叶片制造工艺用于分析鼓包白丝等问题Word下载.docx
《叶片制造工艺用于分析鼓包白丝等问题Word下载.docx》由会员分享,可在线阅读,更多相关《叶片制造工艺用于分析鼓包白丝等问题Word下载.docx(26页珍藏版)》请在冰豆网上搜索。
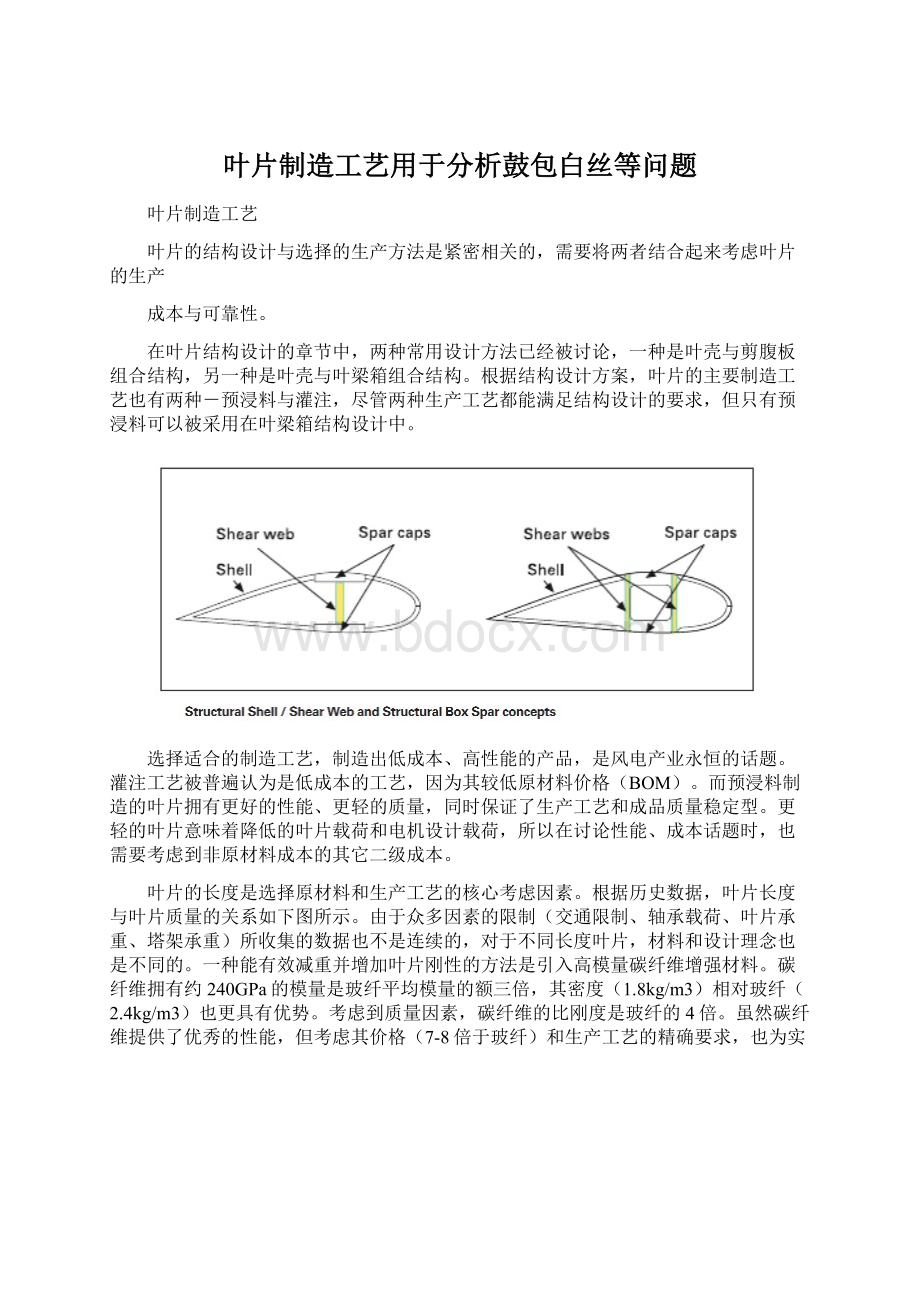
灌注的基本原则是将树脂在真空负压下作用被“吸入”增强纤维或纤维布中。
树脂灌注玻纤布的速度是由以下参数决定;
树脂系统的粘度η
玻纤布或增强纤维的浸润能力D
作用在灌注树脂的压强梯度ΔP
灌注速度v于上述三个参数的相关性为:
灌注速度与纤维浸润能力(D)正相关,与灌注压强梯度(ΔP)正相关,与树脂粘度(η)反相关
树脂粘度
在给定负压下,低粘度树脂保证了更快的流动性,树脂流过增强纤维层时受到的阻力也减小了。
好的流动性意味着可以减少树脂注入点,增大灌注构件同时减小灌注设计的复杂度。
树脂粘度由微观分子结构决定。
以环氧树脂为例,多数用于风电叶片灌注制造的树脂,以稀释剂降低标准环氧单体树脂的粘度值。
对树脂配方的调整要特别注意在改变粘度的同时不会对最终的机械性能和物理性能产生较大影响。
另一种提高灌注速度的方法是提高树脂温度,树脂的粘度是随温度升高而降低的。
加热灌注树脂的好处在于增加了树脂的流动性和浸润能力,减少了树脂注入点,增加了灌注工艺速度,但同时会伴随集中放热危险的加大。
粘度变化的规律引出了一个一般规律:
温度每上升10~15°
C,反应速度加倍,需要的固化时间将减半。
当液态树脂开始发生固化反应,其粘度会不断递增,直至形成凝胶现象,在固化的最后阶段硬化为固体。
粘度的增加限制了灌注工艺的继续进行,当未完全灌注就产生了树脂凝胶,将会导致很难修复的干纤维区域。
所以,灌注用树脂的设计需要考虑具体工艺的需要,以保证粘度和反应度的适中
渗透性
干纤维布或铺层的渗透性取决于以下几个因素:
纤维直径
纤维表面助剂
玻纤布的类型
玻纤与碳纤维在渗透性上具有显著区别,碳纤维的灌注难度明显加大。
这是由于碳纤维直径(5-10μm)小于玻璃纤维的直径(16-24μm),于是碳纤维束将更加紧密排布,妨碍了灌注树脂的浸润。
一种化学的表面助剂保护了纤维在编织时不被损坏,并增加了纤维与树脂的粘合能力以提高层合板的整体性能。
表面助剂的一个重要功效就是增加纤维与树脂浸润能力,这在灌注工艺中尤为重要,使得树脂能快速浸入并流过纤维铺层。
为了更好的供应和使用增强纤维材料,纤维是通过一多种排布方式供应的。
首先将成千根纤维集束成股。
纤维束或纤维股通过表面助剂成为一体,随后通过编织法或针织法成为玻璃纤维布。
更多玻纤布的信息可以从本公司的“GuideofComposite”一书中了解。
玻纤布的主要根据力学性能要求和纤维方向要求选择,在灌注工艺中还需要考虑纤维布的浸润能力
压力梯度
通过真空泵抽真空,外界大气压会使得封闭的真空袋内部产生负压,树脂即可被吸入负压的真空袋继而浸润纤维铺层,浸润的前沿和后沿会产生牵引力,牵引力是与纤维铺层的浸润性成正比,一旦纤维铺层确定牵引力将等于产生的压力梯度。
