侧边传动式旋耕机的设计Word下载.docx
《侧边传动式旋耕机的设计Word下载.docx》由会员分享,可在线阅读,更多相关《侧边传动式旋耕机的设计Word下载.docx(27页珍藏版)》请在冰豆网上搜索。
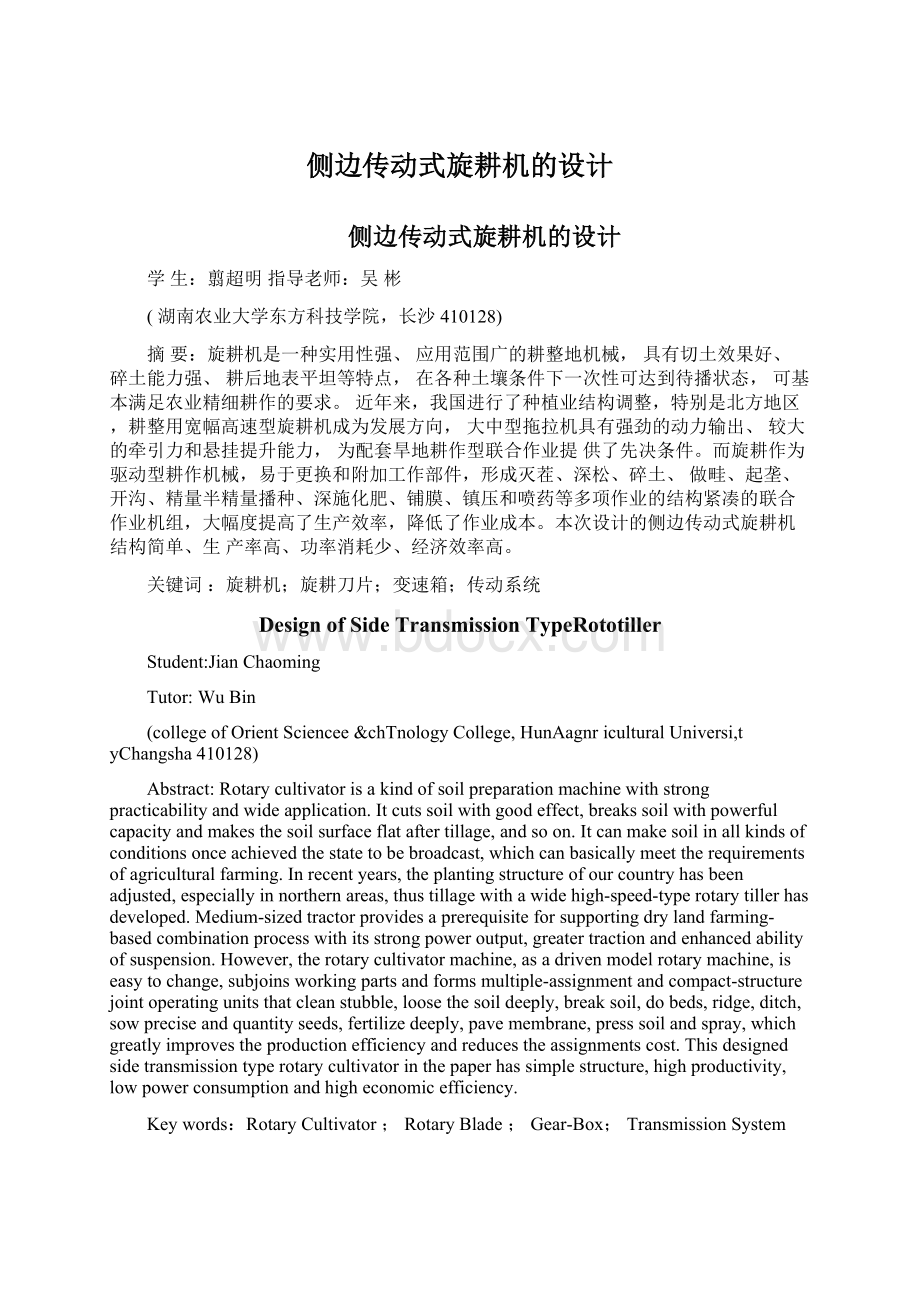
这样可保证农具的最小能耗,最小的材料消耗和较好的工作质量。
根据目前旋耕机的使用现状,预计旋耕机的研究重点将是以下几个方面:
(1)在传动方面,现有的旋耕联合作业机具机架刚性不足,影响传动系统零件寿命,可靠性低。
(2)旋耕刀具设计参数不合理,作业性能差。
(3)侧边传动式旋耕机部件的结构设计。
(4)与发动机功率匹配。
(5)整机应满足基本农艺要求,耕深10~13cm,配套动力为15~30KW的拖拉机。
(6)作业后,地膜与垄台要贴实、无皱折、无卷曲、无漏覆。
本次设计主要是要一次同步完成翻土、碎土、平整地表等作业,并且须通过合理选择参数和优化机构设计,使之整体尺寸、结构设计合理,功率消耗低,满足作业要求,同时克服其他可能存在的问题。
2总体方案的选择及确定随着农业科学技术的发展,旋耕机的研究和使用有很大的进展,出现了多种型式的产品。
通过分析比较本次设计选用卧轴、悬挂式侧边传动的方案,这种结构对土壤适应强、混土效果好,能一次同步完成翻土、碎土、平整地表的要求,而且结构简单、效率高。
2.1工作方式的选择旋耕切削方式的选择由于切削方式的不同,旋耕机的功耗及所达到的效果亦有不同。
目前有旋耕机刀辊的旋向与其前进方向的不同,一般可分为以下两种基本形式:
正转式和反转式。
两者在工作时的切削速度、刀轴切土扭矩等都表现不同,但反转旋耕机存在的最大问题是作业时刀片切下的土块容易随刀滚抛向前方,易造成堵塞,不利于旋耕平土。
故此处选正转更合适。
2.2动力的选择根据现有拖拉机型号使用性能等情况及任务书的要求,现初选东方红-250的轮式拖拉机。
其参数如下表1:
表1东方红-250的轮式拖拉机技术规格
Tab.1Dongfanghong-250-wheeledtractortechnicalspecifications
参
型式
外型尺寸
标定功率
最大提升力
额定牵引
数
值
速度范围
力
(N)
5800
(mm)
(kw)
(KN)
(Km/h)
4*2
2850×
1360×
1190
18.4
4.15
1.25~27.86
参数数值
轴距
1493
最小离地间隙(mm)
430
后轮轮距(mm)1020~
1320
结构质量(kg)1040
动力输出轴转速(r/min)540/730
动力输出轴标定功率(kw)17.5
3工作参数的计算及选择
3.1刀片运动轨迹及其分析
旋耕机工作时,旋耕刀运动轨迹是摆线[1]。
以刀轴旋转中心为原点建立坐标系,x轴正向和旋耕机前进方向一致,y轴正向垂直向下。
设前进速度为vm,刀轴旋转角度为ω,开始时刀片端点位于前方水平位置与x轴重合,则旋耕刀端点运动方程为:
x=Rcosωt+vmt
y=Rsinωt
(1)
式中R——旋耕刀端点转动半径(刀滚回转半径)
