质量管理课程设计报告Word文件下载.docx
《质量管理课程设计报告Word文件下载.docx》由会员分享,可在线阅读,更多相关《质量管理课程设计报告Word文件下载.docx(44页珍藏版)》请在冰豆网上搜索。
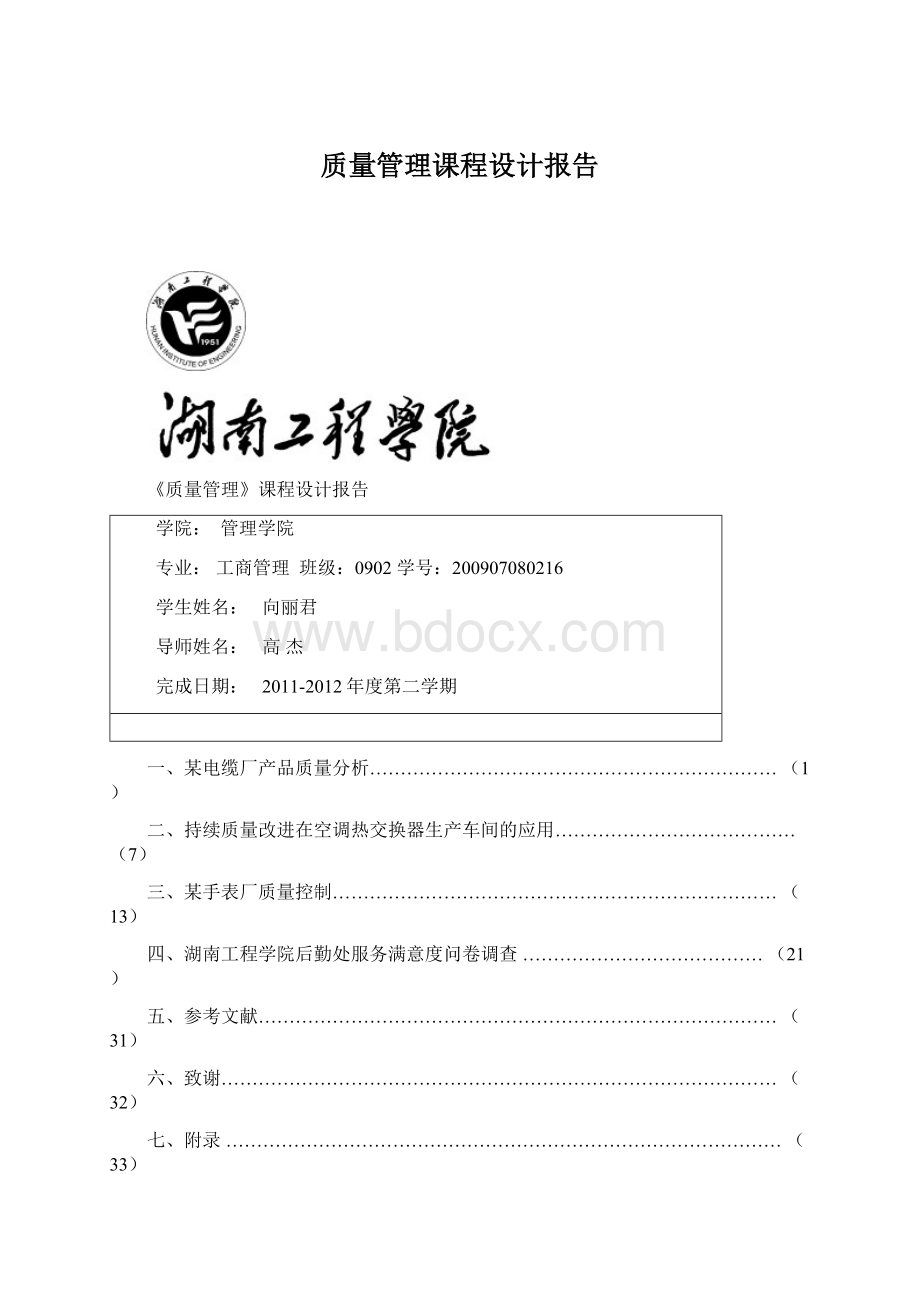
硫化
塑胶
挤橡
其它
不合格数
7
15
20
55
3
注:
试电、编织、过油、包装各工序的不合格率极小,故全部合并为“其他”一项。
请运用所学的QM方法进行分析,找出造成质量不稳定、废品率高的主要质量问题。
2.分析主要质量问题产生的原因
通过上述分析得知,主要质量问题是“挤橡”。
即“挤橡”工序是造成电线质量不稳定的关键工序。
针对这一情况,课题组召开质量分析会,就挤橡工序通过因果图进行详细分析,图1所示。
经过因果图分析,明确了影响挤橡工序质量的各种原因。
并且经现场测试验证后,对相对影响大的原因:
①混合胶质量差,②内外模对不好,采取了相应的措施,保证其处于正常稳定状态。
3.分析关键工序“挤橡”的生产稳定情况
在第“2”步的分析中,虽然明确了影响挤橡工序质量的各种原因,但并不了解挤橡工序质量的现状。
因此,从工序中随机抽取了20组100个数据(挤橡工序的质量特性是挤橡厚度,标准为(1±
0.1)mm),如表2所示:
表2测量单位:
0.01
组号
x1
x2
x3
x4
x5
1
0.96
1.04
