2手工超声车轴探伤规程0301文档格式.docx
《2手工超声车轴探伤规程0301文档格式.docx》由会员分享,可在线阅读,更多相关《2手工超声车轴探伤规程0301文档格式.docx(68页珍藏版)》请在冰豆网上搜索。
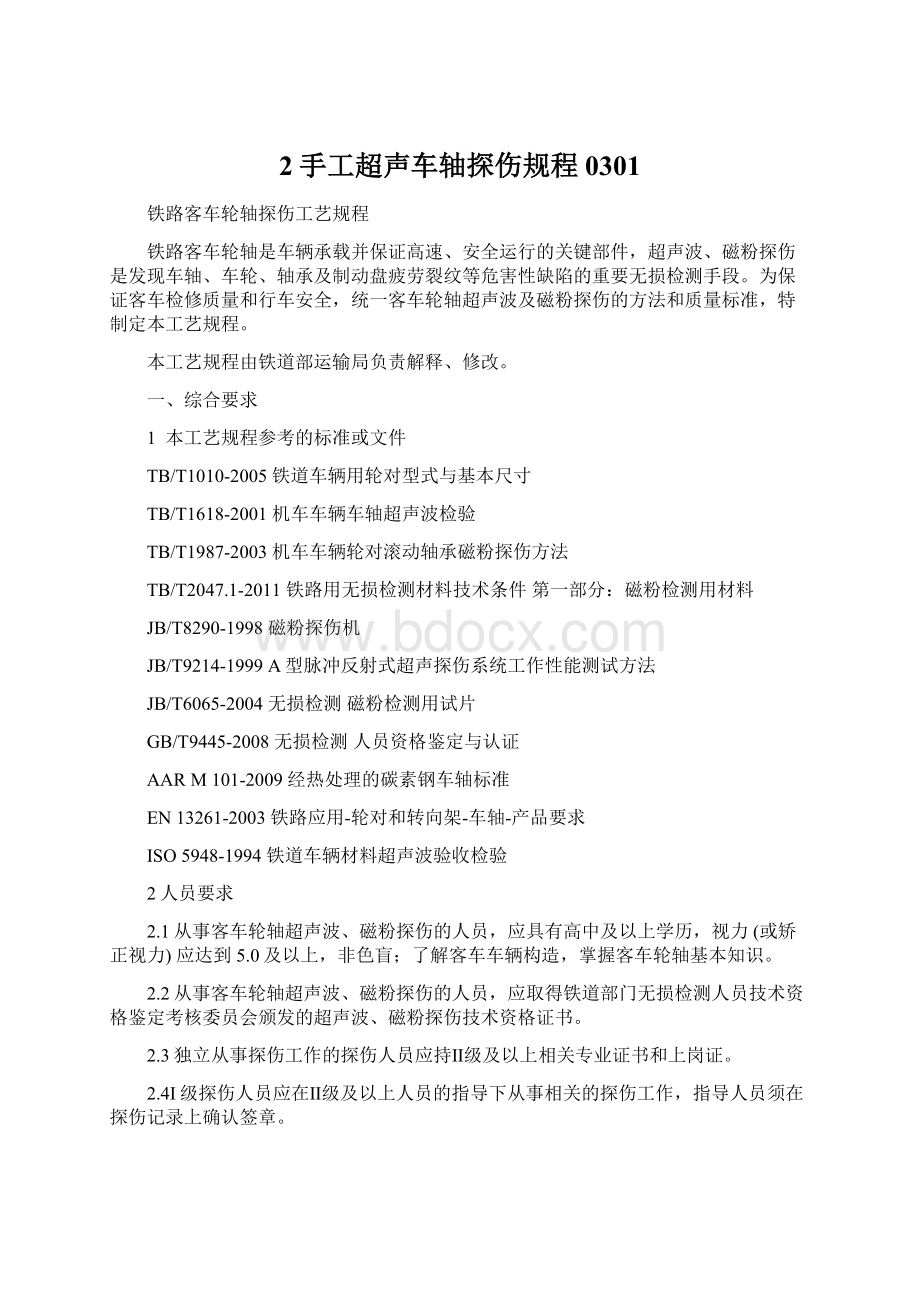
1.1本部分工艺适用于最高运行速度不大于200km/h的铁路客车RC3、RC4、RD3、RD4、RD10、RD13、RD3A、RD4A、RD3A1、RD3B、AM96型轮轴组装、厂(A4)修、段(A2、A3)修时轮轴(不退卸轴承或内圈)、轮对(退卸轴承或内圈)、车轴的超声波探伤检查。
1.2本部分工艺适用于超声A型脉冲反射法对铁路客车轮轴、轮对、车轴施行手工超声波探伤检查。
超声相控阵等其它检测方法可参照执行。
1.3本部分工艺规定了铁路客车轮轴、轮对、车轴超声波探伤的适用范围、检验规则、探伤设备及器材、性能校验、探伤方法、质量标准、探伤标识和记录等。
1.4其它型号的铁路客车轮轴、轮对、车轴的超声波探伤检查,可参照本部分工艺执行。
2检验规则
2.1新制车轴组装前须施行全轴超声波穿透探伤检查。
2.2轮对第一次组装时间达到或超过4年,或剩余组装质量保证期不足一个段(A2、A3)修期时,每次施行段(A2、A3)修及以上修程时,均须对轮对车轴施行全轴穿透检查,对轮座及制动盘座镶入部施行超声波探伤检查,如果轴承(或内圈)不退卸时还须对车轴轴颈根部(卸荷槽)进行超声波探伤检查。
2.3车辆颠覆或脱轨时,须对全车轮对施行全轴穿透检查、轮座及制动盘座镶入部超声波探伤检查。
2.4轮对组装后,须对轮座、制动盘座镶入部施行超声波探伤检查。
2.5建议加:
带轴承或内圈的轮轴,应采取二次作业方式,无论第一次是手工探伤还是微机自动探伤,第二次须手工探伤对探伤部位复探,两次探伤作业不得由一探伤人员完成
3探伤设备及器材
探伤仪器、探头和试块等重要器材,应通过铁道部组织的技术评审或生产质量认证,经验收合格后方可投入使用。
超声波探伤仪应按规定的周期进行检修。
属于计量器具的探伤检测设备须按规定进行计量检定。
3.1超声波探伤仪
3.1.1超声波探伤仪应具有如下技术指标
3.1.1.1衰减器控制总量≥80dB,在规定的工作频率范围内,每12dB误差不超过1dB;
3.1.1.2灵敏度余量≥46dB(2.5MHz钢中纵波);
3.1.1.3分辨力≥26dB(2.5MHz钢中纵波);
3.1.1.4动态范围≥26dB;
3.1.1.5垂直线性误差≤6%;
3.1.1.6水平线性误差≤1%;
3.1.1.7探测深度≥3m(2.5MHz钢中纵波);
3.1.1.8放大器带宽(相对3dB):
1MHz~8MHz。
3.1.2数字式超声波探伤仪还应具有如下功能
自检功能,探伤图形存储和回放功能,峰值搜索功能,距离-波幅曲线制作功能,零点自动校准或测距自动校准功能,探伤图形局部展宽功能,探伤工艺参数存储功能,探伤数据处理和探伤报告打印功能,仪器日常性能校验和季度性能检查功能,高速USB接口,采样频率≥80MHz。
