第三章 制备CNTs结果与讨论Word格式.docx
《第三章 制备CNTs结果与讨论Word格式.docx》由会员分享,可在线阅读,更多相关《第三章 制备CNTs结果与讨论Word格式.docx(20页珍藏版)》请在冰豆网上搜索。
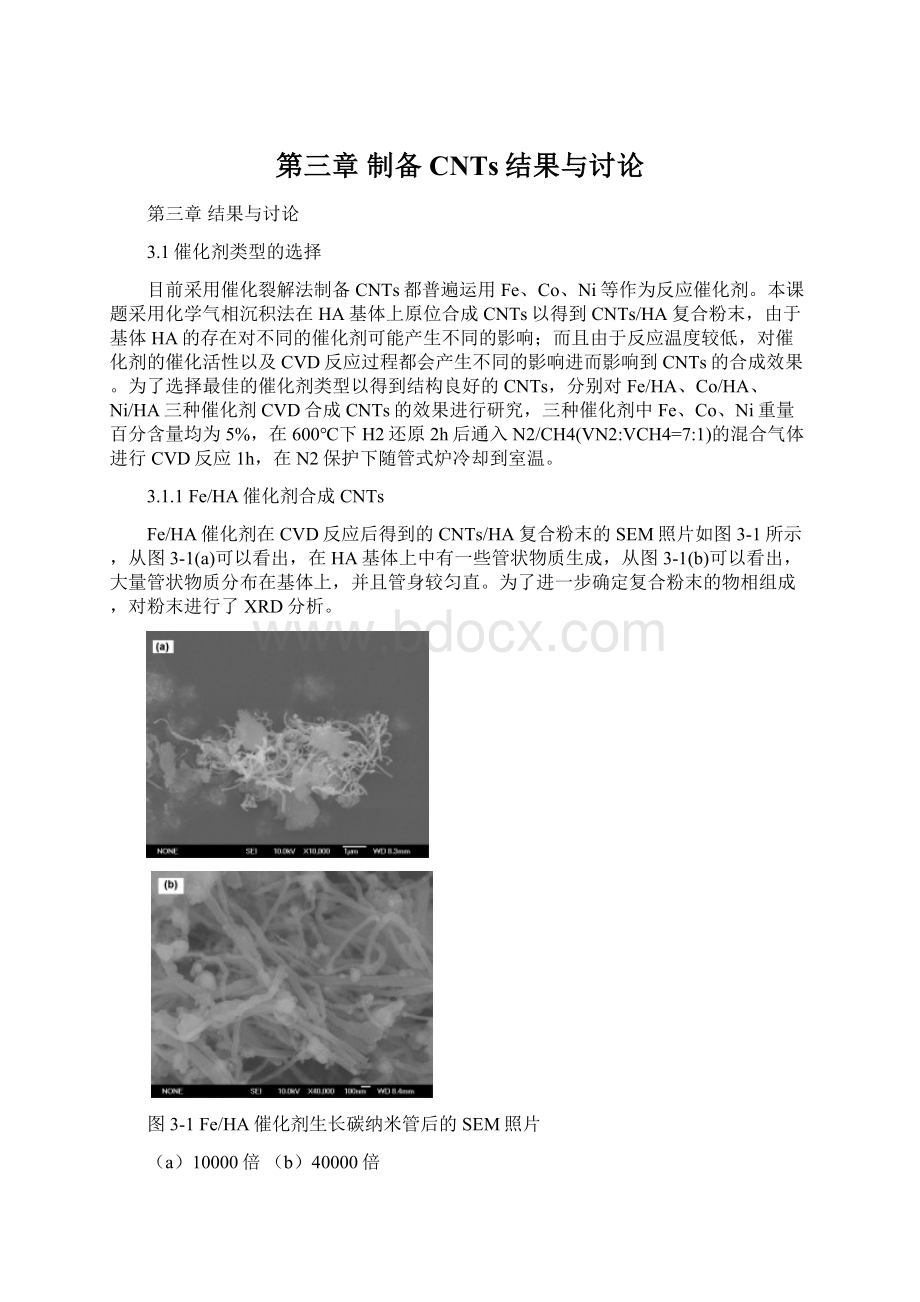
石墨层的结构完整、晶化程度较好,通过采用DigitalMicrograph软件测量得到石墨层的平均片间距为0.344nm,与理想石墨层的片间距0.34nm非常接近,也表明在Fe/HA催化剂上采用CVD法所合成的CNTs具有较好的结构和晶化程度。
图3-3Fe/HA催化剂合成CNTs的TEM、EDS和HRTEM图
(a)CNTs的TEM图(b)CNTs端部催化剂颗粒的EDS图(c)典型CNTs的HRTEM图
3.1.2Co/HA催化剂合成CNTs
以Co/HA为催化剂CVD反应后复合粉末的SEM照片如图3-4所示,由图3-4(a)可以看到,复合粉末中没有CNTs的存在,只是在基体上有一些颗粒状物质。
由图3-4(b)所示HRSEM可见,在某些区域存在极少量CNTs,其长度短并且分布不均匀,只能在某几个区域内观察到。
图3-4Co/HA催化剂生长碳纳米管后的SEM
为了确定采用Co/HA催化剂CVD反应产物的相组成,对复合粉末进行了XRD物相分析,如图3-5所示。
图3-5Co/HA催化剂生长碳纳米管后的XRD谱图
从图3-5XRD的分析结果中,可以发现HA的特征峰以及Co的特征峰,但没有发现石墨C的特征峰,可能是由于CNTs其含量太少,XRD分析仪器无法探测到如此微量的碳,因此,在图3-5中并未出现明显C的衍射峰。
由此可见,以Co/HA为催化剂可以生长出碳纳米管,但是CNTs的合成效果不佳,其原因可能在于Co颗粒的团聚或较低的反应温度下Co颗粒催化活性的发挥不良。
对Co/HA合成产物进行了TEM分析的结果如图3-6所示。
由图3-6(a)可见,Co/HA催化合成的CNTs很短,约为1μm左右。
图3-6(b)为CNTs的HRTEM照片,由该图可见利用Co/HA催化剂也可以合成由多层石墨层壁堆垛成的直管状多壁碳纳米管,但其产率较低。
此外,复合粉末中也可观察到一些由空芯洋葱碳纳米颗粒存在,如图图3-6(c)所示,添加具体的描述。
图3-6Co/HA催化剂合成CNTs的TEM和HRTEM图
3.1.3Ni/HA催化剂合成CNTs
Ni/HA催化剂CVD合成产物的SEM照片如图3-7所示。
由图3-7(a)可见,在较低的倍数下就可以观察到复合粉末中大量管状物质存在,结合XRD谱图(如图3-8所示),这些管状的物质为CNTs。
由图3-7(b)可以观察到,大量弯曲的CNTs均匀地分布在HA基体上,其长度大都在约1μm以上,管径也比较均匀,无明显的团聚现象,这说明以Ni/HA为催化剂在600℃下能够通过CVD法有效的催化合成CNTs并且其催化效果良好。
图3-7Ni/HA催化剂生长碳纳米管后的SEM
