包装产品制造工艺规程范文Word文档格式.docx
《包装产品制造工艺规程范文Word文档格式.docx》由会员分享,可在线阅读,更多相关《包装产品制造工艺规程范文Word文档格式.docx(16页珍藏版)》请在冰豆网上搜索。
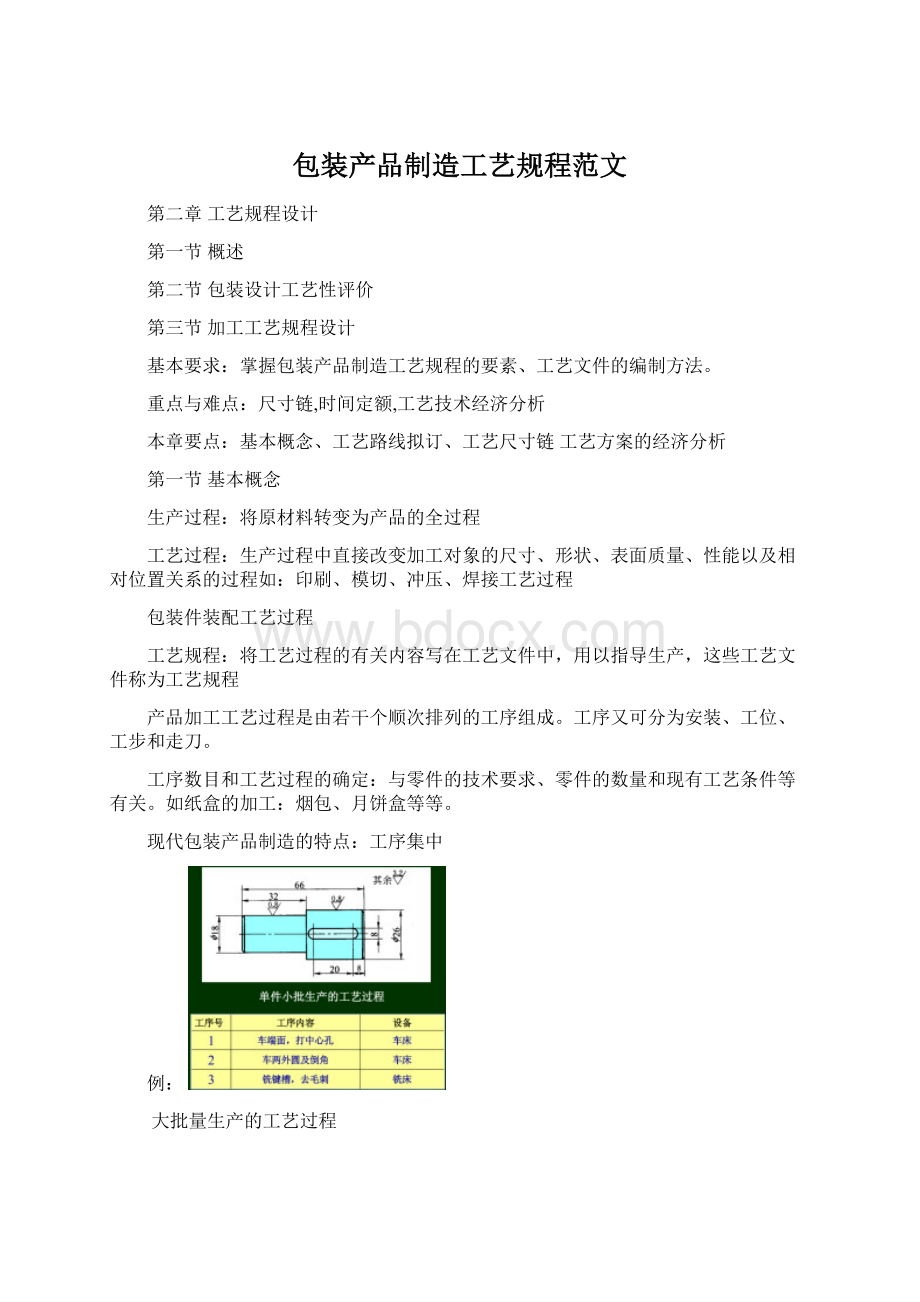
n——单台产品中该零件的数量(件/台);
a——备品率,以百分数计;
b——废品率,以百分数计。
根据生产纲领和产品本身的大小及结构复杂性,产品的制造可分为三种生产类型:
单件、成批、大量。
三种生产类型:
1、单件生产
单个地生产不同结构尺寸的产品,且很少重复的生产。
如重型机械、大型船舶制造、新产品试制等。
2、成批生产
成批地制造相同产品,且周期性地重复生产,如机床制造等。
根据产品特征及批量大小,又分为小批、中批和大批生产三种。
3、大量生产
产品数量很大,大多数工作地一直按照一定的节拍进行同一种零件的某一道工序的加工,称为大量生产。
生产批量:
即一次投入或产出的同一产品或零件的数量。
n=NA/D
式中n’——每批中的零件数量;
N——零件的年生产纲领规定的零件数量;
A——零件应该储存的天数;
D——一年中工作日天数。
生产批量的确定:
需综合考虑市场需求、生产能力、产品制造难易程度、资金投入、生产成本等因素。
4.工艺规程设计所需的原始资料
(1)产品装配图、零件图;
(2)产品验收质量标准;
(3)产品的生产纲领及生产批量;
(4)毛坯材料与毛坯生产条件;
(5)制造厂的生产条件,包括机床设备、工艺装备的规格性能及使用状况,工人技术水平以及自制工艺装备能力、能源状况等资料;
(6)工艺规程、工艺装备设计所用设计手册和有关标准;
(7)国内外先进制造技术资料等。
5.工艺规程的设计原则:
(1)质量第一原则
(2)效益优先原则(3)效率争先原则
1.结构应简约:
技术与艺术的结合2.便于加工和测量3.提高加工效率,保证产品质量4.提高标准化程度
(一)设计的内容和步骤
(二)工艺路线的拟定(三)加工余量、工序间尺寸及公差的确定(四)时间定额(五)工艺方案的经济分析
