材料成型与控制工程开题报告T10钢落料凹模的热处理工艺及变形控制Word格式文档下载.docx
《材料成型与控制工程开题报告T10钢落料凹模的热处理工艺及变形控制Word格式文档下载.docx》由会员分享,可在线阅读,更多相关《材料成型与控制工程开题报告T10钢落料凹模的热处理工艺及变形控制Word格式文档下载.docx(15页珍藏版)》请在冰豆网上搜索。
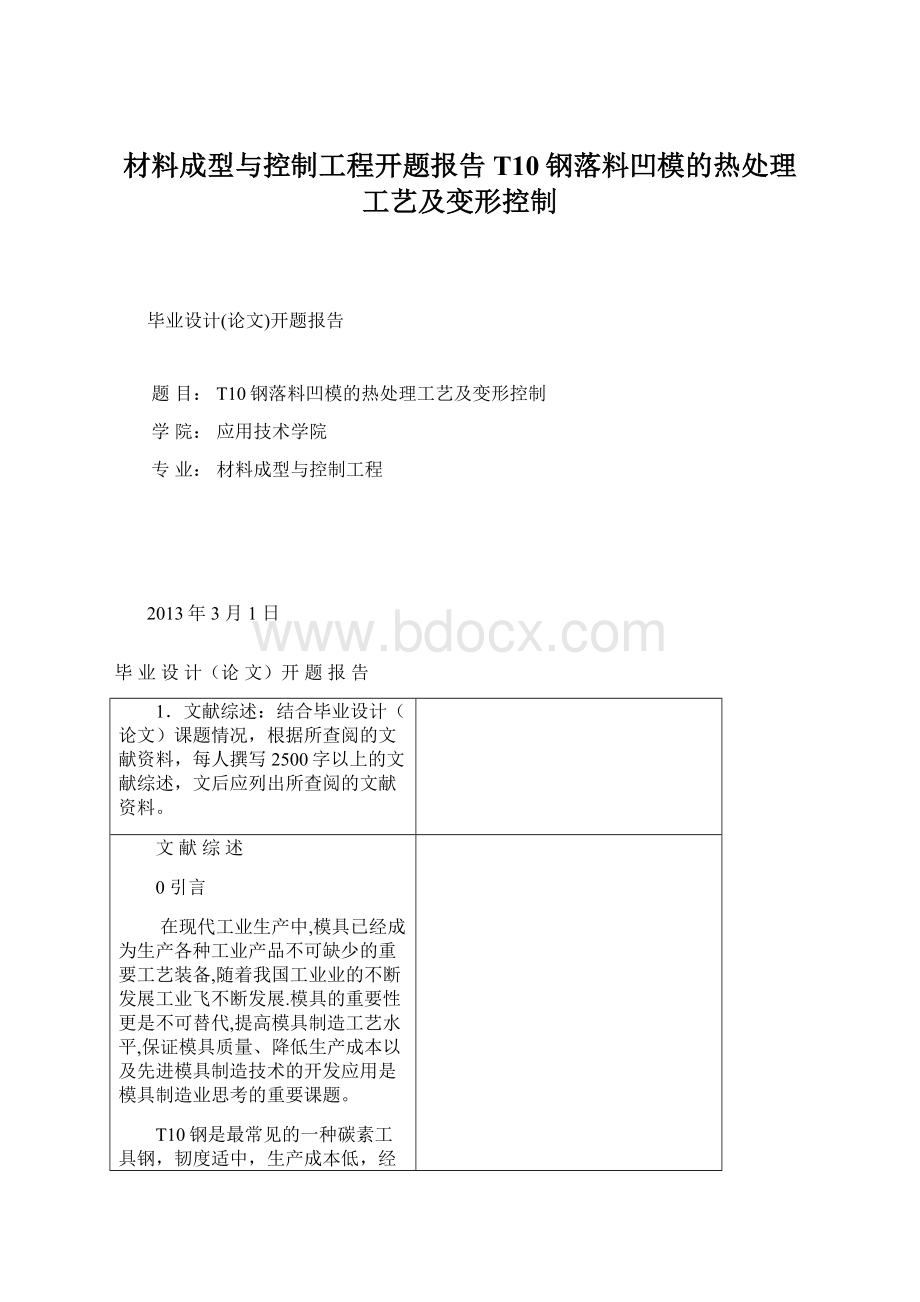
1.2主要失效形式
产生裂纹,变形大,疲劳失效
1.3性能要求
使模具工作部分的内表面为马氏体组织,心部是索氏体、屈氏体组织,外表面为正火珠光体加渗碳组织,从而使模具工作部分有较高的硬度、强度及耐磨性,其它部位又有一定韧性,淬火变形小,又避免开裂。
足够的强度和韧性;
较高的耐磨性和抗蚀性;
热处理后的工作硬度一般为54~58HRC。
1.4T10钢的组织特点
T10A钢锻造后的冷却速度不同,所获得的金相显微组织也不相同。
经砂冷、空冷、喷水冷却和水冷后所获得的显微组织分别为粗片状的珠光体加少量断续网状的二次渗碳体、索氏体、托氏体和托氏体加马氏体。
T10A钢中碳的质量分数较高,脆性较大,为避免开裂,冷却时不宜有马氏体组织存在,因而冷却速度不宜过大,一般情况下喷水冷却时的冷却速度已经足够。
由所获得的金相显微组织可知,在冷却速度允许的情况下,T10A钢锻造后的冷却速度越快,则所获得的珠光体晶粒和渗碳体颗粒越细小。
2分析T10钢落料凹模的失效原因
为减少热处理畸变,需要我们根据具体问题采取有效的措施。
主要问题是T10钢落料凹模热处理后中筋变形大;
初步分析金属热胀冷缩的物理本性及相变时的比容变化引起体积变化,引起形状变化的情况有四种(加热、冷却不均,内外应力);
工艺措施:
去应力,包扎窄筋塞孔,淬火,回火;
.工艺效果:
满足要求;
总结:
防止或减少畸变的有效措施,淬火前的保护、正确的加热、正确选定冷却和运动方向。
2.1提出问题
通常高碳钢模具大都在低温回火条件下工作,它虽有很高的硬度及耐磨性,但因塑性及韧性很低,静载及动载下的缺口敏感性很差,尤其是抗冲击过载能力不足,使用中并非因磨损而失效,常因裂断而报废,这种情况目前较普遍.因此,为使模具在具有高的硬度和耐磨性的同时具有足够的韧性,
T10钢制造的落料凹模(如下所示),技术要求为硬度HRC58-62,落料孔中筋变形不大于0.06mm
2.2分析问题
我们知道,模具畸变有形状变化和体积变化。
体积的变化是金属热胀冷缩的物理本性及相变时的比容变化而引起的。
钢的组织不同其比容不同,其顺序如下:
