上海中心大厦钢巨柱制作工艺及质量控制毕业论文正文1 精品文档格式.docx
《上海中心大厦钢巨柱制作工艺及质量控制毕业论文正文1 精品文档格式.docx》由会员分享,可在线阅读,更多相关《上海中心大厦钢巨柱制作工艺及质量控制毕业论文正文1 精品文档格式.docx(28页珍藏版)》请在冰豆网上搜索。
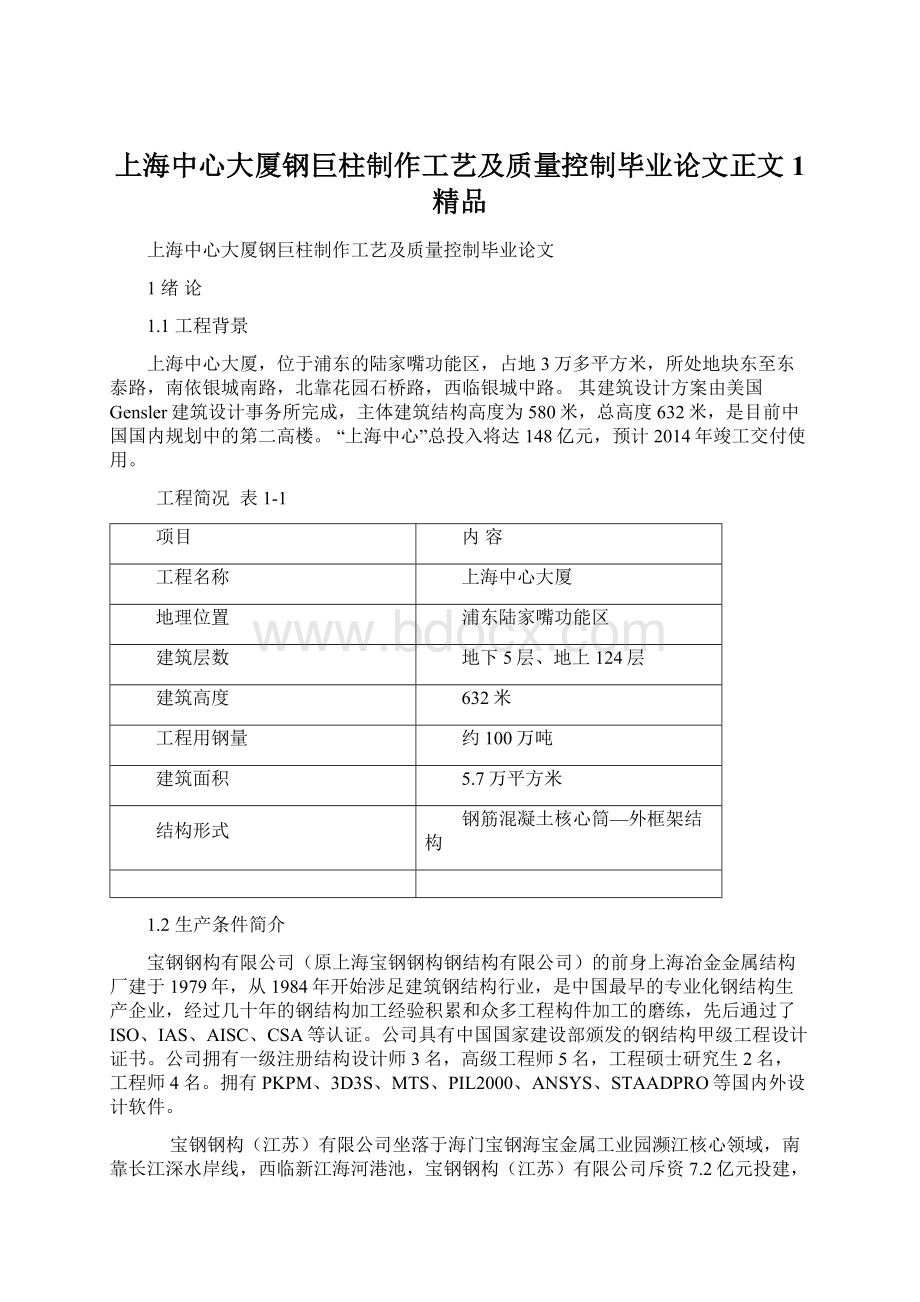
(1)号料前,确认材质和熟悉工艺要求,根据排版图、下料加工单和零件草图进行号料。
(2)号料时,使构件受力方向与钢板轧制方向一致。
(3)划线作记号时不得使用凿子一类的工具,少量的样冲标记其深度应不大于0.5mm,钢板上不应留下任何永久性的划线痕迹。
(4)划线精度
表2-1
允许偏差
基准线,孔距位置
≤0.5mm
零件外形尺寸
≤1.0mm
(5)划线号料后应按本公司质保手册的规定做好材质标记的移植工作。
2.3切割和(刨)铣削加工
(1)切割工具选用
a.条形钢板:
可采用NC多头火焰切割机或半自动火焰切割机。
b.一般零件板:
c.厚度小于9mm的钢板:
可采用剪板机剪切。
d.H型钢:
可采用圆盘锯,冷锯或带锯。
e.BH钢:
可采用自动火焰锁口机。
(2)切割前应清除母材表面的油污、铁锈和潮气;
切割后应去除熔渣,对于组装后无法精整的表面,如弧形缺口内表面,应组装前进行处理。
(3)厚板切割前的预热和切割后的表面检查是保证焊接质量、构件质量的重要措施。
厚板切割前根据规范要求进行预热,气割后进行切割断面的MT和VT检查,特厚钢板焊接应去除表面硬化层,避免切割面由于淬硬而产生微裂纹。
图2-1特厚板焊接示意图
(4)气割的允许偏差表2-2
零件的宽度和长度
±
1.0mm
切割面不垂直度
≤0.05t且≤2.0mm
割纹深度
0.2mm
局部缺口深度
(5)火焰切割后产生的变形(如旁弯等),应矫正合格后才能流入下一道工序。
(6)(刨)铣削加工的允许偏差表2-3
零件宽度和长度
加工边直线度
L/3000且≤2.0mm
相邻两边不垂直度
加工面不垂直度
≤0.025t且≤0.5mm
加工面粗糙度
Ra<50um
(7)筋板锁口处理
筋板板厚t≤19mm时,R=20mm;
筋板板厚t≥19mm时,R=35mm。
2.4制孔
(1)高强螺栓孔、一般螺栓孔和地脚螺栓孔的钻孔优先采用数控钻床,也可采用划线钻孔的方法,采用划线钻孔时,孔中心和周边应打出五梅花冲印,以利钻孔和检验。
钻孔精度表2-4
直径
0~+1.0mm
圆度
2.0mm
垂直度
≤0.03t且≤2.0mm
(2)箱形柱内隔仓板上的灌浆孔允许由NC切割机切割而成;
楼层梁上的方形或圆形设备孔由全自动火焰锁口机切割而成。
精度要求参照气割精度要求。
(3)孔位的允许偏差表2-5
名称
示意图
允许偏差(mm)
1
孔中心偏移△L
-1≤△L≤+1
L△L
同组孔间距偏移△P1
-1≤△P1≤+1
2
两组孔间距偏移△P2
P1+△P1
-2≤△P2≤+2
P2+△P2
3
孔的错位e
e≤1
e
△≥-3
4
孔边缘距△
L+△
L应不小于1.7d
L+△d
或满足设计要求
2.5组装
