栽植机械.docx
《栽植机械.docx》由会员分享,可在线阅读,更多相关《栽植机械.docx(32页珍藏版)》请在冰豆网上搜索。
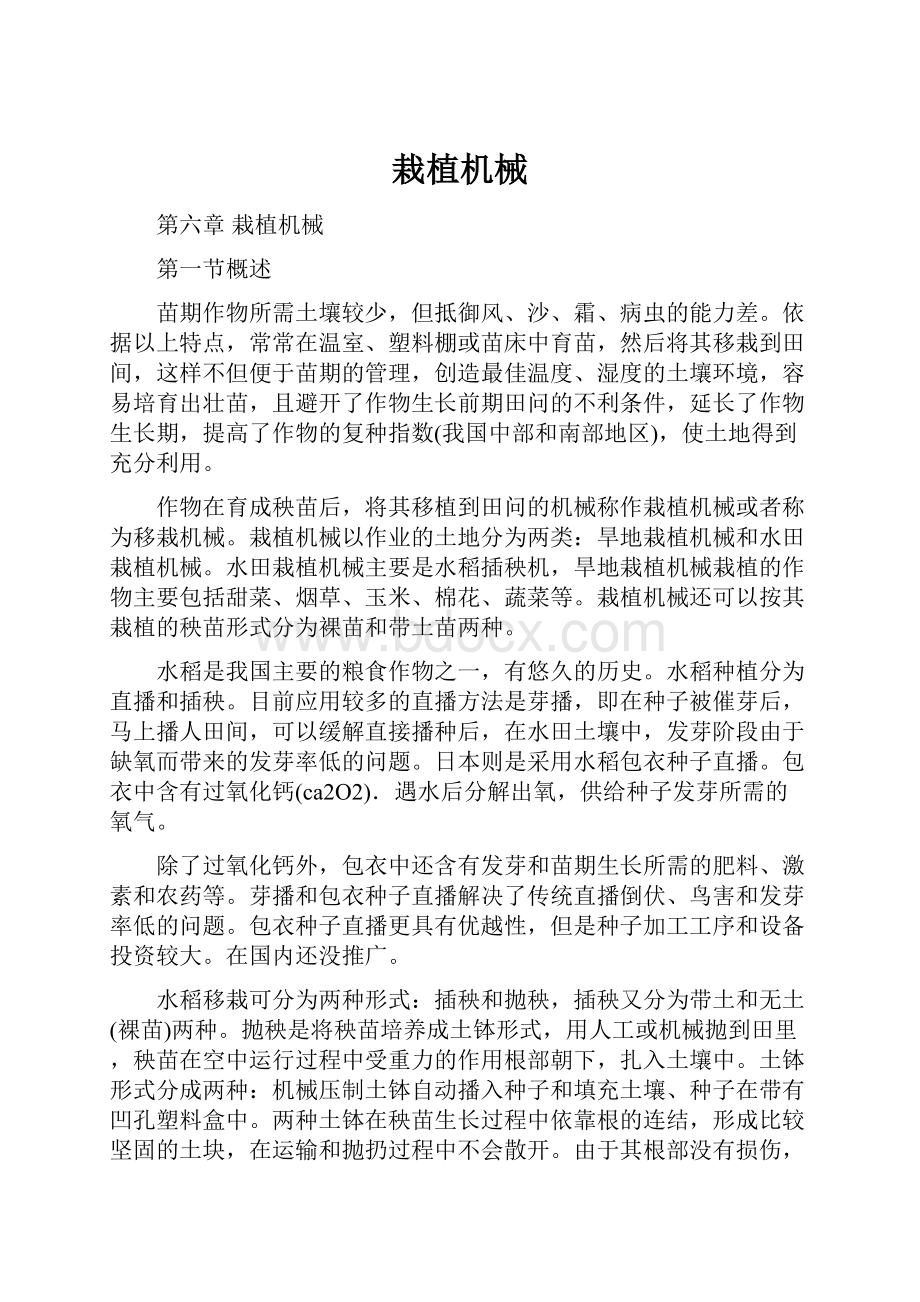
栽植机械
第六章栽植机械
第一节概述
苗期作物所需土壤较少,但抵御风、沙、霜、病虫的能力差。
依据以上特点,常常在温室、塑料棚或苗床中育苗,然后将其移栽到田间,这样不但便于苗期的管理,创造最佳温度、湿度的土壤环境,容易培育出壮苗,且避开了作物生长前期田问的不利条件,延长了作物生长期,提高了作物的复种指数(我国中部和南部地区),使土地得到充分利用。
作物在育成秧苗后,将其移植到田问的机械称作栽植机械或者称为移栽机械。
栽植机械以作业的土地分为两类:
旱地栽植机械和水田栽植机械。
水田栽植机械主要是水稻插秧机,旱地栽植机械栽植的作物主要包括甜菜、烟草、玉米、棉花、蔬菜等。
栽植机械还可以按其栽植的秧苗形式分为裸苗和带土苗两种。
水稻是我国主要的粮食作物之一,有悠久的历史。
水稻种植分为直播和插秧。
目前应用较多的直播方法是芽播,即在种子被催芽后,马上播人田间,可以缓解直接播种后,在水田土壤中,发芽阶段由于缺氧而带来的发芽率低的问题。
日本则是采用水稻包衣种子直播。
包衣中含有过氧化钙(ca2O2).遇水后分解出氧,供给种子发芽所需的氧气。
除了过氧化钙外,包衣中还含有发芽和苗期生长所需的肥料、激素和农药等。
芽播和包衣种子直播解决了传统直播倒伏、鸟害和发芽率低的问题。
包衣种子直播更具有优越性,但是种子加工工序和设备投资较大。
在国内还没推广。
水稻移栽可分为两种形式:
插秧和抛秧,插秧又分为带土和无土(裸苗)两种。
抛秧是将秧苗培养成土钵形式,用人工或机械抛到田里,秧苗在空中运行过程中受重力的作用根部朝下,扎入土壤中。
土钵形式分成两种:
机械压制土钵自动播入种子和填充土壤、种子在带有凹孔塑料盒中。
两种土钵在秧苗生长过程中依靠根的连结,形成比较坚固的土块,在运输和抛扔过程中不会散开。
由于其根部没有损伤,秧苗入土后,返青早,分蘖快,有利于增产。
目前人工和机械抛秧,都属于漫撒型,给以后田问管理带来很大困难,也使人工收割增加难度,土钵自由落体于地表面,扎根浅,后期容易倒伏;优点是无论人工或机械抛秧其效率很高,产量也不低于插秧,即便是机械抛秧,一次性投入也低于插秧,工艺容易掌握。
水稻移栽是一项季节性强、劳动强度大、投放劳动力多的种植环节,实现水稻栽植机械化可改善工作条件,减轻劳动强度,提高作业效率。
日本是水稻插秧机械化先进国家。
60年代之前处于探索阶段,60年代初研制出曲柄摇杆式分插机构作为栽植部件的插秧机。
以后在栽植臂内安装了推秧装置,大大提高了栽植的可靠性。
60年代后期,在秧苗培育上采用了盘育秧,从而使插秧机很快推广。
为了减少振动,延长机器寿命,在分插机构的曲柄上又安装了配重,提高了单位时间插次。
