可编程序控制器是专为工业现场而设计的Word下载.docx
《可编程序控制器是专为工业现场而设计的Word下载.docx》由会员分享,可在线阅读,更多相关《可编程序控制器是专为工业现场而设计的Word下载.docx(8页珍藏版)》请在冰豆网上搜索。
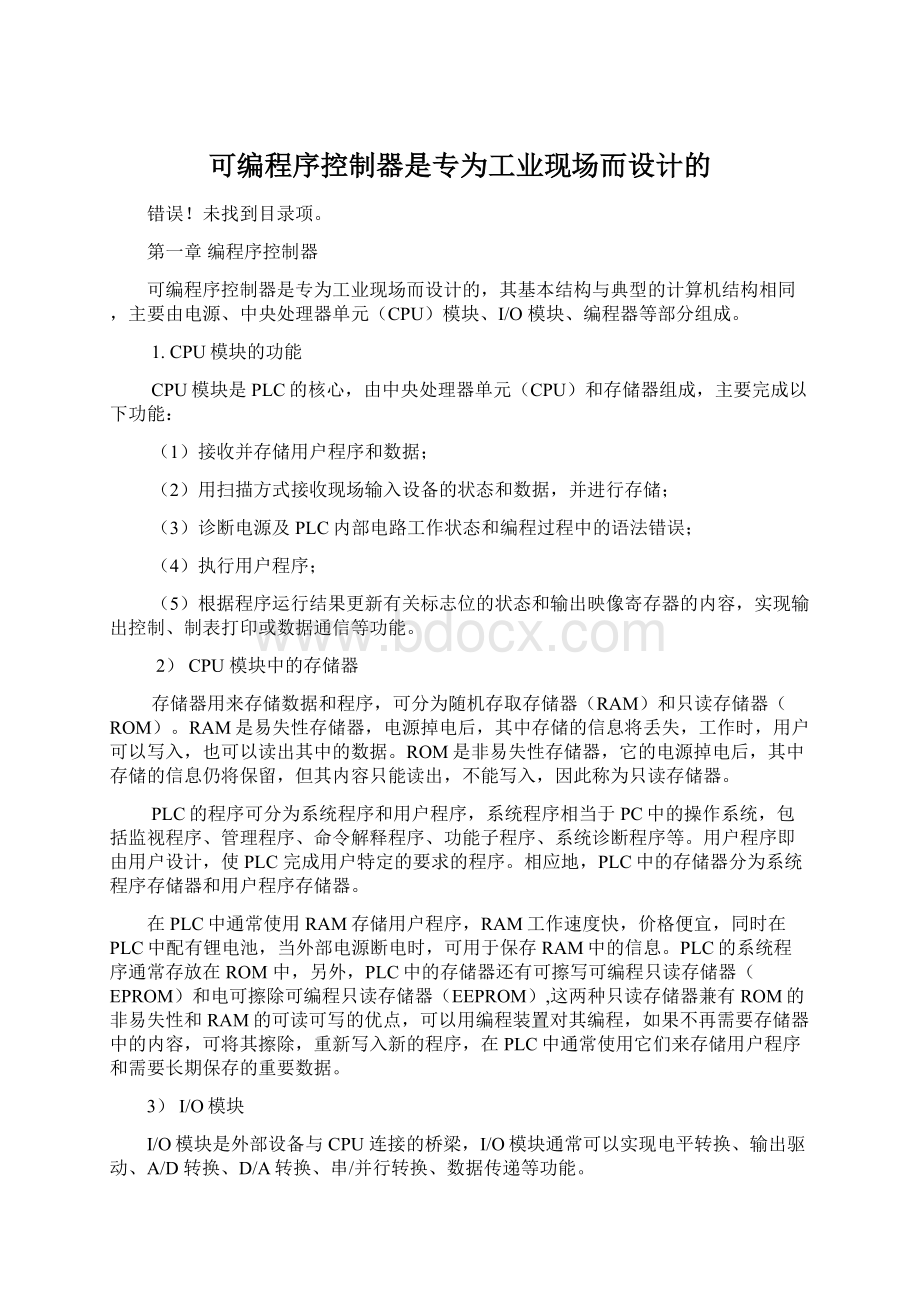
RAM是易失性存储器,电源掉电后,其中存储的信息将丢失,工作时,用户可以写入,也可以读出其中的数据。
ROM是非易失性存储器,它的电源掉电后,其中存储的信息仍将保留,但其内容只能读出,不能写入,因此称为只读存储器。
PLC的程序可分为系统程序和用户程序,系统程序相当于PC中的操作系统,包括监视程序、管理程序、命令解释程序、功能子程序、系统诊断程序等。
用户程序即由用户设计,使PLC完成用户特定的要求的程序。
相应地,PLC中的存储器分为系统程序存储器和用户程序存储器。
在PLC中通常使用RAM存储用户程序,RAM工作速度快,价格便宜,同时在PLC中配有锂电池,当外部电源断电时,可用于保存RAM中的信息。
PLC的系统程序通常存放在ROM中,另外,PLC中的存储器还有可擦写可编程只读存储器(EPROM)和电可擦除可编程只读存储器(EEPROM),这两种只读存储器兼有ROM的非易失性和RAM的可读可写的优点,可以用编程装置对其编程,如果不再需要存储器中的内容,可将其擦除,重新写入新的程序,在PLC中通常使用它们来存储用户程序和需要长期保存的重要数据。
3)I/O模块
I/O模块是外部设备与CPU连接的桥梁,I/O模块通常可以实现电平转换、输出驱动、A/D转换、D/A转换、串/并行转换、数据传递等功能。
(1)输入模块输入接口电路的典型结构如图2-2所示,其内部通常设有RC滤波电路和光耦合器。
RC滤波电路可以滤掉外部干扰脉冲防抖动,光耦合器可以防止强电干扰,起到隔离作用。
图2-2输入接口电路典型结构图
(2)输出模块将主机输出的信号转换成驱动外部设备工作的信号。
输出接口电路也采用电气隔离技术。
典型的输出接口电路如图2-3所示。
图2-3输出接口电路典型结构图
4)电源
PLC一般使用220V的交流电源或24V的直流电源。
内部的开关电源为PLC各模块提供5V及24V的直流电源。
5)编程器
PLC的编程器有两种:
一种是手持编程器,它由键盘、显示器和工作方式选择开关等部分组成,主要用于调试简单程序、现场修改参数及监视PLC自身的工作情况;
另一种是利用上位计算机中的专业编程软件,它主要用于编写较大型的程序,并能灵活地修改、下载安装程序及在线调试和监控程序,它的应用较前者更为广泛。
2.2.2PLC的应用领域
多年来,可编程控制器(以下简称PLC)从其产生到现在,实现了接线逻辑到存储逻辑的飞跃;
其功能从弱到强,实现了逻辑控制到数字控制的进步;
其应用领域从小到大,实现了单体设备简单控制到胜任运动控制、过程控制及集散控制等各种任务的跨越。
