合金的铸造性能Word文档下载推荐.docx
《合金的铸造性能Word文档下载推荐.docx》由会员分享,可在线阅读,更多相关《合金的铸造性能Word文档下载推荐.docx(18页珍藏版)》请在冰豆网上搜索。
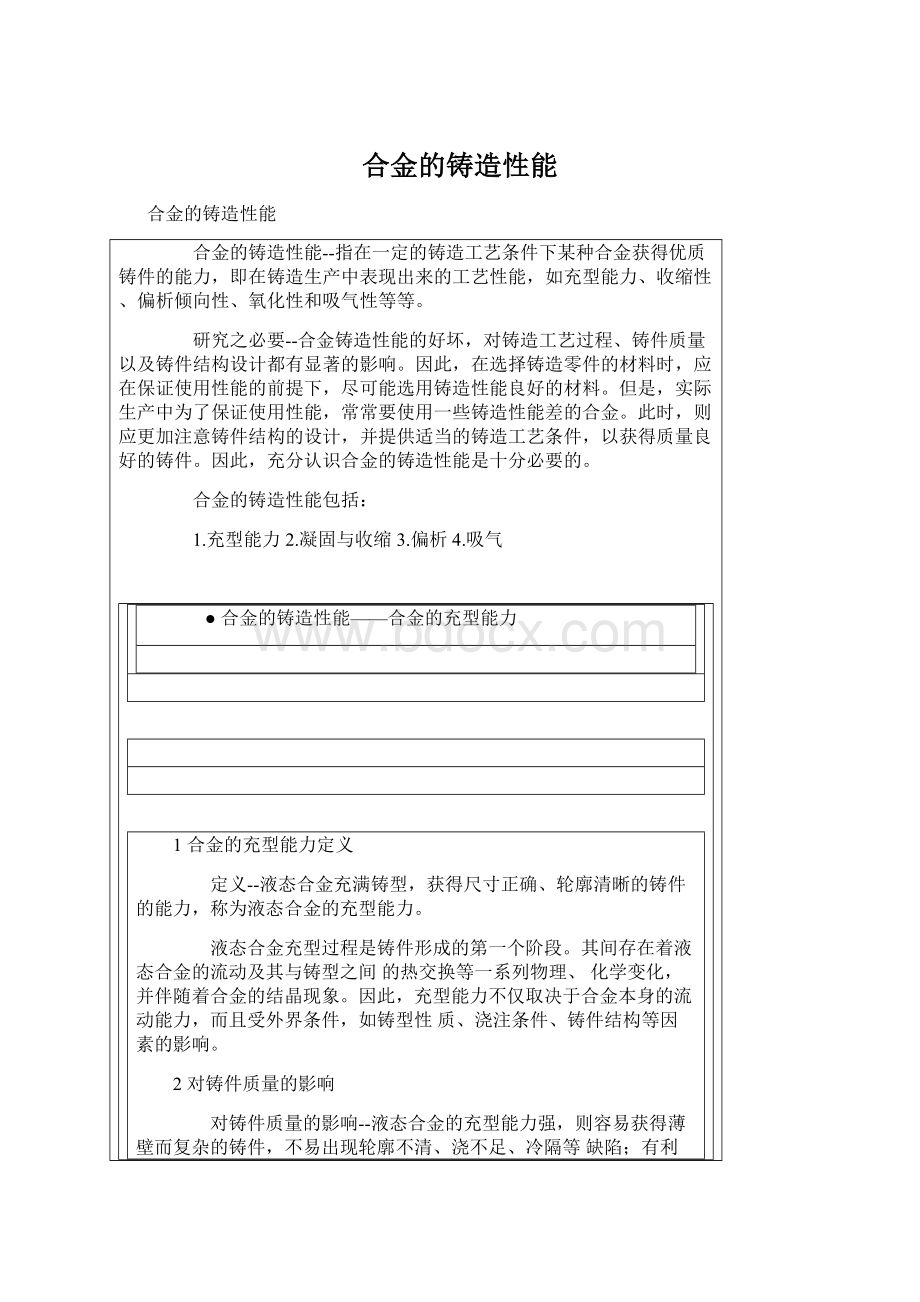
合金的化学成分决定了它的结晶特点,而结晶特点对流动性的影响处于支配地位。
具有共晶成分的合金(如碳的质量分数为4.3%的铁碳合金等)是在恒温下凝固的,凝固层的内表面比较光滑,对后续金属液的流动阻力较小,加之共晶成分合金的凝固温度较低,容易获得较大的过热度,故流动性好;
除共晶合金和纯金属以外,其他成分合金的凝固是在一定温度范围内进行的,铸件截面中存在液、固并存的两相区,先产生的树枝状晶体对后续金属液的流动阻力较大,故流动性有所下降。
合金成分越偏离共晶成分,其凝固温度范围越大,则流动性也越差。
因此,多用接近共晶成分的合金作为铸造材料,其原因就在于此。
(2)铸型性质
①铸型的蓄热系数它表示铸型从其中的金属液吸取并存储热量的能力。
铸型材料的导热率、比热容和密度越大,其蓄热能力越强,对金属液的激冷能越力就强,金属液保持流动的时间就越短,充型能力就越差。
例如,金属型铸造比砂型铸造更容易产生浇不足、冷隔等缺陷。
②铸型温度预热铸型能减小它与金属液之间的温差,降低换热强度,从而提高金属液的充型能力。
例如,在金属型铸造铝合金铸件时,将铸型温度由340℃提高到520℃,在相同的浇注温度(760℃)下,螺旋线试样长度由525mm增至950mm。
因此,预热铸型是金属型铸造中必须采取的工艺措施之一。
③铸型中的气体铸型具有一定的发气能力,能在金属液与铸型之间形成气膜,可减小流动阻力,有利于充型。
但若发气量过大,铸型排气不畅,在型腔内产生气体的反压力,则会阻碍金属液的流动。
因此,为提高型(芯)砂的透气性,在铸型上开设通气孔是十分必要且经常应用的工艺措施。
(3)浇注条件
①浇注温度
浇注温度对金属液的充型能力有决定性的影响。
浇注温度提高,使合金粘度下降,且保持流动的时间增长,故充型能力增强;
反之,充型能力就会下降。
对于薄壁铸件或流动性差的合金,利用提高浇注温度以改善充型能力的措施,在生产中经常采用也比较方便。
但是,随着浇注温度的提高,合金的吸气、氧化现象严重,总收缩量增加,反而易产生气孔、缩孔、粘砂等缺陷,铸件结晶组织也变得粗大。
因此,原则上说,在保证足够流动性的前提下,应尽可能降低浇注温度。
②充型压力
金属液在流动方向上所受的压力越大,则流速越大,充型能力就越好。
因此,常采用增加直浇道的高度或人工加压的方法(如:
压力铸造、低压铸造等)来提高液态合金的充型能力。
(4)铸件结构
当铸件的壁厚过小、壁厚急剧变化或有较大的水平面等结构时,会使合金液充型困难。
