热流道塑料模具设计步骤Word文件下载.docx
《热流道塑料模具设计步骤Word文件下载.docx》由会员分享,可在线阅读,更多相关《热流道塑料模具设计步骤Word文件下载.docx(6页珍藏版)》请在冰豆网上搜索。
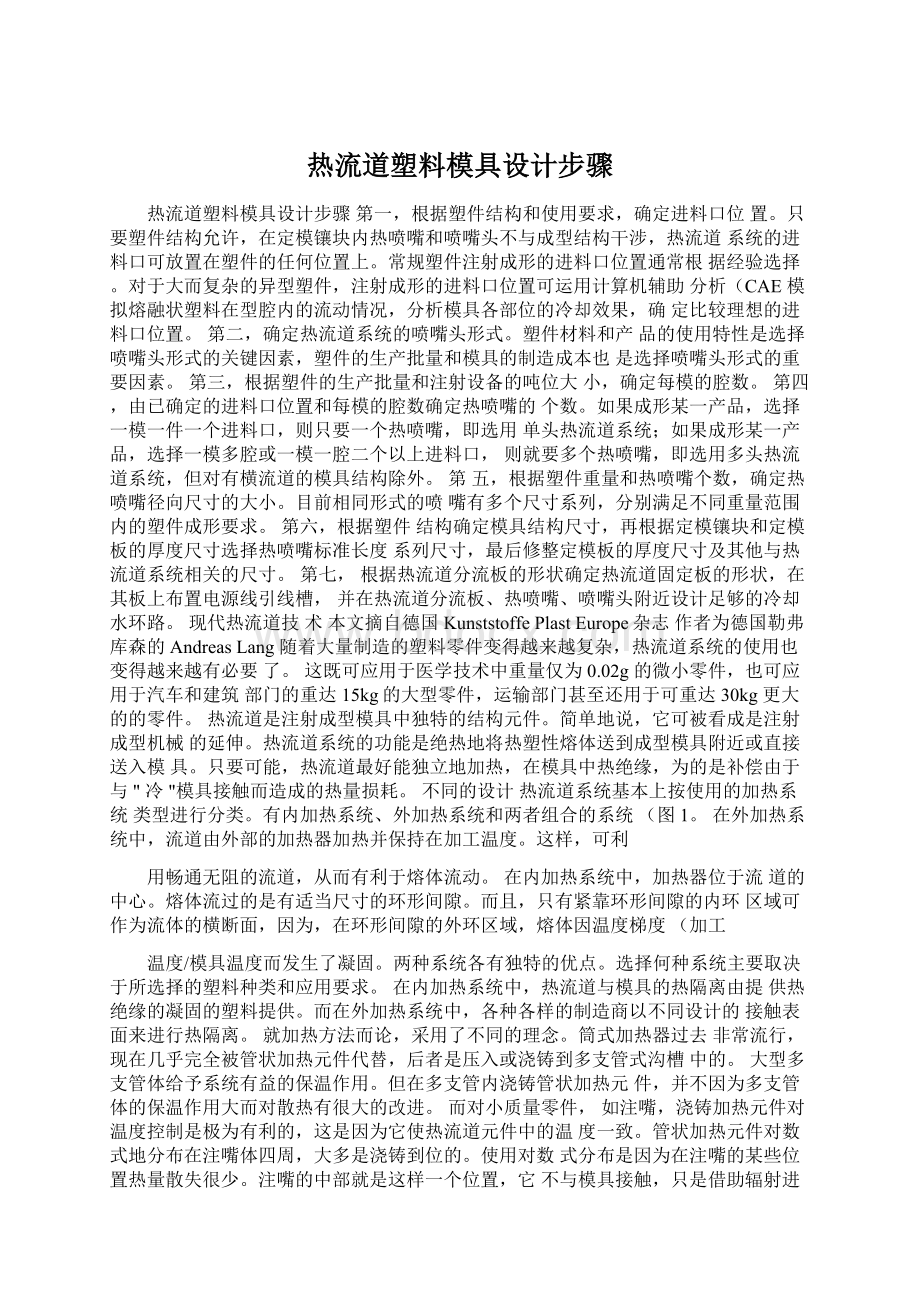
在外加热系统中,流道由外部的加热器加热并保持在加工温度。
这样,可利
用畅通无阻的流道,从而有利于熔体流动。
在内加热系统中,加热器位于流道的中心。
熔体流过的是有适当尺寸的环形间隙。
而且,只有紧靠环形间隙的内环区域可作为流体的横断面,因为,在环形间隙的外环区域,熔体因温度梯度(加工
温度/模具温度而发生了凝固。
两种系统各有独特的优点。
选择何种系统主要取决于所选择的塑料种类和应用要求。
在内加热系统中,热流道与模具的热隔离由提供热绝缘的凝固的塑料提供。
而在外加热系统中,各种各样的制造商以不同设计的接触表面来进行热隔离。
就加热方法而论,采用了不同的理念。
筒式加热器过去非常流行,现在几乎完全被管状加热元件代替,后者是压入或浇铸到多支管式沟槽中的。
大型多支管体给予系统有益的保温作用。
但在多支管内浇铸管状加热元件,并不因为多支管体的保温作用大而对散热有很大的改进。
而对小质量零件,如注嘴,浇铸加热元件对温度控制是极为有利的,这是因为它使热流道元件中的温度一致。
管状加热元件对数式地分布在注嘴体四周,大多是浇铸到位的。
使用对数式分布是因为在注嘴的某些位置热量散失很少。
注嘴的中部就是这样一个位置,它不与模具接触,只是借助辐射进行散热。
结果是沿注嘴长度方向温度分布较为均匀。
MoldMasters提供另一种类型的加热器。
其特征是有用于螺栓连接的平板。
图1外加热流道和内加热注嘴的组合(照片提供:
Ewikon)。
在Dynisco公司的热传导管技术中,长通道(长流道或注嘴可利用来自热源并流经管道的液体介质加热。
热传导管技术和多区段技术的组合对大型热流道系统是有好处的。
长通道最好只用一个热源进行加热,这样,就可减少控制回路的数目。
多区段技术,可在不管何处发生热量损耗(在接触区域的情况下确保精确的温度。
Dynisco的两种系统各具特色。
要求∶看不见注射点制造商们全都提供各式各样的注嘴头。
注嘴头一般用螺栓连接,以方便更换。
带有鱼雷芯的注嘴头有下述好处∶温度易于控制,从而可以做到使聚合物在注嘴处自动撕断开。
鱼雷芯头对于易产生拉丝的材料(如PA、
PC可以形成较好的撕断作用。
鱼雷芯头的缺点是它们造成材料的剪切作用。
对剪切敏感的材料,在鱼雷芯和流道的环形间隙,以及鱼雷芯的倒角处会因强烈的剪切作用而损坏。
如果零件由难加工的材料制成,鱼雷芯的倒角可导致产生印迹。
着了色的聚合物,因已发生色料聚集,是特别难加工的。
Husky公司新开发的装置以减
少制品表面印迹等这类问题而著名(图2。
为了避免机械加工,越来越多的零件要求