3.2超声波探头
3.2.1探头型号
纵波直探头2.0P20Z、2.5P20Z
小角度纵波探头折射角14.5°
、16.5°
、20.0°
、25.8°
、27°
横波探头折射角45°
(K1.0)、50.2°
(K1.2)、52.4°
(K1.3)、54.5°
(K1.4)、
59.5°
(K1.7)
3.2.2中心回波频率及误差
3.2.2.1中心回波频率
小角度纵波探头4~5MHz,穿透检查探头2.0MHz或2.5MHz,其它探头2.5MHz。
3.2.2.2中心回波频率误差Δf/f≤15%
式中f—探头标称回波频率;
Δf—探头回波频率实测值与标称值之差;
3.2.3折射角(β)误差
横波探头β≤45°
时Δβ≤1.5°
横波探头β>
45°
时Δβ≤2°
小角度纵波探头Δβ≤2°
3.2.4分辨力
横波探头≥20dB
纵波直探头≥26dB
小角度纵波探头≥20dB
3.2.5灵敏度余量
横波探头≥60dB
纵波直探头≥46dB
小角度纵波探头≥50dB(DB-H1试块80mm深φ3mm横孔)
3.2.6声轴偏斜角
直探头≤1.0°
3.2.7从防尘板座上探测轮座镶入部的横波探头前沿距离≤12mm;
从AM96型轮轴轴身上探测轮座镶入部外侧的横波探头前沿距离≤12mm。
3.2.8建议加:
探测数量达到1000对轮对时,应对探头折射角(K值)、分辨力、灵敏度余量及入射点进行一次校核,任一值不合格时,探头应报废。
明确探头测试表格。
如
探头测试记录表
探伤编号
探头标定折射角
分辨力
灵敏度余量
探头入射点
备注
3.3试块
3.3.1标准试块主要为CSK-1A、TS-1(W)、TS-3、TZS-R(60、80)、CS-1-5、DB-H1等,示意图见附件1。
3.3.2半轴实物试块主要为RD3型、RD3A型、RD3A1型、RD3B型、RD10型、RD13型和AM96型,图样及技术要求见附件2。
3.4耦合剂
耦合剂可选用机油或铁路专用轴承脂。
校验探伤灵敏度和探伤作业时,应使用同一种耦合剂。
在轴端探测轮轴轴颈根部(卸荷槽)或轮座内、外侧时,应使用铁路专用轴承脂做耦合剂。
3.5工艺装备
3.5.1超声波探伤作业须配备稳压器和专用转轮器,转轮器转速应≤2r/min,并能随时控制转停。
3.5.2超声波探伤人员应配备带有函数运算功能的计算器及直尺、笔、卡尺等常用工具。
4性能校验
探伤仪器性能校验分为日常性能校验和季度性能检查。
4.1日常性能校验
4.1.1项目
检查探伤仪器的技术状态,校验探伤系统灵敏度。
4.1.2要求
每班开工时,应首先进行日常性能校验,由探伤工、探伤工长、质量检查员、验收员和设备维修工共同参加。
校验结束后应填写《铁路客车轮轴超声波探伤系统日常性能校验记录表》(车统—53K10),参加校验人员应确认校验记录内容并签章。
探伤仪器发生故障,检修后投入使用前应重新进行日常性能校验并做好记录。