因此,设计铸件结构时,铸件的壁厚必须大于最小允许值;
有的铸件则需要设计流动通道;
在大平面上设置筋条。
这不仅有利于合金液的顺利充型,亦可防止夹砂缺陷的产生。
●
合金的铸造性能——合金的偏析
合金的偏析
偏析——在铸件中出现化学成分不均匀的现象。
偏析使铸件的性能不均匀,严重时会造成废品。
偏析可分为两大类:
微观偏析和宏观偏析。
晶内偏析(又称枝晶偏析)——是指晶粒内各部分化学成分不均匀的现象,是微观偏析的一种。
凡形成固溶体的合金在结晶过程中,只有在非常缓慢的冷却条件下,使原子充分扩散,才能获得化学成分均匀的晶粒。
在实际铸造条件下,合金的凝固速度较快,原子来不及充分扩散,这样按树枝状方式长大的晶粒内部,其化学成分必然不均匀。
为消除晶内偏析,可把铸件重新加热到高温,并经长时间保温,使原子充分扩散。
这种热处理方法称为扩散退火。
密度偏析(旧称比重偏析)——是指铸件上、下部分化学成分不均匀的现象,是宏观偏析的一种。
当组成合金元素的密度相差悬殊时,待铸件完全凝固后,密度小的元素大都集中在上部,密度大的元素则较多地集中在下部。
为防止密度偏析,在浇注时应充分搅拌或加速金属液冷却,使不同密度的元素来不及分离。
宏观偏析有很多种,除密度偏析之外,还有正偏析、逆偏析、V形偏析和带状偏析等。
合金的铸造性能——合金的吸气性
合金的吸气性
合金的吸气性——合金在熔炼和浇注时吸收气体的性质。
合金的吸气性随温度升高而加大。
气体在合金液中的溶解度较在固体中大得多。
合金的过热度越高,气体的含量越高。
气体在铸件中的存在有三种形态:
固溶体、化合物和气孔。
1)铸件中的气孔
按照合金中的气体来源,可将气孔分为以下三类。
(1)析出性气孔
溶解于合金液中的气体在冷凝过程中,因气体溶解度下降而析出,来不及排除,铸件因此而形成的气孔,称为析出性气孔。
析出性气孔在铝合金中最为常见,其直径多小于1mm。
它不仅影响合金的力学性能,而且严重影响铸件的气密性。
(2)侵入性气孔
侵入性气孔是砂型表面层聚集的气体侵入合金液中而形成的气孔。
(3)反应性气孔
浇入铸型中的合金液与铸型材料、芯撑、冷铁所含水分、锈蚀等或熔渣之间发生化学反应而产生气体,从而使铸件内形成的气孔,称为反应性气孔。
反应性气孔种类甚多,形状各异。
如合金液与砂型界面因化学反应生成的气孔,多分布在铸件表层下1~2mm处,表面经过加工或清理后,就暴露出许多小孔,所以称皮下气孔。
气孔破坏合金的连续性,减少承载的有效面积,并在气孔附近引起应力集中,因而降低了铸件的力学性能,特别是冲击韧度和疲劳强度显著降低。
成弥散状的气孔还可促使显微缩松的形成,降低铸件的气密性。
2)预防气孔的措施
①降低型砂(芯砂)的发气量,增加铸型的排气能力。
②控制合金液的温度,减少不必要的过热度,减少合金液的原始含气量。