(1)组装前,熟悉图纸,仔细核对零件的几何尺寸和各零件之间的连接尺寸;
熟悉相应的制造工艺和焊接工艺,明确各构件的加工精度和焊接要求。
(2)装配用的工具(卷尺,角尺等)必须检验合格,样板和样条在使用前也应仔细核对,组装用的平台和胎架应符合构件装配的精度要求(胎具的水平度应在±
1.0之间)并具有足够的强度和刚度,使用前应经技术质量部认可合格。
(3)构件组装要按照工艺流程进行,零件连接处的焊缝两侧各50mm范围以内的铁锈、油污等应清理干净。
(4)BH钢的翼板和腹板下料后应在BH拼装机上进行拼装,或在拼装胎架上进行拼装,拼装后按工艺进行焊接和矫正,在翼腹板上标出中心线的位置作为构件组装时的基准。
(5)柱接头承压面应进行铣削加工,以保证接触面区域大于柱截面的75%,柱的铣削加工面垂直于柱轴心线。
(6)厚板构件组装时,根据板厚的实际尺寸,调整装配位置尺寸。
(7)构件组装完毕后应进行自检和互检,准确无误后再提交专检人员验收,若在检验中发现问题,应及时进行修理和矫正。
(8)构件组装的精度表2-6
项
次
项目
简图
T形接头的间隙e
T≥16e≤2.0
T﹤16e≤1.0
搭接接头的间隙e
L+△Le
e≤1.0
长度△L
△L:
5.0
T≤16e≤1.5
对接接头的错位e
16﹤T﹤30e≤T/10
(T为较薄板厚)
T≥30e≤3.0
对接接头的间隙e
手工焊0﹤e≤4.0
(无衬垫板时)
埋弧焊0﹤e≤1.0
气保焊0﹤e≤1.0
手工焊0﹤e≤3.0
埋弧焊同上
e
气保焊同上
对接接头的间隙△a
埋弧焊,手工焊、
5
(带衬垫板时)
气保焊
a+△a
-2.0≤△a≤2.0
a+△a
6
坡口角度△a
△a=±
2.5°
气保焊、手工焊
7
有衬垫-2≤△a≤1
坡口钝边△a
无衬垫-2≤△a≤2
埋弧焊-2≤△a≤1
t1≥t2时:
隔板柱t1
e≤2t1/15,且e≤3
8
接头错位e
e翼
缘梁翼缘
t1<t2时:
t2
e≤t1/6,且e≤5.0
9
水平隔板电渣焊
-2.0≤△a≤2.0
间隙偏差△a
高度△h
h≤2000,
-1≤△h≤2.0
10
h>
2000,
be
-2≤△h≤3.0
翼板垂直度△
△≤b/100且≤3.0
腹板中心偏移e
e≤2.0
箱形柱截面高度△h
L1
宽度△b
-1≤△b≤2.0
11
垂直度△
L2
△<
h/200且≤2.0
对角线差
b+△b
L1-L2≤2.5
两腹板至翼板中心
连接处
12
线距离△a
-0.5≤△a≤+0.5
其他处
a+△aa+△a
-1.0≤△a≤+1.5
13
牛腿与柱连接
L
L≤300,△≤1.0
立面倾斜△
△
L>
300,△≤2.0
14
L≤300,△1≤1.0
平面倾斜△1
L△1
300,△1≤2.0
L1+△L1
L2+△L2
L3+△L3
柱长度△L
L<
10m,△L≤2.0
15
L≥10m,△L≤3.0
柱牛腿间距
△Ln
-2.0≤△Ln≤+2.0
焊接组装件端部
-3.0≤a≤+3.0
偏差a
16
aa
17
加劲板或隔板倾
-2.0≤a≤+2.0
斜偏差a
19
连接板、加劲板
间距或位置偏差a
a
20
箱体旁弯e
e≤L/1500,且≤5.0
箱体扭曲k