1.08
11
0.92
1.02
1.0
1.06
2
0.94
0.98
12
0.93
13
4
14
5
6
16
17
8
18
9
19
0.95
10
4.分析关键工序“挤橡”的工序能力
通过第“3”步的分析,可以看出直方图形状为两边低中间高,左右基本对称,没有明显的“失稳”情况,说明工序处于稳定状态。
但其工序能力是否满足技术要求呢?
满足的程度如何?
请进一步分析工序能力,并计算工序不合格品率?
经计算工序能力指数
可知挤橡工序的工序能力不足。
针对这一情况,请你提出提高工序能力的思路和措施(请查阅相关资料)。
课程组在采纳你提出的措施的基础上,又采取了“三自,一控”的质量控制方法(见表3)
表3
序号
检查内容
执行标准
采用手段
操作者检查自己的产品
按工艺规范和标准
卡尺
区分合格品与不合格品
自己做好加工者,日期,质量标记
自己定标记,记录
自检记录表
操作者要控制自检正确率
自检正确率=(专检合格数/自检合格数)×
100%
每天统计
操作者要求自检正确
认真自检
上述措施实施一段时间后,为了验证其是否有效,随机抽检产品,取得100个数据,如表4所示。
表4
5.设计控制图,进行工序的日常控制
为了巩固采取措施的成果,使得工序长期处于稳定的控制状态,课题组决定利用控制图进行日常工序质量控制。
请你依据前述资料,针对挤橡工序设计
-R控制图。
要确认所设计的控制图能够起到控制作用!
