第2章 炼钢过程的物料平衡和热平衡计算Word文件下载.docx
《第2章 炼钢过程的物料平衡和热平衡计算Word文件下载.docx》由会员分享,可在线阅读,更多相关《第2章 炼钢过程的物料平衡和热平衡计算Word文件下载.docx(23页珍藏版)》请在冰豆网上搜索。
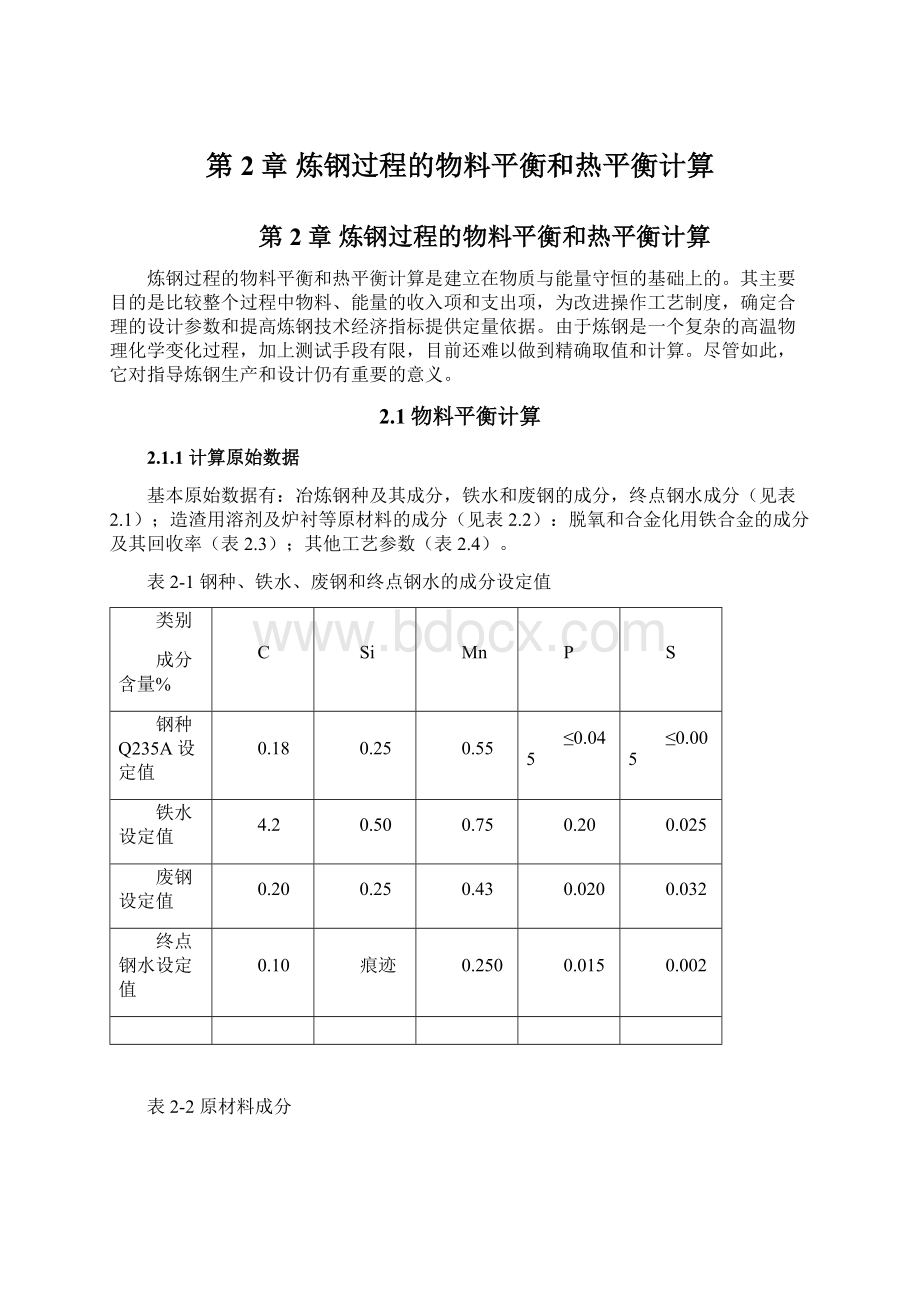
36.40
0.80
25.60
1.00
36.20
炉衬
1.20
3.00
78.80
1.40
14.00
焦炭
0.58
81.50
12.40
表2.3铁合金成分(分子)及其回收率(分母)
成分含量/回收率/%
Al
Fe
硅铁
—
73.00/75
0.50/80
2.50/0
0.05/100
0.03/100
23.92/100
锰铁
6.60/90
0.50/75
67.8/80
0.23/100
0.13/100
24.74/100
注:
上表中的C中10%于氧生成CO2。
表2.4其他工艺参数设定值
名称
参数
终渣碱度
萤石加入量
生白云石加入量
炉衬蚀损量
终渣∑(FeO)含量
(按向钢中传氧量ω(Fe2O3)=1.35ω(FeO)折算)
烟尘量
喷溅铁损
ω(CaO)∕ω(SiO2)=3.5
为铁水量的0.5%
为铁水量的2.5%
为铁水量的0.3%
15%,而ω(Fe2O3)/∑ω(FeO)=1/3,即ω(Fe2O3)=5%,ω(FeO)=8.25%
为铁水量的1.5%(其中ω(FeO)为75%,ω(Fe2O3)为20%)
为铁水量的1%
渣中铁损(铁珠)
氧气纯度
炉气中自由氧含量
气化去硫量
金属中[C]的氧化产物
废钢量
为渣量的6%
99%,余者为N2
0.5%(体积比)
占总去硫量的1/3
90%的C氧化成CO,
10%的C氧化成CO2
由热平衡计算确定,本计算结果为铁水量的13.7%,即废钢比为12.05%
2.1.2物料平衡基本项目
收入项有:
铁水、废钢、溶剂(石灰、萤石、轻烧白云石)、氧气、炉衬蚀损、铁合金。
支出项有:
钢水、炉渣、烟尘、渣中铁珠、炉气、喷溅。
2.1.3计算步骤
以100Kg铁水为基础进行计算。
第一步:
计算脱氧和合金化前的总渣量及其成分。
总渣量包括铁水中元素氧化、炉衬蚀损和计入溶剂的成渣量。
其各项成渣量分别列于表2.5、2.6和2.7。
总渣量及其成分列于表2.8中。
第二步:
计算氧气消耗量。
氧气实际耗量系消耗项目与供入项目之差。
见表2.9。
表2.5铁水中元素的氧化产物及其渣量
元素
反应产物
元素氧化量(㎏)
耗氧量(㎏)
产物量(㎏)
备注
[C]→{CO}
4.10×
90%=3.690
4.720
8.610
[C]→{CO2}
10%=0.410
0.640
0.88
[Si]→{SiO2}
0.500
0.571
1.071
入渣
[Mn]→{MnO}
0.145
0.645
[P]→{P2O5}
0.185
0.239
0.424
[S]→{SO2}
0.03×
1/3=0.008
0.008
0.016
[S]+(CaO)→(CaS)+(O)
2/3=0.015
-0.008
0.034(CaS)
[Fe]→{FeO}
0.897×
56/72=0.685
0.195
0.897
