数控机床与加工工艺Word文档格式.docx
《数控机床与加工工艺Word文档格式.docx》由会员分享,可在线阅读,更多相关《数控机床与加工工艺Word文档格式.docx(16页珍藏版)》请在冰豆网上搜索。
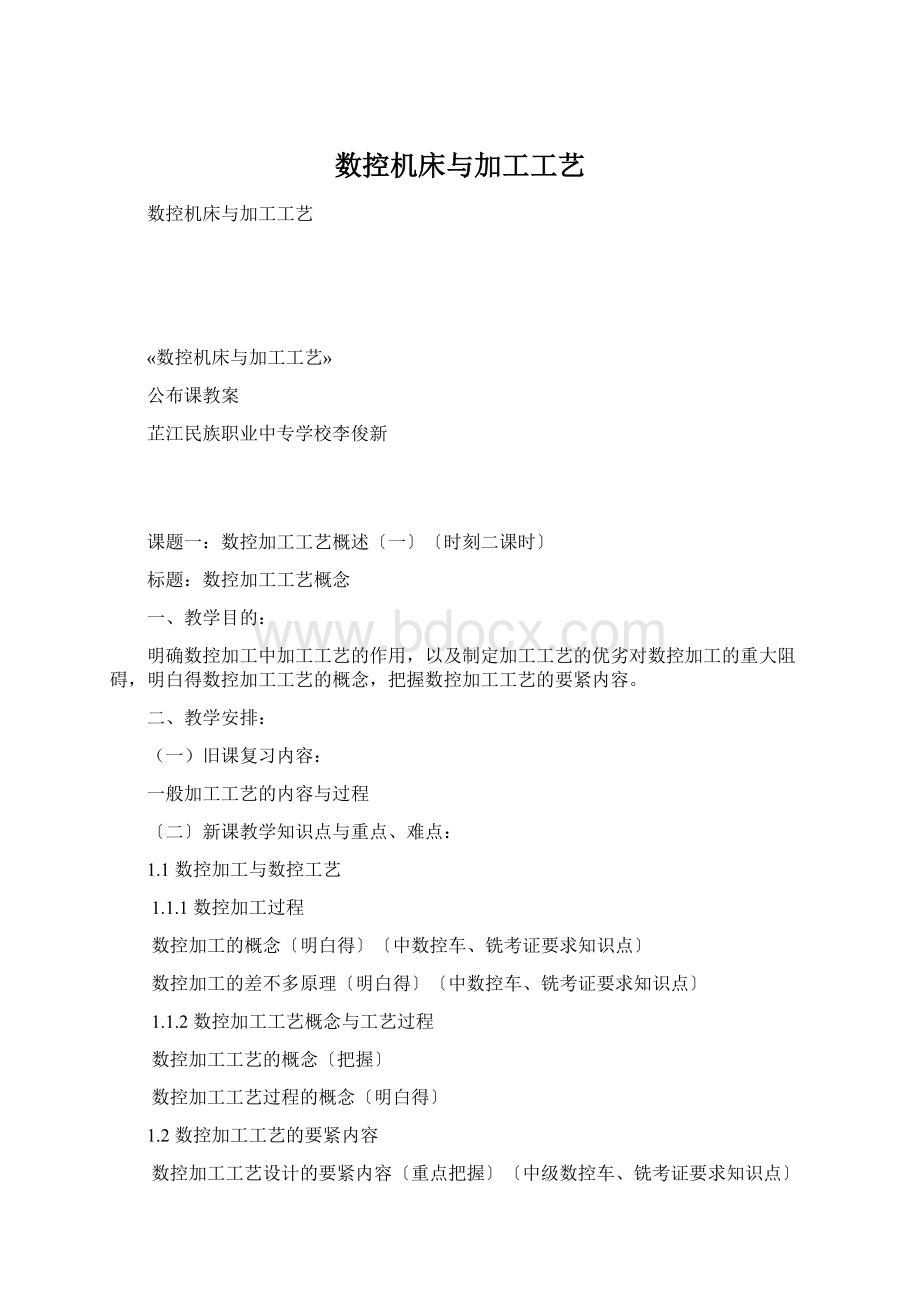
第三步:
依照工艺分析制定出加工所需要的一切工艺信息——如:
加工工艺路线、工艺要求、刀具的运动轨迹、位移量、切削用量〔主轴转速、进给量、吃刀深度〕以及辅助功能〔换刀、主轴正转或反转、切削液开或关〕等,并填写加工工序卡和工艺过程卡;
第四步:
依照零件图和制定的工艺内容,再按照所用数控系统规定的指令代码及程序格式进行数控编程;
第五步:
将编写好的程序通过传输接口,输入到数控机床的数控装置中。
调整好机床并调用该程序后,就能够加工出符合图纸要求的零件。
1.1.2数控加工工艺概念与工艺过程
数控加工工艺的概念
数控加工工艺是采纳数控机床加工零件时所运用各种方法和技术手段的总和,应用于整个数控加工工艺过程。
数控加工工艺是相伴着数控机床的产生、进展而逐步完善起来的一种应用技术,它是人们大量数控加工实践的体会总结。
数控加工工艺过程的概念
数控加工工艺过程是利用切削刀具在数控机床上直截了当改变加工对象的形状、尺寸、表面位置、表面状态等,使其成为成品或半成品的过程。
数控加工工艺设计的要紧内容
数控加工中进行数控加工工艺设计的要紧内容包括以下:
1、选择并确定进行数控加工的内容;
2、对零件图纸进行数控加工的工艺分析;
3、零件图形的数学处理及编程尺寸设定值的确定;
4、数控加工工艺方案的制定;
5、工步、进给路线的确定;
6、选择数控机床的类型;
7、刀具、夹具、量具的选择和设计;
8、切削参数的确定;
9、加工程序的编写、校验和修改;
10、首件试加工与现场问题处理;
11、数控加工工艺技术文件的定型与归档。
工艺设计的优劣对数控加工的阻碍
工艺设计的好坏对数控加工有重大的阻碍
例一:
车削工件加工的先后顺序对工件加工精度的阻碍
例二:
铣削工件选择的刀具走刀路经对工件加工精度的阻碍
〔四〕新课小结:
1、
数控加工工艺是采纳数控机床加工零件时所运用各种方法和技术手段的总和,它包含了确定数控加工内容;
进行工艺分析和零件图形的数学处理;
制定工艺方案;
选择数控机床的类型;
确定工步和进给路线;
选择或设计刀具、夹具和量具;
确定切削参数;
编写、校验和修改加工程序;
编写加工工艺技术文件等方面内容。
2、工艺设计的好坏直截了当阻碍了数控加工的尺寸精度和表面精度、加工时刻的长短、材料和人工的耗费,甚至直截了当阻碍了加工的安全性。
因此要切实把握好数控加工工艺的内容和制定数控加工工艺的方法。
四、作业:
1、数控加工的过程如何?
2、数控加工工艺的概念是什么?
它在数控加工中起到什么样的作用?
3、进行数控加工工艺设计的要紧内容有哪些?
4、工艺设计的好坏对数控加工具有哪些阻碍?
课题二:
数控加工工艺概述〔二〕
数控加工与工艺技术的新进展02