同时,为“挤橡”工序的操作人员提供控制图的使用说明。
(二)要求
1.用Minitab软件画排列图,寻找造成质量不稳定、废品率高的主要质量问题
2.试通过表2用Minitab软件作直方图分析挤橡工序质量的稳定情况(包括图形的分析、工序能力的计算和分析)。
3.试通过表4,核算工序能力指数,计算工序不合格率,来评价采取措施后的工序质量状态。
4.谈谈利用控制图对生产过程进行日常控制的重要意义。
(三)设计过程
1.运用用minitab软件画出排列图(见图2)
图2不合格项目排列图
据上图,55%的不合格品归因于“挤橡”工序,即造成质量不稳定、废品率高的主要质量问题为“挤橡”,因此集中精力解决挤橡问题可使整个电线生产过程得到最大程度的改进。
2.分析“挤橡”工序的质量稳定情况
利用minitab软件,根据表2作出直方图(见图3)。
图3质量特性的直方图
可以看出,直方图形状为两边低中间高,左右基本对称,没有明显的“失稳”情况,说明工序处于基本稳定状态。
3.分析关键工序“挤橡”的工序能力
(1)初始工序能力分析
已知标准中心M=(
+
)/2=(0.9+1.1)/2=1.0mm;
根据表6数据,计算得样本均值,即分布中心µ
=1.0073mm<
M,标准差S=0.0406,故为双侧公差且分布中心与标准中心不重合的情况;
ε=∣M-µ
∣=∣1.0-1.0073∣mm=0.0073mm;
T=
-
=0.2;
K=2ε/T=2×
0.0073/0.2=0.073;
=T/6S=0.2/(6×
0.0406)=0.821;
所以
=
(1-K)=0.821×
(1-0.073)=0.7611﹤1。
作为关键工序,“挤橡”的工序能力明显不足,处于极高风险状态,此时应停止生产,查明系统性因素,可从以下方面采取措施,以提高
值:
1.调整过程加工的分布中心,减少个偏移量ε。
对影响过程质量的5M1E因素进行分析,找出造成加工分布中心偏移的原因。
减少偏移量的主要措施包括:
①对大量生产过程进行统计分析,得出六大因素随时间的推移而逐渐变化的规律,及时进行调整或采取设备自补偿调整;
②根据中心偏移量,通过首件检验调整设备;
③改变操作者习惯,以标准中心为加工依据。
2.提高过程能力,减少分散程度。
可从以下措施入手:
①改进工艺方法,优化工艺参数,推广应用新材料、新工艺、新技术;
②改造更新设备,以使其与产品质量标准要求相适应;
③加强现场质量控制,设置关键、重点过程的过程管理点,开展QC小组活动,是工序处于控制状态。
3.在不影响产品质量的前提下,可适当放宽标准范围。
(2)改进后的工序能力分析
根据表8数据,计算得均值µ
=1.0046,标准差S=0.0269;
∣=∣1.0-1.0046∣mm=0.0046mm;
0.0046/0.2=0.046;
0.0269)=1.239;
(1-K)=1.239×
(1-0.046)=1.182﹤1.239;
不合格率P=2-Φ﹝3
(1-K)﹞-Φ﹝3
(1+K)﹞
=2-Φ﹝3×
1.239×
(1-0.046)﹞-Φ﹝3×
1.239(1+0.046)﹞
=0.03%
采取一定措施后Cpk值得到了提高,且不合格品率大大降低,证明措施是有效的。
工序有所改进,但改进幅度不大,仍处于高风险状态。
这是由于课程组采取的“三自,一控”质量控制措施只是从操作者和产品检验的角度出发。
为进一步提高工序能力,在一定的经济基础上,应当注重设备、工序的创新,从而提高过程能力,减少分散。
4.设计“挤橡”工序的控制图
运用minitab软件作出关键工序的控制图(见图4):
图4关键工序的
-R图
(1)使用说明
如图4所示,纵坐标表示需要控制的质量特性,横坐标表示按系统取样方式得到的样本编号,上、下两条边界虚线表示公差上限(