③加压冷凝,防止气体析出。
因为压力的改变直接影响到气体的析出。
例如液态铝合金放在405~608kPa(4~6个大气压)的压力室内结晶,就可以得到无气孔的铸件。
④熔炼和浇注时,设法减少合金液与气体接触的机会。
如在合金液表面加覆盖剂保护或采用真空熔炼技术。
⑤对合金液进行去气处理。
如向铝合金液中通入氯气,当不溶解的氯气泡上浮时,溶入铝合金液中的氢原子不断向氯气泡中扩散而被带出合金液。
⑥冷铁、芯撑等表面不得有锈蚀、油污,并应保持干燥等。
合金的铸造性能——合金的凝固与收缩
1合金的凝固与收缩
(1)凝固与收缩的定义
凝固----物质由液态变为固态的过程。
收缩----铸件在凝固、冷却过程中所发生的体积减小的现象。
(2)对铸件质量的影响
浇入铸型的液态金属在冷凝过程中,如果凝固和收缩得不到合理的控制,铸件内部就会出现缩孔、缩松、铸造应力、变形、裂纹等缺陷。
2铸件的凝固方式及影响因素
(1)铸件的凝固方式
在凝固过程中,铸件断面上一般存在三个区域,即固相区、凝固区和液相区。
其中,对铸件质量影响较大的主要是液相和固相并存的凝固区的宽窄。
铸件的“凝固方式”依据凝固区的宽窄来划分,有如下三类。
①逐层凝固
纯金属或共晶成分合金(例如图B-1中的a成分)在凝固过程中不存在液、固相并存的凝固区(图B-2铸件的凝固方式(a)),故断面上外层的固体和内层的液体由一条界线(凝固前沿)清楚地分开。
随着温度的下降,固体层不断加厚,液体层不断减少,凝固前沿不断向中心推进,直至中心。
这种凝固方式称为逐层凝固。
②糊状凝固
如果合金的结晶温度范围很宽(例如图B-1中的c成分),且铸件内的温度分布曲线(图B-1中的t铸件曲线)较为平坦,则在凝固的某段时间内,铸件表面并不存在固体层,而液、固相并存的凝固区贯穿整个断面(图B-1(C))。
因为这种凝固方式与水泥类似,即先呈糊状而后固化,故称为糊状凝固。
③中间凝固
大多数合金(例如图B-1中的b)的凝固方式介于上述两者之间,称为中间凝固方式。
铸件的凝固与铸造缺陷的关系:
一般说来,逐层凝固有利于合金的充型及补缩,便于防止缩孔和缩松;
糊状凝固时,难以获得组织致密的铸件。
(2)影响铸件凝固方式的主要因素
①合金的结晶温度范围
合金的结晶温度范围愈小,凝固区域愈窄,愈倾向于逐层凝固。
例如:
砂型铸造时,低碳钢为逐层凝固;
高碳钢因结晶温度范围甚宽,为糊状凝固。
②铸件断面的温度梯度
在合金结晶温度范围已定的前提下,凝固区域的宽窄取决于铸件断面的温度梯度(见图B-2中T1→T2)。
若铸件的度梯度由小变大,则其对应的凝固区由宽变窄。
图B-2铸件的凝固方式
铸件的温度梯度主要取决于:
a.合金的性质合金的凝固温度越低、导温系数越大、结晶潜热越大,铸件内部温度均匀化能力就越大,温度梯度就越小(如多数铝合金);
