安庆石化炼油厂工艺流程及其危险性分析汇总Word格式.docx
《安庆石化炼油厂工艺流程及其危险性分析汇总Word格式.docx》由会员分享,可在线阅读,更多相关《安庆石化炼油厂工艺流程及其危险性分析汇总Word格式.docx(23页珍藏版)》请在冰豆网上搜索。
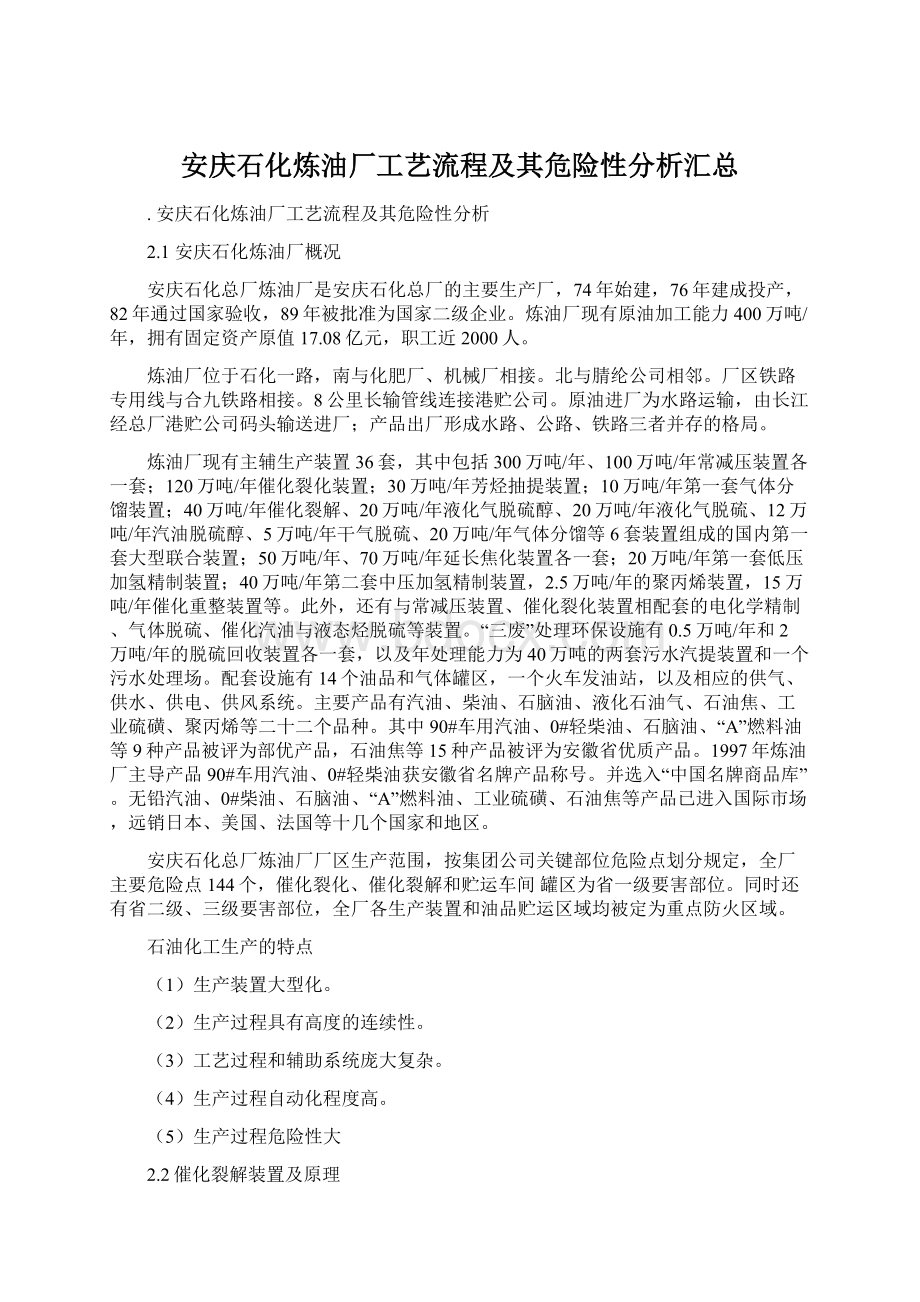
(5)生产过程危险性大
2.2催化裂解装置及原理
催化裂解车间是世界上首套以重质油为原料,生产气体轻烯烃的工业生产装置车间由40万吨/年催化裂解装置,20万吨/年液化气脱硫装置,20万吨/年液化气脱硫醇装置,12万吨/年汽油脱硫醇装置,5万吨/年干气脱硫装置,20万吨/年气体分馏装置组成。
装置于1995年投产,经两次大修改造后。
现处理能力达65万吨/年。
关键设备有加热炉、反应器、再生器、分馏塔、丙烯塔C-703、丙烯塔C704等共39台。
催化裂解工艺是在催化工艺基础上发展起来的石油炼制新工艺,其目的产品是丙系烯,因此在反应过程中控制氢转移反应以控制烯烃饱和,而且高的反应温度及低的催化剂活性对氢转移反应不利,同时裂解反映同属于平行-顺序反应,增加放映深度及反应时间有利于中间产物的进一步裂化,提高丙烯收率。
此外,在裂解过程中催化剂的使用也相当重要,选用好催化剂,才能多产生焦及低分子化合物,减少生焦,尽可能少消耗烯烃多产出丙烯。
2.3反应、再生部分
催化裂解反应温度为510-540℃,反应压力为0.07-0.10MPa。
其反应是以催化反应为主,反应热较大,需要7-10的剂油比。
为了降低油气分压,需在反应器内通入25%(相对总进料)的水蒸气。
催化裂解原则工艺流程与催化裂化基本相似。
1.原料预热系统
裂解主要原料为直馏蜡油,新鲜原料由装置外送入原料油缓冲罐D-203,用泵P-201从D-203抽出。
首先进原料——油浆换热器E-201/1-4换热至300℃左右,分两路进原料加热炉F-201升温至≯380℃后,随雾化蒸汽进入喷嘴,进料喷嘴共四个,对称分布。
2.反应系统
反应进料与来自再生器的约700℃高温催化剂接触,在提升管内立即汽化并反应,反应油气、注入的水蒸气与未转化的原料油携带催化剂经过分布板一并进入流化床反应器进一步反应。
与此同时,在催化剂上沉积一部分芳烃缩合物——焦炭。
携带催化剂的反应油气经四组两级旋风分离器分离,分离出的油气去分馏塔,回收下来的积存有焦炭的催化剂经料腿流入反应器床层下部。
然后经过汽提段,用过热水蒸汽进行汽提,脱去夹带油气的待生催化剂经斜管流入烧焦管。
反应压力由气体压缩机(K-301)入口管线上的压力调节器控制。
正常操作时,压力控制为0.07-0.10MPa。
非正常情况下,可用入口放火炬阀控制。
反应温度由再生斜管单动滑阀开度控制,正常操作时,反应床层温度控制为510-540℃。
3.再生系统
