实习报告汇总Word文件下载.docx
《实习报告汇总Word文件下载.docx》由会员分享,可在线阅读,更多相关《实习报告汇总Word文件下载.docx(73页珍藏版)》请在冰豆网上搜索。
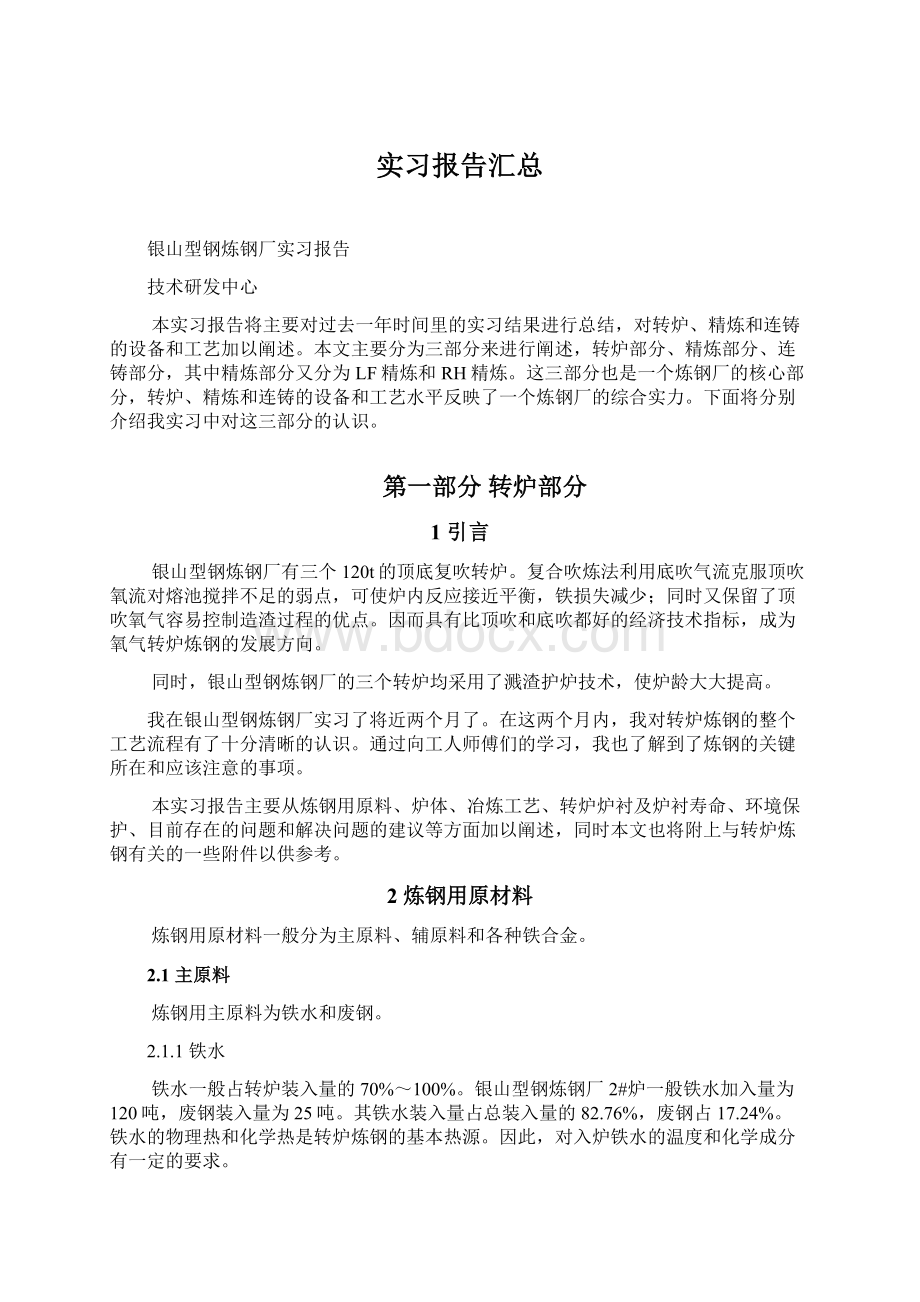
⑵加剧对炉衬的冲蚀。
⑶初期渣中
SiO2超过一定数值时,影响石灰的渣化,从而影响着成渣速度,也影响着P、S的脱除,延长了冶炼时间。
②锰(Mn)
铁水锰含量对冶炼有益,促进初期渣早化,改善熔渣流动性,利于脱硫和提高炉衬寿命;
减少氧枪粘钢;
还利于提高金属收得率;
同时终点钢中余锰高,能够减少合金用量等。
当前使用较多的为低锰铁水,一般铁水中
Mn=0.20%~0.40%。
银山型钢炼钢厂转炉入炉铁水的Mn含量基本上维持在0.32%左右。
③磷(P)
磷是强发热元素,通常是冶炼过程要去除的有害元素。
转炉的脱磷效率在85%~95%,铁水中磷的含量越低,转炉工艺操作越简化,并有利于提高各项技术经济指标。
铁水中磷来源于铁矿石,根据磷含量的多少,铁水可以分为以下三类:
P<0.30%低磷铁水;
P=0.30%~1.00%中磷铁水;
P>1.50%高磷铁水。
银山型钢炼钢厂转炉用铁水的磷含量为0.80%左右,属于中磷铁水。
④硫(S)
除了含硫易切钢(要求
S=0.08%~0.30%)以外,绝大多数钢中硫是有害元素。
转炉中硫主要来自于金属料和熔剂材料等,而其中铁水的硫是主要来源。
在转炉内氧化气氛中脱硫是有限的,脱硫效率有35%~45%。
近些年来由于低硫
S<0.01%的的优质钢的需求量急剧增长,因此用于转炉炼钢的铁水要求
S<0.02%,有的要求甚至更低。
银山型钢炼钢厂转炉用铁水硫含量为0.025%左右。
同时要求铁水入炉之前应扒渣,渣厚不能过厚。
银山型钢炼厂将入炉铁水的渣厚控制在100mm左右。
下面将银山型钢炼钢厂入炉铁水的基本情况列于表1。
表1银山型钢炼钢厂入炉铁水基本情况
铁水量/t
温度/0C
化学成分/%
渣厚/mm
Si
Mn
P
S
121
1371
0.70
0.34
0.87
0.036
95
1324
0.63
0.69
0.029
1270
0.46
0.77
0.035
90
121.4
1338
0.32
0.80
0.026
100
1263
0.56
0.33
0.76
0.024
1360
0.73
0.82
0.033
1342
0.67
0.30
0.83
0.009
1379
120
120.8
1260
0.90
0.028
1310
0.84
0.018
从表中可以看出,铁水的装入量稳定在121吨左右,温度稳定在13000C左右,波动较大。
Si含量波动在0.60%左右,Mn含量波动在0.32%左右,P含量波动在0.80%左右,硫含量含量波动0.025%左右,基本符合入炉铁水的要求。