b.铸型的蓄热能力铸型蓄热系数越大,对铸件的激冷能力就越强,铸件温度梯度就越大;
c.浇注温度浇注温度越高,因带入铸型中热量增多,铸件的温度梯度就越小;
d.铸件的壁厚铸件壁厚越大,温度梯度就越小。
通过以上讨论可以得出:
倾向于逐层凝固的合金(如灰铸铁、铝硅合金等)便于铸造,应尽量选用;
当必须采用倾向于糊状凝固的合金(如:
锡青铜、铝铜合金、球墨铸铁等)时,可考虑采用适当的工艺措施(例如,选用金属型铸造),以减小其凝固区域。
3合金的收缩及其影响因素
(1)合金收缩的原理及过程
液态合金的结构是由原子集团和“空穴”组成的。
原子集团内部的原子呈有序排列,但原子间距比固态时大。
将液态合金浇入铸型后,温度不断下降,空穴减少,原子间距缩短,合金液的体积要减小。
合金液凝固时,空穴消失,原子间距进一步缩短。
凝固后继续冷却至室温的过程中,原子间距还要缩短。
合金由浇注温度冷却到室温的收缩经历了以下三个阶段:
①液态收缩即从浇注温度到开始凝固的液相线温度之间,合金处于液态下的收缩。
它使型腔内液面下降。
②凝固收缩即从凝固开始温度到凝固终了温度之间,合金处于凝固过程的收缩。
在一般情况下,凝固收缩仍主要表现为液面的下降。
③固态收缩即从凝固终了温度至室温之间,合金处于固态下的收缩。
此阶段的收缩表现为铸件线性尺寸的减小。
合金的液态收缩和凝固收缩是铸件产生缩孔、缩松的主要原因;
而固态收缩是铸件产生铸造应力、变形、裂纹的根本原因,并直接影响铸件的尺寸精度。
(2)影响合金收缩的主要因素
①合金的化学成分
不同合金的收缩率不同。
在常用合金中,铸钢的收缩率最大,灰铸铁的收缩率最小。
灰铸铁收缩率很小的原因是:
由于其中大部分碳是以石墨状态存在的,石墨的比容大,在结晶过程,中石墨析出所产生的体积膨胀,抵消了合金的部分收缩。
表B-1不同合金的收缩率
合金种类铸
碳的质量分数
浇注温度/℃
液态收缩
凝固收缩
固态收缩
总体积收缩
铸造碳钢
白口铸铁
灰铸铁
0.35%
3.00%
3.50%
1610
1400
1.6%
2.4%
3.5%
3%
4.2%
0.1%
7.8%
5.4~6.3%
3.3~4.2%
12.46%
12~12.9%
6.9~7.8%
②浇注温度
浇注温度越高,合金的液态收缩量越大。
③铸型条件和铸件结构
铸件的实际收缩区别于合金的自由收缩,它会受到铸型及型芯的阻碍;
而且由于铸件结构复杂及壁厚不均,冷却时各部分相互牵制也会阻碍收缩。
合金的凝固与收缩——铸件中的缩孔与缩松
铸件中的缩孔与缩松——形成过程及原因、危害、对策
缩孔和缩松定义----铸件冷凝时,如果合金的液态收缩和凝固收缩得不到液态合金的补充,就会在最后凝固的部位形成孔洞。
容积大而集中的称为缩孔,细小而分散的称为缩松。
