供应品质管理计划 QMPWord文件下载.docx
《供应品质管理计划 QMPWord文件下载.docx》由会员分享,可在线阅读,更多相关《供应品质管理计划 QMPWord文件下载.docx(5页珍藏版)》请在冰豆网上搜索。
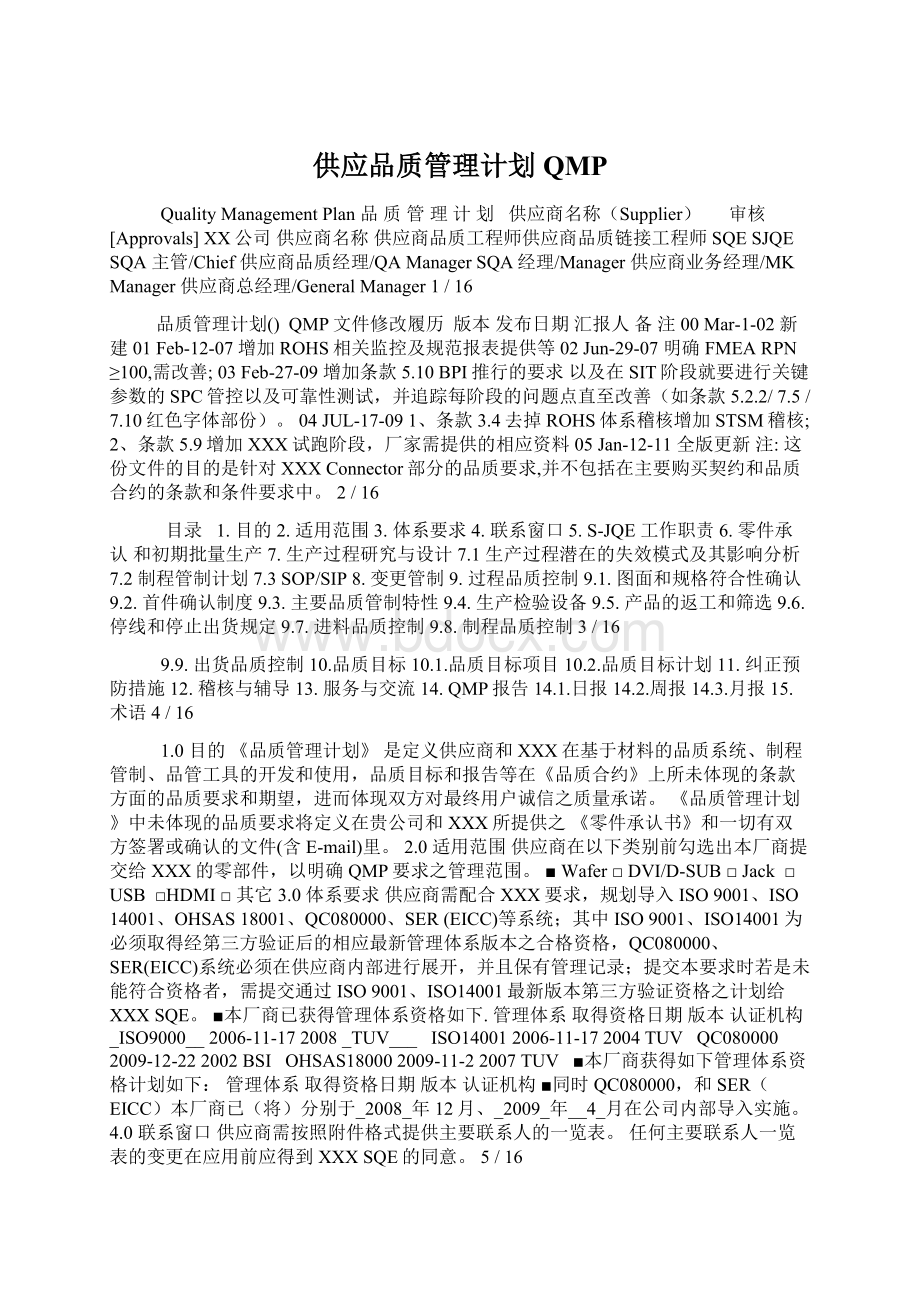
■本厂商已获得管理体系资格如下.管理体系取得资格日期版本认证机构_ISO9000__2006-11-172008_TUV___ISO140012006-11-172004TUVQC0800002009-12-222002BSIOHSAS180002009-11-22007TUV■本厂商获得如下管理体系资格计划如下:
管理体系取得资格日期版本认证机构■同时QC080000,和SER(EICC)本厂商已(将)分别于_2008_年12月、_2009_年__4_月在公司内部导入实施。
4.0联系窗口供应商需按照附件格式提供主要联系人的一览表。
任何主要联系人一览表的变更在应用前应得到XXXSQE的同意。
5/16
CriticalContactMatrix.xls5.0S-JQE工作职责(SupplierJointQualityEngineer)5.1供应商应按要求在组织内部明确指定一名SJQE,就所交XXX零件负责以下事项:
■推行并管理供应商处产品的品质计划与实施;
■管理与执行供应商处的产品检测与检验工作;
■主导推动供应商处产品品质改善专案,如BPI、6Sigma等等;
■收集、分析供应商处产品品质数据,形成相应的品质日报/周报/月报提供给XXXSQE;
■执行ECN/ECR流程,确保工程变更落实执行;
■确保CLCA案件与FA/CA落实执行与结案;
■代表XXXSQE在厂内实施定期的QSA/QPA稽核工作,并将稽核的报告提供给XXX;
■配合XXX完成新产品的数据收集、FAI管理等;
■XXX要求的临时事项的处理。
5.2若供应商所指定SJQE之服务能力达不到XXX要求时,应依照XXX要求予以更换。
6.0零件承认和初期批量生产6.1供应商依XXXRD零件承认流程及零件工程师要求的进度,提供样品及相应测试报告等。
6.2对于提交给XXX的新类型零件,供应商须在初始批量生产前或初期批量生产首三批时提供如下文件给XXXSQE承认。
在未获得XXXSQE承认前不得安排继续批量生产。
6.2.1初始批量生产前需要提交给XXXSQE的资料:
■制程失效模式及效应分析(PFMEA)■QC工程图■检验规范/制程检验规范(SIP)■重点岗位员工培训记录初期批量生产首三批时每批需要提交给XXXSQE的资料:
■电气性能测试报告■关键产品尺寸/特性能力评估资料:
Cp≧2.0,Cpk≧1.5(30pcs/穴(或模))■制程良品率■信赖性测试报告6.2.2处置措施□完全认可:
供应商依交货计划生产满足TPV规定规格和要求之产品.□条件认可:
限时或限量交货.原因分析及改善计划必须在限期内提交XXX承认.□不认可:
产品/文件必须全部改善完成并重新提交XXX承认和批准后方可生产出货.7.0生产过程研究与设计6/16
对于提交给XXX的新类型产品,供应商须按照以下要求进行生产过程的研究与设计。
7.1生产过程潜在的失效模式及其影响分析(PFMEA)在初始批量生产之前或开始时,供应商就要开始对产品的生产过程进行有效的设计,评估和确认,必要时必须对关键制程通过DOE以找到最优化制程参数,确保产品质量的稳定性和可靠性。
