08级推动架课程设计说明书Word下载.docx
《08级推动架课程设计说明书Word下载.docx》由会员分享,可在线阅读,更多相关《08级推动架课程设计说明书Word下载.docx(16页珍藏版)》请在冰豆网上搜索。
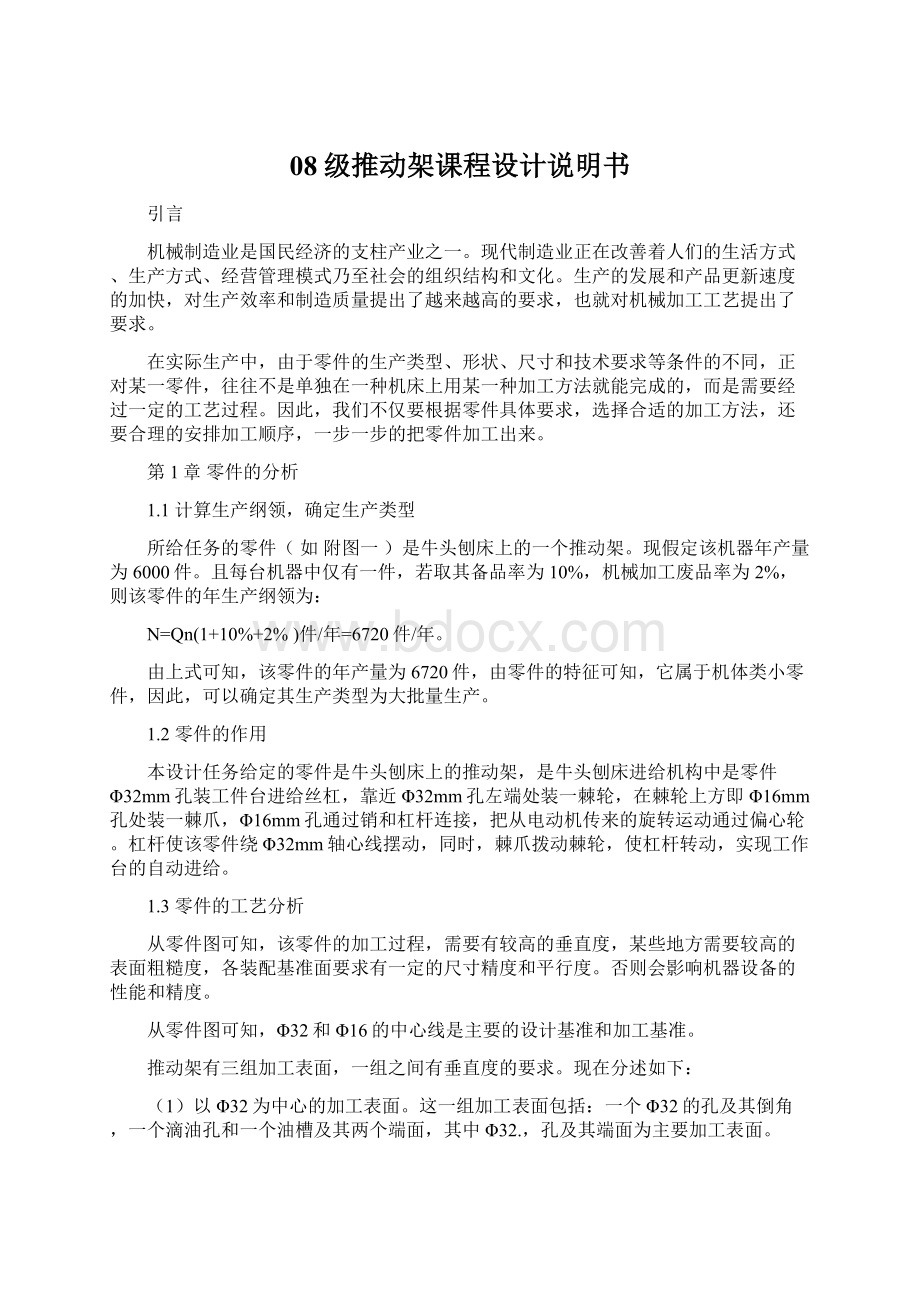
精基准主要应该考虑基准重合的问题。
当设计基准与工序基准不重合时,应进行尺寸换算,选择孔Φ32及其端面为精基准进行加工。
2.3零件加工方法的选择
本设计任务给的零件需要加工的表面有:
端面、内孔、圆角等,其加工方法如下:
(1)Φ32孔左端面:
是重要表面,有一定粗糙度要求,也是定位基准面,但由于零件构造为非规则回转体的原因,该端面不适合于车加工,故采用铣削方式进行加工,又根据其尺寸精度可知,左右两端面间尺寸公差等级为IT11,故每边只需一次铣削加工即可;
(2)Φ32孔右端面:
是重要表面,且零件结构条件适合于车削加工,但考虑该端面的加工可以和Φ16孔的右端面加工可以合并为一个工序,而Φ16的右端面加工只适合于铣削加工,故也采用铣削方式进行加工;
(3)Φ32孔:
是重要工作配合部分,其尺寸公差等级为IT7可通过钻孔、扩孔、铰孔达到要求;
(4)Φ16孔:
表面粗糙度为3.2为重要工作配合部分,其尺寸公差等级为IT7,故可通过钻孔、扩孔、铰孔,达到要求;
(5)Φ16孔两端面:
不是重要表面,表面粗糙度R25,只要铸造完对其粗加工即可;
(6)上端Φ10孔:
表面粗糙度为R12.5,尺寸精度不高,且不是重要工作配合部分,故只需一次钻孔加工即可;
(7)上端Φ16孔:
表面粗糙度R3.2,为重要工作配合部分,由于零件形状关系,考虑到不方便对其加工,故选择从下端用手铰的方式加工该孔;
(8)上端宽6深9.5的槽:
不是重要工作配合部分,粗糙度要求为R12.5,故用铣刀粗加工即可;
(9)Φ32孔内R3的油槽:
不是重要工作配合部分,通过一次拉削加工即可达到要求;
(10)Φ32孔上的滴油孔:
不是重要工作配合部分,通过一次钻削加工即可达到要求;
(11)最上端宽6的槽:
不是重要工作配合部分,通过一次铣削加工即可达到要求。
2.4制定机械加工工艺路线
由于是大批量生产,故加工工艺采用工序集中原则。
(1)工艺加工方案一:
工序1:
铸造毛坯,考虑到零件形状和经济性方面,采用砂型铸造;
工序2:
时效处理
工序3:
铣Φ50右端面,倒角45°
;
工序4:
铣Φ35右端面;
工序5:
铣Φ50和Φ35左端面,倒角45°
工序6:
铣Φ27圆拄上端面,倒角45°
工序7:
钻上端Φ10的孔;
工序8:
手铰Φ16孔;
工序9:
钻扩铰Φ32孔,倒角45°
工序10:
钻扩铰下端Φ16孔,倒角45°
工序11:
钻Φ10油孔,锪120°
的倒角;
工序12:
钻M8螺纹孔,攻丝M8-6H;
工序13:
拉R3的油沟;
工序14:
铣深9.5宽6mm的槽;
工序15:
终检;
工序16:
入库。
(2)工艺加工方案二:
钻、扩、铰Φ16孔;
铣深9.5宽6mm的槽;
(3)工艺加工方案三:
工序2:
时效处理;
铣Φ50的右端面,倒角45°
铣Φ35的右端面,倒角45°
铣Φ32孔和Φ16孔在同一基准的两个端面;
车Φ10孔和Φ16的基准面;