危害----缩孔和缩松会减小铸件的有效承载面积,并在该处造成应力集中,从而降低力学性能。
对于要求气密性的零件,缩孔、缩松还会造成渗漏而严重影响其气密性。
所以,缩孔和缩松是很大的铸造缺陷之一。
(1)缩孔和缩松的形成
①缩孔的形成过程
将液态合金浇入圆柱形型腔中,由于铸型的冷却作用,液态合金的温度逐渐下降,其液态收缩不断进行,但是当内浇口未凝固时,型腔总是充满的(见图B-3(a));
随着温度的下降,首先铸件表面凝固成一层硬壳,同时内浇口封闭(见图B-3(b));
进一步冷却时,硬壳内的液态金属继续液态收缩,并对形成硬壳时的凝固收缩进行补充,由于液态收缩和凝固收缩远大于硬壳的固态收缩,故液面下降并与壳顶脱离(见图B-3(c));
依此进行下去,硬壳不断加厚,液面不断下降,待金属全部凝固后,在铸件上部就形成一个倒锥形的缩孔(见图B-3(d));
在铸件继续冷却至室温时,其体积有所缩小,使缩孔体积也略有减小(见图B-3(e))。
如果在铸件顶部设置冒口,则缩孔将移到冒口中。
图B-3缩孔形成过程示意图
②缩孔出现的部位
一般出现在铸件最后凝固的区域,如铸件的上部或中心处、铸件上壁厚较大及内浇口附近等。
图B-4缩孔出现部位
③缩松的形成
是由于铸件最后凝固区域的收缩未能得到补足;
或者因合金呈糊状凝固,被树枝状晶体分隔开的液体小区得不到补缩所致。
缩松分为宏观缩松和显微缩松两种。
宏观缩松是用肉眼或放大镜可以看见的小孔洞,多分布在铸件中心轴线处或缩孔下方(图B-4)。
显微缩松是分布在晶粒之间的微小孔洞,要用显微镜才能看见。
这种缩松分布更为广泛,有时遍及整个截面。
显微缩松难以完全避免,对于一般铸件多不作为缺陷对待;
但对气密性、力学性能、物理性能或化学性能要求很高的铸件,则必须设法减少。
不同的铸造合金形成缩孔和缩松的倾向不同。
逐层凝固合金(纯金属、共晶合金或窄结晶温度范围合金)的缩孔倾向大,缩松倾向小;
糊状凝固的合金缩孔倾向虽小,但极易产生缩松。
由于采用一些工艺措施可以控制铸件的凝固方式,因此,缩孔和缩松可在一定范围内互相转化。
(2)缩孔和缩松的防止
①实现“顺序凝固”
为了防止缩孔、缩松的产生,应使铸件按“顺序凝固”的原则进行凝固。
“顺序凝固”原则是指利用各种工艺措施,使铸件从远离冒口的部分到冒口之间建立一个递增的温度梯度,凝固从远离冒口的部分开始,逐渐向冒口方向顺序进行,最后是冒口本身凝固。
这样就能实现良好的补缩,使缩孔移至冒口,从而获得致密的铸件。
为此应将冒口安放在铸件最厚和最高处,其尺寸要足够大。
有条件时,应将内浇道开设在冒口上,使充型的炽热金属液首先流经冒口。
与此同时可在铸件一些局部厚大的部位上安放冷铁,加快该处的冷却,以便充分发挥冒口的补缩作用。
顺序凝固的缺点是铸件各部分温差较大,引起的热应力较大,铸件易变形、开裂。
