模具课程设计说明书Word格式.docx
《模具课程设计说明书Word格式.docx》由会员分享,可在线阅读,更多相关《模具课程设计说明书Word格式.docx(24页珍藏版)》请在冰豆网上搜索。
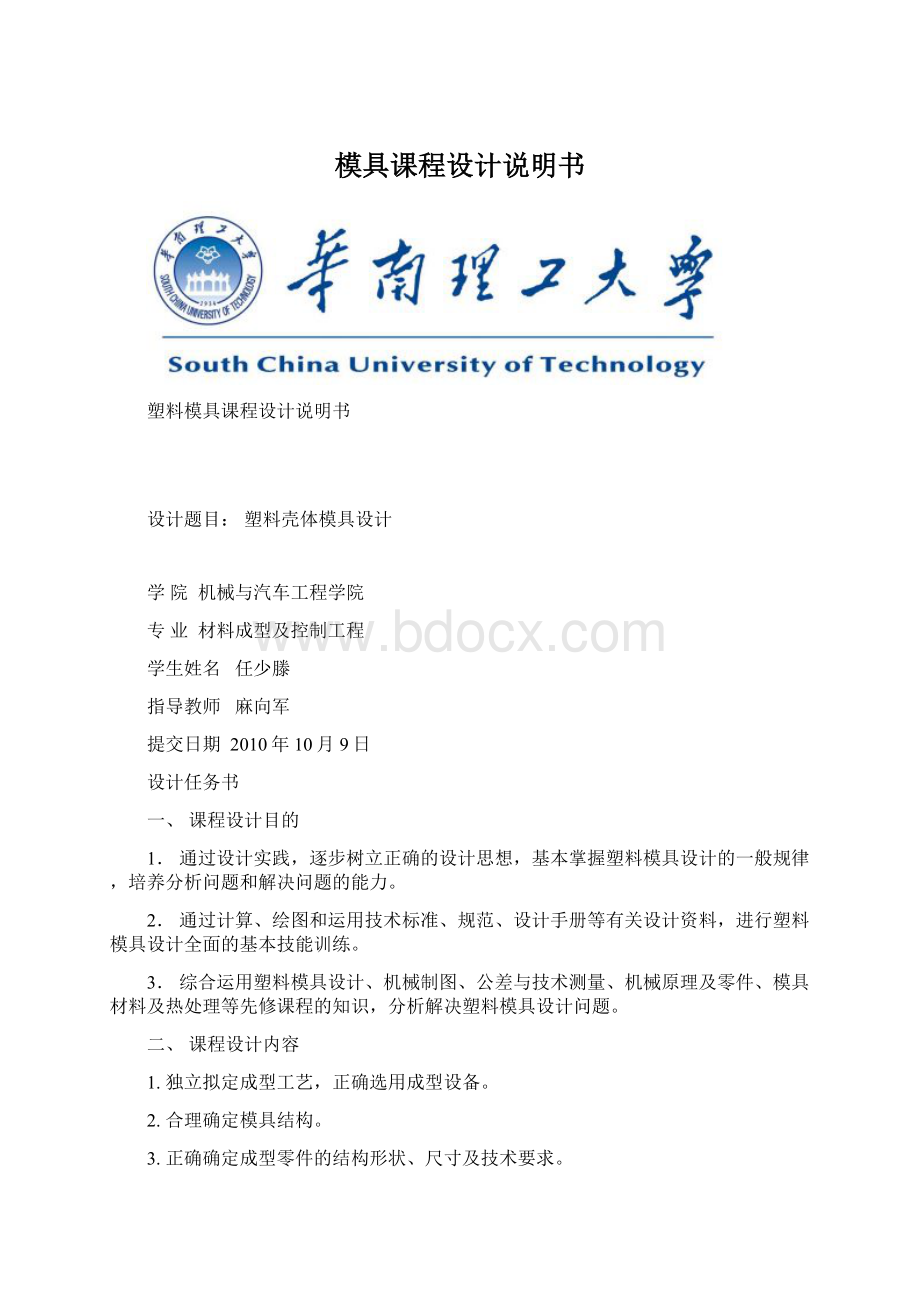
1.定模座板17
2.定模板尺寸17
3.推件板尺寸17
4.垫块的尺寸18
5.动模座板18
6.推板18
7.推杆固定板18
六、合模导向机构的设计18
1.导向机构的整体设计18
2.导柱设计19
七、脱模推出机构的设计19
1.脱模推出机构的设计原则19
2.塑件的推出基本方式20
3.塑件的推出机构20
4.脱模力的校核21
八、排气系统的设计21
九、温度调节系统的设计21
1.加热系统21
2.冷却系统21
十、心得总结23
参考文献23
一、塑件成型工艺性分析
1.塑件结构特征分析
本次课程设计要求对塑料壳体的模具进行设计,该塑料壳体的二维工程图如图1、图2所示:
图1塑件图
图2塑件图
塑料壳体的塑件图如上所述。
从工件本身来看,属于小型件,不需要侧向抽芯,脱模抽芯机构简单,抽拔距离短,由于塑件本身有斜面,容易脱模。
2.塑件成型工艺性分析
1)精度等级
影响塑件精度的因素很多,塑料的收缩、注塑成型条件(时间、压力、温度)等,塑件形状、模具结构(浇口、分型面的选择),飞边、斜度、模具的磨损等都直接影响制品的精度。
本塑件所用材料为低密度聚乙烯(LDPE),由此查塑料模具设计手册可知,本塑件宜选用一般精度6级。
2)脱模斜度
由于塑件冷却后产生收缩,会紧紧地包住模具型芯、型腔中凸出的部分,使塑件脱出困难,强行取出会导致塑件表面擦伤、拉毛。
为了方便脱模,塑件设计时必须考虑与脱模(及轴芯)方向平行的内、外表面,设计足够的脱模斜度。
只有塑件高度不大、没有特殊狭窄细小部位时,才可以不设计斜度。
最小脱模斜度与塑料性能、收缩率、塑件的几何形状等因素有关。
塑件脱模斜度为:
30'—1º
3.塑件材料及工艺参数
1)塑件材料
塑件采用的材料是LDPE,名称Low-densitypolyethylene,全称低密度聚乙烯,是高压下乙烯自由基聚合而获得的热塑性塑料。
2)使用性能
a)LDPE塑料的优点:
其结晶度(55%~65%)和软化点(90~100℃)较低;
有良好的柔软性、延伸性、透明性、耐寒性和加工性;
其化学稳定性较好,可耐酸、碱和盐类水溶液;
有良好的电绝缘性和透气性;
吸水性低;
易燃烧。
性质较柔软,具有良好的延伸性、电绝缘性、化学稳定性、加工性能和耐低温性(可耐-70℃)。
b)LDPE塑料的缺点:
其机械强度、隔湿性、隔气性和耐溶剂性较差。
分子结构不够规整,结晶度(55%-65%)低,结晶熔点(108-126℃)也较低。
其力学强度低于高密度聚乙烯,防渗系数、耐热性和抗日光老化性差,在日光或高温下易老化分解而变色,导致性能下降,所以低密度聚乙烯在制成塑料卷材时添加了抗氧化剂和紫外线吸收剂来改善其不足之处。
