非回转体零件深孔加工机床专用辅具的Word文档格式.docx
《非回转体零件深孔加工机床专用辅具的Word文档格式.docx》由会员分享,可在线阅读,更多相关《非回转体零件深孔加工机床专用辅具的Word文档格式.docx(15页珍藏版)》请在冰豆网上搜索。
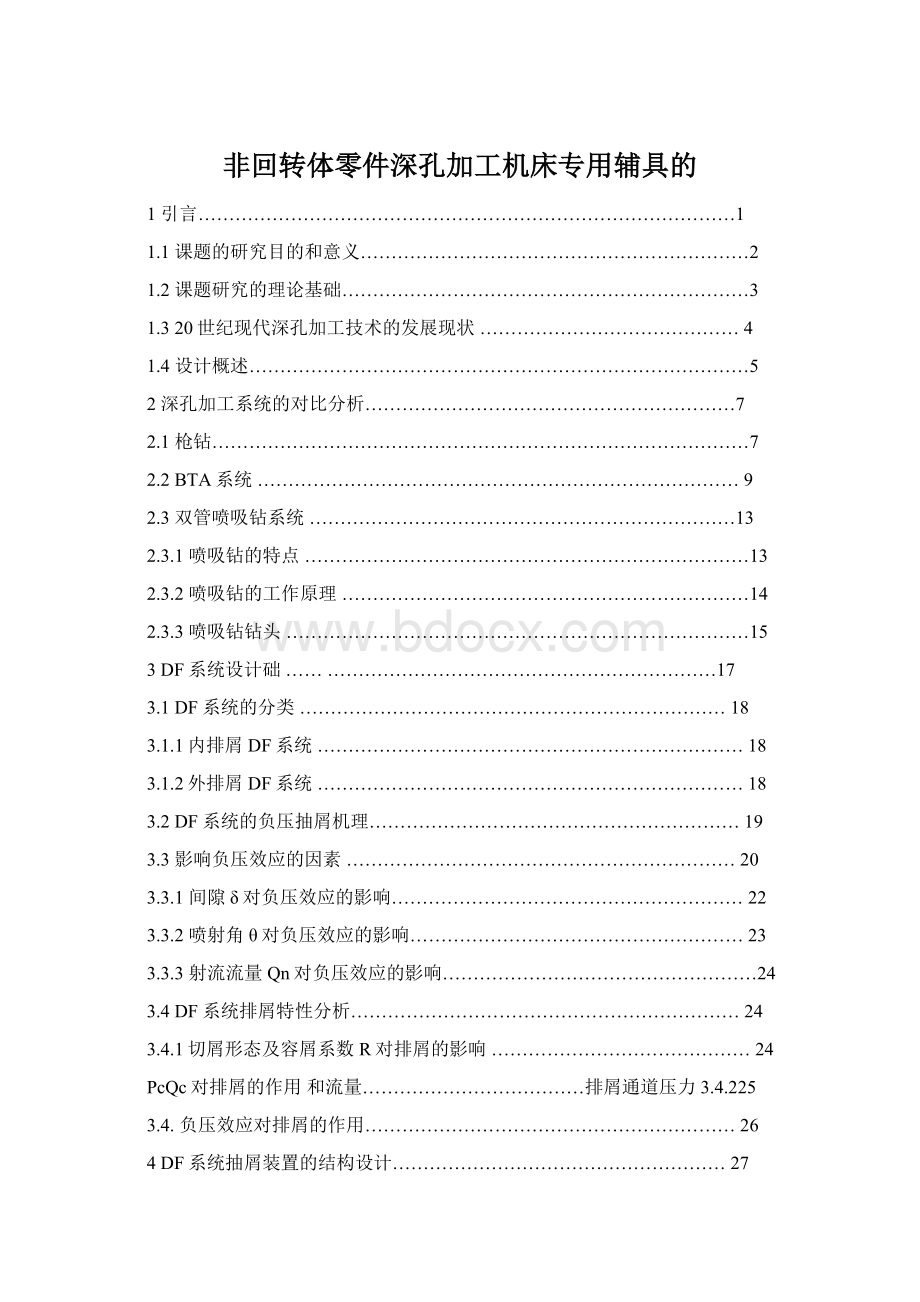
PcQc对排屑的作用和流量………………………………排屑通道压力3.4.225
3.4.负压效应对排屑的作用……………………………………………………26
4DF系统抽屑装置的结构设计………………………………………………27
4.1输油器的设计………………………………………………………………28
4.1.1输油器的结构设计…………………………………………………………28
共Ⅱ页第Ⅱ页.
