方形盒注塑模设计讲解Word格式文档下载.docx
《方形盒注塑模设计讲解Word格式文档下载.docx》由会员分享,可在线阅读,更多相关《方形盒注塑模设计讲解Word格式文档下载.docx(16页珍藏版)》请在冰豆网上搜索。
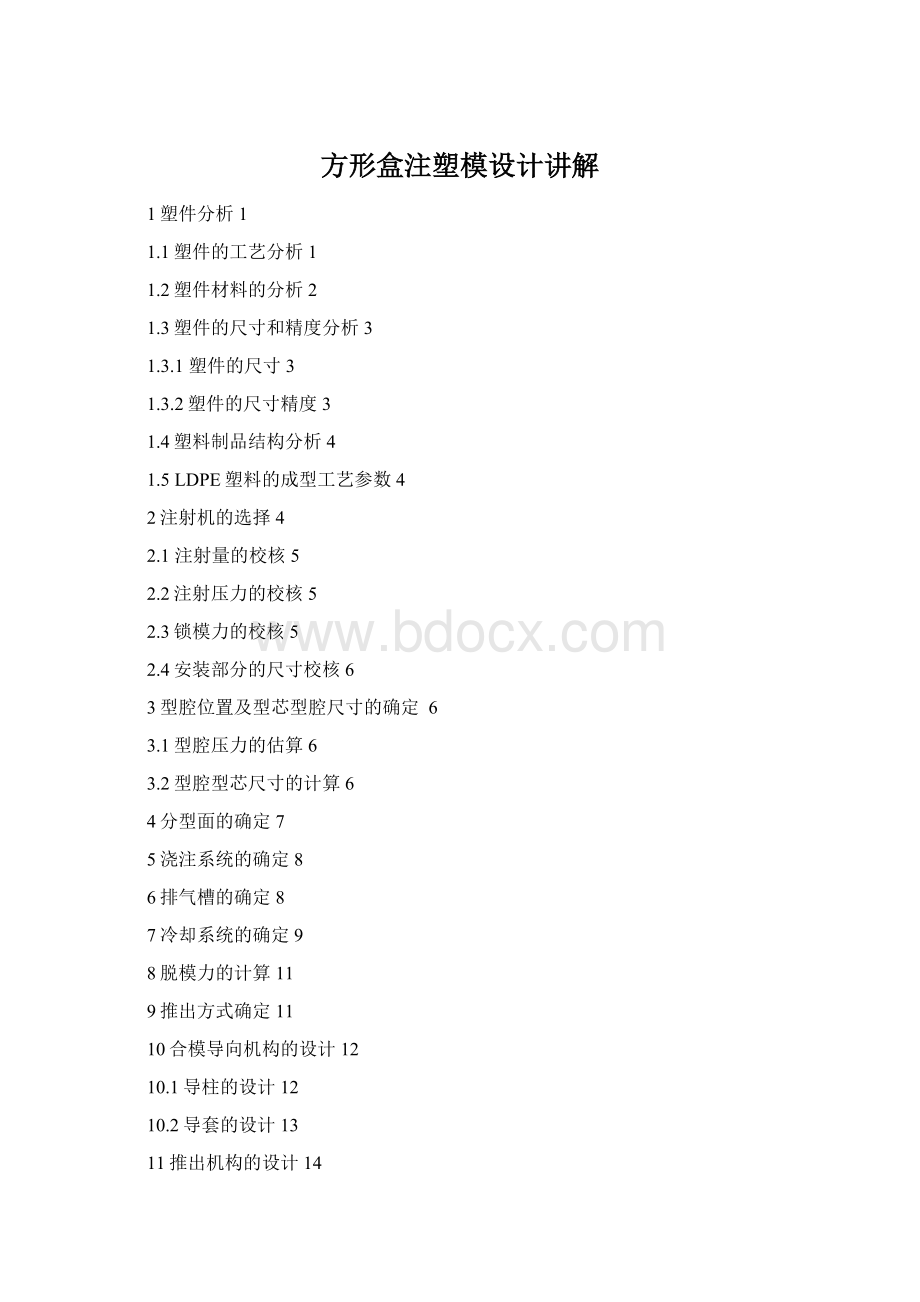
3
V1二S1I=369625=92400mm
V2二S223=822223=41492mm
S1=8444二3696mm2
V二y-V2=92400-41492=50908mm3所以,塑
该塑件的体积为:
V=50908mm3:
5.1cm3
件重量Wg=V-=5.1cm31.13g/cm3=5.763g
注:
取LDPE密度为1.13g/cm3。
1.2塑件材料的分析
丙烯腈-丁二烯-苯乙烯共聚物LDPE树脂微黄色或白色不透明,是丙烯腈-丁二烯-苯乙烯共聚物。
丙烯腈使聚合物耐油,耐热,耐化学腐蚀,丁二烯使聚合物具有优越的柔性,韧性;
苯乙烯赋予聚合物良好的刚性和加工流动性。
因此LDPE树脂具有突出的力学性能和良好的综合性能。
同时具有吸湿性强,但原料要干燥,它的塑件尺寸稳定性好,塑件尽可能偏大的脱模斜度。
1.LDPE塑料主要的性能指标
收缩率
%
0.3~0.8
熔点
C
130~160
热变形温度
45N/cm
65~98
弯曲强度
Mpa
80
拉伸强度
MPa
35~49
拉伸弹性模量
GPa
1.8
弯曲弹性模量
Gpa
1.4
压缩强度
18~39
缺口冲击强度
kJ/m2
11~20
硬度
HR
R62~86
体积电阻系数
Qcm
—13
10
击穿电压Kv.mm-1
15
、电常数
60Hz3.7
(Kg.dm-3)
2.LDPE的注射成型工艺参数:
注塑机类型:
螺杆式
喷嘴形式:
通用式
喷嘴温度180——190
模具温度5070
注塑压60——100
保压40——60
注塑时间2——5
保压时间5——10
冷却时间5——15
周期15——30
后处理红外线烘箱
温度(70)
时间(0.3——1)
由为重要的是因为目前原油价格的下降,导致LDPE的市场价格大幅度的下跌
1.3塑件的尺寸和精度分析
1.3.1塑件的尺寸
塑件的总体尺寸主要取决于塑料品种的流动性。
在一定的设备和工艺条件下,流动性较好的塑料可以成型较大尺寸的塑件;
反之,成型出的塑件较小。
本课题的塑件及所用材料为LDPE树脂具有突出的力学性能和良好的综合性能。
同时具有吸湿性强,但原料要干燥,它的塑件尺寸稳定性好,塑件尽可能偏大的脱模斜度。
在设计中我对塑件采取了拔模3度。
1.3.2塑件的尺寸精度
一般来讲,为了降低模具的加工难度和模具制造成本。
在满足塑件使用要求大前提下应尽量把塑件尺寸精度设计低一些。
另外,塑件尺寸精度还与塑料品种有关,根据各种塑料收缩率的不同,又将塑料的公差等级分为高精度、一般精度、低精度三种。
依据所选材料查《塑料成型加工与模具》表3—3取其一般精度为6级。
1.4塑料制品结构分析
由图1可知,塑件对称。
由于塑件的尺寸分布均匀,无过薄处,无需加强筋。
