板坯连铸机结晶器流场数值模拟及结果分析文档格式.docx
《板坯连铸机结晶器流场数值模拟及结果分析文档格式.docx》由会员分享,可在线阅读,更多相关《板坯连铸机结晶器流场数值模拟及结果分析文档格式.docx(15页珍藏版)》请在冰豆网上搜索。
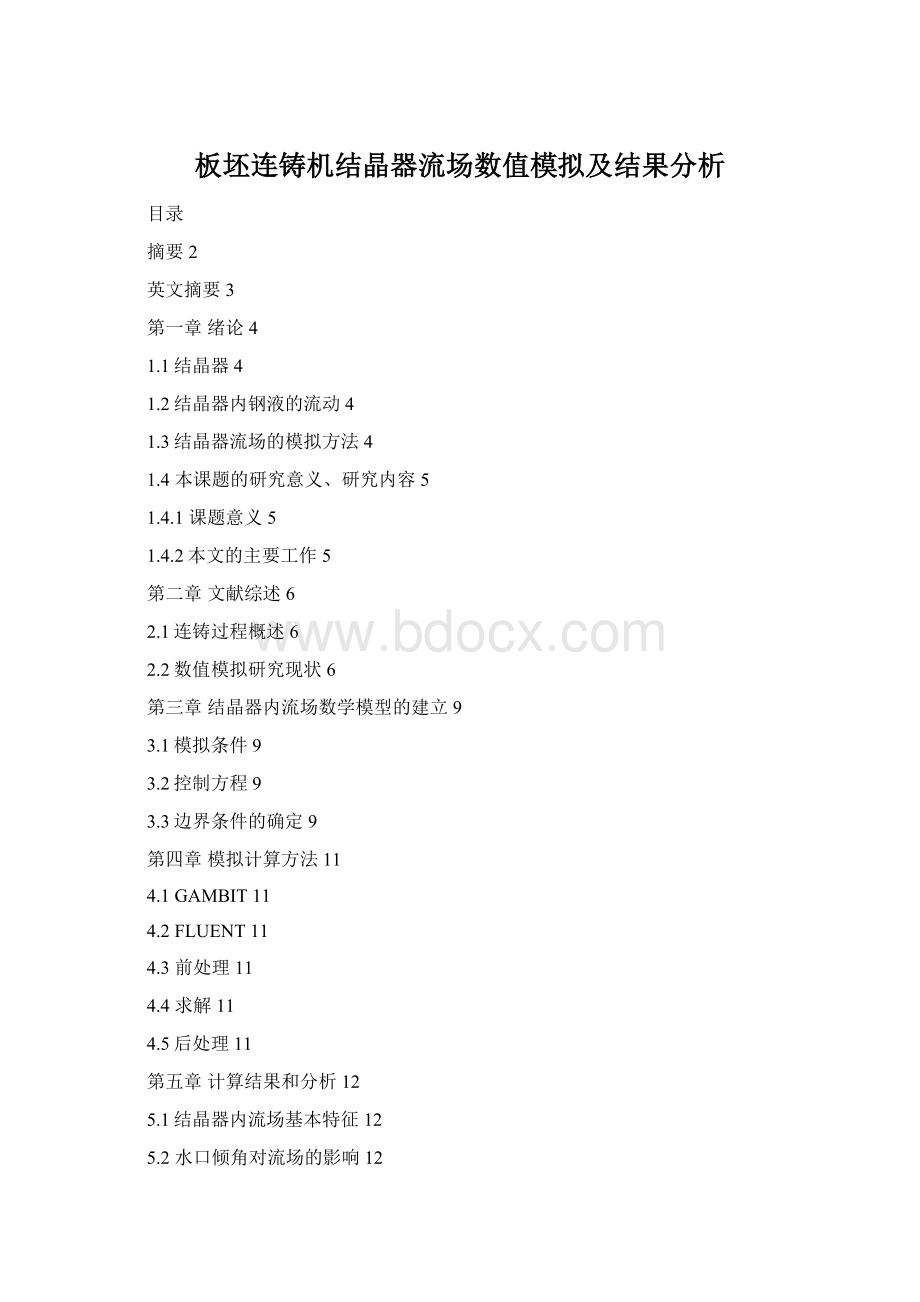
第六章结论15
参考文献16
致谢17
摘要
连铸结晶器过程钢水流动与生产工艺顺序和铸坯质量有密切关系,它不仅涉及到夹杂物分离去除效果和防止保护渣卷入,而且对初生凝固坯壳发育和避免漏钢事故发生具有显著影响。
研究结晶器内钢水流动状态对指导连铸生产具有重要意义。
对结晶器及浸入式水口的一些结构参数对结晶器内流场的影响规律进行了分析。
为避免钢液卷渣现象的发生,同时又有利于夹杂物的上浮,对工艺参数在合理的参数范围内进行优化,得到了较好的结晶器流场,从而达到提高铸坯质量的目的。
本论文以薄板坯连铸机为对象,建立了描述结晶器内钢液流动的二维数学模型,在商业软件FLUENT的平台上对板坯连铸结晶器内钢液的流场进行了数值模拟。
通过模拟浇铸初期钢液的流动状态,分析了结晶器内流场的基本特征。
同时模拟计算了浸入式水口的出口倾角、插入深度以及拉坯速度对钢液流动的影响。
关键词:
板坯;
连铸;
结晶器;
流场;
数值模拟
Abstract
Theprocessesofcontinuouscastingproductionandthequalitiesofslabaregreatlyrelativetothefluidflowinthemoldofcontinuouscaster,bywhichnotonlytheremovalofinclusionsfrommoltensteelandtheprotectionofengulfmentofcastingpowderbutalsothegrowthofsolidifyingshellandtheavoidanceofbreakoutareinfluencedevidently.Togivesomeguidancetothecontinuouscastingproduction,itisverysignificanttohaveaclearunderstandingonthefluidflow.
TheeffectsofsomestructureparameterofmoldandSENontheflowinmoldareanalyzedinthispaper.Inordertoavoidtheslagengulfingandpromotetheinclusionsfloatingtothesurface,theprocessingparametersareoptimizedinareasonablerange,andthereforeanoptimizedflowfieldcanbeobtainedtoimprovethequalityofslabs.
Aimingatthemediumthicknessslabcaster,2Dnumericalmodeldescribingtheflowofliquidsteelinmoldwascarriedout.CommercialsoftwareFLUENTwasusedtosolvethecombinedequationsofturbulentflow.Bysimulatingthepouringinitialstageliquidsteelflowstate,thefluidflowinthemoldwasanalyzed.Simulationresultsshowedtheinfluencesofdifferentportobliquity,deepnessandcastingvelocityetc,ontheflowofslabmold.