2.1.2废钢
废钢是转炉炼钢的主原料之一,是冷却效果稳定的冷却剂。
通常占装入量的30%以下。
适当地增加废钢比,可以降低转炉钢消耗和成本。
银山型钢炼钢厂入炉废钢维持在17.24%左右。
废钢的外观形状尺寸、质量和入炉数量对炼钢的正常操作、产品质量,甚至炉衬寿命都有重要影响。
所以,对转炉炼钢用废钢应有一定要求。
其要求如下:
⑴废钢的外形尺寸和块度应保证能从炉口顺利加入转炉。
废钢单重不能过重,以便减轻对炉衬的冲击。
同时在各吹炼期必须全部熔化。
轻型废钢和重型废钢合理搭配使用。
⑵废钢中不得混有铁合金。
严禁混入铜、锌、铅、锡等有色金属和橡胶,不得混有封闭器皿、爆炸物和易燃易爆品以及有毒物品。
废钢中的硫、磷含量均不得大于0.050%。
⑶废钢应清洁干燥,不得混有泥沙、水泥、耐火材料、油物、珐琅等,不能带水。
⑷废钢中不能夹带放射性废物,严禁混有医疗临床废物。
⑸废钢中禁止混有其浸出液中pH值大于等于12.5或小于等于2.0的危险废物。
⑹不同性质的废钢应分类存放,以免混杂,如低硫废钢,超低硫废钢,普通废钢等。
2.2辅原料
2.2.1石灰
石灰的主要成分CaO,是炼钢的主要造渣材料,具有脱P、脱S能力,也是用量最多的造渣材料。
其质量好坏对冶炼工艺操作,产品质量和炉衬寿命有着重要影响。
石灰的渣化速度是转炉炼钢过程成渣速度的关键。
所以炼钢用石灰除了有效CaO含量要高,SiO2和S含量低,适当的块度要求外,对其活性度也提出要求。
活性度大的石灰反应的能力强,成渣速度快。
2.2.2萤石
萤石的主要成分是CaF2。
纯CaF2熔点在14180C,萤石中还有其他杂质。
因此熔点还要低些。
造渣加入萤石可以加速石灰的熔解,萤石的助熔作用是在很短时间内能够改善渣的流动性。
但过多的萤石用量,会产生严重的泡沫渣,导致喷溅,同时加剧炉衬的损坏,并污染环境。
转炉炼钢用萤石的
CaF2应大于85%;
SiO2≤5.0%,
S≤0.10%,块度在5~40mm,并要干燥清洁。
2.2.3生白云石
生白云石即天然白云石,主要成分是CaMg(CO3)2。
焙烧后为熟白云石,其主要成分为CaO和MgO。
自20世纪60年代初开始应用白云石代替部分石灰造渣技术,其目的是保持渣中有一定的MgO含量,以减轻初期酸性渣对炉衬的侵蚀,提高炉衬寿命。
实践证明效果很好。
生白云石也是溅渣护炉的调渣剂。
银山型钢炼钢厂就是用白云石来调节渣中的MgO含量的,其溅渣护炉用的渣中MgO含量通常为8%左右。
2.2.4污泥块
污泥块作为辅助原料其加入量并不大,它在炼钢中起的作用主要是冷却作用。
其成分主要是铁的氧化物和CaO。
它是转炉炼钢的烟尘收集后再加入石灰经烧结压制而制成的,主要来原于炼钢的烟尘。
2.3铁合金
吹炼终点要脱除钢中多余的氧,并调整成分达到钢种规格,需要加入铁合金以脱氧合金化。
