pvc挤出工艺Word下载.docx
《pvc挤出工艺Word下载.docx》由会员分享,可在线阅读,更多相关《pvc挤出工艺Word下载.docx(9页珍藏版)》请在冰豆网上搜索。
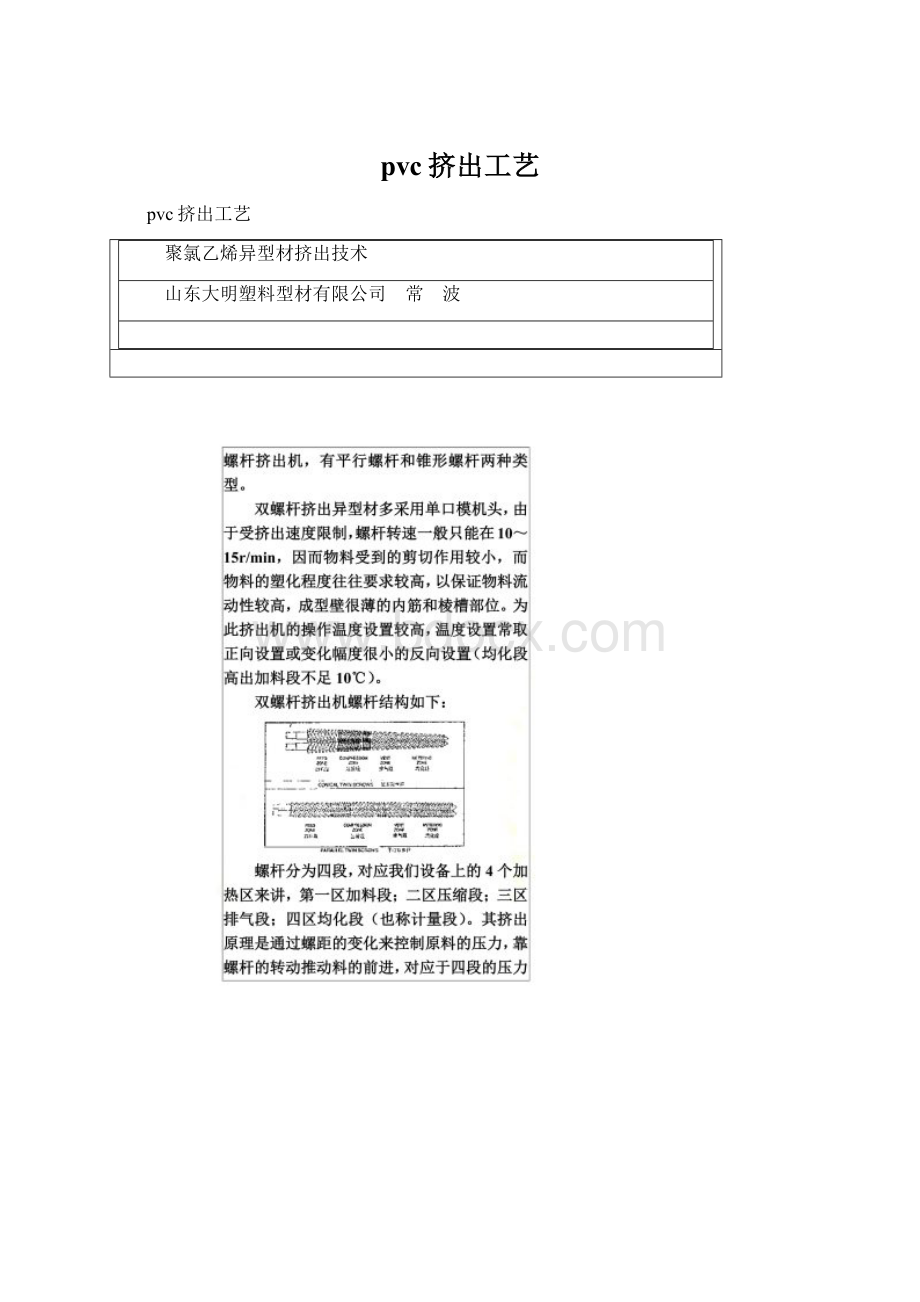
热混部分主要是热缸,其内部有两个叶片,不同厂家的热混叶片结构有所不同,但作用原理一样,均是使物料在热混缸内沸腾起来,以使物料能均化,同时磨擦生热,热混的热量一般来自于自身物料的磨擦,也有一部分厂家的热混缸需用外加热,另外还包括以上部分测温的热电偶,排气用的除尘器,挡料板。
这三个部件对于工艺的影响是非常巨大的,热电偶是测定热混温度的,除尘器过滤排气中的粉尘并排出混料过程中产生的水蒸气,挡料板的作用是使料产生涡流,同时使料不从除尘器口溢出。
冷混部分由冷混缸组成,内部有叶片、热电偶、除尘器,其作用相对简单,是物料均匀冷却,而且不结块。
2、挤出系统
塑料异型材挤出通常采用异向向外式双
该部分将料进一步压缩,以提高产品的密度。
依据以上原理混料的温度设定一般如下:
加料段因料的预热过程需带走大量的热,所以该段温度应高一点,在实际生产中可以看到,一般一区的加热频率较高,而且实际温度不易达到设定温度。
其原因就是该段吸收大量热量而且磨擦产生热少的原因。
均化段的作用主要是保温,使熔体均化,一般温度设定与压缩段一致,连接体,因要使料压缩,磨擦产热量较大,温度设定应稍低。
口模的温度一般较高,主要目的是提高型材的表面光洁度。
在一定的温度范围内,型材的表面光亮度与温度成正比。
同时减少挤出难度,降低挤出压力。
异型材的冷却多以水为冷却介质,因为水的热容量较大。
导热性好,冷却效率较高,然而,由于用水的冷却速度较快,对于形状复杂的、外形不对称的异型材可能导致较大的内应力。
为了减小定型台长度又充分消除内应力,可采取水冷定型,再用红外烤灯进行烘烤进行“回火”处理。
冷却定型装置常见的有以下几类:
(1)干法真空定型 此法是异型材冷却定型的主要方法。
干法真空定型系统常由几个箱式真空定型套组成,箱体内是外型与尺寸与型材很接近的定型模,定型模与箱体板之间有冷水通路构成的夹道和抽真空管道系统。
每个定型箱的长度为400~500mm,不可过长,以便开车时型材进入和穿过定型模。
箱体可对型材的2—4个表面进行冷却和定型。
定型台上冷却定型箱的数量决定于制品的壁厚和牵引的速度。
生产中常要用一台挤出机生产几种规格的型材,在选购定型台的长度时往往要与挤出机的生产能力配套。
定型台底板上,除了安装几个可以滑动并定位的定型箱外,还安装冷却水槽(水浴水冷、喷雾水冷或涡流水冷)。
冷却水槽内有多个支撑型材的滑辊。
定型台框架的下面有数台水环式真空泵和一个回收水箱。
在框架上方或侧面安装有数十个冷却水嘴和真空嘴,通过软管连接于定型箱的入水口和抽气口。