4.1.2输油器标准件的选取………………………………………………………30
4.2抽屑器的设计………………………………………………………………32
4.2.1抽屑器的结构设计…………………………………………………………32
4.2.2抽屑器标准件的选取………………………………………………………35
5结论…………………………………………………………………………39
参考文献………………………………………………………………………40
致谢……………………………………………………………………………42
1引言
制造业中,通常将长径比超过5的圆柱孔称为“深孔”,结构中带有深孔的零件称为“深孔零件”,对加工深孔零件为主件的机械装备称为“深孔类装备”,对专门用于加工深孔的装备(如深孔刀具、深孔加工机床、用于深孔加工机床的专用辅具等)则称之为“深孔加工装备”。
深孔在功能上与浅孔有本质区别。
相对于深孔而言,长径比小于5的普通圆柱孔(又称“浅孔”),是构成各种机械零件的最常见的要素之一。
浅孔的主要功能是连接、定位、支承、导向和在近距离内传输流体,也可用以实现特定的工艺功能(如工艺孔、工艺槽等)或设计目的(如密闭容器、平衡、改善装备的力学功能等)。
从早期管式火器的发明到近代枪炮的产生,虽已证明人类认识到深孔零件的特殊功能(密闭容器、能量转化、精确地向远距离传输介质、能量和信息),但是从实体金属材料上钻出深孔并进一步加工成精密深孔,[1]。
20世纪其难度则远远大于浅孔加工20年代以前,扁钻、半圆形单刃钻、麻花钻等浅孔刀具曾经长期用于加工深孔。
由于浅孔加工刀具无法解决连续自动排屑、刀具自导向和自动冷却润滑三大难题,故工效很低、加工质量差、废品率也高,加工成本十分昂贵。
直到20世纪30~40年代,枪钻和内排屑深孔钻问世之后,深孔加工技术才步入现代化的发展进程。
深孔加工技术中所遇到的技术问题是多种多样的,而且是层出不穷的,但无论在生产实践中或新技术的研究工作中,排屑问题始终是首当其冲的大课题。
从非连续自动排屑钻头到枪钻的出现,是解决深孔刀具连续自动排屑问题的首次突破。
可以认为内排屑深孔钻是通过排屑方式的改变才得以实现的。
双管喷吸钻及DF系统的问世,从根本上说是对BTA实体钻所存在的排屑功能缺陷进行改进而做出的不共Ⅱ页第Ⅱ页.
