9组机器人项目报告Word文档格式.docx
《9组机器人项目报告Word文档格式.docx》由会员分享,可在线阅读,更多相关《9组机器人项目报告Word文档格式.docx(14页珍藏版)》请在冰豆网上搜索。
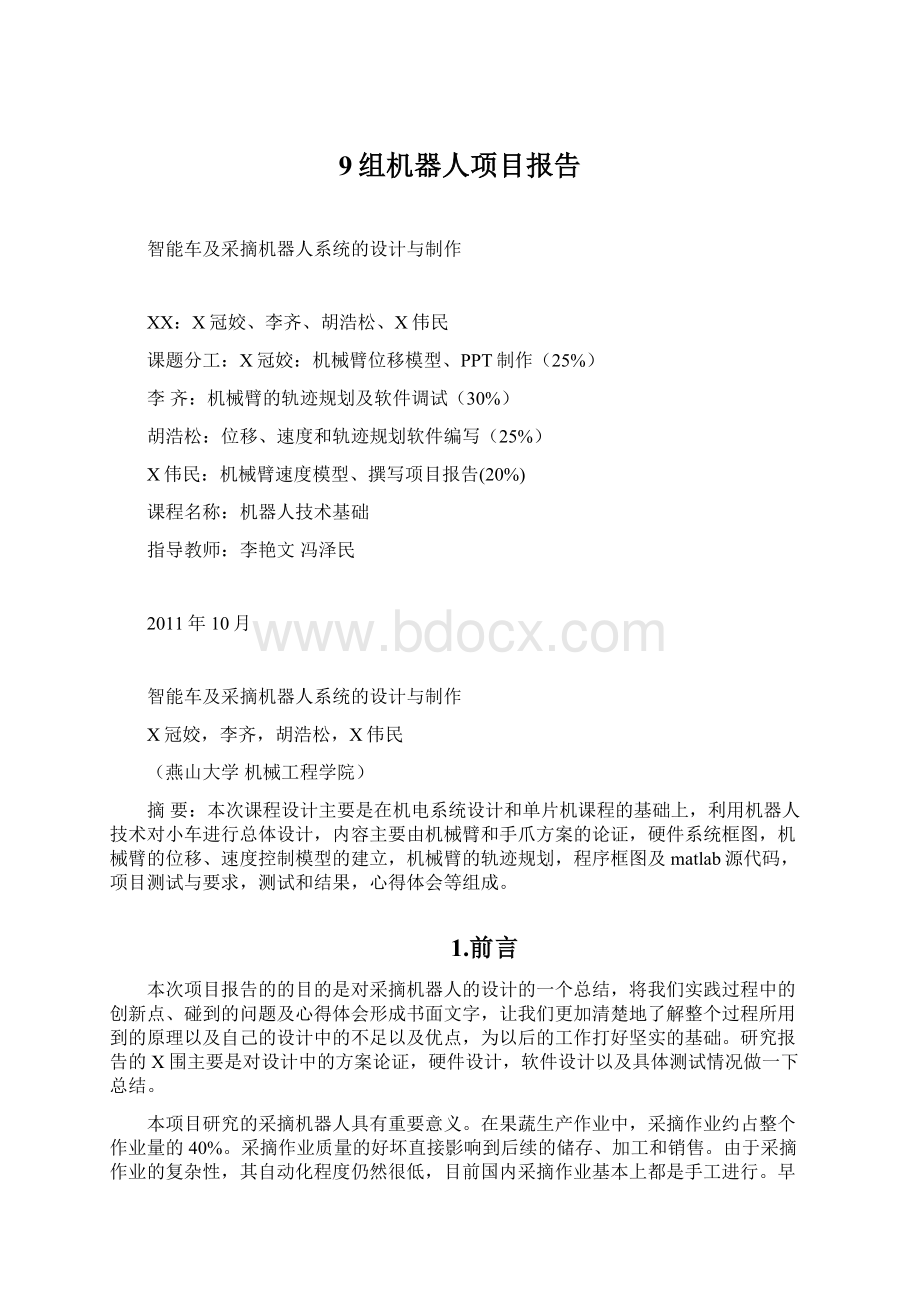
本项目研究的采摘机器人具有重要意义。
在果蔬生产作业中,采摘作业约占整个作业量的40%。
采摘作业质量的好坏直接影响到后续的储存、加工和销售。
由于采摘作业的复杂性,其自动化程度仍然很低,目前国内采摘作业基本上都是手工进行。
早在20世纪70年代,欧美国家和日本就开始了对苹果、柑桔、番茄、西瓜和葡萄等采摘机械臂的研究。
1983年,美国研制出了第一台番茄采摘机械臂。
随着农业机械化的发展,各国对机械臂的研究都取得了长足的发展。
我国甚至已制造出基于神经网络的采摘机械臂。
这次项目是大学所学课程的一个综合运用,使学生更好的掌握和运用机电专业的相关知识。
本次项目的预期结果是让智能车及采摘机器人能够按照事先给定的要求完成任务,即能将球抓取并放到指定位置。
2.方案论证
各功能单元的方案论证主要包括机械臂运动形式的选择,手爪运动形式的选择和驱动方式的确定。
这些因素对采摘机器人能否高效地、精确地、低功耗地完成任务有至关重要的影响,因此要慎重抉择。
2.1机械臂的运动形式
根据主要的运动参数选择运动形式是结构设计的基础。
典型机器人系统机械臂的运动形式有五种:
圆柱坐标型、极坐标型、直角坐标型、关节型、SCARA型。
课题组从中选取两方案对比得出最有方案。
方案一:
极坐标型。
臂部由两个轴线垂直的转动副组成。