来自汽提段的待生催化剂,与经循环斜管自再生器来的约700℃高温催化剂混合,以提高再生起始温度,一般控制在600℃以上。
混合物的催化剂在烧焦管内烧焦(约50%的焦炭)。
烧焦空气由主风机(K-101)供给,经辅助燃烧室(F-101),预混合烧焦管提升待生及再生催化剂与烧焦产生的烟气并流向上,进入再生器床层,根据需要,灵活通入部分新鲜空气用以进一步少掉残存的焦炭。
在再生器稀相床层中,烟气携带的催化剂大量沉积下来。
未沉降的催化剂与烟气一起进入五组两级旋风分离器。
分离出的烟气进入外集气室,通过再生器顶部双动滑阀,然后进入余热锅炉发生中压蒸汽,使烟气温度降至200-240℃去烟囱放空。
分离出的催化剂返回再生器密相床,再生后催化剂进入外脱气罐,脱去催化剂携带的烟气,然后经再生斜管进入提升管反应器。
再生器压力由再生器顶部双动滑阀控制,正常操作时,压力控制在0.1-0.14MPa,温度为700℃。
上述工艺过程中的主要操作条件如下:
反应部分
再生部分
操作压力
操作温度
进料温度
催化剂循环量
剂油比
总注汽量占总进料
回炼比
预提升段衬里内径
进料喷嘴以上提升管内径
提升管入口线速
提升管出口线速
反应床层空速
反应器密相床层线速
反应器密相床层内径
反应器稀相内径
反应器稀相线速
催化剂汽提蒸汽
汽提段内径
汽提段线速
催化剂质量流率
汽提段停留时间
旋风器入口线速
一级入口
二级入口
0.08MPa
565-580℃
330-380℃
700-750t/h
10.77-11.54t/h
25%
0.3
700mm
1160mm
7.32m/s
15.1m/s
2.5-4.0h-l
1.0m/s
4.930m
6.9m
0.508m/s
2861-3230kg/h
3.0m
0.227m/s
1768.2-2262kg/m2*min
2.04min
18.64m/s
21.372m/s
操作压力
操作温度
焦炭含氢量
烧焦流率
烟气中co2/co比
烟气中氧气密度
主风流率
来往风指标
总烟气流率
预混合烧焦管内径
预混合烧焦管主风量
预混合烧焦管出口线速
密相仪表观气速
稀相床表观气速
旋风分离器入口线速
烧焦强度
密相床内径
稀相床内径
1.1-0.14MPa
700℃
10%
4000Kg/h
∝
2%
805.34NM3/min
12.08NM3/Kg
842.8NM3/min
1960mm
513NM3/min
4.0m/s
0.498m/s
19.663m/s
22.56m/s
80.168Kg/t*h
5500mm
8000mm
石油化工企业的生产过程中压力的平衡相当重要,压力不平衡,产生超压或负压状况时就有可能发生物料流动停止、倒流,损坏设备,甚至导致恶性爆炸事故的发生。
因此在反再的工艺过程中需保持以下的压力平衡:
反—再工艺压力平衡
再生线路
推动力
阻力
再生器顶压力
床层压头
脱气罐压头
催化剂立管
合计
0.2MPa
0.0105MPa