k≤6H/1000,且≤5.0
2.6构件标记
(1)构件编号的一般要求
a.钢印深小于0.5mm,单字体10mm高,8mm宽。
在油漆后用漏字板及醒目油漆标记构件表面。
标高标记
b.每根立柱上必须标出柱子的中心线(4面)和1米标高线。
另外还需把柱子轴心线引到柱底板的四个侧面,以便安装定位。
同时必须作好方向标记,见图2-2。
柱中心线
图号
构件号
图2-2柱标记图
c.如图2-3所示,梁的构件编号的朝向为两个箭头指向能够看得到的腹板面及上翼面,位置位于距左端1.0米处。
图2-3梁标记图
d.钢印的内容为:
图号+构件号,敲钢印时应认清方向。
(2)构件编号的方法
a.如图2-4所示,柱子构件编号的朝向为两个箭头指向能够看得到的两个面,位置位于距柱子下端1米处。
b.如图2-5所示,支撑(水平支撑)构件编号的朝向为箭头指向能够看得到的腹板面,位置位于距左端1米处。
c.如图2-5所示,支撑(垂直支撑后拖上或下二字,位置位于距左端1米处。
撑)构件编号的朝向为箭头指向能够看得到的腹板面。
图2-4柱正面标记位置图
图2-5垂直支撑图
(3)标记的颜色应醒目区别基色
a.主标记(图号、构件号):
见标记图。
其中钢印位置为:
柱为两侧面方向标记处;
梁、桁架为左侧腹板及上表面。
b.安装标记:
柱的安装中心线(两侧)、1米标高位置线、底板中心线(四侧)。
3巨柱制作工艺方案
3.1巨柱简介
地下层巨柱全长25.3米,由标高-25.4米(B5层)至标高+0.0(Z1-01层向上1.0米),标准截面为4.1米宽×
2.6米高。
全柱的净重约240吨。
柱本体的基本板厚为55mm,底板厚160mm,如图3-1。
图3-1巨柱截面图
3.2构件分段和加工的总体思路
(1)按工地起重能力要求,将巨柱分为两段制作,地下一节柱13.1米长、净重约130吨,地下二节柱12.3米长、净重约110吨。
图3-2地下一节柱图图3-3地下二节柱图
(2)以现场提供的实际锚栓位置尺寸,在底板上钻孔钻,组装底板时,消除现场锚栓位置误差,使巨柱安装一步到位。
3.3巨柱制作流程(流程中的*号为检验停止点)
原材料进厂
主料复试*
检验,矫正*
表面除锈处理
柱底板
柱本体
牛腿
下料、切割
组合BH
按现场实际锚栓位置钻孔
组合BH
焊接、矫正、栓钉焊接,UT检验*
钻孔、检验*
检验*
设置胎架
第一箱组合,打底焊
第二箱组合,打底焊
半自动焊接、翻身焊接、矫正,UT检验*
标记中心位置、铣本体上、下端口
安装牛腿、焊接、UT检验*
安装柱底板、焊接、UT检验*
包装、发运*
标记构件、安装符号,参与预装
3.4巨柱制作难点和解决方法
(1)巨柱制作难点
①巨柱扭曲控制;
②巨柱截面尺寸控制;
③巨柱安装位置控制;
④厚板焊接变形。
(2)解决方法
①扭曲是大型箱体制作的首要难点。
巨柱箱体板虽较厚,但箱体的尺寸较大,使板的宽厚比大,从而使箱体的抗扭能力较差,而厚板焊接更增加变形量。
为防止出现较大扭曲有必要采取以下措施:
a.部件首先要合格,制作板制BH型钢,矫正BH型钢的旁弯在L/1500,且小于3mm。
组合巨柱时要确认3根BH型钢的旁弯在同向。
b.制作胎架要测平,部件放置后要调平。