因为最大真空负压受限于外界大气压,高的压力梯度的保持与铺层的渗透性和真空吸口的分布有关。
当灌注件的形状和铺层厚度比较多变,真空吸口的分布和数量设置也就更为复杂,必要时可以采用电脑建模分析
抽真空和模具的需求
真空灌注几乎最重要的工艺参数就是系统和模具的抽真空质量。
最小的漏气也会导致空气被吸入铺层,铺层内的压力梯度能很快催生气泡并散布开来,最终带来成品的缺陷(如大量的气泡)和需要修补的区域。
所以真空系统和模具的真空度检查尤为重要,不容许任何漏气点产生。
模具真空度的检查是将透气毡铺于真空袋内并抽真空,当真空度稳定后用真空压力表测量系统真空度的变化。
在连通时所测真空压力应为一个大气压,随后在分离真空泵后系统会经历一个“真空压力下降过程”。
一般的,系统分离真空泵后,五分钟内负压降低不超过2.5%,则可视为真空度合格。
当然需要注意真空度测量点需要尽量远离真空进气口。
一些叶片生产工艺包括铺层前的胶衣涂层。
胶衣涂层的主要作用是提供一个易打磨的底漆表面,配合后续的上漆步骤。
同时,胶衣也起到密封模具表面的作用,形成更好的真空度
真空灌注的消耗材料不仅创造密封真空环境和压力梯度,而且还具有其他几种功能。
尼龙的peel
ply
(脱模布)层紧贴灌注件表面,在使用前可将脱模布撕下获得洁净表面。
脱模布上面有真空倒流网以增加真空灌注速度,可以根据具体铺层选用不同渗透能力的倒流网。
树脂供给管连接在倒流网上,保证树脂能流遍每一处。
最后使用真空袋罩住整个体系,并用真空胶带封闭模具四围以形成一个密闭区域。
真空工艺是需要一定操作经验支持的,从而可以保证系统完整的真空度。
树脂灌注工艺
进行树脂灌注工艺对于每个部件来说并不是一蹴而就的。
这种工艺众所周知的缺点在于潜在的不可缺定性――树脂是否能完全灌注以及系统真空度的保持。
这里需着重说明的灌注方法是边对边的或者中心对两边的灌注路径,这两种方法并不是所有的或对某些部件的最优方法,但成功率和适应性是非常不错的
灌注工艺基础
下图给出一个纯干布(无芯材)铺层的灌注例子。
该例子给出灌注工艺的关键点:
n采用多线树脂补给和设置倒流网有效增加灌注速度。
n树脂补给线需要设计并保证在没有被隔离的区域。
可以采用平行并排的补给线,如树脂从一边流向另一边,或树脂从中间流向两边,这比较适合简单几何外型的部件。
n在铺层上设置的倒流网可以加速树脂在铺层表面的流动行从而增加灌注速度,但可以导致铺层上下浸润面差距的产生,浸润面差距过大则会对整个工艺效果产生影响。
所以需要考虑在灌注结束前消除浸润面的不平衡,比如在关闭灌注工艺前检查系统上下面的是否浸润完全,或者考虑在树脂流端前停止设置倒流网以降低最后阶段的导流速度,保证上下浸润面的平衡。
n如果辅助供给线开启的过早,还没等上下两面的铺层都得到完全浸润,干斑就容易在浸润较慢的下层出现。
n如果铺层上下面浸润差距过大(经常出现在碳纤维灌注中),气孔和干纤的产生也是不可避免的,所以可以使用慢速导流网或阶段性灌注手断。
n避免选用低品质或气密性较差的真空耗材,如真空管、真空膜或树脂阀门等