PFMEA有效执行于生产过程中,尤其RPN高的项目(RPN统一规定大于100的为高风险,各项采用10分制),确实实施改善措施。
供应商参照附件PFMEA格式完成PFMEAformat.xls7.2QC工程图供应商要依据PFMEA执行结果和以往产品的生产管理经验,制定QC工程图,以指导产品生产工序流程的排布与管制。
QC工程图应包含了从进料检验到最后运输出货的所有过程。
QC工程图中包含如下项目,按照附件之格式提供报备给TPVSQE。
工序名称操作规范■■关键参数使用材料■■检验检查点控制点/标准■■工具或设备检验方法■■抽样方法及SPC类操作责任人■■作业指导书■QC工程图格式:
QC工程图(Form).xls依据PFMEA和QC工程图、XXX零件承认书等制定各生产工序和检验工站之SOP/SIP,并在SOP/SIP中清楚的定义了产品的作业标准,检验方法,测试及允收之标准。
7/16
8.0变更管制工程变更的管制包括了工程变更申请(ECR)和工程变更通知(ECN)两部分。
前者是供应商在实施变更时,需要先向XXX提出ECR申请;
后者是XXX发给供应商的ECN,供应商依此实施变更。
8.1变更申请(ECR)8.1.1供应商计划进行的工程变更,将影响到产品兼容、调整、可靠性/市场问题,或为改变原材料、生产的内部变更时,须提交ECR给XXXRD零件部和SQE。
供应商在提交ECR书面的资料中应包括所有能证明变更可以导入的资料。
只有XXX认可变更才可以导入。
以下变更给XXX承认:
■产品设计变更■原材料变更■供应商变更■模具变更■关键工序之生产设备■产品包装变更和LOGO变更■产地变更■生产流程变更■工艺参数变更8.1.2厂地发生变更时,须向TPV申请实地评鉴,评鉴包括了QSA和QPA。
8.2变更通知(ECN)XXX实施零件变更时,零件RD会发出ECN给供应商。
供应商接到ECN的一周(7日)内须回复XXX零件RD关于变更的意见、库存品状况和导入计划。
否则,XXX视为供应商同意强制变更。
8.3实施变更前,确保所有的相关文件得到了更新与发放。
QC工程图文件在每次更新后须提交报备给XXXSQE。
8.4供应商应建立变更管制List,供XXX需要时查阅。
9.0过程品质控制9.1图面和规格符合性确认9.1.1供应商必须确保订单上的料号,版本同图面上的料号,版本一致.如果不符而冒然生产所产生的损失由厂商自己承担。
8/16
9.1.2供应商必须严格按照客户图面上的规格要求生产,遵循客户给出的工程标准要求,并主动调查了解该行业/工程标准是否有更新,积极与TPV及客户协调最新标准的落实执行情况。
9.1.3供应商正式生产之前必须确认零件之图面或规格是最新版本,当厂商无法确认是最新版的图面前应暂做停线处理,除非得到TPV或客户方面的书面同意方可恢复生产。
9.2首件确认制度供应商应建立首件确认制度,以在批量生产前确保所生产品与最新版的图面或规格相符。
9.3主要品质管制特性9.3.1所有尺寸,功能和其它规格要求依照承认书、工程图面或SOP。
9.3.2关键产品参数供应商须依承认书或规格要求合理选择关键产品参数,使用SPC管制并选择适当■的管制图类型,定期监控以确保这些参数得到有效控制。
本厂商对于各产品所管制的产品特性参数以及所采用的管制图类型如下:
