完整版砂石骨料加工系统设计方案.docx
《完整版砂石骨料加工系统设计方案.docx》由会员分享,可在线阅读,更多相关《完整版砂石骨料加工系统设计方案.docx(34页珍藏版)》请在冰豆网上搜索。
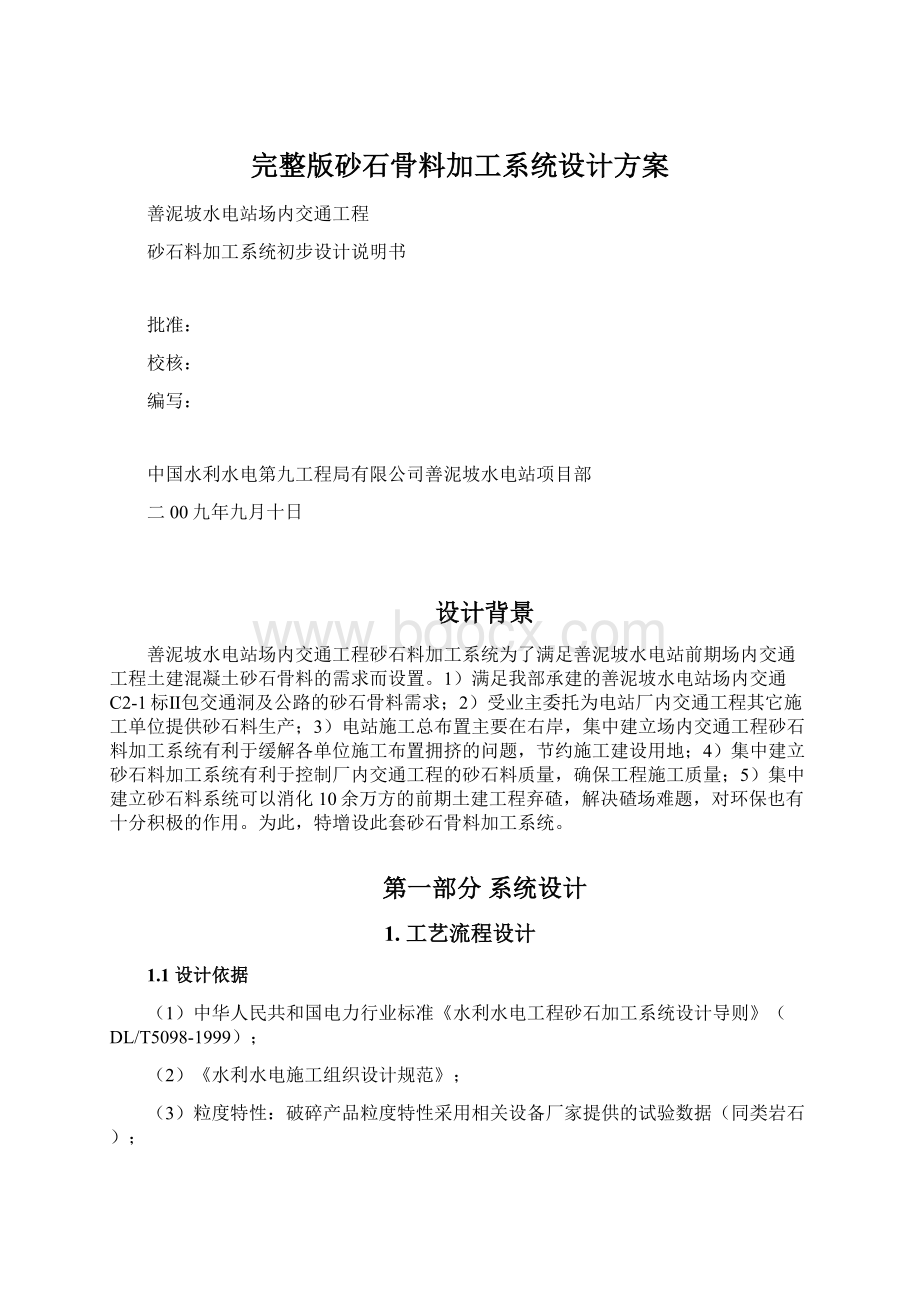
完整版砂石骨料加工系统设计方案
善泥坡水电站场内交通工程
砂石料加工系统初步设计说明书
批准:
校核:
编写:
中国水利水电第九工程局有限公司善泥坡水电站项目部
二00九年九月十日
设计背景
善泥坡水电站场内交通工程砂石料加工系统为了满足善泥坡水电站前期场内交通工程土建混凝土砂石骨料的需求而设置。
1)满足我部承建的善泥坡水电站场内交通C2-1标Ⅱ包交通洞及公路的砂石骨料需求;2)受业主委托为电站厂内交通工程其它施工单位提供砂石料生产;3)电站施工总布置主要在右岸,集中建立场内交通工程砂石料加工系统有利于缓解各单位施工布置拥挤的问题,节约施工建设用地;4)集中建立砂石料加工系统有利于控制厂内交通工程的砂石料质量,确保工程施工质量;5)集中建立砂石料系统可以消化10余万方的前期土建工程弃碴,解决碴场难题,对环保也有十分积极的作用。
为此,特增设此套砂石骨料加工系统。
第一部分系统设计
1.工艺流程设计
1.1设计依据
(1)中华人民共和国电力行业标准《水利水电工程砂石加工系统设计导则》(DL/T5098-1999);
(2)《水利水电施工组织设计规范》;
(3)粒度特性:
破碎产品粒度特性采用相关设备厂家提供的试验数据(同类岩石);
1.2设计原则
(1)确保善泥坡水电站厂内交通工程施工进度和工程质量,砂石系统设计遵循加工工艺先进可靠,成品砂石质量符合规范要求,砂石生产能力满足工程需要的原则;
(2)在保证砂石生产质量和数量的前提下,选择砂石单价相对较低,总投资相对较少的设计方案;
(3)为减小碴场容量、降低环保压力的特点,毛料采用开挖弃碴的方案;
(4)为提高砂石系统长期运行的可靠性,砂石系统加工关键设备采用技术领先、质量可靠、单机生产能力大、使用经验成熟的先进设备;
(5)充分利用地形地貌特点,使总体布置紧凑、合理、降低工程造价。
1.3料源规划
1.3.1料源
本标段施工混凝土13241m3(按招标文件工程量清单统计),估算前期工程其它单位施工混凝土用量30000m3,混凝土总量按50000m3计算,考虑路面碎石用量及其他因数影响,需要的砂石骨料约80000m3,考虑料源的利用率及损失系数,总共需要备石料约100000m3,本标段开挖石料可利用约60000m3,需外运开采料或崩塌堆积体可利用料约40000m3,统计情况如下表:
序号
部位
工程量(m3)
备注
1
路基挖石方
10000
主要用于路基填筑及浆砌石
2
右岸上坝交通洞
30000
3
右岸桥头交通洞
8000
4
左岸上坝交通洞
20000
5
合计
68000
为自然实方
(注:
表中可利用料均为估算量,实际可利用料需开挖时通过试验检验确定)
1.3.2回采(储备)料场
根据电站前期地形地貌情况及业主施工总体规划要求,回采(储备)料场主要考虑布置在2#公路进洞口处的3#堆渣场:
1)、3#堆渣场的挡墙施工按照业主及设计要求另行考虑,砂石系统布置场地一期场平时开挖的土石方弃料、2#公路路基开挖的土石方弃料以及交通洞明挖的土石方弃料等可作为3#堆渣场的填筑料,并经压实;
2)、2#公路右岸上坝交通洞和右岸桥头交通洞开挖时可利用的石料直接运至3#堆渣场作为储备料,不可利用的石渣可以作为3#堆渣场的填筑料;左岸上坝交通洞开挖的可利用的石料经施工索桥运至3#堆渣场作为储备料,不可利用的石渣可以作为3#堆渣场的填筑料;
1.4生产规模
1.4.1系统总统规模
根据本标段施工进度安排,本标段混凝土浇筑高峰强度为4000m3/月。
考虑因客观原因造成工期滞后而抢工期,以及其它施工单位混凝土浇筑的需要,砂石系统规模设计按混凝土浇筑10000m3/月考虑。
加工系统按2班工作制、每班8小时、每月按25天计,则月工作时间为400小时,每1m3混凝土用砂石骨料2.25t,砂石成品率统一按75%考虑,则小时生产强度为:
(10000×2.25)÷(25×8×2×0.75)=75t/h
考虑适当富余,系统生产能力按100t/h设计。
参考我局的施工经验,各粒径砂石骨料需要的比例见下表:
序号
骨料粒级
骨料需要量(%)
备注
1
80~40
5.0
2
40~20
28
3
20~5
32
4
5~0.15
35
5
合计
100.0
1.4.2各车间生产率
根据骨料的需求比例,结合系统工艺流程,各段砂石骨料加工能力分析如下:
1)、粗碎
本标段中预计有6万m3石料为隧洞开挖可利用料,另外4万m3需要外运开挖有用料,所有原料经过粗碎车间,从而达到了增加破碎段数降低砂石骨料中针片状成品含量,提高产品质量的目的。
粗碎车间生产率按系统的总生产能力100t/h设计。
2)、中碎
中碎车间主要是生产5mm~80mm的大石、中石,中碎成品料中各组种粒径料,可根据使用情况作为制砂原料,中碎车间的生产能力按大、中石的需要量设计,并考虑适当的富余。
需要的大石、中石占总量的33%,大、中石成品率按60%考虑(部分粒径小于20为小石或砂)。
P=100×33%÷60%=55t/h,中碎车间生产率按60t/h设计。
3)、制砂
砂石骨料中砂的用量占35%,根据我局的经验,砂石骨料加工系统中往往是砂的产量不足,制砂车间按总生产能力40%设计,同时有中碎车间产生的部分砂,制砂车间能满足要求。
制砂车间生产率按40t/h小时考虑。
砂石骨料车间生产率表
车间
设计生产能力(t/h)
备注
粗碎车间(t/h)
100
中碎车间(t/h)
60
包括部分细骨料
制砂车间(t/h)
40
1.5流程设计
1.5.1总流程工艺方案
砂石骨料加工系统以生产二级配混凝土骨料为主,兼顾一、三级配混凝土骨料生产路面填筑骨料生产。