入渣见表2-8
[Fe]→{Fe2O3}
0.48×
112/160=0.377
0.144
0.490
合计
6.330
7.034
成渣量
3.942
入渣组分之和
①由CaO还原出的氧量;
消耗的CaO量=0.020×
56/32=0.035kg。
表2.6炉衬蚀损的成渣量
炉衬蚀损量/㎏
成渣组分/kg
气态产物/kg
耗氧量/㎏
C→CO
C→CO2
C→CO,CO2
0.3
(据表2-5)
0.004
0.009
0.236
0.005
0.3×
14%×
90%×
28/12=0.088
10%×
44/12=0.015
(90%×
28/12+10%×
44/12)=0.062
0.258
0.103
0.062
表2.7加入溶剂的成渣量
加入量/㎏
CaS
O2
0.5(据表2-4)
0.003
0.028
0.001
0.440
白云石
2.5(据表2-4)
0.910
0.905
5.76
5.080
0.150
0.147
0.075
0.036
0.011
0.006
合计
5.992
0.793
0.108
0.044
1.155
7.593
①石灰加入量计算如下:
由表4.6~4.8可知,渣中已含(CaO)=-0.026+0.004+0.002+0.910=0.890㎏;
渣中已含(SiO2)=1.071+0.009+0.028+0.020=1.128㎏。
因设定的终渣碱度R=3.5;
故石灰的加入量为:
[RΣω(SiO2)-Σω(CaO)]/[ω(CaO石灰)-R×
ω(SiO2石灰)]=3.95/(88.66%-3.5×
2.70%)=4.99kg
②(石灰中CaO含量)-(石灰中S→CaS消耗的CaO量)。
③由CaO还原出来的氧量,计算方法同表2-6的注。
表2.8总渣量及其成分
炉渣成分
MnO
FeO
元素氧化成渣量/kg
0.497
0.897②
0.541
0.034
3.979
石灰成渣量/kg
4.396
0.135
0.130
0.007
5.471
炉衬蚀损成渣量/kg
生白云石成渣量/kg
1.595
萤石成渣量/kg
0.495
总成渣量/kg
5.132
1.263
1.009
0.112
0.973
0.543
0.434
0.041
10.869
①
质量分数/%
50.82
14.44
8.72
0.95
4.21
8.25
5.00
3.73
3.53
0.35
100.00
①总渣量计算如下:
因为表2-9中除(FeO)和(Fe2O3)以外总渣量为:
5.996+1.704+1.029+0.112+0.497+0.440+0.416+0.041=9.249Kg,而终渣Σω(FeO)=15%(表2.4),故总渣量为10.235÷
86.75%=10.681Kg。
②ω(FeO)=10.681×
8.25%=0.881Kg。
③ω(Fe2O3)=10.681×
5%-0.040-0.005-0.008=0.481Kg。
表2.9实际耗氧量
耗氧项/Kg
供氧项/Kg
实际氧气消耗量/Kg
铁水中元素氧化消耗量7.034
炉衬中碳氧化消耗量0.062
石灰中S与CaO反应还原出的氧化量(表2.7)0.002
烟尘中铁氧化消耗量0.340
炉气自由氧含量0.060