塑件的尺寸小,为了便于脱模,塑件表面沿脱模方向应具有合理的脱模斜度。
脱模斜度的大小,与塑件的性质、收缩率、摩擦因数、塑件壁厚和几何形状有关。
1.5LDPE塑料的成型工艺参数
如下:
通用式
料筒一区
150—
—170
料筒二区
180—
—190
料筒三区
200—
—210
喷嘴温度
模具温度
50—-
-70
注塑压
60—
—100
保压
40—
—60
注塑时间
2——
5
保压时间
5——
冷却时间
周期
15—
—30
后处理
红外线烘箱
2注射机的选择
根据以上数据分析计算,查表初选注射机型号为:
XS-Z-60
注射机XS-Z-60有关技术参数如下
额定注射量
60cm
注射压力
122MPa
锁模力
500KN
模板最大行程
180mm
模具最大厚度
200mm
模具最小厚度
70mm
喷嘴圆弧半径
12mm
喷嘴孔直径
4mm
动、定模固顶板尺寸
330mmx340mm
拉杆空间
290mm況368mm
2.1注射量的校核
注射机注射量应满足:
V机-V塑件/0.8
式中V机一注射机额定注射量cm3
V塑—塑件与浇注系统的凝料体积之和cm3
V塑20.143
计算
——25.19cm
0.80.8
M塑件=25.191.39g/cm=35.088g
所以
满足条件
2.2注射压力的校核
所选注塑机的最大注射压力为119MPa,大于塑件的成型注射压力。
2.3锁模力的校核
锁模力-PF
式中P—塑料成型时的型腔压力MPa
F—浇注系统和塑件在分型面上的投影面积之和mm2由于流道凝料(包括浇口)在分型面上的的投影面积A2,在此时还是个未知数,根据经验公式:
A2二°
.2-0.5Al(A1为每个塑件在分型面上的投影面积),在此用°
35叭进行估算:
2
F=nA「A2=nA,0.4nA]=21962.50.421962.5=5495mm
=空502=1965m2m
4
所以锁模力满足要求
2.4安装部分的尺寸校核
模具厚度:
280mm,而注射机规定的最大和最小厚度分别是300mm、200mm。
所以注射机合格。
模具的长度和宽度:
与注射机拉杆间距相适应,模具安装时能够穿过拉杆空间,在动、定模固定板上固定。
定位环尺寸:
100mm。
主流道入口尺寸:
模具主流道始端球面半径是15mm与注射机喷嘴球面半径是12mm。
符合要求。
3型腔位置及型芯型腔尺寸的确定
根据塑件的生产批量及尺寸大小和精度要求,本模具采用一模两腔。
塑件体积V=5.1cm3,单件塑件的重量为Wg=5.763g。
3.1型腔压力的估算
取压力损耗系数k=0.4,设注射机使用的注射压力是119MPa,则型腔压力p=0.4*119=46.8MPa:
3.2型腔型芯尺寸的计算
型腔
Lm=[ls+ls•Scp-3/4△广z0
Hm=[Hs+Hs・Scp-2/3△]+sz。
型芯
Lm=[ls+Is•Scp+3/4△]0-Sz
Hm=[Hs+Hs•Sp-2/3△]0-sz
中心距
Cm=[Cs+CsScp]±
S72
查表得:
收缩率:
&