马氏体>
贝氏体>
珠光体>
奥氏体
其中奥氏体比容最小,马氏体比容最大,因此热处理时钢由其他组织转变为奥氏体时必然引起比容减小,而其他组织转变为马氏体时必然引起体积增加。
形状变化是由于内应力或外应力的作用超过了材料的弹性极限,就产生塑性变形,引起了形状变化。
引起形状变化的情况有四种:
1)在加热过程中,由于工件各部位的温度有差异,造成相变的不同时性,致使冷却过程组织转变的不一致性,而在工件内部产生瞬时内应力。
2)加热过程工件各部位的温度均匀,但由于本身各部位冷却条件
不一样,造成相变的不同时性,而致使组织转变的不一致性,而产生瞬时内应力。
3)工件内部的冷加工或残余应力,在加工过程中的松弛。
4)加热时受到过度的外加应力(如支持不良时自重的影响,工件之间外加重量的影响等)。
落料凹模的形状不太复杂,结构也很对称,但是中间的带状筋很薄,属截面尺寸相差悬殊的模具,显然解决中筋变形是热处理的关键。
如果不采取任何措施进行普通加热时,这条窄筋较快地被加热,首先发生膨胀,但受其他部位的抵制而造成弯曲。
在随后冷却过程中又先较快地冷至低温,先发生马氏体转变,再发生膨胀,弯曲变形被保留下来。
因此,解决中筋变形的措施应使其加热和冷却均应较慢地进行,最好能与其他部位的加热冷却条件相当。
3确定热处理工艺
3.1工艺措施
为减少这种模具的淬火变形,采用图示包扎铁皮的方法,为防止螺纹孔和工艺孔淬火开裂,淬火前所有孔应用石棉绳塞住。
工艺过程如下:
1)去应力处理———640—650℃保温1.5h出炉空冷。
目的是消机械加工应力,减少因加工应力造成的淬火变形。
2)中间窄筋包扎铁皮、塞孔。
3)淬火———450—500℃箱式炉中预热20min,780℃浴炉保温
12—15min后,出炉预冷到750—760℃入水冷却,上下移动7—8s后
转入油中冷却,冷至150—170℃出油冷却。
4)回火———180—200℃保温1h,出炉空冷。
3.2工艺效果
这样热处理后,硬度约为HRC60,变形量在0.06mm以下。
上例模具模具热处理的操作中,注意采取了一些防止或减少畸变的有效措施。
淬火前的保护工件几何形状和截面大小相差悬殊时,因加热和冷却不均匀容易造成变形开裂,用石棉、火泥等把一些非工作孔或型孔堵塞,使其冷却减慢或均匀。
2.正确的加热先在箱式炉中预热,使模具各部分温度均匀后,再移至盐浴炉中。
在盐浴炉中加热时应注意:
合理的吊扎:
使模具重量不集中在某几个孔眼上,而均匀地分布在两边吊扎的铁丝上,这样可以避免因热处理时自身重量而变形。
正确的加热位置:
