H型钢轧机组施工方案Word文档格式.docx
《H型钢轧机组施工方案Word文档格式.docx》由会员分享,可在线阅读,更多相关《H型钢轧机组施工方案Word文档格式.docx(40页珍藏版)》请在冰豆网上搜索。
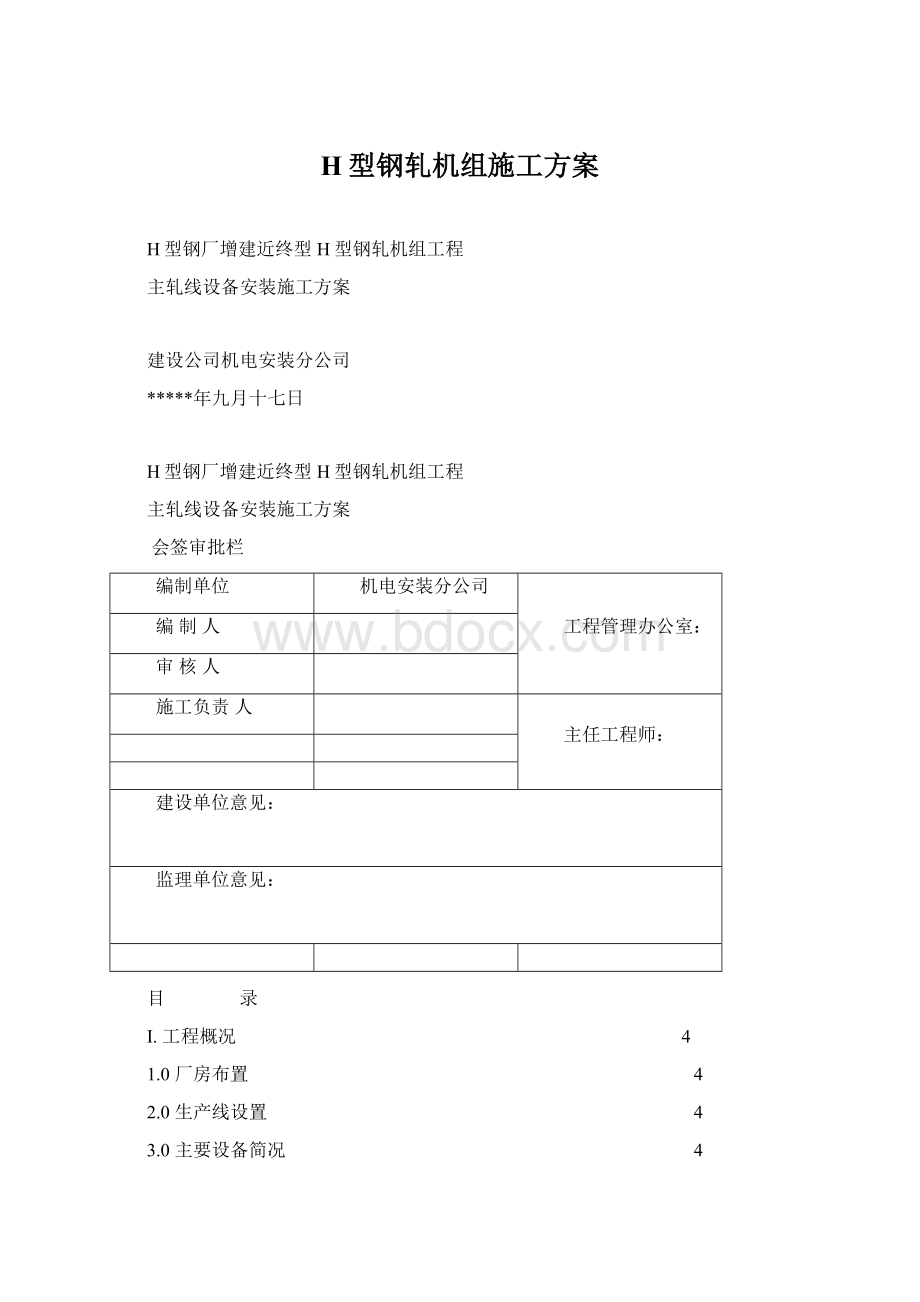
Ⅸ.环境因素及管理方案 40
Ⅹ.重大危险源及管理方案 41
Ⅺ.主要施工机具计划 44
Ⅻ.主要施工材料计划 45
附图一 工艺布置图 46
附图二 大临布置图 47
附图三 中心标板布置图 48
附图四 施工网络图 49
Ⅰ.工程概况
H型钢厂增建近终型H钢铸轧机项目,是为适应市场发展需要,使**的H钢产品能形成大、中、小系列规格及品种配套供货,以满足市场多方面需求,更好地为市场服务。
增建的中小型热轧H型钢,是从意大利DANIELI公司引进一套全连续轧制中小H型钢生产线,其全连续轧制工艺、工艺技术及轧制线主要机械设备由意大利DANIELI公司提供;
电气传动自动控制系统及计算机1级、2级控制系统,从TGA引进。
本工程年生产能力为50万吨,主轧线安装设备总重为2688吨,工艺平面布置图见附图图一。
1.厂房布置:
本车间位于原H型钢厂东侧成品3跨及空地处,由西向东设置两个跨间:
A—A0跨:
30×
492m、14760m2为原料、精整、成品库厂房;
A0—B0跨:
36×
480m、17280m2为主轧跨,跨东侧布置有主电室等辅助用房。
2.生产线设置:
生产线工艺设备设置在+5.1m平台上,辅助设备设置在地平面上
3. 轧制生产线主要设备简况:
3.1加热炉前设备共236.7t;
铸坯存放架:
54组、162t,
上料台架:
1套42.6t含液压驱动、拔爪机构、剔废装置
入炉前辊道及挡板:
1组26.7t,18辊单独传动,辊道长27m,
称量、测长装置:
1套5.4t称量压头,激光测长。
3.2加热炉后设备:
共65.03t:
出炉辊道<
一>
:
1组12.9t10辊单独传动,辊道长15m;
高压水除磷装置:
1套3.9t除磷箱3000×
2000mm,喷水压力;
P=250bar
二>
1组29.4t21辊单独传动,辊道长31.5m
剔废装置:
1组12.5t12×
0.9m8个拨杆、液压缸驱动
升降挡板:
1套1.64t,液压缸驱动
夹送辊:
1套4.69t,上辊液压缸升降,辊子为冷却水
3.3粗轧机组:
机架5组485.32t
机架布置为平立平平立(1H、2V、3H、4H、5V),微张力连续轧制,
机架为无牌坊机架组,有快速更换机架装置,进行整体更换机架。
减速机、齿轮箱、万向接轴传动。
3.4轧机组后设备:
共109.5t:
输出辊道:
1套51.1t34辊单独传动,辊道长51m;
剔废装置:
1套37.5t45×
0.9m32个拨杆液压缸驱动;
升降挡板:
1套1.6t液压缸驱动;
热保护罩:
8套13.6t;
火焰切割机:
1套0.35t;