整个定型台可作三维以及倾斜的移动。
型材经过几级冷却真空定型后,外壁的温度应降至热变形温度以下,外形尺寸基本达到规定偏差,然而型材的内筋往往尚未得到充分冷却。
在冷却水箱中,型材外壁尺寸稳定下来,同时内筋也得到充分冷却,可以经受牵引力的拉力和压力,便进入牵引装置。
(2)湿法真空定型 将类似于干法真空定型的定型模(连同真空管路)浸泡于冷却水槽或喷淋水箱中实现对型材的定型与冷却。
这种定型装置省去了定型模外的水管夹套系统,进一步提高了冷却效率。
但是所用水箱较大,在开车阶段向定型套内导型材的时,操作不便。
此种方法多用于断面形状简单,厚度在3mm以上制品的定型。
中空异型材在定型模真空定型时,要防止密封不好漏气,同时又要注意真空度不可过高,以防型材嵌入真空抽气槽,导致牵引困难以至将型材拉断或牵引速度不稳定的情况发生。
冷却水温恒定14±
1℃,水压稳定,应大于2kg/cm2,水质经过软化和过滤处理。
异型材生产用牵引装置主要是履带式牵引机。
履带牵引机的牵引力为10~30kN,牵引速度为0~15m/min。
牵引机的长度多选3~4m,牵引用胶块的长度为200~250mm。
正常生产时,牵引速度要比挤出速度略快。
牵引速度越慢,型材壁越厚;
反之,型材壁越薄。
但牵引速度过快会导致型材内应力大,加热后尺寸变化率大,影响型材尺寸合格率。
切割机多为电动锯片式,锯片直径300~450mm。
锯片转速2800r/min。
切割时,锯片自动移向型材,从而对型材实现贯穿切割。
切割机有自动与手动控制。
自动控制决定于型材的长度,控制信号可来自于索引机对牵引长度的计量或来自于翻转台处安装的行程开关。
当型材达到预定长度时,切割机的气缸活塞运动,并将型材压紧在切割机工作台面上。
由于切割工作台安装在阻力很小的滑轨上,在牵引机推进下向前移动的型材及切割工作台保持同步。
同时锯片移向型材实现同步切割。
切割之后,置于翻转台上的型材翻向一侧用于包装,然后翻转台复位等待另一根型材输入达到规定的长度,再进行下一次切割与翻转。
翻转台的运动借助压缩空气,气缸压力0.5~0.8MPa,切割长度为4~6m。
奥地利Greiner公司现已研制出无锯屑切割,采用剪切式切割,弥补了锯式切割噪音大、锯屑不卫生和切割有损耗的缺点。
在制品切割完毕后要进行堆放。
卸料台即完成此功能,在牵引切割机切断制品后推到料架上,由料架自动翻板堆放。
三、型材生产中工艺控制
1、混料工艺
型材质量与所用的生产原料有很大关系,采用不同原料和不同配方生产出来的型材会有很大差异。
原料和配方研究是一项非常复杂的工作,这里我们不在赘述。
混料过程的主要任务是:
将所需的稳定剂、填充剂、颜料、润滑剂、改性剂等和PVC原料进行混合,使其均匀的分布,形成一个干燥和松散可流动的干混料。
塑料异型材加工对干混料的均匀性要求很高,这是由挤出加工设备的特性所决定的。