明确数控加工中加工工艺的作用和特点,了解目前国内外数控加工领域在数控加工工艺技术方面的最新进展动向和趋势。
〔一〕
旧课复习内容:
1、数控加工工艺过程的概念
2、数控加工工艺设计的要紧内容
1.3数控加工工艺的特点
数控加工工艺与一般加工工艺的区别及特点〔明白得〕〔难点〕〔中级数控车、铣考证要求知识点〕
1.4数控加工与工艺技术的新进展〔了解〕
高速切削
高精加工
数控加工工艺与一般加工工艺的区别及特点
由于数控加工采纳了运算机操纵系统和数控机床,使得数控加工具有加工自动化程度高、精度高、质量稳固、生成效率高、周期短、设备使用费用高等特点。
在数控加工工艺上也与一般加工工艺具有一定的差异。
1、数控加工工艺内容要求更加具体、详细
一般加工工艺:
许多具体工艺问题,如工步的划分与安排、刀具的几何形状与尺寸、走刀路线、加工余量、切削用量等,在专门大程度上由操作人员依照实际体会和适应自行考虑和决定,一样无须工艺人员在设计工艺规程时进行过多的规定,零件的尺寸精度也可由试切保证。
数控加工工艺:
所有工艺问题必须事先设计和安排好,并编入加工程序中。
数控工艺不仅包括详细的切削加工步骤,还包括工夹具型号、规格、切削用量和其它专门要求的内容,以及标有数控加工坐标位置的工序图等。
在自动编程中更需要确定详细的各种工艺参数。
2、数控加工工艺要求更严密、精确
一般加工工艺:
加工时能够依照加工过程中显现的问题比较自由地进行人为调整。
数控加工工艺:
自适应性较差,加工过程中可能遇到的所有问题必须事先精心考虑,否那么导致严峻的后果。
如:
〔1〕攻螺纹时,数控机床不明白孔中是否已挤满切屑,是否需要退刀清理一下切屑再连续加工。
〔2〕一般机床加工能够多次〝试切〞来满足零件的精度要求,数控加工过程严格按规定尺寸进给,要求准确无误。
因此,数控加工工艺设计要求更加严密、精确。
3、制定数控加工工艺要进行零件图形的数学处理和编程尺寸设定值的运算
编程尺寸并不是零件图上设计的尺寸的简单再现,在对零件图进行数学处理和运算时,编程尺寸设定值要依照零件尺寸公差要求和零件的形状几何关系重新调整运算,才能确定合理的编程尺寸。
4、考虑进给速度对零件形状精度的阻碍
制定数控加工工艺时,选择切削用量要考虑进给速度对加工零件形状精度的阻碍。
在数控加工中,刀具的移动轨迹是由插补运算完成的。
依照差补原理分析,在数控系统已定的条件下,进给速度越快,那么插补精度越低,导致工件的轮廓形状精度越差。
专门在高精度加工时这种阻碍专门明显。
5、强调刀具选择的重要性
复杂形面的加工编程通常采纳自动编程方式,自动编程中必须先选定刀具再生成刀具中心运动轨迹,因此关于不具有刀具补偿功能的数控机床来说,假设刀具预先选择不当,所编程序只能推倒重来。
6、数控加工工艺的专门要求
〔1〕由于数控机床比一般机床的刚度高,所配的刀具也较好,因此在同等情形下,数控机床切削用量比一般机床大,加工效率也较高。
〔2〕数控机床的功能复合化程度越来越高,因此现代数控加工工艺的明显特点是工序相对集中,表现为工序数目少,工序内容多,同时由于在数控机床上尽可能安排较复杂的工序,因此数控加工的工序内容比一般机床加工的工序内容复杂。