对薄而长的零件在盐浴中加热,应使其宽的一面垂直于电极平面,避免盐浴通电时熔盐翻滚剧烈冲击工件而额外变形。
4实验并分析热处理后的金相显微组织
表1T10钢淬、回火后的硬度、晶粒度及显微组织
序号
原始组织
热处理
HRC
级别
金相组织
1
P片
780°
碱浴淬火+200°
回火
61.2
9
隐针状M+细针状M+K十丫
2
P粒
780℃碱浴悴火+200℃回火
61.0
细针状M+细小板M+K十YR
3
840℃碱浴悴火+200℃回火
63.3
8
筐篮编结状M+丫,
4
940℃碱浴悴火+200℃回火
63.0
7
板条状M+针状M+丫,
5
1050℃碱浴悴火+200℃回火
62.7
6
1150℃碱浴悴火+200℃回火
62.9
注:
P粒一粒状珠光体,P片一片状珠光体,M一马氏体,K一碳化物,丫:
一残留奥氏体。
表2T10钢主要机械性能
抗压强度δkgf/mm2
抗压屈服强度kgf/mm2
扭转强度τkgf/mm2
扭转屈服强度kgf/mm2
抗弯强度kgf/mm2
冲击韧度α
kgf/mm2
多次冲击破断用次N
断裂韧性K
kgf/mm3/2
246.5
134
172.7
113.5
311
4.6
15349
52
2
246.7
159
179
131
211.5
5.2
18977
601
408
175.2
131.3
176
1.8
67030
64
612
327
86.9
74
128
0.9
69
76.1
565
319
91
66
90
0.4
83
66.1
399
256
50.3
44.2
71.9
0.3
高老师这里缺金相组织图以后补上
5综合分析确定最后的热处理工艺及主要参数
(1)原始组织为片状珠光体的T10钢试样,采用84O°
C淬火、200°
C回火处理,机性能优良。
这是由于组织中形成了亚结构为高密度缠结位错的筐篮编结状马氏体造成。
原始组织为粒状珠光体的T10钢试样,经传统工艺处理,在组织中的亚结构孪晶针状马氏体片内,及针前端部分出现高密度微裂纹,综合机械性能差。
(2)淬火温度和晶粒度相同时,T10钢原始组织为片状珠光体的淬透性比粒状珠光体的好、采用840°
c加热淬火,其淬透性比传统工艺的高30%。
(3)原始组织为片状珠光体的T10钢,采用新工艺840°
C淬火,200℃回火处理,对于主要承受小能量多次冲击压缩载荷的冷锻模具,及承受扭转载荷的工具,效果良好,特别适用于某些要求淬透层较深的模具。
参考文献
[1]高为国,胡凤兰,董丽君等.T10A钢成型模具的失效分析及热处理工艺的改进[J].湖南:
湖南工程学院机械工程系,2006.
