江苏大学材料工艺课程设计Word格式.docx
《江苏大学材料工艺课程设计Word格式.docx》由会员分享,可在线阅读,更多相关《江苏大学材料工艺课程设计Word格式.docx(3页珍藏版)》请在冰豆网上搜索。
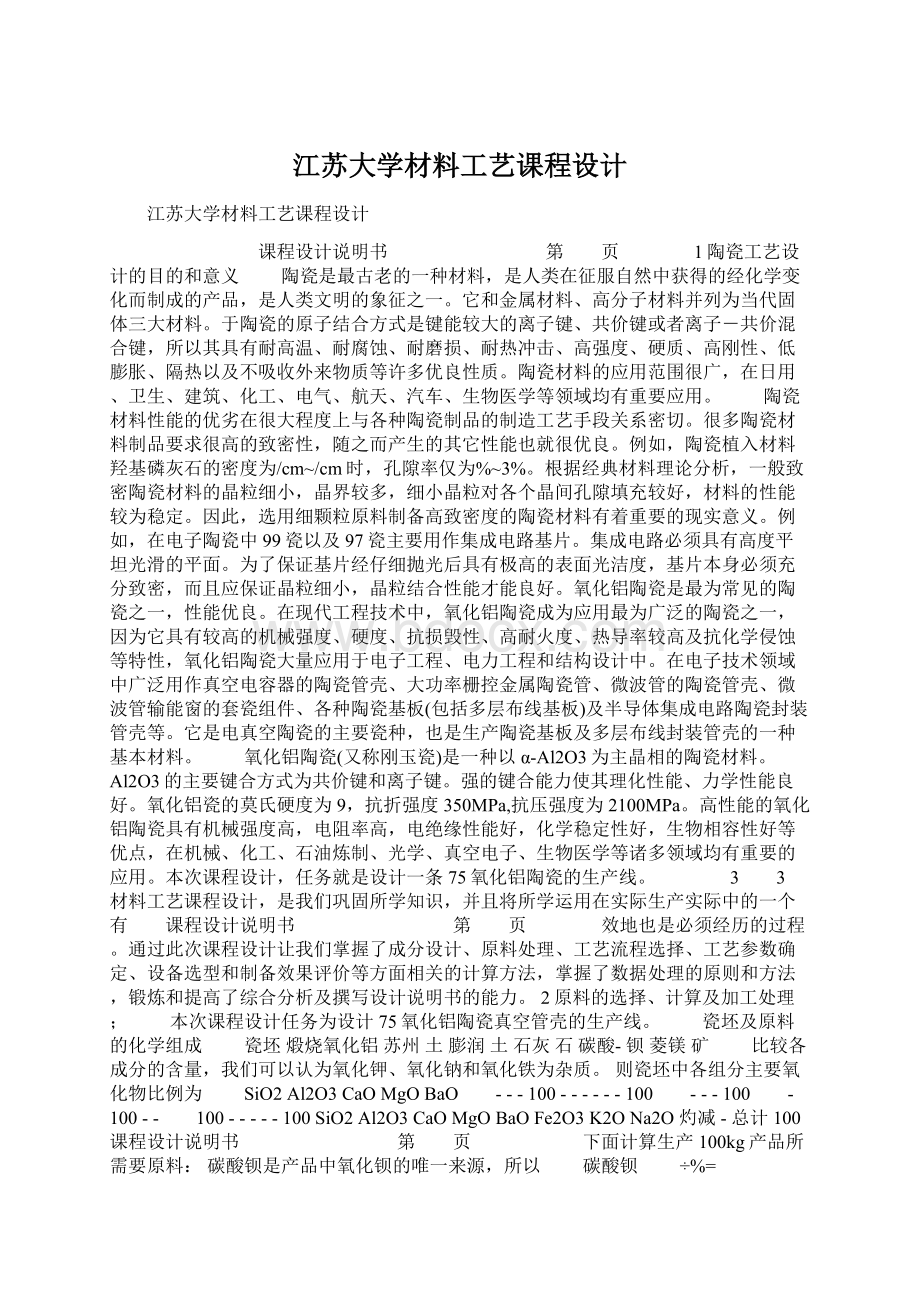
因此,选用细颗粒原料制备高致密度的陶瓷材料有着重要的现实意义。
例如,在电子陶瓷中99瓷以及97瓷主要用作集成电路基片。
集成电路必须具有高度平坦光滑的平面。
为了保证基片经仔细抛光后具有极高的表面光洁度,基片本身必须充分致密,而且应保证晶粒细小,晶粒结合性能才能良好。
氧化铝陶瓷是最为常见的陶瓷之一,性能优良。
在现代工程技术中,氧化铝陶瓷成为应用最为广泛的陶瓷之一,因为它具有较高的机械强度、硬度、抗损毁性、高耐火度、热导率较高及抗化学侵蚀等特性,氧化铝陶瓷大量应用于电子工程、电力工程和结构设计中。
在电子技术领域中广泛用作真空电容器的陶瓷管壳、大功率栅控金属陶瓷管、微波管的陶瓷管壳、微波管输能窗的套瓷组件、各种陶瓷基板(包括多层布线基板)及半导体集成电路陶瓷封装管壳等。
它是电真空陶瓷的主要瓷种,也是生产陶瓷基板及多层布线封装管壳的一种基本材料。
氧化铝陶瓷(又称刚玉瓷)是一种以α-Al2O3为主晶相的陶瓷材料。
Al2O3的主要键合方式为共价键和离子键。
强的键合能力使其理化性能、力学性能良好。
氧化铝瓷的莫氏硬度为9,抗折强度350MPa,抗压强度为2100MPa。
高性能的氧化铝陶瓷具有机械强度高,电阻率高,电绝缘性能好,化学稳定性好,生物相容性好等优点,在机械、化工、石油炼制、光学、真空电子、生物医学等诸多领域均有重要的应用。
本次课程设计,任务就是设计一条75氧化铝陶瓷的生产线。
3 3 材料工艺课程设计,是我们巩固所学知识,并且将所学运用在实际生产实际中的一个有 课程设计说明书 第 页 效地也是必须经历的过程。
通过此次课程设计让我们掌握了成分设计、原料处理、工艺流程选择、工艺参数确定、设备选型和制备效果评价等方面相关的计算方法,掌握了数据处理的原则和方法,锻炼和提高了综合分析及撰写设计说明书的能力。
2原料的选择、计算及加工处理;
本次课程设计任务为设计75氧化铝陶瓷真空管壳的生产线。
瓷坯及原料的化学组成 瓷坯煅烧氧化铝苏州土膨润土石灰石碳酸-钡菱镁矿 比较各成分的含量,我们可以认为氧化钾、氧化钠和氧化铁为杂质。
则瓷坯中各组分主要氧化物比例为 SiO2Al2O3CaOMgOBaO ---100------100 ---100 - 100-- 100-----100SiO2Al2O3CaOMgOBaOFe2O3K2ONa2O灼减-总计100课程设计说明书 第 页 下面计算生产100kg产品所需要原料:
碳酸钡是产品中氧化钡的唯一来源,所以 碳酸钡 ÷
