25MW火筒式加热炉制造要点文档格式.docx
《25MW火筒式加热炉制造要点文档格式.docx》由会员分享,可在线阅读,更多相关《25MW火筒式加热炉制造要点文档格式.docx(26页珍藏版)》请在冰豆网上搜索。
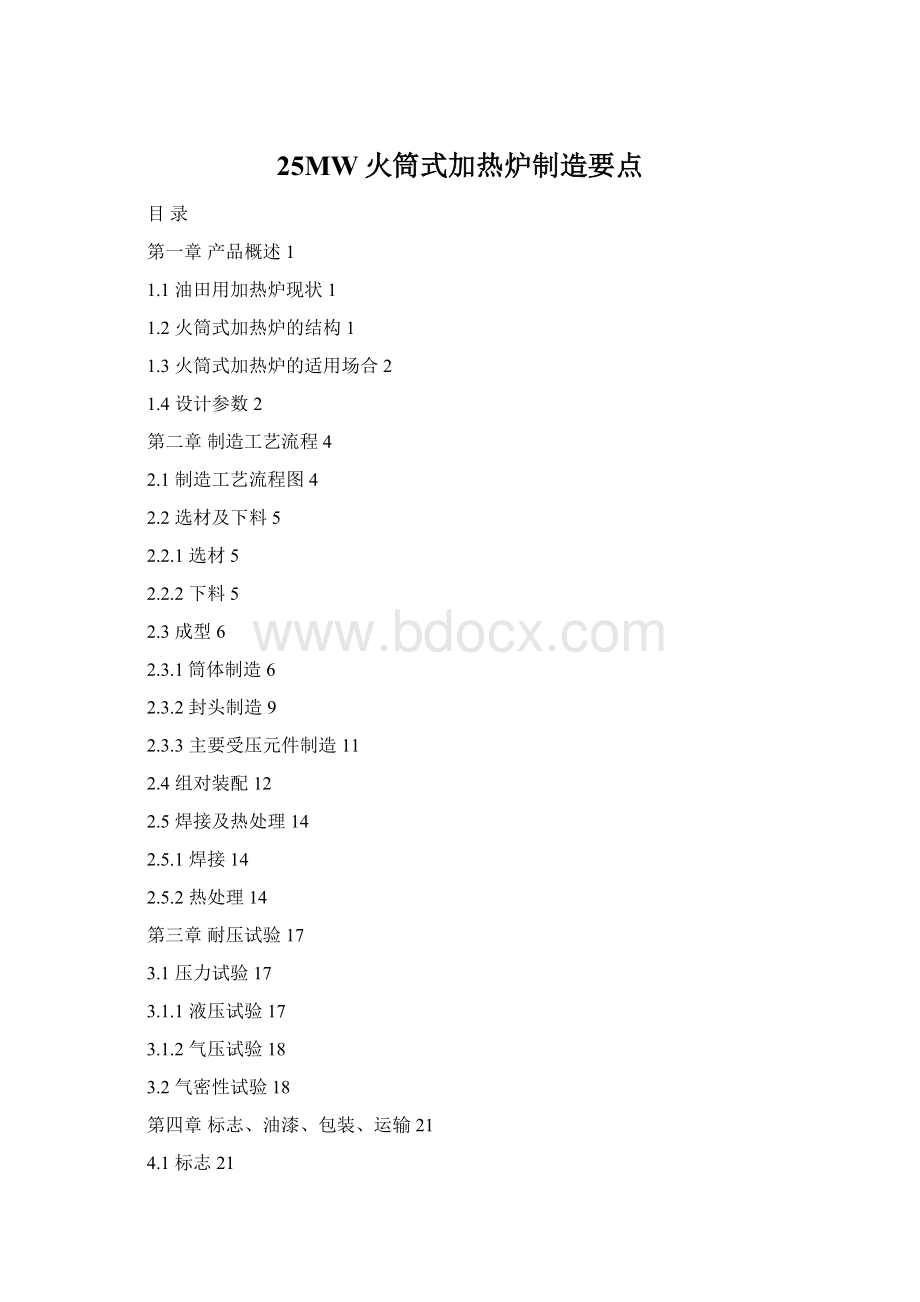
壳体是组成炉的主体部分。
由碳钢钢板焊制而成。
能承受一定的内压力和温度,并具有可容纳内部构件和一定的容积。
支座
用于支承水套炉壳体,一般采用鞍式支座。
火筒烟管
为火筒式加热炉的传热面,一般为“U”型结构,个别是由一个主火筒和几个副火筒或细烟管组成。
火筒部分以辐射传热为主,烟管部分以对流传热为主。
火筒烟管由锅炉钢焊制而成,要求能承受设计外压力和高温。
燃烧器
燃烧器是将燃料和助燃空气混合并按所需流速集中喷入加热炉内进行燃烧的装置。
油田加热炉应用较多的为油燃烧器和天然气燃烧器。
烟囱
烟囱的作用是将炉内废烟气排入大气并产生抽力以使助燃空气进入燃烧器。
烟囱高度及直径由燃烧方式及炉内阻力确定。
同时还应符合环保要求。
安全附件
主要包括压力表,安全阀等。
它们是保证火筒炉安全运行的重要部件。
另外,火筒炉还设有放空阀、排污阀等。
梯子平台
供火筒炉检修和更换阀件用。
保温防护层
保温防护层一般由轻质绝热材料组成,其作用是减少炉体的散热损失。
1.3火筒式加热炉的适用场合
火筒炉主要适用于油品性质较好,操作压力不大于0.6MPa的场所。
可与其它设备组合成带有加热部分的合一设备。
火筒炉的主要优点是压力降特别小,耗用量少,结构简单。
其缺点是适应性差。
燃烧的热量直接通过火筒加热炉壳内的生产介质。
与管式加热炉相比,火筒结垢的敏感性低、对换热影响不太显著。
但是被加热的生产介质在炉壳内流速缓慢,结构件上仍然容易结垢。
因此,火筒式加热炉一般不用于加热易结垢生产介质,如稠油、三次采油污水等。
1.4设计参数
本次2.5MW火筒式加热炉规格为:
Ø
3000×
10×
12800;
容器类别:
Ⅱ类;
产品编号:
13034。
主要设计参数如表1-1。
表1-1压力容器主要设计数据
设计图号
制-40361
容器名称
2.5MW火筒式加热炉
第1页
共1页
容器类别
Ⅱ类
主体材料
Q245R
设计压力
0.44MPa
金属重量
37120kg
续表1-1
设计温度
45℃
试验压力
0.55MPa(卧式)
0.66MPa(火筒)
工作介质
含水油、空气(轻度、易爆)
焊缝系数
0.85(壳体/封头)/1(火筒)
探伤方法及比例
A、B类20%RT,
级合格
制造规范
SY/T5262-2009
SY0031-2004
JB/T4731-2005
TSGR0004-2009
腐蚀余量
1.5mm(壳体/封头)/3mm(火筒)
气密性试验
设计单位
大庆油田工程有限公司
第二章制造工艺流程
2.1制造工艺流程图
图2-1制造工艺流程图
符号:
注释H-停止点;
E-检查点;
W-见证点;
R-审核;
RT-射线检测;
MT-磁粉检测
2.2选材及下料
2.2.1选材
2.2.1.1压力容器的选材原理
1.具有足够的强度,塑性,韧性和稳定性。
2.具有良好的冷热加工性和焊接性能。
3.在有腐蚀性介质的设备必须有良好的耐蚀性和抗氢性。
4.在高温状态使用的设备要有良好的热稳定性。
