Doc4高炉炉况失常及处理文档格式.docx
《Doc4高炉炉况失常及处理文档格式.docx》由会员分享,可在线阅读,更多相关《Doc4高炉炉况失常及处理文档格式.docx(9页珍藏版)》请在冰豆网上搜索。
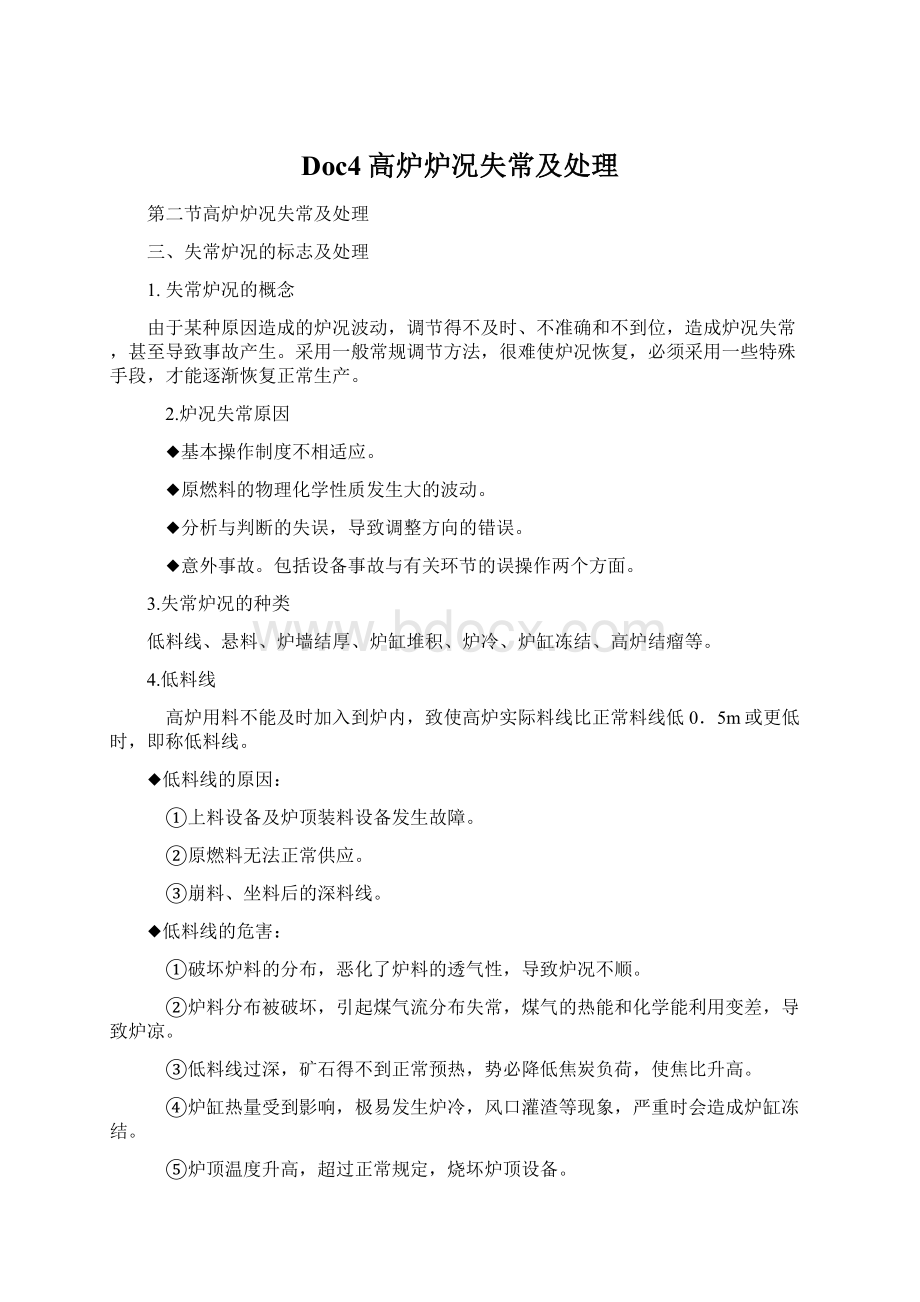
②炉料分布被破坏,引起煤气流分布失常,煤气的热能和化学能利用变差,导致炉凉。
③低料线过深,矿石得不到正常预热,势必降低焦炭负荷,使焦比升高。
④炉缸热量受到影响,极易发生炉冷,风口灌渣等现象,严重时会造成炉缸冻结。
⑤炉顶温度升高,超过正常规定,烧坏炉顶设备。
⑥损坏高炉炉衬,剧烈的气流波动会引起炉墙结厚,甚至结瘤现象发生。
⑦低料线时,必然采取赶料线措施,使供料系统负担加重,操作紧张。
◆低料线的处理:
①由于上料设备系统故障不能拉料,引起顶温高,开炉顶喷水或炉顶蒸汽控制顶温,必要时减风。
②不能上料时间较长,要果断停风。
造成的深料线(大于4m),可在炉喉通蒸汽情况下在送风前加料到4m以上。
③由于冶炼原因造成低料线时,要酌情减风,防止炉凉和炉况不顺。
④低料线1h以内应减轻综合负荷5%~l0%。
若低料线lh以上和料线超过3m在减风同时,应补加净焦或减轻焦炭负荷,以补偿低料线所造成的热量损失。
⑤当装矿石系统或装焦炭系统发生故障时,为减少低料线,在处理故障的同时,可灵活地先上焦炭或矿石,但不宜加入过多。
一般而言集中加焦不能大于4批;
集中加矿不能大于2批,而后再补回大部分矿石或焦炭。
当低料线因素消除后应尽快把料线补上。
⑥赶料线期间一般不控制加料,并且采取疏导边沿煤气的装料制度。
当料线赶到3m以上后、逐步回风。
当料线赶到2.5m以上后,根据压量关系情况可适当控制加料,以防悬料。
⑦低料线期间加的炉料到达软熔带位置时,要注意炉温的稳定和炉况的顺行。
⑧当低料线不可避免时,一定要果断减风,减风的幅度要取得尽量降低低料线的效果,必要时甚至停风。
5.悬料
炉料停止下降,延续超过正常装入两批料的时间,即为悬料;
经过3次以上坐料未下,称顽固悬料。
◆悬料的原因:
悬料主要原因是炉料透气性与煤气流运动不相适应。
◆悬料的种类:
按部位分为上部悬料、下部悬料;
按形成原因分为炉凉、炉热、原燃料粉末多、煤气流失常等引起的悬料。
◆悬料主要征兆:
①悬料初期风压缓慢上升,风量逐渐减少,探尺活动缓慢。
②发生悬料时炉料停滞不动。
③风压急剧升高,风量随之自动减少。
④顶压降低,炉顶温度上升且波动范围缩小甚至相重叠。
⑤上部悬料时上部压差过高,下部悬料时下部压差过高。
◆悬料的预防:
①低料线、净焦下到成渣区域,可以适当减风或撤风温,绝对不能加风或提高风温。
②原燃料质量恶化时,应适当降低冶炼强度,禁止采取强化措施。
③渣铁出不净时,不允许加风。
④恢复风温时,幅度不超过50C/h,加风时每次不大于150m3/min。
⑤炉温向热料慢加风困难时,可酌情降低煤量或适当撤风温。
◆悬料处理:
①出现上部悬料征兆时,可立即用改常压(不减风)操作;
出现下部悬料征兆时,应立即减风处理。
②炉热有悬料征兆时,立即停氧、停煤或适当撤风温,及时控制风压;
炉凉有悬料征兆时应适当减风。
③探尺不动同时压差增大,透气性下洚,应立即停止喷吹,改常压放风坐料。
坐料后恢复风压要低于原来压力。
④当连续悬料时,应缩小料批,适当发展边沿及中心,集中加净焦或减轻焦炭负荷。
⑤坐料后如探尺仍不动,应把料加到正常料线后不久进行第二次坐料。
第二次坐料应进行彻底放风。
⑥如悬料坐不下来可进行休风坐料。
⑦每次坐料后,应按指定热风压力进行操作,恢复风量应谨慎。
⑧悬料可临时撤风温处理,降风温幅度可大些。
坐料后料动,先恢复风量、后恢复风温。
⑨冷悬料难于处理,每次坐料后都应注意顺行和炉温,防热悬料和炉温反复。
严重冷悬料,避免连续坐料,只有等净焦下达后方能好转,此时应及时改为全焦操作。
⑩连续悬料不好恢复,可以停风临时堵风口。
⑾连续悬料坐料,炉温要控制高些。
⑿坐料前应观察风口,防止灌渣与烧穿,悬料坐料期间应积极做好出渣出铁工作。
⒀严重悬料(指炉顶无煤气,风口不进风等),则应喷吹铁口后再坐料。
⒁悬料消除,炉料下降正常后,应首先恢复风量到正常水平,然后根据情况,恢复风温、喷煤及负荷。
6.连续塌料
探尺停滞不动,然后又突然下落,称为塌料。
连续停滞、塌料称为连续塌料。
◆连续塌料的危害:
影响矿石预热和还原,特别是下部连续塌料,能使炉缸急剧向凉,甚至造成炉缸冻结事故。
◆连续塌料的征兆:
①探尺连续出现停滞和塌落现象。
②风压、风量不稳,剧烈波动,风量接受能力变差。
③顶压出现向上尖峰,并且剧烈波动,顶压逐渐变小。
④风口工作不均,部分风口有生降和涌渣现象,严重时自动灌渣。
⑤炉温波动,严重时铁水温度显著下降,放渣困难。
◆处理方法:
①立即减风到能够制止崩料的程度,使风压、风量达到平稳。
②适当减轻焦炭负荷,严重时加入适量净焦。
③临时缩小矿批,减轻焦炭负荷,采用疏导边缘和中心的装料或酌情疏导边缘。
④出铁后彻底放风坐料,回风压力应低于放风前压力,争取探尺自由活动。
⑤只有炉况转为顺行,炉温回升时才能逐步恢复风量。
⑥减氧或停氧。
7.炉缸堆积
◆炉缸堆积的原因:
①原、燃料质量差,强度低,粉末过多,特别是焦炭强度降低影响更大。
