单体液压支柱的结构设计有CAD图Word文档下载推荐.docx
《单体液压支柱的结构设计有CAD图Word文档下载推荐.docx》由会员分享,可在线阅读,更多相关《单体液压支柱的结构设计有CAD图Word文档下载推荐.docx(43页珍藏版)》请在冰豆网上搜索。
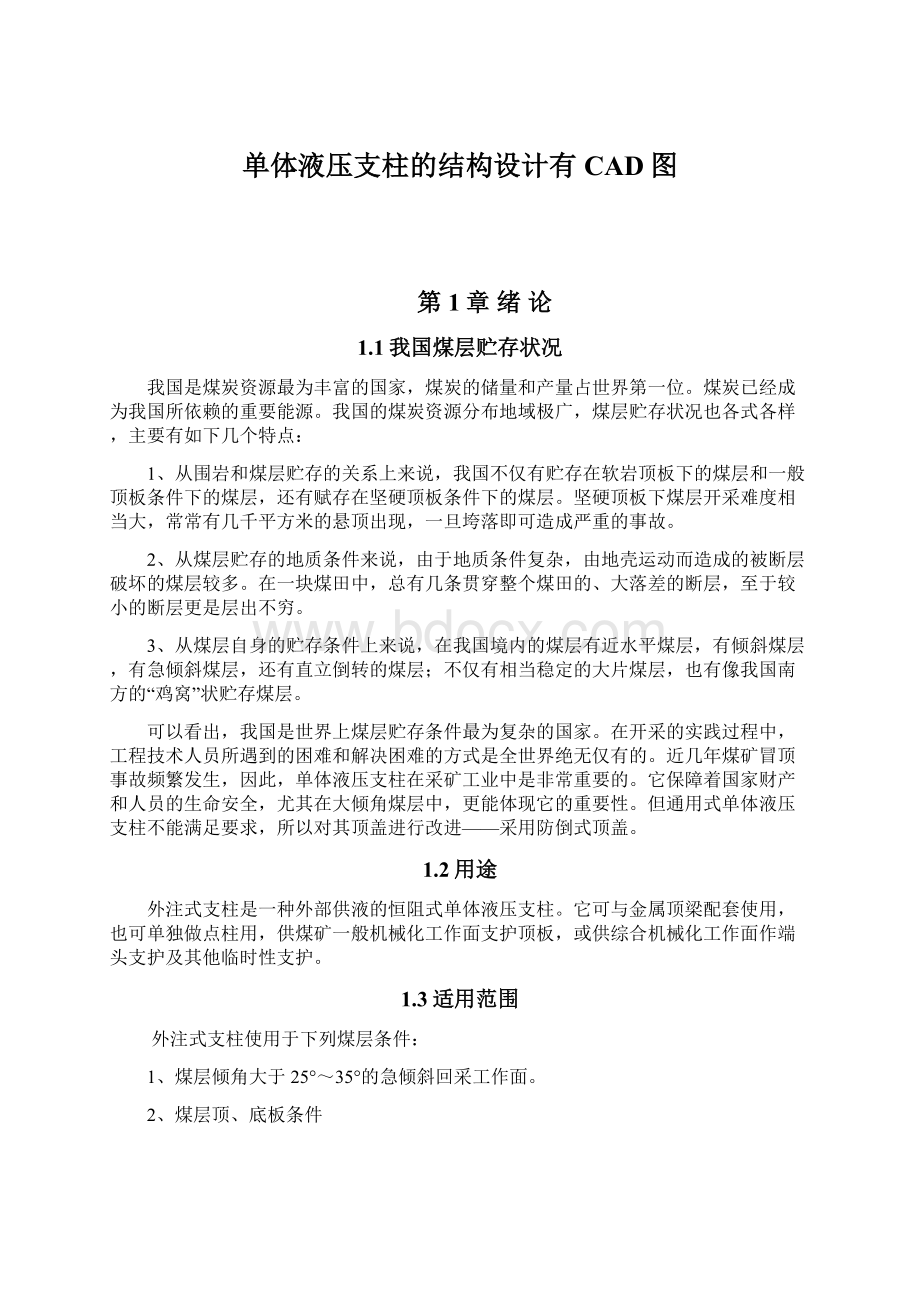
从1956年到1963年,使用单体液压支柱的产量达84.8%,五年左右时间内使用量增长了7~8倍。
国外单体液压支柱的使用情况表明,在六十年代初期技术即达到成熟阶段。
1.4.2使用单体液压支柱的突出优点
1、初撑力高
一般地,初撑力可以达到7~10t,为摩擦式金属支柱的3~10倍(摩擦式金属支柱用液压升柱装置时初撑力2~3t,不用液压升柱装置时初撑力仅1t左右)。
2、恒阻的性能
在较小的顶板下沉量情况下,支柱即可达到额定的工作阻力,并保持恒阻的特点(摩擦式金属支柱在顶板下沉量大,支柱下缩到100mm至400mm以上时才能达到最大工作阻力)。
显然,单体液压支柱能很快达到较高的工作阻力,大大改善了顶板维护状况。
3、支柱承载力均匀
初撑力大与恒阻的特点,使各支柱能较均匀的承受载荷,这是优于摩擦式金属支柱的重要特点,对保持中等稳定以下工作面顶板的完整是十分有利的。
4、支、撤速度快
单体液压支柱的升柱与降柱,靠液压系统来完成。
内注式支柱只须扳动手柄、外注式支柱用注液枪从外部注液、扳动卸载阀排液等轻微操作即可完成回撤与支设作业,其速度一般比摩擦式支柱提高一倍左右。
5、促进安全生产、降低辅助材料消耗
由于初撑力高与顶板接触严实,回撤与支设速度快,控制顶板效果好,提高了工作面推进速度,冒顶事故明显减少,促进了安全生产,相应地降低了木材消耗。
第2章单体液压支柱的结构和工作原理
分类
2.1分类
1、按型号分类
(1)通用型支柱。
用于一般条件下使用。
(2)重型支柱。
用于特殊条件下使用。
2、按升柱时工作液循环方式分类
(1)内部注液式单体液压支柱(简称内注式)。
工作液压油在体内形成闭路循环。
(2)外部注液式单体液压支柱(简称外注式)。
从泵站供给乳化液,通过注液枪注入支柱。
3、按材质分类
(1)热轧低碳合金钢单体液压支柱。
(2)冷拔低碳合金钢单体液压支柱。
(3)轻金属合金钢单体液压支柱。
我国批量生产、使用的是热轧低碳合金钢支柱。
2.2技术特征
类型及特征代号用汉语拼音大写字母表示:
D表示单体液压支柱,第一特征代号中N表示内注式支柱;
W表示外注式支柱。
第二特征代号中S代表双伸缩,无字母代表单伸缩,Q代表轻合金。
主参数用阿拉伯数字表示;
补充特征代号一般不用。
修改序号用加括号的大写拼音字母(A)、(B)、(C)……表示,用来区分类型、主参数、特征代号均相同的不同产品。
2.3压支柱的工作原理
1、工作介质
外柱式单体液压支柱工作介质为乳化液,回柱时乳化液排至工作面采空区。
2、动力来源