转炉常用的合金有Fe-Mn、Fe-Si、Mn-Si合金、Ca-Si合金、铝、Fe-Al、Ca-Al-Ba合金、Al-Ba-Si合金等。
此外,还有其他一些材料,如增碳剂、焦炭、氧气、氮气等。
其中增碳剂用来调整钢中碳含量,使其达到要求;
焦炭主要用于开新炉时烘烤炉衬;
氧气是炼钢吹炼的主要氧化剂;
氮气是底部供气的主要气体和溅渣护炉用气体
3转炉炉体特征
①公称容量:
120t。
同时允许一定的过装量,其实际装入量可以达到146t左右(其中废钢和生铁25吨左右,铁水121吨左右)。
②炉膛:
直径4.8m。
理想状态下炉膛直径为4.8m,但在平常状态下其直径要大于4.8m,以4.83m居多。
③炉底:
理想状态下是7.6m,但工作后炉底会有所改变。
目前炉底为7.57m。
④吹炼工艺:
采用顶底复吹的吹炼工艺。
顶部吹氧气,底部吹氮气。
吹炼时氧气的压力小于1.0MPa,采用变压变枪操作。
氧气流量在吹炼时为13558Nm3/h(在吹炼过程会有所变化)。
⑤吹炼时间:
我记录的一个原始数据是17分11秒。
通过我的观察,吹炼时间基本上维持在17分左右,少的可到15分甚至14分多,多的可到19分甚至可到20分还多。
这与物料情况和冶炼的钢种有关。
⑥氧枪:
银山型钢炼钢厂的三个转炉均配置了两个氧枪,南枪和北枪。
氧枪喷嘴是拉瓦尔管型结构,有五个喷孔,均匀分布于喷嘴的四周。
氧枪直径270mm。
⑦底部供气元件:
采用环缝管结构的喷嘴,有六个喷孔。
炉体的结构特征如图1所示:
1-氧枪;
2-气体控制板;
3-气体分配站;
4-储存罐;
5-底部供气喷孔;
6-炉帽;
7炉身;
8-炉底;
9–出钢口
图1转炉炉型示意图
银山型钢炼钢厂的三个转炉都是顶底复吹转炉,且炉型结构属于锥球型。
银山型钢炼钢厂的2#炉的标准熔池深度为1.3m,炉容比为0.90m3/t左右。
炉子底部全程吹氮。
虽然银山型钢炼钢厂的三个炉子都通有氩气,但是由于氩气的成本较高,因而氩气阀始终关闭,炉子底部全程吹氮进行搅拌。
表2是底吹气体各模式条件下各阶段的流量的设定值,由计算机自动控制。
表2各模式各阶段流量设定值(单位:
m3)
阶段
模式
兑铁装料
吹炼期(顶枪吹氧)
测温取样
点吹
出钢
溅渣
倒炉
等待
1
2
3
4
A
220
348
261
480
B
300
400
580
C
500
D
696
800
E
522
F
底吹气种
N2
Ar
底吹模式一般采用D模式。
从表中可以看出,底部设定值中是有Ar的,但在实际中全部吹的都是氮气。
同时,还要补充说明的是,吹炼和溅渣护炉用的是同一支喷枪(氧枪),氧气和氮气之间可以相互切换。
9月20日,银山型钢炼钢厂2#炉开始大修。
至此,银山型钢2#炉共冶炼了26668炉钢,其炉龄达到26668炉。
4冶炼工艺
炼钢的基本任务是:
脱碳、脱磷、脱硫;