80年代后期,日本又推出了高速插秧机,并配以侧深施肥装置。
高速插秧机采用偏心齿轮行星系分插机构。
侧深施肥装置将肥料按农艺要求施与根部附近位置,不但使施肥量减少到原来的7/16,而且提高了产量和减少了下游水域的污染。
我国从50年代开始研究插秧机,60年代初研制出转臂滑道式分插机构的水稻插秧机,用于裸苗插秧。
1967年鉴定了第一台该形式的插秧机,1979年统一了机型但发展缓慢。
80年代初引进日本工厂化育秧技术,由吉林省四平市农机研究所研制出曲柄摇杆式分插机构为栽植部件的插秧机,在东北三省大量推广,并逐渐在全国取代转臂滑道式分插机构的插秧机。
插秧机工作质量与分插机构有直接关系,常用下列指标来衡量水稻机械插秧质量。
1.漏插率漏插率指无秧苗的穴数(包括漏插和漂秧)占总穴数的百分率。
一般要求漏插率低于2%。
2.勾伤秧率勾秧是指秧苗栽插后,叶鞘弯曲至90°以上。
伤秧是指秧苗叶鞘部有折伤、刺伤、撕裂和切断等现象。
秧苗栽插后,勾秧、伤秧的总数占秧苗总数的百分比称为勾伤秧率。
一般要求勾伤秧率在5%以下。
3.均匀度合格率均匀度合格率指每穴苗数符合要求的穴数占总穴的百分比。
一般要求均匀度合格率在85%以上。
4.直立度直立度指秧苗栽插后与铅垂成偏离的程度,与机器前进方向一致的倾斜称为前倾,用正角表示,反之称为后倾。
为避免刮风时出现“眠水秧”(即秧梢全部躺在水里),该角的绝对_直应小于25°为宜。
5.翻倒率翻倒率指带土苗倾翻于田中,使秧叶与泥土接触的穴数占总穴数百分比。
一般要求不大于3%。
第二节水稻育秧设备
一、一般育秧过程和育秧设备
1.田间盘育秧田间盘育秧是利用稻茬田做床板,放上秧盘的框形模子,铺入有孔地膜,撒上调制好的床土。
然后将经过消毒、浸种、催芽后的稻种播入盘内,覆土后喷洒除草剂并盖上薄膜,齐苗后揭去薄膜,让秧苗在自然环境中生长,一般18~20天后即可上机插秧。
田间盘育秧的工艺流程如下:
做床板用的稻茬田,冬前将稻茬平地面割掉,按2m一畦挖沟(床面宽1.8m,沟宽0.2m),沟土铺放在床面上。
经过冬天风化后整平。
秧盘的规格根据插秧机的行距决定,7寸行距用580×215mm秧盘。
9寸行距用580×275mm秧盘。
床土来源一般是结合表田排水、开沟取土,在田问堆积过冬,经冻融作用,风干后用0.6~0.8cm筛孔过筛,然后拌入一定数量的草木灰、硫酸钾、硫酸铵、过磷酸钙等。
床土放入秧盘后。
应喷洒一定数量的工业硫酸与敌克松混合液,使床土的pH值降到4.5~5.5左右,并可防止立枯病发生。
混合液由50kg清水,10ml工业硫酸和10g敌克松混合而成,每盘喷洒混合液约1.25kg。
注意苗期管理,白天天气晴好气温高时,要揭膜散温,保持床土湿润状态。
2.工厂化育秧带土苗工厂化育秧一般是在育秧盘内播种来进行育秧的,其过程及使用的设备如图6-l所示。
稻种要经过选种、消毒、浸种和催芽。
苗床土经过碎土、消毒、干燥、筛土和混合肥料,因此要配备碎土机、筛土机和肥料混合机。