〔3〕由于数控机床加工的零件比较复杂,因此在确定装夹方式和夹具设计时,要专门注意刀具与夹具、工件的干涉问题。
7、数控加工程序的编写、校验与修改是数控加工工艺的一项专门内容
一般工艺中,划分工序、选择设备等重要内容对数控加工工艺来说属于已差不多确定的内容,因此制定数控加工工艺的着重点在整个数控加工过程的分析,关键在确定进给路线及生成刀具运动轨迹。
复杂表面的刀具运动轨迹生成需借助自动编程软件,既是编程问题,因此也是数控加工工艺问题。
这也是数控加工工艺与一般加工工艺最大的不同之处。
1.4数控加工与工艺技术的新进展
随着运算机技术突飞猛进的进展,数控技术正不断采纳运算机、操纵理论等领域的最新技术成就,使其朝着高速化、高精化、复合化、智能化、高柔性化及信息网络化等方向进展。
整体数控加工技术向着CIMS〔运算机集成制造系统〕方向进展。
高速切削
受高生产率的促使,高速化已是现代机床技术进展的重要方向之一。
要紧表现在:
1、数控机床主轴高转速
作用:
主轴高转速减少了切削力,也减少了切削深度,有利于克服机床振动,排屑率大大提高,热量被切屑带走,故传入零件中的热量减低,热变形大大减小,提高了加工精度,也改善了加工面粗糙度。
因此,通过高速加工的工件一样不需要精加工。
提高主轴转速的手段:
采纳电主轴〔内装式主轴电动机〕,即主轴电动机的转子轴确实是主轴部件,从而可将主轴转速大大提高。
日本的超高速数控立式铣床:
主轴最高转速达100,000r/min
2、工作台高快速移动和高进给速度
当今知名数控系统的进给率都有了大幅度的提高。
目前的最高水平是
辨论率为1μm时:
最大快速进给速度可达240m/min;
当程序段设定进给长度大于1mm时:
最大进给速度达80m/min
〔同时具有1.5g的加减速率〕。
高精加工是高速加工技术与数控机床的广泛应用结果。
往常汽车零件的加工精度要求在0.01mm数量级,现在随着运算机硬盘、高精度液压轴承等周密零件的增多,精整加工所需精度已提高到0.1μm,加工精度进入了亚微米世界。
提高数控设备加工精度的方法:
〔1〕提高机械设备的制造精度和装配精度
〔2〕减小数控系统的操纵误差
提高数控系统的辨论率
以微小程序段实现连续进给
使CNC操纵单位精细化
提高位置检测精度,
位置伺服系统采纳前馈操纵与非线性操纵
〔3〕采纳补偿技术:
齿隙补偿、丝杆螺距误差补偿、刀具误差补偿、热变形误差补偿、空间误差综合补偿等技术。
〔四〕、新课小结:
1、由于数控加工采纳了运算机操纵系统和数控机床,使得数控加工具有加工自动化程度高、精度高、质量稳固、生成效率高、周期短、设备使用费用高等特点。
2、随着运算机技术突飞猛进的进展,数控技术正不断采纳运算机、操纵理论等领域的最新技术成就,使其朝着高速化、高精化、复合化、智能化、高柔性化及信息网络化等方向进展。
五、作业:
1、数控加工工艺与一般加工工艺的区别在哪里,其特点是什么?