有很干净的、几乎看不见的浇注点。
在这种情况下,针阀是必不可少的。
针阀技术的优点是∶◆有缩短周期时间的可能性;
◆通过浇口时的剪切较少(针直径与浇口直径相等和/或,◆较大的注射成型加工范围。
甚至顺序(级联注射也需要使用针阀技术。
缺点是成本较高和需要较多的维护。
现代化的系统已经不再像过去那样对各种干扰极为敏感。
温度控制是关键选择热流道时最重要的判据是技术要求和服务。
较为低廉的内加热系统用于,例如,对剪切不敏感的低粘度的聚合物,而外加热系统应当用于高粘度的和对剪切敏感的聚合物。
公认地,在加工高温材料时,内加热系统或注嘴向模具传递热量较少,因此有优势。
如果注射量大,在内加热系统的环形间隙中的高的压力损耗应当引起充分注意。
并且,在环形流道,因为外层是凝结了的,实际的流体横断面常常只是设计断面面积的30%-50%。
另外,
加工温度范围较小的聚合物时,因为外加热系统对流道中熔体温度控制较好,用它加工较为可靠。
图2超级流体尖端(上:
鱼雷芯,下:
针阀。
照片提供:
Husky)流道是下一个重要判据。
从流变学的观点应当是尽可能自然地平衡,亦即,从注射注嘴到成型零件间的流道应有同样的直径,并且长度相等。
计算得到的流变学平衡只应用于例外情况,并主要用于大型零件(如仪表板。
为了获得有助于流体流动的流道,熔体的回转处应尽可能地和缓。
制造商们用不同的方法和工具实现这些目标。
它们中的一些在多支管中采用回转插塞。
这也可以,例如,借助收缩技术实现,以确保安全、紧密地配合。
另一些制造商将回转插塞置于前侧,这些通常要在此后进行机械加工。
Unitemp公司使用一种管系统来确保缓慢回转(图3。
对热流道系统的温度控制是极其重要的,特别是要选择好安装温度传感器的地方。
经验表明,它应当安装在预期温度最高处,决不要置于出现热量损耗的地方,诸如加压环、密封环附近,或热流道体的外侧区域。
在出现热量损耗的地方要对带状加热器作必要的调整,而这又可能导致聚合物的过热。
当今,热流道制造商将温度传感器安装在正确的、"
最热"
的位置。
一般地讲,所有温度传感器都可以更换。
制造商全都为它们的系统提供控制装置。
许多公司具有公司自己开发的内部控制技术,例如Dynisco就是如此。
图3浇铸的管系统(照片提供:
Unitemp)。
对整个系统
(多支管、注嘴、"
热侧"
的再一个判据是材料选择。
加工某些聚合物,例如PVC时会产生气体,可能腐蚀注射成型模具或热流道零件。
使用高合
金钢(铬含量>
13%可以防止这种腐蚀。
例如,Husky将所有零件都使用这种钢材作为公司的一项政策。
对于由于填充剂成分可能造成磨蚀的聚合物,相关零件,如注嘴头,的耐磨蚀性能是非常重要的。
硬质材料或涂层(TiN、TiC等提供对磨蚀的保护作用。
以服务为基础的选择由于热流道制造商在技术方面趋向于彼此类似,并且较早先的技术也已经大有改进,因而服务水平变成为越来越重要的选择判据。