(b)这张照片选的不好,CNTs形态没有图3-1bFe/HA合成的好,应当替换一张
图3-8Ni/HA催化剂生长碳纳米管后的XRD谱图
对复合粉末进行了TEM分析,如图3-9所示。
由图3-9(a)可见,由Ni/HA催化剂合成的CNTs长度约在几个微米左右,管径均匀且长度也比较一致,但所合成的CNTs都具有不同程度的弯曲。
与之前Fe/HA催化合成的CNTs类似的是,多数CNTs的顶端都有颗粒状的黑色物质,通过对顶端物质进行EDS能谱分析(如图3-9(b)所示),可以确定该黑色颗粒为纳米级的Ni催化剂。
图3-9(c)为典型CNTs的HRTEM照片,可以看出由Ni催化合成的CNTs是由多层石墨层壁堆垛成的直管状多壁碳纳米管,碳纳米管的管径也比较均匀,外径在20nm左右,内径在8nm左右;
石墨层的结构完整、晶化程度较好,测量得到石墨层的平均片间距为0.345nm,与理想石墨层的片间距0.34nm非常接近,这也进一步表明在Ni/HA催化剂上采用CVD法所合成的CNTs具有较好的结构和晶化程度。
图3-9Ni/HA催化剂合成CNTs的TEM、EDS和HRTEM图
(a)CNTs的TEM图(b)CNTs端部催化剂颗粒的EDS图(c)典型CNTs的HRTEM图
(C)这张照片不清楚,选一张我们自己清除的照片
3.1.4不同催化剂合成效果差异的原因
由上述研究可见,Fe、Co、Ni三种催化剂合成的CNTs有其各自的特点。
Fe催化剂合成的CNTs管身较直,管径均匀,具有良好的石墨化结晶程度;
Co催化剂合成的CNTs长度很短,产率很低;
Ni催化生成的CNTs管径均匀,主要为直管状,部分有弯曲现象,结晶程度也较好,并且产率最高。
综合比较,可以确定Ni/HA催化剂最有利的催化剂。
原因可能在于以下几个方面:
首先,Ni的物理性质使其具有更高的催化活性,例如Ni催化剂颗粒相对Fe、Co颗粒尺寸较小、比表面积大、催化活性强,因此可以在更短的时间内使足量裂解的碳吸附到催化剂颗粒表面并在颗粒表面形成碳化物,继而通过C的溶解、扩散与析出形成石墨层生长CNTs;
并且,C在Ni元素中的扩散系数是三种物质中最大的,因此,Ni的催化活性和效果都是最好的。
其次,反应条件对三种催化剂催化活性的发挥也有一定影响。
本实验采用CVD法合成CNTs,反应温度600℃。
虽然都没有达到三种催化剂的熔点,但是由于是纳米颗粒的熔点会随其颗粒尺寸的减小而降低,因此颗粒的熔点可以明显的降低,而在三种催化剂中Ni的熔点最低,因此在600℃它的液化程度相对最好,催化活性的发挥程度也最好。
再次,羟基磷灰石中处于Ca(Ⅱ)位置的Ca2+可以与重金属离子发生交换。
由于Fe3+的离子半径(r=0.064nm)和电负性(Xp=1.83),在实验中用沉淀-沉积法制备催化剂前驱体时,基体HA和溶液中的Fe3+在室温下共同沉淀,由于HA含量较高并且颗粒度小且均匀,Fe3+可与Ca2+发生置换作用,其置换结果明显降低了作为催化剂的Fe含量,使得合成CNTs的产率明显降低,同时,离子交换还可能影响HA本身的物理、化学性质。