硬PVC干混料的热混应严格按合理的加料顺序、加料量、混合时间及混合温度进行,以保证干混粉料的质量。
对有机锡为稳定剂的配方,热混温度为120℃,冷混卸料温度为40℃。
热混温度过高,干混料受热时间长,型材会分解;
过低挤出会造成塑化不良,型材发喘。
发泡所用原料的含水量必须合乎优质品的要求,并应排气或减压排除以除去物料中的潮气。
在热混过程中,物料的变化过程为:
颗粒细化→重新结合→粒径增大→部分凝胶化
用于双螺杆挤出的干粉料的混合工艺特别要严格控制,因为混合工艺条件的改变会导致干粉料密度的改变和物料加工特性的变化,进而可使挤出速度及塑化质量变化,而使生产速度及产品质量波动。
冷混缸的冷却水温度通常控制在13~15℃。
冷混后得的干粉料应经振动筛筛除杂质及混合釜内的结垢,以保证挤出机生产速度的平稳和防止口模堵塞。
振动筛内部应由不锈钢制作,筛网为40~60目。
加料量是高搅容积的2/3,投料量最佳,物料升温时间短。
过多则负荷过大,物料翻腾不好,混合不均;
过少,则摩擦热少,升温慢。
硬PVC配方的组分很多,加料顺序应是严格合理的。
所选择的加料顺序应有利于助剂作用的发挥,避免助剂的不良协同效应,还要有利于提高分散性。
①稳定剂宜在树脂加入后,或与树脂同时加到热混机中,以便及早发挥稳定作用。
②皂类和内润滑剂宜随后加入,以便充分渗入树脂内部。
③蜡类外润滑剂宜在料温接近出料温度时再加,以免蜡类干扰其它助剂的分散,使树脂颗粒表面摩擦系数降低,自摩擦生热速度降低,而延长混合时间。
④填料对助剂有吸收作用,宜最后加入,以便助剂先在树脂中得以分散,减少填料对热混机的磨损,也可避免填料带来的料温升速变慢的弊端。
⑤加工改性剂宜在蜡类加入之前,稳定剂加入之后加入。
抗冲击改性剂可与树脂一并加到热混机中,特别是对具有热分解倾向的改性剂,如CPE。
如果考虑抗冲击改性剂吸收润滑剂的倾向往往强于PVC树脂。
为了避免润滑剂被吸收后物料加工性的明显变化,为了避免吸收润滑剂后改性效果的降低,也可在最后加入。
还有的抗冲击改性剂易结团,为了使其分散良好,也可最后缓缓加入。
总之,助剂的加料顺序应避免助剂之间的相克相消,提高助剂的相辅相成效果,使应该在PVC树脂中分散的助剂,得以充分进入材脂的内部。
混合料要在储料罐中静置24小时以上,使物料进一步熟化,并消除混料过程中产生的静电,提高干混料的流动性。
混料静置时间短,易发生型材发喘(平行双螺杆反应尤甚),在靠自重喂料的设备易发生“架桥”现象。
混料操作中容易出现的问题:
①投料顺序不对,其结果是会形成较厚的壁层,添加剂附着在加热的搅拌叶轮和机筒内壁上。
②冷却水温度太低,其结果是在冷混料机内壁形成一层凝固层,整个设备系统的热量传递效果变差,需要更长的冷却混料时间。
③冷混出料温度高,干混料易发生结块现象。
2、挤出工艺