2、数控加工与工艺技术有哪些新进展动向?
3、实现高速切削有何优越性?
如何实现数控机床主轴的高转速?
4、能够采纳哪些方法实现高精加工?
课题三:
数控刀具与应用〔一〕
数控刀具概述03
介绍并让学说明白得数控刀具的种类、要求与特点,数控刀具的材料、失效形式和可靠度分析,为选用刀具作好知识的预备。
〔二〕
1、数控加工的概念
2、数控加工工艺过程
2.1数控刀具的类型与特点
数控刀具的分类〔了解〕
数控刀具的要求与特点〔把握〕〔中级数控车铣考证要求知识点〕
2.2数控刀具的材料
数控刀具的材料〔了解〕
2.3数控刀具的失效形式及可靠性
数控刀具的失效形式、阻碍与计策〔把握〕〔中级数控车铣考证要求知识点〕
数控刀具的可靠度〔了解〕
数控刀具的种类
〔介绍、了解数控刀具的种类,以便选择先进、合适的数控刀具〕〔预备各式刀具〕
1、从结构上可分为:
整体式,镶嵌式,内冷式,减振式,机夹可转位刀具等。
2、从加工工艺上可分为:
车刀,钻刀〔钻头〕,镗刀,铣刀。
3、数控〝刀具〞的进展趋势:
由整体式工具系统向模块式工具系统进展。
有利于提高劳动生产率,提高加工效率,提高产品质量。
数控刀具的要求与特点
〔让学生明白得数控刀具什么缘故要具备下述条件和特点,这是选择和评判刀具的依据〕
1、要有专门高的切削效率。
提高切削速度致关重要,硬质合金刀具切削速度可达500—600m/min,陶瓷刀具可达800—1000m/min
2、要有专门高的精度和重复定位精度,一样3—5µ
或者更高。
3、要有专门高的可靠性和耐用度,是选择刀具的关键指标,
4、实现刀具尺寸的预调和快速换刀,缩短辅助时刻提高加工效率
5、具有完善的模块式工具系统,储存必要的刀具以适应多品种零件的生产
6、建立完备的刀具治理系统,以便可靠、高效、有序的治理刀具系统
7、要有在线监控及尺寸补偿系统,监控加工过程中刀具的状态,提高加工可靠度。
数控刀具的材料
〔要紧介绍材料的宏观力学性能,为选择刀具作知识预备〕
〔学习刀具材料把握其性能,以便依据工件材料、加工要求和机床等加工条件,选用先进、合适的刀具〕
1、高速钢〔Highspeedsteel〕,分W系和Mo系两大类,具有回火二次硬化功能高于淬火硬度又具有较好的韧度,比一般工具钢耐磨、比硬质合金韧性高。
2、硬质合金〔Cementedcarbide〕,分钨钴类〔WC〕、钨钛钴类〔WC—TiC〕、钨钛钽〔铌〕钴类〔WC-TiC-TaC〕,按ISO标准分为
〔1〕K类,即国标YG,适合加工短切屑黑色金属〔铸铁〕和有色金属及非金属。
〔2〕P类,即国标YT,适合加工长切屑黑色金属〔塑性好的材料低碳钢〕
〔3〕M类,即国标YW,综合性能好,既可加工铸铁又可加工钢材及有色金属
3、陶瓷〔Ceramics〕,分为两大类,纯氧化铝类〔白色陶瓷〕和TiC添加类〔黑色陶瓷〕,陶瓷特耐高温,在2000度条件下,仍具有高的硬度,专门耐磨,然而,韧性专门低,不能承担冲击,适用于精加工和高速切削
