浅埋深整体性强的软岩条件下的长壁综合机械化开采Word文件下载.docx
《浅埋深整体性强的软岩条件下的长壁综合机械化开采Word文件下载.docx》由会员分享,可在线阅读,更多相关《浅埋深整体性强的软岩条件下的长壁综合机械化开采Word文件下载.docx(5页珍藏版)》请在冰豆网上搜索。
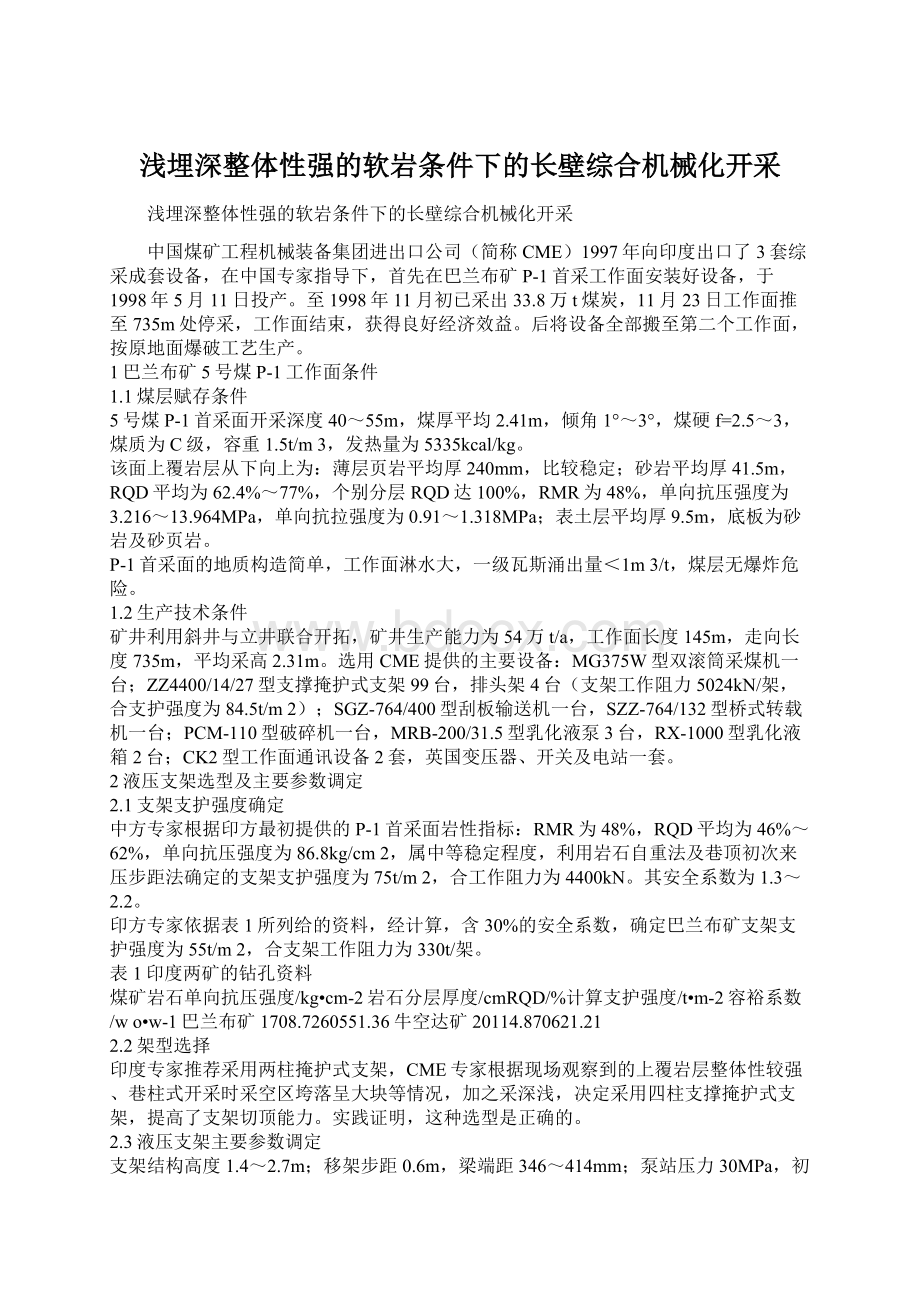
矿井利用斜井与立井联合开拓,矿井生产能力为54万t/a,工作面长度145m,走向长度735m,平均采高2.31m。
选用CME提供的主要设备:
MG375W型双滚筒采煤机一台;
ZZ4400/14/27型支撑掩护式支架99台,排头架4台(支架工作阻力5024kN/架,合支护强度为84.5t/m2);
SGZ-764/400型刮板输送机一台,SZZ-764/132型桥式转载机一台;
PCM-110型破碎机一台,MRB-200/31.5型乳化液泵3台,RX-1000型乳化液箱2台;
CK2型工作面通讯设备2套,英国变压器、开关及电站一套。
2液压支架选型及主要参数调定
2.1支架支护强度确定
中方专家根据印方最初提供的P-1首采面岩性指标:
RMR为48%,RQD平均为46%~62%,单向抗压强度为86.8kg/cm2,属中等稳定程度,利用岩石自重法及巷顶初次来压步距法确定的支架支护强度为75t/m2,合工作阻力为4400kN。
其安全系数为1.3~2.2。
印方专家依据表1所列给的资料,经计算,含30%的安全系数,确定巴兰布矿支架支护强度为55t/m2,合支架工作阻力为330t/架。
表1印度两矿的钻孔资料
煤矿岩石单向抗压强度/kg•cm-2岩石分层厚度/cmRQD/%计算支护强度/t•m-2容裕系数/wo•w-1巴兰布矿1708.7260551.36牛空达矿20114.870621.21
2.2架型选择
印度专家推荐采用两柱掩护式支架,CME专家根据现场观察到的上覆岩层整体性较强
、巷柱式开采时采空区垮落呈大块等情况,加之采深浅,决定采用四柱支撑掩护式支架,提高了支架切顶能力。
实践证明,这种选型是正确的。
2.3液压支架主要参数调定
支架结构高度1.4~2.7m;
移架步距0.6m,梁端距346~414mm;
泵站压力30MPa,初撑3628kN/架,立柱初撑力942kN。
强度试验泵压30×
1.25=37.5MPa,印度对立柱的试验工作阻力为40MPa。
支架型式和强度试验均通过了中国和印度的试验标准,取得了合格证。
在工作面开采过程中,因P-1首采面上覆岩层岩性局部发生变化,致使在该面推至距开切眼84m和168m处两次垮至地表,使工作面中部支架压死,并损坏了液压系统元件和支架顶梁、立柱等部件。
经中印专家研究决定:
在采取地面爆破条件下,将工作面全部安全阀开启压力由35MPa提高到40MPa,支架支撑能力提高约14%,使支护强度从割煤前的74t/m2提高到84.5t/m2。
3P-1首采面岩性变化及其矿压显现特征