为保证成品粗骨料的质量,控制针片状含量,采取减小多段破碎的工艺设计方案。
粗碎为开路生产,依次为粗碎车间、中碎车间、筛分车间及制砂车间。
1.5.2工艺流程过程
根据工艺要求,本砂石加工系统共由毛料处理(粗碎)车间、预筛分、中碎、筛分、制砂、检查筛分等车间组成。
具体流程过程如下:
回采场的毛料经装载机或自卸汽车运输进入设置好的宽为5m深1.5m的储料仓,储料仓中设有I16的字钢网格,并派专人人维护,以避免堵料;一旦发生堵料情况,我们将采用机械进行处理。
粗碎车间布置在储料仓底部。
粗碎车间设有一台PE600×900鄂式破碎机进行粗加工,粗加工后将毛料加工成粒径小于250mm的半成品,再经溜槽J1胶带机输送至预筛分车间。
预筛分车间布置在中碎车间进口,预筛分为一台固定式溜筛,筛孔尺寸为60mm×60mm半成品料由J1胶带机输送经预筛分分级后,大于60mm石料送往中碎车间进行第二次破碎(中碎车间共布置1台PF-1010反击式破碎机),破碎料与预筛分料一道由J2胶带机输送至筛分车间。
筛分车间布置1台3Y1545振动筛,设3层筛网,筛孔尺寸分别为40×40mm、20×20mm、5×5mm三种。
破碎料由胶带机输送至筛分车间进行分级,分级后,一部分满足成品用料的大石(40~80mm)、中石(20~40mm)、小石(5~20mm)分别由胶带机输送到各自成品仓中堆存,多余的大石(40~80mm)、中石(20~40mm)由胶带机分流输送至细碎车间,细碎车间布置1台PFC0909反击式破碎机,破碎后产品由胶带机输送进入检查筛分车间作分级处理。
检查筛分车间布置1台YZ1020圆振筛。
破碎产品分级后,大于5mm的粒径由胶带机返回细碎车间,〈5mm砂粒由胶带机输送到成品砂仓。
具体工艺过程详见《砂石生产系统工艺流程图》(SNP-C2-1标-SS-01)。
1.5.3防止骨料破碎、分离、混料的措施
骨料生产要经历多次转运环节,往往引起粗骨料的破碎、分离、混料,造成针片状、超逊径等问题的出现,在加工系统的设计中主要采取了一些针对性措施。
诸如,设计中力求减少骨料的转运环节,降低自由落差,避免料流的剧烈碰撞和急剧改向;大中石自由落差超过3m时,设置缓降器;胶带输送机的抛料点采用适当形状的溜筒;溜槽、漏斗下部设置有料垫区,减小冲击,同时对防尘、防噪也有好处。
1.6关键加工工艺
1.6.1粗、中碎加工工艺
介于粗碎是采用颚式破碎机,由于其产品粒形相对较差,针片状含量偏高,必须经二次整形加工后方可用于混凝土生产,为此在粗碎车间与筛分车间之间增加一套反击式破碎机,以改善产品粒形,同时为使粗碎与中碎产量的皮配,降低反击式破碎机生产能力,在中碎前增加一次预筛分,把小于60mm的筛过,使大于60mm的破碎料进入反击式进行二次破碎。
结合我局在构皮滩、大花水等项目的的施工经验,通过调整反击式破碎机筛篦的尺寸,可以将产品出料超径粒控制在2%以内。