4、立方碳化硼〔Cubicboronnitride,CBN〕,是在高温、高压条件下人工合成的新型刀具材料,其性能与金刚石相似,能高速切削淬火钢和耐热钢,是高速切削的首选 刀具材料。
5、聚晶金刚石〔Polymerizecrystaldiamond,PCD〕即人工合成的金刚石,是在高温、高压下合成的新型刀具材料,硬度极高,然而,与铁系材料有专门强的亲和力,易使碳元素扩散而磨损,只适用于加工有色金属、非金属如陶瓷等极硬的材料。
控刀具失效形式、缘故、阻碍与操纵失效计策
〔结合实际,讲述数控刀具的各种要紧失效形式、分析其缘故、产生的阻碍、以及操纵失效的方法与计策〕
〔结合实际,讲述数控刀具的各种要紧失效形式、分析其缘故、产生的阻碍、以及操纵失效的方法与计策〕
失效
形式
理念
刀具失效
的缘故
产生的阻碍
操纵失效方法
与计策
后刀面磨损
机械应力导致摩擦磨损
1.刀具材料硬度不足
2.后角偏小
3.切削速度过高
4.进给量过大
降低加工尺寸精度
1、选用耐磨刀具材料
2、降低切削速度
3、加大进给量
4、增大后角
前刀面磨损
摩檫和扩散导致前刀面磨损
1.刀具材料硬度足
2.切削速度过高
3.进给量过大
4.切屑与前刀面损
5.发热区域扩散
阻碍排屑
降低主切削韧强度
1、1、
降低切削速度
2、2、
降低进给量
3、3、
选用涂层硬质合金刀具材料
边界磨损
主切削韧上的边界磨损
1.工件材料表面硬化
2.锯齿状切屑
阻碍切屑流向
导致崩刃
选用耐摸刀剧材料
4、4、
增大前角
积屑瘤
粘附堆积在主切削刃旁的前刀面上的工件材料的微粒
1.工件材料塑性太大
2.中速切削〔5-50〕m/min
3.切削热
引起振动导致崩刃
降低表面质量
降低尺寸精度
改善工件材料的切削加工性
选用亲和力小的涂层硬质合金和陶瓷刀具材料
使用合适的冷却液
刃口剥落
切削刃上显现小缺口
排屑不畅所致
降低加工表面质量
降低尺寸精度
选用强度高的刀具材料
改善刀具几何角度
崩刃
切削刃大片崩落
切削应力过大
刃口强度不足
刀具材料强度与韧度不足
切削不能进行
选用强度刃度高的刀具材料
降低切削负荷
适当减小前、后角
热裂纹
切削热不平均导致
进给量过大被吃刀量过大
降低工件加工表面质量
选用合适的冷却方式
降低进给量
降低被吃刀量
刀具可靠性分析
1、刀具可靠性:
在规定的切削条件和时刻内完成额定工作的能力〔具有统计特点和随机特点〕
2、刀具耐用度:
在规定的条件和时刻内完成额定工作的概率
R〔t〕+F(t)=1
3、靠耐用度:
tr是指刀具能达到规定的可靠度r时的耐用度
即R(tr)=r那么tr=R¯
¹
(t)
多齿刀具可靠度Rz(t)=[R(t)]z因一齿损坏那么刀具损坏,因此可靠度比单齿低。
现行刀具的可靠度评判以长期生产体会为依据。
1、数控〝刀具〞的进展趋势:
2、数控刀具的要求与特点
1、数控刀具的材料有那些?