=1.030%,取3.0%,同时公差按IT9级计
算,△=0.26mm、中小型塑件的Sz=△/3=0.0867mm
所以:
型腔尺寸
Lm1=26.585+00.0867mm
Hm1=18.367=0867mm
型芯尺寸
Im1=14.615-0.0867mm
Im2=18.735-0.0867mm
Im3=22.855-0.0867mm
hm仁59.567-0.0867°
mm
hm2=3.947-0.0867°
hm3=12.187-0.08670mm
hm4=3.988-0.0867°
4分型面的确定
选择平面分型面,便于简化模具结构和塑件脱模,保证塑件质量,便于模具加工。
1
5浇注系统的确定
主浇道设计:
为了让住流道浇口凝料能从浇道顺利拔出,主流道设计为锥形,锥角为4度,便于脱模。
6排气槽的确定
模具中的排气系统通常有三类:
(1)利用配合间隙排气
(2)在分型面上开设排气槽
(3)利用排气塞排气
由于此此塑件为小型逆件,可利用推杆、活动型芯与模板之间的间隙排气,其间隙为0.03~0.05mm。
7冷却系统的确定
注射模具的温度对塑料熔体的充模流动、固化定型、生产效率、塑件的形状和尺寸精度都有重要的影响。
注射模具中设置温度调节系统的目的是通过控制模具温度,使注射成型具有良好的产品质量和较高的成产力。
由于制品平均壁厚为2mm,制品尺寸相对较大,确定水孔直径为8mm。
由于冷却水道的位置,结构形式、孔径、表面状态、水的流速、模具材料等很多因素都会影响模具的热量向冷却水传递,精确计算比较困难。
实际生产中,通常是根据模具的结构确定冷却水路,通过调节水温、水速来满足要求。
冷却回路所需总表面积可控下式计算
A二Mq.3600a九-九
式中A冷却回总表面积,mm2;
M单位时间内注入模具中树脂的质量,Kgh;
q——单位质量树脂在模具内释放的热量,J•Kg,ABS
的q值查表得:
q值为3—4;
a——冷却水的表面传热系数,Wm^K;
-M模具成形表面的温度,C;
0——冷却水的平均温度,C。
冷却水的表面传热系数a可用下式计算
a=◎(pv严/d°
式中a——冷却水的表面传热系数,Wm2*K;
p——冷却水在该温度下的密度,Kg.m3;
d冷却水孔直径,m;
门——与冷却水有关的物理温度,「值可查下表得
A二Mq3600ag
10464102
-■-W0.0087m
36006997.93230-40
去——冷却水入口处温度,c
冷却水流量的计算:
104.6x4x105
604.2101.0280-10
8脱模力的计算
由于塑件较小,材料工艺性能好,而且塑件较厚形状不易变形,所以采用推杆推动推板推出机构即可。
脱模力可用下式计算:
R=APfcos:
-co
式中F1——脱模力,单位N
:
型芯的脱模斜度,单位(0)
A塑件包容型芯的面积,单位为m该模具为
6.45x10m
f——塑件对钢的摩擦系数,通常取为0.1〜0.3
取0.2
P——塑件对型芯的单位面积上的包紧力,模
外冷却时P=(2.4-3.9)x10Pa
故Fj=6.4510’1.01070.2cos0.75-COS0.75