中精轧入口夹送辊:
1套5.35t,上辊液压缸升降,棍子内水冷却。
3.5中精轧机组:
10机架765.57t:
6#、11#、14#为H型轧机(6H11H14H),其余为万能轧机(7H/U、8H/U、9H/U、10H/U、12H/U、13H/U、15H/U),微张力连续轧制,机架为无牌坊机架,有机架快速更换装置,进行机架整体更换。
2#、5#、11#轧机电机600KW,1#、3#、7#、12#轧机电机1300KW,4#、6#、9#、10#、13#、15#轧机电机1200KW,减速机、齿轮箱、万向接轴传动。
3.6剪前后设备:
共81.37t:
外形尺寸检测仪:
1套1.1t;
飞剪前夹送辊:
1套2t上辊气缸驱动;
曲柄式分段飞剪:
1台36.27t带有输入输出设备,飞剪带有双曲轴和飞轮;
飞剪后辊道:
1套42t72辊单独传动,辊道长74m可正反转。
3.7冷床区设备:
944.23t:
冷床输入辊道1套131t72辊单独传动,辊道长84m可正反转,带有升降拔爪;
矫直蓖:
1套72.3t靠冷床边的灰铸铁边导板;
固定挡板1台0.83t;
冷床床体:
1套450t17.6×
78m,齿间距250mm,
步进式液压驱动、水平和垂直行程由曲缸单独完成,
冷却水系统:
1套21.2t设有2排喷水环;
齐头辊道:
1套185t长78m;
冷床出口链式运输移钢机:
1台14t39根链条,2组待动链距2000mm,可正反转;
旋转臂:
39个20t4组活动可正反转;
输出辊道:
1套50t39个辊子单独传动,可正反转辊道长78m。
4.0设计生产工艺
4.1设计生产能力:
增建的近终型H钢铸轧机项目机组工程年生产能力为50万吨,其中H钢42万吨,槽钢、工字钢8万吨。
4.2产品规格:
H钢:
100*50——400*200mm
槽钢:
16#——40#
工字钢:
20#——40#
定尺长度:
6——18m
4.2.1原料:
连铸坯:
方坯:
150*150mm
异型坯:
BB1:
430*300*90mm
BB2:
320*220*85mm
4.2.2钢种:
碳素结构钢、桥梁用结构钢、船体用结构钢、低合金结构钢、低合金钢、耐侯钢等。
4.3生产工艺流程:
入库
4.4生产线主要工艺技术及设备特点:
4.4.1具有快速更换的三种高压水喷咀环自动喷水除鳞;
4.4.2机架粗轧机组及十机架中精轧机组均为微张力连续轧制;
4.4.3粗、精轧机组,机架均为无牌坊整体机架,均采取快速更换装置对机架进行整体更换,离线换辊;
4.4.4精轧机组的最终成型轧制过程为自动进行,是通过激光测量仪(或人工取样)获取后通知主操作台远程,对一个机架或几个机架的辊缝进行微调后,轧机的速度级补偿系统能自动调整轧机的速度,实现微张力连续轧制;
4.4.5粗、精轧机主传动全部采用变频调速交流电机传动;
4.4.5轧辊采用油雾润滑技术,减少轧辊磨损,提高轧件表面的质量;
4.4.6轧件采用在线激光测量外形尺寸技术;