分别按硬度和韧性分析其性能。
2、分析刀具失效的要紧形式及产生的缘故和计策。
课题四:
数控刀具与应用〔二〕
数控刀具分析、选择与运用04
介绍数控刀具特点与要求,选择刀具及刀具系统应考虑的因素,以实例说明选择刀具的过程,使学生学习和把握依据加工环境正确选择和使用加工刀具的方法。
〔三〕
1、数控刀具的类型、材料、特点
2、数控刀具的失效形式、产生的阻碍以及操纵的方法。
2.4数控刀具的选择
选择数控刀具时应考虑的因素〔明白得〕
车削系统、铣镗系统〔把握〕〔中级数控车铣考证要求知识点〕
工具治理系统(了解);
数控刀具〔分两大系统:
车削系统和铣镗削系统〕的特点与要求
数控刀具要求精度高、刚性好、装夹调整方便,切削性能强、耐用度高。
合理选用既能提高加工效率又能提高产品质量。
刀具选择应考虑的要紧因素
1、被加工工件的材料、性能:
金属、非金属,其硬度、刚度、塑性、韧性及耐磨性等。
2、加工工艺类别;
车削、钻削、铣削、镗削或粗加工、半精加工、精加工和超精加工等。
3、工件的几何形状、加工余量、零件的技术经济指标。
4、刀具能承担的切削用量。
5、辅助因数:
操作间断时刻、振动、电力波动或突然中断等。
车削系统〔整体式工具系统〕
1、组成:
由刀片〔刀具〕、刀体、接柄〔或柄体〕、刀盘等
2、可转位刀片的代码及参数
3、可转位刀片的断屑槽槽型:
断屑自如、排屑流畅
4、可转位刀片的夹紧方式:
楔块上压式、杠杆式、螺钉上压式
要求:
夹紧可靠、定位准确、排屑流畅、结构简单、操作方便
5、可转位刀片的选择
1〕、刀片材料选择:
高速钢、硬质合金、涂层硬质合金、陶瓷、立方碳化硼或金刚石
2〕、刀片尺寸选择:
有效切削韧长度、被吃刀量、主偏角等
3〕、刀片形状选择:
依据表面形状、切削方式、刀具寿命、转位次数等
4〕、刀片的刀尖半径选择:
A、粗加工、工件直径大、要求刀刃强度高、机床刚度大时选大刀尖圆弧
B、精加工、切深小、细长轴加工、机床刚度小选小刀尖圆弧
刀具系统〔模块式工具系统〕
1、组成;
刀片〔刀具〕、刀杆〔或柄体〕、主轴或刀片〔刀具〕、工作头、连接杆、主柄、主轴所组成
2、数控铣削刀具的选择
1〕、铣刀类型的选择:
A、加工较大平面选择面铣刀,
B、加工凸台、凹槽、小平面立铣刀,
C、加工毛坯面和粗加工孔选择镶硬质合金玉米铣刀,
D、曲面加工选择球头铣刀,
E、加工空间曲面模具型腔与凸模表面选择模具铣刀,
F、加工封闭键槽选键槽铣刀,等等
2〕、铣刀参数的选择
A、面铣刀要紧参数选择
a)、标准可转位面铣刀直径在Φ16-Φ630〕:
粗铣时直径选小的,精铣时铣刀直径选大的,
b)、依据工件材料和刀具材料以及加工性质确定其几何参数:
铣削加工通常选前角小的铣刀,强度硬度高的材料选负前角,工件材料硬度不大选大后角、硬的选小后角,粗齿铣刀选小后角,细齿铣刀取大后角,铣刀的刃倾角通常在-5--15度,主偏角在45-90度
B、立铣刀要紧参数选择
a)、刀具半径r应小于零件内轮廓最小曲率半径ρ
b)、零件的加工高度H≤〔1/4-1/6〕r
c)、不通孔或深槽选取l=H+(5~10)mm
d)、加工外形及通槽时选取l=H+rε+(5~10)mm
e)、加工肋时刀具直径为D=(5~10)b
f)、粗加工内轮廓面时,铣刀最大直径D
D=d+2[δsin(φ/2)-δ1]/[1-sin(φ/2)]
3、加工中心刀具的选择
加工中心刀具通常由刃具和刀柄两部分组成,刃具有面加工用的各种铣刀和孔加工用的各种钻头、扩孔钻、镗刀、铰刀及丝锥等,刀柄要满足机床主轴自动松开和夹紧定位,并能准确地安装各种刃具和适应换刀机械手的夹持等要求。
1〕、对加工中心刀具的差不多要求
A、刀具应有较高的刚度
B、重复定位精度高
C、刀刃相对主轴的一个定位点的轴向和径向位置应能准确调整
2〕、孔加工刀具的选择
A、钻孔刀具及其选择
B、扩孔刀具及其选择
C、镗孔刀具及其选择,应专门重视刀杆的刚度
3〕、刀具尺寸的确定
要紧是刀具的长度和直径的选择,如加工孔依据其深度和孔径选择
4、刀柄的选择
1〕、依据被加工零件的工艺选择刀柄
2〕、刀柄配备的数量:
与被加工零件品种、规格、数量、难易程度、机床负荷有关
3〕、正确选择刀柄柄部形式
4〕、坚持选择加工效率高的刀柄
5〕、综合考虑合理选用模块式和复合式刀柄
工具系统
1、工具系统进展趋势:
向着柔性制造系统和模块化组合结构进展
2、车削类工具系统
3、镗铣类工具系统:
分整体失和模块式工具系统
4、刀具治理系统:
1