综上,由Ni作为催化剂于HA基体上原位CVD合成CNTs的催化和生长效果较好,从碳纳米管含量、形态和结构完整性综合对比,Ni/HA可作为CNTs/HA复合粉末制备的首选催化剂。
3.2催化剂含量对CNTs合成的影响
采用CVD合成CNTs复合粉末过程中,不同反应参数对CNTs合成的整体效果有很大影响,其主要影响因素有催化剂含量、CVD反应时间、反应混合气体组成比例等。
本实验固定CVD反应时间1h、载气比例为N2:
CH4=7:
1,研究催化剂含量对CNTs/HA复合粉末合成效果的影响。
通过对复合粉末中CNTs的含量测量及粉末SEM、XRD、TEM等检测结果来表征催化剂含量对CNTs合成效果的影响。
3.2.1催化剂含量对CNTs产率的影响
通过对反应前催化前驱体质量及反应后复合粉末质量称量,计算出复合粉末中CNTs的产率及相对含量,其与催化剂中Ni含量关系如表3-1所示。
表3-1CNTs的产率、相对含量与Ni含量的关系
Ni含量/wt%
CNTs产率/%
CNTs相对含量/%
1.0
5.0
8.0
0.9869
1.0277
1.0457
0.68
1.30
5.81
从表3-1中可以明显看出,随着催化剂中Ni含量的增加,CNTs产率增加,即CNTs在复合粉末中的含量增加。
在Ni含量为1.0%到5.0%之间CNTs产率增加的幅度很大,这是因为随着催化剂含量的升高,具有催化活性的Ni颗粒增加,在单位时间内CH4可以催化裂解出更多的碳原子从而使反应气氛中C原子的浓度提高,导致C原子在Ni颗粒上吸附、溶解和析出的速度增加,导致了CNTs的生长速度加快、产率上升。
但是当Ni含量高于5%后,随Ni含量继续提高,产率增加的幅度放慢,这可能因为Ni含量增加后在HA基体表面上的Ni颗粒数量逐渐增多、密度增大,而纳米级的物质极易团聚以减小其表面能来达到稳定状态,因此有部分Ni颗粒可能团聚在一起,降低了其催化活性;
此外,由于很高的Ni含量导致气氛中C原子浓度过高而在催化剂表面沉积成无定形碳也会抑制催化剂活性发挥、导致CNTs产率上升幅度减缓。
3.2.2复合粉末的SEM分析
图3-10为不同Ni含量CVD反应后复合粉末的SEM照片,可以看出,随含Ni量的增加,CNTs数量也在增加。
由图3-10(a)可见,Ni含量为1%时,只是在HA颗粒表面的部分区域出现CNTs,说明Ni催化剂颗粒在基体表面分布不十分均匀;
Ni含量为5%时(图3-10(b)),在基体上的大部分区域都可见到CNTs,CNTs的数量较多且分布均匀;
当含Ni量达到8%时(图3-10(c)),整个基体表面都被密布的CNTs所覆盖。
图3-10不同Ni含量复合粉末的SEM照片
(a)1%Ni(b)5%Ni(c)8%Ni
3.2.3复合粉末的XRD分析
图3-11为含Ni量1%、5%、8%的催化剂CVD反应后复合粉末的XRD图。