5.在低温状态下使用的设备要考虑有良好的韧性。
2.2.1.2压力容器材料的种类
1.碳钢,低合金钢
2.不锈钢
3.特殊材料:
①复合材料(16MnR+316L)
②刚镍合金
③超级双向不锈钢
④哈氏合金(NiMo:
78%20%合金)
2.2.1.3常用材料
常用复合材料:
16MnR+0Gr18Ni9
A:
按形状分:
钢板、棒料、管状、铸件、锻件
B:
按成分分:
碳素钢:
20号钢20RQ235Q245R
低合金钢:
16MnR、16MnDR、09MnNiDR、15CrMoR、16Mn锻件
高合金钢:
0Cr13、0Cr18Ni9、0Cr18Ni10Ti
尿素级材料:
X2CrNiMo18.143mol(尿素合成塔中使用,有较高耐腐蚀性)
2.2.2下料
2.2.2.1下料要求
1、不锈钢板下料采用数控等离子切割机放水切割或用剪板机剪切,复合钢板下料可用普通等离子或数控等离子切割。
2、其余板材下料采用数控或小车式氧-乙炔切割,但当钢板较薄、余量不多切割后易产生变形时也采用数控等离子切割机放水切割。
3、剪切、切割后相对于检查线偏差为±
1mm。
4、采用剪切下料后剪切面允许有深度≤1mm的磕痕和厚度≤0.5mm的毛刺。
2.2.2.2下料工具
1、气割:
碳钢
2、等离子切割:
合金钢、不锈钢
3、剪扳机:
δ≤8㎜L≤2500㎜切边为直边
4、锯管机:
接管
5、滚板机:
三辊
2.3成型
2.3.1筒体制造
钢板的复检
钢材的表面预处理
喷丸是目前工厂应用较多的大面积净化方法之一。
它是利用高速喷出的压缩空气流带出来的高速运动砂粒冲击工件表面,打落铁锈,使金属表面形成均匀而较光洁的表层。
根据所选材料规格,可选用GYX-nM型钢材预处理装置,其具体工艺过程为:
电磁吊上料→辊道输送→预热(40-50℃)→喷丸除锈→清理丸料→自动喷漆→烘干→轨道输出送料。
矫正
矫正的方法可分为冷矫和热矫两种,本设计采用冷矫,使用4200*9辊式中厚板矫平机。
划线、划线与号料
由于筒节是立体图形,需要先把筒节展开,形成展开图。
筒体展开后,其实就是一块矩形金属板。
毛坯宽度为筒节的长度,其大小取决于原材料的宽度和容器上焊缝的分布情况(焊缝不允许十字交叉)。
注意,毛坯实际宽度也要包括加工余量S。
下料
利用GD1-3050型小车式等离子弧切割机进行下料。
边缘加工与制孔
卷制:
采用对称式三辊卷板机来卷制钢板。
纵缝装配
筒节卷制完成后,进行纵焊缝转配焊接。
筒节的装配一般在V形铁或焊接滚轮架上进行。
矫圆:
焊接结束后,在卷板机上进行矫圆,大致可分三个步骤:
(1)工件放入卷板机上辊之后,根据计算,将上辊调至所需要的最大矫正曲率的位置进行加载。
(2)使工件在矫正曲率下多次滚卷,并着重于焊缝区的矫正,使圆筒曲率均匀一致。
经测量,直到合乎要求为止。
(3)逐渐卸除载荷,并使工件在逐渐卸除载荷的过程中多次滚卷。
无损检验:
焊缝进行100%无损检测
表2-1为筒节的制造工艺卡,表2-2为筒体上火管制作工艺卡,表2-3为筒体上烟管的制造工艺卡。
表2-1筒体制作工艺卡
筒体
Ø
3000δ=10mmH=11200mm
材质:
厚度:
10mm
数量:
1
工序
工艺要求
材料检验
钢板检验合格后方可投料,检验项目包括材质证明书和材料标识
切割
