无氧铜生产工艺流程Word下载.docx
《无氧铜生产工艺流程Word下载.docx》由会员分享,可在线阅读,更多相关《无氧铜生产工艺流程Word下载.docx(8页珍藏版)》请在冰豆网上搜索。
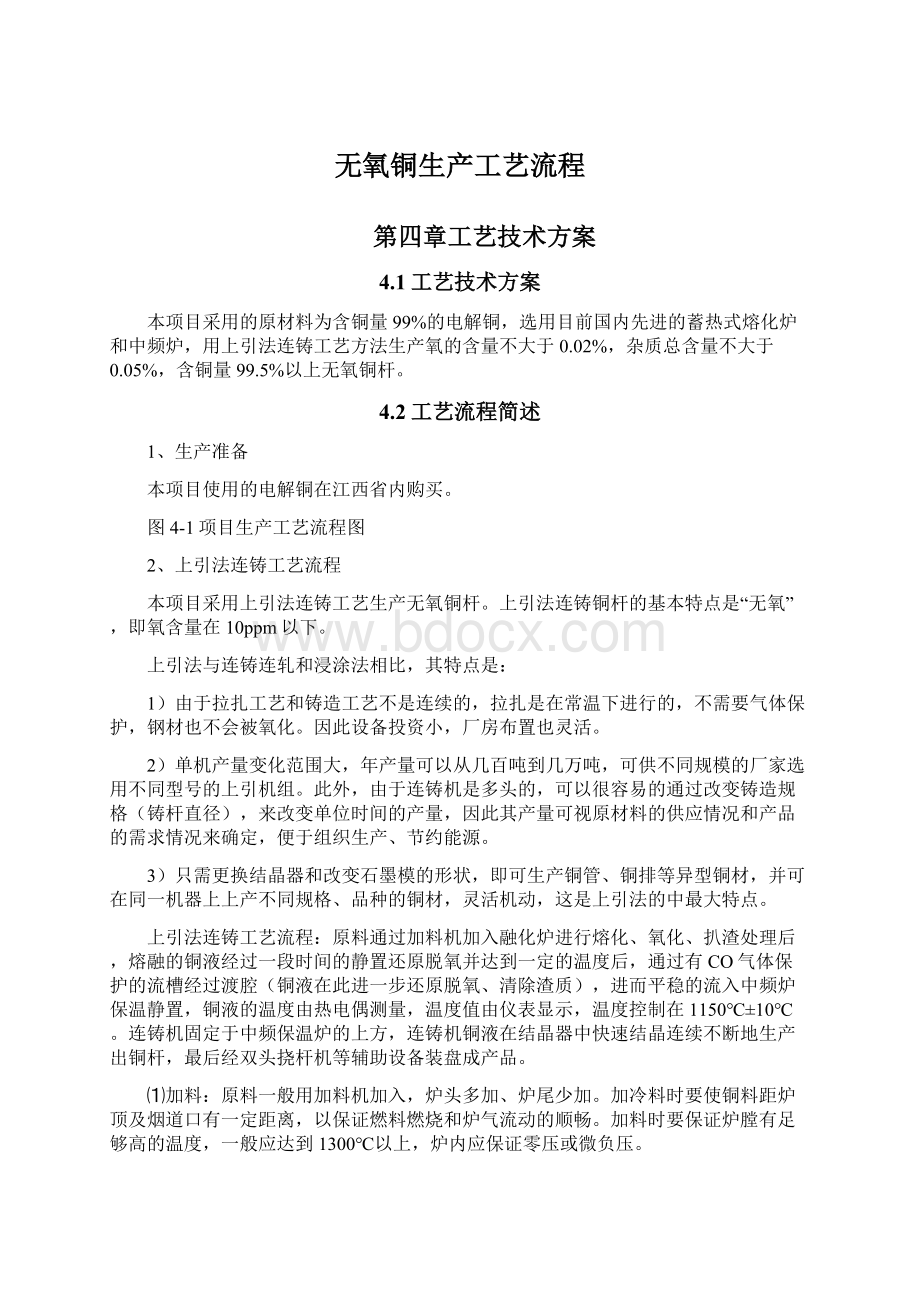
熔化作业系在氧化气氛下进行,一般炉膛温度保持在1300~1400℃以加速冷铜料的熔化,在熔化过程中定期向炉内已熔化的铜液中插入一根风管,鼓入压缩空气剧烈地搅动熔体以加速熔化过程,这时也会有部分杂质熔化,形成炉渣于熔体表面,待熔体大部分熔化完,即可进行氧化操作。
⑶氧化:
其要点是增大烟道抽力(-80~-100Pa),提高炉内空气过剩系数(ξ=1.2~1.4),使炉内成氧化性气氛。
用直径为ф18~50mm的钢管2~3根向熔体内鼓入0.3~0.5MPa的压缩空气,进行氧化作业,为减少钢管熔入铜中的消耗,钢管外用耐火材料包裹。
为增加氧的利用率,钢管应尽可能深插,插入角度为45°
~60°
,插入深度为铜熔体深度的2/3。
氧化期的炉膛温度在1250℃左右,以保证铜液温度为1150℃~1180℃,有利于杂质的氧化。
⑷扒渣:
扒渣是将造渣后的杂质通过扒渣过程将其除去,铜面控制是扒渣操作的关键。
铜液面过低,给以后扒渣作业造成困难,床能率低;
铜液面过高,易出现侧门、渣口跑铜事故。
为控制好渣含铜,应及时进行扒渣作业,避免干渣转变为稀渣,生产过多的氧化亚铜。
⑸保温静置:
熔融的铜液流入中频炉保温静置、还原脱氧并达到一定的温度后,进而处于保温状态,铜液的温度由热电偶测量,温度值由仪表显示,温度控制在1150℃±
中频保温炉引杆腔铜液表面用焦炭覆盖,覆盖厚度为40-60mm,结晶器周围厚度为80-100mm。
⑹结晶出杆、装盘:
1)结晶器准备
a.对新的和使用期超过半月的结晶器,进行水压试验,水压为0.5-0.6Mpa,保持15分钟不漏水。
b.装配石墨模:
把检验合格的石墨模,旋入结晶器,端面到位。
c.结晶器头部包上8mm厚硅酸铝纤维毯或隔热套,用玻璃纤维带扎紧,端面垫上一层硅酸铝纤维毯圈,然后装护套,在石墨模与护套的缝隙用填料或石棉线填实,以防铜液钻入。
填料配方:
耐火粘土95%+水玻璃3%,并合成团。
d.结晶器上口装上石棉盘根,并用装有引锭头的前半节引杆通过,拧紧压套,引锭头端面距石墨模端面5-10mm。
e.结晶器进出水管接上,通少量冷却水,检查管路系统是否畅通,然后放在炉口上预热10分钟以上安装使用。
2)连铸机准备:
调整液位跟踪系统的位置,保证结晶器安装后石墨模插入液面的深度为140-160mm。
操作时确认铜液液面离碳化硅保护套上沿距离为30-40mm左右。
3)引杆操作程序:
a.结晶器就位,插入铜液,接上后半节引棒,压紧牵引轮,开始引棒。
b.调节冷却水量,¢14.4-¢20mm结晶器进出水温保持在15℃左右。
¢8mm结晶器进出水温保持在6-10℃左右,进水温度最高不能超过35℃,在30℃左右为宜。