3)成型性能
a)由于聚乙烯是结晶聚合物,其熔融时结晶晶核还需要吸收一部分热量,故所选哟呵能够的机筒温度通常高压熔点数十度。
b)模具的温度对制品的结晶状况有较大的影响,温度高、熔体冷却速率慢,制品的结晶度便高,制品强度高,但是制品的收缩率会随着温度的增高而增大,易产生内应力及变形,因此低密度聚乙烯模具温度设为30~45度。
c)注塑压力选取主要是考虑流动状况,一般情况聚乙烯在熔融状态下具有较好的流动性,因此选择低的注射压力为60~80MPa,料筒温度为140~300,成型收缩率为1.5%,射出压力为300~1000kgf/cm2。
表1.LDPE加工工艺参数
工艺
预热和干燥
料筒温度
模具温度
注射压力
成型周期
参数
一般不需要
后段:
140~160℃
中段:
165~180℃
前段:
170~200℃
30~60℃
55~170bar
30~130s
二、拟定模具结构形式
1.分型面位置分析和确定
塑件设计阶段,就应考虑成型时分型面的形状和位置,否则无法用模具成型。
在模具设计阶段,应首先确定分型面的位置,然后才选择模具的结构。
分型面设计是否合理,对塑件质量、工艺操作难易程度和模具的设计制造都有很大影响。
因此,分型面的选择是注射模设计中的一个关键因素。
分型面的设计过程中,除了要注意必须将其开设在制件断面轮廓最大的地方外,还应当注意以下几点:
a)因为分型面处不可避免的会在塑件上留下溢料的痕迹,或拼合不准确的痕迹,故分型面最好不选在制品光亮平滑的外表面或带圆弧的转角处。
b)从制件的推出装置设置方便考虑,分型时要尽可能的使制件留在动模边。
c)从保证制件相关部位的同心度出发,同心度要求高的塑件,取分型面时最好把要求同心的部分放在模具分型面的同一侧。
d)有侧凹或侧孔的制件,当采用自动侧向分型抽芯时,除了液压抽芯能获得较大的侧向抽拔距离外,一般分型抽芯机构侧向抽拔距离都较小。
e)有利于保证塑件的精度要求。
f)有利于模具的加工,特别是型腔的加工。
g)有利于浇注系统、排气系统、冷却系统的设计。
h)尽量减少塑件在合模平面上的投影面积,以减少所需的锁模力。
i)便于嵌件的安装。
j)长型芯应置于开模方向。
考虑以上因素,本次课程设计的分型面选择如图3所示:
图3分型面
2.塑件型腔数量和排列方式的确定
1)塑件型腔数量的确定
为了制模具与注塑机的生产能力相匹配,提高生产效率和经济性,并保证塑件精度,模具设计时应确定型腔数目。
型腔数目的确定一般可以根据经济性、注射机的额定锁模力、注射机的最大注射量、制品的精度等。
一般来说,大中型塑件和精度要求高的小型塑件优先采用一模一腔的结构,但对于精度要求不高的小型塑件(没有配合精度要求),形状简单,又是大批量生产时,若采用多型腔模具可提供独特的优越条件,使生产效率大为提高。
该塑件精度要求较高,且尺寸较大,故选用一模一腔的模具形式。
2)型腔排列方式的确定
由于采用了一模一腔的形式,故型腔的设计主要是对一个型腔排列的设计,因此考虑将模具的型腔放置在模具的中心位置。