由该图可见,三组复合粉末都是由HA、C及Ni组成,但随Ni含量不同,复合粉末中各相的峰强有所不同,可能是由于HA在整个复合粉末中所占的比例太大,XRD衍射后它的峰强也最大,造成其它含量较少物质的峰强太小以致在XRD图上的特征峰不明显。
由于CVD反应时间短,生成CNTs的重量百分含量很少(通过计算CNTs含量最多只有5%左右),而且CNTs的特征峰与羟基磷灰石的特征峰位置重合,因此,在谱图中只能通过峰强的微弱差异判断有CNTs生成。
在1%Ni的谱图中由于含Ni量很少,因此Ni的特征峰也不够强,其它两组粉末Ni的特征峰相对较明显。
图3-11复合粉末的XRD谱图
(a)1%Ni(b)5%Ni(c)8%Ni
3.2.4复合粉末的TEM分析
图3-125%Ni合成CNTs的HRTEM分析
图3-12为由含Ni量5%的催化剂合成复合粉末中CNTs的HRTEM照片。
由图3-12(a)可见,所合成的CNTs具有由多层石墨层组成的直管状结构,与鱼骨状、螺旋状、念珠状等形态的CNTs相比,该结构的CNTs具有较好的力学性能,更适合作为复合材料的增强相,在管壁的外侧还结合着少量的HA。
此外,如图3-12(b)所示,在HRTEM下也发现了少量竹节型CNTs结构,即在CNTs芯部间隔分布着拱型的石墨片层。
目前研究认为,这种竹节型碳纳米管的形成机制主要有以下几种:
(1)催化剂颗粒或拱型石墨片运动机制
(2)碳壳形成机制(3)桥式结构(bridgestructure)形成机制(4)催化剂收缩机制(5)碳纳米管管壁弯曲机制。
上述几种机制分别从不同方面说明了竹节型结构碳纳米管的形成,总的来说,竹节型CNTs形成可能是催化剂颗粒和石墨片层的分离、碳原子垂直CNTs管壁的横向扩散和掺杂元素改变了CNTs结构等因素所致。
大部分研究认为,在CNTs生长过程中,碳原子从催化剂底部析出形成石墨片层,之后,石墨片层同催化剂分离形成竹节型的碳层分隔,但有关碳原子的析出过程对竹节型结构CNTs形成的作用有待进一步研究。
另外,一些研究的的实验气氛中含有氮或催化剂本身含有氮元素,同时,氮在催化剂内部、催化剂与CNTs界面以及CNTs的竹节石墨片内均已被检测到;
并且Ma等[参考文献]在制备碳纳米管时,将气体从CH4+N2变为CH4+H2后,CNTs从竹节型结构改变为中空型结构。
由此可见,在生长CNTs过程中,氮可溶解到催化剂中并能从催化剂中析出掺人石墨片层内改变石墨片的结构,因此,氮可能是竹节型CNTs形成的关键因素,但其作用机理仍需进一步研究。
本实验中采用N2作为CVD法合成CNTs的反应载气,因此对竹节型碳纳米管的形成有一定的促进作用。
从图3-12(b)中还可以看出,竹节型CNTs的外壁上附着着一些纳米羟基磷灰石颗粒,有文献指出,与中空直管状CNTs相比,竹节型CNTs更有利于结合纳米HA,因此该结构有可能改善CNTs/HA复合材料的界面结合状况。
3.2.5小结
随着Ni催化剂含量的增加,CNTs的产率和相对含量都明显上升,在基体中的分布也更加均匀。