c.铜杆引出后,将引棒分节拆下,并通过导轮进入收线系统。
4)铸杆日常操作:
a.¢14.4-¢20mm铜杆牵引速度400-700mm/min为宜,¢8mm铜杆牵引速度1800-2800mm/min为宜。
b.经常检查铜杆表面质量,监测冷却水温度,结晶器插入深度,液位跟踪系统工作状况,如遇异常情况,及时排除。
(7)收线
1)收线时将引锭头头部切除,将铜杆通过限位装置,穿过并夹紧收线导轮,引入收线框内。
2)经常注意限位装置工作情况,在限位装置失灵情况下,临时利用收线机上的操作按钮进行人工操作,并及时排除故障。
3)收线框装满后,吊出铜杆,挂上产品跟踪卡,标明日期、炉次、生产班组、重量等项。
(8)水系统控制
1)水系统供水,¢14.4-¢20mm结晶器水压为0.2-0.3Mpa,水套、线圈为0.18-0.2Mpa。
¢8mm结晶器水压为0.28-0.35Mpa,水套、线圈为0.18-0.2Mpa。
2)水池水温用冷却塔调整,进水温度控制在30±
5℃。
3)当临时停电或水泵发生故障,应在一分钟内打开备用水阀门,并关闭原来水阀门,以保证结晶器及水套和线圈的冷却水不间断。
(8)气压控制
对新式¢8上引机组,其上引连铸机铸杆压紧、收线机收线、排线,采用气缸压紧。
其气压控制在:
连铸机:
0.15-0.25Mpa收线机收线:
0.2-0.3Mpa,排线:
0.15-0.25Mpa。
(9)安全生产
1)操作者应按规定穿戴好劳动防护用品,遵守设备安全操作规程。
2)打开炉盖后不要太靠近炉口,以防一氧化碳气体燃烧时火焰伤人(每次待一氧化碳气体燃烧过后再上去操作)。
3)每班应经常检查机组设备运行是否安全可靠。
4)严禁将潮湿未烘干的工具浸入铜液,以免铜水爆炸造成事故。
5)结晶器安装和取下时,注意防止冷却水进入炉内。
6)发生事故应立即采取措施,并报告有关人员及时处理。
(10)检查
铜杆质量就符合GB3952-2008《电工用铜线坯》中无氧铜杆规定。
4、余热回收利用
为提高清洁生产水平,贯彻国家关于节能减排的要求,本项目应对熔化炉烟气和中频炉烟气进行余热回收。
一般地,熔化炉出口烟气温度在1000-1200℃,中频炉出口烟气温度在800-1000℃,均具明显的热回收价值。
对没有蒸汽需求的再生铜工厂,通常采用“预热助燃风(纯氧/空气),立足降低本体消耗,节约一次能源”的余热利用方式。
熔化炉烟气余热利用方案:
采用两段式换热器进行出炉烟气与入炉助燃风的热交换,降温(降至200℃)后的烟气再进入布袋收尘器。
通过两段式换热器预热入炉助燃风,不但可节省燃料消耗,而且还可缩短熔化炉的操作周期,提高设备利用率。
据统计,两段式换热器可将入炉助燃风预热至400℃左右,节省约20%的燃料消耗和缩短1.5小时的操作周期(一般总时间为18小时)。
中频炉烟气余热利用方案:
与熔化炉烟气余热利用方案类似,但因为烟气温度相对较低,通常采用一段管式空气预热器进行烟气与入熔化炉助燃风的热交换。
