m100总则doc文档格式.docx
《m100总则doc文档格式.docx》由会员分享,可在线阅读,更多相关《m100总则doc文档格式.docx(55页珍藏版)》请在冰豆网上搜索。
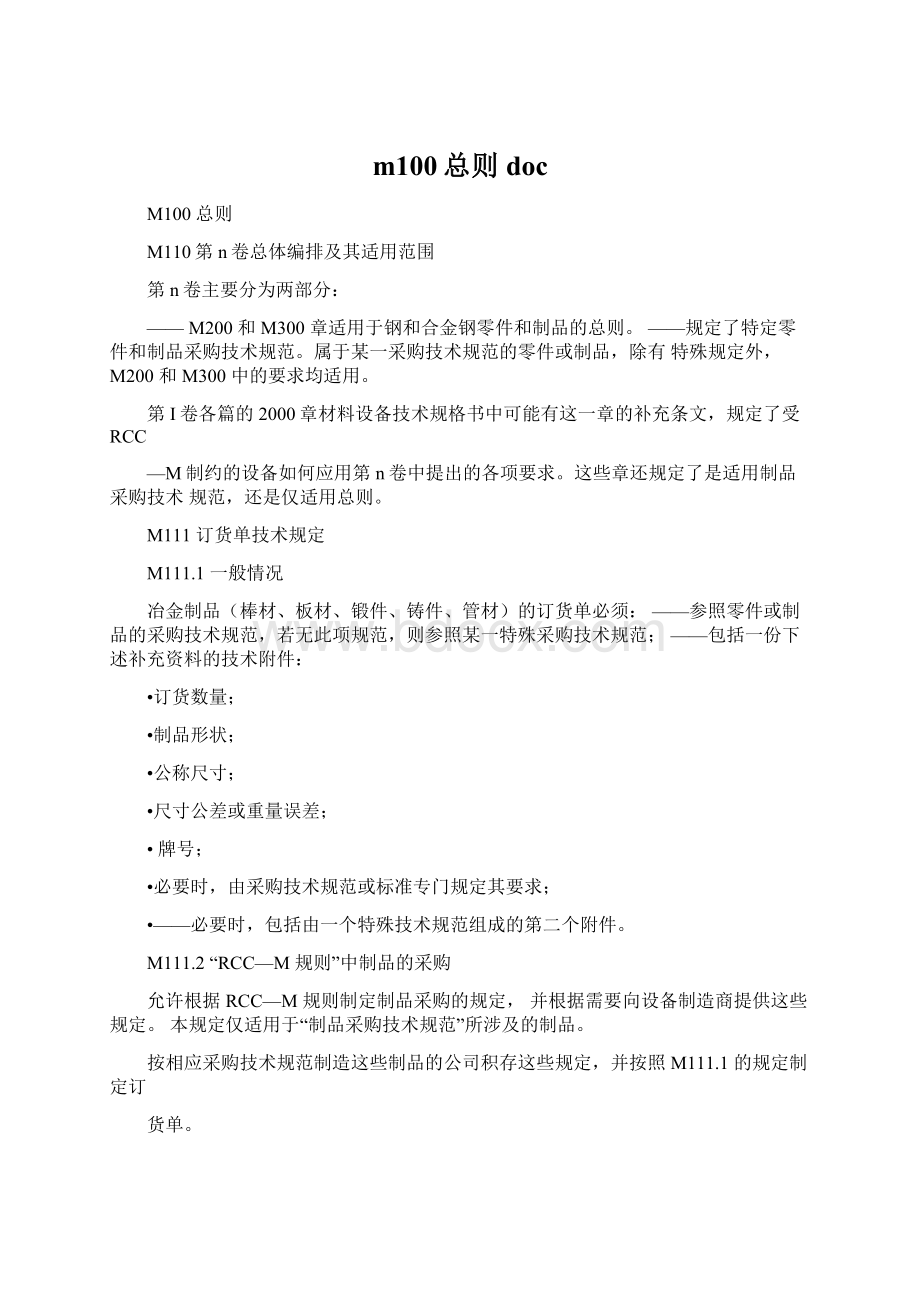
凡属零件技术采购规范范围内的零件采购问题,制造商必须参照零件采购技术规范,而不能参照制品采购技术规范,尽管制品采购技术规范的适用范围也包括了这些零件。
M113制造零件的新方法和新材料的技术鉴定
如果考虑用一种新方法制造某一零件,必须在新方法实施之前,制定一个新的零件采购技术规范。
该规范必须由制造商和AFCEN共同制定。
新规范必须编入RCC—M中,零件或制品
采购技术规范采用的新牌号也按此规定。
制定这些新规范时,必须按照M140规定所提供的所用材料的鉴定报告。
根据第I卷各篇中2000章的规定,有些零件与制品仅能遵照M200和M300的总则时,对于这些零件与制品的采购,制造商经严格选择后,通常采用一种同总则不抵触的现行标准和规范。
否则,制造商必须自行制定一个特定的采购技术规范,该规范须按同类型采购技术规范编号,并与M200和M300的总则相符合。
M120力学性能
M121钢的最高抗拉强度
用以制造高质量等级在C5120和D5000规定的2级和3级承压设备的钢,室温下最高抗拉强度和断裂时的延伸率应满足以下要求:
a)对于承压设备的钢,但不包括压力边界,其断裂时的延伸率A,和可能时材料的抗拉强度R应满足:
——对于连接件应满足以下条件:
A>
12,并当12WAV20时,RA>
10500。
——对于其它零件,至少满足以下两个要求中的一个:
对使用过的零件:
20在这种情况下,零件的使用应不改变任何力学性能例如降低零件的安全性。
对新零件,RA>
10500,同时A>
14。
以上表达式中抗拉强度的单位是MPa,断裂时的延伸率的单位是%,试验应按照
MC1200规定的拉伸试验进行。
b)另外,焊接用不锈钢的抗拉强度不得超过800MPa,其它钢种不得超过700MPa。
M122经消除应力热处理的钢
当M300章的总则或采购技术规范规定,验收前要考虑零件在制造过程中所经受的热处理时,制造商在某些情况下,可对2、3级设备的零件和制品所用的材料,仅在性能热处理
后检查其力学性能。
制造商的这种情况须通过报告书予以证实,该报告书须证明由于进行了消除应力热处理引起力学性能降低的情况,并必须证明在确定许用应力时,已考虑到这种性能的降低。
M123试料保管剩余试块及用于验收的试样必须由供货商予以保管,并从零件验收之日起至少保管12
个月。
这些规定适用于零件采购技术规范所规定的零件,且对于制品采购技术规范限定的制品,也建议采用这些规定。
M130残留元素
a)在进行比验证规定元素含量的分析更为全面的补充化学分析时,其结果须显示的仅是试样通常的残余元素含量,而不是规定元素的含量。
通常,由于硼对可焊性不利。
因而规定奥氏体不锈钢中不加硼。
浇包样品分析中的残余硼含量都不得超过0.0010%。
即使在采购技术规范中没有规定测定硼的含量,也必须在化学分析的报告中注明硼的含量。
b)上述a)项第一段涉及的元素如下:
1)同反应堆冷却剂相接触的材料有:
——铅、汞、硫、磷、锌、铬、锡、锑、铋、砷、铜、稀土元素(铈、镧)。
2)与二回路相接触的材料有:
——低熔点元素及其化合物、特别是铅、汞、砷、硫。
M140制品和车间的技术鉴定
M141适用范围
M140的规定适用于零件采购技术规范所规定的所有以下零件及制品:
——反应堆压力容器:
顶盖;
顶盖法兰;
筒体法兰;
管嘴座;
筒体;
过渡段;
底封头;
进口管嘴;
出口管嘴。
——蒸汽发生器:
椭圆形顶盖;
圆柱形筒体;
锥形筒体;
管板;
蒸汽发生器管;
支撑环;
分配板。
——稳压器:
顶盖;
底封头。
——反应堆冷却剂泵:
壳体;
主法兰;
电动机机座(该机座为承压设备的一个部件时),泵轴;
电机连接套筒;
环绕管;
电机轴;
飞轮。
——一次侧冷却剂管道:
管道;
弯头;
安注管斜接头。
——压力波动管路:
管路。
——阀门:
公称直径大于200mm的1级设备用阀门或锻造阀体;
蒸汽闸阀阀体;
蒸汽发生器供水管道调整阀阀体。
——反应堆堆内构件:
堆芯支撑件;
密封环;
上部支撑板。
——主蒸汽供应系统:
无缝钢管。
M142慨述在使用指定车间按规定的生产工艺所制造的某种制品前,须进行下述评定:
——制品的技术鉴定;
——车间资格评定。
制品鉴定按M143的规定进行,以保证预期的适用程度,并保证操作验收及验收准则具有代表性。
然后根据采购技术规范中规定的一系列“验收试验”采购制品。
只要符合M144的规定,则在同一公司里更换车间可不再要求作制品技术鉴定。
M143产品或部件的鉴定
M143.1适用范围
本鉴定用以检查按规定的程序制造的制品或零件,对生产操作和使用条件将具有满意的性能。
鉴定过程中可弄清其特性,尤其是特殊性及可试验性。
M143.2鉴定报告
M141所述的零件或制品,在采购之前必须作出鉴定报告,报告中须写明下列要求的所有要素与资料。
该报告必须由制品供应商提出,并包括下述文件:
——制造程序(见M143.5);
——核查制品或零件性能的试验规程(见M143.6);
——试验结果。
注:
对具有按类似程序制造类似零件经验的供货商,性能验证试验程序可以按比例缩减,其鉴定报告可以用以前制作的存档资料予以补充。
M143.3鉴定的有效性制品鉴定报告必须明确下述内容。
改变任何一个认为足以影响鉴定的系数或参数时,须通知供应商,并须对这一改变的可能后果作出评价。
根据评价结果,作出以下不同决定:
——鉴定继续有效;
——进行补充试验后,鉴定继续有效;
——制品或零件必须予以鉴定或重新鉴定。
M143.4材料牌号承包商或制造商一般根据设计准则确定材料牌号,设计准则要考虑尺寸大小,加工制造
(可焊性)和使用条件(腐蚀、辐射等)。
M143.5制造程序根据承包商确定的范围,供应商认为能直接影响制造质量的“主要”参数,必须规定并
列入制造程序。
至少考虑以下在a)、b)、c)、d)、和e)节规定的几点。
在某种特殊情况下,采用这些规定会遇到困难时,他们应被告知并相应地修改制造程序。
此外,供应商会感到需要在制造程序中规定一些特殊要求(检验和/或控制程序),以保
证制品的质量或适应性,特别是保证没有裂纹、偏析裂纹等缺陷存在。
a)锻件:
——原材料;
——熔炼工艺;