Keywords:
slab;
continuouscasting;
mold;
flow;
numericalsimulation
第一章绪论
1.1结晶器
结晶器是连铸机设备中最关键的部件,可以称为连铸机的心脏。
钢液在结晶器内凝固成所需的断面形状和一定厚度的坯壳。
当铸坯拉出结晶器时,结晶器要保证在机械应力和热应力的综合作用下,坯壳不拉漏以及不产生变形和裂纹等缺陷。
因此,结晶器的性能对连铸机的生产能力和铸坯质量起着十分重要的作用。
结晶器内钢液的凝固伴随着传热、传质过程,结晶器在材质、结构等方面要满足连铸工艺及其使用性能方面的要求。
因此结晶器应具有下列性能:
有较好的导热性;
有较好的结构刚性,且便与拆装和调整,易于加工制造;
有较好的耐磨性及抵抗热应力的性能;
质量要轻,以便在振动时具有较小的惯性力。
随着对连铸坯质量要求的日益严格,提高钢液的清洁度、严格控制成分已经成为连铸生产中最为关心的问题之一,结晶器是控制钢液清洁度的最后环节,结晶器内的流动方式不仅对夹杂物的行为影响很大,而且对凝固初期坯壳的传热产生很大的影响。
因此,研究结晶器内钢液的流场特征已经引起高度重视。
本文建立了结晶器内二维流动的数学模型,利用FLUENT软件模拟结晶器内钢液的流动。
1.2结晶器内钢液的流动
结晶器内钢液流动的源动力主要来自浸入式水口的钢液的惯性流。
流动对凝固过程的影响主要体现在以下几个方面:
1)结晶器内钢液的流动对钢液中夹杂物的上浮和钢液面保护渣的卷入存在着较大的影响。
合理的流场分布将有助于钢中夹杂物的上浮,防止卷渣现象的发生。
2)结晶器内钢液的流动对初生坯壳的形成及坯壳内钢液的温度分布存在较大的影响。
合理的流场分布将促进初生坯壳的生长,减少钢液对坯壳的冲刷。
避免凝固坯壳内钢液高温区温度过高现象的发生。
3)两相区内钢液的流动对凝固过程的溶质再分配存在较大的影响。
两相区是一个固液共存区,溶质浓度在随着固相分率的变化而变化的同时,液随着流动速度的变化而变化。
结晶器内钢液的流动,主要决定于浸入式水口形状、结晶器断面形状及连铸工艺。
结晶器内钢液的流场可以分为三个区域:
上回流区、水口射流区和下回流去。
拉速、结晶器的形状及尺寸、浸入式水口的设计和工艺参数对结晶器内流场有重要影响。
1.3结晶器流场的模拟方法
流动现象广泛地存在于钢的冶炼过程中。
随着计算机的发展和数值计算技术的不断成熟,利用计算机对实际过程进行数值模拟的计算流体力学方法迅速发展起来。
计算流体力学是近代流体力学、数值数学和计算机科学相结合的产物,其基本特征是数值模拟和计算机实验。
它与物理模型之间的关系式互相依存、互为补充和互相促进的。
数值模拟是基于计算流体力学、计算传热学、计算燃烧学和冶金反应工程学的原理,应用数值计算方法,在计算机上求解联立的非线性质量、动量、能量及组分偏微分方程组,预报出流动、传热及及杂物传递过程的细节,即给出整个研究区域中各变量的时空分布,进而分析冶金过程的速率和效果。
因此,这样的数学模拟以开始成为工程装置优化、仿真设计和实现过程最佳控制的有力工具。
数值模拟技术已日趋成熟,其过程大致可分成:
1)建立基本守恒方程组;
2)确定边界条件;
3)建立模型封闭方法;
4)制定求解方法。
1.4本课题的研究意义、研究内容
1.4.1课题意义
实现薄板坯连铸连轧工艺的技术关键是薄板坯连铸,其中连铸机的结晶器是关键。
结晶器技术是各类连铸连轧技术的分类依据,也是决定产量和质量的主要设备。
板坯连铸机结晶器的连铸效果好坏直接影响铸坯质量。
上回流区、下回流区、水口射流区。
因此,结晶器内钢液流场的研究可以为结晶器及浸入式水口的尺寸、工艺参数的设计提供依据。