断探索的结果。
毫无疑问,排屑问题必然成为深孔加工过程中必须首先加以突破的第一课题,加之目前深孔加工领域内所应用的深孔加工设备绝大多数是基于回转体深孔件的加工,而相对庞大的市场需求来说,用于非回转体深孔件加工的深孔设备却寥寥无几。
这势必会促进对深孔加工辅具——高效的排屑装置的研究和开发。
而本课题的任务就在于设计出基于DF系统和BTA深孔钻头的非回转体工件的深孔加工专用辅具。
1.1课题的研究目的和意义
深孔工件一般分为回转体工件和非回转体工件,深孔工件的加工方法一般分以下三种:
工件旋转刀具进给式;
钻头旋转进给工件固定式;
工件与刀具相对旋转式。
对于各种非轴类、非管类等非回转体工件的深孔加工,以及在各类非回转体工件表面上加工坐标孔等,多采用第二种加工方法。
非回转体工件的深孔加工就是在DF深孔加工系统上采用钻头旋转进给、工件固定式加工方法,在非回转体工件上加工出工件设计所要求的深孔。
DF系统是基于BTA深孔钻(属内排屑深孔钻类)的深孔加工系统,除了抽屑装置以外,其余的要素(工件、输油器、钻头和钻杆)与BTA钻完全相同。
它具有一系列胜于外排屑深孔系统的优势,如钻杆刚度大,钻头与钻杆可快速拆卸,进给量大,适于钻大直径深孔;
在所用的机床设备方面,DF系统比BTA钻适应性更大等等。
但其致命的缺陷是排屑通道不足,且孔径越小,孔的长径比越大,越容易产生堵屑故障。
结合设计任务书的要求可以明确,这里需要设计出基于BTA深孔钻的用于加工非回转体深孔的DF系统专用辅具。
从加工过程中所采用的深孔钻系统以及采用的加工方式两个角度来考虑,可以确定以下设计目的:
(一)设计出在非回转体工件的深孔加工过程中能够较好地实现自动连续排屑、冷却和润滑的供油系统和抽屑系统(主要由前装置输油器和后装置抽屑器组成);
(二)由于采用钻头旋转进给、工件固定式的深孔加工方法,这就要求设计出能够驱动钻头旋转进给的动力头和控制系统。
从本质上讲,用于加工非回转体深孔的DF系统是在传统的DF系统结构基础上的改进,但同样是以输油器和排屑器所组成的抽屑装置作为其主要组成部分。
它采用一台结构简单的抽屑装置取代了双管喷吸钻的一根内管和一套连接器,使双管喷吸钻的结构得以简化,同时,它还在原来的结构基础上增设一台电机,用于驱动钻杆旋转进给,这是非回转体深孔加工DF系统结构设计上的意义所在。
另外,这种装置还继承了DF系统在负压效应方面的设计思路:
第一是喷吸间隙Δ的取值范围为0.2~0.5mm;
其次,前油路流量取为总流量的2/3,而后油路流量取为总流量的1/3,这些基本参数是不变的。
综观目前国内的深孔加工市场,绝大多数深孔装备和深孔辅具均是面向回转体共Ⅱ页第Ⅱ页.
深孔件加工的,关于回转体深孔加工的技术相对来说也是比较成熟的。
与之形成鲜明对比的是非回转体深孔加工设备的极度匮乏,和非回转体深孔加工技术的巨大空白。
随着我国现代化制造业的飞速发展,非回转体深孔件的加工需求亦日趋增长,为了补充非回转体深孔加工技术的空缺,弥补市场的需求,必须投入一定的人力和财力对这个特定的领域进行研究。
1.2课题研究的理论基础
非回转体零件深孔加工专用辅具设计的主要任务是要设计出一套能够实现钻头旋转进给,自动连续排屑的抽屑装置,在DF系统上采用钻头旋转进给、工件固定式加工方法加工出工件设计所要求的深孔。
这就要求必须首先理解深孔钻削的基本原理。
图1.1DF系统示意图
DF是英文DoubleFeeder的缩写。
DF的实质是喷射钻与BTA内排屑钻相结合的一种深孔钻削加工系统,既在被加工零件钻孔端面配置一个以推压方式提供冷却液的油密封装置。
也就是传统的BTA深孔钻削加工系统,在其后部放置一个能够产生喷吸效应的装置。
这样,前部的BTA系统产生推力,后部的喷射系统产生吸力。
由于推拉的双重排屑作用,使冷却液的流速加快,单位时间内的流量增加,排出切屑的能力就越大。
特别适用于小直径深孔钻削加工。
尤其在可加工性差的材料,不易断屑的材料加工中应用此系统更能体现出其优越性。
DF系统负压效应产生的机理是:
切削液经负压装置高速射入排屑通道,与向外共Ⅱ页第Ⅱ页.