用数控切割机及剪板机进行切割,留出5mm的刨销余量。
刨坡口并修磨
用刨边机刨边,检验尺寸。
刨边时进刀量应较小,避免产生撕裂状表面,并用砂轮机修磨整个表面。
滚制组对
卷板时板面应放正使板的边缘与轴中心线平行,防止筒节边缘歪斜;
卷板不要一次成型,要反复几次逐渐形成;
用样板检查曲率合格后,点固焊,焊接要按焊接工艺要求。
点固焊用筋板点焊,棱角≤3mm,对口错边量不大于2.5mm。
焊接A类焊缝
焊接按焊接工艺卡
回床校圆尺寸检验
筒节回滚床校圆,用300mm曲率样板检查曲率环向棱角E不得大于3mm,同一断面最大最小直径差不得大于25mm。
封头与筒节及筒节与筒节组对
筒节间的组对按排版图,在转胎上进行,相临A类焊缝间相距100mm以上,棱角E≤3mm,对口错边量≤2.5mm。
焊接
无损检测
A、B类焊缝按JB/T4730-2005进行20%RT,AB-
级合格,若有返修按原焊接和检验工艺执行。
尺寸检验
用300mm样板检验其纵向棱角度≤3mm,壳体直线度不得大于11mm。
表2-2筒体(火管)制作工艺卡
筒体(火管)
800δ=12mmH=7450mmQ245R
800δ=14mmH=1800mm15CrMoR
800δ=12mmH=2300Q245R
2/2/2
刨边时进刀量应较小,避免产生撕裂状表面,并用砂轮机修磨整个表面
点固焊用筋板点焊,棱角度E≤3.2/3.4/3.2mm,对口错边量不大于3mm。
筒节回滚床校圆,用300mm曲率样板检查曲率环向棱角E不得大于3.2/3.4/3.2mm,同一断面最大最小直径差不得大于8mm
筒节间的组对按排版图,在转胎上进行,相临A类焊缝间相距100mm以上,棱角E≤3.2mm,对口错边量≤3mm
级合格,若有返修按原焊接和检验工艺执行
用300mm样板检验其纵向棱角度E≤3mm,壳体直线度不得大于11.5mm
表2-3筒体(烟管)制造工艺卡
筒体(烟管)
550δ=12mmH=9750mmQ245R
550δ=12mmH=8750mmQ245R
2/2
点固焊用筋板点焊,棱角度E≤3.2mm,对口错边量不大于3mm。
用300mm样板检验其纵向棱角度E≤3.2mm,壳体直线度不得大于9.7/8.7mm
2.3.2封头制造
常用的成形方法:
冲压成形、旋压成形、爆炸成形。
表2-4为封头制作工艺卡。
其工艺如下:
1、坯料准备
2、坯料加热
3、封头冲压
4、热处理
5、封头的后续加工
封头切边前应检查其尺寸是否正确,必要时应进行修正
;
封头切边时应先校正后划线并留出标准线,切边按划线切割,防止割斜
封头坡口应按焊接工艺制作坡口表面应打磨光洁,并按图样要求进行无损检测
碳钢封头制成后应进行喷砂处理以清除表面的氧化层不锈钢封头表面应进行酸洗钝化处理
。
6、封头表面应防止磕碰划伤
7、检验
封头的形状尺寸和表面质量应符合图样或相关封头标准的规定
除非图样另有规定封头的最小壁厚应不小于其名义厚度减去钢板厚度的负偏差
封头成形后,拼接焊缝应按JB4730进行100%射线检测或超声检测检测方法和质量等级按图样规定。
表2-4封头制造工艺卡
规格:
EHA3000×
10(9.7)mm
标准:
GBT25198-2010《压力容器封头》
2
下料切割
按展开尺寸1.3DN下料切割
拼接
对口错边量不得大于1mm。