往育秧盘内装土、洒水、播种和覆土,均由盘秧播种机一次完成。
为了播种后种子的出芽,要有育秧器或育秧房。
秧苗绿化和硬化要在绿化室和硬化室内配备加温设备、控制装置和供水装置等。
在育秧盘的使用上与日本工厂化育秧不同之处是:
我国多采用硬盘(俗称母盘)和软盘(俗称子盘)配合使用。
在播种时,将硬盘内衬软盘,充土、播种、覆土后,软盘连同土壤和种子从硬盘中端出。
育秧硬盘只用于播种,可以重复使用。
这样,在维持能够连续作业情况下,硬盘数量不需太多,大大降低了成本。
图6—1工厂化育秧一般过程
二、盘育秧播种机
为了保证机动插机插秧的均匀度,采用播种比较均匀的盘育秧播种机是很必要的。
盘育秧播种机(图6一2)由机架、育秧盘、移动机构、充土机构、洒水装置、播种机构、覆土机构等组成。
盘育秧播种机工作过程如下:
人工放盘→充土→洒水→播种→覆土→人工取盘
由于人工放盘后,充土、洒水、播种、覆土四个工艺过程机器上一次完成,所以称该机作业为盘育秧播种流水线。
人工放盘:
将内衬软盘的硬盘连续放置于一端输送带上。
输送带是盘育秧移动装置的一部分,由三角带轮驱动,主动三角带轮依靠链条驱动,它们与其它各机构是同步联动的。
充土:
由充土机构完成(图6—3),充土皮带自动将床土箱的土壤送出,落入育秧盘,用经过人字型旋转毛刷,压实和平整盘内土壤,一般充土层为2cm厚。
可通过调节皮带与上方刮土板的问隙来调整充土厚度。
洒水:
由抽水泵将水箱内水抽到喷水管子里,然后均匀喷洒在充土后的秧盘内。
播种:
由播种机构完成(图6—4),播种轮转动,轮表面的凹槽或凹孔将种子均匀排出,落入秧盘内湿土上。
转动调整手柄,联动齿轮带动齿条改变排种间隙,调整排种量。
覆土:
由覆土机构完成(图6—4),覆土轮转动,将土壤均匀地抛洒在种子上,一般为1cm厚。
取盘:
在一端将完成播种作业的育秧盘取下。
图6—3育秧盘充土机构
1.输送皮带2.旋转毛刷3.充土皮带4.床土箱
图6-4播种机构和覆上饥构
1.播种轮2.输送皮带3.种子箱4.土箱5.覆土轮
第三节水稻插秧机的一般构造
插秧机用于水田移栽秧苗,包括带土移栽和无土移栽(水洗苗移栽)两种机械。
日本旱育稀植带土苗技术引进后,无土移栽插秧机已较少使用。
本节主要介绍带土苗移栽插秧机的一般构造(图6—5)。
无论是步行式、乘坐式或者高速插秧机,其主要由以下几个部分组成:
动力机、传动系统、送秧机构、栽植机构和行走装置,下面将分别介绍。
一、动力机
动力机有汽油发动机和柴油发动机两种。
日本生产的各种型式插秧机均采用汽油发动机,其优点为:
重量轻(同样马力是柴油机重量的1/3)、启动方便。
缺点是油料价格高
(相同功率消耗下)。
插秧机所用的小马力汽油发动机,制造工艺要求较高,国内产品使用可靠性差(近几年通过引进技术生产的汽油发动机质量有大幅度提高),国产2ZT系列插秧机当时采用了柴油发动机。
图6—52ZT一9356型水稻插秧机