目前,PLC在国内外已广泛应用于钢铁、石油、化工、电力、建材、机械制造、汽车、轻纺、交通运输、环保及文化娱乐等各个行业,使用情况主要分为如下几类:
(1)开关量逻辑控制
取代传统的继电器电路,实现逻辑控制、顺序控制,既可用于单台设备的控制,也可用于多机群控及自动化流水线。
如注塑机、印刷机、订书机械、组合机床、磨床、包装生产线、电镀流水线等。
(2)工业过程控制
在工业生产过程当中,存在一些如温度、压力、流量、液位和速度等连续变化的量(即模拟量),PLC采用相应的A/D和D/A转换模块及各种各样的控制算法程序来处理模拟量,完成闭环控制。
PID调节是一般闭环控制系统中用得较多的一种调节方法。
过程控制在冶金、化工、热处理、锅炉控制等场合有非常广泛的应用。
(3)运动控制
PLC可以用于圆周运动或直线运动的控制。
一般使用专用的运动控制模块,如可驱动步进电机或伺服电机的单轴或多轴位置控制模块,广泛用于各种机械、机床、机器人、电梯等场合。
(4)数据处理
PLC具有数学运算(含矩阵运算、函数运算、逻辑运算)、数据传送、数据转换、排序、查表、位操作等功能,可以完成数据的采集、分析及处理。
数据处理一般用于如造纸、冶金、食品工业中的一些大型控制系统。
(5)通信及联网
PLC通信含PLC间的通信及PLC与其它智能设备间的通信。
随着工厂自动化网络的发展,现在的PLC都具有通信接口,通信非常方便。
今天的PLC在处理模拟量、数字运算、人机接口和网络的各方面能力都已大幅提高,成为工业控制领域的主流控制设备,在各行各业发挥着越来越大的作用。
第二章污水处理系统及可编程控制器介绍
2.1污水处理工艺流程
图2-1污水处理工艺流程图
整个污水处理工艺流程(如图2-1所示)大致如下:
污水首先进入回转式机械粗格栅,实现污水中较大颗粒悬浮物的栏截,保护水泵和其它机械免受损坏。
经过提升泵站提升泵输送,进入沉砂池。
在沉砂池前设细格栅,以实现污水中较小颗粒悬浮物的栏截。
沉砂池采用旋流式沉砂池,利用水力和机械搅拌造成的旋流,使泥砂和有机物分离,以达到除砂的目的,同时去除砂粒上粘的有机物。
经沉砂处理完成以后的污水进入分配井,通过二根总管向二个生化池输送。
上述过程就是以物理处理技术为主的第一级处理(如表2-1所示)。
从主工艺流程图可以看到污水处理的整个过程都能满足自动化控制,所有电机的运行都有现场与远程两种状态。
表2-1第一级处理
反应池A
曝气或搅拌
反应池B
沉淀池C
一级处理完成以后的污水进入组合交替式生物池。
组合交替式生物反应池有2组,每组2条处理线。
每组平均处理水量3.0万m3/d。
每条处理线的处理主体是由三个三格矩形池组成的组合反应池。
三个池互相连通,每个池中均设有供氧设备,采用充氧搅拌机曝气;
在两侧的三格矩形池内,设有固定出水堰及剩余污泥排放口,两侧池可作反应池,也可作沉淀池;
中间一只三格矩形池只用作反应池。
进入系统的污水,可通过进水闹门控制分周期分别进入三个三格矩形池中的任意一池。
运行过程中,有两个池处于生物处理阶段,而其中的一个侧池是处于沉淀状态,处理完成以后的水由固定堰排出,剩余污泥从池底排出。