——要求达到的化学成分;
——钢锭的重量(及类型);
——头尾切除的最小百分率;
——零件在钢锭中的位置;
——按时间先后排列的各个工序;
•冶炼工艺;
•锻造;
•机加工;
•热处理;
•取样;
•无损检验。
——每次锻造后的零件外形尺寸图,包括按M380确定的锻造比或总缩小比;
——零件锻造毛坯外形图、热处理外形图和交货外形图;
——中间热处理和最终热处理(性能热处理※);
——验收试验和试料在零件上的位置;
——试料上截取试样的位置图。
b)铸件
——原材料和型砂;
——铸造工艺;
——验收试验用试料截取方法和试样截取方向;
•铸模烘干、熔炼工艺;
•浇注和脱模;
•修补;
•试料截取;
——零件铸造毛坯外形图、热处理外形图和交货外形图;
※
——中间热处理和最终热处理(性能热处理※)
c)板材
头尾切除的最小百分率;
板材在钢锭中的位置及取向,特别是相对钢锭轴线的最终轧制方向;
按时间先后排列的各个工序;
•粗轧;
•轧制;
•试样截取;
——主要轧制方向的标志;
——验收试验用试料的位置;
——试料上截取试样的位置图
d)管材
——板材在钢锭中的位置及取向,特别是相对钢锭轴线的最终轧制方向;
——按时间先后排列的各个工序;
•冶炼工艺(若重熔炼,包括钢锭性能“应该是钢包精练”);
•锻造或热轧,棒坯剥皮;
•机加工;
•冲孔(有时);
•挤压成形(有时)
•轧制或冷拔
•试样截取;
•精加工(矫直、弯曲、切割、磨削、抛光、清理);
——截取试料和试样的位置图。
见热交换器管的特殊情况(见M170)。
e)制品的其它类型:
圆材或扁材
根据制造工艺采用a)、b)、c)或d)节。
M143.6制品性能检验
根据上述要点,必须对制品进行检验和测定,以便:
——验证制品的内部质量;
——评定制品的化学成分和力学性能的均匀程度;
——仔细研究制造程序中特别注明的特殊区域。
必要时,获得这些区域材料性能的有效数据;
——保证验证试验具有代表性(就零件而言),以便使无损检验方法适应零件形状和适应这种制造工艺所引起的缺陷类型。
a)制品的加工性能按RCC—M其它各卷评定;
——可焊性,见第"
卷S1200—S3000;
——成形,见第V卷F4120;
对于这些特性测定的重要数据,可参见工业技术资料,以及参照采用其它同类制品的资料,在此情况下,必须证明这些参照资料的有效性。
b)就铸件而言,样件(见M160)是零件鉴定的一个要素,该样件可用于检验制
品的性能。
c)热交换器管材则在按M170确定的预制批上进行制品性能检验。
M143.7验收试验收集到数据以后,可以确定:
——验收试验的检验用以证明制品质量的稳定性;
——检验准则应考虑到制造中的偶然事故,实际要求及最佳经济效益。
必须正确认识制品鉴定与其验收要求之间的关系。
鉴定检验可以用于不同采购技术规范原先规定的验收试验。
M144车间的资格鉴定
M144.1适用范围鉴定的目的中要证实供货商有足够的能力制造出符合设备技术规格书及验收试验准则的制品(必要时鉴定制造工艺)。
M144.2资格鉴定报告制造M141规定的零件或制品的车间,在供货前必须提供鉴定报告。
该报告必须由零件或制品的供货商提供,且报告中须提出以下数据或资料的详细说明。
