油罐施工工艺Word格式.docx
《油罐施工工艺Word格式.docx》由会员分享,可在线阅读,更多相关《油罐施工工艺Word格式.docx(29页珍藏版)》请在冰豆网上搜索。
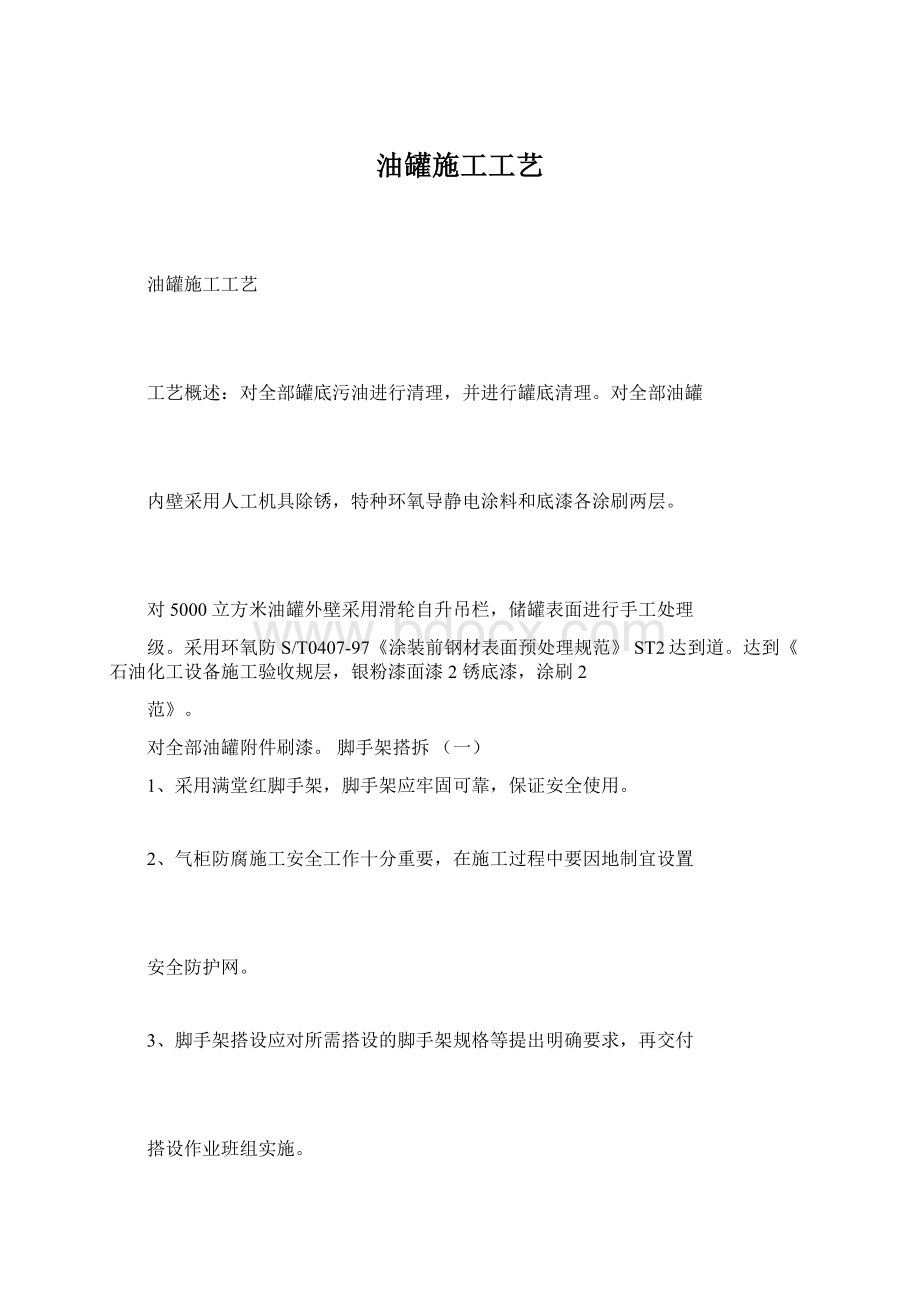
当作业面周围无合适挂靠设置位时,还应专设安全带挂设杆;
10、脚手架的交接验收与使用
10.1.脚手架搭设完毕,架设作业班组必须按施工要求进行全面自检,
然后通知项目部有关人员共同进行检查验收,检查确认合格后,填写
脚手架交接验收单,并在验收单上签字确认,挂牌后方可使用。
10.2验收后的脚手架任何人不得擅自拆改,特殊情况下需作局部修
改时,须经负责人同意,由原架设班组操作,装配成后仍需履行检查
交接验收手续。
11.沿脚手架攀登;
11.1脚手架的使用作业人员应从斜道或专用梯子至作业层,不得.在
;
脚手架上从事三级以上高处作业,应办理《高处作业票》
脚手架必须定期检查,如松动、折裂或倾斜等情况,应及时进11.2
行紧固或更换;
脚手架应设避雷装置,雷雨天时作业人员必须及时撤离脚手架;
11.3
脚手架在使用过程中,不得随意拆除架杆和脚手板,更不得局11.4
部切割和损坏。
12.脚手架的拆除
脚手架使用完毕应及时拆除12.1
临时性脚手架,实行一次性搭设,使用和拆除管理,不许搁置12.2.