最重要的是系统的交货速度,还要能够迅速地变换型号。
热流道制造商有贮存标准件是有好处的。
客户期望制造商对加工质量承担更多的责任。
例子之一是要求对一定数量的成型零件或一种特定的操作压力作业务保证。
各式各样的系统可按照维修方便程度加以区别。
当今,客户希望能更换易于严重磨损的零件,并且在注射成型机的零件方面,此点更为重要。
同样的情况也适用于颜色要频繁更换之处。
易磨损零件,如注嘴尖端、热传感器和加热元件应在世界各处可快速获得。
趋势对产品的责任已越来越多地转移到热流道制造商身上,这可用下述事实来说明∶全"
(中小型零件情况的更完整的单元(如热式仪表板得到愈来愈多的订货。
这些单元仅须在模具上组装。
热流道制造商可以保证它们的功能,或者说,它们能无困难地安装。
通过使用针阀系统来提高加工可靠性,以及在采用难加工的聚合物时设法去拓宽加工范围变得越来越流行。
除了提供很清晰的撕断外,针阀系统能用来影响注射成型加工过程。
针阀在多部件和夹芯注射成型加工中实际上是必不可少的。
越来越经常地使用顺序(级联注射,如果没有针阀和成熟的控制技术,这是不可能的。
由于液压缸体(针驱动机构的密封问题,出现了采用气动驱动方式的驱动针的趋势。
有大量型腔的气动系统特别适用于医学技术和包装方面,因为在那些领域解决油液造成的问题是一个重大的难题。
由于液体的可压缩性低,液压缸体在汽车工业的大型应用中找到了应用之地,因为此时要求针必须有精确的响应。
大多数制造商提供这两种类型的驱动。
小尺寸,或小注射量的大批量制品需要有更小的型腔距离。
型腔距离最小只有11mm,这意味着注嘴距也为11mm,现在已是可行的。
例如,由Guenther公司供应的系统就是这样。
在所谓注嘴组上,在一个轴线上距离只9mm也可以达到。
多层模具用于大批量的大型、两维的零件的生
产变得更为普及。
使用的电压是5V、24V和230V。
趋势是采用230V,因为电缆横断面和联接电缆所需空间较小。
除此之外,现代控制技术甚至在这种电压下也能满意地控制温度-而
在早先,这是低电压的主要优点。
总结和展望制造商们不再将它们的发展仅仅集中于现实的热流道技术,也转向特殊性的应用。
从制造商的观点,这里有一个远未穷尽的列出相关实例的清单∶◆用针阀对平扁型零件(如灵通卡作侧面浇注;
可更换的绝缘帽(对频繁更换颜色有利;
享有专利的针形(M形;
◆能较好混合的超级流体尖端(Husky;
◆熔体流的阀控制(Dynisco,因为供应各式各样的模腔的熔体流可单个地控制,它前景广阔。
控制器的响应时间是0.5ms;
注嘴有各自的注入角度◆最小模腔距离低达9mm;
外嵌入技术(Guenther;
◆共轴针技术;
夹芯技术(Ewikon;
◆借助微注射成型加工方法,标准零件生产可不再昂贵;
高水平的标准化;
注嘴尖选择可能性大(MoldMasters;
