4小时补一次,每次10-15L,使发酵液中氨氮浓度不低于45mg/100ml。
补氢氧化钠:
调节发酵液pH,保持发酵液pH在6.8-7.2之间。
5.2发酵过程PH控制
pH值直接影响到发酵过程中各种酶活动,影响菌体对基质代谢的速度,甚至改变菌体的代谢途径及细胞结构。
菌体的发育生长和抗生素的合成有不同的适宜pH值。
发酵过程中pH值必须予以控制,才能符合菌体生长和抗生素合成的需要。
影响pH值的因素有生化反应过程特性,以及发酵过程的环境变量,如温度。
另外,作为发酵过程氮源的硫酸铵和碳源的糖等补料加到发酵液中也会影响pH值。
适合链霉菌菌丝生长的pH约为6.5~7.0,适合于链霉素合成的pH约为6.8~7.3,pH低于6.0或高7.5,对链霉素的生物合成不利。
pH对链霉素发酵影响很大,故很多国家为了准确控制pH值,使用pH自动控制装置。
这样,可提高发酵单位,又可以减少培养基中碳酸钙的用量,在发酵液预处理时,还可减少中和用的酸量。
本设计采用参考文献[3]中的PH调节程序进行PH调节控制。
5.3.发酵过程中温度控制
由于灰色链霉菌对温度敏感。
且生长适宜温度(30℃)和生产适宜温度(28℃)不同,所以需要对温度进行调控。
在生长期,需恒定温度在±
30℃,生产期需要恒定温度±
28℃。
因此在生产过程中,分期检测调整温度恒定范围。
使不同时期均可以达到最适宜温度。
5.4发酵过程中溶氧调控
链霉素产生菌一灰色链霉菌是一种高度需氧菌。
它在整个代谢过程中以葡萄搪做为主要碳源,只有以氧做为最终电子受体时方能获得大量能量,来满足菌体生长、繁殖和合成链霉素的需要.物质代谢与能量代谢是相辅相成的。
据文献记载,空气中,氧在培养液中的饱和浓度(1atm,25°
C})大约只有0.2毫克分子(O2)/升,而链霉素发酵液中菌体的摄氧率在10~50毫克分子(O2)/升小时。
因此向发酵液中迅速地补充溶解氧.是链霉素发酵中的重要问题。
对溶氧水平有较大影响的因素主要有:
a、菌体代谢是否旺盛。
b、培养液的粘度:
过高的粘度会影响氧的传递,即影响氧由气相溶解于液相之中。
c、补料:
补糖后糖代谢加快,补入10秒钟后溶氧即明显下降,但经30~40分钟后又逐渐恢复到补前水平。
这种变化当补糖量超过1.0%时较明显。
当补无机氮源使氨基氮增加l0mg/100ml以上时,亦有这种变化。
d、罐压:
实验证明罐压对溶氧的影响较空气流量对溶氧的影响更为明显。
在菌体生长前期,空气流量在一定范围内的增减对溶氧几乎没有什么影响,而罐压变化则溶氧变化明显。
在培养前期,一般罐压每升高或降低0.lkg/cm2溶氧浓度就升高或降低4%左右;
在培养中、后期,罐压每升高或降低0.lkg/cm2溶氧浓度就升高或降低3%左右。
但罐压不能控制过高,超过一定限度对菌体的生长、代谢就要产生不良影响。
e、空气流量:
体积氧传递系数中Vs为空气在罐中的直线速率,它与空气流量是等效的。
从提高KLa的角度看,应尽量增大Vs,但超过一定限度后溶氧浓度不再上升,反而会造成泡沫上升,发酵中间产物未及被利用即被带出而造成不良后果,甚至使搅拌器周围充满气泡从而使搅拌失去作用,造成溶氧下降。
从价值工程原理出发,应确定一个最适空气流量vs,即不使通气量过剩,又满足灰色链霉菌对氧的需求。
f、搅拌:
搅拌对溶氧浓度影响最大。
在培养过程中如停止搅拌、溶氧浓度迅速下降几乎到0,此时如果增加空气流量,增大罐压都无济于事。
同时对于不同的搅拌桨形式以及速度对溶氧也会产生很大的影响。
机械搅拌能损坏菌丝体,对发酵液过滤不利,采用空气搅拌器则克服了这一缺点,提高了罐的利用率。
采用大直径小浆叶的搅拌器,在适当增加转速下,能得较高的吸氧率。
另外将涡轮式改为多棒式搅拌器,可降低功率消耗近一半。
5.5泡沫的影响及调控
由于通气搅拌和发酵过程中产生的二氧化碳及糖类蛋白质等物质纯在,使得发酵液含有一定量的气泡。
泡沫存在虽然有利于液气交换,但大量泡沫存在易出现冒顶染菌的风险,同时也占用装罐体积。