n真空管进出真空系统的区域需要特别注意,因为在该区域最容易产生漏气现象。
n在灌注工艺前系统整体真空度的检查非常重要。
真空度由占大气压的百分比来衡量,如灌注系统的真空度需要大>
95%(95%的大气压),在检查真空度时将系统停止抽真空,并静置观察真空气压表的气压降,如果放置五分钟后系统气压降<
5mbar则视为正常。
n真空袋铺放时需注意防止铺层连接处形成中空的通路(真空短路桥接),否则会使树脂在此区域“快速跑动”导致灌注的不均匀和不可控。
n灌注停止后,真空需被保持至树脂完全凝胶并失去流动性,否则空气会通过流动的树脂不断渗入结构中。
n初步固化后,部件一般需要50°
C下后固化,后固化可以增强开模前的机械性能和力学性能。
纤维布的铺放
纤维布铺放前,首先需要贴好真空密封带(tacktape)以避免干纤维束混入影响系统的真空度。
铺放纤维布时也要特别注意避免纤维导通密封的真空系统,一旦导通就会出现局部的干斑。
可以通过事先裁剪玻纤布为合适的形状,适合铺放复杂形状的区域与角落。
真空灌注的耗材
在玻纤布的铺层以及后续耗材(peelply脱模布、倒流网、真空膜、真空导管)的铺放中,真空短路桥接和漏气是需要特别注意的,一种减少真空短路桥接的方法是尽量分片铺置耗材并提前进行真空压实处理。
真空袋必须是一个整体,以减小分片真空漏气的几率。
在抽真空时妥善铺摆真空袋和耗材的位置是需要经验和技术的,可以先以10-15%真空度调整真空袋和材料的位置后再完全抽真空进行压实处理。
除导流网外,需要使用树脂引流管在灌注初期快速分配树脂到相应的补给区,可选择的引流管包括螺旋引流管,该管在一个大气压下仍然保持坚硬的管型表面,同时树脂可以从螺旋的管缝中均匀流出。
树脂的准备
在灌注之前,还有一项准备工作是计算树脂混合量和混合后的操作时间,只有确定这两点,灌注工艺才能获得成功。
几乎所有类型的树脂(环氧树脂、乙烯基树脂、聚酯树脂)在混合灌注中都伴随放热现象的产生,放热是由于树脂从液态转化为固态,化学键结合时放热所致。
为激发反应的产生,会加入催化剂或固化剂,而反应的速度和所需时间也是有他们的性质决定的。
不同的灌注工艺,所需操作时间不同,如大厚部件的灌注需要慢速固化剂。
降低反应速度也就是树脂粘稠度增加的速度,保证完成灌注工艺充分的时间。
在保证工艺成功的前提下,当然需要优化设计灌注方案减小完成灌注时间和系统的不确定性。
树脂和固化剂(催化剂)混合以后,反应就开始缓慢进行。
当大体积的树脂一次性的混合,放热一旦发生就很难控制,热出的热很难释放则会产生集中放热与快速升温,加速了反应。
所以在灌注工艺中,树脂需要即混即用,需要提前安排好树脂的供应链和供应量。
可以在树脂即将用完时将刚刚混好续液树脂倒入桶中,同时保证桶中树脂的余量防止空气的吸入。
混合搅拌树脂时多少都会引入气泡,灌注件中的气泡会影响最终力学性能,可以使用真空罐对混合树脂抽去气泡或者采用专门的混合设备。
灌注
一旦全面抽真空,铺层会压实和层间导通会消失,系统气密性检查完成后即可进行灌注。