产生绕基座轴Y的转动和绕关节轴Z的摆动。
其手臂可作绕Z轴的俯仰运动,能抓取地面上的物体。
方案二:
关节型。
由动力型旋转关节和前、下两臂组成。
关节型机器人以臂部各相邻部件的相对角位移为运动坐标。
动作灵活,所占空间小,工作X围大,能在狭窄空间内饶过各种障碍物。
方案示意图如下:
图1各方案图示
方案一占地空间较大,且可达工作空间狭小;
方案二为平面2R机械手,不动作时是可将手臂折叠,占地空间小,可达工作空间为两连杆长为半径的圆。
因此经对比优先选择方案二。
2.2手爪的运动形式
手爪用于抓取物体,并进行细微操作。
不同的抓取方式决定手爪的结构和自由度。
因为对象为球形果实,故手爪采取夹持形式。
回转型。
当手爪夹紧和松开物体时,手指做回转运动。
当被抓物体的直径大小变化是,需调整手爪的位置才能保持物体的中心位置不变。
平动型。
手指由平行四杆机构传动,当手爪夹紧和松开物体时,手指姿态不变,做平动。
和回转型手爪一样,夹持中心随被夹物体直径的大小而变。
方案三:
平移型。
当手爪夹紧和松开工件时,手指做平移运动,并保持夹持中心固定不变,不收工件直径变化的影响。
a)b)c)
图2各方案图示
通过比较,考虑到制作成本及制作难易程度,取简单合理之方案,即方案一,并将其进一步简化,将两手指的固连处缩至为一点,具体造型可参见实物制作。
2.3驱动形式的确定
机械臂的驱动与控制方式也要结合生产工艺的要求来选择,选用原则为控制性能好、体积小、维修方便、成本低。
舵机就是能够转舵并保持舵位的装置。
由于它控制简单,编程任务量小,故我们一致选取舵机驱动。
图3舵机
3.硬件设计
1.
2.
3.