产品类型工序名称管制特性管制图类型管制频率管制图上的点显示制程失控或异常发生时,或CpK能力不足时要采取■在监控过程中改进措施。
可靠性测试要求9.3.3■供应商应制定《产品(零件)可靠性测试计划》,保留测试记录,必要的时候,采取CLCA追踪结案.TPVSQE会定期确认可靠性之实施情况,同时TPVSQE保留将可靠性测试不合格信息报告给客户的权利.■如供应商不愿或无法进行相应的可靠性测试,TPV可以选择并通知供应商由第三方完成同样的操作,费用由供应商支付。
■供应商应定期将《产品(零件)可靠性测试计划》的实施结果报告提供给XXXSQE9.4生产、检验设备9.4.1供应商为确保进料品质、制程管控、出货检验,将使用如下检测仪器。
9/16
■进料检验:
2.5次元影像測量儀■制程检验:
2.5次元影像測量儀■出货检验:
2.5次元影像測量儀/卡尺9.4.2如果缺乏足够的检验设备确保产品品质之符合性,本厂商将采取如下方法加强产品控制:
現有檢驗設備儀器可滿足現生產需求9.4.3所有检测仪器需要有定期的校正计划,委托外校机构需要有相应的资质。
9.4.4所有检测仪器和生产设备、治工具需保留有校正记录和/或保养记录、寿命管制记录。
9.5产品的返工和筛选9.5.1返工与筛选的程序应形成文件,以规定内部返工和筛选流程。
9.5.2发生在XXX或XXX市场上退货,决定返工或筛选时,需将返工或筛选作业流程与指导书提交XXXSQE核准许可,未经XXXSQE的许可不得私下操作。
9.6停线和停止出货规定9.6.1供应商应制定停线和停止出货的规定,以防止重大品质问题在采取防范措施前继续发生和漫延。
9.6.2停线或停止出货发生时,供应商应采取预防纠正措施。
9.6.3停止出货发生时,SJQE需及时通报给XXXSQE,并在24Hrs内提交CLCA给XXXSQE审核批准后方可恢复出货。
9.7进料品质控制9.7.1物料需从AVL厂商处采购,供应商按照如下AVLList格式提供AVL清单。
AVL发生变更时,要及时更新AVLList(要版本控制),并报备给XXXSQE。
AVLformat.xls10/16
9.7.2AVL名册中的供应商应是按照供应商评鉴程序的规定进行了适当的评鉴与认可。
供应商之进料检验规范进及料检验抽样计划9.7.39.8制程品质控制供应商须依据生产工序特点和产品特性要求确定关键工序控制点,并明确在QC工程9.8.1图中。
对于关键工序控制点,要采用适当的监控手段(如点检表、管制图等)予以管制。
本供应商对于各产品之关键工序控制点所采用的监控手段如下:
产品类型工序名称控制点监控方式监控频率_____________________________________________供应商之制程检验规范9.8.29.8.3供应商之制程IPQC抽样计划9.9出货品质控制9.9.1供应商至少每类型料号都要制定出货检验SIP。
出货前各检验须依照XXX已核准的产品规格和行业要求进行。
每批出貨需按XXX要求提供电子档《出货检验报告》和相关RoHS報告一起交给9.9.2XXX。
XXX料号、版次、数量、批号、制造日期、合格标签和RoHS標签必须在最小包装9.9.3上标示清楚。
供应商所采用的标签[含产品标识,料号编码说明]、包装规格/图案等按附件给XXX。
在产品承认前完成运输,储存和包装测试,测试结果及其SOP提交XXXSQE确认.9.9.4供应商执行下列运输/包装测试:
跌落测试其它试验1□□:
______________________■振动实验其它试验2:
□______________________注意:
对于尾数箱的包装方式,供应商也应评估并文件化的规定包装要求,以防止因包装方式的不适当造成品质问题。
11/16
品质目标10.010.1供应商应以上一自然年度之下半年实际水平为基础,对所交XXX材料制定本自然年度的品质目标品质目标可按季度分别订定目标值。
此目标的设定须报备XXXSQE。
品质目标项目至少包括:
电测不良率<计算方法:
Σ电测不良品数/电测数量*1000000(DPPM)>■制程不良率<计算方法:
Σ各工序不良数/总投入数*1000000(DPPM)>■出货检查批退率<计算方法:
出货检查批退率=不合格批数/检查批数*100%)>■出货检查不良率<计算方法:
出货检查不良数/抽样检查数*1000000(DPPM)>■XXX客户抱怨次数<计算方法:
累计抱怨次数(次数))>■10.22011年品质目标计划■XXX材料LRR目标计划(单位:
DPPM)材料类别Q1-Y11Q2-Y11Q3-Y11Q4-Y11Wafer30282624■供应商品质目标计划品质指标项Q1-Y11Q2-Y11Q3-Y11Q4-Y11电测DPPM2500PPM15000PPM15000PPM15000PPM制程DPPM20000PPM20000PPM20000PPM20000PPM出货检查批退率0.5%0.3%0.3%0.25%出货检查DPPM1000PPM1000PPM500PPM500PPMXXX客户抱怨次数011110.3品质目标要尽可能按照产品类型进行分解,如Wafer、DVI、D-SUB、Jack、USB、HDMI等等。
10.4供应商应至少每周/每月要对前三项不良进行原因分析采取措施。
12/16
11.0纠正预防措施11.1供应商内部应制定纠正预防措施程序,以维持与提升品质水平。
11.2供应商发生XXX月品质目标未达标、清仓、拆箱不合格、产线每周不良品退货等问题时,要采取矫正预防措施,形成CLCA报告,CLCA采用标准的7/8D格式(见附件)。
CLCAFormat.doc11.3在XXX产线或客户端质量事件重复发生3次或潜在性质量问题,XXXSQE会要求供应商发起CIP改善项目,预防再度发生。
11.4所有CLCA都要进行有效性确认,有效性确认时要规定一定的总批数与总数量,所确认之对象批均有效时方可予以结案,否则需要重新检讨或采取新措施。
本厂商之客户抱怨处理程序如附件:
12.0稽核与辅导12.1自主稽核:
供应商应按照XXX之QSA和QPA检查表要求依不低于1次/年的频率进行内部品质稽核,检查结果与改善报告由S-JQE提报给XXXSQE。
每次实施稽核前,要与XXXSQE确认是否为最新版的QSA/QPA。
12.2XXX稽核与辅导:
XXX稽核与辅导按照需要分为定期稽核和不定期稽核与辅导两种,供应商应积极配合XXX的稽核与辅导要求。
■定期稽核正常情况下,XXXSQE依不低于1次/两年的频率在供应商现场执行品质系统和生产过程稽核(QSA/QPA)。
■不定期稽核与辅导在以下情况,XXX会实施临时性的现场稽核与辅导●新产品试产或批量开始时●产线上出现异常或客户端品质异常时●TPV客户要求时供应商收到稽核缺失报告后,必须于7个工作日内回复改善行动方案,并于一个月内全12.3部结案(特殊情形除外)。