1.4.2本文的主要工作
第二章:
文献综述
第三章:
建立数学模型
第四章:
Fluent软件的运用
第五章:
数值模拟结果分析
第六章:
总结全文
第二章文献综述
2.1连铸过程概述
薄板坯连铸连轧和棒线材连铸连轧生产线的突出,打破了传统的生产模式。
“连铸连轧”这个词包括如下概念:
由连铸机生产出来的高温无缺陷坯,无需清理和再加热而直接轧制成材,这样吧“铸”和“轧”直接连成一条生产线的工艺流程就称为连铸连轧。
连铸连轧生产工艺与传统的生产工艺相比较,直接将连铸和连轧工艺相连接形成连铸连轧生产方式,在经济上收效显著。
连铸连轧的生产特点有:
生产周期短,从钢水到产品的生产流程从数天缩短到不足0.5小时;
占地面积少,对于薄板坯连铸连轧厂占地面积大约为常规流程的四分之一;
固定资产投资少,约为常规流程的五分之一;
金属的收得率高;
钢材性能好;
能耗少;
工厂定员大幅降低;
连铸连轧生产技术的发展趋势具有以下特点:
高速化、大型化;
新技术相互渗透;
高度连续化;
高精度轧制;
开发新钢种;
高度自动化;
高性能辅助设备。
采用控轧控冷技术;
生产计划调度系统。
连铸是用连铸机把钢水浇注、冷凝、切割而直接得到铸坯的工艺。
作为炼钢生产厂的重要组成部分和连接炼钢和轧钢的重要环节,连铸生产的正常与否不但关系到炼钢和轧钢工序的顺行,而且也将影响到轧材质量和成材率。
一台连铸机由钢包、中间包、中间包车、结晶器、结晶器振动装置、二次冷却装置、矫直装置、切割装置和铸坯运出装置等部分组成。
连铸过程从本质上讲是一个传热和凝固相变的过程,钢水的传热和凝固决定了坯壳生长、内部缺陷和热应力应变等,它在很大程度上影响着铸机的生产效率和铸坯质量。
钢水的流动控制着钢水温度分布和过热消除,影响着钢水与坯壳间传热、初生坯壳形成以及溶质分配等,进而对坯壳生长发育和内部微观组织结构产生影响。
连铸是连接炼钢和轧钢的中间环节,是炼钢生产的重要组成部分。
连铸技术的出现从根本上改变了一个世纪以来占统治地位的钢锭粗轧等一系列复杂的钢铁生产工艺流程,简化了钢水到钢坯的生产工艺。
这项技术的应用,为炼钢生产向连续化、自动化的方向的发展开辟了新的途径。
连铸是一门将冶金与机械及控制相结合的综合生产技术。
连铸生产的技术和管理水平不仅影响到炼钢生产任务的完成,而且也影响到轧材的质量和成材率。
此外,连铸技术自身的发展,还会带动冶金系统其它行业的发展,对企业结构和产品结构的简化和优化,有着重要的促进作用。
上世纪后期,连铸技术发展迅速,新型连铸技术不断涌现,连铸技术应用的钢种不断拓宽,不论连铸坯质量,还是连铸生产的技术经济指标均大幅提高。
2.2数值模拟研究现状
冶金过程中存在流体流动现象,然而研究冶金过程中流体流动现象并不是一件容易的工作。
冶金过程的高温使传统的室温下的物理模拟和直接测量遇到很多困难,难以获得足够可靠的信息和数据。
计算机技术和相关软件的发展,为深入研究冶金过程中流体流动现象提供了一种新的方法和可能。
计算流体力学(ComputationalFluidDynamics,CFD)是近代流体力学、数值计算和计算机科学等学科综合发展后,出现的一门新的学科,也是一种研究传输过程为基础各种自然和工程现象的手段。
1965年,Harlow和Fromn提出“流体动力学的计算机实验”,是计算流体力学成为一种实验研究方法的开始。
随着高速度、大容量、多功能计算机的出现和不断更新,特别是计算机软件的发展,计算流体力学的内容、方法和相关软件也有了飞速发展,仅仅几十年即形成为一门独立的学科。
计算流体力学研究方法的基本特征是数值模拟和计算机实验,它遵从传统的物理定理,可以考虑各种反应那个过程和多为多相体系的存在。