c.组合巨柱本体时,要设置工艺隔板。
d.将合格范围内构件扭曲消化在底板安装上。
②巨柱在下料时考虑焊缝收缩量。
上、下节柱的端口处设置工艺隔板来控制端口的尺寸。
尺寸检验在每步制作过程中进行。
构件的长度放余量,本体焊接完成后铣削端口来定长。
③在焊接工艺上优化焊接顺序,多次构件翻身,焊接过程中及时采用反变形措施,避免大坡口焊缝一次完成。
3.5巨柱制作工序
(1)部件准备
①牛腿准备:
下料考虑长度、焊接收缩余量。
组合焊接完成后矫正、探伤。
以牛腿上翼板为基准划线、钻孔。
切割坡口,坡口位置向上。
图3-4牛腿加工流程图
②隔板和工艺隔板的准备:
下料后的隔板四边铣削,检验对角线尺寸之差≤3mm。
图3-5牛腿加工流程图
③本体BH柱的制作:
巨柱由3根大型板制BH型钢组合而成,因此首先要保证板制BH型钢的制作质量。
a.翼板下料后矫正旁弯≤3mm,并观察、调正、翻身使旁弯处于同向。
b.在胎架上组合板制BH型钢。
控制BH型钢扭曲≤3mm。
c.焊接组合板制BH型钢要垫实各支撑点,多次翻身焊接,矫正变形。
图3-6本体BH柱加工流程图
(2)巨柱组装
a.组装胎架经测量后调平,安放BH型钢部件。
BH型钢上划腹板、隔板安装位置线。
先安装隔板,后安装巨柱腹板(腹板内侧已焊接栓钉)。
控制端口尺寸及端口对角线误差。
BH型钢与腹板间部分打底焊接。
焊接隔板、工艺隔板与腹板的焊缝。
图3-7巨柱组装图一
b.安装第二根板制BH型钢,第二根板制BH型钢的旁弯方向同第一根。
检测端口平齐、间距和对角线尺寸。
图3-8巨柱组装图二
c.对组件进行稳定加固,按画线位置安装隔板和巨柱腹板。
主要控制端口尺寸及端口对角线误差。
焊接隔板与工艺隔板的焊缝。
图3-9巨柱组装图三
d.安装第三根板制BH型钢,旁弯方向同第一根。
打底焊接。
加固本体,用翻身架吊离胎架,翻身准备半自动焊接箱体纵缝。
图3-9巨柱组装图四
e.垫平组合构件,在构件的翼板间加支撑。
按焊接工艺进行焊接,预热后,正面纵缝完成1/3焊高后,翻身焊接另一面纵缝。
当另一面纵缝焊接完成1/3焊高后,矫正BH型钢腹板的焊接变形,使其反变形约2度,即720mm高的腹板向外偏25mm左右。
完成焊缝焊接。
矫正腹板。
再翻身构件,同样处理反变形,完成焊接工作,矫正构件。
图3-10构件焊接图
图3-11构件变形控制图
f.构件上端口腹板开锁口,焊接现场柱对接的衬垫。
按巨柱翼板上中心线定铣端口截面线,用对角线法验证截面线与本体垂直,以牛腿隔板为基准铣削上端口。
以上端口为基准定下端口位置,下端口开坡口。
焊接箱体外部栓钉、检验。
g.巨柱的中心面调水平,将柱微量扭曲消化在柱底。
以上端口为基准在巨柱腹板上画出牛腿、墙板位置线。
图3-12牛腿墙板尺寸定位图
h.安装牛腿、墙板连接板。
焊接牛腿及墙板连接板,矫正。
焊接过程中、制作完成后的构件在墙板位置均设墙板距离、变形控制件。
图3-13墙板安装图
i.复核柱底板孔位,安装柱底板。
以吊线方法确定底板四周的轴线位置,钢印标记。
柱底板的安装工作一般是在牛腿安装前进行,视现场地脚螺栓尺寸提供时间而定。
图3-14柱底板安装图
