汽车的神经和血管之痛.docx
《汽车的神经和血管之痛.docx》由会员分享,可在线阅读,更多相关《汽车的神经和血管之痛.docx(9页珍藏版)》请在冰豆网上搜索。
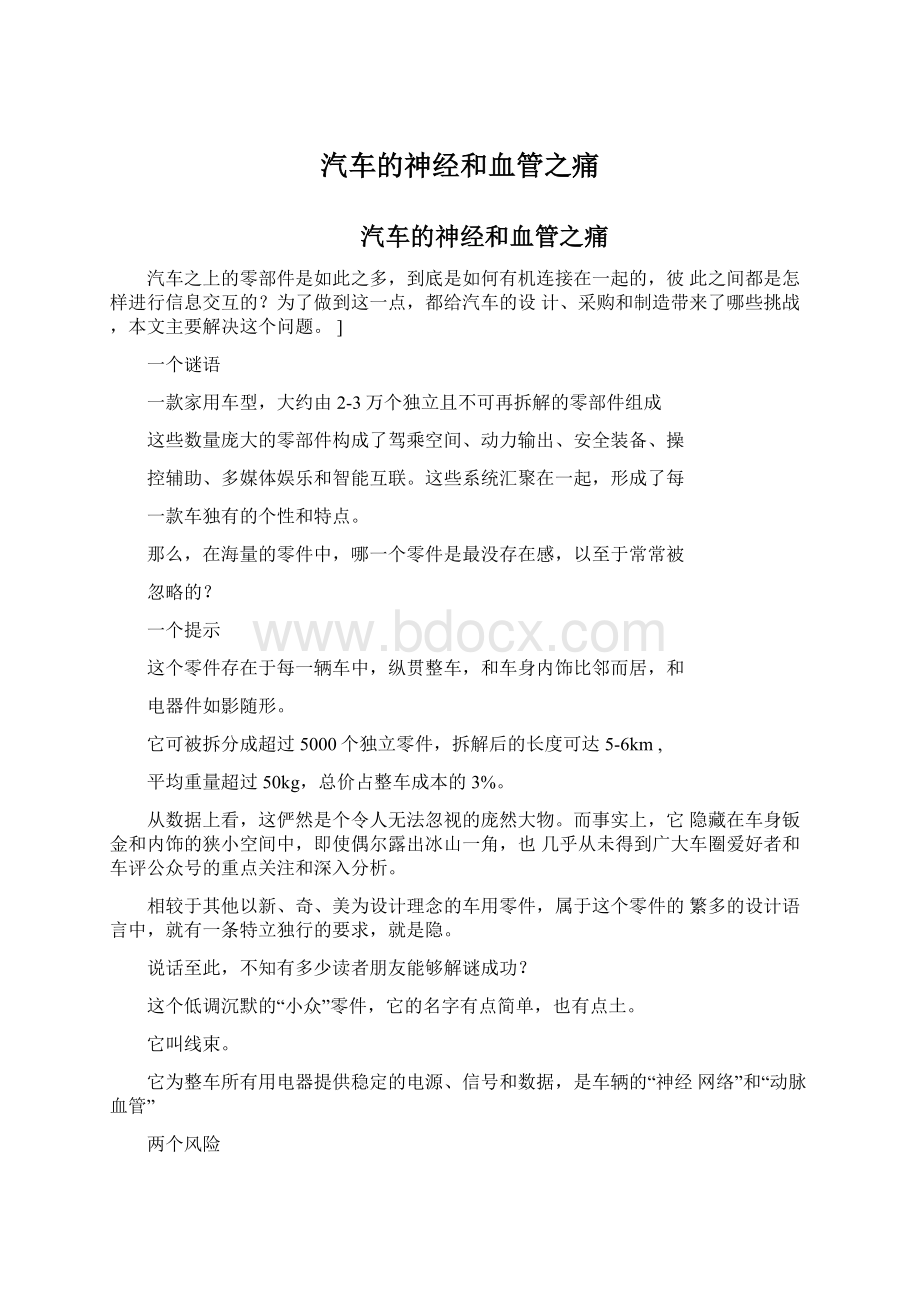
汽车的神经和血管之痛
汽车的神经和血管之痛
汽车之上的零部件是如此之多,到底是如何有机连接在一起的,彼此之间都是怎样进行信息交互的?