◆集成入冷却功能的特殊注嘴衬套;
即使大系统交货时间也很短(Yudo;
◆在公司内作模具试验。
为使客户能作初步选择,某些热流道制造商提供选择程序。
它们中的某些可在因特网上访问或直接订货(例如,Mold-Masters的Merlin程序,Ewikon的SystemGuide程序。
注射模热流道故障及其对策与普通流道模具相比,热流道模具有省时省料、效率高、质量稳定等显著优点,但曾一度因在使用上易产生故障而影响其广泛应用。
随着模具工业的技术进步,热流
道模塑在流道熔体温度控制、结构可*性及热流道元件设计制造等方面都有了长足的进步,这使得热流道技术重新得到人们的重视和青睐。
在热流道模具的设计和应用中,有诸多值得考虑和重视的问题,这些问题解决得好坏,直接关系着热流道系统的成败和制品质量。
因此,对热流道系统的故障及其成因进行探讨,了解热流道模塑应用中应注意的事项,无疑十分有助于热流道模塑技术的成功运用。
2热流道模塑常见故障分析及其对策2.1浇口处残留物突出或流涎滴料及表面外观差2.1.1主要原因浇口结构选择不合理,温度控制不当,注射后流道内熔体存在较大残留压力。
2.1.2解决对策(1浇口结构的改进。
通常,浇口的长度过长,会在塑件表面留下较长的浇口料把,而浇口直径过大,则易导致流涎滴料现象的发生。
当出现上述故障时,可重点考虑改变浇口结构。
热流道常见的浇口形式有直浇口、点浇口和阀浇口。
主流道浇口,其特点是流道直径较粗大,故浇口处不易凝结,能保证深腔制品的熔体顺利注射;
不会快速冷凝,塑件残留应力最小,适宜成型一模多腔的深腔制品,但这种浇口较易产生流涎和拉丝现象,且浇口残痕较大,甚至留下柱形料把,故浇口处料温不可太高,且需稳定控制;
特点基本
同,但在塑件上的残痕相对较小;
的特点是塑件残留应力较小,冷凝速度适中,流涎、拉丝现象也不明显;
可应用于大多数工程塑料,也是目前国内外热流道模塑使用较多的一类浇口形式,塑件质量较高,表面仅留有极小的痕迹;
具有残痕小、残留应力低,并不会产生流涎、拉丝现象,但阀口磨损较明显,在使用中随着配合间隙的增大又会出现流涎现象,此时应及时更换阀芯、阀口体。
浇口形式的选择与被模塑的树脂性能密切相关。
易发生流涎的低粘度树脂,可选择阀浇口。
结晶型树脂成型温度范围较窄,浇口处的温度应适当较高,如POM、PPEX等树脂可采用带加热探针的浇口形式。
无定型树脂如ABS、PS等成型温度范围较宽,由于鱼雷嘴芯头部形成熔体绝缘层,浇口处没有加热元件接触,故可加快凝结。
(2温度的合理控制。
若浇口区冷却水量不够,则会引起热量集中,造成流涎、滴料和拉丝现象因此出现上述现象时应加强该区的冷却。
(3树脂释压。
流道内的残留压力过大是造成流涎的主要原因之一。
一般情况下,注射机应采取缓冲回路或缓冲装置来防止流涎。
2.2材料变色焦料或降解2.2.1主要原因温度控制不当;
流道或浇口尺寸过小引起较大剪切生热;