外注式的工作介质是由设在巷道中的泵站经高压软管、注液枪等组成的管路系统供给,并由泵站保证支柱一定的初撑力。
3、降柱方式
一般靠活柱的自重和复位弹簧降柱。
2.4压支柱的结构
DZ型单体液压支柱为外部注液的单体液压支柱。
单体液压支柱有活柱体、油缸、三用阀、顶盖、底座体、复位弹簧、手把体、活塞等主要零部件组成。
如图2.1所示:
图2.1外注式单体液压支柱装配图图2.2单体液压支柱的三维实体造型
2.5零部件尺寸的计算与选择
2.5.1给定参数
直径Φ100mm;
工作阻力300KN;
最大高度2000mm。
2.5.2油缸与活柱体
1、油缸
油缸是支柱下部承载杆件。
如图2.3所示:
图2.3油缸
(1)主要技术要求
有足够的强度,能长期承受最高工作压力以及短期动态试验压力而不会产生永久变形。
有足够的刚度,能承受活柱侧向力,而不至于产生弯曲。
内表面在活塞密封件及导向环的摩擦力作用下,能长期工作,且磨损少,几何精度高,确保活塞密封。
(2)材料
缸筒材料一般要求有足够的强度和冲击韧性,根据油缸的参数、用途和毛坯,可选用的材料是27SiMn。
(3)缸筒的计算
①立柱的工作阻力,缸内压力,缸筒内径之间的关系为
P=
D22p(2.1)
式中p——缸筒内压力,N/mm2;
D2——缸筒内径,mm;
P——立柱工作阻力,KN。
Kb=
则p=
(2.2)
式中pR——乳化液泵的工作压力;
Kb——一般在0.52~0.78之间。
=
=0.52(2.3)
初撑力=Kb×
工作阻力=0.523×
300=157KN(2.4)
②预算缸径尺寸和缸壁厚度
缸筒内压力为
p=
=38.2MPa(2.5)
式中P——立柱工作阻力300KN;
D2——缸筒内径100mm。
缸筒材料为27SiMn无缝钢管,
s=833.85MPa(2.6)
[
]=
=555.9MPa(2.7)
缸壁厚度为
=3.1mm(2.8)
考虑到缸口要车槽口和台阶,所以选用缸壁厚度为7mm。
(4)缸筒的加工要求
①缸筒内径采用H8、H9配合;
②缸筒内径D的圆度公差值可按9、10、11级精度选取,圆柱度公差值可按8级选取;
③缸筒端面T的垂直度公差值可按7级精度选取。
2、活柱体尺寸的确定
图2.4活柱体
活柱体是支柱上部承载杆件。
根据油缸的外径可以确定出活柱的内外径分别为78mm和95mm。
在外注式单体液压支柱的活柱外侧还装有限位装置,其是限制活柱升高,保证油缸与活柱具有一定重合长度,防止活柱拔出和损坏的装置。
限位装置有限位套、限位环、钢丝挡圈和限位台阶等多种形式。
缸径为100mm的DZ型支柱采用活柱上限位台阶限位。
支柱升高,活柱上限位装置与手把体接触后,如果继续供液,活柱也不再升高。
因此,限位装置必须具有一定强度,使其承受初撑力时,不至于损坏。
限位台阶高度尺寸计算过程如下
H=
mm=
mm=151mm(2.9)
式中L——立柱最大工作行程,mm;
D2——缸筒内径,mm。
2.5.3单体液压支柱三用阀和复位弹簧