为了做到这一点,都给汽车的设计、采购和制造带来了哪些挑战,本文主要解决这个问题。
]
一个谜语
一款家用车型,大约由2-3万个独立且不可再拆解的零部件组成
这些数量庞大的零部件构成了驾乘空间、动力输出、安全装备、操
控辅助、多媒体娱乐和智能互联。
这些系统汇聚在一起,形成了每
一款车独有的个性和特点。
那么,在海量的零件中,哪一个零件是最没存在感,以至于常常被
忽略的?
一个提示
这个零件存在于每一辆车中,纵贯整车,和车身内饰比邻而居,和
电器件如影随形。
它可被拆分成超过5000个独立零件,拆解后的长度可达5-6km,
平均重量超过50kg,总价占整车成本的3%。
从数据上看,这俨然是个令人无法忽视的庞然大物。
而事实上,它隐藏在车身钣金和内饰的狭小空间中,即使偶尔露出冰山一角,也几乎从未得到广大车圈爱好者和车评公众号的重点关注和深入分析。
相较于其他以新、奇、美为设计理念的车用零件,属于这个零件的繁多的设计语言中,就有一条特立独行的要求,就是隐。
说话至此,不知有多少读者朋友能够解谜成功?
这个低调沉默的“小众”零件,它的名字有点简单,也有点土。
它叫线束。
它为整车所有用电器提供稳定的电源、信号和数据,是车辆的“神经网络”和“动脉血管”
两个风险
看不见、摸不着、纯硬件、体量大一一这些线束与生俱来的基因,
使其在过去很长时间里,成为了车辆设计的薄弱点和降本的重灾区。
来看一组新闻。
2019年6月,造车新势力蔚来发布声明称,今年发生的多起ES8自
燃事故,根本原因在于电池包内电压采样线束走向不当,被电池模
组上盖板挤压,绝缘表皮破损,造成短路,引发安全事故。
2018年3月,一汽大众向国家质检总局备案召回计划,计划召回宝
来和蔚领共计43万辆汽车。
其召回声明称,仪表板线束在仪表台内部发生干涉,造成线束磨损,导致车辆可能出现熄火、无法启动等现象,存在安全隐患。
2018年1月,吉利博瑞的4万多辆车同样因为线束问题被要求召
回。
主因是电动助力转向线束内部可能腐蚀,在极端情况下可能出
现转向助力失效的问题,同样存在安全隐患。
失效、失速、熄火、自燃,这些涉及车辆安全和人员安全的事故和大
批量的召回事件,不断触动消费者敏感的神经。
让大众不经发问,
如此严重的风险点为什么没有在幵发设计和试验验证阶段被发现?
若就单个问题进行分析,原因无外乎是线束零件在设计幵发、试验论证、生产制造环节出现了重大疏漏。
可若以宏观角度去看,就会发现,线束不可被目视,难以被接触的特性,才是了它问题频出的根源。
现如今,不论是传统车企,或是造车新势力,无一不是在集洪荒之力打造一个由电子电气件组成的瑰丽世界,唯恐自己在车辆智能化网联化的赛道上落人下风。
而对于这个电子世界的基石——线束,却往往不屑一顾。
甚至简单粗暴地认为,一个不会出现在消费者眼皮子底下,不会被消费者直接使用到的零件,并不值得耗费大量时间和精力去精益求精。
如果读者朋友们觉得上述事例是危言耸听,能遇上的概率很小,遇上了也只能叹一句“命也”。
那下面这些真相里或许会令人熟悉的味道。
RVC后视摄像头的画面总是有干扰?
那可能是因为RVC电源线和视频线布置不在一侧,节省了电源线的长度,受到了各类PWM信号的影响
收音机总是有杂音,怎么调频都没用?
那可能是因为收音机和其他大电流用电器接地在了同一处,节省了
接地点物料,增加了噪音干扰。
只是给爱车增加了行车记录仪或通风座椅,点烟器的12V电源就烧
了保险丝?
那可能是因为在电源分配时,掐着电器件的额定工作电流给配的保
险丝和导线,并未考虑可预见的用户滥用的情况。
行车途中总会听见车厢里传来轻微的碰撞声,又遍寻不着出处,怀
疑自己幻听?