=1.21104N
顶出力为12KN即能满足注射机的要求
9推出方式确定
采用推板推出装置,由推杆顶出推板,从而使工件从型腔内脱出。
推出方式已经确定为推板推出根据塑件的总质量,我们可以确定推板的厚度:
对于筒形或圆形,推件板受力状况可以简化为“圆环形平板周界
到集中的载荷。
按强度计算可得厚度为:
?
h=(K2Q/[(T])(3.16)
=40
所以对推件板采用40mm其中h是推件板的厚度,K2是系数,Q是脱模阻力。
10合模导向机构的设计
导向机构是保证动模或上下模合模时,正确定位和导向的零件。
本副模具是采用导柱、导套导向。
导向机构它起到的作用有:
定位作用、导向作用、承载作
用、保持运动平稳的作用。
导柱导向通常是由导柱和导套的间隙配合而组成的。
导柱分带头导柱和有肩导柱。
因为该产品是成批量的生产,导柱经常运动,容易磨损,所以采用导套,这样导套坏了,可以随时更换。
小型模具采用带头导柱。
10.1导柱的设计
技术要求包括:
导柱的长度、形状、材料、数量及布置。
此副模具把导柱设在动模一侧,这样有利于推杆的运动。
导柱固定端与模板之间采用H7/m6,而导柱与导套采用H7/f7的间隙配合。
导套也分直导套和芾头导套。
其用法与导柱的用法一样。
导套的技术要求的技术要求包括:
导套的形状、导套的材料、及固定形式及配合精度。
导套采用H7/r6配合镶入模板。
导柱结构和尺寸如下图所
10.2导套的设计
其结构和形状
导套采用直导套,这样简单易制作,而且也适用
如下图所示:
导套的前端倒圆角,是为了让导柱顺利进入导套。
材料通常也采用20钢,热处理,使其硬度达到一定硬度,以利于耐磨。
粗糙度为Ra为0.8,固定采H7/r6配合镶入模板。
11推出机构的设计
使塑件从成型零件上脱出的机构称之为推出机构。
本副模具是通过注塑机的合模机构,把力传给推板,然后通过固定板,再通过推杆,最后传给推件板,把塑件推出的。
推出零件常分为推件板、推杆、推管、成型推杆等。
此副模具所设计的塑件是属于薄壁塑件,而且在推出时不允许有推出痕迹,所以该模具采用推件板推出,这样有利于保证塑件的精度。
此模具的设计也要满足一般推出机构的设计原则:
塑件滞于动模一侧,这样有利于设计推出机构,以致于使模具结构简单、防止塑件变形、力求良好的塑个外观、结构可靠、脱模时工作可靠,运动平稳,制造方便,更换容易。
12绘制装配图
图2模具装配图
13模具的安装试模
1.试模前的准备
试模前要对模具及试模用的设进行检验。
模具的闭合高度,安装
与注射机的各个配合尺寸、推出形式、开模距、模具工作要求等符合所选设备的技术条件。
检查模具各个滑动零件配合间隙适当,无卡住及紧涩现象。
活动要灵活、可靠,起止位置的定位要准确。
各镶嵌件、紧固件要牢固,无松动现象。
各种水管接头、阀门、附件、备件要齐全。
对于试模设备也要进行全面检查,即对设备的油路、水路、电路、机械运动部位、各操纵件和显示信号要检查、调整,使之处于正常运转状态。
2.模具的安装及调试
模具的安装是指将模具从制造地点运至注塑机所在地,并安装在指定注射机的全过程。
