制造技术基础综合实践课程设计齿轮Word文件下载.docx
《制造技术基础综合实践课程设计齿轮Word文件下载.docx》由会员分享,可在线阅读,更多相关《制造技术基础综合实践课程设计齿轮Word文件下载.docx(16页珍藏版)》请在冰豆网上搜索。
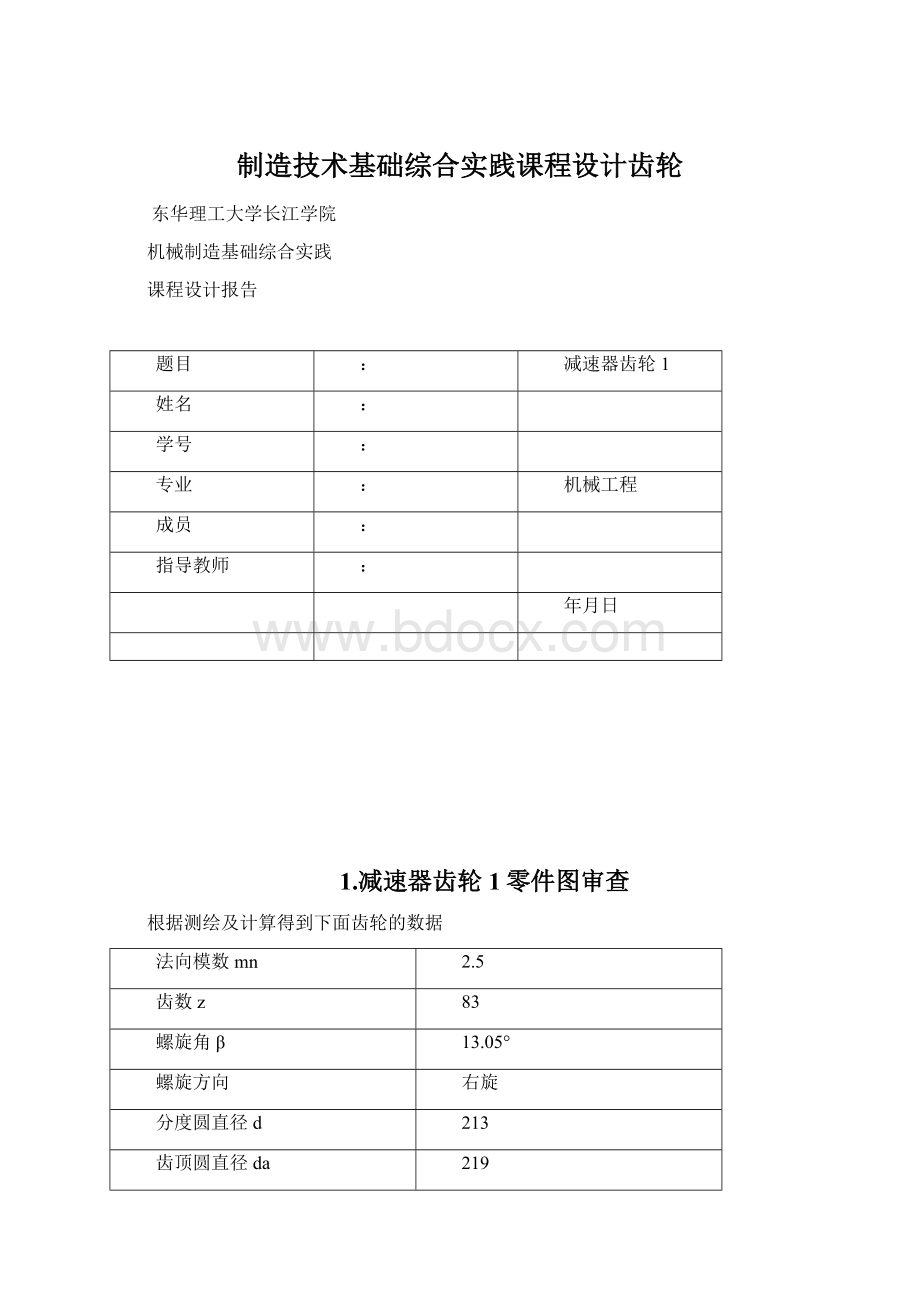
键长l
40
键宽b
14
键高h
9
2.减速器齿轮1零件的结构分析
(1)齿轮机构的优点有:
1)齿轮机构传别可达100000kw、300m/s。
2)齿轮机构的传动比恒定,寿命长,工作可递的功率和圆周速度分靠性高。
3)齿轮机构能够实现平行轴和不平行轴之间的传动。
(2)齿轮机构的缺点有:
1)齿轮机构得制造成本过高。
2)齿轮机构不适用于远距离的传动。
3)低精度齿轮会产生有害的冲击,噪音和振动。
3.减速器齿轮1零件的工艺分析
为了便于我们了解齿轮加工,下面我们对齿轮加工的方法进行一个简单的探讨。
齿轮加工的关键是齿面加工。
目前,齿面加工的主要方法是刀具切削加工和砂轮磨削加工。
前者由于加工效率高,加工精度较高,因而是目前广泛采用的齿面加工方法。
后者主要用于齿面的精加工,效率一般比较低。
按照加工原理,可分为成形法和展成法两大类。
一般情况下:
a.加工直齿圆柱齿轮用插齿机b.加工斜齿轮用滚齿机c.加工伞齿轮用刨齿机
(滚齿机也可以加工斜齿轮)所选用的刀具由齿轮加工机床决定:
a.滚齿机有专用的齿轮滚刀b插齿机有专用的齿轮插刀c.刨齿机有转用的齿轮刨刀以上刀具都是标准件,可以在刀具书中选型(根据模数)齿轮轴的加工一般用滚齿机就可以加工,选用相应模数的齿轮滚刀,不需要专门的夹具就可以加工。
成形法
成形法是采用与被切齿轮齿槽相符的成形刀具加工齿形的方法。
用齿轮铣刀在铣床上加工齿轮是常用的成形法加工。
(1)齿轮铣刀的选择
铣刀应选择与被加工齿轮模数、压力角相等的铣刀。
同时按齿轮齿数根据下页表选择合适号数的铣刀。
刀号
1
2
3
4
5
8
加工齿数范围
12-13
14-16
17-20
21-25
26-34
35-54
55—134
135以上及齿条
(2)铣削方法
我们在铣削的过程中,在卧式铣床上应将齿坯套在心轴上安装于分度头和尾架顶尖中,对刀并调好铣削深度后开始铣第一个槽,铣完一齿退出进行分度,依次逐个完成齿数的铣削。
(3)铣齿加工特点
1)用普通的铣床设备,且刀具成本低。
2)生产效率低。
每切完一齿要进行分度,占用较多的辅助时间。
3)齿轮精度低。
齿形精度只达11-9级。
以上主要原因是每号铣刀的刀齿轮廓只与该范围最少齿槽相吻合,而此号齿轮铣刀加工同组的其它齿数的齿轮齿形都有一定的误差。
展成法
展成法就是利用齿轮刀具与被切齿坯作啮合运动而切出齿形的方法。
主要有以下分类:
(1)插齿加工