0.022MPa
0.0315MPa
0.264MPa
反应器顶压力
预提升管
提升管
提升管出口分布板
床层压降
再生滑阀压降
0.18MPa
0.015MPa
0.01MPa
0.034MPa
待生线路
反应器压力
床层静压
汽提段
待生立管
0.04MPa
0.0422MPa
0.2722MPa
再生器压力
预混合烧焦管
待生滑阀压降
0.03MPa
0.0317MPa
反再过程中的有以下主要的危险点:
反应器再生器:
内部装有高温催化剂,充满易燃易爆的高温烃类油气。
若再生器床层稀密相严重超温,处理不当或不及时,将会损坏催化剂和设备,若因操作失误,将导致催化剂倒流,大量空气进入反应器,甚至造成火灾爆炸事故。
提升管:
提升管出口温度应控制在520℃-545℃。
反应温度过高会引起反应深度过大,使生焦增大,再生器温度容易超温,若注风量不足,会引起碳堆积造成事故,若反应温度过低,原料油中的重组分不能完全汽化,会引起待生催化剂带油,引发事故。
预混合烧焦管:
提高预混合烧焦管压降,可提高预混合烧焦管烧焦效果,但预混合烧焦管压降过大,会引起烧焦管噎噻,主风机压力超高,造成主风机飞动,两路催化剂循环中断。
反应切断进料。
加热炉:
加热炉炉膛温控≯800℃,操作温度300℃-400℃之间。
炉管由于长期高温作用,腐蚀冲刷、局部过热。
过高的油气线速,极易导致炉管减薄穿孔,引起火灾或爆炸。
如因事故熄火,瓦斯在烟道中聚焦极易发生爆炸。
在开工点炉过程中,如操作程序错误或处理不当也易发生爆炸事故。
加热炉火源也是装置唯一明火点,如某一部位大量油气泄露,扩散至炉区将发生恶性爆炸事故。
余热锅炉:
主要是利用高温烟气与各受热面管内介质进行对流换热使水蒸气汽化,最终形成高温高压蒸汽。
余热锅炉超温超压、满水缺水等等都可以引发恶性事故。
2.4分馏部分
来自反应器的油气进入分馏塔(C-201)下部。
分馏塔共有3层舌型塔板,底部设有8层冷却洗涤用的人字挡板。
油气自下而上通过人字挡板,经分离后塔顶得到裂解气体、粗汽油、侧线抽出裂解轻油,塔底为裂解重油(油浆)。
为了提供足够的内回流和使塔的负荷比较均匀,分馏塔分别建立了四个循环回流。
塔顶温度为110℃,压力为0.04-0.06MPa,分馏塔顶油气先经分馏塔顶前冷器(E-203/1-4)冷至80℃,进入分馏塔顶回流罐(D-201),冷凝的液体经分馏塔顶回流泵(P-203)抽出,大部分作为分馏塔顶冷回流送入分馏塔第30层塔板,另一部分与D-201中未冷凝的气体一起进入分馏塔顶后冷器(E-204/1-5)冷至40℃后进入塔顶油气分离器(D-202)。
在D-202中分离出的粗汽油用粗汽油泵(P-202)送至吸收塔。
分出的富气进入气体压缩机,经压缩冷却,再经吸收脱吸,脱硫及气体分馏等过程,将C3、C4等气体产物进行分离回收,得到所需化工原料或民用燃料。
D-201、D-202分出的含硫污水排至含硫污水处理系统。