如果手动搅拌混合树脂,可以稍稍静置一下确保大部分气体已排出,树脂就绪后可以缓慢开起阀门让树慢速流入铺层中,初始阶段可以调慢灌注速率,过快操作容易产生铺层上下面过大的浸润面差距对灌注效果不利,同时可能过度消耗树脂对树脂供给不利。
灌注进行并得到很好控制时,新鲜树脂混合可以同时进行。
只有铺层上下表面的浸润面都超过灌注点时才能开启该点的阀门。
新灌注点开启后,附近区域的灌注速度会增加(压力梯度增加),不断重复此工艺直至灌注的完成。
在灌注完成后,可以关闭树脂吸入管并保持管口仍旧沉入液面下,同时将抽真空的压力调小,这样可以在保持系统真空负压状态下减少树脂被吸出的量。
开始静置灌注件直至树脂凝胶变硬,空气不能被吸入为止。
可采用提高环境温度的方法加速树脂凝胶速度,同时需要注意保持灌注的完整性。
固化
为了提高固化件最终力学性能,需要进行热处理工艺。
在常温下达到良好的固化效果需要4周时间,而实际生产中为了提高生产效率,起模时间需越快越好,可以采用加温固化工艺增加整体进度。
对于一个慢速固化的大灌注件,可以采用典型的16hrs@50°
C的固化工艺;
也可采用4hrs@70°
C加速工艺,具体温度需要考虑模具耐温状况。
另一种热处理可选方式是后固化。
如果模具的材料限制和设计精度决定不能承受太高温度,可以将灌注件停留在模具上直至完全固化,开模时固化件保持了良好的尺寸精度。
后固化的过程是将固化件放入烤箱以极慢的升温速度加热,缓慢的升温速度避免了固化件的变形,而更高的加热温度提高了固化件热学(耐热温度)和力学性能。
后固化同时提高了固化件的玻璃化转变温度Tg,材料的高温抗软化能力得到增强。
风电叶片的灌注
风电叶片几何构造不太复杂,是比较适合灌注工艺的。
然而叶片作为庞大的部件,三明治芯材区域的灌注,叶梁盖单向纤维的集中分布都为叶片灌注增加了难度。
叶片主要结构承力部件――叶梁盖的铺层是大部分是由单向纤维贯穿排布的(从叶根位置扑向叶尖位置)。
单向纤维的紧密排布增加了力学性能,但树脂的浸润能力却大幅降低。
可以采用的解决方案包括在单向纤维层间铺放增加浸润速度的编织玻纤布或者采用分离式灌注单独制作叶梁,剪腹板也可以采用分离制作的方法最后进行粘接组装。
一站式灌注方案(如同时灌注叶壳和剪腹板),可以减免二次粘接,但增加了结构的复杂度和灌注的危险性
对于制造商来讲,尽可能的提高工厂的货品周转,缩减单位叶片的制造时间,最有效率运用现有资源进行生产。
分离叶壳灌注中叶梁盖、剪腹板的制造,采用平行生产的工艺更加稳定,所以分离制造的方案更适合工厂。
最后,叶片灌注的着眼点就落在了其余部分,主要是三明治结构的生产制造中
三明治结构
仅由增强纤维(无论玻纤、碳纤维、芳纶纤维)制作的层合板在厚度方向上缺乏稳定型和刚度,同时结构缺乏厚度。
传统的增加刚度方式多采用多层板复合或增厚、复杂形状的方法,在现代复合材料技术中,被广泛应用的是增加结构刚度、厚度的泡沫芯材三明治夹心结构。
三明治结构有表面的加强板和中间的轻质夹心材料组成。
在层板间加入一定厚度的夹心材料可以在不大幅增加总量的情况下提高结构厚度,其增加刚度的原理和工字钢(梁)基本一致,工字钢中间的剪腹板将上下缘连接并减轻总重。
