液压动力单元的结构设计Word格式文档下载.docx
《液压动力单元的结构设计Word格式文档下载.docx》由会员分享,可在线阅读,更多相关《液压动力单元的结构设计Word格式文档下载.docx(26页珍藏版)》请在冰豆网上搜索。
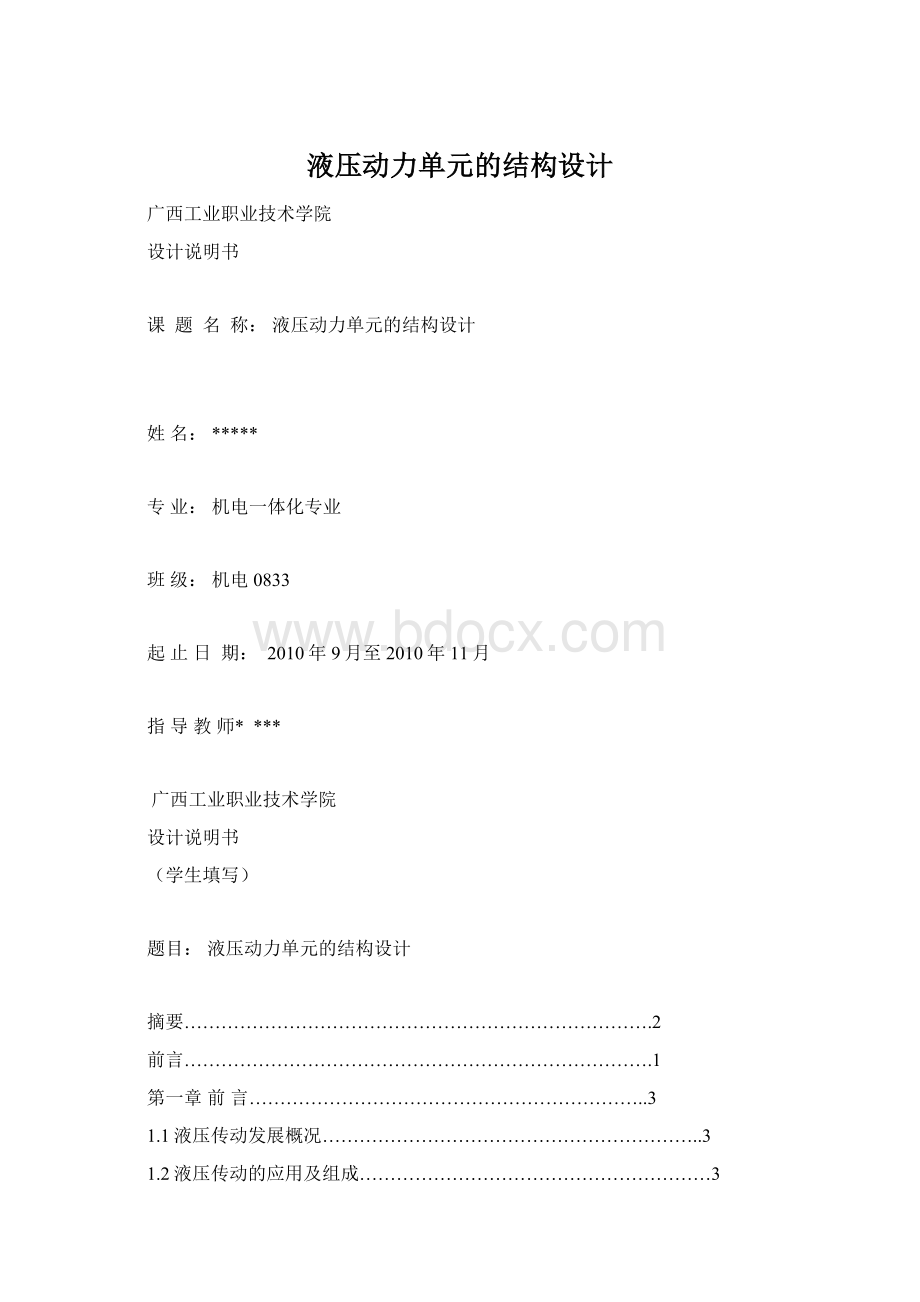
2.5液压动力单元的油箱………………………………………………..…10
2.5.1油箱分类………………………………………….…………..10
2.5.2油箱的设计…………………………………………………….10
2.5总体系统的结构……………………………………………………...12
第三章液压动力源各个部件的选型………………………………….13
3.1液压泵的选型……………………………………………………..…13
3.2电动机的选型……………………………………………………..…13
3.3液压泵与电动机之间连接的设计…………………………………………14
3.4过滤器的选择………………………………………………………..15
3.5压力仪表的选型、…………………………………………………...16
3.6密封装置的选型…………………………………………………...…16
3.7接口部件的选型…………………………………………………….17
第四章系统材料的选择……………………………………………….20
4.1油箱外壁材料的选择………………………………………………….20
4.2压力平衡结构中的非金属材料的选择………………………………….…21
第五章液压动力单元系统性能的校核…………………………………...23
5.1油箱壁的强度校核………………………………………………...….23
5.2压力平衡结构的体积校核……………………………………………....23
结论………………………………………………………………...26
谢辞………………………………………………………………...27
参考文献………………………………………………………….28
摘要
随着个国的经济飞速发展和世界人口的不断增加人类消耗的自然资源越来越多,陆地的资源正在日益减少。
。
本文设计内容为开发一套6000M深海液压动力单元,工作压力为21MP,额定排量35mL/min,作为液压动力源在考虑了一般陆地环境必须注意的问题,如液压系统的污染、泄漏、液压冲击、振荡和噪音外,还必须考虑在深海环境下的新问题重点归纳来包括压力平衡问题、密闭问题、电缆的接口问题以及材料防腐蚀问题。
海洋深处有很大的压力的,而且随着深度的加深,压力也就越大,当到达6000米时,压力为60MPa。
如果这么大的压力都由液压动力源来承担,再加上系统工作所要的压力,液压泵的负担是很重的,而且这样也不经济,液压动力单元的效率会非常低,同时整个结构的外壳也必须做得很厚以承受水压。
这样就加大了系统的重量,在系统的密封工作方面也带来很大的难度,所以必须要设计一个特别装置来平衡系统的内外压力。
同时也对压力平衡后的系统平衡问题、密闭问题、电缆的接口问题以及材料防腐蚀问题进行了分析。
关键词:
动力单元压力平衡压力系统
前言
液压传动和气压传动称为流体传动,是根据17世纪帕斯卡提出的液体静压力传动原理而发展起来的一门新兴技术,是工农业生产中广为应用的一门技术。
如今,流体传动技术水平的高低已成为一个国家工业发展水平的重要标志。
第一个使用液压原理的是1795年英国约瑟夫·