去除有害气体和夹杂;
提高温度;
调整成分。
炼钢过程通过供氧、造渣,加合金搅拌、升温等手段完成炼钢的基本任务。
为了顺利完成转炉炼钢的基本任务,转炉炼钢冶炼通常采用五大制度:
装入制度、供氧制度、造渣制度、温度制度、终点控制及脱氧合金化制度。
同时本部分也将对副枪作一简单的阐述。
4.1装入制度
装入制度就是确定转炉合理的装入量,合适的铁水废钢比。
转炉的装入量是指主原料的装入数量,它包括铁水和废钢。
实践证明每座转炉都必须有个合适的装入量,装入量过大或过小都不能得到良好的技术经济指标。
若装入量过大,将导致吹炼过程的严重喷溅,造渣困难,延长冶炼时间,吹损增加,炉衬寿命降低。
装入量过小时,不仅产量下降,由于装入量少,熔池变浅,控制不当,炉底容易受氧气流股的冲击作用而被损坏,甚至使炉底烧穿,进而造成漏钢事故,对钢的质量也有不良影响。
银山大型2#转炉的装入量为146t左右,其中废钢25t左右,铁水121t左右。
在正常冶炼时废钢和铁水的加入顺序是先加废钢再兑铁水。
但补炉后的第一炉钢采用先兑铁水再加废钢的装入顺序。
同时,在冶炼时为了通过测液面来确定枪位也采用先兑铁水后加废钢的的装入顺序。
铁水和废钢的具体装入量见表3。
表3铁水和废钢的装入情况
铁水/t
废钢/生铁(t)
铁水温度/0C
25.88/18.38
1382
23.1/17.8
1333
25.7/19.5
1284
26.6/19.6
1345
120.2
1332
25.5/19
1351
26/18.7
1253
25.3/18.1
1364
从表3可以看出,铁水和废钢的总装入量维持在146吨左右,其中生铁121左右,废钢25吨左右,铁水温度大于12500C,满足装入要求。
而其中的25吨左右的废钢中包括18吨左右的生铁,废钢的实际装入量只有7吨左右。
4.2供氧制度
供氧制度就是使氧气流股最合理地供给熔池,创造良好的物理化学反应条件。
因此供氧制度内容包括确定合理的喷嘴结构、供氧强度、氧压和枪位操作。
4.2.1喷嘴结构
合理的喷嘴结构应使压力能最大限度地转换成速度能。
同时,喷出的氧流应该满足吹炼的要求。
在工艺操作上的反映是化渣的速度快、不喷溅,不粘枪,不烧枪,枪位稳定,便于控制。
所以选择合理的喷嘴结构是氧气顶吹转炉炼钢的关键之一。
银山型钢炼钢厂的三个转炉的氧枪喷嘴均采用拉瓦尔管型结构,且喷孔为五孔。
拉瓦尔管型结构喷嘴能够最大限度地把压力能(势能)转换成速度能(动能),获得最大流速的氧射流,因而被被广泛应用。
4.2.2枪位的影响
枪位在适当的范围内变动,可以调节熔池表面和内部的化学反应速度,尤其是碳氧反应速度,从而也起到调节熔池的搅拌作用。
如果短时间内采用高低枪位交替操作,还有利于消除炉内液面上出现的“死角”。
枪位与渣中TFe含量也有关系。