1.压秧杆2.秧箱3.操向盘4.发动机‘5.行走传动箱6.水田轮7.挂链8.秧船
9.尾轮10.链箱n.栽植臂12.摇杆
注:
传动箱在秧箱下面
二、传动系统
将发动机动力传递到各工作部件,主要有两个方向:
传向驱动地轮和由万向节传送到传动箱。
传动箱又将动力传递到送秧机构和分插机构。
分插机构前级传动配有安全离合器,防止秧针取秧卡住时,损坏工作部件。
传动箱是传动系统中间环节,又是送秧机构的主要工作部件。
传动箱中主动轴上有螺旋线槽(凸轮滑道),从动轴上固定着滑块,当主动轴转动时,滑块在螺旋线槽作用下横向送动,将主动轴的转动变成滑块和从动轴的移动,该轴的移动即是横向送秧的动力来源。
三、送秧机构
在每次分插机构取秧后,秧苗移动,秧块填补已取秧位置,为下一次取秧做准备。
送秧分横向和纵向两种,每横向取完一排秧苗,纵向送秧一次,将秧苗推向下方,为取下一排秧做准备。
横向送秧分为连续式和间歇式。
间歇式是在每次横向送秧结束后取秧。
此时,秧块处于静止位置。
从理论上讲,切下秧块比较平整,但是随着单位时间插次提高,间歇式横向送秧振动太大,目前大多已被连续式送秧机构替代。
送秧机构与分插机构同步联动,对于曲柄摇杆式分插机构是,曲柄旋转一周,移动一个取秧宽度距离;对于偏心齿轮行星系分插机构,则旋转一周,移动两个取秧宽度距离。
四、栽植机构
栽植机构(或称移栽机构)在插秧机上统称分插机构,是插秧机的主要工作部件之一。
目前市场上最常见的分插机构是曲柄摇杆式分插机构和偏心齿轮行星系分插机构(配置高速插秧机上),其栽植臂的结构、功能和原理大致相同。
取秧前,凸轮的作用使推秧杆回收,秧针(秧爪)前部腾出2cm左右位置取秧,当秧针随同秧苗插入土壤中时,凸轮转到缺口处,拨叉在弹簧作用下,推动推秧杆将秧苗推离秧针,直立于土壤中。
五、行走装置
插秧机的行走装置由行走轮和船体两部分组成。
常用的行走装置(除船体外)分为四轮、二轮和独轮三种,所用的行走轮都具备以下三个性质:
(1)泥水中有较好的驱动性,轮圈上附加加力板;
(2)轮圈和加力板不易挂泥;
(3)具有良好的转向性能。
插秧机到地头要转向180。
,因此要求有较好的转向功能。
四轮行走装置的转向是由前轮引导的,二轮行走装置由每个轮子的离合制动作用来完成转向,国产2ZT系列插秧机(乘坐式)是依靠独轮转向来完成整机转向。
而日本产独轮步行机,是依靠操作者提升浮子摆动扶手完成。
日本插秧机,无论是乘坐式还是步行式插秧机,其船体部分均为分体液力自动控制浮子式,其优点是承重能力强,防陷,消除水浪和防壅泥等性能均较船板式优越,但其液压件加工精度要求高,成本也较船板式高。
国产插秧机配置的船板基本上仅适应东北三省水稻种植工作要求,但在泥脚较深和含沙量较少的土壤中,仍然会产生下陷、壅泥、壅水推倒已插秧苗的问题,特别是在南方双季稻地区,春季稻收获后,不可能在平整土地后有两、三天作为土壤沉淀的时间,船板式壅水壅泥的现象十分严重,也曾在结构上采取一些改进措施,但在部分地区仍然不能根本解决壅水壅泥带来的漂秧、埋秧等问题。