布拉曼(JosephBraman,1749-1814),在伦敦用水作为工作介质,以水压机的形式将其应用于工业上,诞生了世界上第一台水压机。
1905年他又将工作介质水改为油,进一步得到改善。
我国的液压工业开始于20世纪50年代,液压元件最初应用于机床和锻压设备。
60年代获得较大发展,已渗透到各个工业部门,在机床、工程机械、冶金、农业机械、汽车、船舶、航空、石油以及军工等工业中都得到了普遍的应用。
当前液压技术正向高压、高速、大功率、高效率、低噪声、低能耗、长寿命、高度集成化等方向发展。
同时,新元件的应用、系统计算机辅助设计、计算机仿真和优化、微机控制等工作,也取得了显著成果。
第一章液压传动的概况
1.1液压传动发展概况
自18世纪末英国制成第一台水压机算起,液压传动技术已有二三百年的历史,到20世纪30年代它才较普遍的用于起重机、机床及工程机械。
在第二次世界大战期间,由于战争需要,出现了由响应迅速、精度高的液压控制机构所装备的各种军事武器。
第二次世大战结束后,战后液压技术迅速转向民用工业,液压技术不断应用于各种自动机及自动生产线。
我国的液压工业开始于20世纪50年代,液压元件最初应用于机床和锻压设备。
目前,我国的液压件已从低压到高压形成系列,并生产出许多新型元件,如插装式锥阀、电液比例阀、电液伺服阀、电业数字控制阀等。
我国机械工业在认真消化、推广国外引进的先进液压技术的同时,大力研制、开发国产液压件新产品,加强产品质量可靠性和新技术应用的研究,积极采用国际标准,合理调整产品结构,对一些性能差而且不符合国家标准的液压件产品,采用逐步淘汰的措施。
由此可见,随着科学技术的迅速发展,液压技术将获得进一步发展,在各种机械设备上的应用将更加广泛。
1.2液压传动的应用及组成
1.1.1液压传动的应用
液压动力单元是一种以受压为工作介质进行能量传递。
转换和控制的传动。
与机械相比,液压传动具有功率-质量比大,布局灵活多变并能实现无级调速等多种技术优势,在现代工业、农业、建筑业、航空航天、河海工程。
科学实验,公共设施与环境等领域中得到广泛应用。
液压传动技术作为现代机械设备中一种实现传动与控制的重要技术,对先进液压动力单元的发展具有很大的促进作用。
1.1.1液压传动的组成
液压动力源一般由液压泵组、油箱组件、控温组件、过滤器组件和蓄能件5个相对的组件组成;
液压动力源的组成
组成部分
包含元器件
作用
液压
泵组
液压泵
将原动机的机械能转换为液压能
原动机(电动机或内燃机)
链接原动机和液压泵
联轴器
安装和固定液压泵及原动机
传动底座
油箱组
油箱
存储油液,散发悠然热气,逸出空气,分离水分,沉淀杂质和安装元件
液位机
显示和观测液面高度
通气过滤器
过滤空气
放油塞
清洗油箱或放油
控温
组件
温度计
显示观测油液温度
温度传感器
检测并控制油温
加热器
油液加热
冷却器
油液冷却
过滤器组件
各类过滤器
分离油液中的固体颗粒,防止堵塞小截面流道,保持油液情节等
蓄能器组件
蓄能器
蓄能,吸收液压脉动和冲击
支承台架
安装蓄能器
1)能源装置——液压泵。
它将动力部分(电动机或其它远动机)所输出的机械能转换成液压能,给系统提供压力油液。
2)执行装置——液压机(液压缸、液压马达)。
通过它将液压能转换成机械能,推动负载做功。
3)控制装置——液压阀。
通过它们的控制和调节,使液流的压力、流速和方向得以改变,从而改变执行元件的力(或力矩)、速度和方向,根据控制功能的不同,液压阀可分为村力控制阀、流量控制阀和方向控制阀。
压力控制阀又分为益流阀(安全阀)、减压阀、顺序阀、压力继电器等;