(六)工艺文件的编制
思考题:
自选一饮料两片罐,计算其毛坯及变薄拉伸过程各道工序的工序尺寸(含公差)。
(一)设计的内容和步骤
1)分析零件图和产品装配图;
2)工艺审查;
3)确定毛坯;
4)拟定工艺路线;
5)确定各工序所用机床设备、工艺装备等;
6)确定各工序的加工余量、计算工序尺寸和公差;
7)确定各工序的技术要求和检验方法;
8)确定各工序的加工(切削)用量和工时定额;
9)编制工艺文件。
(二)工艺路线的拟定
1.选择定位基准
(1)基准分类:
1)设计基准:
尺寸标注的起始位置2)工艺基准:
①工序基准工序图上用来确定本工序所加工表面加工后的尺寸、形状、位置的基准②定位基准:
a.粗基准和精基准b.附加基准③测量基准④装配基准
确定粗基准的前提:
保证得到所选精基准
(2)粗基准的选择
选择粗基准一般应遵循以下原则:
1)选择不加工面为粗基准2)合理分配加工余量3)便于工件装夹4)同方向上粗基准不得重复使用
(3)精基准的选择
主要应保证加工精度和装夹方便,选择精基准一般应遵循以下原则:
1)基准重合原则设计(工序)与定位2)基准统一原则各工序的基准相同
3)互为基准原则两表面位置精度高4)自为基准原则加工余量小而均匀
2.表面加工方法的选择
(1)尽量采用经济加工精度方案进行加工零件结构形状虽多种多样,但都是由基本表面组合而成。
同一种表面又有不同的加工方案,一般选择原则如下:
(2)首先考虑主要表面的加工方案,3)确定加工方案时应考虑零件的材料、硬度、结构形状、尺寸大小等属性。
(4)加工方案要和生产类型、生产率的要求相适应,考虑现有技术力量和设备。
3.加工阶段的划分
(1)粗加工阶段
去除各表面大部分余量,关键是提高生产率
(2)半精加工阶段
次要表面达到要求,为主要表面的精加工作准备
(3)精加工阶段
各主要表面达到零件图规定的质量要求
(4)光整加工阶段
主要用于高精度、小粗糙度要求的表面
注意:
非金属材料的加工并不完全遵循上述阶段划分
思考:
纸盒加工过程如何划分?
金属罐呢?