那可能是因为四门线束或是车顶线束减少了固定件,时间一久就脱落幵,来回撞击车身和内饰,发出的声响。
后排的USB只能充电,无法和车载导航之间传输数据、投射APP?
那可能是为了节省一段价值超过20元的数据传输线,索性只提供充
电功能。
查看Model3、BMWi3和ChevyBolt的整车线束价格,就能明
白为什么车企和零件制造商们会绞尽脑汁地在消费者们看不见的线束零件上使劲薅羊毛了。
■LowvoltagewiringHighvoltdg?
1wiring
总之,那些以降本为目的手段,五花八门、百花齐放,相信总有一款
能让车主们对号入座。
可是,不间断的召回事件和汽车评论网站上的吐嘈声,已经证明了,
如果车企和制造商只是一心追逐行业热点和风口,在设计上对基础
零件抱着得过且过的敷衍态度,在成本控制方面推行不合理的降本
措施,那么不论在风口飞翔的是不是猪,最终都只会自折羽翼,遭
到消费者的抛弃。
三个趋势
如同下水道是一个城市的良心。
沉默地蜷缩在车内的线束,在很大
程度上代表着一个车企的诚意和良心。
对线束而言,花哨和张扬,并不是它的特长。
最正确的打幵方式,就是让它维持好“磐石”的设定,完善其“提供支持和链接”的基础功能。
并随着行业技术的革新浪潮,顺势而为,朝着轻量化&小型化、集成
化&标准化、通信高速化的三大方向上寻找突破口。
1.轻量化&小型化
不论是传统车企,或是造车新势力,在面对愈发严苛的排放法规和
油耗标准,以及消费者所追求的更快更壕更智能,这两个几乎背道
而驰的要求时,都需要使出浑身解数,才能在夹缝中求生存。
减重,不仅能够提升车辆的能量使用率,还会增大推重比,使动力更猛,制动距离更短,操控性更强,也更安全。
在满足法规要求的同时,又完全戳中了消费者“购买萌点“,自然成了夹缝中的救命稻草。
实验证明,在耗油节能方面,燃油车的重量每下降10%,油耗即可
下降6-8%。
车辆重量减少100kg,其百公里油耗即可降低0.3-0.6L
燃油车的减重势在必行,新能源也无法逃离魔咒,只作壁上观。
虽然没了内燃机和变速箱,但取而代之的三电动力系统、配套充电系统(包括全套高压线束),都是压在新能源车身上的沉重枷锁。
每减重100Kg即可将续航里程提高10%-11%。
这一实验结论对深
陷里程焦虑且迟迟无法突破瓶颈的新能源车企来说,可谓是久旱逢甘霖。
如何通过减重来摆脱带着铐链奔跑的现状,就变得极为重要且迫切了。
线束零件覆盖整车的使用范围以及对金属铜的大量使用,使其在重量上,仅次于车身、底盘和动力总成。
提供几组整车线束的重量数据,某合资品牌C级车的整车线束重量
为77.7Kg,某豪华品牌D级车的整车线束重量为80Kg。
而某款
BEV车型和特斯拉Model3的对比数据,则分别为40Kg和20Kg。
换句话说,若将来BEV车型的线束重量都能够下降到20Kg甚至更
低,则可额外贡献至少2个点的里程。
对于线束零件的轻量化小型化趋势,一言蔽之,即在最合适的地方,
用最轻薄的材料,做出最小型的设计。
最轻的材料。
铝和镁作为公认的轻量化材料,已经被广泛运用在多种结构件和冲
压件上,并非新鲜事物。
这种材料的革新同样适用于线束。
虽然纯铝导线的导电性不如铜,
但在重量方面具有碾压性优势。
而重量更轻、线径更细、拉伸和弯曲性能更好的铜镁合金导线,则
可以使用在对布置要求特别严苛的活动区域,诸如需要反复幵关的
四门和行李箱门等区域,为可预见的用户滥用做出合理设计。
最薄的材料
与现有的导线相比,超薄壁导线具有相同的载流能力,但在尺寸和
重量方面,却能够下降11%和7%之多。
可以在极为狭窄的空间中
顺畅通过,从而为消费者省出更多的车内空间。
最小型的设计
和家用电器只需一个用于供电的两眼或三眼的插头不同的是,车载