%= 设煅烧氧化铝akg,苏州土bkg,膨润土ckg,石灰石dkg,菱镁矿ekg,则列出如下方程 二氧化硅%a+%b+%c+%d+%e=氧化铝 %a+%b+%c+%d+%e=氧化钙 %b+%c+%d+%e=氧化镁 %c+%d+%e= 根据所查市场价格,苏州土市场均价为1500元/t,一级膨润土市场均价为500元/t,苏州土价格较膨润土相比过高,从控制成本考虑选择苏州土与膨润土的比例为1:
4,则:
4b=c 联立以上5个方程解得:
a=,b=,c=,d=,e=综上,生产100kg产品,需要设煅烧氧化铝,苏州土kg,膨润土kg,石灰石,菱镁矿kg,碳酸钡。
设计的生产线日产量为1215×
150×
10÷
300=6075000=6075kg则需要的原料为:
煅烧氧化铝 ÷
100×
6075=苏州土 ÷
6075=膨润土 ÷
6075=kg石灰石 ÷
6075=菱镁矿 ÷
6075=碳酸钡 ÷
6075=原料总计质量为 4 +++++= 3工艺原理运用、工艺流程选择与工艺方法确定;
工艺流程:
配料→湿磨→泥浆的过筛、除铁→喷雾造粒→等静压成型→半成品加工→热等静 课程设计说明书 第 页 压烧成→磨加工→成品原料粉体制备 陶瓷工业伸长粉碎加工断的最通常任务是将大块的长石、石英、干硬泥块等物料进行粉碎知道达到球磨机对于入料的要求,大致尺寸范围100~300mm至~3mm。
为此,一台机械难以完成任务。
于主要原料膨润土主要成分是二氧化硅和氧化铝,硬度为1~2,故此次组合如下:
颚式破碎机粗中碎→旋磨机细碎粗磨→球磨 颚式破碎机,是通过鄂板摆动对物料进行破碎,其特点是产量大,但破碎比较小,一般为4。
旋磨机,又称碾轮机,主要是通过碾轮的重力作用及碾轮与碾盘之间的相对滑动用对物料进行破碎与研磨。
其特点是可用干碾,也可用湿碾,碾轮和碾盘多是石质的,可有效的防止铁质带入。
此次设计的工艺采用间歇式球磨机,采用湿磨,它既可细碎并且混合,球磨机筒体的长径比一般<2,为不致污染原料,球磨机的衬板和磨球应采用硬质岩石或瓷质的磨球,内衬采用橡胶内衬。
筛分是使固体颗粒通过具有一定大小孔径或细缝的筛面,通过筛孔的筛下料,被截留在筛面上的为筛上料。
陶瓷原料需要筛分的重要原因在于①利用筛面的截留作用去除原料中有害杂质,例如泥浆中的云母、颗粒快等。
②控制筛物料粒度和级配,因为原料的细度会直接影响泥料或泥浆的成形、烧成性能。
原料除本身含铁外在加工及运输过程中混有一定量的铁质,通过磁选机或永久磁铁出去 [3] [2] [1] 强磁型物质。
泥浆漏斗加入,然后在静水压的租用下,下往上经过筛格板,则含铁杂志被吸住,而净化的泥浆溢流槽流出,筛格板应定时取出,进行冲洗。
喷雾造粒时将一定浓度的溶液或悬浮液通过雾化分手拿起分散成洗涤,在干燥塔用热风干燥而获得颗粒状粉料的过程,即将有一定水分的泥浆直接地一次性地制成颗粒状粉料。