图1刀片运动轨迹Fig.lInsertstrajectory
由公式
(1)可见—旋耕刀端点的绝对运动,其运动轨迹随着R、ω、和vm的不同而有不同的形状和特性。
将式对时间求导,可得刀片断点在x轴和y轴方向的分速度:
vx=dx/dt=vm-Rωsinωt
(2)
vy=dy/dt=Rωcosωt(3)
刀片端点绝对速度V的大小为:
V=vx2vy2R22vm22Rcost(4)
由公式(4)可见Rω=vp是旋耕刀端点的圆周线速度,令λ=vp/vm=Rω/vm,λ称为旋耕速度比,它表示旋耕刀端点旋耕速度比与旋耕机前进速度的比值,λ的大小对旋耕刀运动轨迹及工作状况有重要影响。
因λ=Rω/vm
故vx=vm-Rωsinωt=vm(1-λsinωt)(5)
如果λ<
1,即vp<
vm,则不论旋耕刀运动到什么位置,均有vx>
0,即刀片端点的水平分速度始终与旋耕机前进方向相同,其运动轨迹是短摆线,这时旋耕刀不能向后切土,而出现刀片端点向前推土的现象,使之不能正常工作。
若λ>
1,则当旋耕刀旋转到一定位置时,就会出现vx<
0的情况,既刀端绝对运动的水平分速度与旋耕机前进的方向相反,从而使旋耕刀能够向后切削土壤。
只要刀片开始切土时vx<
0,整个切土过程都可满足这个条件。
λ>
1时刀端运动轨迹为余摆线。
为保证旋耕刀正常切土,刀刃上切土部分各点的运动轨迹都应是余摆线,即其圆周速度大于旋耕机的前进速度[1]。
3.2机组前进速度与刀片回转速度的配合
由以上可知,为保证刀刃切土,刀片从开始切土直到铣切完毕都不应使刀片顶土。
即:
vx=vm-Rωsinωt<
0(6)
由公式(6)可见在切土过程中刀刃向后的分速度是逐渐增大的。
一般旋耕机的前进速度vm=0.5~1.5米/秒,刀片的端点切线速度V=3~8米/秒。
为使机组减少功耗提高效率需合理选择配合两者的速度[2]。
3.3耕作深度
通常耕深与旋耕机的结构参数R和运动参数vm、Rω有关。
设耕深为H,由刀片运动轨迹图可知,当旋耕刀端点开始切土时其纵坐标y=R-H,变换得y=Rsinωt则sinωt=(R-H)/R
代入公式(6)中,得:
vx=vm-(R-H)ω(7)
要使vx<
0,必须,vm<
(R-H)ω
即H<
R-vm/ω或H<
R(1-1/λ)λ的选择即要保证旋耕机正常工作及满足设计耕深要求,还要综合考虑旋耕机结构、功率消耗及生产率等其他因素。
如增大R、ω不仅使结构变大,而且回增大切土扭矩及功率消耗,减小vm又会降低生产率。
目前常用的速度比为λ=4~10左右[2]。
根据旱耕耕深的设计要求取为H=12cm。
3.4切土节距沿旋耕机前进方向纵垂面内相邻两把旋耕刀切下的土块厚度,即在同一纵垂面内相邻两把刀相继切土的时间间隔内旋耕机前进的距离。
sz=vmt=vm×
60/zn或sz=vm×
2π/zω(8)
式中t——刀轴每转一个刀片所需时间,s
Z——同一旋转平面内的刀片数
n——刀轴转数,r/min
由公式(8)可见,增加z或n,sz变小,切土细碎,但随着转数的提高,功率消耗亦显著增加。