应用计算流体力学的方法可以代替许多实验室研究和实物内研究,而且可以完成实验室和实验研究中无法观测到的现象、机理和时空过程。
冶金领域是近几十年来应用计算流体力学进行科学研究和工程开发的主要行业之一。
早在20世际70年代,国际主要冶金学刊物就开辟专栏或经常刊登冶金过程CFD数值模拟的研究论文。
在连续铸钢的生产过程中,钢液在结晶器内的流动直接影响铸坯质量,结晶器内的合理流场有助于钢液在温度、成分方面的均匀性,避免在液面结冷钢,减少铸坯在宏观上的偏析现象,同时有助于夹杂的上浮,减轻钢流对坯壳的冲击,同时抑制柱状晶的生长趋势,减少表面裂纹和内部裂纹的产生,提高铸坯质量。
而结晶器内的流动状况与结晶器的尺寸、浸入式水口参数、;
拉速等直接有关。
针对结晶器内流体流动的研究已有许多报道,从大的方面可归结为两类,其一是物理模拟,其二是数值模拟。
1973年,Szekely和Asia将单方程紊流模型和Spalding的离散化方法第一次应用到结晶器内钢液的流动,编制程序模拟方坯结晶器中的二维情况下的流动现象。
1974年Launder和Spalding使用k-
双方程模型较合理地解决了流场的数值计算。
在他们所建立的数学模型中所采用的经验常数取值一直为后人所用【1】。
1975年,Asia和Szekely就采用涡量—流函数法模拟了圆坯结晶器内的流动与凝固过程,他们使用Navier-Stokes方程湍流模型分析湍流特性对流场合传热过程的影响。
尽管当时所建立的模型不十分完善,但是对后来数学模型的建立起到了不可忽视的影响。
1990年ThomasB.G等人采用Re高数的k-
双方程模型研究板坯中二维紊流流动,使用商业软件FIDAP求解了二维流场并使用水模型来验证。
Thomas还专门建立了水库出口模型,研究证实了出口湍动能和湍动能耗散率主要与出口速度有关,与出口角度关系不大。
流场的技术结果反映特定的水模拟结晶器情况。
1990年,Flint使用商业软件PHOENICS模拟板坯三维湍流流动和传热,Flint选取宽面沿水口对称的1/2结晶器为计算区域,在水口出口处,宽面和窄面靠近壁面的地方网格划分比较细,从而可以更好地分析流场在这些关键部位的分布情况。
由于PHOENICS并不能很好地处理有相变过程的流动和传热的耦合模型计算,其结果未经过实验的定量验证。
1992年,利用商业软件FIDAP,HuangX和ThomasB.G研究热量传输方程的时候,应用双方程模型研究板坯中三维紊流流动,在动量方程的右边重力项中考虑了热浮力的作用,得到了比较符合实验数据的结果并把结果应用于温度场的求解。
1995年,M.R.Aboutalebi、M.Hasan、R.LL.Gurhrie等人开发了一个同时耦合方坯连铸过程中流动、传热、凝固和溶质分布的二维数学模型,并通过该模型研究了不同工艺参数对钢液流动、凝固和碳的分布的影响。
根据计算结果预测了夹杂物的轨迹和不同夹杂物尺寸的密度分布。
在模型中整个结晶器内的钢液看作两相运动,即固相和液相。
为较好的模拟固液两相区,模拟中采用修正的k-
双方程紊流模型,在k、
方程的右端增加一个源项。
1991年,陈克、徐宝升开发了一个轮式连铸的钢液湍流的凝固的三维耦合模型。
此模型将固体视为粘性无穷大的流体,采用k-
双方程模型处理湍流流动,将两相区视为参透流,用提高分子粘性系数的办法计入枝晶网状组织对钢液流动的阻力。
1998年,杨宏亮、邓开文等开发了连铸过程的三维耦合模型,次模型主要耦合流体流动、传热凝固等单元过程,研究了传输过程与宏观偏析的关系,是在一个直角坐标系中利用有限差分方法和SIMPLE算法的三维耦合模型。