待用。
脚手架需拆除时,拆除人员应填写脚手架拆除单。
12.3.
拆除脚手架,周围应设警戒标志,设专人监护,禁止他人入内。
12.4.
拆除时,应按顺序由上而下,不准上下同时作业;
严禁整排拉12.5.
倒脚手架。
拆下的架杆、连接件、脚手板等材料,应采用分类堆放,严禁12.6.
向下投掷。
拆除脚手架时,作业人员、架杆及作业面等与电线的安全距离12.7.
不足时,应切断电源或采取可靠的安全措施。
卸(解)开的脚手杆、板、应一次全部拆完。
12.8.
脚手架材料保管脚手架所有用的架杆、连接件、脚手板应定期12.9.
除锈防腐,分类整齐放置,不得散放在施工现场。
12.10.入钢管入库前应检查扣件是否有裂纹,螺栓是否有滑扣现象,
库前螺栓以及活动部分应涂以黄油。
(二)油罐清理
制定油罐清理方案,首先对技术人员及相关施工人员应熟悉现场储油罐的位置和工艺流程。
施工前项目部应对施工人员进行岗前技术和安全培训,确保施工安全性和准确性。
1、蒸馏
关闭采光孔,用蒸汽从油罐罐壁人孔处通入加温,罐内温度必须
达到70℃以上,吹扫掉罐壁与罐底残挂原油及石蜡,蒸馏时间为48小时(指70℃以上时间)。
蒸馏完毕后方可进行通风清罐工作。
2、通风
原油罐蒸完后,打开油罐的采光孔和人孔,自然通风24小时后,
并用空气压缩机向罐内强行通风48小时,将罐中油气排净。
经甲、乙双方安全员用可燃气体报警仪检查,合格后,使罐内烃类气体在爆炸下限25%以下后,作业人员方可进入罐内进行清理作业。
3、清罐
进行人工清罐,打开人孔,人工清除罐内剩余的原油污水及沉积物,必须按甲方要求运至指定位置,掩埋。
防止污染罐区地坪,考虑到环保因素拉运中车辆及罐区铺设塑料布或用毛毡,确保原油不滴漏,防止污染沿途路面。
清理时,人孔处必须有专人看守,如夜间施工罐内照明设备充足(必须使用防爆照明灯具)。
一般作业人员每30分钟更换一次,罐口必须有专人监护,确保清油施工安全。
清罐时,应使用防爆清理工具,采用自制铝,铜刮油器,将污油
刮到清油口进行清理。
(三)内壁人工机具除锈及修整
1、制定油罐防腐方案,首先对技术人员及相关施工人员应熟悉现场
储油罐的位置和工艺流程。
施工前项目部应对施工人员进行岗前技术
和安全培训,确保施工安全性和准确性。
2、油罐内除锈
(1)采用敲锈锤除掉金属表面焊接飞溅物或旧的厚锈,采用钢丝刷、铲刀、刮刀清理钢铁表面上松动的氧化皮、疏松的锈涂层。
金属结构
的夹角、死角部位除锈一定要彻底。
再用棉纱或破布将金属表面上浮尘擦干净。
如有油污的地方,应用汽油或稀释剂擦洗。
(2)动力驱动的旋转式或冲击式除锈工具可除掉钢铁表面上松动的
氧化皮、锈和旧涂层。
采用冲击式工具除锈时不应造成表面损伤、变形;
(3)油罐内表面上动力工具不能达到的地方,必须用手动工具进行补充除锈。
3、修整