1、外注式单体液压支柱三用阀的选择
三用阀顾名思义,即有三种用处的阀。
它是外注式单体液压支柱的心脏,支柱靠它的单向阀完成开柱和支撑;
靠它的卸载阀完成支柱的回收;
靠它的安全阀在支柱过载时使支柱缓慢下缩,保护支柱不致受损。
外注式支柱将三个阀组装在一起,便于更换和维修。
三用阀利用左右阀筒上的螺纹装在支柱柱头上,并用阀筒上的O形密封圈与柱头密封。
图2.5三用阀
1—左阀筒;
2—注油阀体;
3—限位套;
4—单向阀阀座;
5—压紧螺套;
6—钢球Φ8;
7—锥形弹簧;
8—卸载阀垫;
9—卸载阀弹簧;
10—连接螺杆;
11—阀套;
12—阀座;
13—O形圈Φ13×
1.9;
14—O形圈Φ28×
3.5;
15—安全阀针;
16—安全阀垫;
17—六角导向套;
18—O形圈Φ42×
19—弹簧座;
20—安全阀弹簧;
21—调压螺丝;
22—右阀筒
2、复位弹簧
采用复位弹簧降柱可加速支柱下降速度。
复位弹簧一头挂在柱头上,另一头挂在底座上,并使它具有一定的预紧力。
并且使用复位弹簧支柱的底座不能焊在油缸上,而必须活接,且采用连接钢丝与油缸连接。
复位弹簧是单体液压支柱在进行回收时,使活柱筒快速回缩的重要零件。
检验复位弹簧时,应根据支柱实际支设状况,将其拉伸到最大使用高度后保持24小时,最多允许弹簧有4mm的残余变形,这样的复位弹簧才算合格。
2.5.4单体液压支柱用锻件
外注式单体液压支柱中有5个零件是用模锻加工而成。
它们分别是顶盖、手把体、底座、活塞和柱头。
1、顶盖
本次单体液压支柱主要针对大倾角煤层的工作状况而设计的,在大倾角工作面中单体支柱的倾倒与下滑问题一直都很严重,顶板冒落甚至大面积垮落事故时有发生,严重威胁着工作面的安全生产。
改进单体液压支柱顶盖的结构将有助于改善以上几种情况,因此,我采用了防倒式顶盖。
防倒顶盖的基本结构如图2.5所示,它由顶盖底板、楔卡、挡板组成。
楔卡安装在顶盖底板导槽内。
楔卡为“L”形。
每只防倒顶盖内安装两只楔卡,每只楔卡有一个侧面带有斜度。
防倒顶盖取代普通顶盖后,通过楔卡卡住顶梁底部的π型扁钢,实现支柱与顶梁的相互联接。
由于两只楔卡均带有斜度,因而安装时可以相互砸紧。
回柱时,只须锤击楔卡的小端,使楔卡张开,脱离顶梁,便可按正常程序回拆支柱。
防倒顶盖与顶梁联接后,限定了支柱与顶梁的支设状态。
顶盖是可更换件。
它通过三个弹性圆柱销与活柱体的柱头(或接长柱筒)连接在一起,将顶板岩石的压力传递到支柱上,并利用四爪与楔卡防止顶板来压时支柱滑倒失效。
(1)尺寸的计算
楔卡的高度是由顶梁的厚度、宽度和煤层的角度所决定的;
h=a+c+b×
tanα(2.10)
式中h——楔卡的高度;
a——楔卡厚度;
c——顶梁厚度;
b——顶梁宽度;
α——煤层倾角。
其余尺寸均由自行设计而定。
如图2.6所示
图2.6防倒顶盖结构图2.7顶盖的三维实体造型图
(2)顶盖的有限元分析