流动的切削液混合进行能量交换。
排屑通道内向外流动的切削液在射流喷嘴口处的能量转换区获得能量,切削液流速得到提高。
这样,排屑通道内向后流动的切削液在能量转换前后的流速产生梯度,具有不同的能量,形成压力差。
在能量转换区前的切削液压力低,在能量转换区后边的压力高,因而产生真空区,即负压区。
在负压区切削液的流动速度加快,提高了排屑效果。
1.320世纪现代深孔加工技术的发展现状
20世纪现代深孔加工技术的发展与贡献,可归纳为:
(1)枪钻、内排屑深孔钻的发明,使精密枪炮管的大批量流水生产成为可能,同时也为枪炮功能的不断完善提供了重要物质基础;
(2)深孔钻削技术的现代化,为深孔零件用于各种机械装备的开发奠定了基础。
至20世纪末,已经形成跨越各个经济部门的“深孔类装备”的特殊装备门类,例如:
石油和煤炭采掘装备中的抽油泵和液压支架,大型发电机转轴,工程机械、塑料机械和液压机械中的液压缸,传感器及仪表关键件,纺织机械、饲养机械关键件,冶金、重化工、核电站、材料加工机械等行业中的加热器、冷却器、裂解管道等等。
由于深孔所具备的特殊功能的不可替代性,可以预料深孔[9];
(3)二战以前,枪钻、内排屑深孔钻主要用于相类装备将会得到更广泛地应用对封闭的军工行业,深孔加工机床高度专用化,深孔刀具由兵工厂自行制造。
为适应二战后“军转民”的客观形势,瑞士、瑞典、西德、日本等工业国开始建立面对广大市场需要的专业化、现代化深孔加工装备制造行业。
在20世纪60~80年代期间,实现了深孔机床的一系列技术更新(如数控深孔钻床、深孔加工中心等)和深孔钻具的硬质合金化、内排屑深孔钻的错齿结构、机夹可转位涂层刀片用于BTA刀具等。
为使不具备深孔钻床的许多中小企业能够广泛采用BTA又称内排屑深孔加工刀具,瑞典SANDVIK/coromant公司于60年代推出了一种在改装设备上采用的双管喷吸钻(EjectorDrilling)装备。
在此基础上,日本一家冶金公司于70年代后期进一步推出了一种基于BTA刀具的、只需要单层钻杆的喷吸钻系统(DF系统)。
但是由于这两种喷吸钻的功能有限(前者只能用于孔深1000mm以内工件的大批量生产,后者也不适用于孔径Φ15以下和多品种生产),所以未能从根本上改变BTA刀具与枪钻以孔径大小为界的格局,故在深孔钻削领域中形成“平分秋色”的总格局;
(4)基于20世纪航空航天工业的发展,难加工材料、复杂形体、微型元器件的加共Ⅱ页第Ⅱ页.
工制造,促成了特种加工技术的发展。
自20世纪50年代以来,已有多种特殊加工技术在深孔加工中得到较广泛的应用,例如电解加工、电解珩磨、成形管电板电解加工、电火化加工、电子束加工、电液流加工等。
特种加工在深孔加工中的应用,在难加工材料、特殊复杂型面、特小(Φ1mm以下)、特深小孔、异形截面深孔、超精、超光、超薄、超小零件的深孔加工方面具有机械加工方法所难于取代的作用,同时也为深孔加工技术开辟了一个全新的发展领域。
20世纪微电子技术、数字化技术、材料技术、信息技术的迅猛发展,为制造技术(特别是装备制造技术)、生产模式、管理模式的不断进步注入了新的活力。
市场的激烈竞争,要求生产装备通用化、多功能、自动化、柔性化,以适应产品多品种、批量小、更新快、技术含量高、生产成本不断降低的新形势。
与传统制造技术发展规律不同的是,深孔加工技术的现代化,必须以其核心技术(排屑、冷却润滑和工具自导向)的突破为前提,在此基础上进一步实现设备的通用化、多功能、自[17]。
动化、柔性化
20世纪80年代以来,深孔加工技术发展中出现的危机,根源在于装备的核心技术落后和其价格居高不下,其突出表现是:
(1)内、外排屑机床、刀具互不兼容。
为了加工不同直径的深孔,企业必须同时拥有内、外排屑两类设备工具和相应操作人员,同时导致深孔加工装备利用率低下,企业经济效益不佳。
(2)深孔加工机床主要用于钻孔。
深孔加工技术中缺少各种与钻孔相配套的后续深孔加工手段。
(3)回转体深孔零件与非回转零件,在同一深孔加工机床上不可兼容。