划分加工阶段的主要目的:
(1)保证加工质量
粗加工余量大,较大夹紧力、变形力,工件产生较大变形和加工误差,通过半精、精加工逐步纠正
(2)合理使用设备
有利于按照不同要求选不同精度、刚性、功率的机床
(3)及时发现毛坯的缺陷
以决定零件的报废或修补,避免盲目加工造成的浪费
4.工序的集中与分散
确定工序内容时有两种思路,即工序集中与分散。
工序集中的特点是:
(1)可减少工件装夹次数,易保证位置精度;
(2)工序数少,减少了设备数量、操作工人和生产面积;
(3)可采用高效专用设备、工艺装备,提高加工精度和生产率;
(4)设备的一次性投资大、工艺装备复杂;
工序分散的特点:
(1)设备、工装比较简单,调整、维护方便,生产准备工作量少。
(2)每道工序的加工内容少,便于选择最合理的切削用量,对操作工人的技术水平要求不高。
(3)工序数多,设备数量多、操作人员多、占用生产面积大。
工序集中分散各有所长,工序集中优点较多,现代生产的发展趋于工序集中。
5.工序顺序的安排
(1)加工顺序的安排
1)先基(准)后(其)它2)先平(面)后孔3)先主后次4)先粗后精四个先后
(2)辅助工序的安排
1)检验工序
①粗加工结束后;
②重要工序前后;
③转向另车间前后;
④全部加工结束后.
2)去除毛刺
3)特种检验:
无损探伤、平衡试验
4)表面处理:
表面涂层、镀层
5)洗涤防锈
主辅工序的相对性
6.机床与工艺装备的选择
工艺装备直接影响加工精度、生产效率和制造成本。
机床尺寸规格与工件的形体尺寸相适应;
精度等级与本工序加工要求相适应;
电机功率与本工序加工所需功率相适应;
自动化程度和生产效率与生产类型相适应。
中小批条件下可选用通用工艺装备;
大批大量生产中可考虑制造专用工艺装备。
不仅要考虑投资的当前效益,还要考虑产品改型
及转产的可能性,应使其具有足够的柔性。
(三)加工余量、工序间尺寸及公差的确定
1.加工余量
(1)加工余量的概念
总余量Z0与工序余量Zi的关系:
ZO=ZI+Z2+Z3+….+ZI
单边余量
对于非对称表面,其加工余量用单边余量Zb表示
Zb=la-lb
双边余量
对于外圆内圆等对称表面加工余量用双边余量2Zb表示
\
双边余量:
外圆表面2Zb=da-db,内圆表面2Zb=Db-Da
单边余量:
由于各工序尺寸都有偏差,故实际切除的余量是变化的。
工序余量又分为公称余量Zb、最大余量Zmax、最小余量Zmin
对于被包容面(轴的外径),上偏差为0,其最大尺寸就是基本
尺寸,本工序的公称余量Zb=la-lb。
工序尺寸公差一般按“入体原则”标注:
Zmax=la–(lb–Tb)=Zb+Tb
Zmin=(la–Ta)–lb=Zb–Ta
工序余量变动范围
Tz=Zmax–Zmin=Tb+Ta
。
对于包容尺寸(孔径、槽宽),下偏差为0,其最小尺寸就是基本尺寸,本工序的公称余量Zb=lb-la
Zmax=(lb+Tb)–la=Zb+Tb
Zmin=lb–(la+Ta)=Zb–Ta
Tz=Zmax–Zmin
=Tb+Ta
(2)加工余量的确定
1)计算法
掌握影响加工余量的各种因素具体数据的条件下,计算法比较科学,但目前统计资料较少。
2)经验估计法
为避免出现废品,估计余量一般偏大,用于单件小批生产。
3)查表法
以生产实践和实验研究为基础制成数据表格,查表并结合实际情况加以修正。
查表法确定加工余量,方法简便,较接近实际,应用广泛。
2.工序尺寸及其公差的确定
1)工艺基准与设计基准重合
同一表面经多次加工才能达到图纸尺寸要求,其中间工序尺寸根据零件图尺寸加上或减去工序余量即可得到,即从最后一道工序向前推算,得出相应的工序尺寸,一直推算到毛坯尺寸。
(反推)
2)工艺基准与设计基准不重合
必须通过工艺尺寸的计算才能得到。
(换算)
例1:
简单工序尺寸及公差的确定
如图所示小轴零件,毛坯为普通精度的热轧圆钢,装夹在车床前、后顶尖间加工。
主要工序:
下料–––车端面–––钻中心孔–––粗车外圆–––精车外圆–––磨削外圆。
工序尺寸及公差的计算(单位:
mm)
例2:
以查表法确定工序余量,各加工方法按经济精度和相