利用Pro/Engineer对该零部件进行有限元分析,只要输入顶盖的最大工作阻力,就能分析出该零部件的受力情况。
并且能够通过受力情况的分布云图,很直观的看出各部分的受力情况。
下图是以顶盖为例的受力分析云图:
根据云线的颜色可以看出各部分受力情况的大小,红色受力最大,视为危险截面。
图2.8顶盖的受力分析云图
图2.9顶盖的受力分析云图
2、手把体
手把体是单体液压支柱上唯一的一个可用手抓住的零件,对搬运、支设、移动支柱非常重要。
手把体内装有防尘圈、导向环。
它通过手把体连接钢丝与油缸相连接,能绕油缸自由转动便于操作和搬运。
手把体内孔的尺寸根据油缸外径、活柱外径、手把体连接钢丝、防尘圈和导向环的尺寸确定,防尘圈和导向环的尺寸根据活柱外径选取。
手把体结构形式如图2.10所示
图2.10手把体图2.11手把体三维实体造型图
3、底座
底座体由底座、弹簧挂环、O形密封圈、防挤圈等组成。
它是支柱底部密封和承载的零件。
它通过底座连接钢丝与油缸相连接。
底座体外径由油缸内径而定,各凹槽部分分别由安放在此处的标准件的尺寸决定,而各标准件的尺寸是根据油缸内径值查表而得。
结构形式如图2.12所示。
图2.12底座体图2.13底座体三维实体造型图
4、活塞
活塞是支柱的活柱体和液压缸之间密封的零件,当支柱受力时承受一定的载荷和弯矩。
活塞上装有Y形密封圈、皮碗防挤圈、活塞导向环、O形密封圈、活塞防挤圈等。
它通过活塞连接钢丝与活柱体相连接。
活塞起活柱导向和油缸密封作用。
活塞根据密封装置形式来选用其结构形式,而密封装置则按工作压力、环境、介质等条件来选定。
(1)材料活塞材料一般不同于缸筒的材料,选用45钢。
(2)加工要求
活塞最大的外径根据油缸内径所得,但不能完全等同与油缸内径,因为活塞要延着油缸内径进行上下往复运动,所以要小于油缸内径。
活塞与活柱接触的尺寸根据活柱内径所得,其它凹槽尺寸的计算原理同手把体一样,都是根据密封结构形式来确定;
①活塞外径d对内孔D1的径向跳动公差值,按7、8级精度选取。
②端面T对内孔D1的垂直度公差值,按7级精度选取。
③外径d的圆柱度公差值,按9、10、11级精度选取。
利用Pro/Engineer的模型分析模块,能够即快又准确的计算出零件的体积和各个截面的面积。
只要给它输入该材料的密度后,就能够计算出零件的质量。
使用起来方便、快捷、准确。
下面以活塞为例进行说明
打开活塞的零件图后,在分析中点击模型分析,然后选择零件体,再输入其密度7.9×
10-6kg/mm3,完成后便输出如下数值
体积=2.34×
109mm3;
面积=2.67×
107mm2;
密度=7.9×
10-6kg/mm3;
质量=1.85kg。
图2.14活塞图2.15活塞三维实体造型图
5、柱头
柱头是支柱上安装三用阀的地方,承受和传递支柱的载荷。
柱头与活柱的连接方式为焊接,其外径可根据活柱外径确定,上端销孔尺寸则由标准件弹性销的尺寸所决定,安装三用阀的孔也由三用阀的外径确定。
柱头的结构形式如2.14所示