(4)深孔钻削对操作技术、加工条件有苛刻的要求。
堵屑、刀具损伤、加工致废等事故易于发生。
仅靠设备的自动化、数控化、柔性化改造,无法从根本上解决问题。
深孔加工装备价格之所以居高不下,主要原因在于其市场销量的萎缩、西方工业国生产成本过高以及深孔加工装备自身存在的结构和工艺性缺陷;
20世纪80年代后,国际经济格局的变化,特别是我国和亚洲新兴工业国的经济振兴,导致发达工业国制造业的重心转移;
由于少数工业发达国家已对深孔加工装备市场形成垄断,而发展中国家一时又无力开发出更先进的实用技术,导致深孔加工技术及装备[1]。
的市场新需求与供给之间出现长期严重失衡
1.4设计概述
本文从深孔加工技术的发展历程着手,导出DF系统较其之前出现的种种深孔加工系统的优势,以及其在现代深孔加工中的重要地位;
继而简要介绍了DF系统的工作机理和设计过程中所需要注意的几个要点,并指出了非回转体深孔件的DF系统与回转体深孔件的DF系统在功能上和结构设计中的不同点;
最后在设计理论明确和设计手段充分的基础之上,结合设计课题的要求完成对非回转体深孔件DF系统专用辅具(输油器和抽屑器)的结构设计。
2深孔加工系统的对比分析
根据所采用的冷却、排屑系统的不同,可将深孔加工系统分为以下几类:
枪钻系统、BTA系统、双管喷吸钻系统、DF系统,以及新近问世的SIED系统。
这些系统除用于与之对应的钻头进行钻削外,亦可以用于其它深孔刀具的切削加工,如深孔镗削、铰削和珩磨等。
在上述各类深孔加工系统中,枪钻属于外排屑深孔钻,其余几种均属于内排屑深孔加工系统。
枪钻适用于加工小孔径的深孔,并且具有良好的自导向功能。
与枪钻相比,内排屑深孔加工系统则有以下优点:
(1)由于切屑是由钻杆内部排出,切屑
不会划伤已加工孔表面,已加工表面质量较好,排屑流畅;
(2)钻杆为圆形截面,其扭转刚度及弯曲强度比枪钻高,因而进给量大,生产效率高;
(3)排屑空间大,冷却润滑液的压力比枪钻低,一般为0.5~3MPa。
因此对密封及供油系统的要求比枪钻低;
(4)加工范围广。
内排屑深孔钻既可用于较大孔径的深孔加工,也可用于较小直径如Φ6mm)的深孔加工;
(5)内排屑深孔钻既可用于钻孔,也可在一定的余量范围内用于扩孔。
2.1枪钻
枪钻(gundrill)产生于1930年,是最早用于实际生产的一种单边刃切削外排屑深孔钻头。
因其产生于枪管和小口径炮管制造,故名枪钻。
最早的枪钻有钻头(切削部分)、钻杆和钻柄(driver)三段焊为一体,钻头切削刃偏离轴线一侧的钻尖区分出内、外两个切削刃。
沿钻头和钻杆的全长上有一个前后贯通的V形排屑槽。
钻杆由薄壁无封钢管轧出V形槽而成。
钻头上与V形排屑槽的对侧有通孔,与钻杆的空腔相连,构成切削液供入通道。
枪钻曾演变出不同的一些异形结构和双边刃外排屑钻头。
但各种双边刃外排屑钻头并不具有枪钻的自导向功能,从严格意义上讲不应该称为枪钻,但可列入外排屑深孔钻门类。
枪钻系统属于外排屑方式,其结构如图2.1所示,主要由中心架、扶正器、钻杆联结器和冷却润滑油路系统组成。
其中中心架辅助机床卡盘用于装夹工件;
扶正器主要用于钻头人钻时导向,并提供向外排屑的通道;
尾架用于夹持钻头柄部,支
2.1枪钻系统图承钻削扭矩和轴向力。
枪钻系统的工作原理是:
切削液通过尾架上输油入口进入钻型槽中排出。
V杆内部,到达钻头头部进行冷却润滑,并将切除的切屑从钻头外部的由于切屑由钻头和钻杆外部排出,容易擦伤已加工孔表面,其加工质量要低于内排深孔加工。
<20mm)(屑方式的系统。
该系统主要用于小直径一般Φ
2.2枪钻的结构图所示。
钻头材2.2)三部分组成,如图柄部、钻杆枪钻由头部12和传动部3(料有高速钢和硬质合金两种,并与钻杆焊接为一体。
目前常用硬质合金枪钻。
为了进行校直、在焊接后,常采用如图定位准确,2.3所示的焊口形式。
保证焊接牢固,精磨工序,以保证头部与柄部的同轴度。
枪钻的这种不可拆卸结构带来了一些本质性的缺陷,如重磨时拆卸、安装不便,钻头报废时钻杆不能重复使用,因而也增大共Ⅱ页第Ⅱ页.