一个完整的生物反应过程由下面两个阶段构成:
第一阶段:
污水从A池进水,A池作反应池,可以是厌氧、缺氧、好氧反应,污水经过A池的反应后,从连通渠至B反应池,B池也可以是厌氧、缺氧、好氧反应池,污水经过B池的反应后,从连通渠至C池,在第一阶段,C池作为沉淀池,经过A、B反应池处理的污水在C池中沉淀,出水由固定堰排出。
第二阶段:
经过一定时段后,关闭A池的进水闹,启B池的进水闹,此时,A池停止曝气,而污水从B池流向C池,经过一个短暂的过渡段后,关闭B池的进水间,开启C池的进水间,于是,污水从C池进水,该池作反应池,从连通渠至B反应池,再经连通渠至A池,此时A池作为沉淀池,处理出水由固定堪排出。
到此完成一个反应过程。
如此周而复始,这就是该处理工艺的运行过程。
3.1方案设计原则
本方案制定以设计图纸为基础,同时考虑污水处理厂地理位置分布及污水处理厂工艺流程特点,对电气自动化化控制系统的软硬件配置、网络系统的构成以及设备的选型配置方面按如下原则设计,使整个系统更加符合实际生产控制需求,具有更高的性能价格比。
(1)根据污水处理厂的工艺特点,考虑系统可靠,风险分散,本方案按照“集中监测,分散控制”的总原则对全厂自控系统进行设计和配置。
整体上自控系统由厂级中央监控系统和分布在各工艺流程工段的现场PLC控制站组成。
(2)在系统结构及网络方面,本方案主要按“分层、分级、安全可靠”的原则考虑。
现场控制分站采用施耐德(Schneider)公司的UnityPremium系列PLC系统,现场控制分站与高低压配电系统智能仪表以及工艺设备配套控制装置之间采用专用的MODBUS工业现场总线通讯,保证数据通讯的可靠性;
现场控制站与中央监控系统采用工业以太网通讯,保证数据通讯的高速性。
中央监控系统通过计算机图形界面,通过计算机图形界面,对整个污水处理厂的下端设备集中控制。
在现地层,可以通过现场控制分站的触摸屏进行手/自动化控制,对区域内工艺流程被控设备实现分区控制。
各层之间有一定的约束或协调关系,凡对整个系统有全局性的影响,需要广泛协调的监控功能由上一层完成,而局部性的监控功能则由相关的下一层来完成,下一层除了承担分配给它的功能外,还接受上一层的指导和制约,整个系统从上至下构成完善的二级监控体系。
(3)在系统软、硬件容量的配置上,本方案主要按“留有余量,易于扩展”的原则考虑。
已配置的系统卡件I/O点数及机架内空槽都有一定的备用容量,所有信号类型留有余量,保证在规模范围内由于工艺流程的变化引起的I/O的增加;
选择的PLC系统可方便的进行机架扩展,现场控制柜的结构设计也留有增加系统机架及相应控制较件的空间,以满足远期规模自控系统的改扩建。
(4)在系统软、硬件性能的配置上,本方案主要按“区别对待、先进适用、节约投资”的原则考虑。
污水处理自控系统及分析仪表等关键设备采用国际知名进口品牌产品,保证系统的可靠性。
其它国内产品质量可靠的产品,采用国内知名品牌产品,整个配置具有较高性能价格比,在目前及今后一段时间内保持一定水平的技术领先。