j.补全构件外部栓钉,清理构件表面,按主视图位置确定构件安装位置,钢印标记构件号、标高位置线、轴线(双向),将轴线位置引至底板厚度向。
按规范要求构件检验。
准备预装。
4巨柱的开洞与处理
在制作图上已标明的孔洞,下料时按图纸开洞。
如需在工地开孔的按现场图纸在工地现场开孔。
开孔后的补强方案如下:
孔边距梁段距大于梁高的钢板可利用火焰切割机,型钢上可利用自动爬行切割机。
方孔的四角应钻孔以防切割时伤及母材,厚板切割需预热。
构件开孔的一般的补强方式为:
(1)用环形加劲肋板补强;
(2)用套管补强;
(3)用加劲肋补强。
图4-1构件开洞补强图
开孔及补强时应考虑下列因素:
(1)不应在隅撑范围内设孔。
(2)当圆孔直径小于或等于hb/3时,孔边可不补强。
当圆孔直径大于hb/3时,可视具体情况选用上述b.款1~3中任何一种补强方法均可。
(3)补强板件应采用与母材强度等级相同的钢材。
5结语
按照上述工艺制作的巨形钢柱,在制作完成后经检查,均符合设计及质量验收规范的要求,经在现场安装后,厂房各部位连接良好,进一步证明了制作工艺的可行性,为以后制作此类钢柱积累了宝贵经验。
钢结构制作质量决定着钢结构能否达到设计要求的使用功能,钢结构制作涉及多学科、多专业,控制要点多,隐蔽工程多,制作技术复杂,质量控制难度大,在钢结构制作过程中,只有对影响质量的因素进行全过程、全方位控制,才能达到满意的效果,才能确保工程质量。
参考文献
【1】《钢结构工程施工质量验收规范》(GB50205-2001)
【2】《钢结构制作工艺规程》(DBJ08-16-95)
【3】《建筑钢结构焊接规程》(JGJ81-2002)
【4】《高层民用建筑钢结构技术规程》(JGJ99-98)
【5】杨国正.钢结构制作过程质量控制要点.施工技术,2011-06
【6】尹卫泽等.深圳北站钢结构构件制作及安装技术,2010-08
【7】宝钢钢构.上海中心大厦设计图纸及设计说明文件
致谢
经过半年的忙碌和工作,本次毕业论文已经接近尾声,作为一个高职学生的毕业设计,由于经验的匮乏,难免有许多考虑不周全的地方,如果没有导师的督促指导,以及一起工作的宝钢钢构同事及师傅的支持,想要完成这个设计是难以想象的。
自2011年12月,我在宝钢钢构(江苏)有限公司进行实习工,恰逢公司中标上海中心大厦项目,参与该工程地下层钢巨柱的制作流程过程,亲自体验了钢结构的制作与生产过程,也是本论文的选题之所在。
论文的完成首先要感谢我的导师谢云飞老师。
谢老师平日里工作繁多,但在我做毕业设计的每个阶段,从查阅资料到制作工艺的确定和修改,中期检查,后期完善,工艺指导书规范等整个过程中都给予了我悉心的指导。
我的工艺指导书较为复杂繁琐,其中图形较多,但是谢老师仍然细心地纠正图纸中的错误。
除了敬佩谢老师的专业水平外,他的治学严谨和科学研究的精神也是我永远学习的榜样,并将积极影响我今后的学习和工作。
其次要感谢装配作业区的领导和同事对我无私的帮助,特别是在工作流程制作方面,正因为如此我才能顺利的完成设计,我还要感谢我的母校——南通航院,是母校给我们提供了优良的学习环境。
另外,我还要感谢那些曾给我授过课的每一位老师,是你们教会我专业知识。
在此,我再说一次谢谢!
谢谢大家!