3)模具结构形式的确定
由以上分析可知,本模具采用一腔一模,推件板推出,只有主流道,定模和动模都不需要设置侧向分型机构。
动模部分需要一块型芯固定板和支撑
板,因此基本上可以确定模具结构形式为A型带推件板的单分型面注射模。
3.注塑机型号的确定
1)注射量计算
通过计算塑件的体积可得V1=92.70cm3。
流道凝料的体积
还是个未知数,故可根据经验公式,即可按塑件体积的0.6倍来估算。
从上述分析中确定为一模一腔,所以注射量为
m=1.6nm=1.6×
1×
92.70=148.30cm3
2)塑件在分型面上投影面积和锁模力计算
流道凝料(包括浇口)在分型面上的投影面积A2,在模具设计前是个未知数,根据多型腔模的统计分析,A2是每个塑件在分型面上的投影面积
的0.2~1倍,A2是每个塑件在分型面上的投影面积
的0.2~0.5倍,因此可用0.35n
来进行估算,所以
A=n
+
=n
+0.35n
=194.022cm2
式中
=80×
100-2×
3.14
8^2=14372mm2
因此
=194.022*25=485KN
3)选择注塑机型号
根据上面计算得到的m和Fm值来选择一种注射机,注射机的最大注射量G和额定锁模力F应满足
G≥m/α
α——注射系数,结晶型塑料取0.75。
F≥Fm
由此选择SZ—200/100卧式注射机,其参数见下表:
表2.注射机主要技术参数
理论注射容量/cm3
210
锁模力/kN
800
螺杆直径/mm
42
拉杆内向距/mm
370×
320
注射压力/MPa
150
移模行程/mm
300
注射速率/(g/s)
110
最大模厚/mm
350
塑化能力/(g/s)
14
最小模厚/mm
螺杆转速/(r/min)
10~250
定位孔直径/mm
125
喷嘴球半径/mm
15
喷嘴尺寸/mm
4
4.工艺参数的校核
1)模具型腔数的校核
a)由注射机料筒塑化速率校核模具的型腔数n
=(0.8×
14×
30-0.6×
92.70)/92.70=3.02≥1
式中k—注射机最大注射量的利用系数,一般取0.8
M—注射机的额定塑化量(14g/s)
t—成型周期,取30s
型腔数校核合格。
b)由注射机的最大锁模力确定型腔数量n
n≤(F-p型A2)/p型A1=F/(p型A1)-0.35=2.43>1
2)注射工艺参数校核
a)注射压力的校核
=1.3×
100=130MPa<150MPa
式中
—取1.3
—取100MPa
故校核后得出注射压力合格。
b)锁模力的校核
=1.2×
194.0×
25=582KN<1000KN
故校核后得出锁模力合格。
3)安装尺寸校核
a)最大与最小工艺模具厚度校核
模具厚度H应满足Hmin﹤H﹤Hmax
式中Hmin=150mm,Hmax=350mm,而选中的模具厚度H=258mm,符合要求。
b)开模行程校核
开模行程H≥H1+H2+(5-10)mm
其值为H≥60+60+10=130mm,代值计算,符合要求。
