挤压铸造原理及缺陷分析正式版Word格式.docx
《挤压铸造原理及缺陷分析正式版Word格式.docx》由会员分享,可在线阅读,更多相关《挤压铸造原理及缺陷分析正式版Word格式.docx(3页珍藏版)》请在冰豆网上搜索。
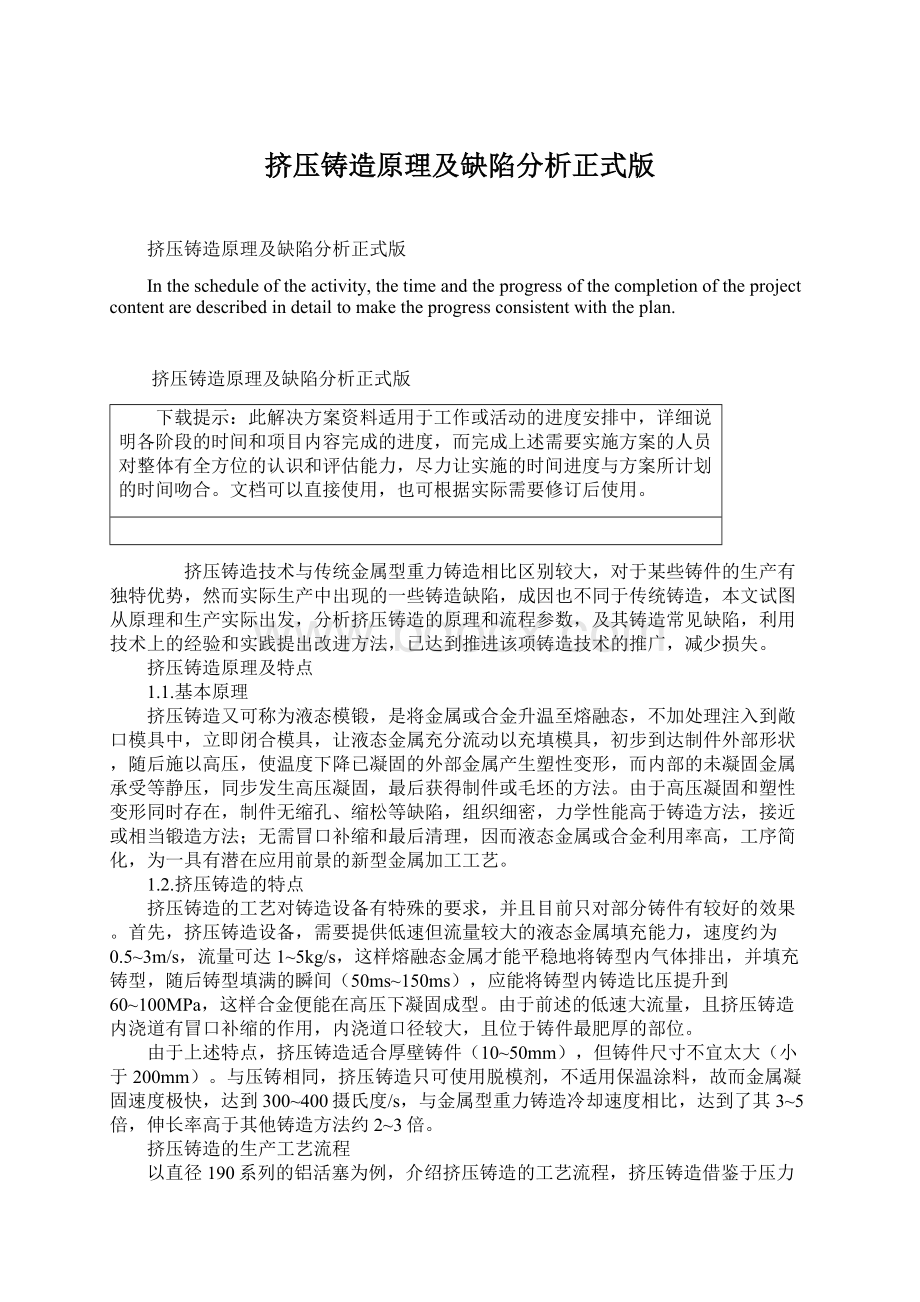
下载提示:
此解决方案资料适用于工作或活动的进度安排中,详细说明各阶段的时间和项目内容完成的进度,而完成上述需要实施方案的人员对整体有全方位的认识和评估能力,尽力让实施的时间进度与方案所计划的时间吻合。
文档可以直接使用,也可根据实际需要修订后使用。
挤压铸造技术与传统金属型重力铸造相比区别较大,对于某些铸件的生产有独特优势,然而实际生产中出现的一些铸造缺陷,成因也不同于传统铸造,本文试图从原理和生产实际出发,分析挤压铸造的原理和流程参数,及其铸造常见缺陷,利用技术上的经验和实践提出改进方法,已达到推进该项铸造技术的推广,减少损失。
挤压铸造原理及特点
1.1.基本原理
挤压铸造又可称为液态模锻,是将金属或合金升温至熔融态,不加处理注入到敞口模具中,立即闭合模具,让液态金属充分流动以充填模具,初步到达制件外部形状,随后施以高压,使温度下降已凝固的外部金属产生塑性变形,而内部的未凝固金属承受等静压,同步发生高压凝固,最后获得制件或毛坯的方法。
由于高压凝固和塑性变形同时存在,制件无缩孔、缩松等缺陷,组织细密,力学性能高于铸造方法,接近或相当锻造方法;
无需冒口补缩和最后清理,因而液态金属或合金利用率高,工序简化,为一具有潜在应用前景的新型金属加工工艺。
1.2.挤压铸造的特点
挤压铸造的工艺对铸造设备有特殊的要求,并且目前只对部分铸件有较好的效果。
首先,挤压铸造设备,需要提供低速但流量较大的液态金属填充能力,速度约为0.5~3m/s,流量可达1~5kg/s,这样熔融态金属才能平稳地将铸型内气体排出,并填充铸型,随后铸型填满的瞬间(50ms~150ms),应能将铸型内铸造比压提升到60~100MPa,这样合金便能在高压下凝固成型。
由于前述的低速大流量,且挤压铸造内浇道有冒口补缩的作用,内浇道口径较大,且位于铸件最肥厚的部位。
由于上述特点,挤压铸造适合厚壁铸件(10~50mm),但铸件尺寸不宜太大(小于200mm)。
与压铸相同,挤压铸造只可使用脱模剂,不适用保温涂料,故而金属凝固速度极快,达到300~400摄氏度/s,与金属型重力铸造冷却速度相比,达到了其3~5倍,伸长率高于其他铸造方法约2~3倍。
挤压铸造的生产工艺流程
以直径190系列的铝活塞为例,介绍挤压铸造的工艺流程,挤压铸造借鉴于压力铸造和模锻工艺,其大体工艺流程为把液态金属直接浇入金属模内。
然后在一定时间内以一定的压力作用于熔融的金属液体使之成形。
并在此压力下结晶和塑性流动。
从而获得铸件。
在315t的液压机上生产铝活塞的具体流程是:
首先将铝加热到700~720摄氏度,形成铝液,倒入凹模中,进行扒渣得到相对纯净的铝液,液压机上缸下行,上压头对铝液加压,主缸的峰值加压压力达到280t,上压力加压至最大表压力22MPa起,到上压头起模止,维持保压时间在350秒,保压结束后开模,用底缸将铸件顶出即可。