焊接件焊接工艺卡
成型
压制符合GBT25198-2010及《封头制造工艺守则》
A类焊缝按JB4730-2005进行100%RT,
级合格。
焊缝表面应光滑并圆滑过渡,且对接焊缝内外表面不允许有咬边。
检验
实测厚度:
封头厚度不小于9.7mm;
用内样板检查椭圆封头形状偏差,椭圆度不得大于15mm,最大间隙外凸不得大于37.5mm,内凹不得大于18.75mm;
封头直边不得有纵向褶皱;
直边高度允差-2mm~4mm;
封头总深度公差-6mm~18mm。
2.3.3主要受压元件制造
主要受压元件的制造工艺和筒节制造工艺类似,具体工艺要求如表2-5和表2-6。
表2-5主要受压件制造工艺卡
部件名称
人孔筒节
材质
规格
外Ø
530×
6
数量
2件
执行标准
HG/T20592-2009
钢板检验合格后方可投料。
点固焊用筋板点焊,对口错边量不大于1.5mm。
筒节回滚床校圆,用300mm曲率样板检查曲率环向棱角E不得大于2.6mm,同一断面最大最小直径差不得大于5.1mm。
A类焊缝按JB/T4730-2005进行100%RT,AB-
用300mm样板检验其纵向棱角度E≤2.6mm。
表2-6主要受压件制造工艺卡
人孔法兰
PL500-6RF
下料、粗加工
根据尺寸对法兰进行下料,然后进行粗加工。
划线
根据图纸及标准要求尺寸对法兰进行划线允许偏差为0.25mm。
车削加工
根据图纸尺寸对法兰车削加工,工件在调头装夹前应在尾架车出找正带,保证图样要求。
钻孔
螺栓孔中心圆的偏心±
1.25mm,螺栓孔直径L偏差±
0.5mm。
按图纸给定尺寸及相关标准进行检验。
2.4组对装配
组对:
凡用焊接等不可拆连接进行拼装的工序称为组对。
组对完后进行焊接以达到密封和强度方面的要求。
装配:
凡用螺栓等可拆联接进行拼装的工序。
称为装配。
装配后可试验、使用。
组对工艺的重要性:
1、组对直接决定设备的整体尺寸和形状精度),常用评价参数:
错边、棱角、间隙。
2、组对的生产工艺复杂,通常会占去大量时间。
组对时设备零件之间没有固定定位。
使组对难度加大。
3为焊接提供良好条件。
主要工序:
测量、调整、固定、翻转
烟火管和容器的组对装配工艺如表2-7和表2-8
表2-7容器组装工艺(烟火管)
工序名称
筒体划线
先划出烟火管0°
、180°
两条基准线,再按施工图划出火管和烟管的加强圈边缘线
续表2-7
烟管接管与大小头组焊
烟管及火管与大小头及弯头组焊
组对按排版图,在转胎上进行,相临A类焊缝间相距100mm以上,冷角度E≤3.2mm,对口错变量≤3mm。
焊接按焊接工艺卡进行。
B类焊缝按JB/T4730-2005进行100%RT,AB-II级合格。
烟管与烟火管焊接的角接头按JB/T4730-2005进行100%MT检测,I级合格。
若有返修按原焊接和检验工艺执行。
附件组装
按施工图纸位置尺寸进行加强圈及烟管支座等附件安装、组焊。
连接及密封件组装
将烟管接管及烟火管进行密封,密封时各紧固件受力应均匀。
水压试验
按水压试验工艺对烟火管进行水压试验
防腐
防腐见防腐工艺卡。
燃烧道砌筑
按施工图纸砌筑燃烧道。
表2-8容器组装工艺
、90°
、270°
四条基准线,再按施工图划出各开孔位置的中心线及开孔边缘线
开孔
切割开孔并修磨,对于小孔应用锉刀清理坡口表面。