钻Φ10和钻、半精铰、精铰Φ16孔,倒角45°
钻、扩、铰Φ32孔,倒角45°
钻螺纹孔Φ6的孔,攻丝M8-6H;
钻Φ10的孔,锪120°
入库;
(3)工艺方案的比较与分析。
上述三个工艺方案的特点在于:
都是按先加工面再加工孔的原则进行加工的。
方案一和方案三是先加工上端Φ10的孔和手铰Φ16孔,然后以孔的中心线为基准距离12mm钻扩铰Φ32孔,而方案二则与此相反,先钻扩铰Φ32孔,然后以孔的中心线为基准距离12mm钻φ10mm和手铰Φ16孔,两相比较可以看出,先加工φ32mm的孔,以孔作为基准加工φ10mm和φ16mm的孔,这时的垂直度容易保证,并且定位和装夹都很方便。
并且方案二加工孔是在同一铣床上加工的。
避免了不必要的搬动及装假,节约了工时,提高了生产效率。
因此,选用方案二是比较合理的。
2.5工艺方案的经济技术比较
本零件为大批量生产的中小型零件推动架,根据《机械加工工艺手册》可知采用湿型砂型铸造,有不用烘干、粉尘少、可用机器造型、容易实现机械化自动化、采用膨润土活化砂及高压造型、可以得到强度高透气性较好的铸件的特点。
该零件主要涉及几个孔和面的加工工艺,由于工件的结构较复杂,用车床或刨床加工的话会给加工带来很大的困难,给工人增加很大的工作难度,如果用镗床来镗孔,也是可以的,但考虑到经济性原则,在加工时我们尽量选用了普通钻床进行加工,也可以达到指定的要求。
2.6加工设备和工艺装备的选择
2.6.1机床的选择
(a)工序2,3,4,5,6,7,是铣平面工序,用的是X62W型万能卧铣床;
(b)工序8,9,10,11,12,13,是孔加工工序,选用Z535型立式钻床;
(c)工序14,是拉削加工,用L515A立式内拉床加工。
2.6.2选择夹具
本零件结构比较简单,故加紧定位方案比较简单,可采用典型夹具进行加紧,可采用一面两孔定位方案,用个活动V型块代替另一个孔进行定位。
2.6.3选择刀具
(1)在工序2,3,4,5,6,7,铣平面时,铣刀可以选择直齿或错齿的端铣刀和周铣刀;
(2)钻孔有Φ32,Φ16,Φ10三种孔,需要留一定的加工余量,Φ32孔可用Φ18,Φ30麻花钻钻加工,Φ16孔可用Φ14麻花钻钻加工,Φ10孔可用Φ10麻花钻钻加工;
(3)对于工序8,9,对Φ16和Φ32的孔要用机用高速钢机用铰刀及直柄扩孔钻进行加工;
(4)对于工序11,可用套式手铰刀进行铰孔;
(5)对于工序13,拉沟槽,用专用拉刀。
(6)对于工序3,5,有倒角的加工,可选用CA6140进行加工。
(7)钻螺纹孔Φ6mm,攻丝M8-H6用锥柄阶梯麻花钻,机用丝锥。
2.6.4选择量具
(a)由零件图上看,各平面的相互位置要求不是非常严格,其最小不确定度为0.027mm,选用分度值为0.001mm,测量范围为0-150mm的游标卡尺就行了,因为其不确度为0.002mm,显然满足要求。
(b)选择内孔的量具:
此零件对孔的精度要求较高,其中例如Φ16孔的下偏差要求在0.029之内,故可选用分度值为0.001mm,测量范围为0-150mm的内径千分尺,,满足测量精度的要求。
工序
加工尺寸
尺寸公差
使用量具
1
45mm
0.17mm
分度值为0.02mm,测量范围为0-150mm的游标卡尺
2
20mm
---
3
Φ32mm
0.027mm