(5)针对污水处理厂许多工艺室外生产、地势较为空B广的特点,方案将考虑在相关供电回路、通讯线路以及室外仪表低电平信号回路均配置有高质量防雷模块,形成完善的防雷接地系统,可有效地防止因雷击造成设备损坏,使系统运行更加安全可罪。
(6)针对高压综合保护系统、低压多功能电力监测仪表系统以及工艺设备配套控制装置,将全厂将电气系统与自控系统统一在一个监控平台上,实现真正意义上的电、仪一体化。
3.2PLC控制站系统
整个控制系统采用施耐德(Schneider)公司的UnityPremiumPLC硬件平台和iFIX监控软件平台。
整个控制系统由现场PLC控制站和中央监控系统二级构成。
UnityPremiumPLC硬件平台(如图3-1所示)和iFIX监控软件平台作为工业控制领域的知名进口品牌,均支持MOBUS/TCP通讯协议,为现地PLC控制站和中央监控系统之间提供了无缝快速的工业以太网通讯连接,保证了整个系统构架的可靠性,同时也完全满足招标文件的要求。
控制网络主干为100M光纤冗余工业以太环网,中央交换机同样采用施耐德的ConneXium系列工业以太网交换机,通讯介质为光纤。
该系统完全能满足污水处理厂全厂设备及工艺参数的监视和控制要求。
由于系统具有真正的分层和分布式结构,可实现现场远程直接控制、远程全自动控制和手动控制等三种操作方式。
污水处理自控系统的设计及构造符合“集中监控、分散控制”原则,由二级组成控制网络:
第一级现场PLC控制站:
由5套分布在工艺流程中、基于施耐德(Schneider)公司的UnityPremiumPLC的现场控制站和相关在线检测仪表以及检测、执行设备组成。
根据工艺流程相关性及地理位置分布,这5套UnityPremiumPLC现场控制分站将分别设置在提升栗房站、细格栅及旋流沉砂池分控站、生化池分控站、脱水机房分控站以及消毒池分控站。
变根据工艺关联性原则。
依托于UnityPremiumPLC强大的通讯能力,变电所内高压综合保护装置及低压电量监测装置可通过通讯的方式接入生化池分控站,实现真正意义上的电仪一体化;
消毒机工艺配套控制系统通过以太网通讯的方式接入消毒池分控站,使全厂的工艺流程监控更加完善。
智能配电设备及工艺配套控制设备与各自的现场PLC控制站连接采用在工业上应用广泛且性能可靠的MODUBS现场总线。
MODBUS作为事实上的工业标准,为全球广大电气及自动化化仪表厂家接受_。
施耐德公司作为MODBUS通讯协议的创始厂家,其全系列PLC均将MODBUS作为标准接口,可快速、简单的与第三方设备实现通讯。
MODBUS具有全开放、可靠性高、成本低廉的特点,是远距离数据通讯的最佳选择,在城市供水、污水处理等行业的厂区内远程数据通讯有广泛的应用。
大量的电量、非电量数据采用通讯方式采集,在减少PLCI/O卡件数量,保护用户投资的同时,大大增加了系统的信息采集量。
各PLC现场控制分站内的UnityPremium系列TSXP573634MC型CPU内置了以太网口,比使用专门的以太网模块速度更快,成本更低。