工字钢的上下缘主要承受拉伸压缩等载荷,而剪腹板承力则较少,三明治结构中的芯材同样也承力较少,载荷主要由高模量的复合层板承担。
设计理论近似认为板类挠曲刚度与其厚度的立方成本比,复合材料中引入夹心泡沫可4EE5在不明显增加结构重量的同时,通过提高层板厚度大幅增加结构整体刚度。
三明治结构的灌注
灌注工艺的一大优势可以将结构泡沫和铺层同时灌注一次形成三明治结构,一次制造大幅压缩了生产时间,而传统的三明治板制造是通过将板和芯材粘接而成的。
对大型三明治结构的一次性灌注其工艺难度将远高于简单结构,但是一旦工艺步骤确定下来,重复的操作将并不困难。
经灌注的三明治结构件重量会轻于手糊成型的三明治板,原因在于流入铺层和泡沫切槽中的树脂是刚刚好,而不是过量的。
为提高三明治结构的灌注效果,可以对芯材稍加改动以增加灌注流动性。
通过改变芯材与铺层间树脂的浸润速度,是提高灌注效率的关键因素。
可以通过多种方式实现此效果:
芯材可以通过开槽、打孔、表面槽、双面切槽等加工方式改变灌注速度。
通过选择不同形式的芯材,适应不同的灌注速度,尤其在使用慢速倒流网时也要同时注意选用慢速浸润的芯材配合达到灌注效果。
通过优化泡沫浸润结构可以明显提高灌注速度,同时减少了导流网的使用,铺放导流网中滞留的树脂损失也会降低。
同时需要了解的是,更多的开槽、打孔意味着留存更多的树脂,最终结构的整体总量会有所增加。
壳结构的灌注
在对现有灌注工艺进行核心开发和不断优化后,仍然无法克服一些潜在可改变的影响因素,如环境温度和真空压力。
在以前的讨论中曾经提到灌注工艺的速度和树脂的粘度以及与压力梯度是正相关的,而树脂的粘度对操作环境温度的变化非常敏感。
所以需要操作环境温度的持续不变性以保证灌注工艺步骤不受影响。
但是实际生产中,在气候温度变化较大的区域,在大型厂房中加装空调是高成本、高耗能的。
可以采用的方法是加热模具表面至环境可达到的最高温度如30-35
°
C
,这样既能保持灌注工艺的稳定性,也能通过降低树脂粘度提高灌注速度。
很遗憾,没有什么方法能有效的稳定真空压力,从而控制压力梯度。
提高灌注温度可以减小真空压力对工艺的影响,因为较低的树脂粘度下,铺层对树脂的阻隔能力也会减小,真空压力的转递效率增加了。
真空压力的变化同样也影响铺层的压实程度,对最终产品的厚度稳定型产生影响。
玻纤布铺层和芯材的铺放过程也是影响灌注工艺质量、重量稳定型的关键因素。
前面讨论的因玻纤布铺放不当的引起的空隙导通造成“短路桥接”现象,以及空隙通路所堆积的额外树脂都添加了工艺的不稳定性。
综合考虑所有的不确定因素,叶片的工艺和总重的稳定型令人担忧。
一套叶片安装在叶轮上是需要首先经过配重的,重量相近的叶片才能成套安装以减小作用在发电机上载荷的变数,不同重量的叶片同时安装对整机是不利的。
灌注叶片的结构粘接绑定
在叶片生产的最后阶段,制造完毕的部件需要经过梁壳粘接为一整体,在叶壳(带梁盖)和剪腹板的设计中,大量载荷是需要在不同部件间传递的,载荷从叶梁盖传递至叶壳再传递至剪腹板。