裂解轻油和贫吸收油(温度155-160℃)自分馏塔第18层板自流入轻油汽提塔(C-202),经水蒸气汽提后用轻柴油泵(P-204)抽出,经贫吸收油-富吸收油换热器(E-202/1.2),然后再进贫吸收油冷却器(E-204/1.2)冷却至40℃,绝大部分作为贫吸收油送至吸收稳定部分,少部分为裂解轻油送出装置作轻柴油调合组分。
富吸收油在E-202中换热升温至100-130℃返回分馏塔第21层塔板。
第一中断回流由分馏塔(C-201)第16层塔板,用第一中断回流泵(P-205)抽出送至脱吸塔(C-302)做塔底重沸器(E-301)的热源,然后进第一中断回流冷却器(E-206/1.2)用循环水冷却至150℃返回分馏塔(C-201)第18层塔板。
第二中断回流(包括回炼油)由分馏塔(C-201)第二层塔板自流入回炼油罐(D-204),温度为330℃,然后用第二中断回流泵(P-206)抽出,分三路,一路作为第二中断循环回流,做稳定塔(C-304)底重沸器(E-304)的热源,然后返回分馏塔(C-201)第五层塔板,另一路作为内回流返回分馏塔第二层塔板上,再一路为回炼油在原料加热炉(F-201)对流室出口与原料油汇合一并进入辐射室,加热至330-380℃进入提升管进料喷嘴。
循环油浆经油浆泵(P-207/1-3)从C-201底部抽出后,先与原料-油浆换热器(E-201/1-4)换热,再经循环油浆冷却器(E-207)冷却至275℃后,一部分返回C-201人字挡板上部,另一部分返回人字挡板下部。
少部分送至油浆冷却器(E-208)冷至90-100℃作为裂解重油送出装置。
在设计中亦考虑了油浆回炼,以满足反应、再生热平衡。
尽量做到再生器不打燃烧油,使两器达到自身热平衡。
在上述整个分馏过程中,分馏装置是重点设备,因此分馏塔的各项操作条件相当重要。
具体如下表:
塔顶温度
110℃
冷回流
13.3%
进料温度
560℃
吸收油
1.68%
塔底温度
330-350℃
第一中断回流
16.723%
塔顶压力
第二中断回流
21.657%
塔底压力
0.06MPa
油浆回流
46.64%
汽提蒸汽
200Kg/H
搅拌蒸汽
400Kg/H
分馏塔回流取热
1985.5Kcal/h*10000
小计
100%
分馏过程中存在大量的危险性,对此过程中的重要危险设备的工艺参数的监控,原料油经裂解反应后,其反应产物就要经过容器进行油气分离油气分离器液位的控制非常重要。
液位过高会导致反应系统增压,而且气压机入口富气带油会损坏气压机,甚至有爆炸危险,液位过低,将引起稳定系统操作波动。
原料油油浆换热器:
定期对原料油-油浆换热器进行巡检。
看其介质温度、压力是否超高,设备、管线、阀门等有无泄露,保温是否完好,消防设施是否完好。
在分馏的过程中,油浆泵相当重要。
油浆泵出口压力为1.0-1.2MPa。