3.1硬件系统框图
核心部分为AT89S52,它发出控制信号,驱动舵机进行转角,舵机带动与它固连的机械臂进行转动。
安装在手爪头部的红外传感器检测果实位置,并将信息传达给单片机。
3.2设计要求数据
承球台与黑色迹线的距离:
270mm
小球高度:
280mm
小车车身与地面距离:
120mm
舵机主轴与车板高度:
60mm
黑白线检测传感器距舵机距离:
30mm
小车车身长度:
300mm
数据与设计的内在联系:
(1)承球台距小车一侧的黑色迹线的距离为270mm,而小车黑白线检测传感器距舵机是30mm,说明机械手臂必须可以伸出车身X围去抓球,伸出距离的多少,如何去实现伸出动作在设计机械手臂时必须仔细考虑。
(2)车身的布局需要慎重考虑,由于手臂自身有一定的重量,如何合理安排手臂在车身上的安装位置,是小车可以正常行进而不至于发生翻车的危险。
3.3机械臂安装位置及尺寸确定
图4
图中单位为毫米。
假设α为30°
,则由几何关系可确定两连杆的最短长度(图示情况即为最短),这里我们取两连杆等长均为260mm。
3.4机械臂的三维建模
图5机械臂的三维效果图
4.软件设计
4.1基本参数
4.1.1初始位姿
图6初始位姿
4.1.2过渡位姿
图7过渡位姿
4.1.3抓取位姿
图8抓取位姿
4.1.4机械臂连杆参数
运用D-H法建立连杆之间的运动关系
连杆序号
ai-1
αi-1
di
θi
关节变量
初始值
1
θ1
150°
2
260
θ2
-60°
3
90°
-
表1机械臂连杆参数
4.2位移模型的建立
4.2.1各齐次变换矩阵
symst1t2
T10=[cos(t1)-sin(t1)00;
sin(t1)*cos(0)cos(t1)*cos(0)-sin(0)0;
sin(t1)*sin(0)cos(t1)*sin(0)cos(0)0;
0001];
T21=[cos(t2)-sin(t2)0260;
sin(t2)*cos(0)cos(t2)*cos(0)-sin(0)0;
sin(t2)*sin(0)cos(t2)*sin(0)cos(0)0;
T32=[cos(t3)-sin(t3)00;
sin(t3)*cos(pi/2)cos(t3)*cos(pi/2)-sin(pi/2)-260;
sin(t3)*sin(pi/2)cos(t3)*sin(pi/2)cos(pi/2)260*cos(pi/2);
T30=T10*T21*T32;
4.2.2中间位姿到过渡位姿
x=260;
y=260;
f1=x-T30(1,4);
f2=y-T30(2,4);
[t1,t2]=solve(f1,f2,t1,t2)
t1=vpa(t1/pi*180,6)
t2=vpa(t2/pi*180,6)
运算结果为:
t1=90.0.
t2=0.180.