M144.3鉴定的有效性在供货商的鉴定报告中必须论述以下各小节的范围和内容。
对影响鉴定的参数或该鉴定的有关制品有所更改,应对其可能造成的后果作出估计。
供货商报告中的论述结果必须是下述结论之一:
——鉴定继续有效或延期;
——进行一定数量的补充检验后,鉴定继续有效或延期;
——车间必须鉴定或重新鉴定。
M144.4设备车间必须具备符合要求的设备。
必须提供下述设备的使用说明(包括所在位置的说明)。
——炼钢和成形用的主要设备;
——热处理设备;
——破坏性试验设备和无损检验设备;
——化学分析和金相研究的主要设备。
如果供货商的车间不具备相应的热处理设备或检验设备,供货必须在鉴定报告注明分包商从事这些活动具备的条件,并必须提供有关使用方面的资料。
M144.5人员和编制所有人员须具有必要的技能和资格。
人员一般归属于车间。
M144.6生产经验
a)生产对每一种熔炼工艺和制品的加工过程须提供以下资料:
——每种类型牌号(或钢种)能供给的吨位;
——制品的外形和/或允许的尺寸(重量、厚度、长度等);
——新产品的主要用户和主要用途;
——通常使用的技术规范类型(规范、标准、规则等);
要使供货商制造的产品(必要时经过鉴定)尽量同其总体产品及其同类型产品(牌号、
尺寸、成形方法)相似。
b)开发条件必须以下述方式指出影响供货的现行或预期进行的开发工作:
——开发条件简介;
——牌号的研究与开发;
——出版物。
有关焊接工序参照第"
卷S6000对评定的要求。
M150热处理热处理必须按照F8000的规定进行。
注:
如果采购技术规范规定必须将热电偶放置在制品或部件上,且采购技术规定采用
F8140,仅在此情况下,则可不采用本规则。
M151模拟热处理当采购技术规范规定的验收程序,必须考虑到零件在以后的制造加工中所经受的热处理时,从随后进行性能热处理的零件上截取的试块必须要经受模拟热处理。
如果在采购技术规范中没有规定进行模拟热处理的程序,承包商须向制品或零件的供应商提供该程序。
需要时这些程序须列入制造程序。
当模拟性能热处理或消除应力热处理时,还必须满足下列要求。
M151.1模拟热处理当在设备技术规格书中规定的模拟热处理,包括回火时其最低保温温度必须精确到±
5C。
M151.2模拟消除应力热处理模拟消除应力热处理,必须考虑到零件在以后加工制造中实际要经受的全部消除应力热处理。
该热处理的特征如下,尤其是:
――额定保温温度(精确到土5C)必须是:
其相应的温度区间要于制造过程中审定的最大区间一致;
――保温时间必须至少是制造过程中实际进行的各个热处理的保温时间总和的80%。
该保温时间须考虑到制造过程中可能要作补充热处理的时间。
在温度超过400C时的加热和冷却速率必须符合S7544d)的规定。
M160样件
M161目的和定义样件的主要目的是按某一批铸件产品进行选择制造方法的试验。
因此样件必须经受:
――无损检验和最终的破坏性试验,要对零件进行整体检验,以保证无不可验收的缺陷;
外观检验(目检、液体渗透或磁粉检验)须按相应的采购技术规范进行。
如果供货商以前从未制造过这种零件,则按给定的制造程序(见M164)所制造的第一
个零件就认为是样件。