流量控制阀包括节流阀、调整阀、分流集流阀等;
方向控制阀包括单向阀、液控单向阀、梭阀、换向阀等。
根据控制方式不同,液压阀可分为开关式控制阀、定值控制阀和比例控制阀。
4)辅助装置——油箱、管路、蓄能器、滤油器、管接头、压力表开关等.通过这些元件把系统联接起来,以实现各种工作循环。
5)工作介质——液压油。
绝大多数液压油采用矿物油,系统用它来传递能量或信息。
1.3设计与使用一般液压动力源的关键
液压系统的污染、泄漏、液压冲击、振动和噪声问题,这些是设计与使用一般液压动力单元的几个关键,并对液压站的设计质量的优略和使用效益。
效果的发挥有很大影响。
污染控制。
油液中各种颗粒污染物在滑阀间隙内会引起滑阀卡阻故障,会导致出现液压元件中的阻尼小孔或节流小孔堵塞造成元器件失灵等问题。
有研究资料表明,液压系统的故障约有80%以上是因液压油所造成,而不同的污染途径和污染物形态对液压系统造成的危害又不尽相同,所以污染控制十分重要。
泄漏。
如果由于某种原因导致油液超过了边界,流到不应该去的其他容腔或系统外部,称为泄漏。
内泄漏是从元件的高压腔流到低压腔的泄漏,而外泄漏是从元件或管入中流到外部的泄漏。
按照泄漏机理不同,又有缝隙泄漏、多孔隙泄漏、黏附泄漏和动力泄漏等多种形式。
液压冲击。
在液压系统中,由于某种原因引起的压力急剧交替升降的阻尼波动过程,称为液压冲击。
液压冲击使系统的瞬间压力较正常压力大许多倍,这种现象常使液压元器件、管道及密封装置损坏失效,引起系统振动和噪声。
振动和噪声。
是液压装置运行中经常发生的两种现象。
振动是弹性物体的固有特性,噪声源于振动,发声噪声的振动称为声源,所以噪声的控制归结为振动的控制。
除了某些利用振动原理工作的液压设备外,液压系统的振动多数情况下是有害的,它影响主机和系统工作性能及使用寿命。
噪声除了造成人的听力损伤外,还会分散操作者的注意力,还可能淹没报警信号,造成人身、设备事故。
随着液压系统的高压、高速化,振动与噪声的控制就显得重要。
它也是液压动力源设计中应重点注意的一个问题。
除此之外,油箱的设计也是一个相当重要的问题,油箱除了有存储液压油液的作用外,
还担负了散发油液热量、逸出空气、沉淀杂质、分离水分的作用。
1.4设计深海液压动力源的特殊要求
首先深海液压动力源也是一个液压动力源,所以也要注意一般环境用的液压动力源的要求,由于他的特殊环境要求,液压动力源也需要有特殊的设计。
海水含有很多矿物质并且显示碱性,液压动力源要在海底作业,肯定是要整日整夜泡在海水里,自然会对一般材料产生腐蚀作用,所以需对其进行防护,或者选择防腐材料,此外在海水的相对高压环境里密封、润滑和接口工作也是一项相当重要的技术。
一般环境下使用的液压动力源,大多数的邮箱设计都是邮箱与外界接通的,只需在邮箱与外界之间设置一个通气过滤器,这样保证液压动力源邮箱内的压力和外界压力相等。
但是内在海底是不能直接这么处理,油箱中的油液不可能与海水接触,所以怎样使系统压力平衡是一个需要解决的问题,现在假设在深6000M的海底进行作业,计其相对压力可用公式P=pgh
第二章液压动力单元的总体设计
2.1液压动力源的集中结构形式
液压动力源按布置方式分为上置式、非上置式和柜式。
1上置式液压动力源。
泵组布置在邮箱之上的布置方式成为上置式。
上置式布置方式按电动机的摆放位置又可分为立式和卧式。
当电动机立式安装,液压泵置于邮箱内时,称为立式液压动力源;
当电动机卧式安装,液压泵置于邮箱上时,称为卧式液压动力源。
2非上置式液压动力源。
将组布置在底座或地基上的液压动力源称为非上置式。