在中国专家组织领导下,采用四八交叉作业,采煤机斜切入刀,双向采煤,追机作业,先移架,后推溜及时支护顶板,计划日产1950t。
在工作面推采过程中,于5月28日和6月17日工作面上覆岩层两次垮至地表,顶板大面积垮落,活柱急速下缩,工作面矿压显现剧烈,使工作面中部部分支架被压死,并遭破坏。
经分析认为:
发生上述剧烈矿压显现是由于上覆岩层岩性同最初提供的资料相比有变化,变化了的岩层,导致了难垮顶板的矿压显现。
3.1P-1首采面岩性变化勘测
由表2可知:
P-1首采面岩性分布是不均的。
沿工作面走向,靠近开切眼附近顶板完整性较高,RQD>75[换行]%,顶板属难垮顶板。
压死支架正处在此区内。
表21998年6月以后印方提供的P-1首采面岩性资料
钻孔号钻孔位置RQD平均值/%一些分层RQD最大值/%BIX-145至开切眼外侧70m处76.081~100CMBK-1至开切眼内侧45m处47.882~100CMBK-4至开切眼内侧238m处64.279~100BIX-146至开切眼内侧270m处46.069BIX-144至开切眼内侧695m处63.676~96
根据在P-1首采面采空区上方新打的BH-3和BH-4钻孔资料,自地表至22.5~47.5m和33~49.4m岩层下落后仍呈大块规则排列,可取出各个分层的完整岩芯,这表明其岩性整体性是很强的。
巴兰布矿P-1首采面上覆岩层断裂步距是有规律的,共垮至地表4次,其步距分别为84、84、86和84。
除第一次垮至地表前其间上覆岩层断裂次数较少外,其余三次垮至地表前其间上覆岩层断裂分别为5、7和7次。
来压强度分别在1.22~1.41、1.28~1.37和1.12~1.37之间。
历次垮至地表时老顶来压强度分别为1.44、1.43、1.33和1.38(后两次是在地面滞后爆破条件下发生的)。
总之,巴兰布矿P-1工作面上覆岩层整体性是较强的,远高于中等稳定,属于难垮顶板。
3.2浅埋深整体性强厚砂岩剧烈的矿压显现特征
巴兰布矿P-1首采面上覆难垮顶板,在未采取地面爆破前,第一次和第二次垮至地表呈现剧烈矿压显现:
(1)上覆岩层垮至地表步距稳定,呈大面积来压。
该面在未采取地面爆破前,发生过17次以上顶板来压,但在上覆岩层垮至地表前,顶板分层垮落,因整体性强,垮落岩块未能充满采空区,下沉0.76m,下沉系数为0.35,在垮落岩块与未断裂垮落岩层之间总有空隙(自由空间)。
因此,当工作面推至距开切眼84m和168m处,上层岩层垮至地表,形成大面积来压,瞬间垮落的大块岩石使工作面中部30余台支架被压死,并使支架液压装置、立柱和顶梁遭到不同程度的破坏。
这个有规律的上覆岩层断裂间距可视为浅埋深、整体性强厚砂岩的来压步距。
据来压步距84m,面长150m计,大面积来压垮落面积为12600m2,按印度顶板分类(标准为初次来压步距76~100m,垮落最大面积为10000~14000m2,属难垮顶板)。
(2)顶板来压强度大,来压显现剧烈。
从工作面立柱压力表记录看,历次顶板来压时立柱平均压力比来压前高40%。
两次垮至地表时立柱最大压力比来压前高126%~154%,这就是说,平时顶板压力小,而来压时顶板压力猛增,动载系数大于2.5。