4.4.7冷床为液压驱动步进式,水平和垂直行程由油缸单独完成,同步由液压系统完成;
4.4.8冷床采用强制水雾喷淋冷却系统,控制轧件出冷床温度低于80℃;
4.4.9采用计算机三级控制系统,一级为基础自动化级,二级为过程控制级,三级为生产管理级。
4.4.10工程特点:
(1)高空作业部位多。
上料台架、加热炉输出辊道、粗轧机组、精轧机机组设备安装作业部位在+5.1m钢平台上,第2、5架立轧机及冷床设备安装存在着高空作业。
(2)设备进场场地狭小。
设备在厂房内安装,厂房内无空余场地,设备进场只有南北两个通道口,设备卸货比较困难,又影响设备安装的工期。
(3)设备散件较多。
设备散件较多因而费工费时,另外设备供货不及时,影响施工工期,到施工后期可能会出现加班加点。
Ⅱ.施工进度及计划安排
开工时间为2004年10月至2005年1月
H型钢厂增建近终型H型钢轧机组工程安装总工期为120天,其中设备、机体管道安装为二班制。
1.0施工项目:
1.1粗轧机区设备(含上料台架);
1.2精轧区设备;
1.3冷床区设备。
1.4维修区设备安装
2.0施工部署及任务安排:
2.1加热炉出炉辊道、粗轧机组及输出辊道,安排一个班
2.2精轧夹送辊及精轧机,尺寸检测仪,安排一个班
2.3冷床及输入、输出辊道,安排一个班
2.4另外一个钳工班根据施工条件作临时增援。
计划安排钳工班3个50人,管道班2个18人,起重班2个22人,
电工3人,管理技术人员5人。
Ⅲ.施工方案
1.0施工准备:
1.0起重机械的选用:
轧线设备利用车间(A0-B0跨内)行车40/10t,25t,16t吊装。
1.2施工条件:
1.2.1车间行车已安装调试,轨道、滑触线具备行车运行条件;
1.2.2基础已施工完,已清扫,测量放线,已进行工序交接;
1.2.3厂房屋面已安装不漏水;
1.2.4设备图纸及有关安装技术资料已发到施工单位;
1.2.5设备按网络计划到货,并经开箱验收合格;
1.2.6进出厂道路畅通,厂房地坪平整;
1.2.7施工材料已批发;
1.2.8外方现场施工指导人员已到现场。
1.3.0施工前期条件:
1.3.1做好各种物质供应准备工作,按工期进度要求,按时组织送到施工现场;
1.3.2根据设计和厂方要求,做好永久性基准点,中心标板的加工制作;
1.3.3安排好各部位的施工力量,提前做好施工方案,技术安全交底工作,组织施工人员熟悉施工图,施工方案,掌握施工方法,了解施工要求;
1.3.4及时进行中心标板、标高基准点的埋设和测量放线工作;
1.3.5及时做好设备基础和地脚螺栓的复测验收工作;
1.3.6做好各种机具、仪表、器具等的准备工作;
1.3.7做好施工用电、用水等大临设施的布置工作;
1.3.8做好各种技术准备工作,满足工程进度的需要。
2.0通用施工方案:
2.1机械设备安装施工总则及其它施工方法:
2.2机械设备安装的通用程序:
设备单体调试及单体试车
2.3测量控制方案:
2.3.1 H型钢工程设备安装测量的技术要求,应严格执行《冶金建筑安装工程施工测量规范》-YBJ212-88的要求及设计图纸要求;
2.3.2 测量工作之前,应做好测量仪器及器具的检校工作,使所有投入H型钢工程的测量仪器必须选国家技术监督局认可的测量仪器检测部门校验,严禁未校验仪器进入施工现场;
2.3.3 H型钢工程的设备安装测量工作大体可分为控制测量和施工测量两部分,由于H型钢工程的轧制生产工艺线较长,纵向、横向、中心线数量较多,因此该工程的控制测量显得尤为重要;
2.3.4 设备安装的控制测量工作分为平面控制和标高控制两部分,为了能够尽快地使设备安装测量人员进入工作状态,从事设备安装测量人员应提前介入施工现场,熟悉工作环境和工艺平面布置情况,掌握H型钢工程外围方格图的布置情况,对整个工程应心中有数;
2.3.5 当接到土建工程的测量交接资料后,应根据设备安装的需要,立即布置设备安装的测量控制图,在平面控制中,设备主轧制中心线最长,是一条极为重要的设备控制线,生产线上另外几条中心线相对也较长,也是很重要的设备控制线,中心标板埋设见附图三。
中心线最好是一次布置完毕,如果受施工条件的限制,也可分几次布置,每条中心线的两头必须有至少两个埋设稳定的中心点控制,必要时中间位置还应适当加设一定的中心控制点,并保证通视条件良好,设备主控制中心线受H型钢施工方格图控制;
2.3.5 设备主轧制中心线及各纵向中心线确定后,应立即放样第一条横向中心线,应谨慎操作,严格检查纵、横向中心线的正交度,中心线两头应埋设中心样板,投设中心点,这条中心线,是其余设备横向中心线控制的基准,
2.3.6第一条横向设备中心线放样完毕后,依次放样各主要设备区域内的横向中心线,所有的中心线必须检查纵、横向正交度,所有中心线放样结果必须平差,尽可能消除测量误差带来的影响,所有中心线的两头必须埋设中心标板投放中心点;
2.3.7平面控制测量完毕后,整个H型钢工程的设备安装的骨架已形成,在基础上布置各设备施工区域内的施工测量网,施工测量网必须以各区域内的控制点为基准,分级布置设备中心线,关键部位必须检查设备纵、横向中心线的正交度,并及时进行平差,所有中心线两头必须埋设中心标板,投设中心点;
2.3.8 标高控制测量应以该区域内的施工方格网为基准,在设备基础上埋设标高控制点,控制点稳定后,采取二等水准测量的方法,将设备基础上的标高点同方格图进行联测,一次性标高点引测到安装区域,测量结果应平差;
2.3.9 设备安装测量控制网布置完毕后,应及时提交设备安装测量控制成果资料;
2.3.10 测量控制网和施工控制网布置完毕后,应根据图纸设计要求,对上道工序交接内容进行全面检查,其中包括设备基础顶面标高、中心线以及各设备区域内的预埋螺栓情况(包括预埋螺栓顶面标高,中心位置、垂直度等),检查完毕后,提交基础测量复测资料;
2.3.11 H型钢工程中重要设备中心线应埋设永久性中心标板和标高点,其布置位置和埋设数量应按设计所提供的永久性中心标板和标高点布置图,进行埋设、测量;