4.2.3过渡位姿到抓取位姿
x=300;
y=100;
t1=-34.110570.9803
t2=-164.909-15.0911
4.3雅可比矩阵及速度模型的建立
4.3.1我们利用矢量积法来构造雅可比矩阵。
0001]
T21=[cos(t2)-sin(t2)0-170;
t3=0
sin(t3)*cos(pi/2)cos(t3)*cos(pi/2)-sin(pi/2)-130;
sin(t3)*sin(pi/2)cos(t3)*sin(pi/2)cos(pi/2)130*cos(pi/2);
T31=T21*T32;
T30=T10*T21*T32;
T20=T10*T21;
z1=T10(1:
3,3);
z2=T20(1:
p1=T31(1:
3,4);
p2=T32(1:
r1=T10(1:
3,1:
3);
r2=T20(1:
p11=cross(z1,r1*p1);
p22=cross(z2,r2*p2);
j=[p11p22;
z1z2]
j=
[-sin(t1)*(-170+130*sin(t2))+130*cos(t1)*cos(t2),130*cos(t1)*cos(t2)-130*sin(t1)*sin(t2)]
[cos(t1)*(-170+130*sin(t2))+130*sin(t1)*cos(t2),130*cos(t1)*sin(t2)+130*sin(t1)*cos(t2)]
[0,0]
[1,1]
4.3.2各位姿的雅可比矩阵
当t1=90,t2=0时,雅可比矩阵为
-260.00000.0000
260.0000260.0000
00
1.00001.0000
当t1=70.9803,t2=-15.0911
j=-43.3261205.4828
-234.7604-159.3010
4.3.3操作速度模型
symsq1q2v1v2
v=[v1;
v2;
0;
0];
q=[q1;
q2];
je=j*q;
f3=v(1,1)-je(1,1);
f4=v(2,1)-je(2,1);
[q1,q2]=solve(f3,f4,q1,q2)
q11=vpa(q1,3);
设置精度
q22=vpa(q2,3)
q11=-.289e-2*v1-.373e-2*v2
q22=-.786e-3*v2+.426e-2*v1
4.4各关节轨迹规划
我们可以采用任意平滑函数作为关节差值函数,但由于平面2R机械手只能确立四个约束方程,因此采用三次多项式插值法进行关节的轨迹规划。
4.4.1中间位姿到过渡位姿的关节轨迹规划
关节角1:
初值150终值90
a0=150a1=0a2=-20a3=4.4444
图9过渡位姿关节1轨迹规划
关节角2:
初值-60终值0
a0=-60a1=0a2=20a3=-4.4444
图10过渡位姿关节2轨迹规划
4.4.2过渡位姿到抓取位姿的关节轨迹规划
初值90终值70.9803
a0=90a1=0a2=-6.3399a3=1.4089
图11过渡位姿关节1轨迹规划
初值0终值-15.0911
a0=0
a1=0
a2=-5.0304
a3=1.1179
图12过渡位姿关节2轨迹规划
5.具体测试情况
由于机械臂材料短缺,采摘情况只能在三维软件里进行模拟仿真,经过验算,初步证明所建模型正确使用。
接下来就要等待实体的检验了。
6.项目心得
在这次机械臂设计过程中我们都深刻体会到了团队合作的力量。
或许是因为时间比较紧X的缘故吧,也或者是这次的项目是紧接着课程完成就开始了,使本来就对于机器人基础知识掌握的不是很好的我明显开始感觉吃力。
但是还好有大家一起帮助,我们的项目顺利完成。
在这次项目中,收获了很多,通过全程参与机械臂的制作,使我几乎不用复习便可以去完成几天后的机器人基础的考试;
同时手臂设计过程中,如何选材,如何构造,让我们进一步熟悉了机械原理和大学物理的一些知识要点;
三维仿真,坐标系建立,种种以前觉得太麻烦的事情在亲自动手之后也不会在觉得怵头了。
这样刚刚好,将知识完全的融入到了现实当中,自己考虑成本,自己动手制作样品,自己完成位姿、速度控制,自己检查作品实现的可行性,完全的依靠自己,让自己的成就感油然而生。
以后的参加设计工作的我们或许就是这样吧,有些东西其实可以按部就班的,因为自己曾经完成过,所以再去做起来便不再会感觉我所是从。
谢谢老师们这几天的辛苦,或许这种感谢不是来的那么深刻,但是当你看到每一位老师总是在我们走之后才离开的话,就会有一些感动吧。
总之这次项目,让我体会到了原来我所学习的东西是这样运用在现实当中的,如此具象的呈现在众人面前。
7.参考文献
1.X建民.工业机器人.:
理工大学,2003.
2.JorgeAngels.机器人机械系统原理、理论和算法.:
机械工业,2004.
3.X印越.机器人技术.:
电子工业,2000.
4.XX大学编写组.工业机械手设计基础.XX:
XX科学技术,2005.
5.熊有伦.机器人技术基础.XX:
华中科技大学,2002.