喷雾干燥制粉最主要的特点在于:
①可以实现全自动化的生产功一次完成,进去的是泥浆,出来的是颗粒。
②颗粒粉料是一颗颗似苹果形状具有很好流动性的粉料,满足了成型对粉料的要求。
③于使用了热风干燥,所以需要消耗较多的能源。
成型 课程设计说明书 第 页 陶瓷产品的成型是将坯料加工成具有一定形状和尺寸的半成品。
陶瓷产品的种类很对,形状也相差悬殊,不同类型的陶瓷产品对坯料性能和制备工艺也不相同。
目前在陶瓷真空管壳的生产中常用的成型方法有以下几种:
热压铸、注浆、干压和等静压法。
现就这几种成型方法的特点及其对产品性能的影响分析如下:
热压铸造成型法是我国陶瓷真空管壳生产中使用最早且普遍的一种成型方法。
它主要是 利用石蜡料浆加热融化后具有流动性和可塑性,冷却后能在金属模中凝固成一定形状这一特点来完成的。
成型过程的具体操作是将加热后的石蜡混合粉料用空气压力将料浆注人模中,冷却定型。
热压铸成型法的优点是能制作形状复杂、精密度高的中小型制品、工效高、产量大设备投资小、操作简单、模具损耗少。
其缺点是工序繁杂、粉尘多、工期长,不适用大件、薄壁产品。
于热压铸成型在配料中添加了有机物,因此多了一道排蜡工序,且在排蜡、注模等工艺过程中容易有空气介入,排蜡时有机物的排出,很容易使制品产生不均匀的气孔。
烧后产品中气孔有开口和闭口两种,开口气孔用肉眼容易看到,一般检验后就能剔除,而闭口气孔存在于晶粒之间或晶体内部,一般不易查到。
这对真空陶瓷管壳无疑是一大危害,直接影响到陶瓷制品的体积密度、气密性。
况且,于成型压力小,受力不均,烧成后制品的均匀性、电气性能和透液性都受到一定的影响。
因此在国外很少用热压铸方法来制作陶瓷真空管壳。
干压成型法是将粉料采用机械压力强制压人模内的一种成型方法。
干压成型的优点是操 作简单、方便、周期短、工效高、产品精度高、产量大,机械强度和电性能也较好。
缺点是设备投资大,只能生产形状较为简单而又扁平的产品。
对模具要求很高而且损耗大。
干压的主要问题是对于较高的制品存在纵横压力的差异。
如果采用双向加压法成型,于受压方向的局限性和压力传递的影响,在制品的中间部位也存在着压力小、收缩较大,密度较低的缺陷。
因此也不很适宜用来制作中大型陶瓷真空管壳。
其烧后产品于受加压方式或作用力方向以及配料流动性的影响,局部气孔仍然存在,层次感也较明显,但总体烧结程度及气孔状况较前两者要好。
注浆成型法是传统陶瓷生产最常用的一种成型方法。
它主要是利用石膏模型的毛细管作用力将悬浮的浆料吸附于模具内壁而形成一定形状和强度的坯件。
这一传统工艺也被应用于工业陶瓷的生产。
其注浆成型的优点是能制作一些形状复杂且不规则、制品大且尺寸要求不严的产品,工艺简单、模具投资小。
缺点是劳动强度大,生产周期长,环境卫生差。
等静压成型法是一种先进的成型方法是,利用液体介质不可压缩性和均匀传递性的特点