流道内的※点导致滞留料受热时间过长。
2.2.2解决对策(1温度的准确控制。
为了能准确迅速地测定温度波动,要使热电偶测温头可*地接触流道板或喷嘴壁,并使其位于每个独立温控区的中心位置,头部感温点与流道壁距离应不大于10mm为宜,应尽量使加热元件在流道两侧均布。
温控可选用中央处理器操作下的智能模糊逻辑技术,其具备温度超限报警以及自动调节功能,能使熔体温度变化控制在要求的精度范围之内。
(2修正浇口尺寸。
应尽量避免流道※点,在许可范围内适当增大浇口直径,防止过甚的剪切生热。
内热式喷嘴的熔体在流道径向温差大,更易发生焦料、降解现象,因此要注意流道径向尺寸设计不宜过大。
2.3注射量短缺或无料射出2.3.1主要原因流道内出现障碍物或※角;
浇口堵塞;
流道内出现较厚的冷凝层。
2.3.2解决对策(1流道设计和加工时,应保证熔体流向拐弯处壁面的圆弧过渡,使整个流道平滑而不存在流动※角。
(2在不影响塑件质量情况下,适当提高料温,避免浇口过早凝结。
(3适当增加热流道温度,以减小内热式喷嘴的冷凝层厚度,降低压力损失,从而利于充满型腔。
2.4漏料严重2.4.1主要原因密封元件损坏;
加热元件烧毁引起流道板膨胀不均;
喷嘴与浇口套中心错位,
或者止漏环决定的熔体绝缘层在喷嘴上的投影面积过大,导致喷嘴后退。
2.4.2解决对策(1检查密封元件、加热元件有无损坏,若有损坏,在更换前仔细检查是元件质量问题、结构问题,还是正常使用寿命所导致的结果。
(2选择适当的止漏方式。
根据喷嘴的绝热方式,防止漏料可采用止漏环或喷嘴接触两种结构。
应注意使止漏接触部位保持可*的接触状态。
在强度允许范围内,要保证喷嘴和浇口套之间的熔体投影面积尽量小,以防止注射时产生过大的背压使喷嘴后退。
采用止漏方式时,喷嘴和浇口套的直接接触面积要保证由于热膨胀造成的两者中心错位时,也
不会发生树脂泄露。
但接触面积也不能太大,以免造成热损失增大。
2.5热流道不能正常升温或升温时间过长2.5.1主要原因导线通道间距不够,导致导线折断;
装配模具时导线相交发生短路、漏电等现象。
2.5.2解决对策选择正确的加工和安装工艺,保证能安放全部导线,并按规定使用高温绝缘材料,定期检测导线破损情况。
2.6换料或换色不良2.6.1主要原因换料或换色的方法不当;
流道设计或加工不合理导致内部存在较多的滞留料。
2.6.2解决对策(1改进流道的结构设计和加工方式。
设计流道时,应尽量避免流道※点,各转角处应力求圆弧过渡。
在许可范围内,流道尺寸尽量小一些,这样流道内滞留料少、新料流速较大,有利于快速清洗干净。
加工流道时,不论流道多长,必须从一端进行加工,如果从两端同时加工,易造成孔中心的不重合,由此必然会形成滞留料部位。
一般外加热喷嘴由于加热装置不影响熔体流动,可以较容易地清洗流道,而内加热喷嘴易在流道外壁形成冷凝层,故不利于快速换料。
(2选择正确的换料方法。