要获得外观和内在质量均优良的异型材挤出制品,挤出工艺非常重要,挤出工艺条件又随挤出机结构、模具及配方的不同而有相当大的改变,所以挤出工艺条件变化最为复杂,必须在实践中不断地摸索总结。
挤出机排气段要保证管路畅通,真空度应有0.08~0.09MPa。
真空度低会影响排气效果,导致物料中卷入的空气、挥发物、水气等不能被抽走,型材中有微小气泡,严重降低型材的机械性能,并造成型材发泡起皮。
在生产中,物料应在排气孔处刚好凝胶化,塑化过度,气体不易逸出;
粉料未粘连,又易被真空吸出,要注意避免排气管阻塞。
主机转速与喂料转速保持线形关系,一般情况下喂料转速应保证加料覆盖整个螺杆,否则因剪切不均匀,挤出速度不稳定型材发喘(从真空孔可以观察)。
挤出压力是一个重要的指标,主要和模具的设计有关。
挤出压力过高对设备有损害,背压过大物料因剪切力而分解,型材发泡而影响挤出速度;
背压太低,物料塑化不良,低温落锤冲击受影响。
温度是型材挤出加工中一个相当重要的工艺条件。
物料温度一般控制在流动温度和分解温度之间。
温度过高会引起分解,温度过低,物料会塑化不良。
挤出机机身温度其影响机理在在介绍挤出机时已经进行了详尽的介绍,这里不再赘述。
连接体温度一般控制在170~180℃之间,温度过高,物料易分解导致制品表面产生黄线、黑线等缺陷。
模具温度直接影响产品质量,当模具温度偏高时,虽然型胚可以顺利进入定型模,但会使产品形状稳定性差,收缩率增加,致使产品无法保证外型尺寸;
温度过高,还会引起气泡、产品发黄、物料分解等。
如果温度偏低,则物料塑化不良、熔体粘度增大、机头压力上升、扭矩值增加,虽然这样会使产品较密实,后收缩小,产品形状稳定,但物料离模膨胀率大、产品表面粗糙,还导致挤出机背压增大。
如果温度过低,则产品无法成型,还会因压力巨增而损坏设备。
锥形双螺杆挤出机和平行双螺杆挤出机挤出硬聚氯乙烯中空型材加工温度范围列于下表(仅供参考):
部位
机身温度℃
连接体温度℃
模具温度℃
1
2
3
4
平双
185
160
170
195
锥双
180
异型材在挤出过程中,物料离模时完全处于熔融状态,并直接受牵引进入真空定型模,借助真空负压作用,使处于软化状态,但有一定形状的型胚,被紧紧吸附在定型模型腔面上,并通过真空定型模内循环冷却水的冷却。
当异型材出真空定型模后,就最大限度的成型为理想的异型材形状尺寸,并且具有一定的硬度。
当真空度过高时,会导致牵引阻力过大,甚至卡料。
当真空度过低时,则对型胚吸附不足,无法保证产品外观质量和尺寸精度。
具体的控制调节措施如下:
a、如果通过真空度反复调节或其他措施,都无法将制品吸足,则可适当降低牵引速度,特制品被吸足后再恢复正常生产时的速度。
b、开车时应等异型材进入牵引机夹紧后,方能打开真空,以防止与定型模之间积料堵塞。
特牵引稳定后,最后拧紧模具螺钉。