2.3.12 设备区域内的标高应经常检查是否有变化,所有的标高皆应同施工方格图上的标高点联测,标高测量采用二等水准测量,测量结果必须进行平差,如有异常情况出现应及时向有关人员汇报;
2.3.13 设备安装过程中,重要设备及关键部位的安装找平、找正,亦采用测量配合测量找平、找正,以提高安装精度和加快施工进度;
2.3.14 施工结束后,应及时提交相关测量资料,做好现场测量记录,绘制测量竣工成果图。
2.4.0机械设备安装的一般原则:
2.4.1 设备基础强度、坐标(标高、中心线)、地脚螺栓埋设的平面位置尺寸和螺栓顶标高、预留孔垂直度等应符合设计要求和施工规范中有关各项技术标准。
2.4.2 设备开箱检查应有出厂合格证等,应无损坏和缺损件。
2.4.3设备安装中采用的各种计量和检测器具、仪器、仪表和设备,应符合国家现行计量法的规定,必须经检验合格并在有效期内,其精度等级,应不低于被检测对象的精度等级。
2.4.4 设备安装工程应按设计要求施工,发现问题时,应及时提出,经设计、甲、乙三方研究,作出变更决定,书面通知,方可施工。
2.4.5 设备安装用垫板,应设置在尽量靠近地脚螺栓的位置,其长度应超过地脚螺栓的半径,设备底座外露尺寸15--30mm;
垫板应在设备受力筋板附近,相邻两地脚螺栓间距超过500-1000mm时,其间应加辅助垫板;
重要大型较重设备或底座(底板)刚度较小的设备,应适当加辅垫板,以提高垫板的承压能力或减小设备底座(底板)的变形;
垫板设置应平稳,接触紧密,每堆垫板数不应超过5块,顶面一块不能放置薄垫,二次灌浆前,应三方点焊牢,并去除焊渣。
2.4.6 设备安装过程中的隐蔽工程,应先经检查,甲方认可后,方可进行隐蔽,并应作好隐蔽记录和甲方签证认可。
2.4.7设备安装中,应严格执行自检、互检和专业验收检查,并对每道工序进行检验和记录,方可进行下道工序,工程验收时,各项记录应齐全。
2.4.8设备安装的坐标,根据设备布置要求和依据施工测量放线的标高、中心线进行找正,其偏差极限和水平度、平行度、铅垂度公差,应根据图纸要求或设备技术文件要求,或外方标准、外方现场安装人员要求执行,均无要求时,可按国内《冶金机械设备安装工程施工及验收规范》及《机械设备安装工程施工及验收规范法》等规范中相关设备的标准进行。
2.5.0设备安装找平、找正和标高测量点,一般可选择在设备的下列部位为测量依据:
2.5.1设计或设备技术文件指定的部位;
2.5.2施工及验收规范中的各专用设备所明确的以何部位为依据找正;
2.5.3设备的主要工作面;
2.5.4部件上加工精度高的表面;
2.5.5零、部件间的主要结合面;
2.5.6支承滑动部件的导向面;
2.5.7轴承剖分面,轴颈表面、滚动轴承外圈;
2.5.8设备上应为水平或铅垂的主要轮廓面。
2.6.0 设备安装找平、找正、水平、平行度、铅垂度偏差或误(公)差的方向,一般可按下列因素确定:
2.6.1能补偿受力或温度变化后所引起的偏差或误差;
2.6.2能补偿使用过程中磨损所引起的偏差或误差;
2.6.3使有关的零、部件更好地联接配合;
2.6.4使运转平稳;
2.6.5使零、部件在负荷作用下受力较小;
2.6.6使物件在运行中走行平稳,不跑偏。
2.7.0 垫板的设置:
2.7.1 垫板设置可采用在基础上经研平基础直接设平垫板,每堆块数不超过5块,也可采用在上述方法中上部两块为成对斜垫板,便于标高调整;
2.7.2 为加快施工进度和减少钢垫板块数和调整方便,采用座浆平垫板,加上一队成组斜垫板,可满足二次灌浆层厚度要求,保证垫板的承压面积达到全部紧密接触;
2.7.3 垫板承压面积A的计算:
Q1+Q2
R
A≥C×
104(mm2)
A--垫板总的承重面积mm2
Q1—设备总重量及负荷重的总重量(t)
Q2—地脚螺栓拧紧后的压力(t),可取螺栓的许用拉力
R—设备基础的混凝土抗压强度(MPa)一般取R=20MPa
C—安全系数,宜取1.5—3.
根据设备的地脚螺栓数量和选择的垫板堆数n进行计算每块垫板的面积:
Ai=A/n(mm2)
根据地脚螺栓的直径和设备底座边缘至螺栓孔间尺寸确定垫板的长×
宽的尺寸,其面积应≥Ai
2.7.4地脚螺栓的紧固及紧固力的计算:
2.7.4.1设备技术文件有明确要求紧固力时,按其要求达到紧固。
2.7.4.2无要求时,可按下式计算紧固力:
Q2=「δ」A
Q2—地脚螺栓的紧固力,Kgf;
「δ」--地脚螺栓所用材质的许用拉应力,Kgfmm2
A--地脚螺栓螺纹根部的面积,mm2
2.8.0垫板的座浆法:
2.8.1座浆材料:
600#以上早强无收缩硅酸盐水泥、中砂、石子粒度为5--15mm
2.8.2座浆砼配合比例:
水泥:
石子:
砂子:
水=1:
1:
0.37
砼的塌落度应为0—1cm。
水泥浆:
水泥0.5kg水1—1.2kg
2.8.3座浆的施工程序:
打坑
2.8.4座浆要求:
2.8.4.1座浆坑的长度和宽度应比垫板的长度和宽度大60--80mm
2.8.4.2座浆坑的凿入深度应不小于30mm
2.8.4.3座浆层混凝土的厚度应不小于50mm
2.8.4.4水润应使基础坑的原混凝土充分湿润,净坑后应无积水和油污
2.8.4.5坑内刷水泥浆应满刷,但不宜厚。
2.8.4.6厚度宜为40mm左右,连续捣至浆浮表层以利拍浆。
混凝土顶表面呈中间高四周低的弧形顶面,以便放置垫板时,易排出空气。
2.8.4.7当混凝土表面水迹消失后,即可放置垫板,混凝土表面应低于垫板2--5mm,拍实垫板四周混凝土,检测垫板标高,极限偏差为±
0.3mm。
水平度公差为≤0.1/1000(用方水平仪200×
200/0.02/1000检查),应防止碰撞和振动。
2.8.4.8当混凝土初凝前,应再次复查垫板标高水平,当无误后,盖上草袋或纸袋并浇水湿润养护,养护期间不得碰撞和振动,经养护48小时,强度达到,可进行下道工序的安装工作。