如果泵组安装在与邮箱一体的用底座上,则称为整体液压动力源;
将泵组单独安装在地基上则称为分离型液压动力单元。
整体型液压动力源又可分为旁置式和下置式两种。
柜式液压动力源。
将泵组合邮箱整体置于封闭型柜体内的结构称为柜式液压动力源。
2.2各种布置的比较
上置式液压动力源占地面积小,结构紧凑,液压泵置于邮箱内的立式安装动力源,噪声低且便于收集漏油,一般应用于中小功率的液压泵站。
当采用卧式动力源时,由于液压泵置于邮箱之上,必须注意各类液压泵的吸油高度,以防液压泵油口处产生过大的真空度,造成吸空或气穴现象。
非上置式液压动力源由于液压泵置于邮箱面以下,故能能有效改善液压泵的吸入能力,这种动力源装置高度低,便于维护,但占地面积大,适用于泵的吸入允许高度受限制,传动功率较大,而使用空间不受限制,以及开机率低,使用时又要求很快投入运行的场合。
新一代的这种布置方式的液压动力源可以将液压泵组、邮箱组件、控温组件等集成为一个整体,机构做得相当紧凑,并且能保证一定压力和排量,如近些年来出现的通用性较强的液压动力单元就是典型代表。
柜式液压动力源装置可在柜体上方便布置各类仪表板和电控箱,且外观整齐美观,因泵组被柜体封闭而屏蔽了噪声,同时能有效减少外界污染,其缺点式由于需顾及操作和维护的空间及液压泵系统的散热,致使其外形尺寸较大,通常仅在中、小功率场合及实验室采用。
2.3布置方案的选定
考虑到本次设计的液压动力源的实际使用环境,在满足压力和排量要求的前提下,整个系统做得越小越紧凑越好,不仅占地面积小,而且也节省了不少材料,在这个大前提下,初步选择的方案是采用非上置式整体型液压动力源,在体积和布置上向液压动力单元形式靠进。
因为海水的腐蚀性,液压动力单元最外层与海水接触部分材料要选用特殊材料,并且希望这种材料的面积尽量小且形状规则,如果电动机和液压泵放在邮箱外面,这样必将增加外壳材料表面积,也会使得外壳的形状相对复杂,随之而来的装配和焊接问题就会更多,这里采用将电动机和液压泵放在邮箱内部,如图里2-1所示,这样整个液压动力单元从外形上看就较为简洁。
图2-1系统布置方式图
图2-1所示结构采用的电动机式一般陆地环境使用的普通三相异步电动机,电动机外壳内时有空气的,这样就需要在电动机轴的出口处加动密封装置,防止液压油进入电动机线圈内,因为当海水深度达到6000m时,压力将达到60MP
,所以对这个密封装置的要求很高。
为解决这个问题,考虑将电动机换成现在较为先进的水下电动机,由于这项技术属于较为前沿的技术,还没有完整的系统资料,所以下面引用国外某水下电动机的资料。
水下电动机应着重考虑电动机耐受水压以及水的隔离问题,某公司的产品用了两种方法。
·
耐水压的机械结构:
采用高机械强度材料增加壁厚的机壳以承受水压及隔离海水。
平衡压力结构:
电动机内部充油,以非金属膜盒加以封闭,靠此膜盒的伸缩适应内部油液的热膨胀以及外部水压的变动,使电动机内外压力达到平衡。
显然选用第二种方法的水下电动机比较合理,在还没有完整资料的情况下,在此基础上对电动机进行改进,设计出一个在理论上行得通的水下电动机。
电动机的压力平衡部分一般放在电动机的尾部,改进后的设计也是从尾部进行示意。
既然选择的是深海电动机,则电动机的防腐问题在电动机设计时已经考虑了,那么其外壳材料肯定选择了防腐材料。
在这种情况下液压动力源如与原来的布置一样,会造成防腐材料的损失,那么就可以将电动机放在邮箱外面而只将液压泵放在邮箱内,这样会使得液压动力单元的体积和重量都变小,不足的是其长度会有所增加,结构如图2-2所示