如果供应商过去在车间内制造过同样的零件,且其制造方法也相同,无损检验或破坏性试验又能查明零件各部位都能满足要求时,则供应商可建议不制造样件。
对不受M140限制的少量铸件订货,供应商可不生产样件,但在按合同验收阶段,除按采购技术规范规定检验外,要对设计零件(按M163准则)进行100%射线检查。
M162适用范围
――按制品采购技术规范制造供货铸件时,必须制造样件。
――按零件采购技术规范采购时,把制造的第一个零件作为样件。
该样件是鉴定的一个要素之一。
(M140)。
只有材料的制造商,一般地说也就是承包商,对于与M140有关的零件,分析其样件的检验结果后,才能开始制造成批的零件。
M163样件的检验条件M163.1内部缺陷检验在补焊前进行无损检验。
内部缺陷检验主要采用射线照相检验。
在该项检验前,应使铸件表面无缺陷(例如浇注口、冒口……),并按供货外形图去除
加强部分。
此外,最后需在制造厂对全部表面都将进行机加工的样件应征得制造厂同意,在铸造车
间尽量粗加工到接近最后尺寸。
去除外观检验探测到的缺陷。
在这种情况下,去除缺陷的深度应限制在缺陷处壁厚的5%,即使不能完全去除缺陷,该处的去除深度也不应超过10mm。
然而,由于清除缺陷造成壁厚减小的最大量为:
——壁厚20—60mm时,为3mm;
——壁厚20mm或小于20mm时为2mm。
缺陷打磨区须平滑过渡到邻近表面,以便不妨碍射线照相检验的判断。
在不可能用射线照相对整个零件体积进行检验时,射线照相的最小区域应如MC3240
图示。
在此情况下,可考虑用超声波进行补充检验。
这些检验原则上按MC3000和MC2000
的规定进行。
然而供货商可采用不同措施,以扩大检验区域。
当无损检验不能有效地检验整个体积,或不能确切断定样件质量时,可进行破坏性试验。
须绘制标有采用不同检验方法的零件图,并将该图交给制造商和承包商保管。
可记录的条件及验收准则
a)射线照相检验不得有热裂纹、裂缝、芯撑残片和冷铁残片等缺陷存在。
由AFNOR标准NF04—160规定的可适用的验收准则如下:
——焊缝边缘:
按1级严重程度;
——零件的其余部分;
1级设备:
按2级严重程度;
2级设备:
管嘴按2级严重程度,零件的其余部分按3级严重程度;
3级设备:
按3级严重程度。
——铸件的特殊情况,当其壁厚小于或等于25.4mm时,用石蜡精密铸造。
表I给出了适用的准则和按ASME192标准规定的参考底片,以及参考底片与上述严重
程度的关系。
注意:
当出现不连续的若干类型缺陷时,其程度等于选择的每种类型显示的允许最严重程度的值,须判定该铸件不可验收。
b)超声波检验以下情况必须作为可记录条件:
——所有大于或等于参照曲线50%的底面回波衰减幅度的显示值;
——所有底面回波衰减幅度大于18dB的区域;
——底面回波衰减幅度大于参照曲线高度,且其表面积大于或等于100mm2的显示值。
c)样件的判断(由内部缺陷检验探测的缺陷)
1)缺陷超过规定标准,但是一种数量不多且是偶然产生的缺陷(如夹砂),因此不能否
定该铸造方法;
2)缺陷超过规定标准,并是一种直接与铸造方法有关的缺陷(浇注不良引起的缩孔或凝固裂缝等)。
必须改进铸造方法,重新制作样件,并在改进样件的全部相关区域检查其改进的有效性。