(1)除锈合格后,用测厚仪与目测相结合的办法对罐底、罐内壁进
行100%的检测。
检测标准依据中国石油天然气管道局企业标准:
Q/GD0205-1997《立式圆筒形钢制焊接原油罐修理规程》第5章的检测与评定要求的二倍进行检测布点。
根据腐蚀面积及腐蚀深度确定工作量,罐底中副板腐蚀深度超过原设计厚度的1.2mm的,即如下进行相关作业:
如腐蚀面积小于30%的,进行局部补焊。
对于个别属点状腐蚀深度较高的腐蚀点,腐蚀深度超过原设计厚度2.4mm的,采用点
焊方式处理。
罐底边缘板腐蚀深度超过原设计板厚度的1.2mm的,对
腐蚀部位进行点焊补焊;
对于罐内壁腐蚀深度超过原设计厚度的,20%
必须采取局部补焊处理。
(2)申报动火报告
(3)出具检测报告底板腐蚀分析说明。
(四)吊栏施工
1.为确保设备安全、高效的运行,操作人员须严格遵照上海市技监局颁布的“高处悬挂作业安全规程”《DB31/95-1998》及如下操作规程使用高处作业吊栏。
2.操作人员必须佩带好安全帽、安全带并系好安全带将其挂扣在安全绳上;
3.患不宜高空作业疾病、酒后人员严禁操作吊栏;
4.高处作业使用的工具及物品必须采取防坠措施;
5.严禁将吊栏当作材料及人员的垂直运输工具使用并严格控制吊栏载荷;
6.在使用吊栏时,应划出安全区,并设置护栏、安全网等防护设施;
升降作业时,操作人员应密切注意电缆线是否挂卡在墙面或障碍物上;
7.禁止在阵风风力大于6级(相当于风速10。
8m/s)以上时,应停止吊栏使用。
8.每天下班停用时,应将设备停放至地面或用绳索将设备固定在建筑物上避免随风晃动;
9.每天下班停用时,应切断电源、锁好电箱门以免他人擅自使用;
吊栏操作人员须经劳动局有关部门培训,持劳动部门颁发的资格证书上岗;
10.吊栏设备应经有关部门检测合格后方可投入使用;
每天使用设备前,吊栏操作人员按《高处作业吊栏日常检查表》的内容进行检查,并做好检查记录;
11.高处作业吊栏是用钢丝绳从建筑物顶部,通过悬挂机构,沿立面悬挂的作业平台能够上下移动的一种悬挂设备。
12.高处作业吊栏主要用于高层建筑及多层建筑物的外墙施工、装修(如抹灰浆、贴墙砖、刷涂料)以及幕墙玻璃的安装、清洗等工程作业,也可用于电梯的安装作业以及油库、大型罐体、高大烟囱、桥梁和大坝工程检查、维修施工等作业。
13.高处作业吊栏操作简单、移位容易、方便实用、安全可靠。
使用高处作业吊栏,可免搭脚手架、使施工成本大大降低。
14.操作人员上机前,必须认真学习和掌握高处作业吊栏的说明书内容,且载荷在平台全上应基本均匀。
当施工高度较前梁较高及前梁伸出长度超出规定范围时,平台的载重量必须减少,风力较大时,还必须考虑风压的影响(相当于增加平台的载重量)。
具体的规定是必须保证悬挂机构的配重稳定力矩要大于两倍的吊栏升降部分自重、钢丝绳自重、重锤、额定载荷及风载荷所引起的倾履力矩。
.