通过该以太网口与分站以太网交换机一中央工业以太网交换机相连,各现场PLC控制分站与中央监控系统形成星形工业以太网结构,采用国际通用标准的MODUBS/TCP通讯协议以实现高速数据通讯。
第二级中央监控系统:
中央监控系统在厂办公楼中控室,由2台基于IFIX4.0SCADA系统监控软件及组态编程软件的运行工作站、1台基于SQLSERVER数据服务器、打印机、UPS、工业以太网交换机以及计算机操作台等设备构成。
生产操作人员可通过中央监控站对生产流程进行集中监控、管理,可实现车间现场层的无人值守。
2台运行工作站采用独立节点的配置模式,通过光纤工业以太环网与各现场PLC分站通讯。
任意一个节点故障不影响其它接点的正常工作,每个节点均可独立地担负全厂的监控任务,操作人员可在任意一台操作站上完成综合监视过程控制级的所有信息,进行显示,记录,数据处理,报表输出,并且可以按一定权限进行控制回路的组态和参数修改等操作。
依托于IFIX内嵌的SQL任务方式,任意一台运行工作站均可将系统的实时采集数据和历史数据存放在数据服务器中,以便日后查询。
同时在在厂长室和化验室各设置1台监控计算机,作为2台运行工作站的客户端,也可对全厂的工艺流程进行动态监视。
整个系统结构配置符合“集中监控、分散控制”原则,具有高度的可靠性、安全性、放性、可扩展性、可维护性且操作简单、维护诊断方便,满足污水处理厂全厂设备及工艺参数的监视和控制要求,符合现代污水处理厂自动化化发展方向。
全厂自控系统网络结构配置图如下:
图3-1总体硬件框架
PLC(如图3-2所示)分站系统设置在提升泵房配电间,主要完成粗格栅、进水泵房等构筑物设备的监控及相关检测仪表的供电。
主要包括分站PLC系统、及相应的通讯网络和通讯接口组件。
PLC分站系统采用施耐德公司PREMIUM系列TSXP573634MC型内置以太网的高端PLC,包括机架、电源、CPU、I/O、通讯接口等模块。
I/O卡件及机架空槽均按设计图纸中的实际需求并留有一定的备用容量,保证在规模范围内由于工艺流程的变化引起的I/O的增加;
模块化结构可方便的进行机架扩展,现场控制柜的结构设计也留有增加系统机架及相应控制较件的空间。
其基本功能包括:
采集粗格栅、螺旋输送压榨机、提升泵等设备的控制方式、运行状态及故障报警的开关量信号;
采集各粗格栅液位差、提升泵房集水井液位、硫化氧气体浓度以及提升泉房各泵的电流及出口流量等仪表的检测模拟信号;
粗格栅的手/自动化控制,自动化方式下根据粗格栅液位差或时间控制粗格栅的开启/关闭以及相应的螺旋输送压榨机启/停;
提升菜的手/自动化控制,自动化方式下根据提升泵房集水井液位实现多台提升泵的自动化轮询工作;
实时传送所有检测参数和设备的各种运行状态到中央监控系统执行中央监控系统计算机下达的控制指令与中央监控系统计算机的工业以太环网通讯,实现远程监。
图3-2PLC系统结构图
3.3污水处理系统的硬件设计
3.3.1TSXP573634