若增加z或n,刀片间距变小,易产生堵塞现象[2]。
故一般为10~12mm。
综上所述,旋耕部分设计时以上各参数相互影响。
根据设计任务要求及拖拉机规格,p=18.4Kwvm=1.25~3.07Km/h。
取λ=7,V=Rω=2.43~5.97m/s,由sz=12cm,H=12cm,n=203r/min,则ω=2πn/60=20.9rad/s,R=V/ω=117~286mm。
若同一旋转平面内的刀片数Z=2,sz=6cm。
3.5耕幅的确定
工作幅宽应根据配套的拖拉机功率的大小,旋耕比能耗(旋耕比阻),耕深要求等确定。
拖拉机输出动力轴功率pe=17.5Kw取功率利用η=0.8,则1000peη=BHkrvm,kr为旋耕机工作时的比阻,当h=12cm时,砂壤土Kr:
1.2~1.4kg/cm2。
得耕幅为:
B=1000pe(9)
HkrVm
将数据代入公式(9),得:
=162cm
100017.50.8
121.21060
取B=90cm。
3.6机具的配置
由于耕幅B=900<拖拉机后轮轮距外缘1020,故要采用偏右侧悬挂。
Fig2Cultivationsitesconfiguration
3.7功率耗用
旋耕机工作时所需的功率计算。
在耕作过程中,旋耕机工作所需的功率与多种因素有关,如地块地形、耕深、耕宽、耕速和土壤性质等。
功率消耗主要包括旋耕刀切削土壤消耗的功率、抛掷土块消耗的功率、推动前进消耗的功率、传动部分消耗的功
[4]
。
率及土壤沿水平方向作用与刀辊上的反作用力所消耗的功率。
设计时,假定旋耕机组
在比较平坦的田地里进行匀速直线作业,旋耕机工作时所需的功率可用下式估算
将数据代入公式(10),得:
N=1.33×
0.9×
0.12×
0.6×
12×
10000=10.3Kw
式中:
B——旋耕机工作时的耕幅B=0.9m
H——旋耕机工作时的耕深H=0.12m
vm——旋耕机组前进速度vm=0.6m/s
Kr——旋耕机工作时的比阻,当h=12cm时,砂壤土Kr:
1.2~1.4kg/c㎡即:
12×
10000~14×
10000N/㎡
由N=10.3Kw,旋耕机工作装置工作效率1取0.85,所需的功率pw=N/1=12.1(kW)。
动力传动装置效率,可取η=0.85,旋耕机工作时所需要的功率p0=pw/η=14.3kW,故所选动力满足旋耕机的功率耗损。
4结构设计
4.1传动方案拟订目前有的旋耕机采用变速箱式的传动装置,有的旋耕机动力从中央传给刀轴,整机受力均匀,根据任务书采用侧边传动。
由于侧边齿轮结构复杂,加工精度要求高,而侧边链传动零件少、质量轻、结构简单、加工精度要求低,所以本设计采用侧边链传动。
柴油机的输出速度,经V带传到拖拉机的离合器,通过变速箱变速后,一部分动力传到拖拉机的行走轮上,另一部分传到旋耕机的输入轴上。
考虑到旋耕机的设计尺寸,旋耕机齿轮箱的输入轴和拖拉机变速箱的输出轴可能不在同一直线上,两者之间采用万向节传动。
为了增加旋耕机的输出力矩,在其输入轴和刀轴间采用单级齿轮减速器和链轮传动[4]。
结构如图2:
1.万向节2.圆锥减速机构3.链传动机构4.刀轴总成
图3传动方案
Fig3Ransmissionprogram根据与所选轮式拖拉机的连接方式选取图2的传动方式,由万向节连接到拖拉机的动力输出轴。
万向节的主要作用是补偿拖拉机动力输出轴与旋耕机第一轴的偏移量,并以最大传动效率和扭矩带动旋耕机工作,同时当负荷更大时保护旋耕机。
4.2传动装置设计
4.2.1总传动比的计算及分配由所选拖拉机的动力输出轴转速ne和刀滚的工作转速n可确定传动装置的总传动比i,由ne=730r/min,n=203r/min。
i=ne/n(11)
由公式(11)可知总传动i=3.6,传动比不大,两级减速一对圆锥齿轮和链轮即可满足要求。
考虑到单级圆锥齿轮减速器的传动比不易过大,以减小齿轮的尺寸,便于加工。
取链传动比为i1=2,则锥齿轮传动比[5]:
i0=i/i1=3.6/2=1.8。
4.2.2计算传动装置的运动和动力参数
各轴转速,拖拉机动力输出轴为0轴,减速器输入轴为Ⅰ轴,输出轴为Ⅱ轴,刀滚轴为Ⅲ,各轴转速为:
n0730r/min
n0nⅠ=730r/min
nⅡ=n1/i0=730/1.8=406r/min
nⅢ=nⅡ/i1=406/2=203r/min
各轴输入功率按旋耕机所耗功率计算各轴输入功率,得:
p0=14.3kw
pⅠ=p0×
η1=14.3×
0.98=14kw
pⅡ=pⅠ×
η2×
η4=14×
0.95×
0.99=13.18kw
pⅢ=pⅡ×
η3×
η4=13.18×
0.95×
0.99=12.3kw式中η1、η2、η3、η4分别为万向节、圆锥齿轮、链轮、滚动轴承的效率。
各轴转矩:
T=9550×
P/n(12)
T0=9550×
p0/n0=9550×
14.3/730=187.07N·
m
TⅠ=9550×
pⅠ/nⅠ=9550×
14/730=183.15N·
TⅡ=9550×
pⅡ/nⅡ=9550×
13.18/406=310.02N·
TⅢ=9550×
pⅢ/nⅢ=9550×
12.3/203=578.65N·
m将以上计算结果整理后列于下表2:
表2传动装置动力参数
Table2Analysisonmainqualityofendproductsofdifferentconcentrationtechnology
项目
动力输出轴
输入轴Ⅰ轴
输出轴Ⅱ轴
刀滚轴Ⅲ
转速(r/min)
730
406
203
功率(KW)
14.3
14
13.18
12.3
转矩(N·
m)
187.07
183.15
310.02
578.65
传动比
1
1.8
2
效率
0.96
0.94
4.2.3
圆锥齿轮计算及校核
齿轮采用45号钢,调质处理后齿面硬度180~190HBS,齿轮精度等级为7极。
取
Z1=20,则Z2=1.8×
20=36。
参考机械零件的齿轮计算方法。
设计准则:
按齿面接触疲劳强度设计,再按齿根弯曲疲劳强度校核。
1)按齿面接触疲劳强度设计。
齿面接触疲劳强度的设计表达式
ZHZE4KT1
[H]0.85R(10.5R)2u