所以结构胶连接各个部件是非常关键的。
粘接时首先借助夹具将剪腹板粘接在下叶壳上,然后在上叶壳预先涂敷粘接剂,缓慢下降上叶壳至指定位置完成粘接,可以通过加热加速粘接剂固化速度以减小脱模时间。
然后将叶梁盖与剪腹板再次粘接,并用手糊工艺添加加强层,确保载荷在部件间的顺利传递。
制造高质量的绑定结构需要考虑一系列材料特性和工艺要求,几乎所有绑定接头设计的案例说明,最优化的绑定接头方案需要综合考虑结构设计、材料选择以及最后的粘接工艺
接头设计JointDesign
获得良好接头的第一步就是好的接头结构设计,优化接头的承载方式。
其它需要考虑的设计因素包括:
粘接工艺,周边结构,良好的工艺重复性和劳动力时间成本。
接头设计也需要注意粘接剂的用量,涂敷厚度和潜在的放热收缩等因素。
涂敷速度Dispenserate
和其它工艺一样,在保证粘接质量的同时,粘接工艺须完成的越快越好。
对于大型叶片更需要高效率的粘接方式并获得高质量、高精确度的粘接效果。
粘接剂的配方设计需要考虑适应高效率混胶机的涂敷工艺,涂敷后仍保持触变性(静置时抗下垂和流动的能力)。
这为配方的设计带来了挑战,混胶时会对粘接剂作用较大剪切力,此作用力严重降低了混合物的触变性
触变性和压缩性ThixotropyandCompressibility
叶片庞大的几何尺寸意味着即使粘接厚度达到了30mm也比较正常。
所以粘接剂必须达到30mm以上的厚度涂敷能力,即使在竖直面上涂敷也要具有良好的抗垂度。
通过了高剪应力的混胶机后,粘接剂有一定时间的剪切恢复期,竖直涂敷是更值得注意这点。
混胶涂敷后,叶壳的合模将实现上下两部分的粘接,粘接带会被合模积压,产生厚度的压缩和胶被挤出。
粘接剂的“压缩性”与其粘度和触变性紧密相关。
所以了解“压缩性”对确定粘接带的尺寸的使得粘接工艺具有稳定和可重复性。
放热与固化收缩ExothermandCureShrinkage
粘接剂的配方设计要满足优良的工艺属性,给予使用和完成粘接留出足够的工艺时间。
一旦粘接完毕接头形成,产品需要能够快速固化以适应高生产效率的和模具利用率。
粘接剂的配方设计,尤其控制其化学反应活性,相对于厚层接头的单纯放热反应要复杂的多。
放热现象是粘接剂在固化时产生的热量,由于周边的铺层或泡沫散热效果不佳形成了热量的积累。
放热现象带来的局部高温容易引发热收缩现象,同时带来接头的残余应力和应力集中。
所以粘接剂的化学配方需要考虑到控制放热反应,也需要调节配方缓解残余应力。
韧性Toughness
韧性可以定义为材料抵抗裂纹产生和扩展的属性,也是材料防止脆性断裂的能力。
韧性是粘接剂一个重要性能属性,即可防止固化收缩裂纹的产生,也可减缓叶片运行过程中疲劳裂纹的扩展速率。
所以风电叶片粘接剂配方设计上需要考虑加入一定的韧性,可以通过材料的断裂延伸率来衡量。
下面的曲线说明了不同韧性的粘接剂的断裂失效,红色体现为脆性材料而蓝色体现为韧性材料,被曲线包围的区域可以理解为断裂前材料所吸收的能量,所以可以用该图量化粘接剂的韧性。
预浸料技术
引言