了刀具成本等。
钻头直径越大,钻杆越长,上述弊端就越显著。
这是枪钻不适用于加工Φ35mm以上深孔的一个重要原因。
图2.3枪钻钻头焊口形式
2.2BTA系统
由欧洲跨国研究机构“钻镗孔与套料加工协会”(BoringandTempanning
Association,缩写为BTA)对德国人Beisner发明的一种单边内排屑自导向深孔钻进行改进后推出的三种规范化深孔钻头的总称(BTA实体钻、BTA扩钻、BTA套料钻)。
由于枪钻不太适用于较大直径深孔的加工,Beisner于20世纪40年代初参照枪钻单边刃切削及自导向的两大基本特点,推出一种由钻杆和钻头外部供入切削液,从钻头和钻杆内腔排出切屑的内排屑深孔钻头。
由于钻头体和钻杆为空心圆住体,以方牙螺纹互相连接,易于拆装更换,从而成为钻大直径深孔的理想钻头。
Beisner钻头的切削刃与枪钻十分相似,只有一个出屑口,专用于实体钻孔。
后经BTA改进,成为规范化的双出屑口错齿BTA钻,并同时推出了结构功能类似的一种BTA扩钻和一种BTA套料钻,总称为BTA钻。
BTA系统属于内排屑方式。
其结构如图2.4所示。
主要由中心架、输油器、钻杆联结器和冷却润滑油路系统组成。
BTA系统中的输油器与枪钻系统中的扶正器功共Ⅱ页第Ⅱ页.
能不同,输油器除了具备导向扶正功用外,还提供了向切削区输油的通道。
BTA系统的工作原理是:
切削液通过输油器从钻杆外壁与已加工表面之间的环形空间进
图2.4BTA系统
入,到达刀具头部进行冷却润滑,并将切屑经钻杆内部推出。
该系统使用范围广泛,适用于深孔钻削、镗削、铰削和套料,但受到钻杆内孔排屑空间的限制,主要用于[24]。
12mm的深孔加工直径Φ>单刃内排屑深孔钻(BTA钻)的结构如图2.5所示。
钻头的切削部分主要由内刃、外刃、钻尖、导向块以及排屑孔组成。
刃形和切削过程与枪钻相似,但切屑从深孔钻内部排屑孔中排出。
钻头圆周上布置有两个导向块,切削刃一般磨有两个或更多的分屑台阶。
出于冷却液和切屑的排出都集中从一个排屑口进入钻杆,相对就保证了冷却液的流量和压力,有利于排屑。
与多刃错齿内排屑深孔钻比,所受的径问力及扭矩较大,导向块的磨损较严重;
所需的功率较大,一般只适用于中小直径的深孔加工。
单刃内排屑深孔钻结构简单,制造容易、刃磨及重磨方便,它所适用的孔径范围为6~65mm,最大可达100mm;
孔的长径比可达100,最大达250;
加工精度达IT28~IT10级,孔表面粗糙度为Ra3.2~0.8μm。
对于直径为6~12mm的小直径内排屑深孔钻,为便于刀块的制造与焊接,可以将硬质合金刀块做成“T”型整体,焊在空心钢管上,“T”型刀块的主刃与导向块连成一体。
也可采用两块硬质合台分别焊在钻杆上,形成切削刃和导向块。
直径d<50mm的单刃内排屑深孔钻,常采用焊接0式结构,刀片和导向块都直接焊在刀体上。
直径大于50mm的,则多采用机夹式结构。
钻头结构图2.5BTA单刃内排屑深孔钻仅有一个排屑口,为便于分屑和排屑,必须将切削刃磨成分屑阶梯刃。