7.766-0.002+0.041=7.805
合计7.766
合计0.002
①炉气N2(存在于氧气中,见表2.4)的质量,详见表2.10。
第三步:
计算炉气量及其成分。
炉气中含有CO、CO2、N2、SO2和H2O。
其中CO、CO2、SO2和H2O可由表2.5~2.7查得,O2和N2则由炉气总体积来确定。
现计算如下。
炉气总体积V∑:
式中Vg—CO、CO2、SO2和H2O各组分总体积,m³
。
本设计中,其值为6.598×
22.4/28+2.310×
22.4/44+0.020×
22.4/64+0.011×
22.4/18=7.864m³
;
GS—不计自由氧的氧气消耗量,Kg。
其值为:
7.691+0.062+0.34=8.093Kg;
VX—石灰中的S与CaO反应还原出的氧气量(其质量为:
0.001Kg);
99—由氧气纯度99%转换得来;
0.5%—炉气中自由氧含量。
表2.10炉气量及其成分
炉气成分
炉气量/Kg
体积/m³
体积分数/%
CO
8.698
6.958
79.76
2.652
0.891
17.77
SO2
1.06
0.01
0.012
0.21
0.040①
0.057①
N2
0.057
0.071②
0.70
11.465
6.617
①炉气中O2的体积为6.617×
0.5%=0.033m³
质量为0.033×
32/22.4=0.047kg。
2炉气中N2的体积系炉气总体积与其他成分的体积之差;
质量为0.046×
28/22.4=0.058kg。
第四步:
计算脱氧和合金化前的钢水量。
钢水量Qg=铁水量-铁水中元素的氧化量-烟尘、喷溅、和渣中的铁损
据此可以编制出未加废钢、脱氧与合金化前的物料平衡表2.11。
2.11未加废钢时的物料平衡表
收入
支出
项目
质量/kg
%
质量/Kg
铁水
100.00
86.48
钢水
92.614
79.23
4.99
4.98
炉渣
10.87
10.19
炉气
9.04
7.81
生白云石
2.50
2.16
喷溅
0.86
0.26
烟尘
1.30
氧气
7.805
5.69
渣中铁珠
0.71
0.61
113.072
115.81
计算误差为(115.63-115.81)/115.63
100%=-0.15%。
表2.12废钢中元素的氧化量及其成渣量
元素氧化量/kg
耗氧量/kg
产物量/kg
进入钢中的量/kg
13.7×
0.08%×
90%=0.012
0.028(入气)
10%=0.001
0.004(入气)
0.25%=0.034
0.039
0.0510
0.435%=0.025
0.1047
0.005=03.001
0.009%×
1/3=0.0013
0.0013
0.0026入气)
[S]+(CaO)→(CaS)+[O]
2/3=0.0026
-0.0013
0.0059(CaS)
0.077
0.066
13.7-0.077=13.623
成渣量/kg
0.1660
第五步:
计算加入废钢的物料平衡。
如同“第一步”计算铁水中元素氧化量一样,利用表2.1的数据先确定废钢中元素的氧化量及其耗氧量和成渣量(表2.12),再将其与表2.11归类合并,遂得加入废钢后的物料平衡表2.13和表2.14.