可以说在某种程度上,氧气顶吹转炉的氧枪操作,就是通过改变枪位来调节和控制熔渣中有合适的TFe的含量,以满足吹炼各期的需要。
同时枪位也对熔池的温度有影响。
采用低枪位操作,氧气、熔渣、金属液的接触密切,化学业反应速度快,结果熔池升温速度加快,吹炼时间短,热损失部分减少,炉温升高。
枪位高,反应速度缓慢,因而熔池升温速度缓慢,吹炼时间延长,热损失部分增多,温度偏低。
4.2.3枪位的确定
在确定合适的枪位时,主要考虑两个因素:
一是要有一定的冲击面积;
二是在保证炉底不被损坏的条件下,有一定的冲击深度。
①开吹枪位的确定原则是早化渣,多去磷。
②过程枪位的控制原则是化好渣,不喷溅,快速脱碳,熔池均匀升温。
在碳的激烈氧化期间,尤其要控制好枪位,枪位过低,会产生炉渣“返干”,造成严重的金属喷溅,有时甚至粘枪而损坏喷嘴。
枪位过高,渣中TFe含量较高,又加上脱碳速度快,同样会造成大喷溅或连续喷溅。
③吹炼后期枪位操作要保证达到出钢温度,拉准碳。
银山型钢炼厂2#转炉枪位操作采用变压变枪操作。
其枪位一般是开吹1.5m,基本枪位1.8m,终点枪位1.2m,氧压一般在0.78-0.92Mpa变化。
4.2.4供氧强度和氧压
银山型钢炼钢厂2#转炉吹炼时氧气压力为小于1.0MPa,在0.32-0.92Mpa之间变化;
氧气流量为13558Nm3/h(在吹炼过程有变化)。
吹炼时间基本维持在17分左右。
4.2.5枪位及枪位图
在银山型钢炼钢厂2#炉实习的第二个月,我特别关注了一下枪位的变化,并学会了如何通过标尺来看枪位。
现阐述如下。
要看枪位就要学会看标尺,标尺分为内标尺和外标尺。
实际上内标尺是不存在的,因为内标尺指的是测液面时从氧枪喷嘴到液面的铝条的长度。
通常测液面时将外标尺的游标放到1m处,测氧枪喷嘴到液面的铝条长度,进而可确定出枪位。
这么说还有点模糊,下面我举例说明。
例如当标尺读数为1m时,测得的铝条长为1.1m,那么当标尺读数为1.2m时,喷嘴到液面的高度,即枪位就是:
(1.2-1)+1.1=1.3m
且已知熔池深度为1.3m,那么此时喷嘴到炉底的高度为:
1.3+1.3=2.6m
同时在计算枪位时还要考虑加入废钢后液面上升的高度,通常要在液得液面的基础上再加上0.2m。
还要注意的是,标尺上“1”到“2”之间的真实距离不是1m,而是0.5m,即标尺上的每一小格代表的是0.05m而不是0.1m。
另外,电脑画面上显示的枪位和实际枪位也不太一致。
下面我将我记录的电脑上的数据和标尺上枪位数据列成表,并绘出枪位图。
表4电脑操作画面显示的数据
时间
0~5分30秒
~9分50秒
~11分50秒
~15分
16分30秒
~17分
~17分20秒
~18分35秒
枪位/m
1.9
2.0
2.1
2.2
2.4
1.7
1.5
图2根据电脑的显示的数据绘制的枪位图
在吹炼过程中,氧压变化范围为:
0.32~0.85~0.92Mpa.