接管与法兰组焊
接管与法兰组对时,法兰端面的倾斜度不得大于法兰外径的1%,不大于3mm。
焊接件焊接工艺卡。
接管与壳体、封头组焊
法兰跨中均布;
外伸长度允差5mm;
法兰端面的倾斜度不得大于法兰外径的1%,不大于3mm;
位置允差1.5mm。
内件组装
按施工图纸位置尺寸进行烟火管等内件安装、组焊。
火管和烟火管封头处的角接头表面按JB/T4730-2005进行100%MT检测,I级合格。
按施工图纸位置尺寸进行鞍座等内件安装、组焊。
筒体与封头组对
筒体与封头的组对按排版图,在转胎上进行,对口错边量≤2.5mm。
焊接B类焊缝
焊接按焊接工艺卡。
B类焊缝按JB/T4730-2005进行20%RT,AB-
续表2-8
按水压试验工艺进行水压试验。
2.5焊接及热处理
2.5.1焊接
(一)焊前准备与焊接环境
1、焊条、焊剂及其他焊接材料的贮存库应保持干燥,相对湿度不得大于60%;
2、当施焊环境出现下列任一情况,且无有效防护措施时,禁止施焊。
手工焊时风速大于10m/s;
气体保护焊时风速大于2m/s;
相对湿度大于90%;
雨、雪环境。
(二)焊接工艺
1、容器施焊前的焊接工艺评定,按JB4708进行;
2、A、B类焊接焊缝的余高不得超过GB150的有关规定;
3、焊缝表面不得有裂纹、气孔、弧坑和飞溅物。
(三)焊缝返修
1、焊逢的同一部位的返修次数不宜超过两次。
如超过两次,返修前均应经制造单位技术总负责人批准,返修次数、部位和返修情况应记入容器的质量证明书;
2、要求焊后热处理的容器,一般应在热处理前进行返修。
如在热处理后返修时,补焊后应做必要的热处理。
2.5.2热处理
(一)正火
①目的:
细化晶粒,提高母材及常化处理焊缝的综合机械性能,消除冷作硬化,便于切削加工。
②方法:
把要正火的零件放入加热炉中加热到一定温度按每毫米1.5分~2.5分保温出炉空冷,风冷或雾冷。
③应用:
16MnR高温保温时间过长,使奥氏体晶粒大(正火)35﹟锻件(正火)封头,筒体(正火)
(二)调质处理:
提高零件的综合机械性能。
淬火+高温回火(500℃以上)。
得到索氏体。
封头,筒体,法兰,管板等。
20MnMo20MnMoNb13MnNiMoNb900℃~950℃2分~3.5分/mm水冷+空冷。
螺栓螺母:
①35CrMoA25Cr2MoVA35CrMoVA
②30Mn40Mn35CrMoA
硬度HB=187~229用亚温淬火。
(三)固溶处理:
(针对奥氏体不锈钢)即在室温条件下保留奥氏体。
①目的:
将零件加热使碳化物溶到奥氏体中,再以足够快的冷却速度将碳化物固定在奥氏体中。
具有最低的强度、最高塑性、最好的耐蚀性。
②应用:
封头
③方法:
加热到1000℃~1150℃,以2分到4分/㎜保温后快冷,然后水冷,再进行空冷。
(四)焊后热处理:
(消除应力,退火)PWHT
一般热处理:
SRISR
A.改善焊接接头及热影响区的组织和性能。
B.消除焊接和冷作硬化的应力。
C.防止产生焊接裂纹。
②方法:
A.优先采用炉内整体消除应力方法(另一法:
把容器视为加热炉,在设备内部加热外壳保温),压力容器规则:
(高压容器、中压反应器、储存容器、石油液化器储罐)不能用内部加热法。
B.分段热处理:
一端在炉内,采取适当保温措施以防有害的温度