13/16
稽核不合格者,视需要XXXSQE将于三个月后安排复核,供应商必须予以全力配合。
12.413.0服务与交流13.1厂商来料在XXX因突发的或严重的异常可能导致停线的,在接到XXXSQE电话(或邮件)通知后,须于1H内回复应急措施。
必要时,供货商安排工程师以上人员到XXX现场协助分析处理。
13.2CLCA报告回馈时限要求:
■国内厂商:
关键问题3个工作日内回复、重要问题7个工作日内回复、一般问题15个工作日内回复。
■国外厂商:
关键问题请于7个工作日内回复;
重要问题请于15个工作日回复;
一般问题请于22个工作日内回复。
13.3对于客户指定的供应商,CLCA跟催不回复或改善效果不明显的,XXXSQE可以直接向客户报告。
13.4供应商应XXX要求,因品质异常将派员至XXX驻厂检验。
13.5依照XXXSQE要求定期提交品质报告,或其它临时性的品质相关资料。
13.6在XXX要求的场合,供应商应安排相关人员至XXX参加QBR会议,或MQR会议,或临时性的品质检讨会议。
13.7XXX要求供应商所安排的质量服务人员,需具备如下基本能力:
■了解交付给XXX产品的生产流程和产品特性;
■懂得最基本ISO知识;
■经历过CP/CPK,SPC基本运用培训;
■有一定沟通技巧及能力;
■有一定报告的能力。
14.0QMP报告14.1日报~以出货检验报告替代,不在另行提供。
dailyreportformat.xls14.2周报~上周周报在本周二前提交给XXXSQE。
具体内容如下:
●电测不良率14/16
●制程不良率●出货检查批退率●出货检查不良率●CLCA●NPI(注:
指提交给XXX的新类型产品)。
weeklyreportformat.xls14.3月报~上月的月报应在本月的10日前提交给XXXSQE。
●电测不良率●制程不良率●出货检查批退率●出货检查不良率●XXX客户退货率●产品关键特性Cpk●CLCA●NPI(注:
指提交给XXX的新类型产品)monthlyreportformat.xls15.0术语AVLApprovedVendorListCLCAClosedLoopCorrectiveActionCACorrectiveActionDPPMDefectPartPerMillionECNEngineeringChangeNotificationECREngineeringChangeRequestFAFailureAnalysisFMEAFailureModeEffectAnalysisIPQCIn-processQualityControlIQCIncomingQualityControlJQEJointQualityEngineerNPINewProductIntroduceOQCOutgoingQualityControlPFMEAProcessFailureModeEffectAnalysisQMPQualityManagementPlanQPAQualityProcessAudit15/16
QSAQualitySystemAuditRMAReturnMaterialAuthorizationSJQESupplierJointQualityEngineerSPCStatisticalProcessControlSQESupplierQualityEngineer16/16