②操作制度不合理。
主要包括:
长期边缘过分发展,鼓风动能过小,或长期减风,易形成中心堆积;
长期边缘过重或鼓风动能过大,中心煤气过度发展,易形成边缘堆积;
长期冶炼高标号铸造生铁,或长期高炉温、高碱度操作;
造渣制度不合理,Al2O3和MgO含量过高,炉渣粘度过大;
长期过量喷吹。
冷却强度过大,或设备漏水,造成边缘局部堆积。
◆炉缸堆积的类型:
炉缸中心堆积和边缘堆积两种,见表4—28。
表4—28高炉炉缸堆积对比表
◆炉缸堆积征兆:
①接受风量能力变坏,热风压力较正常升高,透气性指数降低。
②中心堆积上渣率显著增加,出铁后,放上渣时间间隔变短。
③放渣出铁前憋风、难行、料慢,放渣出铁时料速显著变快,憋风现象暂时消除。
④风口下部不活跃,易涌渣、灌渣。
⑤渣口难开,带铁,伴随渣口烧坏多。
⑥铁口深度容易维护,打泥量减少,严重时铁门难开。
⑦风口大量破损,多坏在下部。
⑧边缘堆积一般先坏风口,后坏渣口;
中心堆积一般先坏渣口,后坏风口。
⑨边缘结厚部位水箱温度下降。
◆炉缸堆积处理:
①改善原、燃料质量,提高强度,筛除粉末。
②边缘过轻则适当调整装料制度,若需长期减风操作,可缩小风口面积、改用长风口或临时选择堵塞部分风口。
③边缘过重,除适当调整布料外,可根据炉温减轻负荷,扩大风口。
④改变冶炼铁种。
冶炼铸造铁时,改炼炼钢生铁;
冶炼炼钢生铁时,加均热炉渣、锰矿洗炉。
降低炉渣碱度,改变原料配比,调整炉渣成分。
⑤减少喷吹量,提高焦比,既避免热补偿不足,又改善料柱透气性。
⑥适当减小冷却强度。
加强冷却设备的检查,防止冷却水漏入炉内。
⑦保持炉缸热量充沛,风、渣口烧坏较多时,可增加出铁次数、临时堵塞烧坏次数较多的风口。
渣口严重带铁时,出铁后应打开渣口喷吹,连续烧坏应暂停放渣。
⑧若因护炉引起,应视炉缸水温差的降低,减少含钛炉料的用量,改善渣铁流动性。
⑨处理炉缸中心堆积,上部调整装料顺序和批重,以减轻中心部位的矿石分布量。
⑩若因长期边重,引起炉缸边缘堆积,上部调整装料,适当疏松边缘。
另外,在保持中心气流畅通的情况下,适当扩大风口面积。
8.炉冷
炉冷是指炉缸热量严重不足,不能正常送风,渣铁流动性不好,可能导致出格铁、大灌渣、悬料、结厚、炉缸冻结等恶性事故。
◆炉冷发生的原因:
(1)冷却设备大量漏水未及时发现和处理,停风时炉顶打开水未关。
(2)缺乏准备的长期停风之后的送风。
(3)长时间计量和装料错误,使实际焦炭负荷或综合负荷过重,或煤气利用严重恶化,未能及时纠正。
(4)连续塌料或严重管道行程,未得到及时制止。
(5)长期低料线作业,处理不当。