第四节分插机构
分插机构是水稻插秧机的主要工作部件,包括分插器和轨迹控制机构,在供秧机构(秧箱和送秧机构)的配合下,完成取秧、分秧和插秧的动作,其工作性能对插秧质量有十分重要的影响。
分插器又称秧针,是直接进行分秧和插秧的零件,有钢针式(分离针)和梳齿式两种。
钢针式分插器上还带有推秧器,用于秧苗插入泥土后,把秧迅速送出分离针,使秧苗插牢。
轨迹控制机构的作用是控制分秧器,使其按一定的轨迹运动,完成所要求的分、插秧工作,目前多用曲柄摇杆机构,此外还有偏心齿轮行星系机构。
一、曲柄摇杆式分插机构
1.结构曲柄摇杆机构主要由曲柄、摇杆和栽植臂组成(图6-6),曲柄安装在与机架固定铰接的传动轴上,把传动轴的动力传给栽植臂。
摇杆一端连接栽植臂,另一端固定在机架上。
栽植臂是一连杆体零件,前端安装分离针。
由于摇杆的控制作用,栽植臂把曲柄的圆周运动变为分插秧的特定的曲线运动,带动秧针完成分秧、运秧、插秧和回程等动作。
曲柄摇杆式分插机构的工作过程由曲柄、栽植臂、摇杆和机架组成的四连杆机构控制。
当曲柄随传动轴旋转时,栽植臂被驱使绕传动轴作偏心转动,但其后端又受摇杆的控制,从而使秧针形成特定的运动轨迹(图6-7),保证秧针以适当的角度进入秧门分取秧苗,并近似于垂直方向把秧苗插入土中。
秧苗入土后,栽植臂中的曲轮卸去对推秧弹簧的压力.于是弹簧推动拨叉使推秧器迅速推出分离针。
图6一6前插式曲柄摇杆分插机沟
l.摇杆2.推秧弹簧3.栽植臂盖4.拨叉5.分离针6.推秧器7.凸轮8.传动轴9.曲柄10.戡植臂
曲柄摇杆式分插机构根据配置方式的不同可分为前插式(又称卧式.图6一6)和后插式(又称立式,图6—8)两种。
沿插秧机前进方向,前插式分插机构配置在秧箱的后方,其摇杆与机架铰接点位于曲柄传动轴的后上方,我国2ZT系列插秧机和日本产的乘坐式插秧机基本上采用前插式。
后插式分插机构配置在秧箱的前方,其摇杆与机架铰接点位于曲柄传动轴的下方,日本产的一些步行式插秧机采用后插式。
前插式和后插式曲柄摇杆机构,其构造和工作原理基本相同,但秧针的运动轨迹有所不同。
图6—7是这两种分插机构秧针运动轨迹示意图,实线部分是秧针相对于插秧机的运动轨迹(相当于插秧机不行驶时秧针的轨迹),它是一条封闭的环线;虚线部分是秧针的绝对运动轨迹,即插秧机前进和秧针相对于插秧机运动的合成运动轨迹。
对于大苗移栽,特别是双季稻的后季稻插秧,由于秧苗较长,前插式容易发生“连桥”现象,即把前面已插秧苗的秧尖,又插到下一株秧苗的根部(图6—7a),后插式则可避免这种情况。
图6—7曲柄摇杆分插机构
(a)前插式(b)后插式
曲柄摇杆机构插秧频率一般为200~220r/min,加平衡块后,插秧频率可达250~270r/min。
这种分插机构运动平稳、结构简单、密封耐用。
其各铰接点均为滚动轴承.以保证转动层灵活和运动轨迹准确。