插齿加工在插齿机上进行,是相当于一个齿轮的插齿刀与齿坯按一对齿轮作啮合运动而把齿形切成的。
可把插齿过程分解为:
插齿刀先在齿坯上切下一小片材料,然后插齿刀退回并转过一小角度,齿坯也同时转过相应角度。
之后,插齿刀又下插在齿坯上切下一小片材料。
不断重复上述过程。
就是这样,整个齿槽被一刀刀地切出,齿形则被逐渐地包络而成。
因此,一把插齿刀,可加工相同模数而齿数不同的齿形,不存在理论误差。
插齿有以下切削运动:
主运动
插齿刀的上下往复运动
展成运动
确保插齿刀与齿坯的啮合关系的运动
圆周进给运动
插齿刀的转动,其控制着每次插齿刀的切削量
径向进给量
插齿刀须作径向逐渐切入运动,以便切出全齿深。
让刀运动
插齿刀回程向上时,为避免与工件摩擦而使插齿刀让开一定距离的运动
插齿除适于加工直齿圆柱齿轮外,特别适合加工多联齿轮及内齿轮。
插齿加工精度一般为7-8级。
齿面粗糙度Ra值为1.6μm。
(2)滚齿加工
滚齿是目前应用最广的切齿方法,滚齿加工原理是滚齿刀和齿坯模拟一对螺旋齿轮作啮合运动。
滚齿刀好比一个齿数很少(一至二齿)齿很长的齿轮,形似蜗杆,经刃磨后形成一排排齿条刀齿。
因此,可把滚齿看成是齿条刀对齿坯的加工。
这种方法可用一把滚齿刀加工相同模数不同齿数的齿轮。
不存在理论齿形误差。
滚齿精度一般为7~9级,当采用高精度滚刀和滚齿机时,可滚切5级精度的齿轮。
滚齿时,产生齿轮的基节偏差较小,而齿形误差通常较大。
滚切直齿圆柱齿轮时有以下运动:
1)主运动滚刀的旋转运动。
2)展成运动是保证滚齿刀和被切齿轮的转速必须符合所模拟的一对齿轮的啮合运动关系。
即滚刀转一转,工件转K/Z转。
其中:
K是滚刀的头数,Z为齿轮齿数。
3)垂直进给运动要切出齿轮的全齿宽,滚刀须沿工件轴向作垂直进给运动
滚齿加工适于加工直齿、斜齿圆柱齿轮。
齿轮加工精度为8-7级,齿面粗糙度Ra值为1.6μm。
在滚齿机上用蜗轮滚刀、链轮滚刀还能滚切蜗轮和链轮。
(3)剃齿加工
剃齿是用剃齿刀对齿轮的齿面进行精加工的方法。
加工原理:
剃齿时刀具与工件作一种自由啮合的展成运动。
安装时,剃齿刀与工件轴线倾斜一个剃齿刀螺旋角β。
剃齿刀的圆周速度可以分解为沿工件齿向的切向速度和沿工件齿面的法向速度,从而带动工件旋转和轴向运动,使刀具在工件表面上剃下一层极薄的切屑。
同时,工作台带动工件作往复运动,以剃削轮齿的全长。
(4)珩齿加工
珩齿特点:
珩齿的加工原理与剃齿相同,表面粗糙Ra0.4~0.2μm。
主要作用是降低齿面粗糙度,生产率高,一般用于大批量加工8~6级精度的淬火齿轮。
(5)磨齿加工
磨齿是获得高精度齿轮最有效和可靠的方法,既可磨削不淬火的齿轮,又可磨削淬火的齿轮。
加工精度可达6~4级,Ra0.4~0.2μm。
⊙磨孔
对于淬硬零件中的孔加工,磨孔是主要的加工方法。