)和公差下限(
),中间两条红色的虚线线分别表示上控制界限(UCL)和下控制界限(LCL),正中间的细直线表示中心线(CL)。
在控制图上,采取系统取样方式取得样本质量特性,用点子描绘在图上相应位置。
根据日常工作中该项目的分析频率和分析人员的技术水平,每间隔适当时间,取两份平行的控制样品,随环境样品同时测定,对操作技术较低的人员和测定频率低的项目,每次都应同时测定控制样品,将控制样品的测定结果,根据下列规定检验分析过程是否处于控制状态。
①如此点在上、下控制限之间区域内,则测定过程处于控制状态,环境样品分析结果有效;
②如果此点超出上、下控制限,但仍在上、下公差限之间的区域内,提示分析质量开始变劣,可能存在“失控’,倾向,应进行初步检查,并采取相应的校正措施:
③若此点落在上、下公差限之外,表示测定过程“失控”,应立即检查原因,予以纠正。
环境样品应重新测定;
④如遇到7点连续上升或下降时(虽然数值在控制范围之内),表示测定有失去控制倾向,应立即查明原因,予以纠正;
⑤即使过程处于控制状态,尚可根据相邻几次测定值的分布趋势,对分析质量可能发生的问题进行初步判断。
当控制样品测定次数累积更多以后,这些结果可以和原始结果一起重新计算总均值、标准偏差,再校正原来的控制图。
(2)利用控制图进行日常控制的意义
利用控制图对生产过程进行日常控制具有重要的实践意义,具体表现在以下几方面:
①判断生产工序质量的稳定性。
②评定生产过程的状态,发现以便及时消除生产过程的异常现象,有效预防废、次品的产生。
③确定设备与工艺装备的实际精度,以便正确的做出技术上的决定。
④为真正地制定工序目标和规格界限确立了可靠的基础,也为改变为能符合经济性的规格标准提供了依据。
题目二持续质量改进在空调热交换器生产车间的应用
(一)题目和要求
空调制冷能力一年不如一年,原因有很多,排除安装和保养不当,制冷剂泄露为主要原因之一:
有数十个焊接点的热交换器存在漏点往往是制冷剂泄露的最主要原因。
从顾客的角度来说,热交换器的散热性能好当然是很重要的,但可靠性高,不能泄露制冷剂也非常关键。
制冷剂泄露导致空调制冷/热效果低于使用初期的效果,会大大降低顾客对企业的信心。
通过市场调查及维修记录分析,可以看出热交换器泄露的主因在于焊口缺陷;
而从历史数据来看,在该企业空调产品的焊接质量缺陷中,自动焊接工序造成的缺陷约占70%左右。
经过粗略的质量成本核算,该企业每年由于热交换器泄露导致的直接经济损失就达到1000万元,如果将由此带来的外部损失成本记入在内,如顾客的流失、企业信誉的下降,企业损失势必更高。
因此,提高热交换器的产品可靠性对空调整机的“长效”至关重要。
找到了质量改进的方向后,生产部成立热交换器生产车间质量改进小组对热交换器的生产过程质量进行调查和研究。
首先确定热交换器生产过程质量改进的流程图,如图5所示:
图5热交换器生产过程质量改进流程图
1.确定关键工序
生产过程中的各个工序,尤其是关键工序,对产品质量的影响重大,尤其对下道工序有较大影响的工序更是至关重要,因此,在查找主要泄漏问题之前,先要了解热交换器的生产流程。
图6为热交换器的生产流程示意图。
主要原材料为铜管和铝箔,一部分铜管经过弯长u管设备,与冲床冲过的铝箔组装在一起再经过涨管机使得长u管的外壁同铝箔充分接触以便提高热交换率;
另一部分铜管经过弯半圆管设备成为半圆管,经过清洗,并套上焊环,然后将其按一定顺序插在涨管后的长u管管口,经过自动焊接设备,热交换器部件基本完成了。
随后将经过包括人工在内的多个检漏工序,最终作为合格品送往总装配车间进行整机装配。
图6热交换器生产流程图
图7热交换器焊口示意图
2.定性分析