日常性能校验时,系统探伤灵敏度(半轴实物试块1mm人工缺陷基准波高时的仪器dB值)须稳定,若相邻两次误差超过4dB,则应对仪器或探头性能重新检验。
4.2季度性能检查
4.2.1项目
4.2.1.1日常性能校验所规定的项目。
4.2.1.2半轴实物试块与TZS-R(60、80)型标准试块相对应的人工缺陷的差值(△CR)。
4.2.1.3超声波探伤系统技术状态及主要性能指标(水平线性、垂直线性、灵敏度余量、分辨力)。
测试时以仪器+直探头组成的系统为代表,直探头采用2.5P20Z。
4.2.2要求
每季度由单位主管检修(生产)领导组织,轮轴(探伤)专职、设备专职、验收员、质量检查员、探伤工长、探伤工和设备维修工共同参加,检查结束后应填写《铁路客车轮轴超声波探伤系统季度性能检查记录表》(车统—53K11),参加检查人员应确认检查记录内容并签章。
新购置及大、中、小修后的探伤仪器,第一次使用前应按季度性能检查的要求进行检查并做好记录。
5探伤方法
5.1全轴穿透检查
全轴穿透检查包括透声检查和大裂纹检查。
5.1.1透声检查
透声检查分为TS-1(W)法和TS-3法,推荐采用TS-3法。
5.1.1.1TS-1(W)法
5.1.1.1.1测距标定
将2.5P20Z探头放置在TS-1(W)标准试块B面上,调整仪器,使试块第1、第10次底面回波前沿分别对准荧光屏水平刻度的第1、第10大格,此时水平刻度的每1大格代表车轴实际长度240mm(如图2.1)。
图2.1直探头在TS-1(W)型试块上测距标定(请标注TS-1(W))
5.1.1.1.2灵敏度确定
在测距标定的基础上,调整仪器,使第10次底面回波高度达到荧光屏垂直刻度满幅的90%,增益6dB,耦合差另加0dB~4dB。
在此基础上再增益8dB~10dB【钢印(2dB~4dB)、中心孔(3dB)、螺栓孔(3dB)】,作为透声检查的灵敏度(如图2.2)。
图2.2直探头在TS-1(W)型试块上灵敏度确定(请标注TS-1(W))
5.1.1.1.3透声扫查
扫查时,转轮器轮对应停止转动。
探头均匀受力,以20mm/s~50mm/s的速度,分别在车轴两端面按图2.3所示的方式移动,同时观察回波的变化。
探头扫查范围应遍及轴端面的可移动区域。
图2.3直探头在轴端面的扫查方式
5.1.1.1.4透声检查时,不得改变调节后的透声灵敏度。
如发现底面回波与始波间有可疑回波出现,应进行危害性分析,即大裂纹扫查。
5.1.1.2TS-3法
5.1.1.2.1测距标定
将2.0P20Z探头放置在TS-3标准试块测试面上,调整仪器,使水平线性测量范围为2400mm,即试块第3、第6次底面回波前沿分别对准荧光屏水平刻度的第5、第10大格,此时水平刻度的每1大格代表车轴实际长度240mm(如图2.4)。
图2.4直探头在TS-3型试块上测距标定示意图
5.1.1.2.2灵敏度确定
适当改变水平线性测量范围,调节仪器,使TS-3标准试块φ3.2平底孔第1次回波高度达到荧光屏垂直刻度满幅的20%,如图2.5所示。
然后仅调节仪器水平测量范围,其他按钮禁止调节,回到测量范围为2400mm的状态,如图2.6所示。