模具安装到注射机上要注意以下几个问题:
1)模具的安装方位要满足设计图样的要求。
2)模具中有侧向滑动机构时,尽量使其运动方向为水平方向。
3)当模具长度与宽度尺寸相差较大时,应尽可能使较长的边与水平方向平行。
4)模具带有液压油路接头、气路接头、热流道元件接线板时,尽可能放置在非操作一侧,以免操作不方便。
模具在注射机上的固定多采用螺钉、压板的形式,一般每侧采用
4―8块压板,对称布置。
模具安装于注射机上之后,要进行空循环调整。
其目的在于检验模具上各运动机构是否可靠、灵活、定位装置是否有效作用。
要注意以下几个方面:
1)合模后分型面不得有间隙,要有足够的合模力。
2)活动型芯、推出及导向部位运动及滑动要平稳、无干涉现象,定位要正确、可靠。
3)开模时,推出要平稳,保证将塑件及浇注系统凝料推出模具。
4)冷却水要畅通,不漏水,阀门控制正常。
3.试模
将模具安装在注射机上,选用合格的原料,根据推荐的工艺参数调整好注射机,采用手动操作。
开始注射时,首先采用低压,低温和较长的时间条件下成形。
如果型腔未充满,则增加注射时的压力。
在提高压力无效的时,可以适当提高温度条件。
试模注射出样件。
试模过程中,应进行详细记录,将结果填入试模记录卡,并保留试模的样件。
4.检验
通过试模可以检验出模具结构是否合理;
所提供的样件是否符合用户的要求;
模具能否完成批量生产。
针对试模中发现的问题,针对试模中发现的问题,对模具进行修改、调整、再试模,使模具和生产的样件满足客户的要求,试模合格的模具,应清理干净,涂防锈油入库保存。
结论
模具课程设计结束了,在这次的课程设计中不仅检验了我所学习的知识,也教会了我如何更好地把握一件事情、完成一件事情。
设计过程中,和同学们相互探讨,相互学习,相互监督。
学会了合作,学会了运筹帷幄,学会了宽容,学会了理解,也学会了做人与处世。
课程设计是我们专业课程知识综合应用的实践训练,是我们迈向社会,从事职业工作前一个必不少的过程。
“千里之行始于足下”通过这次课程设计,我深深体会到这句千古名言的真正含义。
我今天认真的进行课程设计,学会脚踏实地迈开这一步,就是为明天能稳健地在社会大潮中奔跑打下坚实的基础。
通过这次模具设计,本人在多方面都有所提高。
通过这次模具设计,综合运用本专业所学课程的理论和生产实际知识进行一次密封圈模具设计工作的实际训练从而培养和提高学生独立工作能力,巩固与扩充了模具设计等课程所学的内容,掌握密封圈模具设计的方法和步骤,掌握模具设计的基本的模具技能懂得了怎样分析零件的工艺性,怎样确定工艺方案,了解了模具的基本结构,提高了计算能力,绘图能力,熟悉了规范和标准,同时各科相关的课程都有了全面的复习,独立思考的能力也有了提高。
在这次设计过程中,体现出自己单独设计模具的能力以及综合运用知识的能力,体会了学以致用、突出自己劳动成果的喜悦心情,从中发现自己平时学习的不足和薄弱环节,从而加以弥补。
在此感谢老师以及帮助过我的同学们。
由于本人的设计能力有限,在设计过程中难免出现错误,恳请老师多多指教。