应公差值,确定某箱体零件上孔加工的各工序尺寸和公差。
设
毛坯为带孔铸件,零件孔要求达到Φ100H7(+0.035),Ra为
0.8μm,材料为HT200。
其工艺路线为粗镗→半精镗→精镗→精密镗
3.工艺尺寸的计算
按尺寸链在空间分布的位置关系,分为直线尺寸链、平面尺寸链和空间尺寸链。
在尺寸链中,以直线尺寸链,即全部组成环平行于封闭环的尺寸链用得最多。
尺寸链:
由相互联系、按一定顺序首尾相接排列的尺寸封闭图。
根据用途不同分为工艺尺寸链和装配尺寸链
工艺尺寸链是由单个零件在工艺过程中有关尺寸形成的;
装配尺寸链指机器在装配过程中由相关零件的尺寸或相互位置关系所组成的尺寸链
(1)极值法解工艺尺寸链
1)工艺尺寸链的基本概念
A1和A2是在加工过程中直接获得,尺寸A0是间接保证的,
A1、A2和A0构成一个封闭的尺寸组,都叫尺寸链的环。
组成环:
加工过程中直接获得的尺寸如A1、A2是组成环;
封闭环:
间接获得的尺寸A0称为封闭环;
增环:
它增大将使封闭环随之增大的组成环,如A2;
减环:
它增大反使封闭环随之减小的组成环,如A1。
尺寸链计算的关键:
正确画出尺寸链图,找出封闭环,确定增环和减环
①作尺寸链图按照加工顺序依次画出各工序尺寸及零件图中要求的尺寸,形成一个封闭的图形。
②找封闭环根据工艺过程,找出间接保证的尺寸A0为封闭环。
③确定增环和减环可用以下简便的方法得到:
从封闭环开始,给每一个环画出箭头,最后再回到封闭环,像电流一样形成回路。
凡箭头方向与封闭环方向相反者为增环(如A2),箭头方向与封闭环方向相同者为减环(如A1)。
2)尺寸链的基本计算公式
用极值法解尺寸链的基本计算公式如下:
a)封闭环的基本尺寸等于增环的基本尺寸之和减去减环
的基本尺寸之和,即
b)封闭环的最大极限尺寸等于增环最大极限尺寸之和减去减环最小极限尺寸之和,即
c)封闭环的最小极限尺寸等于增环最小极限尺寸之和减去减环最大极限尺寸之和,即
d)封闭环的上偏差等于增环上偏差之和减去减环下偏差之
和,即
e)封闭环的下偏差等于增环下偏差之和减去减环上偏差之
f)封闭环的公差等于组成环公差之和,即
封闭环的公差比任何一个组成环的公差都大,应尽量选择最不重要的尺寸作封闭环;
为减小封闭环公差,应尽量减少组成环数及其公差。
计算尺寸链时,常遇到两种类型的问题:
1)已知全部组成环的极限尺寸,求封闭环基本尺寸及公差,称为“正计算”,结果唯一。
2)已知封闭环的极限尺寸,求一个或几个组成环的极限尺寸,称为“反计算”。
通常在制定工艺规程时,由于基准不重合而需要进行的尺寸换算属于这类计算,结果不唯一,需优化计算。
(2)统计法解直线尺寸链
统计法解算尺寸链的基本计算公式除可应用极值法解直线尺寸链的有些公式外,有以下两个基本计算公式:
1)封闭环中间偏差
Δi=(ESi+EIi)/2
2)封闭环公差
如图活塞上加工销孔,要求保证尺寸A0,设计基准
为活塞顶面。
为加工方便常用B面定位,按工序尺
寸A1加工销孔。
试确定工序尺寸A1及其公差。
(3)几种工艺尺寸链的分析与计算
1)定位基准与设计基准不重合的尺寸换算
解:
①作出尺寸链图;
②按照加工顺序确定封闭环A0;
③画箭头分出增环A2和减环A1;
④进行尺寸链计算
A1的基本尺寸A0=A2-A199=155-A1得A1=56mm
验算封闭环公差T0=T1+T2T0<T2修正T2=0.063
A1上偏差EIA0=EIA2–ESA1ESA1=(-0.063)-(-0.087)=0.024
A1下偏差ESA0=ESA2–EIA1EIA1=0–0=0
故工序尺寸A1为:
A1=56+0.024mm
2)一次加工满足多个设计尺寸要求时工序尺寸
及公差的计算
齿轮上内孔及键槽的
加工顺序如下:
工序1:
镗内孔至Ф39.6+0.062;
工序2:
插槽至尺寸A1;
工序3:
热处理—淬火;
工序4:
磨内孔至Ф40+0.039,
同时保证键槽深度43.3+0.2。
③画箭头分出增环A1、A3和减环A2;
④中间工序尺寸A1的计算