用CVD法可以在HA基体上原位生长出均匀分布的CNTs增强体,该CNTs具有多层石墨壳构成的直壁管状结构,管内、外径均匀,长度在1µ
m以上并与基体结合良好。
采用本实验方法进行CNTs/HA复合粉末的制备过程中,除了得到大量中空直管状的碳纳米管,还有一些其它碳纳米结构形成(如竹节型碳纳米管、无定形碳、洋葱碳)但数量较少。
通过控制工艺参数,用不同Ni含量催化剂可以生长出CNTs含量可控的CNTs/HA复合粉末,可为下一步制备不同CNTs含量的CNTs/HA复合材料块体制备提供了原始粉末。
3.3粉末冶金工艺参数及CNTs含量对CNTs/HA复合材料组织、性能的影响
本实验通过粉末冶金工艺对原位合成的CNTs/HA复合粉末进行压制、烧结,制备成了CNTs/HA复合材料,主要研究了工艺参数对复合材料组织和性能的影响,通过试验优选出适合该材料的最佳工艺参数并制备了具有不同CNTs含量的CNTs/HA复合材料。
3.3.1压制压力的选择
采用一系列CNTs含量不同的CNTs/HA复合粉末,分别在450MPa、550MPa、700MPa下保压90s制备CNTs/HA复合材料,其压制效果如表3-2所示。
表3-2压制压力对CNTs/Al复合材料成型的影响
压力CNTs含量(wt%)
450MPa
550MPa
700MPa
可以成型
可以成型
0.5
1.5
2.0
2.5
成型困难,出现分层现象
3.0
出现分层现象
从表中可以看出,在压制压力为450MPa时,不同CNTs含量的CNTs/HA复合粉末都可以压制成型;
当压制压力为550MPa时,CNTs含量为3.0%时出现分层现象;
当压制压力为700MPa时,CNTs含量为0、0.5%、1.0%、1.5%、2.0%的复合粉末可以成型,而当CNTs含量达到2.5%和3.0%时,复合粉末压制成型出现困难,复合粉末不能成型而出现分层现象。
复合材料在压制过程中组织发生变化。
压制过程开始时,由于压力的作用,材料内尺寸大小不一的颗粒开始互相填充孔隙,颗粒凸凹不平的表面可以使其与其它颗粒的表面紧密锲和在一起,这是压坯强度提高的主要原因。
当压制过程继续时,材料颗粒之间的接触更紧密、机械咬合力更大,并且颗粒间距极大的缩短,当它们之间的距离达到原子间的距离时,原子间的引力又将颗粒紧密结合在一起,进一步提高了材料的强度和致密度。
压制初期颗粒是以位移为主要形式来填充孔隙的,因此,颗粒的组织没有明显变化,而随着压制压力提高或压制时间延长,压力会大于颗粒的屈服强度而使复合材料颗粒变形,同时使颗粒之间的孔隙明显减小。
当压制压力超过颗粒的强度极限时,可能使颗粒发生粉碎性断裂而使材料细小的孔隙增加,导致烧结后的强度降低。
此外,对于CNTs/HA复合材料在550MPa、700MPa下压制时,可能由于压力过大导致复合材料中的CNTs因应力集中断裂而使其长径比下降,同时,复合材料内部出现显微裂纹并且材料的孔隙增加、性能下降。