另外,因为设置冒口,增加了金属的消耗和清理费用。
顺序凝固一般用于收缩率大、凝固温度范围窄的合金(如铸钢、可锻铸铁、黄铜等),以及壁厚差别大、对气密性要求高的铸件。
图B-6冷铁的作用
②加压补缩
即将铸型置于压力室中,浇注后,迅速关闭压力室,使铸件在压力下凝固,可以消除缩松或缩孔。
此法又称为“压力釜铸造”。
③用浸渗技术防止铸件因缩孔、缩松而发生的渗漏
即将呈胶状的浸渗剂渗入铸件的孔隙,然后使浸渗剂硬化并与铸件孔隙内壁联成一体,从而达到堵漏的目的。
(3)缩孔和缩松位置的确定
为了防止缩孔和缩松的产生,必须在制定铸造工艺方案时正确判断它们在铸件中的位置,以便采取必要的工艺措施。
确定缩孔和缩松位置一般采用等温线法或内接圆法。
①等温线法
此法是根据铸件各部分的散热情况,把同时到达凝固温度的各点连接成等温线,逐层向内绘制,直到最窄的截面上的等温线相互接触为止。
这样,就可以确定铸件最后凝固的部位,即缩孔和缩松的位置。
图B-7(a)所示为用等温线法确定的缩孔位置,图B-7(b)所示为铸件上缩孔的实际位置,两者基本上是一致的。
图B-7等温线法
②内接圆法
此法常用来确定铸件上相交壁处的缩孔位置,如图B-8(a)所示。
在内接圆直径最大的部分(称为“热节”),有较多的金属积聚,往往最后凝固,容易产生缩孔和缩松(图B-8(b))。
图B-8内接圆法
合金的凝固与收缩——铸造应力、变形和裂纹
铸造应力、变形和裂纹——形成过程及原因、危害、对策
(1)铸造内应力的分类及形成
定义----铸件的固态收缩受到阻碍而引起的应力,称为铸造应力。
铸造应力可分为三种。
①机械应力
这种应力是由于铸件的收缩受到机械阻碍而产生的,是暂时性的。
只要机械阻碍一消除,应力也随之消失。
形成机械阻碍的原因是:
型(芯)砂的高温强度高,退让性差;
砂箱箱带、芯骨的阻碍等。
图1-12是套筒收缩受阻的情况,经落砂、清理后,应力即可消除。
②热应力
由于铸件各部分冷却速度不同,以致在同一时期内收缩不一致,而且各部分之间存在约束作用,从而产生的内应力,称为热应力。
铸件冷却至室温后,这种热应力依然存在,故又称为残余应力。
③相变应力
合金在弹性状态下发生相变会引起体积变化。
若铸件各部分冷却速度不同,相变不同时进行,则由此而产生的应力称为相变应力。
铸造应力是热应力、机械应力和相变应力三者的代数和。
根据情况不同,三种应力有时相互叠加,有时相互抵消。
铸造应力的存在会带来一系列不良影响,诸如使铸件产生变形、裂纹,降低承载能力,影响加工精度等。
(2)减小和消除铸造应力的途径
①工艺方面
a.使铸件按“同时凝固”原则进行凝固(如图1-14所示)。
为此,应将内浇道开设在薄壁处,在厚壁部位安放冷铁,使铸件各部分温差很小,同时进行凝固,由此热应力可减小到最低限度。