传动轴上安装有牙嵌式安全离合器,在分秧和插秧阻力过大时(如秧针碰到石块、树根等),可以通过牙嵌斜面压缩弹簧自动切断动力,使栽植臂停止工作,起到保护分插机构的安全作用。
2.分插机构的运动分析两种形式分插机构所建立的运动学和动力学数学模型是相同的,下面以前插式分插机构为例进行分析.在动力学分析中,应注意:
驱动力(平衡力)不是假设为力偶矩,而是以实际链条力来分析;铰链点摩擦矩由于凸轮(图6—9中A点)密封圈作用而较大,计入动力学方程;推秧装置在推秧和碰撞过程计入动力学方程,而不是简化为曲柄摇杆机构。
图6—8后插式曲柄摇杆分插机构
1.摇杆2.曲柄3.凸轮4.推秧弹簧5.栽植臂盖6.栽植臂7.拨叉8.分离针9.推秧器
矢量方程:
位移方程:
将两式联立,得到
(6—4)
其中,
可求
由于
所以由式6-4可求α3。
XB,YB,α2以及X2,Y2,X3,Y3,XD,YD可求。
XD,YD方程为:
对式(6-2)、(6—3)求导后联立得到
对式(6—2)、(6—3)二次求导联立得到:
图6一9分插机构的运动分析
其中
由此X2,Y2,X3,Y3可求。
在对曲柄摇杆式分插机构作动力学分析时,应注意以下几点:
①曲柄摇杆式分插机构动力学分析较之一般曲柄摇杆机构更为复杂,它的栽植臂内含推秧装置,在推秧过程中其随栽植臂运动同时又相对栽植臂转动,在推秧结束时,碰撞缓冲垫。
通过试验结果知道,碰撞瞬时,给栽植臂的作用力传递到曲柄转动中心和摇杆轴,使它们产生一个作用力峰值,是不可忽略的,因而不能作为一般的曲柄摇杆机构进行动力学分析。
②平衡力(驱动力)产生的力偶矩在一个周期内时而为正,时而为负,而平衡力是依据链条伸出的两个方向确定的,它没有正负之分。
因而不能用矩阵方法求解动力学方程组。
用矩阵求动力学方程,势必在平衡力矩为负时,求得链条力为负值,这与实际不符。
③由于其橡胶密封圈作用产生较大铰链点摩擦力矩,忽略它们产生误差,在方程中引入摩擦力矩,则使线性方程组转为非线性,再则有的摩擦力矩的方向在周期内发生变化,以上问题需在计算时作数学和程序编制方面的处理。
④计入以上因素,所建立的模型和计算结果才有可能与试验测定结果比较吻合。
二、偏心齿轮行星系分插机构
行星系齿轮机构对称设置作为插秧机分插机构,每旋转一周可以插秧二次,与曲柄摇杆式分插机构比较,振动小,在提高单位时间插次方面,具有较大潜力。
该机构可以有三种齿轮传动形式供选择:
圆齿轮传动、非圆(椭圆)齿轮传动和偏心齿轮传动。
圆齿轮传动的优点是加工工艺简单,但有以下缺点:
(1)相对运动工作轨迹为圆,只有在机速较高的情况下其工作轨迹(绝对运动轨迹)一余摆线的摆环,才能满足插秧要求,而栽植株距变大。
(2)其半径为中心齿轮(太阳轮)与第三齿轮中心距离。
增加封闭环(在此是圆)高度,势必增大齿轮和机构尺寸。
(3)秧针不能同时满足取秧和插秧。