内孔为断续圆周表面(如有键槽或花键的孔)、阶梯孔及盲孔时,常采用磨孔作为精加工。
磨孔时砂轮的尺寸受被加工孔径尺寸的限制,一般砂轮直径为工件孔径的0.5~0.9倍,磨头轴的直径和长度也取决于被加工孔的直径和深度。
故磨削速度低,磨头的刚度差,磨削质量和生产率均受到影响。
磨孔的方式有中心内圆磨削、无心内圆磨削。
中心内圆磨削是在普通内圆磨床或万能磨床上进行。
无心内圆磨削是在无心内圆磨床上进行的,被加工工件多为薄壁件,不宜用夹盘夹紧,工件的内外圆同轴度要求较高。
这种磨削方法多用于磨削轴承环类型的零件,其工艺特点是精度高,要求机床具有高精度、高的自动化程度和高的生产率,以适应大批大量生产。
由于内圆磨削的工作条件必外圆磨削差,故内圆磨削有如下特点:
1)磨孔用的砂轮直径受到工件孔径的限制。
约为孔径的0.5~9倍,砂轮直径小则磨耗快,因此经常需要修整和更换,增加了辅助时间。
2)由于选择直径较小的砂轮,磨削时要达到砂轮圆周速度25--30m/s是很困难的。
因此,磨削速度比外圆磨削速度低的多,故孔的表面质量较低,生产效率也不高。
近些年来已制成有100000r/min的风动磨头,以便磨削1~2mm直径的孔。
3)砂轮轴的直径受到孔径和长度的限制,又是悬臂安装,故刚性差,容易弯曲和变形,产生内圆磨削砂轮轴的偏移,从而影响加工精度和表面质量。
4)砂轮与孔的接触面积大,单位面积压力小,砂粒不易脱落,砂轮显得硬,工件易发生烧伤,故应选用较软的砂轮。
5)切削液不易进入磨削区,排屑较困难,磨屑易积集在磨粒间的空隙中,容易堵塞砂轮,影响砂轮的切削性能。
6)磨削时,砂轮与孔的接触长度经常改变。
当砂轮有一部分超出孔外时,其接触长度较短,切削力较小,砂轮主轴所产生的压移量比磨削孔的中部时为小,此时被磨去的金属层较多,从而形成“喇叭口”。
为了减小或消除其误差,加工时应控制砂轮超出孔外的长度不大于1/2~1/3砂轮宽度。
内圆磨削精度可达IT7,表面粗糙度可达
。
(6)齿轮加工的其它方法
滚制:
齿轮的滚制加工有利用成形法与展成法。
利用展成法的滚制是利用齿条与小齿轮、小齿轮与大齿轮、内齿轮与小齿轮的啮合;
将淬火硬化的齿条形工具、小齿轮形工具、内齿轮形工具按压于齿轮轮坯,使轮坯滚动,借塑性变形加工成齿形。
利用成形法的滚制是用对应于滚制齿轮的齿轮形状的成形滚制刀具,藉特殊的滚轧加工成形齿形。
热间锻造:
热间锻造的主要对象为直齿伞齿轮、螺旋伞齿轮及正齿轮,通常为以非铁合金为材料的齿轮,可不计加热之际发生的氧化皮时,热间锻造的精度及表面粗糙度不亚于机械加工。
高速锻造:
1957年由美国GeneralDynamics公司开发
冷间锻造:
主要有利用锻粗或锻头法扩大齿坯尺寸的成形与减少齿坯断面的挤出成形。
冲剪:
玩具等不大要求精度的小型板齿轮常用冲剪法作成。
普通铸造:
超大型齿轮不得不用铸造放来加工。
直接将熔融的金属注入铸模中,凝固后取出,直接使用或机械加工后使用。
精密铸造法:
有毂模法、石膏模法等。
还有粉末冶金法、射出成形法等齿轮加工方法
齿形加工方法比较
⑴、滚齿、插齿与铣齿比较
铣齿采用普通设备和简单刀具即可加工齿形。
但是只能加工11~9级精度、齿面粗糙度Ra值为6.3μm~3.2μm的齿形。
滚齿和插齿的分度精度和齿形精度均较铣齿高,可以加工6级精度、齿面粗糙度值Ra为3.2μm~1.6μm;
滚齿和插齿是连续分度和切削,生产效率比铣齿高。
用同一模数的滚到和插齿刀,可以各种不同齿数的齿轮,大大减少了刀具数目,提高了经济效益。
⑵、滚齿与插齿比较
滚齿是刀齿作连续的旋转切削、切削速度较高,插齿是刃齿作往复运动,限制了切削速度,故滚齿生产率比插齿烙高,滚齿机可以加工直齿、斜齿圆柱齿轮和蜗轮,但不能加工内齿轮和相距太近的多联齿轮;
插齿时播齿刀沿齿全长连续切出,包络线数量也多,而滚齿时轮齿全长是由滚刀多次连续切出,故插齿的齿面粗糙度值较小;
插齿刀的制造、刃磨检验壁滚刀方便,易得到高精度,但插齿机分齿传动链比滚齿复杂,因此,加工齿轮的精度基本一样;
插齿机可以加工内齿轮和多联齿轮,但不能加工蜗轮。
4.毛坯的选择
对齿轮材料的基本要求是:
应使齿面具有足够的硬度和耐磨性,齿心具有足够的韧性,以防止齿面的各种失效,同时应具有良好的冷、热加工的工艺性,以达到齿轮的各种技术要求。
可以知道的是,常用的齿轮材料为各种牌号的优质碳素结构钢、合金结构钢、铸钢、铸铁和非金属材料等。
一般多采用锻件或轧制钢材。
当齿轮结构尺寸较大,轮坯不易锻造时,可采用铸钢。
开式低速传动时,可采用灰铸铁或球墨铸铁。
低速重载的齿轮易产生齿面塑性变形,轮齿也易折断,宜选用综合性能较好的钢材。
高速齿轮易产生齿面点蚀,宜选用齿面硬度高的材料。
受冲击载荷的齿轮,宜选用韧性好的材料。
对高速、轻载而又要求低噪声的齿轮传动,也可采用非金属材料、如夹布胶木、尼龙等。
5.定位基准的选择
定位基准有粗基准和精基准。
粗基准的选择有两个出发点:
一是保证各表面有足够且均匀的加工余量;
二是保证不加工表面与加工表面间的尺寸和位置符合设计要求。
精基准的选择主要考虑以下几个方面:
一是尽可能选择用设计基准或工序基准作为定位基准:
二是尽可能选用同一组定位基准加工各个表面,即遵守“基准统一”原则:
三是应保证工件的装夹稳定可靠,机床夹具结构简单,工件装夹操作方便。
根据上述基准的选择原则,粗基准用未加工过的毛坯表面做基准,精基准用以加工过的表面做基准。
具体基准的选择如下:
1粗车小端面以大端外圆轴线作为基准加紧,以大端端面作为轴向的定位基准
2粗车大端面以大端外圆轴线作为基准加紧,以小端端面作为轴向的定位基准
3粗车内孔时以大端外圆轴线作为基准加紧,以大端外圆轴线作为定位基准