在此基础上再增益8dB~10dB【钢印(2dB~4dB)、中心孔(3dB)、螺栓孔(3dB)】,再补偿TS-3试块与车轴端面粗糙度耦合差0dB~4dB。
注:
“钢印(2dB~4dB)”是指探头放置的位置无钢印,车轴另一端有钢印。
图2.5φ3.2平底孔第1次回波高度20%图2.6回到测量范围为2400mm
5.1.1.2.3透声扫查
a)透声扫查从车轴两端面分别进行,全端面扫查。
b)扫查时,转轮器轮对应停止转动。
5.1.1.2.4透声扫查时,不得改变调节后的透声灵敏度。
5.1.2大裂纹扫查
5.1.2.1大裂纹的定义
在透声检查的灵敏度基础上,直探头轴向探伤时所能发现的轴颈根部(卸荷槽)、轮座(盘座)镶入部和轴身部位的裂纹称为该部位的大裂纹,此时裂纹反射回波高度达到屏幕高度80%,信噪比10dB以上。
5.1.2.2大裂纹的发现能力示例
5.1.2.2.1轴颈根部(卸荷槽)部位大裂纹的发现能力见图2.7
(裂纹深度)
图2.7轴颈根部(裂纹距轴端面175mm)
5.1.2.2.2轮座镶入部外侧大裂纹的发现能力见图2.8
图2.8轮座镶入部外侧(距轴端面308mm)
5.1.2.2.3轮座镶入部内侧大裂纹的发现能力见图2.9
图2.9轮座镶入部内侧(裂纹距轴端面444mm)
5.1.3.2.4制动盘座镶入部外侧大裂纹的发现能力见图2.10
5.1.3.2.5制动盘座镶入部内侧大裂纹的发现能力见图2.11
5.1.3.2.6轴身中央部位大裂纹的发现能力见图2.12
图2.12轴身中央部位(裂纹距轴端面1073mm)
5.1.2.3大裂纹扫查
扫查时,只允许调节增益或衰减量,其它按钮键及参数均不得调整。
5.2轮对探伤
轮座或制动盘座镶入部横波探头探伤检查
5.2.1测距标定
将横波探头置于TZS-R型试块R面上,调节仪器,使下棱角和上棱角最高反射波的前沿分别对准荧光屏水平刻度的第2和第4大格(如图2.13、图2.14、图2.15),此时,水平刻度每1大格代表深度40mm,代表水平距离40×
Kmm。
图2.13横波探头K≤1.2时在TZS-R型标准试块上测距标定示意图
图2.14横波探头K>
1.2时在TZS-R型标准试块上测距标定示意图
图2.15横波探头在TZS-R型标准试块上测距标定波形示意图
5.2.2灵敏度确定
将探头置于相应的探测面上,调节仪器,使半轴试块轮座(制动盘座)上深度为1.0mm的人工缺陷最高反射波幅度达到荧光屏垂直刻度满幅的80%(见图2.16),然后轮座外侧增益6dB,轮座内侧和制动盘座增益9dB,耦合差增益(0~4)dB,再补偿半轴实物试块与TZS-R标准试块相对应的人工缺陷的dB差值(△CR)(K1.7横波探头△CR=0),以此作为横波探伤灵敏度。
探测RD3A、RD4A、RD3A1、RD3B和AM96(退卸轴承)型轮对轮座镶入部中央区域的K1.7横波探头调节灵敏度时,以半轴实物试块轮座镶入部外侧人工缺陷为准。
图2.16横波探头在半轴试块上灵敏度确定位置和波形示意图(有何意义?