温度为330-350℃,电流120-130A,定期检查泵出入口位置是否正确;
备用泵有无预热;
泵管线,阀门等有无泄露,油箱冷却与投用情况;
封油压力,温度是否正常;
润滑油油箱液面、油质情况,下水道、排污口是否畅通;
消防设施是否完好。
2.5气体压缩机和吸收稳定部分
1.气压缩及冷却系统
从分馏部分D-202来的富气被气体压缩机K-301两段加压到1.5MPa。
富气经一段压缩后压力为0.32MPa,温度为110℃。
为防止气体在冷却器形成胺盐结晶和硫腐蚀,为此,在冷却前注入洗涤水。
气体经冷却后(温度为40℃)进入气压机一级出口中间凝液罐(D-303)把凝缩油、水和不凝气分离,然后不凝气进入第二压缩,压力升至1.4MPa温度约为115℃。
送至气压机出口前冷器(E-305/1.2)前与从脱吸塔(C-302)来的脱吸气混合送入E-305/1.2冷却至50℃,与用吸收塔底泵(P-307)送来的饱和吸收油混合进入压缩机出口后冷器(E-306/1.2)冷至40℃进入气压机出口油气分离器(D-301),在D-301分离罐中把凝缩油和不凝气分离,然后分别去脱吸塔、吸收塔。
为了防止氮化物、硫化物对后面设备的腐蚀,在E-305/1.2前后注入软化水洗涤,污水从D-301排至含硫污水脱油脱气罐。
2.收脱吸系统
吸收塔顶操作压力1.3MPa,从D-301来的压缩富气进入吸收塔(C-301)底部,自下而上逆流与来自D-202粗汽油和从补充吸收剂泵(P-304)送来的稳定汽油(补充吸收剂)逆流接触。
气体中的C3及C3以上的组分被吸收,剩下含有少量吸收剂的气体(贫气)离开塔顶去再吸收塔(C-303)。
为了取走吸收时放出的热量,在吸收塔用P-302/1-4分别抽出四个中断回流经冷却器(E-307/1-4)冷却后再返回吸收塔。
在D-301中平衡汽化得到的凝缩油经泵(P-301)抽出经脱吸塔进料-汽油换热器换热至70℃进入脱吸塔(C-302)顶部,脱吸塔顶操作压力1.5MPa,温度71℃,脱吸塔底部由脱吸塔底重沸器(E-301)提供热量用分馏部分第一中断回流作热载体。
以脱除吸收C2组分,脱乙烷汽油送至稳定系统。
贫气从C-301顶出来进入C-303,操作压力为1.22MPa。
与从分馏部分来的贫吸收油(轻柴油)逆流接触,以脱除气体中夹带的轻汽油组分。
吸收后的气体(干气)送至脱硫装置,富吸收油则靠C-303的压力自流到E-202/1.2与贫吸收油换热后,再返回分馏塔(C-201)进行蒸脱。
3.汽油稳定系统
脱乙烷汽油从脱吸塔底出来,用稳定塔进料泵送至稳定塔进料换热器(E-302/1.2)和脱丁烷汽油换热后进入稳定塔(C-304)。
塔的操作压力1.27MPa,顶温59℃左右,丁烷和更轻的组分从塔顶馏出,经过塔顶冷凝冷却器(E-308/1-4)冷却后进入回流罐(D-302),液体产品-液化气用稳定塔顶回流泵P-305升压,大部分作为C-304的回流,另一部分作为化工原料送至脱硫装置。