2000年,西安交通大学的杨乘俭、苏俊义等对薄板坯连铸结晶器中钢液的紊流流动进行了有限元数值模拟。
在数值模拟中,考虑了凝固壳厚分布对流程的影响。
在掌握了结晶器内紊流粘性系数分布规律的基础上,将流动域在空间进行了分区,采用分区选定有效粘性系数的当量层流模型数值模拟了三维紊流流动。
在这次计算过程中,虽然考虑了凝固坯壳对流场的影响,但是没有考虑温度的因素,俨然凝固皮哦可的得来时假设得来的。
2001年,包头钢铁学院的张凰、贺友多等人建立了板坯连铸机结晶器内流动及传热过程的数学模型。
应用三维流场合温度场计算软件,对首钢第二炼钢厂的板坯连铸机结晶器内钢液的流场合温度场进行了研究,通过研究得到了现有操作条件下结晶器内钢液的流动特征及温度分布情况,同时确定出他们对铸坯的影响。
但是在他们建立的数学模型中源项的处理不够完善,动量方程没有源项,即没有考虑热浮力及重力对流场的影响,在湍动能和耗散率方程中温度的影响也没有体现出来,子啊温度场的能量方程中包含了凝固潜热源项,这种处理方法克服了传统等价比热在一些情况下失效的缺陷,但是这种方法给计算过程中源项的线性化带来了不便。
2000年东北大学的赫翼成等人在描述三维流体流动数学模型——N-S方程结合湍流低Re数k-
双方程模型的基础上,耦合能量守恒方程对结晶器内温度分布和钢液凝固过程进行计算,同时考虑凝固壳及糊状区队流动过程的影响,对流动控制方程进行修正,从而开发出描述结晶器内钢液流动与传热、凝固过程耦合的数学模型。
在其计算过程中采用了多孔介质理论运用达西定律对糊状区进行处理。
用自己编制的软件来讨论了不同的浇注温度、拉坯速度对结晶器内流场的影响。
2001年,KoujiTSKSTSNI等人采用大涡模拟法,建立了结晶器内瞬变流场的数学模型。
分析了浸入式水口中吹入氧气对钢液和凝固坯壳的影响。
他们通过把计算区域分为刚体区域和可移动区域两部分,根据计算得出的压力初步推测出了弯月面的形状。
近年来,电磁场已逐渐应用于连铸过程,包括结晶器内金属液流场的控制、二冷区的电磁搅拌、交变磁场控制凝固过程和利用静磁场生产复合连铸坯等,因而,结合Maxwell方程的电磁流体力学的计算研究发展迅速。
瑞典的Lehman等人、日本Idogawa等人及法国Gardio等人分别计算了静磁场和低频交变磁场作用下结晶器内钢液流场。
日本的Tanaka等人还对高频磁场作用下结晶器内流场和坯壳边缘温度分布进行模拟研究。
第三章结晶器内流场数学模型的建立
3.1模拟条件
某钢厂连铸机结晶器部分主要参数如下:
结晶器断面尺寸为1270mm×
207mm,水口倾角向下18°
,水口插入深度为180mm,拉坯速度为1.0m/min,水口出口尺寸为60mm,连铸坯断面尺寸为1250mm×
200mm。
本工作仅对流场进行分析,不考虑温度的影响,需要的材料参数中钢水的密度为7000kg/
,动力粘度为0.055kg/(
)。
并作如下假设:
1)将含自由面(结晶器液面)的的开口系统,作为封闭系统来模拟,且自由面看作光滑的壁面;
2)将钢液流动视为不可压缩牛顿流体流动,湍流效应采用高雷诺数k-
方程模型模拟;
3)不考虑结晶器内化学变化;
4)结晶器为矩形;
5)将连铸过程视为稳态过程,采用固定直角坐标系;
6)不考虑结晶器表面渣对流动的影响;
7)忽略传热及结晶器振动对流场的影响;
8)不靠率结晶器内凝固壳对流动的影响。
3.2控制方程
铸坯坯壳内的流动分为液相穴内的湍流流动和两相区内的枝晶间内流动。
液相穴内的湍流流动采用高雷诺数k-
方程模型模拟。
两相区的枝晶间流动被当作随充满液态网中流动。