整体上可分为四个步骤,模具准备,浇注,合模加压,开模出件。
具体的铸造过程,注意的参数如下:
顶缸上升速度和金属流速;
对铸造机而言,顶缸上升速度应该是丰富可调的,而金属流速须由铸件壁厚和尺寸决定,以不产生湍流,平稳填充铸型为原则,铸件的壁厚越大,尺寸越小,则流速较小,壁厚越小,尺寸越大,则流速较大。
挤压机顶缸上升顶力和瞬间及时增压速度;
当前我国普遍装备的油顶机顶缸顶力足够满足挤压铸造的需求。
瞬间及时增压速度是较为重要的参数,在合金液刚刚充满铸型之初,铸造比压极小,在50ms~150ms内,下顶缸顶力上升到额定顶力,以保证高比压下合金液凝固成型。
挤压铸造缺陷分析
以铝活塞为例,介绍常见的挤压铸造的缺陷分析和解决措施。
3.1.气孔
气孔的出现一般是由于最初的铝液中气体含量较高,或者浇注过程中侵入了气体,因此气孔可分为析出性气孔和侵入性气孔。
具体的应对措施由其形成原因入手。
析出性气孔的减少,主要需要对铝液的精炼处理进行强化,得到含气量低的铝液。
侵入性气孔则涉及更多的流程,首先熔融态合金注入模具的速度要平稳,不超过0.08m/s,避免产生涡流卷入气体,并且充分排出铸模中的气体,速度太低也可能造成金属凝固而没有充满铸模,这需要由上压头加压速度来控制,一般厚壁铸件需控制住0.03~0.06m/s,而壁薄的铸件则速度稍高,控制在0.05~0.08m/s。
3.2.缩松和缩孔
缩松和缩孔会伴随着气孔产生,通常会出现在活塞最后凝固的区域,上压头下行至型腔封闭时,铝液存在向上的反向流动,而挤压铸造不能设置冒口补缩,故只能将未凝固的铝液挤入活塞销座和头部热节处,实现补缩,这有赖于上压头的压力对铸件进行压缩,而压力不足会导致补缩效果不明显,活塞稍座和头部可能出现缩孔和缩松。
对于该问题,首先是对上压头的压力进行合理选取,依据合金类型和铸件外形因素设置压力。
上压头的最低压力值需在80MPa以上,而最高不宜超过120MPa,在该范围内逐步提高压力值以减少缩松和缩孔,其次,一定的保压时间也是消除缩松和缩孔所需条件,持续的保压中,确保金属能够全部冷却凝固,不发生卸压后仍有液态金属继续凝固产生缩孔缩松,同时,过长的保压时间会导致模具温度升高,且脱模困难,不利于模具的寿命,经过验证,保压时间在150s~350s内,铸件质量较好,该时间由铸件最大壁厚来大致估计。
3.3.氧化夹杂
挤压铸造中,不设置浇冒口,也很少设置集渣包,排渣系统不足,但铝液在熔炼和浇注中,不断产生氧化夹杂,在形成铸件后,氧化夹杂融入其中,导致外圆氧化夹杂的缺陷。
对于氧化夹杂问题,首先铝合金的融化过程,温度精确控制在700~720摄氏度,使渣浮起,除尽铝液内氧化渣,并且坩埚和浇勺也清理干净,浇注之时,避免直接通过漏斗直浇道,可使用孔眼直径在1mm左右的过滤网以便滤去氧化渣和溶剂渣。
加压之前,进行一个快速的扒渣,由模壁向中心,从中心剔除残渣,而在压制之前,不得有冷隔金属参与挤压铸造过程。
挤压铸造是一项优质高效的生产工艺,如果各工艺环节控制得当,可以产生质量较好的铸件,然而在实际生产中,却因为种种原因产生缺陷,给厂家和使用者带来损失,本文对缺陷原因从技术上进行了分析,从生产流程上提出了应对措施,结合实际情况,使挤压铸造技术更好地用于生产。
——此位置可填写公司或团队名字——