据统计,经预热器的入熔化炉助燃风温度可达300℃,可节省能源消耗约10%。
4.3主要生产设备方案
4.3.1设备选择的基本原则
1、生产性原则:
选择生产设备时,注重设备的模块化、标准化、高速化、自动机械化,以提高设备的生产率;
2、可靠性原则,设备要求安全可靠,零件的耐用性好、通用性强,设备能够生产高质量产品,要求设备故障率小,准确性高;
3、维修性原则,选择可修性、设备的结构简单,零部件模块化设计,零部件通用性强,可迅速拆卸,易于检查,实现标准化和通用化;
4、节能性原则,设备要节约能源消耗;
5、成套性原则,机器设备要配套,形成整条生产线,尽量选择同一厂家产品;
6、环保性原则,设备的噪音和排放的有害物质应达到国家环保限制指标和要求;
7、灵活性原则,尽可能做到设备结构紧凑,重量体积小、轻,操作灵活方便,通用性强,可适应工艺相近的产品转换,转换操作简单方便。
4.3.2主要设备方案
本项目采用蓄热式熔化炉作为本项目的主要生产设施,其燃料为重油,该项目原料为电解铜,设备能进一步去除电解铜中的氧和其它杂质,不含硫,因此,选用蓄热式熔化炉处理是可行的,且选择蓄热式熔化炉作为熔炼炉具有适应性强、回收率高等特点,符合《铜冶炼行业准入条件》的要求。
上引法无氧铜杆连铸机组用于生产长度光亮的无氧铜杆。
和传统的铜锭压延生产黑铜杆相比,上引法无氧铜杆新工艺具有工艺技术先进,产品质量很好,单位能耗低,生产品种及规格灵活多样,适应性强,没有三废污染,投资少等特点。
本项目选用主要设备清单见表4-1。
工艺设备优点如下:
⑴加料、扒渣方便。
可在炉体侧面靠近平台处设置加料门和渣门,炉料可用加料车方便快速的加入。
炉渣门靠近渣线设置,既可倒渣,也可方便扒渣;
⑵热效率高。
炉体紧凑、密闭,氧化管道固定在炉体上,作业时不需要打开炉门操作,热量外泄少,漏入的冷空气少。
在炉体上布置了多块透气砖,通入氮气搅拌,加速了传热传质,缩短操作时间,节省燃料消耗;
⑶安全性高。
由于炉体可以转动且氧化、还原管道固定在炉体上,避免了人工持管操作可能发生的安全事故,减少了工人的劳动强度;
遇到故障时炉子可迅速转到安全位置,避免“跑铜”事故的发生,操作安全;
⑷环保条件好。
炉体密闭性能好,氧化时不需要打开炉门操作,减少了烟气外逸;
借助炉体转动可以控制氧化管道的埋入深度,加上透气砖的氮气搅拌作用可提高还原剂的利用率,减少黑烟生成;
在炉后设置有完善的烟气处理系统,烟气通过烟罩导入双体结构的二次燃烧室,烧尽可燃物后进余热锅炉回收余热,再进入布袋收尘达标后排放;
⑸熔化炉采用富氧助燃的燃烧器。
采用富氧助燃,烟气量仅为空气助燃时的20%,烟气带走的热量少,燃料消耗低,烟气处理系统可大为缩小,减少投资和运行费用。
⑹连铸机是实现上引连铸的主要设备。
它由牵引机构、液位跟踪和结晶器三大部分组成。
牵引机构由交流伺服电机和牵引辊轮等组成,它可实现每分钟0~1000次的间歇运动并通过牵引辊轮将铸杆连续上引出来,每组牵引机构可带动5付牵引辊轮,分别牵引5根铸杆,并通过更换结晶器生产其它规格的铜杆;