如此高的来压强度可使顶板沿煤壁台阶下沉600~700mm,煤壁片帮600~700m,支架安全阀、液控单向阀开启,并与压力表一起遭到破坏,导致支架压死多架。
(3)全工作面支架受载不均。
从工作面立柱压力记录统计,全工作面支架受载不均。
表现为:
①顶板剧烈来压时,后柱工作阻力比前柱高19.8%;
②工作面中部顶板压力高于两端,见表3;
③第一、二次垮至地表时,沿工作面长度方向,顶板来压强度不均,其中以61~80#支架处最高,见表4;
④采空区顶板呈圆弧形悬顶,在此悬顶范围内,上覆岩层垮至地表时,支架损坏多是后柱,多集中在35~65#支架之间。
(4)支架受水平推力作用推向煤壁。
第二次上覆岩层垮至地表的过程中,断裂岩块发生转动,朝向支架尾部,产生水平推力,可使支架向前200~400mm,冲击破坏支架推移装置与输送机连结筒和立柱接长杆。
表3P-1工作面上覆岩层垮至地表时的立柱压力统计
支架位置1~20#21~40#
41~60#61~80#81~103#来压日期18/517/628/517/617/628/517/628/517/6记录个数1715131578151218压力平均值/MPa60.562.889.277.898.776.193.393.772.4均方差/MPa13.27.914.812.67.512.68.530.918.2最大值.010*********坏表数358518136125
(5)来压速度快,立柱刚性支撑损坏支架。
工作面上覆岩层两次垮至地表,来压速度均是很快的,活柱下缩迅速,支架很快被压死。
特别是第二次垮至地表后,顶板继续来压,立柱郸于刚性支撑顶梁状态,立柱穿透顶梁,柱窝破裂,立柱罐口损坏。
上列特征与中国大同坚硬顶板工作面剧烈来压破坏支架的表现相类似。
4针对压特点采取的改进措施
上述[换行]分析表明,巴兰布矿P-1工作面岩性变化区内岩层属难冒顶板,中印专家面对现实,除在支架上采取提高支撑能力将支护强度提高到84.5t/m2,工作阻力提高到5024kN/架以外,主要采取了地面滞后工作面于其中部钻眼爆破。
4.1炮眼布置
在工作面中部采空区上方从地面打6至26个炮眼,一般每排布置13~15个炮眼。
从1998年8月12日至P-1工作面结束,共在地面爆破30排炮眼。
前四排爆破不太正规,后来步入正轨。
其排距15m,孔深一般为30~35m,滞后工作面16~27m。
爆破参数见表5。
表4P-1工作面上覆岩层垮至地表时来压强度
支架位置
来压日期1~20#21~40#41~60#61~80#81~103总计
28/51.071.361.291.681.321.35
17/61.161.641.461.601.301.43
4.2炮眼装药结构
炮眼直径100mm,装药长度约6m,分两段装药。
药卷直径为83mm,每卷炸药长45cm,重2.75kg,每孔装药约18卷,每孔装药总量约50kg。
利用导爆索、电雷管及发爆器起爆。
利用砂子、泥土和速凝水泥及水充填炮眼,填充深度约30m。