(6)边缘气流过分发展、炉瘤、渣皮脱落以及人为操作错误等。
◆初期向凉征兆:
(1)风口向凉。
(2)风压逐渐降低,风量自动升高。
(3)在不增加风量的情况下,下料速度自动加快。
(4)炉渣变黑,渣中FeO含量升高,炉渣温度降低。
(5)容易接受提温措施。
(6)顶温、炉喉温度降低。
(7)压差降低,透气性指数提高,下部静压力降低。
(8)生铁含硅降低,含硫升高,铁水温度不足。
◆严重炉冷征兆:
(1)风压、风量不稳,两曲线向相反方向剧烈波动。
(2)炉料难行,有停滞塌陷现象。
(3)顶压波动,悬料后顶压下降。
(4)下部压差由低变高,下部静压力变低,上部压差下降。
(5)风口发红,出现生料,有涌渣、挂渣现象。
(6)炉渣变黑,渣铁温度急剧下降,生铁含硫升高。
(1)必须抓住初期征兆,及时增加燃料喷吹量,提高风温,必要时减少风量,控制料速,使料速与风量相适应。
(2)要及时检查炉冷的原因,如果炉冷因素是长期性的,应减轻焦炭负荷。
(3)严重炉凉且风口涌渣时,风量应减少到风口不灌渣的最低程度。
为防止提温造成悬料,可临时改为按风压操作,保持顺行。
(4)炉冷时除采取减少风量、提高风温、增加燃料喷吹量等提温的措施外,上部应加入净焦和减轻焦炭负荷。
(5)组织好炉前工作。
当风口涌渣时,及时排放渣铁,防止自动灌渣,烧坏风口。
(6)严重炉冷且风口涌渣,又已悬料时,只有在出渣出铁后才允许坐料。
放风时,当个别风口进渣时,可加风吹回(不宜过多)并立即往吹管打水,不急于放风,防止大灌渣。
(7)若高炉只是一侧炉凉时,首先应检查冷却设备是否漏水发现漏水后及时切断漏水水源。
若不是漏水造成的经常性偏炉凉,应将此部位的风口直径缩小。
9.炉缸冻结
由于炉温大幅度下降导致渣铁不能从铁口自动流出时,就表明炉缸已处于冻结状态。
◆炉缸冻结的原因:
(1)高炉长时间连续塌料、悬料、发生管道且未能有效制止。
(2)由于外围影响造成长期低料线。
(3)上料系统称量有误差或装料有误,造成焦炭负荷过重。
(4)冷却器损坏大量漏水流入炉内,没有及时发现和处理。
(5)无计划的突然长期休风。
(6)装料制度有误,导致煤气利用严重恶化,没有及时发现和处理。
(7)炉凉时处理失当。
◆炉缸冻结的处理:
(1)果断采取加净焦的措施,并大幅度减轻焦炭负荷,净焦数量和随后的轻料可参照新开炉的填充料来确定。
炉子冻结严重时,集中加焦量应比新开炉多些,冻结轻时则少些。
同时应停煤、停氧把风温用到炉况能接受的最高水平。
(2)堵死其他方位风口,仅用铁口上方少数风口送风,用氧气或氧枪加热铁15,尽力争取从铁口排出渣铁。