液位跟踪系统可保证连铸机上结晶器插入铜液的深度相对稳定,确保连铸生产的连续性;
结晶器可将液态的铜快速冷却成固态铜并实现热交换,每根结晶器都能单独更换和控制而不影响其它结晶器的正常工作。
⑺导轮架:
导轮架布置在连铸机的上方,主要由平台、支架、竖导轮和滚筒组成,它使铸杆平滑地导入各组双头挠杆机,互不干扰。
⑻限位装置:
是在导轮架和双头挠杆机之间设置的两台装置,它由6组24V低压上、下限位,通过铜杆与上下限位的接触来控制双头挠杆机的速度。
⑼双头挠杆机是由牵引辊轮、成圈装置和收线转盘组成,每组双头挠杆机由二台电动机分别驱动两套装置收圈两根铜杆,曲率自动调整。
⑽水冷系统是一个独立的循环供水系统,保证一以0.2~0.4Mpa的冷却水供结晶器、水套和线圈冷却,它由120m3水池、循环水泵、管道组成,保证进水温度在20~30℃,流量在50m3/d左右。
⑾电器系统:
由电源系统、控制系统组成,电源系统通过若干电源柜将电源分别供给每个感应器,控制系统保证机组正常生产。
⑿加料系统:
采用机械加料机,保证合格原材料连续供给熔化炉。
表4-1主要设备一览表
序号
设备名称
规格型号
单位
数量
单价
总价
备注
(万元)
1
加料机
台
6
12.5
75
2
蓄热式熔化炉
100t
3
450
1350
配套电动葫芦
中频炉
350kw
63.5
381
保温静置
4
扒渣机
25
150
5
园盘定量浇铸机
38.4
230.4
燃油喷嘴
3kg低压油喷嘴
12
36
7
引风机
26880-59738m3/h
9
15
135
4用4备
8
螺杆式空压机
72
2用2备
管式空气预热器
套
60
180
10
喷流空气预热器
11
燃油风机
32120-6334m3/h
24
连铸机
18
13
导轮架
126
14
限位装置
108
双头挠杆机
80
720
16
循环水泵
3.75
17
重油罐
80m3
个
4.5
油泵
1.5
与重油罐配套
19
电控系统
90
20
行车
2t
21
人力推车
辆
22
供电设备
1000KVA
390
23
消防设备
300
布袋除尘器
1500m2
55
220
含喷雾冷却器
其他
122
合计
139
6291.9
4.4原辅材料的成分与消耗情况
1、原材料
本项目原料主要是电解铜,项目消耗100356吨电解铜来源于省内市场。
2、燃料
低硫重油3800t/a,硫份0.26%,热值38038KJ/kg,闪点(开式)不低于80℃。
3、辅助原料
石灰石(熔剂)3420t/a,CaO~50%,粒度60-80mm。
石英砂(熔剂)2050t/a,SiO2~90%,粒度20mm。
焦炭(还原剂)197t/a,固定炭92%,灰份3%,硫份0.4%,热值33440KJ/kg。
氧气(助燃剂)10155.3t/a,含量99.5%。
标况下折合710万立方米。
项目原材料及燃料均由项目单位从市场自行采购。