炮眼布置和装药量可视岩性变化而调整,因顶板来压使钻孔变形、漏气,也可封堵后再装药放炮。
表5印度巴兰布矿P-1工作面地面爆破参数
序号日/年月炮眼至开切眼距离/m工作面至开切眼距离/m裂缝至开切眼距离/m炮眼至工作面距离/m炮眼至支架尾距离/m炮眼数量炮眼覆盖范围(支架数)钻孔漏气
112/98.8176191172161112531~67
217/98.819020918919149531~67
320/98.820622*********630~40
423/98.82262472292116262614~88
526/98.8241258229171210735~72
628/98.8256278251221710720~16
5采取改进措施后的效果
5.1地面爆破对切断上覆岩层效果明显
(1)由表6可知,地面爆破后上覆岩层断裂步距缩短25%,来压强度降低6%,在垮至地表时支架工作阻力占额定值之比降低了12%。
(2)P-1工作面结束后,全套设备撤至第2工作面,从至P-2工作面开切眼内侧17m处布置第一排炮眼,而后每隔15m布置一排炮眼,每排炮眼13个,其它爆破参数、装药结构基本上与P-1工作面相同。
在第一次垮至地表范围内,下沉盆地P-2工作面大于P-1工作面,最大下沉量分别为87mm和69mm,P-2工作面比P-1工作面减少了20%。
因此,在P-2工作面上覆岩层垮至地表时,工作面矿压不明显,支架受载中部略有增大,最大工作阻力为43MPa,支架无损坏,比较安稳地渡过了顶板初次来压。
其后因坚持地面爆破,顶板来压也未导致支架压死和损坏。
表6巴兰布矿P-1工作面地面爆破前后上覆岩层来压参数对比
地面爆破状况未爆破地面滞后工作面20m左右间隙15m工作面中部爆破
上覆岩层断裂区间第1-2次垮至地表期间第2~3次垮至地表期间第3~4次垮至地表期间
断裂间距/m848684
来压次数/次688
平均来压步距/m1410.7510.5[换行]垮至地表来压强度1.431.331.38
垮至地表工作阻力/kN4678~519952175162
支架受载与额定值之比/%118104103
5.2在坚持地面爆破的条件下,提高支架工作阻力后,支架未发生损坏1998年6月17日巴兰布矿P-1工作面上覆岩层垮至地表,工作面停产。
经更换已损坏的安全阀、液控单向阀、压力表、立柱和顶梁,于1998年8月3日恢复生产。
1998年8月10日在工作面推至距开切眼183~184m处,顶板来压。
当工作面推至距开切眼192m处,在至开切眼175m处于工作面中部采空区上方,第一次在地面爆破了12个炮眼。
尔后至开切眼190m处,于地面爆破了9个炮眼。
在至开切眼206m处地面爆破了6个炮眼,结果工作面又一次显现强烈来压,支架实测工作阻力达5400kN,为额定值的108%,来压强度达1.41。
随即在至开切眼226m处地面爆破了26个炮眼,支架受载立即降了下来。
以后每隔15m在地面爆破9~13个炮眼。
当工作面推至距开切眼254m处,上覆岩层第三次垮至地表。