分度值为0.001mm,测量范围为0-150mm的内径千分尺
Φ16mm
0.029mm
Φ10mm
0.1mm
注:
本零件要求测量的尺寸并不是很复杂,故只要这两种量具就足够了。
2.7机械加工余量、工序尺寸和公差及切削用量的确定
2.7.1“推动架”零件材料为HT200,生产类型为大量生产,采用铸造生产毛坯。
根据上述原始资料及加工工艺,分别确定各加工表面的机械加工余量、工序尺寸及毛坯尺寸如下:
砂型机械造型及壳型的尺寸公差等级为8~10;
根据《机械加工工艺手册》,查表《3.1-26铸铁件机械加工余量》,加工余量为5.0mm.
工序间加工余量的计算:
(1)Φ50外圆表面的长度,考虑加工长度为45mm,表面粗糙度要求为R6.3
只需进行左右两端面粗铣即可。
现根据《机械加工工艺手册》取加工余量为1.0mm,即2Z=2.0mm,厚度偏差为-0.25~--0.39mm;
(2)Φ35外圆表面的长度,考虑加工长度为20mm,表面粗糙度要求为R25
现根据《机械加工工艺手册》取加工余量为1.0mm,即2Z=2.0,毛坯长度为22mm,厚度偏差为-0.21~-0.33mm;
(3)Φ27圆拄上端面,Φ27外圆表面的长度,考虑加工长度约为43mm,表面粗糙度要求为R6。
只需进行上端面粗铣即可。
现根据《机械加工工艺手册》取加工余量为1.0mm;
厚度偏差为-0.25~-0.39mm
(4)Φ32孔
毛坯为实心,不铸出孔,Φ32孔的精度要求界与IT7-IT8之间,参照《工艺手册》表2.3-9及表2.3-12确定加工余量为
第一次钻孔:
Φ15mm2Z=17mm
第二次钻孔Φ30mm2Z=2mm
扩孔:
Φ31.75mm2Z=0.25mm
铰孔:
Φ32mm2Z=0.027mm
(5)下端Φ16孔
毛坯为实心,不铸出孔,Φ16孔的精度要求界与IT7-IT8之间,参照《工艺手册》表2.3-9及表2.3-12确定加工余量为
钻孔:
Φ15mm2Z=1mm
Φ15.85mm2Z=0.15mm
Φ16mm2Z=0.033mm
(6)Φ10孔
毛坯为实心,不铸出孔,Φ10孔的精度要求界与IT10-IT11之间,参照《工艺手册》表2.3-9及表2.3-12确定加工余量为
Φ9.8mm2Z=0.2mm
2.7.2确定工序9的切削用量
钻上端Φ10孔
(1)钻孔Φ10。
确定进给量f,根据《切削手册》表2.7,d=Φ10时,f=0.10~0.28mm/r,由于l/d=13/10=1.3,修正系数kf=1,则
f=(0.10~0.28)*1=0.10~0.28mm/r
根据Z535机床说明书,现取f=0.15。
切削速度:
根据《切削手册》表2.13及表2.14,查得切削速度在10~14m/min.现取12m/min
所以ns=1000vc/πdw=325.6(r/min)
根据机床说明书,取ns=275r/min,故实际切削速度的为
Vc=11.48m/min
2.8机械加工工艺过程综合卡
长沙大学
机电工程系
机械加工
工艺过程卡片
产品型号
零件图号
共1页
产品名称
推动架
零件名称
第1页
材料牌号
HT200
毛坯种类
铸件
毛坯外形尺寸
每毛坯件数
1
每份件数
备注
工序号
名称
工序内容
设备
工艺设备
(夹具,刀具)
工时
准终
单件
铸造
采用砂型铸造
2