图2.16柱头图2.17柱头三维实体造型图
2.6单体液压支柱的橡胶件和塑料件
单体液压支柱及三用阀中所使用的各种橡胶件和塑料件共15件,详见下表2.1。
表2.1单体液压支柱的橡胶件和塑料件
项目
类别
名称
规格
材料
数量
备注
单
体
液
压
支
柱
Y形密封圈
防尘圈
O形密封圈
活柱导向环
活塞导向环
皮碗防掎圈
活塞防掎圈
底座防掎圈
—
100×
3.1
80×
97×
10×
2.5
99.4×
2×
1.5×
P228丁腈橡胶
P229
聚甲醛
1
外径×
高×
厚
厚(不切口)
三
用
阀
安全阀垫
卸载阀垫
单向阀阀垫
42×
3.5
28×
13×
1.9
6×
2
27×
14×
3
WS—520
QJ5511—1
P907
其中大流量三用阀的安全阀部分,有一特制密封圈
所谓防挤圈是指防止O形密封圈受挤的一个圈,故它在安装时应该放在O形密封圈或Y形密封圈的低压一侧。
防尘圈的作用是紧抱单体液压支柱的活柱,在支柱升降时防止煤粉进入液压缸。
Y形密封圈是单体液压支柱的活柱通过活塞和支柱油缸密封的关键零件,又是支柱在承载时的承压件。
同时在支柱回柱时,它又能使支柱的活柱快速回缩而达到回收的目的。
2.7本章小结
本章介绍了单体液压支柱的结构总体方案及工作原理。
确定了用于特殊条件下使用的重型外部注液式单体液压支柱支柱。
详细的介绍了单体液压支柱的主要零部件,以及各零部件的材料和作用,并对各个零部件进行尺寸的计算与选择。
第3章单体液压支柱结构及尺寸的验算
3.1已知设计参数
立柱初撑力:
P1=157KN
立柱工作阻力:
P=300KN
油缸外径:
D0=114mm
油缸内径:
D=100mm
活柱外径:
D1=95mm
活柱内径:
D2=78mm
支柱最大高度:
2000mm
支柱最小高度:
1240mm
液压行程:
760mm
3.2油缸稳定性的验算
验算活塞杆全部伸出并受最大同心纵向载荷的稳定性。
油缸稳定性条件为
Pk>
P即Pk=
(3.1)
式中Pk——稳定的极限力;
P——最大工作阻力;
J1——活塞杆断面惯性矩,
=2.18×
106mm4;
(3.2)
J2——缸体断面惯性矩,
=3.38×
106mm4。
(3.3)
根据
=1.2及
=0.9查极限计算图得:
立柱稳定性的极限力为
Pk=
=600KN(3.4)
立柱的最大工作阻力P=300KN
Pk可满足稳定条件上述Pk值仅当活塞杆头部距离在载荷下发生最大挠度处的距x
时才适用
x=2280
=2280
=6555mm
(3.5)
所以适用。
3.3活塞杆的强度验算
1、在承受同心最大载荷情况下油缸的初挠度
1.027mm(3.6)
式中
——活塞杆与导向套处的最大配合间隙,
=0.25cm;
——活塞杆全部外伸时,导向套前端至活塞末端间距,
=151mm;
——活塞和油缸的最大配合间隙,
=0.355mm;
——活塞杆全部外伸时,活塞杆头部销孔至油缸尾部销孔间距
+
=1971mm;