15.工作平台悬挂在空中时,严禁随意拆卸提升机、安全锁、钢丝绳等。
由于故障确需要进行修理的,应由专职人员在落实安全可靠的措施后方可进行。
16.吊栏不宜在粉尘、腐蚀性物质或雷雨、六级以上大风等环境中工作。
(五)拟投入本工程防腐材料性能
环氧红丹防锈漆防腐涂料
组成成份:
环氧红丹防锈漆由环氧树脂、红丹颜料,填料、助剂及固化剂等组成,分甲、乙组份包装。
产品特性:
环氧红丹防锈漆具有优良的防锈性能,附着力强,强度高,漆膜干燥快,耐水防潮。
产品用途:
环氧红丹防锈漆适用于防锈要求高的钢铁表面,煤气柜,油罐,贮槽,地下管道,海洋矿井钢结构及其它工业设施的防锈。
颜色:
铁红色
2.45约重:
比
2/米145-155克理论用量:
漆膜厚度:
湿膜:
70μm干膜:
40μm
比:
甲(漆料):
乙(固化剂)=100:
5-7配
23±
2℃:
30分钟熟化时间:
适用期:
23±
6小时
表干:
2小时,实干:
24小时干燥时间:
最短2小时,最长2天涂装间隔:
高压无气喷涂、刷涂、辊涂涂装方式:
5%环氧涂料稀释剂≤稀释比例:
一年存贮期:
Sa2.5级,特钢材表面采用抛丸或喷砂处理,达到标准表面处理:
殊要求除锈达Sa2.5级,手工除锈达St3级。
FH52-42厚浆型环氧铝粉面漆
组成:
由环氧树脂、防锈颜料、铝粉、改性胺加成物固化剂、助剂等组成的双组份重防腐涂料。
特性:
漆膜具有优异的防锈性能和耐腐蚀性。
漆膜具有优异的耐酸碱、耐油、耐溶剂、耐化学药品性能。
漆膜具有优异的附着力、柔韧性、耐冲击性、耐久性和高耐磨性。
漆膜抗水渗透性好,耐海水、耐盐雾性能优越。
用途:
适用于船舶、化工设备、管道、贮罐、油罐、电力系统、海洋气候下的钢铁结构等作重防腐面漆之用。
物理参数:
颜色银灰色
平光光泽
重比1.5
干膜厚度100um
湿膜厚度120um
2理论用量180g/m
23±
2℃表干≤4h实干≤1Oh完干燥时间
℃甲组份闪7d全固化40乙组份℃27点
施工说明:
混合配化甲组份:
乙组份=25:
3.2(重量比)
20C20min熟化时间
适用期236h±
2℃
稀释剂环氧稀释剂
施工方法无气喷涂有气喷涂刷涂/辊涂
喷嘴口径—0.40.5mm2.0—3.Omm一
一喷出压力15-20Mpa0.3-0.6MPa
0-5%稀释量5—15%3—15%
工具清洗环氧稀释剂
涂装间隔
底材温度5℃20℃30℃
最短24h10h4h
最长7d
表面处理:
钢材表面经机械喷射除锈应达到瑞典除锈标准Sa2.5级或
人工、动力工具除锈达到St3级。
涂有底漆或中间漆的涂
层表面应干燥、无油脂、油污、锈蚀、水渍等一切杂物。
施工条件:
底材温度须高于露点以上3℃,相对湿度须小于85%。
雨、
雪、雾、大风等恶劣天气不能进行涂装,施工底材低于5℃
时,环氧与固化剂停止反应,不能进行施工。
建议涂装道数:
2—3道。
包装规格:
甲组份20升桶装25kg,乙组份4升桶装3.2kg。
贮存:
本产品应贮存于阴凉、干燥、通风的室内仓库,贮存期
一年。
注意事项:
.被涂物表面必须除锈、除油、除灰尘及其它附着物。
.若前道漆涂装时间过长,应用砂纸打磨,清除掉表面灰
尘污物后再涂漆,以保证层间附着力。
.施工所用工具应清洁干燥,涂料不得混入水份及其它杂
质,涂料现配现用,须6小时内用完。
·
漆膜未完全干燥固化之前,应采取保护措施,避免受到雨
水和其它液体的7中洗和践踏。
涂料应存放于温度较低通
风干燥处,远离热源,避免日光直射,并隔绝火种。
安全:
避免长期吸入溶剂蒸气或漆雾,皮肤、眼睛不得接触本品,
在狭窄处或空气不流通处施工,必须加强通风换气,并严禁烟火,
施工人员应戴好防护用具。
声明:
本说明有关数据为理论值或是在实验室中所得,实际施工
时会略有不同。