非圆齿轮行星系分插机构相对运动轨迹为腰果形,其工作轨迹(相对地面)符合插秧要求,秧针的取秧和插秧角度以及封闭环高度也较易满足设计要求,工作平稳,但加工工艺复杂。
偏心齿轮行星系分插机构与非圆齿轮行星系分插机构比较,具有相类似的相对运动轨迹和绝对运动轨迹,在偏心距较大情况下,工作过程齿隙变化大,引起振动,但加工工艺简单。
由于分插机构轴的转速较低(170~180转/分),在偏心距较小的情况下,齿隙变化也较小。
目前市场出售的日本高速插秧机采用了偏心齿轮行星系机构作为分插机构,在机构上附加了消除齿轮的防振装置。
1.结构与工作过程偏心齿轮行星系分插机构如图6—10所示,其栽植臂结构形式与曲柄摇杆式分插机构相近。
栽植臂固定在末端齿轮。
共5个齿轮,半径相同,齿轮I为太阳轮,固定不动,对称两边分置两对齿轮。
靠近太阳轮的为齿轮Ⅱ,两端齿轮为齿轮Ⅲ,推秧凸轮固定在齿轮Ⅲ的轴上,行星系架在转动时,齿轮Ⅲ相对行星系架转动,由于栽植臂随齿轮Ⅲ相对凸轮的转动,带动推秧杆运动而压缩推秧弹簧。
在凸轮缺口处,推秧弹簧释放能量,驱动推秧杆将秧苗从秧针上推入土中。
由于机构旋转一周插秧两次,在中心轴转速降低(比较曲柄摇杆式)的情况下,单位时间插次反而多,而且取秧速度也有所降低,伤秧率随之减少。
2.偏心齿轮传动的性质
(1)偏心齿轮行星系机构在转动过程中。
轴心距大于或等于(φ=O或φ=π时)两圆心距,这个性质对机构的设计是非常重要的。
它决定了偏心齿轮两个节圆半径之和小于轴心距,否则在工作中会产生“顶死”现象,即两个齿轮啮合到一定位置,其节圆中心距离小于两节圆半径加齿顶间隙之和。
图6—11为图6—10中两偏心齿轮I和Ⅱ,0点和B点为齿轮轴心,O1和02分别为两偏心齿轮中心。
当行星系架转过φ角后。
其啮合齿数相等,则有
过B点作BB1和过O1点作01B1相交于B1点,使
因为
且
所以
故,
因此,无论行星系架转动到任何位置,
在直角三角形,
也就证明了
(2)对图6—11分析,可以得到齿轮中心距最大值和最小值。
当行星系架转角φ=0和φ=π时,且矢量O1O2和02B处于同方向,O2和B2点重合,三角形02BB1变成一条线段,此时0102=OB,齿轮中心距等于轴心距,处于最大值。
当行星系架转到
时。
010∥02B且矢量001和O2B处于反方向,三角形02BB1中∠02BB1=π(变成02BB1线段),此时02B1处于最大值。
在三角形0102B1中,01O2处于最小值。
图6一l0偏心齿轮行星系分插机构示意图
1.推秩凸轮2.推秧弹簧3.插秧拨杆4.栽植臂壳5.推秧杆6.秧针7、8、9.齿轮I、Ⅱ、Ⅲ10.行星系架
图6-1l偏心齿轮传动示意图
设齿轮节圆半径为R,
εo为齿顶最小允许间隙,为加工方便,设ε为偏心率,
由性质1知,L>2R,则K<εo。
(3)两啮合齿轮中心线等分两齿轮轴心连线。
证明这个性质为偏心齿轮行星系机构理论分析建立了基本依据,证明如下:
前面已推得θ1=θ4,可见OA=AB=L/2。