2.8.4.9垫板的接触面:
垫板间的接触应紧密,用0.05mm塞尺检查,塞入面积不得超过垫板接触面积的1/3。
对于大型、较重设备、负荷大的设备、高速运转设备、精度高的精密设备等重要设备的垫板间的接触面,应将垫板成对进行研磨处理,接触点面积应大于垫板面积的70%,用0.05mm塞尺检查时,接触周长应不小于70%。
2.8.4.10大型重要设备机架与底座的接触面:
用0.05mm塞尺检查时,接触面应大于75%。
2.9.0设备找正、找平:
2.9.1中心线找正:
一般用线架挂线、吊线锤进行找正,重要中心线可用经纬仪配合找正;
2.9.2标高找正:
一般用平尺、方水平仪、钢尺、外径千分尺找正标高,也可用水准仪测量;
2.9.3水平度找正:
一般用平尺、方水平仪:
0.02/1000找平,也可用水准仪测量找平;
2.9.4平行度:
用外径千分尺检测;
2.9.5垂直度:
挂线锤用钢尺、游标卡尺、外径千分尺测量;
2.9.6同心度:
用挂钢丝、线锤、外径千分尺测量,也可用激光对中仪测量。
2.9.7联轴器同轴度找正:
一般同轴度要求不高的联轴器:
可用直尺、塞尺进行找正即可。
同轴度要求高的设备的联轴器:
用磁力座、千分尺、四点旋转找正法,分别测出联轴的径向偏移偏差和轴向偏斜度值,经反复调整与检测,直至达到所规定的要求值。
2.10.0 设备的清洗、修理:
对于设备装配接触面、外裸的光滑加工面的锈蚀、脏污和防锈油(剂),在设备装配、安装前,均应进行清除和清洗、修理。
2.10.1设备清洗:
可用蒸汽、热空气吹洗(但水份必须及时除尽)、热油(100℃ 以下)清洗、碱性清洗液应清洗(60--90℃以下)并用清水冲洗洁净并干燥,煤油、柴油、汽油等清洗剂清洗,设备零、部件经清洗后,必须放置于洁净地方干燥。
2.10.2设备的锈蚀、伤痕迹的修理:
锈蚀痕迹应用最小金刚砂子打磨,圆柱体件沿圆周方向打磨,伤痕迹用细料油石,打磨掉凸起部位,圆柱体应沿圆周方向打磨。
2.11.0设备的拆卸、装配:
2.11.1 设备拆卸、装配前,应了解设备的构造和技术要求,确定其拆装顺序和方法,拆卸时对所拆的零、部件应作出相应位置的标记;
2.11.2 设备装配时,应先检查零、部件与装配有关的尺寸偏差、形状和位置误差,符合设备技术文件的要求后,按照装配顺序和标记、装配方法进行装配;
2.11.3螺纹连接件装配:
螺纹连接件装配时,应在光杆及螺纹处涂油(对于含Ni、Gr的材质的连接件,应涂含二硫化钼的润滑剂,特别是细牙的锁紧丝扣,容易相互咬合,造成零件报废),螺纹连接件接触应紧密、紧固、无松动现象,有预紧力要求的,必须达到设备技术文件的要求。
2.11.4键的装配:
2.11.4.1各种不同形式的键装配前,应检查各种不同键,相应的键和键槽的剖面尺寸应符合相应规范的规定。
2.11.4.2楔键的斜面与轮毂键槽的斜面应接触紧密,切向键的每对键的斜面、键与轴槽和键与轮