由于链霉菌生长生产对溶氧量要求较高,本设计采用机械消泡和消泡剂同时采用的方法消除泡沫。
消泡剂选用聚氧丙烯甘油醚和豆油,在前期泡沫较少时先采取豆油和机械进行消泡,中后期改用聚氧丙烯甘油醚和机械进行消泡。
机械搅拌转速控制在350rpm。
5.6异常控制
考虑到工厂洁净程度及员工熟练程度影响,在生产过程中可能存在染菌的风险。
在加强员工无菌观念培养的同时,本设计列举几个常见的发酵异常情况,以便在生产过程中查阅。
培养基变稀:
噬菌体污染,营养成分缺乏
培养基过浓:
生产水污染,
糖类消耗过慢;
种子衰退,生长受到抑制,发酵条件不适宜
6下游加工
6.1产品分离纯化
四级或三级发酵生物合成链霉素。
发酵液用水稀释,草酸酸化至pH3.0左右,加热至75~80"
C,通过离心分离或板框过滤,除去大量不溶性菌丝体、酸性蛋白、钙镁离子、培养基残渣等杂质,冷却至15℃以下,再用NaOH中和得到符合离子交换工艺要求的澄清链霉素原液。
这一过程在生产上称为发酵液的预处理。
原液中的链霉素在水溶液中离解成三价阳离子,应用钠型弱酸性阳离子交换树脂110树脂进行吸附,5%硫酸洗脱后成为链霉素酸性洗脱液,之后再通过401树脂并经过8%硫酸洗脱;
在这一步提取过程中使水溶液中的链霉素得到富集,含量由不到1%浓缩到20%,同时,通过离子交换树脂的选择作用,除去绝大部分的无机离子、色素、蛋白及可见的固形物等。
之后,再经过330-OH和110×
H中和得到提纯液。
提纯液先经药用活性炭脱色处理,吸附色素和细菌内毒素,中和过滤进一步除去杂质,在45°
C以下超滤浓缩,链霉素含量由10%左右浓缩到45%。
最后通过氢氧化钙调PH为弱碱性。
成品浓缩液经过石棉板除菌过滤,喷雾干燥得到白色或类白色的无菌粉末,分装出厂。
6.2质量检测
酸度:
取本品,加水制成每1ml中含20万单位的溶液,依法测定pH值应为4.5~7.0。
溶液的澄清度与颜色:
取本品5份,分别加水5ml,溶解后,溶液应澄清无色;
如显浑浊,与2号浊度标准液比较,均不得更浓;
如显色,与各色5号标准比色液比较,均不得更深。
干燥失重:
取本品,以五氧化二磷为干燥剂,在60°
C减压干燥4小时,减失重量不得过6.0%
异常毒性;
取本品,加氯化钠注射液制成每1ml中含2600单位的溶液,依法检查按静脉注射法给药,观察24小时,应符合规定。
热原;
取本品,加灭菌注射用水制成每1ml中含2万单位的溶液,依法检查剂量按家兔体重每1kg注射0.5ml,应符合规定。
降压物质:
取本品,依法检查,剂量按大鼠体重每1kg注射3000单位,应符合规定。
无菌:
取本品,分别加入100ml0.9%无菌氯化钠溶液中,使溶解,用薄膜过滤法处理后,依国标检查应符合规定。
另取装量10ml的0.5%葡萄糖肉汤培养基6管,分别加入每1ml中含2万单位的溶液0.25~0.5ml,3管在30~35°
C培养,另3管在20~25°
C培养,应符合规定。
6.3HPLC法含量测定
分别从5个三角瓶中取100μl发酵液,过0.45μm孔径膜除去杂质,4摄氏度保存备用。
之后,加1%硫酸铁铵0.5ml,之后超纯水定容,过0.45μm膜除去杂质。
SymmetryshieldTMRP18C18柱(5μm,3.9mm×
150mm),流动相:
30℃检测波长330nm,进样体积:
2.477min。
7发酵罐设计
7.1发酵罐选型及尺寸
根据发酵物的发酵特性,选用机械涡轮搅拌通风发罐(通用式发酵罐),选用此种发酵罐的原因主要是:
历史悠久,资料齐全,在比拟放大方面积累了较丰富的成功经验,成功率高。
7.1.1发酵罐容积的确定
已知:
工作天数为330d/年,装料系数70%,单日放罐次数2次,年产量330t单日放罐次数由公式:
计算单罐放液体积:
G=300t
M=330day
μp=800u/mg
μm=25000u/ml
ηp=0.95
所以:
计算得知Vd=31m3
同时,查表确定罐体高径比为2,但考虑公称容积等因素,所以整体罐高为7.04m,柱高5.36