下面是从标尺上读取的枪位数据,(液面1.3m)。
表5
0~6分
~9分30秒
~12分10秒
~13分10秒
~14分40秒
~16分30秒
~17分30秒
~19分10秒
读数/m
1.4
1.6
1.8
1.0
表6
~17分40秒
~18分
~19分5秒
1.2
将表5和表6标尺上的读数换算成枪位数据,可以得到表7和表8的枪位数据。
表7
1.55
1.65
1.75
1.3
表8
根据表7和表8的枪位数绘制成的枪位图见图3和图4。
图3
图4
图中,枪位的单位是m,时间的单位是min。
从图中可以看出,枪位在一定范围内变化,变化幅度不是太大。
银山型钢炼钢厂2#炉的一般枪位操作要求是,开吹枪位1.5m,基本枪位1.8m,终点枪位1.2m。
由此可知标尺上的读数更接近操作实际枪位。
4.3造渣制度
造渣制度就是要确定合适的造渣方法,渣料的加入时间,以及如何加速成渣。
转炉炼钢造渣的目的是:
去除磷硫,减少喷溅,保护炉衬,减少终点氧。
造渣的方法有单渣操作、双渣操作、留渣操作等。
银山型钢炼钢厂2#转炉采用单渣操作。
同时同于采有了溅渣护炉技术,也间接地采用了留渣操作(可以看作留渣操作的特例)。
渣料的加入量要根据铁水成分及碱度等情况来确定。
银山型钢炼钢厂的三个转炉均采用溅渣护炉技术,这要求熔渣中有适量的MgO含量。
一般控制MgO含量在8%左右。
MgO在银山型钢炼钢厂主要是通过加入的白云石来获得,因此应确定合理的白云石加入量。
4.4温度制度
温度制度主要是指过程温度控制和终点温度控制。
吹炼任何钢种,对其出钢温度都有要求。
如果出钢温度过低,可能造成短锭,水口套眼、钢包粘钢、甚至要回炉处理如果出钢温度过高,不仅会增加钢液夹杂和气体含量,影响钢的质量,而且还会增加铁的烧损,降低合金元素的吸收率,降低炉衬寿命,造成连铸坯多种缺陷甚至浇注漏钢。
因此,控制好终点温度也是转炉吹炼工艺的重要环节之一。
终点钢水温度即出钢温度,它的确定要考虑钢种的凝固温度,还要考虑浇注钢水的过热度,以及从出钢到开始浇注过程中各阶段的温降。
银山型钢炼钢厂2#转炉冶炼Q235B和Q345B时的出钢温度一般控制在16700C左右。
4.5终点控制及脱氧合金化制度
4.5.1终点控制
出钢时机的主要根据是钢水的碳含量和温度,所以终点也称作“拉碳”。
银山型钢炼钢厂终点控制采用一次拉碳法。
这种方法要求终点碳和温度同时达到要求,否则需要补吹或增碳。
银山型钢炼钢厂出钢操作采用挡渣操作,其目的是有利于准确控制钢水成分,有效地减少回磷,提高合金元素吸收率,减少合金消耗。
同时,也提高了转炉出钢口的耐火材料的寿命。
挡渣的方法有挡渣球法、挡渣棒法、挡渣塞法、挡渣帽法、挡渣料法、气动挡渣器法等多种方法。
银山型钢炼钢厂常用的挡渣方法是挡渣球法、挡渣塞法和挡渣棒法。
4.5.2脱氧合金化制度
常用的脱氧方法有:
沉淀脱氧、扩散脱氧、和真空脱氧等。
银山型钢炼钢厂2#炉采用沉淀脱氧法。
沉淀脱氧时,铁合金直接加入到钢水中,脱除钢水中的氧。
这种脱氧方法效率比较高,耗时短,合金消耗较少,但脱氧产物容易残留在钢中会造成内生夹杂物。
常用的脱氧元素有Mn、Si、Al、Ca等。
由这些元素组成的合金作为脱氧剂,如Fe-Mn,Mn-Si合金、Fe-Si、Ca-Si合金、Fe-Al合金等。
银山型钢炼钢厂采用钢包内脱氧,即在出钢过程中,将全部合金加到钢包内。
这种方法简便,大大缩短了冶炼时间,而且能提高合金元素的吸收率。
4.5.3合金加入量的确定
吹炼终了,在出钢的过程中要加入合金进行脱氧合金化。
各种铁合金的加入量可按下列公式计算:
(kg/t)
这几个公式,很清楚地说明了合金加入量的确定方法。
一旦各种参数确定,便可算出合金加入量。
因此,不再详细阐述。
由于合金的的回收率不是太稳定,因此合金的加入量也不太稳定,主要是根据经验来估算的。
4.6副枪
4.6.1副枪的总体特点
采用副枪