铁口角度要尽量减小,烧氧气时,角度也应尽量减小。
(3)尽量避免风口灌渣及烧出情况发生,杜绝临时紧急休风,尽力增加出铁次数,千方百计及时排净渣铁。
(4)加强冷却设备检查,坚决杜绝向炉内漏水。
(5)如铁口不能出铁说明冻结比较严重,应及早休风准备用渣口出铁、保持渣口上方两个风口送风,其余全部堵死。
送风前渣口小套、三套取下,并将渣口与风口间用氧气烧通,并见到红焦炭。
烧通后将用炭砖加工成外形和渣口三套一样、内径和渣口小套内径相当的砖套装于渣口三套位置,外面用钢板固结在大套上。
送风后风压不大于0.03MPa,堵铁口时减风到底或休风。
(6)如渣口也出不来铁,说明炉缸冻结相当严重,可转入风口出铁,即用渣口上方两个风口,一个送风,一个出铁,其余全部堵死。
休风期间将两个风口问烧通,并将备用出铁的风口和二套取出,内部用耐火砖砌筑,深度与二套齐,大套表面也砌筑耐火砖,并用炮泥和沟泥捣固并烘干,外表面用钢板固结在大套上。
出铁的风口与平台间安装临时出铁沟,并与渣沟相连,准备流铁。
送风后风压不大于0.03MPa,处理铁口时尽量用钢钎打开,堵口时要低压至零或休风,尽量增加出铁次数,及时出净渣铁。
(7)采用风口出铁次数不能太多,防止烧损大套。
风口出铁顺利以后,迅速转为备用渣口出铁,渣口出铁次数也不能太多,砖套烧损应及时更换,防止烧坏渣口二套和大套。
渣口出铁正常后,逐渐向铁口方向开风口,开风口速度与出铁能力相适应,不能操之过急,造成风口灌渣。
开风口过程要进行烧铁口,铁口出铁后问题得到基本解决,之后再逐渐开风口直至正常。
10.炉墙结厚
炉墙结厚分为上部结厚和下部结厚。
上部结厚主要是由于对边缘管道行程处理不当,原燃料含钾、钠高或粉末多,低料线作业,炉内高温区上移且不稳定等因素造成的。
下部结厚多是炉温、炉渣碱度大幅波动,长期边缘气流不足,炉况长期失常,冷却强度过大,以及冷却设备漏水,长期堵风口等因素造成的。
11.连续崩料的征兆和处理方法
征兆
(1)料尺连续出现停滞和塌落现象
(2)风压风量不稳、剧烈波动,接受风量能力差。
(3)炉顶煤气压力出现尖峰,剧烈波动。
(4)风口工作不均,部分风口生降和涌渣现象,严重时自动灌渣。
炉温波动,严重时渣铁温度显著下降,放渣困难。
连续崩料会影响矿石的预热与还原,特别是高炉下部连续崩料,能使炉缸急剧向凉,必要时果断处理,处理方法是:
(1)立即减风到能够制止崩料的程度,使风压风量达到平稳。
(2)加入适当数量的净焦
(3)临时缩小料批,减轻焦炭负荷,适当发展边缘。
(4)出铁后彻底放风坐料,回风压力应低于放风前压力。
(5)只有炉况转为顺行,炉温回升是才能逐步恢复风量。