其中,d0.8,u=1.8
ZE189.8MPa,ZH1.8,
T19.55106P9.551061418.3104Nmm
1n730
选择材料的接触疲劳极根应力为:
14)
应力循环次数N由下式计算可得
N160n1at
60730300816
1.68109
N1
9
4.231099
N2
0.92109
u
5
接触疲劳寿命系数ZN11.1,ZN21.02
弯曲疲劳寿命系数YN1YN21
接触疲劳安全系数SHmin1,弯曲疲劳安全系数SFmin1.5,又YST2.0,试选
Kt1.3。
求许用接触应力和许用弯曲应力:
动载荷系数Kv1.0;
使用系数KA1;
齿向载荷分布不均匀系数K1.02;
齿间载荷分配系数取Ka1,则KHKAKvKKa1.011.01.021.01.03,修正:
K1.03
d1d1t3H104.431.0396.6mm(15)
11tKt1.3
取标准模数m5mm
(2)计算基本尺寸。
d1mz1520100mm
d2mz2536180mm
66.7MPaF1
所以齿轮完全达到要求。
表3齿轮的几何尺寸
Tab.3Geargeometry
名称
符号
公式
分度圆直径
d
d1mz1520100mmd2mz2536180mm
齿顶高
ha
haham155mm
齿根高
hf
hf(hac)m(10.2)54mm
齿顶圆直径
da
da1d12hacos110mmda2d22hacos188mm
齿根圆直径
df
df1d12hfcos92mmdf2d22hfcos172mm
齿顶角
a
tanaha/R0.04854
齿根角
f
tanfhf/R0.0388
分度圆锥角
sinmz/2R0.485
顶锥角
aa26.2
根锥角
ff26.78
锥距
R
Rmz/2sin103mm
齿宽
b
b(0.2~0.35)R30mm
由于小齿轮的分度圆直径较小,所以作成齿轮轴[8]
4.2.4滚子链传动的设计计算
(1)选择链轮齿数Z1,Z2
假定链速v=0.6~3m/s,选取小链轮齿数Z1=15;
从动链轮齿数Z2iZ12×
15=30。
(2)计算功率pca。
由表查得工作情况系数Ka=1,故:
pca=Ka×
P=1×
13.18=13.18kw
(3)确定链条链节数Lp。
初定中心距a0=20p,则链节数为:
Lp=2×
a0+z1+z2+p(z1z2)2(17)
pp2a02=62.8取Lp=64节
(4)确定链条的节距p。
由小链轮系数kz=0.77,kl=0.90,kp=1.7,
p0=
pca
kzklkp
18)
=8.3kw
查表得链
根据小链轮转速n1=406r/min及功率p0=8.3kw,选链号为12A单排链,节距P=19.05。
(5)确定链长L及中心距a。
L=
Lpp
1000
=1.22m
p(LZ1Z2)(L
a=4(Lp2)(LP2
Z1Z22Z2Z12
)8()
19)
20)
=393mm
中心距减小量Δa=(0.002~0.004)a=(0.002~0.004)×
393=0.78
1.56mm
实际中心距