——立柱总重,
=415kg;
——油缸轴线与水平面的交角,
。
2、油缸的最大挠度
当
,
时
(3.7)
0.8×
10-3;
(3.8)
0.4×
(3.9)
1.08;
(3.10)
0.4;
(3.11)
E——钢的弹性模量,E=2.1×
105Mpa。
3、活塞杆的合成应力
(3.12)
式中A——活塞杆的断面积,
2308.7mm2;
(3.13)
W——活塞杆的断面模数,
37564.5mm2。
(3.14)
安全(3.15)
活塞杆材料为45#钢,
=360Mpa;
——一般最小取1.4。
3.4缸体强度验算
油缸壁厚验算
时,按中等壁厚缸体公式计算(3.16)
(3.17)
式中P——油缸内工作压力,P=38.2Mpa;
c——计入管壁公差及侵蚀的附加厚度,一般取c=2mm;
——强度系数,当无缝钢管时,
=1;
——缸壁厚,取22.5mm;
b——缸体材料,27SiMn无缝钢管
b=980Mpa;
——许用安全系数,一般在3.5~5范围内选取。
把上列公式化为:
(3.18)
(3.19)
所以可以安全使用。
3.5制定活塞的工艺路线
制定工艺路线的出发点,应当是使零件的加工精度(尺寸精度、形状精度、位置精度)和表面质量等技术要求能得到合理的保证。
在生产纲领已经确定为中批量生产的条件下,可以考虑采用通用机床配以专用夹具并尽量使工序集中来提高生产率。
除此以外,还应当考虑经济效果,以便使生产成本尽量下降。
1、工序的合理组合
确定加工方法以后,就按生产类型、零件的结构特点、技术要求和机床设备等具体生产条件确定工艺过程的工序数。
确定工序数的基本原则:
(1)工序分散原则
工序内容简单,有利选择最合理的切削用量。
便于采用通用设备。
简单的机床工艺装备。
生产准备工作量少,产品更换容易。
对工人的技术要求水平不高。
但需要设备和工人数量多,生产面积大,工艺路线长,生产管理复杂。
(2)工序集中原则
工序数目少,工件装,夹次数少,缩短了工艺路线,相应减少了操作工人数和生产面积,也简化了生产管理,在一次装夹中同时加工数个表面易于保证这些表面间的相互位置精度。
使用设备少,大量生产可采用高效率的专用机床,以提高生产率。
但采用复杂的专用设备和工艺装备,使成本增高,调整维修费事,生产准备工作量大。
一般情况下,单件小批生产中,为简化生产管理,多将工序适当集中。
但由于不采用专用设备,工序集中程序受到限制。
结构简单的专用机床和工夹具组织流水线生产。
加工工序完成以后,将工件清洗干净。
清洗是在80—90°
C的含0.4%—1.1%苏打及0.25%—0.5%亚硝酸钠溶液中进行的。
清洗后用压缩空气吹干净。
保证零件内部杂质、铁屑、毛刺、砂粒等的残留量不大于200mg。
2、工序的集中与分散
制订工艺路线时,应考虑工序的数目,采用工序集中或工序分散是其两个不同的原则。
所谓工序集中,就是以较少的工序完成零件的加工,反之为工序分散。
(1)工序集中的特点
使用设