预浸料(Prepreg)是Pre和impregnation的连写,是将增强纤维或纤维布预先与树脂浸润,获得均匀、稳定的中间产品,该中间产品可以作为制造复合材料成品部件的原材料。
预浸料的树脂都是半固态并带有一定的表面粘度,树脂的状态可以保证在常温下正常使用(如手动工序、裁剪、模具上铺层)且不会产生树脂的污染和损失。
一旦铺层结束可以通过抽真空加热固化法(温度一般在80
~
120
C)使材料固化成型。
预浸料通常以整卷供应,提供准确的树脂含量,树脂相对灌注或手糊具有更高性能,单向纤维达到准确垂直排布,快捷的使用可以实现自动化的生产和制造。
然而高性能树脂的预浸需要树脂升温和冷却系统,同时成品的储藏和运输需要冷藏,并增加了制造工艺成本,这些都是预浸料相对等量的灌注材料更加昂贵。
同时,提高温度的固化工艺,对模具的需求和成本也会提高。
预浸料的制造
预浸料的制造同样遵循树脂灌注速度的三个准则:
树脂粘度,压力的大小和纤维(玻纤布)的浸润速度。
树脂在生产工艺温度下的粘度η
纤维或纤维布的浸润能力D
作用于织布的压力P
三者的关系可以简单定义和正相关与预浸料设备的生产线速度PLS
所以要提高生产线速度,树脂的粘度要低,一定的压力需要施加,纤维或纤维布的浸润性需要考虑。
因为预浸料树脂在常温下的高粘度可能达到预浸效果,所以产生了两种截然不同的预浸料制造方式:
溶剂稀释树脂;
通过加温降低粘度,第二种方式是风能用预浸料的主要制作方法。
为了大幅提高预浸料工业成品的产量和价值目标,产线速度须越快越好,这需要大幅提高树脂温度的同时增加预浸压力,成品收卷前需要快速冷却产品。
所以生产预浸料的机器需要配备大型加热和压实系统来尽可能提高生产速度。
步骤1将树脂加工为树脂薄膜并加载在蜡光纸面上
步骤2:
纸面的树脂膜与纤维布合并(未预浸),同时在另一面加盖蜡光纸
步骤3a:
纤维/树脂/蜡光纸共同经过加热区域来减小树脂粘度
步骤3b:
纤维/树脂/蜡光纸共同经过夹紧轴使纤维获得树脂的预浸
步骤4:
通过冷却板快速冷却树脂
步骤5:
蜡光纸脱离
步骤6:
材料上下面加铺保护膜(Polyethylene/polypropylene)在保护材料的同防止在收卷时材料粘合
步骤7:
成卷预浸料放入冷库冷却延长使用寿命`
对生产线速度的精确控制对减小预浸料成品缺陷有重要作用。
加热熔融的树脂在高温停留较长的时间会产生过量的反应,导致产品变硬、表面粘度降低、使用寿命减少。
预浸料特性
评价灌注树脂性能时,通常着眼于树脂的粘度和不同温度下的反应活性,与某些标准纤维复合固化后的热学和力学性能也会予以考量,数据可以对较树脂体系的优良程度。
对预浸料而言,成型过程中的粘度和反应活性同样得到重视,特定产品的力学和热学性能变得更容易衡量,同时增加了一些定义操作特性的参数。
随形性(Drape)
将高粘度树脂和纤维/纤维布预浸在一起的工艺,材料能否满足模具几何形状的要求非常重要。
预浸料与模具表面的贴合程度被称为随形性,这种性能与纤维/纤维布结构(纤维类型、方向、缝合方式等)以及树脂化学特性密切相关。
粘性
虽然预浸料中的树脂在室温下呈半固态,预浸料表