产品的质量有50%以上在产品设计阶段已经被决定了,因此在质量改进之前了解产品设计原理,对查找慢性质量缺陷的原因,改进过程的质量非常重要。
热交换器的基本构造是用半圆管连接多个长u管,形成曲折的回路,以便于制冷剂有充分的时间和面积与套在
长u管上的铝箔进行热量交换。
半圆管与喇叭口的配合间隙是影响焊口质量的主要因素,如图7所示,长u管口被略微涨大形成喇叭口,在弯好的半圆管上套上焊环(熔点低于半圆管和长u管),再插入喇叭口,送入自动焊接机,焊环融化后可以均匀地分布在半圆管外壁和长U管内壁的间隙中。
因此在设计上要保证半圆管和长u管的间隙配合不能太松,也不能太紧。
太松会造成焊漏,充制冷剂时必然会出现大量泄露,在批量生产情况下造成不小的经济损失;
太紧则焊环融化后堆积在喇叭口上,看似焊好了,实际没有将两管连接在一起,形成虚焊,在空调运行一段时间后必然会出现问题。
目前,工艺上通过控制半圆管中心距和喇叭口中心距来控制配合间隙。
半圆管的中心距和喇叭口的中心距技术要求为(30.8±
0.2)mm,但半圆管与喇叭口的配合间隙仅为0.2mm(9.72mm-9.52mm),那么在理论上,当半圆管的中心距为上限31mm,而喇叭口的中心距为下限30.6mm时半圆管刚好能插入喇叭口。
在实际加工时,半圆管的中心距和喇叭口中心距部分超出了公差上下限,使得半圆管不能顺利插人喇叭口而要依靠其他工具敲人。
此时,半圆管与喇叭口其中一边的配合间隙为0,另一边的配合间隙为0.2mm,容易导致焊堵、焊漏、虚焊等焊接缺陷,部分虚焊情况甚至经过一段时间使用后才产生泄漏,这就是空调不能保持“长效”的主要原因。
因此尽管热交换器焊接口的工艺设计是可行的,但也需要加工过程有足够的过程能力来保证,控制中心距以保证它不超出公差上下限。
热交换器车间的自动焊工序是反映焊接质量最客观的一环,因此在这个工序进行成品质量调查采样,对各类焊口质量缺陷及发生频率作出统计,如表5。
表5焊口缺陷统计表
缺陷类型
虚焊
夹渣
过烧
焊料不饱和
其他
样本数量
56
35
3.定量分析
应用统计过程控制查找出现不合格品较多的工序。
首先对各个关键工序进行过程能力分析,对过程能力严重不足的工序进行改进,对过程能力尚可的工序用控制图进行监控,以保证工序质量处于稳定状态。
首先确定关键工序,图2显示的生产流程中有阴影的6个工序都会不同程度地影响焊口质量:
半圆管的中心距是否符合标准决定半圆管与喇叭口间隙配合适当与否,缺陷类型以虚焊居多;
焊口清洗不干净,喇叭口在胀管工序中破裂,以及自动焊接工序的火焰温度、焊枪距离配合都会造成各种焊口缺陷或影响焊接质量。
其中自动焊接工序是实现焊接的最关键的工序,但其焊接质量水平在很大程度上取决于半圆管与喇叭口间隙配合是否得当。
因此,在对自动焊接工序进行分析和改进之前,先要分析和改进半圆管弯制工序、套环工序及胀管工序的过程能力。
(注:
插半圆管工序为人工操作)鉴于弯管工序、套环工序和胀管工序对自动焊接工序的质量将产生十分关键的影响,因此质量小组决定先分别调查柜机厂热交换器车间及热交换器车间各半圆管弯管机、套环机及胀管机的工序过程能力。
在进行工序过程能力测算之前,质量小组首先绘制X–bar-R分析用控制图,并用去掉异常点的方法调整分析用控制图,根据分析用控制图得到控制用控制图。
确定工序处于稳定受控状态后,对各台机器的产品进行随机抽样,并计算各机器的过程能力指数CP和CPK.以热交换器一车间2号弯管机为例,随机抽取2号机生产的88个半圆管,测量其中心距,确定半圆管生产工序处于稳定受控状态,然后检验样本数据的正态性。
经过计算,该机的Cp=1.117,Cpk=0.581,这说明其过程能力尚可,但是过程分布中心与公差中心有偏差。