钻头直径越大,分屑阶梯刃的数量就愈多,刃磨工作量及难度也愈大;
钻头焊接后的残余应力容易产生焊接缺陷。
整体式刀片结构不仅硬质合金耗量大,而且不能针对刀刃各处的具体切削状态合理选择刀片材料。
单刃钻头的径向力较大,扭矩较大,容易产生打刀、扭钻现象,同时导向块受到的压力大,容易磨损。
钻)切削部分的切削力分布及切削扭矩的变化与单刃单刃内排屑深孔钻(BTA基本相似。
当钻削开始时,钻头通过导向套或工件的引导孔引)枪钻外排屑深孔钻(与钻头间有间隙,钻刃在径向力的作用)(或引导孔2.6导钻削,见图。
由于导向套下,将钻头压向导向套的一边,使钻头与导向套之间一边有间隙,另—边无间隙。
则导向块当导向块一进入已加工孔中,I~Ⅱ段,如开始时钻出的孔小于钻头直径,一方面与孔壁摩擦挤光,同时又把切削刃挤向外侧,使孔径扩大至最终尺寸。
由于共Ⅱ页第Ⅱ页.
这一时刻(Ⅴ段)钻头的摩擦扭矩迅速增大到最大,钻头常常会突然产生抖动,切削刃和导向块容易损坏。
通常在工件的入口端会出现喇叭口,其大端尺才约等于导向套的孔径。
图2.6BTA钻切入工件过程中扭矩的变化
相对于单刃内排屑深孔钻而言,还有一种BTA钻叫多刃错齿内排屑深孔钻。
多刃错齿内排屑深孔钻是将相错开的刀齿分别置于钻头排屑槽的两侧,径向错齿排列有3~7个刀齿(小直径取小值),各刀齿间相错开且留有少量搭接量。
圆周上还分布两个导向块,刀体与钻杆用方牙螺纹联接,见图2.7
3DF系统设计基础
20世纪70年代中期,日本冶金有限公司利用流体喷射所产生的负压效应,设计出一种深孔钻抽屑装置,装设在BTA钻进刀座位置,从钻杆末端产生负压以促进排屑。
这种系统所用的深孔刀具BTA刀具完全相同,其输油器BTA钻也完全相同,只是将切削液分出另外一支用以产生喷流。
因此,这种深孔抽屑装置与BTA钻的单一油路相比成为一种与之相区别的双向供油系统(DoubleFeederSystem,简称DF系统),因而命名为DF系统。
DF技术于1980年在日刊《机械技术》上相继报道后,由于其抽屑装置比较简单,刀具成本低于双管喷吸钻,将现有内、外排屑深孔钻床或车床进行简易改进后即可采用。
DF系统特别适合于钻Φ16~Φ30mm的深孔,具有比BTA钻排屑状况好,比枪钻、双管喷吸钻投资少、成本低等优势,因而在我国的应用比较广泛。
到了80年代,DF原理披再次被推广应用到外排屑钻削系统中。
该系统不仅可以应用到枪钻床上,解决了小直径深孔的排屑、密封等难题,而且还可以应用到普通立式钻床和普通车床上,为解决深孔麻花钻钻深孔的冷却、排屑问题开避了一个新途径。
枪钻为内排屑深孔钻,钻杆的结构决定了其刚性不足,只能适用于小孔径的零件加工,加工效率低,加工质量较差。
但枪钻的密封问题容易解决。
BTA系统的产生是深孔加工技术的一大突破。
BTA系统的特点是冷却润滑液由钻杆和已加工孔壁之间的环形通道输入切削区,而后带着切屑一起由钻杆排屑通道排出。
钻杆刚性好,可钻直径60mm以上的实心孔;
由于切屑从钻杆内排出,避免了切屑划伤孔