c)拉杆内间距校核
该套模具模架的外形尺寸为250mm×
315mm,而注射机拉杆内间距为370mm×
320mm,符合要求。
三、浇注系统设计
1.流道的设计
主流道通常位于模具中心塑料熔体的入口处,它将注射机喷嘴射出的熔体导入分流道或型腔中。
主流道的形状为圆锥形,以便于熔体的流动和开模时主流道凝料的顺利拔出。
1)主流道设计要点
a)为便于将凝料从主流道中拉出,主流道通常设计成锥形,其锥角α=2°
~6°
。
内壁表面粗糙度一般为Ra=0.8。
b)为防止主流道与喷嘴处溢料及便于将主流道凝料拉出,主流道与喷嘴应紧密对接,主流道进口处应制成球面凹坑,其球面半径为R2=R1+(1~2)mm,凹入深度3~5mm。
c)为了物料的流动阻力,主流道末端与分流道连接处呈圆角过渡,其圆角半径r=1~3mm。
d)主流道长度L应尽量短,否则将增加主流道凝料,增大压力损失,一般主流道长度由模具结构和模板厚度所确定,一般不大于60mm,取L=37.1mm。
e)因主流道与塑料熔体反复接触,进口处与喷嘴反复碰撞,因此,常将主流道设计成可拆卸的主流道衬套,用较好的钢材制造并进行热处理,一般选用T8A、T10A制造,热处理硬度为HRC53~57。
2)主流道尺寸
a)根据所选注射机,则主流道小端尺寸为
d=注射机喷嘴尺寸+(0.5~1)=4.5mm
b)主流道球面半径
SR=注射机喷嘴球头半径+(1~2)=15+2=17mm
c)主流道长度
尽量小于60mm,取L为37.1mm
d)主流道大端直径
D=d+2Ltanα=6.44mm(半锥角α为2~4度)
3)主流道衬套的形式
主流道小端入口处与注射机喷嘴反复接触,属易损件,对材料要求较严,常用碳素工具钢,如T8A、T10A等,热处理硬度为50HRC~55HRC,由于主流道较短,故选用整体式,如图4所示:
图4浇口套
4)主流道凝料体积
=37.1π×
(6.442+4.5×
6.44+4.52)/12=0.881cm3
5)主流道剪切速率校核
由经验公式γz=3.3q/(πRS3)=(3.3×
46.35)/(3.14×
0.27353)=2831s-1,
在5×
102/s与5×
103/s之间,剪切速率合格。
由于是一模一腔的模具设计,故可以不用设计分流道。
2.浇口的设计
1)浇口介绍
浇口也称进料口,是连接流道与型腔之间的一段细短通道,除直接浇口外,它是浇注系统中截面尺寸最小的部分,但却是浇注系统的关键部分。
浇口的形状、位置和尺寸对塑件的质量影响很大。
浇口的作用是使从流道来的熔融塑料以较快的速度进入并充满型腔,型腔充满塑料以后浇口应按要求迅速冷却封闭,防止型腔内还未冷却的熔体回流。
浇口的设计与塑件的形状、截面尺寸、模具结构、注射工艺参数(压力等)及塑料性能等因素有关。
浇口的截面尺寸要小长度要短,这样才能增大料流速度,快速冷却封闭。
便于与塑件分离或切除,且浇口的痕迹不明显。
塑件的质量缺陷,如憋气、收缩、银丝、分解、波纹、变形等,往往都是由于浇口设计不合理造成的。