4精车与粗车的基准选择一致
5滚齿和插齿时以内孔轴线作为定位基准,小端端面作为基准加紧
6磨削内孔及端面止口时以大齿分度圆圆心作为定位基准,大端面做基准夹紧
6.加工阶段的划分
⑴、热处理:
调质、渗碳淬火、齿面高频感应加热淬火等;
⑵、齿轮毛坯的形成:
锻件、棒料或铸件;
⑶、粗加工:
切除较多的余量;
⑷、半精加工:
车、滚、插齿;
⑸、精加工:
精修基准、精加工齿形
7.确定工序的集中与分散
工序集中:
把加工内容集中在一个工序,一台设备上进行,工序集中便于提高生产率,减少装夹次数,便于保证各加工表面之间的形状位置公差,有利于组织生产和计划工作。
为保证每一道工序所保证的工序尺寸,有时需将一个大的工序拆分成几个小工序。
在上述工艺路线
粗车可以归为一类在数控车床S3-242上加工,精车可以归为一起在数控车床S3-242上加工。
总之,对于第五速齿轮的加工可以分以上几个阶段进行不同工位的加工。
8.热处理与辅助工序的安排
热处理:
应考虑齿轮尺寸大小,毛坯成型方法及热处理和制造工艺;
钢制软齿面齿轮,其配对两轮齿面的硬度差应保持在30~50HBS或更多。
1、表面淬火
一般用于中碳钢和中碳合金钢,如45、40Cr等,表面淬火后轮齿变形小,不可磨齿,硬度可达52~56HRC,面硬芯软,能承受一定冲击载荷。
2、渗碳淬火
渗碳钢为含碳量0.15~0.25%的低碳钢和地碳合金钢,如20、20C等。
齿面硬度达到56~62HRC,齿面接触强度高,耐磨性好,齿芯韧性高,常用于受冲击载荷的重要传动。
通常渗碳淬火或要磨齿。
3、调质
调质一般用于中碳钢和中碳合金钢,如45、45C、35SiMn等。
调质处理后齿面硬度为:
220~260HBS。
因为硬度不高,故可在热处理后精切齿形,且在使用中易于跑合。
4、正火
正火能消除内应力、细化晶粒、改善力学性能和切削性能。
机械强度要求不高的齿轮可用中碳钢正火处理。
大直径的齿轮可用铸钢正火处理。
5、渗氮
渗氮是一种化学处理。
渗氮后齿面硬度可达60~62HBC。
氮化处理温度低,轮齿变形小,适用于难以磨齿的场合,如内齿轮。
特点及应用:
调质、正火处理后的硬度低,HBS
350,属于软齿面,工艺简单,用于一般传动。
当大小齿轮都是软齿面时。
因小轮齿很薄,弯曲强度低,故在选材和热处理时,小轮比大轮硬度高20~50HBS。
表面淬火、渗碳淬火、渗氮处理后齿面硬度高,属硬齿面。
其承载能力高,但一般需要磨齿。
常用于结构紧凑的场合。
所以为制造方便,才用软吃面,大小齿轮均用45钢,小齿轮调制处理,吃面硬度:
229~286HBS,大齿轮正火处理,吃面硬度:
169~217HBS。
9.减速器齿轮1零件加工工艺路线
材料为40Cr,精度为7-6-6级,其加工工艺过程见从表中可见,齿轮加工工艺过程大致要经过如下几个阶段:
毛坯热处理、齿坯加工、齿形加工、齿端加工、齿面热处理、精基准修正及齿形精加工等。
模数
基节偏差
±
0.016
齿数
齿形公差
0.017
精度等级
7GK
齿向公差
公法线长度变动量
0.039
公法线平均长度
21.360-0.05
齿圈径向跳动
0.050
跨齿数
工艺过程
序号
工序名称
工序内容及要求
锻造毛坯
正火
检查
车序
⑴粗车小端外圆、端面、内孔、倒角粗车小端外圆至φ222mm,表面粗度Ra=6.3粗车端端面端面至52mm,表面粗度Ra=6.3粗车内孔至φ50mm车倒角2×
45°
精车大端外圆、端面、端面止口、内孔、倒角
(2)半精车内孔至φ220mm,表面粗糙度Ra=3.2车倒角,2×
(3)精车小端外圆、端面、车端面空刀槽、倒角精车小端外圆至φ219.5mm,表面粗度Ra=3.2精车小端端面至50mm,表面粗糙度Ra=3.2精车车止口至50.5mm,表面粗糙度Ra=1.6车倒角,1×
、2×
中间检查
插齿
精车大端外圆φ219mm,表面粗糙度Ra=3.2精车大端端面至50mm,表面粗糙度Ra=3.2精车止口端面至φ050mm,表面粗糙度Ra=1.6精车内孔至φ50.0030mm,表面粗糙度Ra=1.6车倒角,2×
滚齿
倒棱
10
铣键槽
插接合齿z=83
11
钻孔
滚斜齿z=83
12
倒z=83斜齿两端锐角
13
热处理
铣键槽宽14mm深9mm
钻油孔均布3-φ42
15
挤光
16
磨内孔
渗碳淬火
17
磨端面
18
磨齿
挤斜齿Z=83
A19
垳齿
磨内孔至42mm,表面粗糙度Ra=0.4
20
磨端面至H=7mm,表面粗糙度Ra=0.8
21
磷化处理
磨Z=83斜齿,表面粗糙度Ra=0.8mm磨齿端面磨齿端面保证H=7mm
22
最终检查
加工的第一阶段是齿坯最初进入机械加工的阶段。
由于齿轮的传动精度主要决定于齿形精度和齿距分布均匀性,而这与切齿时采用的定位基准(孔和端面)的精度有着直接的关系,所以,这个阶段主要是为下一阶段加工齿形准备精基准,使齿的内孔和端面的精度基本达到规定的技术要求。
在这个阶段中除了加工出基准外,对于齿形以外的次要表面的加工,也应尽量在这一阶段的后期加以完成。
第二阶段是齿形的加工。
对于不需要淬火的齿轮,一般来说这个阶段也就是齿轮的最后加工阶段,经过这个阶段就应当加工出完全符合图样要求的齿轮来。
对于需要淬硬的齿轮,必须在这个阶段中加工出能满足齿形的最后精加工所要求的齿形精度,所以这个阶段的加工是保证齿轮加工精度的关键阶段。
应予以特别注意。
加工的第三阶段是热处理阶段。
在这个阶段中主要对齿面的淬火处理,使齿面达到规定的硬度要求。
加工的最后阶段是齿形的精加工阶段。
这个阶段的目的,在于修正齿轮经过淬火后所引起的齿形变形,进一步提高齿形精度和降低表面粗糙度,使之达到最终的精度要求。