热处理
铣Φ50尺寸右端面
铣右端面至50
X62W型万能卧铣床
直齿端铣刀
4
倒角
CA6140
硬质合金弯头刀
5
铣Φ35尺寸右端面
铣右端面至25
6
铣Φ50尺寸左端面
铣左端面至45
7
8
铣Φ35尺寸左端面
铣左端面至20
9
铣宽6深9.5槽
在Ф27端铣出深度为9.5,宽度为6的槽
10
直齿周铣刀
11
铣Φ27圆拄上端面
铣上端面至40
12
13
钻、扩、铰Ф32
钻孔至Ф30,扩孔至Ф31.75,铰孔至Ф32
Z535
莫氏锥柄麻花钻直柄扩孔钻高速钢机用铰刀内径千分尺
14
15
钻、扩、铰Ф16
钻孔至Ф14,扩孔至Ф15.75,铰孔至Ф16
Z525
16
17
钻Φ10的孔
钻孔至10
高速钢麻花钻、细柄机用丝锥游标卡尺、螺纹塞规
18
扩、铰Φ16的孔
扩、铰至Φ16
套式手铰刀、细柄机用丝锥游标卡尺
19
钻M8螺纹孔及铰螺纹
钻孔至Ф6.5mm,攻螺纹至M8-6H钻孔至Φ10
20
钻Φ10的油孔孔,锪120°
的倒角
钻孔至10,锪120°
21
铣槽
22
去毛刺
平锉
23
清洗
清洗机
24
终检
塞规百分表卡尺
2.9工序9的机械加工工序卡
工序卡片
产品名称及型号
工序名称
第页
牛头刨床
钻孔
共页
车间
工段
材料名称
力学性能
灰口铸铁
200
同时加工件数
每料件数
技术等级
单位时间/min
准备—终结时间/min
设备名称
设备编号
夹具名称
夹具编号
工作液
钻床
Z535
专用夹具
更改内容
工步号
工步内容
计算数据/mm
切削用量
工作定额/min
刀具量具及辅助工具
直径或长度
进给长度
单边余量
背吃刀量/mm
进给量/(mm./r或/mm./min)
切削速度/(r/min或双行程数/n/min)
切削速度/(m/min)
基本时间
辅助时间
工作地点服务时间
规格
编号
数量
Φ=14
mm
0.72
高速麻花钻
编制
陈辉
抄写
校对
审核
批准
第3章夹具设计
为了提高提高劳动生产效率,保证加工质量,降低劳动强度,需要专门设计专用夹具。
经过选择和比较,决定设计第9道工序——钻Φ10孔的钻床夹具。
本夹具将用于Z535立式机床。
刀具为高速钢麻花钻。
3.1提出问题
本夹具主要用来钻Φ10的孔,这个孔有一定的技术要求。
但加工本道工序时,Φ10mm孔尚未加工,本工序加工时要考虑如何提高劳动生产效率,降低劳动强度。
3.2夹具的设计
3.2.1定位基准的选择。
由零件图可知,可考虑采用类似与一面两孔的定位方案来进行定位。
用一个心轴和棱形销定位。
3.2.2切削力及夹紧力的计算。
刀具:
高速钢麻花钻,钻刀直径为Φ10,
(查《切削手册》)得:
其中CF=420ZF=1.0YF=0.8
KF=1.33do=14mmf=0.72mm/r
(查《切削手册》和《机械制造工艺学》)
则 F=420×
10×
0.720.8 ×
1..33=4022N
安全系数:
K=
式中:
——基本安全系数,1.5;
——加工性质系数,1.1;
——刀具钝化系数,1.1;
——断续切削系数,1.1。
在计算切削力时必须考虑安全系数,查相关手册可得安全系数为
K=1.3×
1.1×
1.1=1.73
所以力F=1.73×
4022=6958N
其应力为F/(3.14×