用电器还需要进行多路的信号传输和交互,插头往往体积大,数量
多。
以奔驰E-Class为例,整车的电器件插头就高达208个,仅插
头的重量就达1.35kg,其价格占线束总价的15%之多。
而在实现相同功能的前提下,设计新的紧凑型插头,可带来至少减重20%的效
果。
综上,相较于造价昂贵、工艺繁复的铝制或碳纤维车身部件,通过降低线束零件的重量,来达到改善能量使用率的目的,贝焜性价比极高的做法。
2.模块化&标准化作为复杂程度位列前茅的零件,除了从材料和设计层面对线束进行大刀阔斧的革新外,车企还应考虑如何通过降低线束零件的复杂度,扩大单一零件的需求量,来提高商务议价能力,降低单件成本。
言而简之,就是“拼多多“的团购思维一一统一货号,扩大需求,降低
单价。
线束零件的组合数量和复杂程度,归根到底,是由消费者手上那张车辆配置表上有多少可选项来决定。
车企大肆宣传的“客户定制”,其本质是由各类零部件,尤其是电器件
相互交叉、搭配组合来实现的。
这就好像女生们新入了一件上衣,就会需要裙子、鞋子、包包来搭
这些“套装“还会按照场合的不同,衍生出很多微小的差异。
这个例子可能不那么恰当,但想表达的语义是相同的。
对于车辆用
电器而言,每产生一种新的组合关系,也同样需要线束提供支持和
匹配,满足其通信和供电等多种需求。
BOM愈
这种点对点的固定搭配不仅非常低效,还直接导致线束的发臃肿复杂,组合数量爆炸式增长。
而车辆的空间和衣柜一样,总有再也塞不下的一天。
严格来说,造成组合数量无法控制的“罪魁祸首“在于,现有车载控制
器的软件在硬件中的嵌套程度太深,软件和硬件相互捆绑。
若要多实现一个功能,就必须新增对应的电器件,而线束的组合数量也将被迫呈几何级增加的态势。
以一款大家耳熟能详的C级车为例,全系可实现的选装组合数量高
达164种,需使用到的零件共计12个大类,6600多件。
且不论为
了厘清组合关系而付出的设计幵发成本,单单考虑随之而来的仓储、制造、检验、安装等环节,费用就高昂的令人咋舌为了拯救有限的空间和有限的钱包,时尚圈幵始推崇干净清爽的“百搭款”。
同样的道理也适用于车企。
这种在已有电子电气架构上,通过单纯增加硬件来实现功能扩展的传统手段,已被来势汹汹的造车新势力给颠覆了。
特斯拉便是个中高手。
其最核心的设计原则是将软件彻底从硬件上剥离幵,将软硬件之间
的交互形式标准化,由多个中央控制器在标准的操作系统上运行,
在量产车上直接预置统一的硬件,再通过OTA来为硬件赋予实际功
能,升级系统、扩展功能、优化体验等。
线束作为对软件0诉求,以链接整车所有用电器为目标的纯物理层
零件,在“软硬件剥离”的趋势下,完全可以尝试直接以覆盖最大范围电器件为设计导向,进行标准化、模块化设计,从160+个组合关系
的泥沼中挣脱出来,将组合数量大幅减少至十几甚至是个位数,进行批量重复地生产
成为“百搭基础款”的线束零件,不仅可以为自动化生产提供便利条件,还会给车企带来诸如技术变更频率降低、仓储成本减少、物流
控制便捷等一系列的隐性好处,而最终这些变化会转换为真金白银,
回馈给这个产业链上下的从业者。
3.通信高速化
轻量化小型化,模块化标准化,这些“节流”措施虽然可以让车企在凛
冽的寒冬中活下来,但若想在百舸争流中占有一席之地,那就必须
在以V2X、ADAS、自动驾驶为目标的赛道上发足狂奔。
UlUiic曲Lbch
Ult站电hzHMhUFenUftr*禅槪
uiEradMi(wfiwr
以AUDIA8L为例,整车配备了12个超声波传感器、4个360度全景摄像头、1款前置摄像头、4个中程雷达、1个远程雷达、1个红外摄像头和激光雷达。
可以说,这些传感器和摄像头已经将车辆武装到了牙齿。
这些数据