表2.13加入废钢的物料平衡表(以100Kg铁水为基础)
收入
支出
项目
铁水
83.54
钢水
90.944+13.623=104.567
79.81
废钢
13.7
3.39
炉渣
10.681+0.113=10.794
9.97
石灰
4.81
炉气
11.465+0.0346=11.5
7.54
萤石
0.42
喷溅
0.83
轻烧生白云石
2.09
烟尘
1.25
炉衬
0.641
氧气
7.085+0.066=7.87
129.86
120.02
计算误差为(119.71-120.02)/119,71
100%=-0.26%。
表2.14加入废钢的物料平衡表(以100Kg(铁水+废钢)为基础)
质量/kg
87.95
91.43
12.05
9.52
4.40
10.15
0.44
2.20
1.32
0.56
6.94
115.04
115.33
第六步:
计算脱氧和合金化后的物料平衡。
先根据钢种成分设定值(表2.1)和铁合金成分及其烧损率(表2.3)算出锰铁和硅铁的加入量,再计算其元素的烧损量。
将所得结果与表2.14归类合并,即得冶炼一炉钢的总物料平衡表。
锰铁加入量
为:
=
硅铁加入量
铁合金中元素的烧损量和产物量列于表2.15
表2.15铁合金中元素烧损量及其产物量
烧损量/kg
脱氧量/Kg
成渣量/Kg
炉气量/Kg
入钢量/Kg
0.51×
6.60%×
10%=0.003
0.010
0.015(CO2)
90%=0.030
67.80%×
20%=0.069
0.089
80%=0.277
0.50%×
25%=0.001
75%=0.002
0.23%=0.001
0.13%=0.001
24.74%=0.126
0.073
0.031
0.091
0.410
0.38×
2.50%×
100%=0.011
20%=0.0004
0.0005①
0.0005
80%=0.002
73.0%×
25%=0.0694
0.0793
0.149
75%=0.208
0.05%=0.0002①
0.03%=0.0001①
23.92%=0.0908
0.0798
0.0894
0.172
0.301
总计
0.153
0.12
0.247
0.711
脱氧和合金化后的钢水成分如下:
可见,含碳量尚未达到设定值。
为此需要在钢包内加焦炭粉增碳。
其加入量W1为:
焦粉生成的产物如下:
炭烧损量/Kg
耗氧量/Kg
气体量/Kg
成渣量/Kg
碳入钢量/Kg
0.06×
81.50%×
25%=0.012
0.037+0.05×
(0.58+5.52)%=0.047
0.05×
12.40%=0.007
81.50×
0.75%=0.037
由上述计算可得冶炼过程(即脱氧和合金化后)的总物料平衡表2.16。
表2.16总物料平衡表
82.62
92.71
79.74
3.35
9.77
10.11
4.76
7.51
0.41
0.82
2.06
1.23
6.94①
5.58
锰铁
0.51
硅铁
0.38
0.36
焦粉
0.05
116.32
116.60
计算误差为(114.06-115.25)/114.06×
100%=-1.04%。
①可近似认为(0.102+0.016)的氧量系出钢水时二次氧化所带入的氧量。
2.2热平衡计算
2.2.1计算所需原始数据
计算所需基本原始数据有:
各种入炉料及产物的温度(表2.17);
物料平均热容(表2.18);
反应热效应(表2.19);
溶入铁水中的元素对铁熔点的影响(表2.20)。
其他数据参照物料平衡选取。
表2.17入炉料及产物的温度设定值【3】
表2.名称
入炉物料
产物
铁水①
废钢
其他原料
温度/℃
1320
25
与钢水相同
1450
1纯铁熔点为1536℃
表2.18物料平均热容
物料名称
生铁
钢
矿石
固态平均热容/kJ·
(kg·
K)-1
0.745
0.699
1.047
0.996
熔化潜热/kJ·
kg-1
218
272
209
液态或气态平均热容/kJ·
0.837
1.248
1.137
表2.19炼钢温度下的反应热效应
组元
化学反应
△H/kJ·
kmol-1
[C]+1/2{O2}={CO}氧化反应
-139420
-11639
[C]+{O2}→{CO2}氧化反应
-418072
-34834
[Si]+{O2}→{SiO2}氧化反应
-817682
-29202
[Mn]+1/2{O2}=(MnO2)氧化反应
-361740
-6594
2[P]+5/2{O2}=(P2O5)氧化反应
-1176563
-18980
[Fe]+1/2{O2}=(FeO)氧化反应
-238229
-4250
2[Fe]+3/2{O2}=(Fe2O3)氧化反应
-722432
-6460
(SiO2)+2(CaO)=(2CaO·
SiO2)成渣反应
-97133
-1620
(P2O5)+4(CaO)=(4CaO·
P2O5)成渣反应
-693054
-4880
CaCO3
CaCO3=(CaO)+{CO2}分解反应
169050
1690
MgCO3
MgCO3=(MgO)+{CO2}分解反应
118020
1405
2.2.2计算步骤
以100Kg铁水为基础。
计算热收入Qs。
热收入项包括