1.6.2制砂工艺
人工砂生产是砂石骨料生产中技术含量最高、难度最大的环节。
目前国际国内常用的制砂工艺主要有棒磨机和破碎机制砂两种。
棒磨机是传统的制砂设备,国内应用较多,破碎机制砂目前国际上发展较快,应用亦越来越多。
用于制砂的破碎机种类较多,主要有锤式破碎机、卧式反击式破碎机、旋盘破碎机、惯性圆锥式破碎机和立轴式冲击破碎机等。
反击式破碎机出料粒径小、产量高、磨耗低、性能稳定、易维修等特点,适用于破碎各种中等硬度的脆性物料。
外形尺寸小,所需要的电机功率低,可以有效降低设备耗电量,反击式破碎机易损件使用寿命长,长期运行成本低。
针对上述制砂工艺的特点,结合我局索风营、大花水人工砂石骨料生产性试验中的相关成果报告,在本砂石系统工程制砂工艺设计中,决定采用以PFC0909反击式破碎机闭路制砂为主,根据需要可配以常规的锤式制砂机进行补充的工艺,以达到综合两种工艺的优点,取长补短,提高工效、降低钢耗能耗、确保成品砂的产量和质量,满足设计要求。
1.7设备选型
1.7.1粗碎设备
粗碎设备跟开挖料有关,根据本工程招标文件估计,约有6万m3洞挖料可作为利用料,另需外运约4万m3开采料或崩塌堆积体可利用料,此部分渣料破碎比较大。
根据工程特点,初步选定PE600×900颚式破碎机,其主要技术参数:
给料口尺寸:
宽600mm,长900mm;
推荐最大给料尺寸:
600mm;
出料粒径:
60~150mm;
主电动机功率:
75kW;
生产率:
60~100t/h;
重量:
15.2t;
1.7.2中碎设备
粗碎料进入中碎前需经过预筛分,小于60mm的级配料不需经过中碎,大于60mm的级配料按粗碎料的60%计算,相应中碎配置的反击式破碎机生产能力50~80t/h,初步选定PF1010反击式破碎机,其主要技术参数:
进料粒径:
≤250mm;
出料粒径:
≤50mm;
生产能力:
50~100t/h;
电机功率:
75~90kW;
重量:
12.5t;
1.7.3制砂设备
制砂车间制砂设备配备PFC0909反击式破碎机1台。
PFC0909反击式破碎机单机处理能力为20~40t/h,其主要技术参数:
转子工作直径:
900mm;
转子工作长度:
900mm;
最大入料粒径:
≤100mm;
出料粒径:
≤20mm;
处理能力:
20~40t/h;
功率:
75~90kW;
设备重量:
4.8t;
1.7.4成品砂检查筛分设备
成品砂检查筛分选用1台YZ1020圆振动筛,生产能力为8~60t/h,其主要技术参数:
单层筛网面积:
2m2;
筛网层数:
1层;
筛孔尺寸:
3~50mm;
频率:
930次/min;
最大入料粒度:
80mm;
双振幅:
6;
生产能力:
8~60t/h;
电机:
3kW;
槽面倾角:
15;
理论重量:
1.46t;
1.7.5筛分楼设备
筛分楼选用1台3Y1545振动筛,生产能力为50-120t/h