热流道系统换料、换色过程一般由新料直接推出流道内的所有滞留料,再把流道壁面滞留料向前整体移动,因此清洗比较容易进行。
相反,若新料粘度较低,就容易进入滞留料中心,逐层分离滞留料,清洗起来就较为麻烦。
倘若新旧两种料的粘度相近时,可通过加快新料注射速度来实现快速换料。
若滞留料粘度对温度较为敏感,可适当提高料温来降低粘度,以加快换料过程。
3选择和应用热流道的注意事项为尽可能排除或减少使用中的故障,在选择和应用热流道系统时应注意以下事项。
3.1加热方式的选择(1内加热方式。
内热式喷嘴结构较为复杂,造价较高,零件更换困难,对电热元件要求较高。
把加热器安放在流道中间,会产生环形流动,增大容体摩擦面积,压力降可能有外热
式喷嘴3倍之多。
但由于内加热的加热元件设在喷嘴内的鱼雷体中,热量全部
供给物料,故热损失小,可节约电能。
若采用点浇口,鱼雷体尖端保持在浇口中心,利于注射后浇口切断并因浇口凝结晚而使塑件残留应力较低。
(2外加热方式。
采用外热式喷嘴,可以消除冷膜,降低压力损失。
同时由于其结构简单,加工方便,以及热电偶安装于喷嘴中部使温控准确等优点,目前在生产中获得了普遍应用。
但外热式喷嘴热损失较大,不如内热式喷嘴节能。
3.2浇口形式的选择浇口的设计和选择直接影响塑件质量。
在应用热流道系统时,应根据树脂的流动性能、成型温度以及产品质量要求来选用合适的浇口形式,以防止出现流涎、滴料、漏料和换色不良等现象。
3.3温度控制方式当浇口形式确定后,熔体温度波动的控制将对塑件质量起关键作用。
很多时候出现的焦料、降解或流道阻塞现象大都是温度控制不当造成的,尤其是热敏性塑料,往往要求能迅速准确地反应温度波动情况。
为此,应该合理地设置加热元件,防止出现局部过热,确保加热元件与流道板或喷嘴的配合间隙,尽量减小热损失,同时应尽量选择较为先进的电子温控器,以满足温控要求。
3.4热流道系统结构确定后的计算内容(1各分流道的温度和压力平衡计算。
热流道系统的目的就是将从注塑机喷嘴中注入的热塑料,以相同的温度通过热流道并以均衡的压力将熔体分配到模具的各个浇口,故应对各流道加热区的温度分布以及流入各浇口的熔体压力进行计算。
(2热膨胀引起的喷嘴和浇口套中心偏移量计算。
即应保证热(膨胀的喷嘴和冷(没有膨胀浇口套的中心线能准确定位对准。
(3热损失计算。
内加热的流道是由冷却的模套包围和支撑的,所以应尽量准确地计算由于热辐射和直接接触(传导所导致的热损失量,否则,实际的流道通径会因流道壁冷凝层的加厚而变小。
3.5流道板的安装应充分考虑绝热和承受注射压力两方面的问题。
通常在流道板和模板间设置垫块和支撑件,这一方面可承受注射压力,以免流道板变形而产生漏料现象,另一方面还可减小热损失。
3.6热流道系统的保养对于热流道模具,使用中定期进行热流道元件的预防性保养是十分重要的,这项工作包括电气测试、密封元件和连接导线的检查以及元件脏物的清洗工作等。