在这个阶段中首先应对定位基准面(孔和端面)进行修整,因淬火以后齿轮的内孔和端面均会产生变形,如果在淬火后直接采用这样的孔和端面作为基准进行齿形精加工,是很难达到齿轮精度的要求的。
以修整过的基准面定位进行齿形精加工,可以使定位准确可靠,余量分布也比较均匀,以便达到精加工的目的。
10、确定各工序所需的机床和工艺装备
所需的机床和工艺装备
锻造床
车床
精车车床
插齿机
滚齿机
铣床
钻床
专用磨床
普通磨床
设备
11、减速器齿轮1零件加工工艺过程卡片
基面
外圆及端面
⑴粗车小端外圆、端面、内孔、倒角粗车小端外圆至φ222mm,表面粗度Ra=6.3粗车端端面端面至52mm,表面粗度Ra=6.3粗车内孔至φ50mm车倒角2×
(3)精车小端外圆、端面、车端面空刀槽、倒角精车小端外圆至φ219.5mm,表面粗度Ra=3.2精车小端端面至50mm,表面粗糙度Ra=3.2精车车止口至50.5mm,表面粗糙度Ra=1.6车倒角,1×
粗加工:
外圆及端面
精加工:
内孔及端面
外圆及A端面
內孔及A端面
内孔
内孔及A端面
桁Z=83齿
12、心得体会
首先很感谢饶江华老师在这一个拜给予我的支持和帮助。
虽然课程设计就只有短短的25页,但是在制作她的过程中,我学到了以前没有了解的知识;
也可以说,我把大学学到的一些知识进行了一个巩固和深入探讨。
课程设计完全是出于我们自己的选择,我要好好地感谢学院给了我这个自由,虽然用这个自由却没有换来相应的成功,但我们自己切身去做了我们希望做的事情,并给我们以后将要走的路作了必要的铺垫,对我来说,这已经是成功在向我们招手了。
最后,用一句话来结束我的毕业设计。
“提出一个问题往往比解决一个问题更重要,因为解决问题也许仅是一个数学上或实验上的技能而已。
而提出新的问题、新的可能性,从新的角度去看旧的问题,都需要有创造性的想象力,而且标志着科学的真正进步。
”
13、参考文献
[1]
付春生,张克义.机械制图.北京航空航天大学出版社
[2]
上海金属切削技术协会.金属切削手册[M].上海:
上海科学技术出版社,2004.
[3]
李洪.机械加工工艺手册[M].北京:
机械工业出版社,1990.
[4]
卢秉恒.机械制造技术基础
第3版[M].北京:
机械工业出版社,2009.
[5]
王光斗,王春福.机床夹具设计手册[M].上海科学技术出版社,2000.
[6]
关慧贞.机械制造装备设计
机械工业出版社,2009.
[7]
吴宗泽.机械设计实用手册[M].北京:
化学工业出版社,2000.
[8]
刘文剑,曹天河,赵维.夹具工程师手册[M].哈尔滨:
黑龙江科学技术出版社,1987.
[9]
上海科学技术出版社,1984.
[10]
周瑞强,陈桂平.机械原理.西北工业出版社
[11]
黄如林.切削加工简明实