对本说明书,我们将随着产品的不断改进进行修改,
恕不另行通知。
FH54-70油罐内壁耐油导静电涂料(双组份)
组成:
由耐蚀环氧树脂、氨基树脂为基料,添加复合型导电颜料
和抗静电剂及助剂配制而成。
漆膜具有优良的附着力、柔韧性和抗冲击性。
具有良好的耐油和耐腐蚀性,使用后不溶解。
具有良好的导静电性能。
不溶涨、不溶解,对油品无污染。
用途:
主要用于油罐、油槽内壁的防护涂装。
颜色黑色
光泽无光
比重0.90
湿膜厚度200um
2理论用量180g/m
±
2℃表干≤1h实干≤24h干燥时间23
闪点℃25
甲组份:
乙组份=10:
1混合配比施工说明:
℃±
2熟化时间30min23
6h—±
2℃期适用423
环氧涂料稀释剂剂释稀
刷涂/辊涂有气喷涂施工方法无气喷涂
喷嘴口径0.4-0.5mm2.0-2.5mm
喷出压力0.3-0.5MPa15-30Mpa
稀释量0-5%5-10%0-3%
环氧涂料稀释剂工具清洗
涂装间隔
℃℃305℃20底材温度
最短12h24h48h
最长5d14d7d
钢铁表面整体除锈达到瑞典除锈标准Sa2.5级后整体涂
st3级+。
装;
或手工、动力工具除锈达到瑞典除锈标准
底材温度须高于露点以上3℃,相对湿度须小于85%。
施工底材温度低于℃时,环氧与固化剂停止反应,不能5
进行施工。
环氧红丹防锈漆等。
前道配套涂料:
环氧富锌底漆、环氧云铁防锈漆、
天以上方可投入使用。
℃条件下1023±
2保养期:
。
升容器装1.5kg包装规格:
甲组份18升容器装15kg乙组份3
存:
本产品应贮存于阴凉、干燥、通风的室内仓库,贮存期一贮
注:
涂装间隔时间较长时,应对上道涂层表面进行除油、年。
备
除其它附着物,涂层在未完全干燥前,应有保护措施。
除尘及清注意事项:
在
应将前道漆面打磨粗糙后再涂·
如果超过最大重涂间隔,
装,以确保漆膜间的层间附着力。
皮肤、眼睛不得接触本品,安全:
避免长期吸入溶剂蒸汽或漆雾,
在狭窄或空气不流通处施工,必须加强通风换气,并严禁烟火,
本说明有关数据为理论值或是在实验室中所得,说明:
实际施工时
会略有不同。
(六)涂刷工艺
机械无气喷涂
涂装作业要在清洁环境中进行,避免未干的涂层被灰尘等杂物污染。
(1)喷涂距离表面300-500mm为宜。
(2)喷枪与被喷涂面应垂直,两端以45度为限,并应平行移动,尽量避免弧形移动。
(3)喷枪的移动速度以达到规定膜厚且不出现流挂为宜。
(4)涂装前对油孔、轴孔加工后的配合面、螺丝装置等非涂装部位进行遮蔽保护。
(5)涂料各层间的涂覆间隔时间应按涂料厂家规定执行,如因某种原因超过其最长间隔时间,则将前一涂层粗砂布打毛后,再进行涂装,以保证涂层间的结合力。
(6)施工过程中设专人进行各道油漆涂层的补涂作业。
(7)喷涂安全注意事项
1)为保证喷涂机安全使用,最高进气压力不准超过0.6Mpa。
2)喷涂过程中会产生静电,因此喷涂操作时,要将喷涂机接地,以
防静电。
3)喷涂过程中,在清洗更换喷嘴或不喷时,应及时将喷枪板机保险
装置锁住。
在任何情况下,喷枪枪口不能朝向自已或他人,以免误压
板机,高压涂料喷出击伤人体。
(8)非涂覆面的保护
应采用可靠的手段(如粘贴胶带、纸板)对非涂覆面予以保护。
手工刷涂法:
(1)涂刷时,将刷子的2/3沾上油漆,沾上漆的刷在桶边刮一下
以减少刷子一边的油漆,拿出时,有油漆的一边向上进行涂刷。
栏杆扶手的圆钢及死角位置涂漆时,用刷尖沾上油漆作来回弹拍涂装。
用过的漆刷要及时用稀料洗干净,以免刷毛变硬,刷柄要保持清洁。
(2)涂装前,金属表面处理后应无灰尘、油污、浮土等。
特别注意交叉及阴角处的涂刷。
(3)防腐涂料使用前,首先应核对油漆的种类、名称以及稀释剂是否符合涂料说明书的技术要求,油漆还应做二次检查,各项指标.