2)影响浇口设计的因素
浇口设计包括浇口截面形状及浇口截面尺寸的确定,浇口位置的选择。
影响浇口截面形状及其尺寸的因素,就塑件而言,包括塑件的形状、大小、壁厚、尺寸精度、外观质量及力学性能等。
塑件所用塑料特性对浇口设计的影响因素是塑料成型温度、流动性、收缩率及有无填充物等。
此外,在进行浇口设计时,还应考虑浇口的加工、脱模及清除浇口的难易程度。
3)浇口的选用
在之前的设计过程中已经预设了使用直接浇口。
直接浇口又叫中心浇口、主流道型浇口。
该浇口注塑压力和热量损失最小,具有很好的成型性,由于它的尺寸大,故固化时间长,延长了补料时间,使补缩效果很好,但由于补料时间长,在浇口附近容易产生残余内应力。
当采用这种浇口时,主流道浇口的根部不宜设计得太太粗,否则该处的温度高,容易产生缩孔,浇口截除后缩孔明显的留在制件表面上。
加工薄壁制品时,浇口根部的直径最多等于制件壁厚的两倍。
在浇口处要光滑的去除凝料也是比较困难的。
但它在单型腔中,塑料熔体直接流入型腔,因而压力损失小,进料速度很快,成型比较容易。
另外,它传递压力好,保压补缩作用强,模具结构简单紧凑,制造方便。
因此其适合各种塑料成型,尤其加工热敏性及高黏度材料,成型高质量的大型或深腔壳体、箱型塑件。
4)浇口位置的选择
模具设计时,浇口位置及尺寸要求比较严格,初步试模后还需进一步修改浇口尺寸,无论采用何种浇口,其开设位置对塑件成型性能及质量影响很大,因此合理选择浇口的开设位置是提高质量的重要环节,同时浇口位置的不同还影响模具结构。
总之要塑件具有良好的性能与外表,一定要认真考虑浇口位置的选择。
通常要考虑以下几项原则:
a)浇口应开设在塑件壁厚最大处,使熔体从厚壁流向薄壁,并保持浇口至型腔各处的流程基本一致。
b)避免浇口出产生喷射和蠕动,而在充填过程中产生波纹。
c)考虑分子的取向影响,浇口应设置在塑件的主要受力方向上,因为顺着流动方向的力学性能要高于其他方向。
特别是带填料的增强塑料,这种特性更加明显。
d)在选择浇口位置时应考虑到塑件尺寸的要求,因为塑料流经浇口充填型腔时,在流动方向与垂直于流动方向上的收缩率不尽相同,所以要考虑到变形和收缩的方向性。
e)须尽量减少熔接痕迹,应有利于型腔中气体的排出。
f)注意对外观质量的影响。
综合以上因素,由于本次的制品壁较厚,达到3—4mm,而且体积较大,用点浇口不太合适,因此用直接浇口。
且由LDPE的性能可知,其浇口的截面积应大一点好,防止熔接痕的产生。
浇口处的外观不好,后处理也有一定的麻烦。
由于是接近与正方形,为了使其容易充满,减少熔体在型腔内的阻力,且避免熔接痕的产生,浇口位置设置在制件即塑料盒的顶部的中心位置。
四、成型零件的设计
模具中确定塑件几何形状和尺寸精度的零件称为成型零件。
成型零件包括凹模。
型芯、镶件、成型杠和成型环等。
成型过程中成型零件受到塑料熔体的高压作用,料流的冲刷,脱模时与塑件间发生摩擦。