半圆管的中心距均值向公差中心右方偏移,即偏大,不能满足规格要求,潜在缺陷的比例非常大。
调查结果如表6和表7所示。
表6热交换器一车间弯半圆管、套环、胀管工序过程能力情况
工序
过程能力
备注
Cpl
Cpu
Cpk
Cp
弯半圆管
1号
-0.07
1.26
0.6
对应1号弯半圆管工序
对应2号弯半圆管工序
2号
0.12
1.07
套环
0.06
1.43
0.75
1.41
0.74
胀管
0.97
1.15
1.01
1.10
3号
0.82
1.92
4.解决方案
热交换器出现大量潜在焊接质量缺陷,从表面上看似乎是自动焊接工序的原因,如果直接应用试验设计来调整焊接设备参数并不能达到理想目标。
因为如果生产过程不稳定,存在系统误差,则不能找到最优的参数组合,所以首先应使用基础质量工具鉴定热交换器的生产过程是否处于统计上的稳定状态,消除系统误差。
经过应用统计工具发现,该生产流程本身不必要进行大幅度改进,但个别工序的过程能力过于低下,导致最终的自动焊接工序产生大量潜在质量缺陷,因此需要首先提高这些工序的过程能力,待整个生产过程稳定后再对自动焊接工序作进一步改善。
具体改进方案:
5.换热器生产过程的进一步质量改进
在对自动焊接工序有重要影响的各个工序进行分析和改进后,质量小组已经完成了一个PDCA循环,但这并不代表造成热交换器焊接质量低的原因已经得到了彻底解决。
质量大师戴明提出PDCA概念的目的也是要强调质量改进是一个保持基本目标不变的、持续不断的过程。
因此在对弯管、套环和胀管工序进行质量改进后,除了需要不断运用统计质量控制工具,如控制图等来保持现有成果,及时发现问题,还要进一步对自动焊接工序立项,作单独的质量改进项目。
因为在降低了由配合间隙不当造成的虚焊可能性之后,焊口缺陷仍然存在较高比例的虚焊和过烧问题(参见图4),这主要由自动焊接工序决定。
作为完成焊接功能的关键工序,由于其工艺复杂,影响因素众多,因此对自动焊接工序的改进还需要使用更高一级、更加复杂的统计工具——试验设计J。
但是,值得注意的是,如果不对整个热交换器生产流程进行统计过程控制而直接进行自动焊接工序的试验设计,则会由于系统误差导致试验结果不尽如人意。
因此在进行试验设计之前,首先需要保证该工序质量稳定,工序波动范围尽可能地小;
在建立自动焊接工序控制用控制图后,再对工艺参数进行优化。
这将是一个长期的过程,需要质量小组作长期的努力。
表7热交换器二车间弯半圆管、套环、胀管工序过程能力情况
1.459
0.882
1.17
1.654
0.581
0.518
1.117
1.255
0.976
1.116
1.721
1.34
0.933
1.177
1.327
1.259
0.514
0.496
0.529
0.489
0.509
0.58
0.655
0.617
(二)设计过程
1.根据表6,对产品质量补充定性分析
热交换器车间的自动焊工序是反映焊接质量最客观的一环,因此在这个工序进行成品质量调查采样,对各类焊口质量缺陷及发生频率作出统计图(),从下图可以看出,目前热交换器焊口质量缺陷最严重的问题为虚焊和夹渣,这两种缺陷占总缺陷的82%,需要集中力量解决这两个方面的问题。
从前面的焊口原理分析可以看出,半圆管和喇叭口的配合间隙不当是导致虚焊的主要原因。
图8焊口缺陷排列图
2.根据表6和表7的相关数据进行改进
分别对弯管机工序、套环工序、胀管工序补充改进方案。
具体改进方案如下:
①弯管机工序。
从得到的数据来看,柜机厂热交换器车间半圆管弯管机的过程能力明显不足,同时弯制后的半圆管中心距普遍偏小,这说明半圆弯模中心距的设计尺寸偏小,建议重新制作半圆管弯模。
热交换器车间的弯管机过程能力也不足,且尺寸偏大,说明是由于弯模长期使用后磨