c、如果发现异型材在定型模入口端变形或不成形,或内筋粘附型腔内表面没有吸起时,则可用尖头工具在定型模入口端,不成形部位或内筋部位戳数个小孔,使型材进入真空定型模时呈开放性腔室,则较容易被真空吸足并贴附模腔表面,得到理想的型材。
由于PVC塑料熔体粘度较高,在高温下进入定型模,需得到及时、合适的冷却方式和恰当的冷却水温,进行冷却定型,才能得到理想的制品。
否则会使制品产生弯曲、凹陷、翘曲等变形现象。
在调节冷却水量时应注意:
a、在生产过程中,如果发现异型材从定型模出来后,仍有不平直的弯曲现象,可适当调节各部位的冷却水流量和模头加热板温度来纠正,还可采用喷淋冷却水来纠正。
b、在刚开车将异型材型胚引入定型模和牵引机过程中。
为防止型材被拉断,应及时在型材表面喷淋冷却水,使其表面得到冷却并具有一定的硬度不至被拉断。
但注意不要使冷却水倒流到口模,造成刚出模的型胚骤冷而断裂,同时造成口模成形板变形和生锈。
在生产中常常会遇到各种异常现象,由于其产生原因复杂,需要认真的分析其症结所在,现将在生产中经常遇到的几种异常现象及其原因进行分析,见表1。
表1 生产异常现象分析与排除
异常现象
产生原因
排除措施
型材表面有黄色分解线
1、物料在机头口模内分解
2、稳定剂或润滑剂不足
3、模具有模具死解和表面缺陷
1、清理机头口模或降低机头温度
2、填加稳定剂或润滑剂
3、清除模具死角和表面缺陷
型材内壁毛糙
1、芯模温度偏低
2、机身温度过低
3、螺杆温度太高
1、提高芯模温度
2、提高机身温度
3、降低螺杆温度
型材弯曲或翘曲
1、机头温度不均,出粒不均
2、机头内流道设计不合理
3、口模定型模未对中
4、定型冷却不均
5、定型冷却不足
6、模具未装正
7、挤出速度太快
8、滤网部分阻塞
9、真空冷却水道不畅
10、真空泵补水管阻塞
11、真空泵滤网阻塞
12、定型模漏气
1、调整加热器,降低出料快处温度
2、确认机头设计问题时,研修型腔或型芯
3、调整口模、定型模位置
4、按热胀冷缩原理,调整定型模内水流分布
5、加大冷却水,提高冷却效率
6、装正模具
7、降低挤出速度
8、换网,清理
9、清理真空冷却水道
10、清理补水管
11、清理滤网
12、调整定型模
型材内壁有气泡
1、物料含水量
2、挤出机排气真空度低
3、挤出温度偏高
4、稳定剂不足
1、干燥物料
2、清理管路,提高真空度
3、检查温度仪表,降低机头与口模温度与机筒温度
4、调整稳定剂
四、小 结
综上所述,型材生产中影响因素很多,要根据实际设备、原料及产品来确定生产工艺,在生产中各工艺参数相辅相成,调整时必须要综合考虑。
以上简要介绍了塑料异型材挤出技术的应用及影响因素,由于其技术的复杂性和技术创新的日新月异,挂一漏万,难以尽述,不当之处,敬请指正。
参考文献:
[1]李志英编,硬聚氯乙烯塑料异型材和塑料窗制造和应用。
[2]刘晓明主编,硬聚氯乙烯改性加工。
原载《天辰周刊》2002年第1期