因此,从CNTs/Al基复合材料的压制效果对比来看,压制压力选择450MPa较为适宜。
3.3.2烧结工艺参数对复合材料性能的影响
烧结是制备陶瓷基复合材料的关键步骤,通过烧结,材料才能变得致密并且获得相当的强度等力学性质和其他各种功能,因此,烧结工艺参数对陶瓷的密度、组织结构和力学性能有非常重要的影响。
3.3.2.1烧结温度对材料微观结构的影响
由于羟基磷灰石的物理化学特性,尤其是高温不稳定性,导致其烧结过程非常复杂,主要涉及到HA的脱水反应(800℃)和分解反应(1300℃)。
HA的脱水反应可提高其可烧结性能;
而分解反应则会阻碍烧结并降低其力学性能。
CNTs的加入对HA的烧结可产生了一定的影响,高温下CNTs在空气中的热稳定性比较低,在烧结过程中如何保持其结构不变且不与其他相发生化学反应并最终保持其原有结构和性能也是一个关键问题。
将CNTs/HA复合粉末压制后,在N2保护气氛下进行烧结。
先在600℃保温3h,目的是消除块体材料的内应力;
然后分别在900℃,1000℃,1100℃保温1h,最后以1.5℃/min的速率降至室温。
烧结后的CNTs/HA复合材料的SEM图片如图3-13所示。
图3-13不同温度烧结后复合材料SEM
(a)900℃(b)1000℃(c)1100℃——字号
从图3-13可以看出,烧结后复合材料中仍然有CNTs的存在。
由图3-13(a)可见,当烧结温度为900℃时,CNTs的形状基本没有发生变化而是保持原状并在HA基体中分布均匀。
随着烧结温度的升高,烧结后复合材料中剩余CNTs的含量也随之减少(如图3-13(b)、(c)所示),这表明CNTs发生了部分分解情况。
在烧结温度为1100℃时,复合材料中CNTs含量明显降低,CNTs的管径增粗,同时羟基磷灰石的晶粒有长大的现象,这说明在1100℃下,CNTs因热稳定性差已发生了部分分解,而CNTs的增粗有可能是HA在1100℃左右发生分解反应生成的少量CaO覆盖在CNTs表面所致,反应如下:
2Ca5(PO4)3OH→3Ca3(PO4)2+CaO(v)+H2O(3-1)
由于CaO的熔点较低,在1100℃时部分以气态存在,该部分CaO与CNTs反应生成CaC覆盖于CNTs表面致使CNTs增粗,由于CaC属于脆性相,它的形成会造成复合材料韧性的降低,因此应合理控制烧结温度以避免该反应发生。
3.3.2.2烧结气氛对材料微观结构的影响
分别在N2、Ar保护以及真空中对复合材料进行烧结,烧结温度为1000℃,烧结后材料的SEM如图3-14所示。
图3-14不同气氛下烧结的复合材料SEM
(a)N2保护烧结;
(b)Ar保护烧结;
(c)真空烧结——字号
从图上可以看出,在N2或Ar气氛条件下烧结所得CNTs/HA复合材料中存在大量孔洞,材料致密度差(如图3-14(a)、(b)所示),这将大大降低复合材料的力学性能;
但复合材料中CNTs的存留量明显多于在真空条件下烧结得到的复合材料。