图2-2改进后的系统布置方案图
这样整个系统的大致结构就定下来了,核心问题是考虑怎样才能使邮箱内的压力和海水的压力相等,或者是使邮箱内的压力略大于海水的压力。
2.4系统压力平衡问题的分析
要使系统内部油液压力增加,可以向邮箱内加入更多的油液,在体积不变的情况下,油液越多压力就会越大,但是在深海,这种方法是行不通的。
而采用的方法是在油液量不变的情况下,减小油液的体积来增加油液的压力。
分析的方法为蓄能器状气囊结构方法,蓄能器状气囊结构既实现油箱较大的体积变化,又方便于压力补偿装置的安装,也容易计算所能补偿体积的大小,气囊外包着金属壳,因而,气囊不会发生太大的变形,金属壳还可有效地防止外界尖锐物品刺破气囊。
所以压力平衡机构选用蓄能器状气囊结构。
方案的工作原理一个油箱,包含一个能进行弹性变形的部件,当有压力差存在时,该部件就发生变形,将压力传递到油液中,从而使油液的体积减小,压力增大至与外界环境相等时,也就油箱内部的压力与外界的水压力达到平衡,这样,不论多大深度,油箱内部的压力总与外部水压力相等,油箱壳体所受到的内、外压力相等,压差为零,实现了对不同水深的压力补偿。
2.5液压动力单元的油箱
2.5.1油箱分类
通常油箱可分为整体式油箱、两用油箱和独立油箱三类。
1.整体式油箱是指在液压系统或机器的构件内形成的油箱。
2.两用油箱是指液压油与机器中的其他目的用油的公用油箱。
3.独立式油箱是应用最广泛的一类油箱,它常用于工业生产设备,一般制成矩形,也有圆柱形和油罐形。
通过计算机可以发现
2.5.2油箱的设计
本设计采用独立式圆柱形油箱,因为在材料用量相同的情况下将箱体制成圆柱形所获得的体积最大,而电动机的外形一般也是圆柱形的,将电动机与油箱连接在一起后,其形状比较规则、美观和统一的,电动机和油箱都要横向摆放,圆柱形的母线与地面平行。
为了能够其进行容易更换和使杂质排出,要在圆柱形油箱的内壁底部设置一个排油槽。
油箱容量按经验公式来计算,因为系统工作时整个油箱是浸泡在海水里的,并且海底的温度一般为4℃左右,所以整个系统的散热效果是非常好的,相当于是水冷,没必要从散热角度来计算油液的容积。
油箱容量的经验公式:
V=aQv
式中Qv————液压泵的流量;
a———经验系数,一般情况下取3~5
则可求得系统所需油液的体积V油为
V油=3×
52.5=157.5(L)
所设计的系统结构是液压泵及其他的一些部件放置在油箱内部,所以要计算油箱的体积需要将这些部件的体积加上所需油液的体积。
液压泵的外形体积是很不规则的,要精确计算它的体积大小是很困难的,所以将其近似看成一个立方体,各个方向的尺寸这合后为195mm×
202mm×
233mm。
则液压泵所占的体积V泵为
V泵=195×
202×
233=9.18×
106(mm3)
液压泵的体积加上其他部件的体积,最后将总的体积圆整为9.18×
106(mm3),即9.2L
这样整个油箱的体积为
V箱=V液+V泵=157.5+9.2=166.7(L)=166.7X105(mm3)
选取的深海直流电动机直径大约为400mm,为保证整个系统的美观性,同时也保证整个装置不至于过长,将油箱的端面直径选取为560mm,这样就可以根据体积计算出油箱的长度。
V箱=Ld2/4×
h=1.667×
105
h=4V箱/Ld2=1.667×
105×
4/3.14×
562≈68
式中V箱-----油箱所需的积,mm3;
d------油箱端面的直径,cm;
h------油箱长度,cm
最后将油箱长度选定为68cm.