从理论上讲,两相区内枝晶间流动可以通过求解非牛顿液体的控制方程来求解。
但由于很难确定液相内的牛顿流体于两相区内的非牛顿流体的界面值。
因此,我们采用牛顿流体的计算方法研究两相区的枝晶间流动。
1)
连续性方程:
2)
动量方程:
3.3边界条件的确定
(1)入口边界条件
入口定义在水口入口处,设为速度入口,速度由拉坯速度、结晶器断面和水口的直径共同确定,其公式为
同时假定入口截面上速度分布相同。
(2)出口边界条件
出口定义在结晶器计算区域底部,设为压力出口,出口边界的静压设为0.计算时适当延长模拟计算区域,结晶器高度取为2500mm。
(3)结晶器液面和对称面。
各物理量的对称面上的速度梯度都等与0,结晶器液面出设为自由面。
(4)结晶器壁面
假定在结晶器壁面包括浸入式水口壁面,垂直于壁面的速度分量设为0;
平行于壁面的速度、压力及k、
用无滑移边界;
与壁面相邻的节点上,平行于壁面的速度分量k,
由壁面函数确定。
第四章模拟计算方法
4.1GAMBIT
GAMBIT是专用前处理软件包,用来为CFD模拟生成网格模型。
由它所生成的网格可提供多种CFD程序或商用CFD软件所使用。
GAMBIT的主要功能包括3个方面:
构造几何模型、划分网格和指定边界。
其中,划分网格式其最主要的功能。
它最终生成包括含有边界信息的网格文件。
4.2FLUENT
FLUENT是用于计算流体流动和传热问题的程序。
它提供的非结构网格生成程序,对相对复杂的集合结构网格生成非常有效。
可以生成的网格包括二维的三角形和四边形网格;
三维的四面体、六面体及混合网格。
FLUENT还可根据计算结果调整网格,这种网格的自适应能力对于精确求解有较大梯度的流场有很实际的租用。
由于网格自适应和调整只是在需要加密的流动区域里实施,而非整个流场,因此可以节约计算时间。
从本质上讲,FLUENT只是一个求解器。
FLUENT本身提供的主要功能包括导入网格模型、提供计算的物理模型、施加边界条件和材料特性、求解和后处理。
4.3前处理
利用GAMBIT建立结晶器及水口计算区域的二维计算模型。
4.4求解
采用商用FLUENT软件求解流动方程组,通过控制求解精度及迭代步骤,最终达到收敛。
收敛的判断标准为各变量残差小于
,计算时间大约1小时。
4.5后处理
将计算结果进行可视化处理。
第五章计算结果和分析
5.1结晶器内流场基本特征
图1为模拟的工艺参数为水口倾角向下18°
,插入深度为180mm,拉速为1.0m/min时的结晶器内流场云图。
由图可以看出:
(1)出口射流区:
在水口出口射流方向上有一个冲击流区,这个冲击射流从水口一直延伸到结晶器窄面,把结晶器内的钢液流动分为上下两个区域。
(2)上回流区:
射流碰到结晶器窄面后改变方向,分成向上和向下两个流股,向上的流股在结晶器上部形成一个小的回流区,这个回流区对夹杂物的去除,自由液面的扰动产生直接的影响,对结晶器保护渣的熔化起决定性的作用。
(3)下回流区:
向下的流股沿结晶器窄面向下流动,达到一定深度后回流流向中心,其强度随着向下距离的延伸而减弱,其对夹杂物的上浮,初生凝固坯壳的均匀生长有着较大的影响。
图1结晶器内流场云图
5.2水口倾角对流场的影响
由图2可看出,水口倾角对结晶器内的流动影响很大。
改变水口出钢孔倾角后,上、下回流区的大小和相对应位置发生了明显变化。
当水口出口角度减小时,射流对板坯结晶器窄面的冲击位置向上移动,从水口流出的钢水首先占据结晶器的上部然后碰击结晶器的窄面而改变流动方向,使上回流区回流变强,湍流程度加大,会引起液面波动幅度增大,容易造成保护渣卷入。
保护渣覆盖不良容易导致钢液面裸露,造成钢液