脱丁烷汽油自塔底靠本身压力依次进入E-303/1.2、E-302/1.2,换热后进入稳定汽油冷却器(E-309/1.2),被冷到40℃。
一部分作为补充吸收剂,用泵P-304压送至吸收塔,期于部分送往脱硫装置。
稳定塔底重沸器(E-304)的热源,来自分馏部分第二中断回流,为稳定塔提供热量。
在整个的吸收稳定部分中有脱吸塔、稳定塔、再生器等重要设备。
很好的控制这些设备在生产工艺过程中的各种数据相当重要,具体如下:
吸收塔
稳定塔
40℃
59.3℃
1.3MPa
215℃
富气流率
23284kg/h
1.27MPa
补充吸收剂量
43218kg/h
151.3℃
回流比
2
重沸器负荷
5000.4kw
脱吸塔
再生塔
70℃
45℃
1.4MPa
1.22MPa
109-110℃
贫气流率
7654kg/h
2970.9998kw
吸收剂流率
22000kg/h
稳定吸收的过程中对液化气冷凝气的监控相当重要,该装置具体工艺参数及监控要点是:
压力1.05-1.15MPa、温度30-45℃,设备管线、阀门等有无泄露;
可燃性气体报警仪是否完好,操作时防止冻伤、防止爆炸,消防设施是否完好。
2.6气、液化气脱硫
1.干气脱硫系统
来自催化裂解装置的干气,先进入稳定干气分液罐(D-401),在罐内除去携带的重烃,然后进入干气脱硫塔(C-401)的下部。
在塔内干气自下而上流动,在通过每层塔盘处与从塔上部流下的贫胺液逆流接触进行传质,干气中的酸性物质H2S、CO2被胺液吸收,使干气逐渐被净化,最后干气通过塔顶部的升气管进入溶剂分离段,将携带的胺溶液进行自然分离,净化干气从塔顶出来进入净化干气分液罐(D401/1)以进一步除去携带的胺液后去全厂燃料气系统。
2.液化气脱硫
由裂解装置拉的含有H2S的稳定液化气进入液化气脱硫原料罐(D-402),用液化气脱硫进料泵(P-403)抽出升压进入液化气脱硫塔(C-402)下部与塔上部下来的贫胺液逆流接触,液化气中的H2S被胺液吸收使液化气得到净化,净化液化气在塔上部分离出携带的溶剂后靠自压进入液化气脱硫醇部分。
3.溶剂再生系统
从干气脱硫塔C-401和液化气脱硫塔C-402底部流出的富胺液,溶解了少量轻烃,经塔底液位控制阀减压后进入富液闪蒸罐(D-403),在低压下闪蒸出溶解的轻烃,经压控阀去全厂火炬系统。
闪蒸后的富液泵(P-402)抽出经贫富液换热器(E-401)与从溶剂再生塔(C-403)底来的高温贫胺液换热,富液经换热升温后进入溶剂再生塔(C-403)上部,C-403是富胺液解吸塔,塔底温度约121℃,塔顶压力约0.1MPa,解吸所需热量由再生塔底重沸(E-404)提供热源,所用蒸汽是经减压减温到0.3MPa、143℃的低压蒸汽。
进入再生塔的胺液自上而下流动,随温度升高而分解放出酸性气(H2S和CO2)同时使溶液得到再生,再生后的贫胺液从塔底流出,先与富液换热,然后进到贫液冷却器(E-402)用水冷却至40℃后进入溶剂贮罐(D-404)中贮存。