2.5总体系统的结构
确定了油箱的端面直径和长度,还要确定油箱的厚度。
虽然油箱有了压力平衡装置后。
在深海所承受的压差约为零,但还是要承受较大的内压,同时还会打出取多螺纹孔用于其他部件的安装和固定,所以选定油箱壁的厚度为10mm。
油箱的制定方法选取铸造工艺。
为了使整个系统便于安装,油箱的右端面是开通的,整个内部结构安装完毕后用一块油箱盖板将油箱盖住,为了整个系统注油方便,还在油箱壁的上方开了个注油口。
使用蓄能器状气囊结构作问为压力平衡结构,考虑到安装方便,就把其放在油箱的上背面,但是为了系统在初始的状态下气囊内就能装满油液,气囊结构的最够位置要低于油箱壁的最高位置。
这样,整个设计方案的大致布置及尺寸就确定下来了,其结构平面图如图2-3所示。
图2-31-深海电动机;
2-通轴;
3-油箱外壳;
4-注油口盖;
5-压力平衡装置;
6-油箱后盖;
第三章液压动力源各个部件的选型
3.1液压泵的选型
液压泵是将源动机的机械能转换为液压能的能量转换元件,在液压传动中,液压泵是动力元件,向液压系统提供液压能。
液压泵可分为齿轮泵、叶片泵、柱塞泵、螺杆泵四类。
通过各类泵的比较,柱塞泵具有流量范围大、工作压力高、变化形式多等优点,以及本设计的要求压力是21PMa是一个不小的压力,并且是工作在深海作为一些机构的动力源,流量范围要求会比较大,所以选用柱塞泵。
柱塞泵有轴向和径向之分,因经向布置不如轴向布置紧凑,故泵的体积和重量都较大。
柱塞与定子为点接触,应力高,配油轴磨损后间隙不能补偿,漏损较大,故这种径向泵的工作压力、容积效率和转速都比轴向柱塞泵低。
深海液压系统用液压泵的设计还要考虑振动和噪声问题,因为如果振动和噪声较高将会影响整个执行系统上其他设备的正常运行。
而在振动和噪声指标满足要求的情况下,一般陆上液压系统用液压泵均可满足深海的使用要求。
最后选择斜盘轴向式柱塞泵。
传统泵是整个油路的一部份,除了选择泵外,还要连接一些液压阀及相关油路来组成一个基本回路,现在又些泵已经集成了一些基本的液压控制阀,这样就简化了整个油路的设计。
考虑到本设计所需求的排量为35mL/r,压力为21MP,最终选用某公司的C4低压卸荷控制型液压泵,具体型号BK35-F-R-C4-※-A-K-11,其主要参数如下:
排量:
35mL/r。
最高压力:
25MPa。
额定转速:
1500r/min。
最高转速:
2200r/min。
容积效率:
0.98。
3.2电动机的选型
通过各类电动机以及本设计所需选择的电动机为直流无刷电动机。
直流无刷电动机价格比较相当,密封结构也比较简化,电动机壳上装有压力补偿器,电动机内充有一定的补偿油。
通过压力补偿器使电动机壳体内外压力平衡。
电动机的定子机壳、前端盖、后端盖构成一个密封壳体,属于静密封问题。
因此在前、后端盖处采用O形圈进行密封。
而组合密封圈采用聚四氟乙烯内环与O形圈外环的有机结合,使轴伸处的密封是动密封。
根据液压泵在满负载额定转速下可以确定电动机的最大功率。
已知液压泵的排量V=35mL/r,泵的压力p=25MPa,这里所选定泵的转速n=1500r/min,泵的总效率取η=0.98.
流量:
q=Vn×
10-3=15000×
35×
10-3=52.5(L/min)
功率
P=pq/60V=21×
52.5/60×
0.95=19.34(kW)
式中q―液压泵的流量
V―液压泵的排量,L/min
n―电动机的转速,r/min;
η―系统总功率;
P―电动机的功率;
kW;
最后确定电动机的功率为22kW。
3.3液压泵与电动机之间连接的设计