R2)=6958/3.14×
52
=87﹤200(铸铁强度为200)
转矩:
M=9.81CFdoXMfyM KM
=9.81×
0.021×
142×
0.20.8×
0.94
=15.8N.m
强度够了。
3.2.3定位误差的分析
钻孔的垂直度由钻套来保证。
孔的轴线的误差由一面和心轴加和棱形销定位来保证。
3.2.4钻套的设计钻(d=10mm)
假定该元件大批量生产,有资料1表9-1查得,应选用快换钻套(JB/T8045.2-1999),该钻套1装在衬套2中,而衬套则是压配在夹具体或钻模3中。
钻套由螺钉4固定,以防止它转动。
钻套与衬套间采用F7/m6或F7/k6配合。
便于钻套磨损后,可以迅速更换。
适于大批量生产。
钻套高度H=(1~2.5)10=(1~2.5)*10=(10~25)mm取其值为15mm
钻套位置尺寸L以工件平均尺寸为基准尺寸,取公差取工件相应公差的(1/5~1/2),偏差对称标注。
Lg=(20±
0.1)mm,L=20mm,
3.2.5夹具的设计及操作的简要说明,如前所述,为了提高劳动生产率,应首先招眼于机动夹,本道工序的钻床夹具就选择了活动V形块进行夹紧。
钻床夹具的装配图及夹具具体的零件图分别见附图。
结论
1设计出、了牛头刨床零件-推动架,加工第9道工序加工的专用夹具。
该机器年产量为6000件。
且每台机器中仅有一件,若取其备品率为10%,机械加工废品率为2%。
2、采用心轴和棱形销为定位元件,螺纹夹紧机构夹紧。
3、在这套方案中夹具的设计,能较好的满足零件加工的效率、形位公差以及经济性。
该夹具是一个结构简单,易于制造的专用夹具,能利用简单、典型的定位原理实现工件的定位、完成该工序的加工任务。
课程设计心得
又一次将理论与实际结合的课程设计。
在两周的时间里,我们从零件加工工艺到最后的夹具设计及成型遇到了很多的困难。
通过反复查找资料、和同学一起讨论、老师的指教,这加深巩固了我们所学的知识,让我们得到了锻炼。
我在这次的夹具课程设计中的任务是设计推动架Ф10的孔,想过多种定位方式,最终确定采用心轴和棱形销定位。
确定了夹具的原理,但各种零件要如何配合,通过查找各种资料才找出合理的方案。
夹具结构设计确定好了,但CAD和PROE又有难题了,CAD很久没用了相当不熟练,而PROE我们到目前还没学过。
所以还要自学一点简单的PROE的操作。
在设计过程中,我们还要用到之前学过的很多知识,例如《画法几何》,《互换性》,《机械制造装备》等。
能顺利完成这次课程设计,要感谢老师的指导和同学的帮助。
参考文献
[1]邹青主编.机械制造技术基础课程设计指导教程[M].北京:
机械工业出版社,2005
[2]艾兴,肖诗纲主编.切削用量简明手册[M].北京:
机械工业出版社,1994
[3]李洪主编.机械加工工艺手册[M].北京:
北京出版社,1990
[4]朱冬梅,胥北澜主编.画法几何及机械制图[M].北京:
高等教育出版社,2000
[5]王先逵主编.机械制造工艺学[M].北京:
机械工业出版社,2006
[6]李益民主编.机械制造工艺设计简明手册[M].北京:
机械工业出版社,1999
[7]张学政,李家枢主编.金属工艺学实习教材[M].北京:
高等教育出版社,2003
[8]王小华主编.机床夹具图册[M].北京:
机械工业出