以上推论是对偏心齿轮行星系分插机构齿轮I和齿轮Ⅱ所作分析得到的,实际上如果让行星系架固定不动,齿轮I反向转动,可以得出同样的结论。
因此以上三点也是偏心齿轮传动的性质。
3.参数关系通过建立模型,编程计算得到以下关系:
(1)随着行星系架转角φ改变,齿轮中心距与齿轮轴心距之差(K1和K2)的变化规律近似于下移的余弦曲线(图6—12)。
K1为轮I(太阳轮)和轮Ⅱ的齿轮中心距与齿轮轴心距之差,K2为轮Ⅱ和轮Ⅲ的齿轮中心距与齿轮轴心距之差。
(2)图6-12表明最大齿轮中心距与轴心距相对偏差K1max与K的关系,以及轨迹封闭环高度H和两倍轴心距L的比值HL(HL—H/2L)与K值的关系。
随着K值增大,Klmax增大加快,而HL增长变缓,建议取K<0.14。
(3)通过图6-13,由K值确定最大齿轮间隙,最大齿隙即为轴心距L和齿轮中心距之最大差值K1max,再加上允许最小齿顶间隙。
实际加工中,精度要求是一个范围,其基本原则是:
在转动过程中,既不会由于轴心距太小而造成齿轮旋转过程中“顶死”,又不会因为轴心距太大,形成齿隙过大,而引起振动,建议在设计中满足以下公式:
式中εd——齿顶间隙最大值。
这是一个比较小的范围,除了加工精度要求较高之外,在计算时,K值用e/L,而不用偏心率ε值e/R代替,以免造成误差。
(4)各参数变化与秧针相对运动轨迹的关系
改变ε、α0、φ0、S、R,秧针相对运动轨迹发生变化(图6—14)。
ε为偏心率,α0为秧针与齿轮Ⅲ轴心连线相对各轴心连成的角位移,仍为各轴心连线与x轴(水平线)的初始角位移。
在此位置,各齿轮中心与各齿轮轴心连线重合。
s为齿轮Ⅲ轴心到秧针尖距离,R为齿轮节圆半径。
各参数值的变化情况见表6—1。
图6-14秧针相对运动轨迹变化图
表6-1各参数的变化
图号
a
b
c
d
e
参数
I号轨迹
Ⅱ号轨迹
Ⅲ号轨迹
ε
O.05
O.15
O.25
α(°)
30
50
70
φ(°)
10
30
50
S(mm)
110
123
136
R(mm)
16
19
22
第五节送秧机构
送秧机构包括横向送秧机构和纵向送秧机构,其作用是从横向和纵向两个方向将秧箱中的秧苗不断地、均匀地向秧门输送,供分插器取秧。
一、横向送秧机构
横向送秧机构的作用是使秧针能在秧箱的工作幅宽内依次均匀取秧,采用的方式是使秧箱连同秧苗作整体移动,因此横向送秧机构又称移箱机构。
横向送秧根据秧箱移动的特点可分为问歇移箱和连续移箱两种。
问歇移箱在分插机构取秧过程中秧箱停止不动,等秧苗基本脱离秧箱后开始移箱。
其优点是分取秧过程中秧苗较整齐,有利于提高分秧质量。
缺点是秧箱自静止到运动或由运动到静止状态时,需要克服较大的惯性力,机器振动较大,易磨损,尤其在秧箱移动频率较高时,机器的工作状况变差。
拨洗苗插秧机和手动插秧机上常采用问歇移箱方式。
连续移箱在分插机构取秧过程中,秧箱保持连续不断地匀速移动。
从理论上说这种移箱