)
5.2.3扫查
5.2.3.1确定探伤灵敏度后,实际探测轮对时,只允许调节增益或衰减值,其它按键及参数均不得调整。
5.2.3.2扫查时如提高探伤灵敏度,发现缺陷后,灵敏度应恢复到规定的探伤灵敏度,再对缺陷进行判定。
5.2.3.3扫查时探头移动区域须保证探头主声束扫查区域之和不小于轮座(制动盘座)镶入部全长。
5.2.3.4扫查时探头指向镶入部,沿轴向前后移动,同时沿车轴圆周方向转动,探头均匀受力,探头移动速度为20mm/s~50mm/s。
探头位置及移动方式如图2.17、图2.18、图2.19所示。
图2.17RC3、RC4、RD3、RD4、RD10、RD13型轮座镶入部扫查示意图
图2.18RD3A、RD4A、RD3A1、AM96型轮座和制动盘座镶入部扫查示意图
图2.19RD3B型轮对轮座和制动盘座镶入部扫查示意图
5.2.4轮对型号与探头型号、探头移动及探测范围
表2.1轮对型号与探头型号、探头移动和探测范围表
轮对型号
探头型号
探测面
探测部位
探头移动
起始位置
移动
范围
探测
各型
2.0P20Z
轴端面
全轴穿透
TS-3法
2.5P20Z
TS-1(W)法
RC3
RC4
K1.0
轴身
轮座镶入部内侧
轮座后肩
48~168
0~120
K1.2
轴颈
轮座镶入部外侧
轴颈后肩
37~115
轮座前肩
0~78
RD3
RD4
60~184
0~124
42~116
0~74
RD13
K1.2
68~221
0~153
43~116
0~73
RD10
56~221
0~165
RD3A
RD4A
K1.3
防尘板座
48~73
0~25
K1.7
轮座镶入部中央
37~118
79~160
37~116
0~79
制动盘座镶入部
盘座后肩
62~242
0~180
盘座修改前
98~242
0~144
盘座修改后
RD3A1
45~93
0~48
43~130
53~140
43~96
0~53
87~242
0~155
RD3B
K1.4
43~83
0~40
43~138
73~168
两侧制动盘座镶入部
86~241
中间制动盘座镶入部
盘座前、后肩
164~241.5
0~77.5
AM96
42~63
0~21
46~115
75~144
46~121
0~75
72~216
轮对探伤时,探头实际的移动范围以主声束覆盖轮座(制动盘座)镶入部全长即可。
5.2.5各种探头的探测面和探测部位如图2.20~图2.27
图2.20RC3(RC4)探测部位示意图
图2.21RD3(RD4)探测部位示意图
图2.22RD13探测部位示意图
图2.23RD10探测部位示意图
a.制动盘座修改前
b.制动盘座修改后
图2.24RD3A(RD4A)探测部位示意图
图2.25RD3A1探测部位示意图
图2.26RD3B探测部位示意图
图2.27AM96探测部位示意图
5.3轮轴探伤
5.3.1轮座(制动盘座)镶入部横波探头探伤检查
5.3.1.1测距标定
同5.2.1条。
5.3.1.2灵敏度确定
将探头置于相应的探测面上,调节仪器,使半轴试块轮座(制动盘座)上深度为1.0mm的人工缺陷最高反射波幅度达到荧光屏垂直刻度满幅的80%(见图2.28),然后增益9dB,耦合差增益(0~4)dB,再补偿半轴实物试块与TZS-R标准试块相对应的人工缺陷的dB差值(△CR),以此作为横波探伤灵敏度。
图2.28横波探头在半轴试块上灵敏度确定位置和波形示意图
5.3.1.3扫查
5.3.1.3.1确定探伤灵敏度后,实际探测轮轴时,只允许调节增益或衰减值,其它按键及参数均不得调整。
5.3.1.3.2扫查时如提高探伤灵敏度,发现缺陷后,灵敏度应恢复到规定的探伤灵敏度,再对缺陷进行判定。
5.3.1.3.3扫查时探头移动区域须保证探头主声束扫查区域之和不小于轮座(制动盘座)镶入部全长。
5.3.1.3.4扫查时探头指向镶入部,沿轴向前后移动,同时沿车轴圆周方向转动,探头均匀受力,探头移动速度为20mm/s~50mm/s。
探头位置及移动方式如图2.29、图2.30、图2.31所示。
图2.29RC3、RC4、RD3、RD4、RD10、RD13型轮座镶入部扫查示意图
图2.30AM96轮座和制动盘座镶入部扫查示意图
图2.31RD3B轮对轮座和制动盘座镶入部扫查示意图
5.3.1.4轮轴型号与探头型号、探头移动和探测范围
表2.2横波探测轮座和盘座时,轮轴型号与探头型号、探头移动和探测范围表
轮轴型号
RC3、RC4
42~120
RD3、RD4
65~139
RD13、RD10
65~221
0~156
65~107
156~198
两侧盘座镶入部
0~1