因此,成型零件要求有正确的几何形状、较高的尺寸精度和较低的表面粗糙度,此外还要求成型零件具有合理的结构和良好的加工工艺性,具有足够的强度、刚度和表面硬度。
在设计模具时,应根据塑件的尺寸精度等级确定模具成型模具成型零件的工作尺寸及精度等级。
影响塑件尺寸精度的因素相当复杂,这些因素因作为确定成型零件工作尺寸的依据。
影响塑件尺寸精度的主要因素有如下几个方面:
a)塑件收缩率所引起的尺寸误差。
塑件成型后的收缩率与塑料的品种,塑件的形状、尺寸、厚度、模具的结构,成型工艺条件等因素有关。
在模具设计时,要准确的确定收缩率是很困难的,因为成型后实际收缩率与计算收缩率是有差异的,生产中工艺条件变化,塑料批次的改变也造成塑件收缩率的波动,这些都会引起塑件尺寸的变化。
b)模具成型零件的制造误差。
模具成型零件的制造精度是影响塑件尺寸精度的重要因素之一。
成型零件加工精度愈低,成型塑件的尺寸精度也愈低。
c)模具成型零件的磨损。
模具在使用过程中,由于塑料熔体流动的冲刷、脱模时塑件的摩擦、成型过程中可能产生的腐蚀性气体的锈蚀以及由于上述原因造成的成型零件表面粗糙度提高而重新进行打磨抛光等,均会造成成型零件尺寸的变化。
磨损的结果使型腔尺寸变大,型芯尺寸变小。
d)模具安装配合的误差。
模具成型零件装配误差以及在成型过程中成型零件配合间隙的变化,都会引起塑件尺寸的变化。
一般情况下,收缩率的波动、模具制造公差和成型零件的磨损是影响塑件尺寸精度的主要原因。
而收缩率的波动引起的塑件尺寸误差随塑件尺寸的增大而增大。
因此生产大型零件时,若单靠提高模具制造精度等级来提高塑件精度是比较困难和不经济的,应稳定成型工艺条件和选择收缩率波动较的塑料。
生产小型塑件是,模具制造公差和成型零件的磨损是影响塑件尺寸精度的主要因素,因此,应提高模具精度等级和减少磨损。
设计成型零件是应根据塑料的特性和塑件的结构及精度要求,确定型腔的总体结构,选择分型面和浇口位置,确定脱模方式、排气部位和冷却水道的布置等,然后根据成型零件加工、热处理、装配等要求进行成型零件的结构设计,计算成型零件的工作尺寸,对重要的成型零件进行刚度和强度的校核。
1.成型零件的结构设计
1)凹模(型腔)
塑料壳体的外壁周围为长方体形状,外壁没有任何条纹且要求光滑,而且其尺寸较大(100×
150×
60mm),若采用整体式型腔,其机械加工方法并不困难,成本不会太高,且维修也不会太麻烦,故可采用整体式的设计。
如图5所示:
图5型腔
2)型芯
塑件厚度适中且比较均匀,高度不大,故可以依据其形状设置整体式型芯。
如图6所示:
图6型芯
3)成型零件钢材的选用
塑料壳体是大批量生产,成型零件所选用的钢材耐磨性和抗疲劳性能应该良好,机械加工性能和抛光性能也应良好。
因此构成型腔的嵌入式凹模钢材选用45号钢。
定模板构成外壁,成型时有料流的冲刷,但没有脱模时塑件的摩擦,因此采用45钢调质。
动模板的要求与定模板的要求相似,故也可采用动模板的材料进行加工。
2.成型零件工作尺寸的计算
塑件尺寸公差由塑料成型模具书中的模塑料件尺寸公差表差得,LDPE可选用一般等级精度,即选用MT6