A1基本尺寸A0=A1+A3-A243.3=A1+20–19.8得A1=43.1
验算公差T0=T1+T3+T2T1=0.2–0.031–0.0195=0.1495
A1上偏差0.2=ESA1+0.0195–0ESA1=0.2–0.0195=0.1805
A1下偏差0=EIA1+0–0.031EIA1=0.031
故插键槽时的工序尺寸A1=43.1+0.1805
+0.031
(四)时间定额
在一定条件下规定生产一件产品或完成一道工序所耗时间
时间定额由以下几部分组成:
1)基本时间tm:
如机动时间
2)辅助时间ta:
装卸工件、开停机器、改变用量、测量尺
寸、进退刀具等
基本时间与辅助时间的总和称为作业时间。
3)布置工作地时间ts:
润滑机床、清理切屑、收拾工具等
4)休息和生理需要时间tr
单件时间tp为:
tp=tm+ta+ts+tr
5)准备与终结时间tbe:
一批产品只有一个tbe。
单件工时定额tpc为:
tpc=tp+tbe/n
(五)工艺方案的经济分析
通过比较不同工艺方案的生产成本选出最经济的加工方案
1.工艺成本的组成及计算
可变费用V与零件的年产量有关,包括材料费、工人工资、机器水电汽费、通用机器和装备维护折旧费。
不变费用C与零件的年产量无关,包括专用设备专用工艺装备维护折旧费等。
零件加工全年工艺成本S为:
S=VN+C
S与N是线性关系,即全年工艺成本与生产纲领成正比,直线的斜率为工件的可变费用,直线的起点为工件的不变费用,当生产纲领产生ΔN的变化时,则年工艺成本的变化为ΔS。
1.工艺成本的组成及计算
单件工艺成本St为:
St=V+C/N
在曲线的A段,N值很小,设备负荷率低,单件St就高,如N略有变化时,St将有较大的变化。
在曲线的B段,N值很大,大多数采用专用设备(C较大,V较小),且C/N值小,故St较低,N值对St变化影响较小。
表明:
当C值一定时(主要是指专用工装设备费用),就应有一个相适应的零件年产量。
所以单件小批生产时,因C/N所占的比例大,就不适合使用专用设备(以降低C值);
在大批大量生产时,因C/N占用的比例小,最好采用专用工装
设备(减小V值)。
St与N呈双曲线关系,当N增大时,
St逐渐减小,极限值接近可变费用。
2.工艺方案的经济评比
(1)采用现有设备或基本投资相近
1)比较各方案工序单件成本来评比
Sd1=V1+C1/N
Sd2=V2+C2/N
可直接计算比较或根据
曲线进行比较
N<Nk时,可选方案2;
N>Nk时,可选方案1
单件工艺成本比较图
Nk—临界年产量
(1)采用现有设备或基本投资相近
2)比较各方案全年工艺成本
S1=V1N+C1
S2=V2N+C2
N>Nk时,可选方案1;
N=Nk时,S1=S2,则
(2)基本投资相差较大应考虑投资差额回收期限
回收期是指一种方案比另一种方案多用的投资,需要多长
时间方能收回。
回收期可用下式求得:
T=k2-k1/{(s1-s2)+ΔQ}=ΔK/(ΔS+ΔQ)
式中ΔK—基本投资差额(追加投资)
ΔS—全年工艺成本节约额(追加投资年度补偿额)
ΔQ—先进设备使产品上市快取得的全年增收总额
回收期越短,则经济效益越好。
回收期是指一种方案比另一种方案多用的投资,需要多长时间方能收回。
T=k2-k1/{(s1-s2)+ΔQ}=ΔK/(ΔS+ΔQ)
投资回收期应满足以下要求:
1)回收期应小于专用设备或工艺装备的使用年限;
2)回收期应小于市场对该产品的需求年限;
3)回收期应小于国家规定的标准回收期,一般专用工艺装
备标准回收期为2~3年,专用机床标准回收期为4~6年。
常用的加工工艺规程有以下三种形式:
(1)加工工艺过程卡片
以工序为单位,主要列出零件加工的工艺路线和工序内容的概况,指导零件加工的流向。
在单件小批生产中,通
常不编制较详细的工艺文件,而以这种卡片指导生产。
(2)加工工艺卡片
以工序为单位,除详细说明零件加工过程,还具体表示各工序、工步的顺序和内容。
是指导工人操作和生产管理主要工艺文件,用于成批生产零件和小批生产的重要文件。
(3)加工工序卡片
以工序为单位,对各工序制定更详细、严密的加工规划。