来压期间支架工作阻力实测平均为5217kN,为额定值104%。
立柱下缩仅100mm,安全阀有时开启,经快速推进,支架恢复到正常工作状态。
地面爆破后,P-1工作面上覆岩层两次垮至地表,此间经历17次顶板来压,支架工作阻力实测平均值为5093kN,仅超过额定值1.4%。
经历276个循环,支架工作阻力实测总平均值为4199kN,为额定值的83.4%,但最大值为6280kN,为额定值的125%,支架无一损坏。
表7地面爆破前后支架初撑力实测值对比
爆破状态架号平均值P0均方σPoP+σPoPmax>P+σPo比例/%P<+σPo比例/%/kN/%/kN/%/kN/%/kN/%未爆破52#275773.055314.7331087.8376810020.7979.21爆破后54#354794.252814.0040761084961131.720.4079.60
注:
为额定值与额定值之比
5.3支架初撑力提高
经对安全阀和液控单向阀调定、检修,在地面爆破期间,支架初撑力明显提高了21%,见表7。
其后柱比前柱提高的更多,显然对控制顶板来压是有作用的。
5.4地面爆破后支架工作状况明显改观
地面爆破后,由于安全阀、液控单向阀得到调定和检修,立柱工作阻力由35MPa提高到40MPa,加之精心操作,保证了初撑力,结果如表8所示,立柱初撑式所占比例比未爆破时降低了70%~75%。
立柱降阻式所占比例比未爆破时降低了65%。
这样增阻式所占比例上升为83.5%,比未爆破时提高44%~53%。
显然支架工作状况是良好的。
它对控制好顶板起到了积极作用。
表8地面爆破前后支架运转特性(P—T)类型分布对比%
柱别爆破状态架号初撑式Po=Pm一次增阻式二次增阻式三次增阻式多次增阻式降阻式Po>
Pm增阻式Po
未爆破52#44.8714.8019.981.852.9615.5439.59爆破后54#11.0028.4035.805.1014.25.5083.50后柱未爆破52#41.1120.2820.281.954.6811.7047.19爆破后54#12.5029.033.208.0013.204.0083.50
总而言之,针对巴兰布矿5号煤层围岩条件及矿压特点,因将支架工作阻力由4400kN提高到5024kN,保证足够初撑力,缩小梁端距,控制采高,加快推进,特别是在工作面中部采空区上方采取滞后煤壁地面爆破等措施,使得该面上覆岩层岩性发生了变化,顶板来压步距缩短,来压强度降低,岩石膨胀性增大,工作面顶板来压平缓,活柱下缩量减少,支架工作正常。
尽管工作面中部支架安全阀在顶板来压时还有时开启,但在推采2m左右,支架受载升高就可恢复到支架额定工作阻力以下。
全工作面支架在较长时间内在低于额定工作阻力状况下工作,支架再未发生损坏。
因此,提高了工作阻力[换行]的ZZ4400/14/27型支撑掩护支架,在工作面中部地面滞后爆破的条件下,基本上能适应巴兰布矿5号煤层难冒顶板的需要。
实践得来的经验是宝贵的,生产获得的效益是显著的。
此经验已在巴兰布矿P-2工作面和拉金达矿P-16工作面推广。