1)型腔径向尺寸
由公式
式中s—塑件的收缩率,取0.015
Ls—塑件外径尺寸
x—修正系数(查表)
Δ—塑件公差值(由塑件的公差表查得)
δ—制造公差,取Δ/6
可得Lm(A)=[(1+0.015)×
150.2-0.7×
0.3]=152.2430+0。
050
=152.2+0.093+0.043
Lm(B)=[(1+0.015)×
100.2-0.7×
0.3]=101.4930+0.050
=101.5+0.043-0.007
[(1+0.015)×
137.86-0.53×
2]=138.8680+0.333
=138.9+0.265-0.068
74.14-0.54×
1.28]=74.5910+0.213
=74.6+0.204-0.009
2)型芯径向尺寸
由公式
可得lm(F)=[(1+0.015)×
129.98+0.8×
0.02]=131.9140-0.003
=131.9+0.014+0.011
lm(G)=[(1+0.015)×
69.98+0.8×
0.02]=69.9990-0.003
=70.0-0.001-0.004
lm(H)=[(1+0.015)×
95+0.8×
0.05]=96.3850-0.008
=96.4-0.015-0.023
lm(J)=[(1+0.015)×
49.7+0.58×
0.6]=50.0980-0.1
=50.1-0.002-0.102
lm(I)=[(1+0.015)×
19.69+0.58×
0.32]=19.6260-0.103
=19.6+0.026-0.077
3)型腔深度尺寸和型芯高度尺寸
及
可得(H)=[(1+0.015)×
60.02-0.65×
0.03]=60.9010+0.005
=60.9+0.006+0.001
3.13-0.6×
0.26]=3.0210+0.043
=3.O+0.064+0.021
(h)=[(1+0.015)×
59.99+0.65×
0.03]=60.8700-0.005
=60.9-0.030-0.035
2.87-0.6×
0.26]=2.7570-0.043
=2.7+0.057+0.014
以上的尺寸即为型腔和型芯的尺寸。
由于本次是课程设计,参考的资料有限,故在选择材料的过程中都是选择型号和材料以及尺寸略高于要求的,故对于型腔零件强度、刚度的校核可以不用进行。
五、模架的确定和标准件的选用
以上内容计算确定之后,便可根据计算结果选定模架。
在学校做设计时,模架部分可参照各模板标准尺寸来绘图;
在生产现场设计中,尽可能选用标准模具,确定出标准架的形式、规格及标准代号,这样能大大缩减模具制造周期,提高企业经济效益。
模架尺寸确定之后,对模具有关零件要进行必要的强度或刚度计算,以校核所选模架是否适当,尤其是对于大型模具,这一点尤其重要。
由前面型腔的布局以及相互的位置尺寸,在根据成型零件尺寸结合标准模架,选用结构形式为A3型、模架尺寸为250mm