如果检验的结果是满意的,该样件的记录要特别注意,须包括第1和第2样件的检验结果;
如若不然,还将需要一个新的样件。
3)在有许多缺陷超过规定标准的情况下(偶然的或/和铸造方法有关),重要的是必须
选择铸造方法,这必然导致精心制作新样件(100%体积检验),并进行必要次数的重复操作。
样件的检验结果记入由供货商编的记录卡中,并由零件的制造商和承包商保管。
特别要注意,该记录卡中有一注明射线照相源与底片的位置图,以供零件检验时参考。
M163.2外观检验(目检、液体渗透或磁粉检验)
体积检验后,铸造厂可向零件制造厂建议,经修理后样件可考虑作为产品零件(在这种情况下,样件须按产品零件采购合同文件的要求修补和检验)。
a)阶段、范围、检验条件和准则
见采购技术规范(或M360):
外观检验——表面缺陷。
b)对样件的判断
如果外观检验显示的缺陷会导致大的修补,才能恢复到原来状态,这需要在样件记录卡中说明。
外观检验以后,经过若干大的修补工作可能会使样件报废。
M164有效范围
限定样件有效范围的主要因素至少有:
——铸件图;
——铸造车间;
——材料牌号;
——炼钢工艺;
——按冒口分布图确定铸造工艺;
——面砂类型。
在采购过程中或在新的采购中要改变任一参数时,通常可由零件制造商和与M140有关的零件承包商要求重新审查存档资料,并可要求制造一个新样件。
对制品零件,有影响一炉料的偏差(外观检验和内部缺陷检验后,有不可接受的缺陷)都要经过仔细分析,它可能使样件报废。
在这种情况下,制造商(或按M140制造的零件承包商)都需要重新检验样件记录和制品零件的检验条件。
这可能引起下述结果:
——制造方法作废;
——如果样件的记录适用,则可根据适用的采购技术规范,补充无损检验。
M170热交换器管的管材预制批
M170.1定义和目的预制批是由任意限量管材所组成。
其制造条件与工业钢管的制造条件相同。
该限量钢管的生产应有可能:
规定实际制造条件和参数,制订预制批实施程序(见M170.5)中要求的无损检验方法,并注明达到质量等级遇到的困难;
——评定由制造程序、材料种类、或制品尺寸特性引起的特有类型缺陷,以便建立缺陷一览表(M170.6);
——在上述结果的基础上制订一批工业钢管的加工程序(见M170.5)。
M170.2预制批验证报告
首先,按M170规定试制预制批钢管的验证报告必须包括:
制造程序(见M170.5)。
缺陷一览表(见M170.6)。
预制批验证报告及其相关文件应由供应商完成。
制造商考虑要改变制造程序中的一个基本参数时必须得到承包商的认可。
在制造商和承包商的地区代表尚未认可预制批的验证报告之前,不应开始一批管材的制造(定货单中包括的)见M140。
M170.3范围
以下情况必须制作预制批:
——制造商根据RCC—M规则第一次生产该类型产品;
——制造商考虑要改变以前工业制造中使用的制造程序中的一个基本参数时;
制造商若能提供以前进行过的预制批鉴定报告,或以往制造相同制品的试验结果,只要所有涉及到的试验结果能满足预制批的要求,并该报告附有相应的制造程序,则可以不进行预制批的制作。
M170.4预制批实施条件
制造商在预制批投产前须制订:
——符合M170.5规定的制造