真空中烧结的CNTs/HA复合材料的致密性则明显提高,空隙率较低,如图3-14(c)所示,这将在一定程度上提高复合材料的力学性能。
造成复合材料致密性不同的原因可能是在真空中与气氛烧结过程中,坯体烧结致密化过程的气体排出难易程度不同所致。
3.3.3CNTs含量对复合材料微观结构及力学性能的影响
在前期实验中得出了制备CNTs/HA复合材料的最优工艺参数,即450MPa压制,烧结工艺为600℃/3h+1000℃/1h真空烧结,在此基础上,对不同CNTs含量的CNTs/HA复合粉末进行压制、烧结,研究CNTs含量对CNTs/HA复合材料组织和性能的影响
3.3.3.1CNTs含量对复合材料密度和致密度的影响
复合材料的理论密度是假设复合材料内没有任何缺陷时的密度,其计算公式如式(3-2)所示:
(3-2)
式中,ρx和Vx分别为第X相的理论密度和体积分数,这里取ρHA=3.16g/cm3、
=1.3g/cm3对CNTs/HA复合材料理论密度进行计算,复合材料的致密度则是块体材料的实际密度ρa与其理论密度ρt的比值来表征,实测和理论计算结果如图3-15所示。
由图3-15(a)可见,随着CNTs含量增加,由于CNTs非常小的密度,使复合材料的密度明显降低;
同时由于复合材料中有空隙存在,复合材料的实际密度要低于其理论密度,并且随CNTs含量的增加,实际密度偏离理论密度的值越大。
由3-15(b)可见,CNTs含量增加,CNTs阻碍HA基体的致密化的效果越明显,导致复合材料中的孔隙也相对地增加并降低了材料的致密度。
图3-15密度和致密度图
(a)密度(b)致密度的影响—字号,(a)不要用颜色区分,打印出来都一样了
3.3.3.2不同CNTs含量复合材料SEM分析
图3-16所示为纯HA和不同CNTs含量的CNTs/HA复合材料SEM照片。
由该图可见,烧结后复合材料中仍有CNTs的存在且在基体中均匀分布,并且随着复合材料中CNTs含量的增加,材料的气孔率明显增加,与之前的致密度测量结果相一致。
(描述不够充分,应当逐张图说明)
图3-16不同CNTs含量CNTs/HA块体材料的断口SEM
3..PureHA,(b)1%CNTs/HA,(c)2%CNTs/HA,(d)3%CNTs/HA
3.3.3.3不同CNTs含量复合材料抗弯强度
对不同CNTs含量的CNTs/HA复合材料进行了抗弯强度测试,结果如图3-17所示。
图3-17不同CNTs含量复合材料抗弯强度——字号,数据是否太高了?
从图3-17可以看出,随着CNTs的加入,复合材料的抗弯强度逐渐增加,CNTs起到了较好的补强作用,当CNTs含量达到2%时,复合材料的抗弯强度达到最大值;
之后,随后随CNTs含量增加,复合材料的抗弯强度急剧下降。
当CNTs含量达到3%时,复合材料的抗弯强度比纯HA材料还要低。
分析其原因可能在于复合材料中CNTs含量的增加严重阻碍了烧结过程中HA基体的致密化,导致复合材料的力学性能恶化。
3.3.4复合材料的增韧机理分析
目前,