合格后方可调制涂装。
(4)涂料的配制应严格按照说明书的技术要求及配比进行调配,
并充分搅拌,使桶底沉淀物混合均匀,放置15-30分钟后,使其充分熟化方可使用。
工程用量允许的施工时间,应根据说明书的规定
控制,在现场调配时,据当天工程量配多少用多少。
)使用涂料时,应边刷涂边搅拌,如有结皮或其他杂物,必需5(
清除掉,方可使用。
涂料开桶后,必须密封保存。
)使用稀释剂时,其种类和用量应符合油漆生产的标准规定。
(6
)涂刷时,首先对边角、棱角处、夹缝处进行预涂,必要时采7(
用长杆毛笔进行点涂,以保证漆膜厚薄均匀无漏涂。
,遇雨、雾、度为宜,相对湿度不宜大于70%8()施工环境温度以15-30
大风少天气不得进行施工。
)涂层的第一道漆膜干后,方可进行下道涂层的施工。
9(
)涂刷时,尽量减少涂层的往复次数,以免将底层漆膜拉起,(10按纵横交错方式涂漆以保证漆膜的涂刷质量。
应以漆膜厚度控制施工质量。
)为充分发挥涂料的耐腐蚀性能,(11
颜色一致无针孔、2
(1)所有涂层不得漏涂,涂层表面应光滑平整,
气泡、流挂、剥落、粉化和破损等缺陷,无明显的刷痕、纹路及阴
影条纹。
每道厚度及总干膜厚度完全满足该涂料的技术指标及甲方的要求。
做好表面干净、31()每道工序施工前要经甲方质检人员检查验收,无灰尘、无油污等,每一道油漆必须采用漆膜测厚仪测漆膜厚度,
防腐完工后组织竣工验收。
(14)使用稀释剂时,其余漆类的用量应符合生产厂家的规定标准。
配制涂料时,应搅拌均匀。
技术要求:
对于死角部位,要用毛刷进行点涂,不允许有漏涂、漏刷、流淌、流挂等不良现象存在,要达到外观颜色均匀一致、光滑靓丽。
养护:
自然养护7-10日,即可交付使用。
(15)质量检验
1)每一道漆涂敷完,应在不同部位测定涂层的湿膜厚度,并及时对
工艺参数进行调整。
2)每涂完一道漆后进行目视检查,不得有气泡、褶皱、分离起皮、
流挂等现象。
3)最后一道漆实干后固化前应检查防腐层厚度,厚度不合格应增加
涂敷遍数直至合格。
4)外观检查
防腐层外观应平整连续、光滑、无气泡、无漏涂部位,并且不得
发粘、脱皮、气泡、斑痕等缺陷存在。
厚度检查
A、采用无损测厚仪进行测量,试验结构应达到下列要求
2
B、在油罐壁上选取若干检测单元(应包括不同部位和构件),以1m
为一个检测区域,每个区域至少抽测两个点,检查布点应均匀,所
有检测面积的和应大于或等于涂漆总面积的5%-10%进行检查。
C、每个检测区域有一个以上点不合格的区域进行复涂,若不合格
区域不超过5%,则相应对防腐层不合格的区域进行复涂,若有5%
5%以上的区域不合格,则相应部分应加倍检查。
若加倍检查仍有