解吸出来的酸性气体从再生塔顶逸出经再生塔冷凝器(E-403)冷凝后进到再生塔顶回流罐(D-405),罐内的冷凝液体通过再生塔顶回流泵(P-404)抽出做C-403塔顶回流,以控制塔顶温度,回流罐内的酸性气体经压力控制阀去硫磺回收装置。
溶剂贮罐(D-404)内的贫胺液用干气脱硫贫液泵(P-401)和液化气脱硫贫液泵(P-405)抽出升压后分别泵入C-401和C-402上部做干气、液化气脱硫溶剂,另外,根据稳定液化气含酸气量的情况,液化气脱硫所用贫液也可先与液化气一起经静态混合器(M-401)混合脱除酸性气后进塔,此时脱硫塔(C-402)将起到净化液化气与胺液沉降器分离作用。
为了防止溶剂发泡,对在进入气体吸收塔C-401和C402前的贫液都设有阻泡剂罐(D-410/1.2)。
装置内的凝结水收集在蒸汽汽液分离罐(D-407)中,凝结水自压至气分装置凝结水罐(D-708)。
装置内设有溶剂补充系数,将桶装醇胺液加至溶剂配制回收罐(D-414)中,用溶剂配制回收泵(P-406)抽送或用非净化风压送至溶剂贮罐(D-404)中。
装置内设有溶剂回收系统,由于装置停工时系统内会残余少量溶剂,须自压进入溶剂配制回收罐(D-414)中,然后用溶剂配制回收泵抽送或用非净化风压送至溶剂贮罐(D-404)中。
4.汽油脱硫醇部分
由催化裂解来的稳定汽油分两路进入汽油预碱液混合器(M-501/1.2)与循环碱液混合后一起进入汽油预碱洗分离罐(D-501)经沉降分离出碱液后汽油从罐顶溢出进入汽油脱硫醇抽提塔(C-501)下部,自下而上与塔顶流下的含催化剂碱液在装有FG格栅填料的填料层中逆向接触,汽油中的硫醇与碱反应生成溶于碱液的硫醇钠盐,含盐碱渣从塔底流出经汽油脱硫醇碱液加热器(E-501)用低压蒸汽加热至60℃左右进入碱液氧化混合器(M-502)与进入混合器的空气充分混合,然后进入碱液氧化塔(C-502),在催化剂作用下,空气中的氧与硫醇钠反应生成不溶于碱液的二硫化物,同时碱液得以再生,二硫化物随碱液一起从C-502顶部流出进到汽油抽提碱液分离罐(D-502),碱液由汽油抽提碱液循环泵(P-501)抽出泵入C-501上部循环使用。
D-502中的二硫化物定期用二硫化物泵(P-504)送入装置,D-502中的废气经压控阀送往全厂火炬系统。
经抽提后的汽油从C-501顶部流出与来自混合氧化碱液循环泵(P-502)的循环碱液和空气一起进入混合氧化混合器(M-503),混合进入混合氧化塔(C-503),汽油中尚未脱除的硫醇在塔内继续被氧化成二硫化物,然后从塔顶流出进入氧化碱液分离罐(D-503)中沉降分离,罐底碱液由P-502抽出循环使用,废气排入全厂火炬系统,精制汽油由罐顶进入汽油砂滤塔(C-504)自上而下通过砂滤层,除掉其杂质及破乳后进入精制汽油碱