应该注意的是,此时铸件中心区域往往出现缩松,组织不够致密。
b.提高铸型和型芯的退让性,及早落砂、打箱以消除机械阻碍,将铸件放入保温坑中缓冷,都可减小铸造应力。
②结构设计方面
应尽量做到结构简单,壁厚均匀,薄、厚壁之间逐渐过渡,以减小各部分的温差,并使各部分能比较自由地进行收缩。
③铸件产生热应力后,可用自然时效、人工时效等方法消除。
图B-9铸件的同时凝固
(3)变形和裂纹
①变形
有带铸造应力的铸件处于不稳定状态,会自发地通过变形使应力减小而趋于稳定状态。
显然,只有受弹性拉伸的部分缩短,受弹性压缩的部分伸长,铸件中的应力才有可能减小或消除。
图B-10热应力引起变形的示意图
T形铸件产生变形的方向如图B-10(a)虚线所示。
这是因为T形铸件冷却后,厚壁受拉,薄壁受压,相当于两根不同长度的弹簧(图B-10(b)),将上面的短弹簧拉长,下面的长弹簧压短,以维持同样长度(图B-10(c))。
但这样的组合弹簧系统是不稳定的,力图恢复到原来的平衡状态,即上面的弹簧要缩短,下面的弹簧要伸长,于是就出现了与上述情形相似的弯曲变形(图B-10(d))。
危害、对策
防止铸件变形的根本措施是减少铸造内应力,例如:
设计时,铸件壁厚力求均匀;
制定铸造工艺时,尽量使铸件各部分同时冷却,增加型(芯)砂的退让性等。
在制造模样时,可以采用反变形法,即预先将模样做成与铸件变形相反的形状,以补偿铸件的变形。
图所的机床床身,由于导轨较厚,侧壁较薄,铸造后产生挠曲变形。
若将模样做出用双点划线表示的反挠度,铸造后会使导轨变得平直。
应当指出,铸件变形后,往往只能减小而不能彻底消除铸造应力。
机械加工后,零件内的应力失去平衡而引起再次变形,会使加工精度受到影响。
因此,对于重要的铸件,机械加工之前应进行去应力退火。
图B-11机床床身的挠曲变形和反挠度
②裂纹
当铸造应力超过当时材料的强度极限时,铸件会产生裂纹。
裂纹可分为热裂和冷裂两种。
热裂——是在高温下形成的,是铸钢件、可锻铸铁坯件和某些轻合金铸件生产中最常见的铸造缺陷之一。
其特征是:
裂纹形状曲折而不规则,裂口表面呈氧化色(铸钢件裂口表面近似黑色,而铝合金则呈暗灰色),裂纹沿晶粒边界通过。
热裂纹常出现于铸件内部最后凝固的部位或铸件表面易产生应力集中的地方。
冷裂——是在低温下形成的。
塑性差、脆性大、热导率小的合金,如白口铸铁、高碳钢和一些合金钢易产生冷裂。
裂纹形状为连续直线状或圆滑曲线状,常常是通过晶粒的。
裂口表面干净,有金属的光泽或呈轻微的氧化色。
冷裂常出现在铸件受拉伸的部位,特别是应力集中的部位,如内尖角处、缩孔和非金属夹杂物附近。
凡是减小铸造应力或降低合金脆性的因素(如减少钢铁中有害元素硫、磷的含量等)均对防止裂纹有积极影响。
欢迎您的下载,
资料仅供参考!
致力为企业和个人提供合同协议,策划案计划