[2]高为国,楼易,郭明康.模具材料.北京:
机械工业出版社,2004.2.
[3]徐桃.多次冲击碰撞载荷下T10钢的累积宏观塑性变形及其机理分析[D]苏州大学2011.4
[4]彭其风,丁洪太.热处理工艺及设计[M].上海:
上海交通大学出版社,1994.
[5]谭家骏.金属材料及热处理专业知识解答[M].北京:
国防工业出版社,1997.
[6]俞德刚.钢的组织强度学[M].上海:
上海科技出版社,1980.
[7]高玉芳,张文忠.Crl2MoV钢的强韧化热处理工艺研究[J].理化检验-物理分册,2001(4):
43-52.
[8]丁厚福,邓志煜.显微组织对高碳钢韧性的影响[J].热加工工艺,1994(5):
26.
[9]牛学超,程锋,王克伍.冲模失效原因及改进措施探讨.中国资源综合利用,2011,29(6).
[10]刘胜国.我国冲压模具技术的现状与发展.黄石理工学院机电工程学院,2007
[11]王宏伟.碳素工具钢的热处理及其应用[J]煤炭技术.200608
[12]邹敢锋,黄元盛,袁叔贵.T10钢低温盐浴渗铬工艺的研究[J]金属热处理2000
[13]张宇巍.T10钢冲模开裂原因分析.[J]热处理技术与装备2011(4)
2.开题报告:
一、课题的目的与意义;
二、课题发展现状和前景展望;
三、课题主要内容和要求;
四、研究方法、步骤和措施
开题报告
一、课题的目的与意义
本课题主要是研究T10钢落料凹模的热处理工艺及变形控制。
是生产企业提高产品质量,降低成本的重要改良工艺之一。
是模具行业和产业急需解决的技术难题,是模具产业存在的主要问题之一。
本课题研究能够为解决模具失效过早、开裂、磨损等问题。
提供有效工艺路线及技术支持。
可使企业模具生产成本降低,产品质量和性能大幅提高。
大大提高企业生产效益,有利于模具产业的发展。
2、课题发展现状和前景展望
冲模模具是机械制造业中技术先进、影响深远的重要工艺装备,具有生产效率高、材料利用率高、制件质量优良、工艺适应性好等特点,被广泛应用于汽车、机械、航天、航空、轻工、电子、电器、仪表等行业。
然而,与国际先进水平相比,我国冲压模具产品的质量和生产工艺水平,总体上比国际先进水平低许多,而模具生产周期却要比国际先进水平长许多。
产品质量水平低主要表现在精度、表面粗糙度、寿命及模具的复杂程度上;
生产工艺水平低则主要表现在加工工艺、加工装备等方面。
模具寿命也只有国际先进水平的50%左右,大型、精密、技术含量高的轿车覆盖件冲压模具和精密冲裁模具,每年都需要花费大量资金进口。
三、课题主要内容和要求
1、课题主要内容
(1)分析T10钢落料凹模的工作条件、主要失效形式及性能要求;
(2)根据给定T10钢落料凹模的结构特点,分析给定T10钢落料凹模变形的主要原因,特别是热处理方面的原因;
(3)根据分析结果,确定出T10钢落料凹模的热处理工艺方案及其主要的热处理工艺参数,并说明理由;
(4)针对所确定的热处理工艺方案进行热处理操作,测定热处理后的硬度,分析其
热处理后的金相显微组织;
(5)根据测定的硬度数据和热处理后的显微组织状态,进行综合分析、比较,确定出最终的热处理工艺及其主要参数;
2、课题主要要求
(1)查阅与本课题相关的中外文献资料,了解T10钢落料凹模的应用发展状况以
及国内外T10钢热处理工艺的研究进展;
(2)围绕本课题的研究内容确定实验研究的技术路线;
(3)分析T10钢落料凹模的工作条件、主要失效及性能要求;
(4)根据T10钢的特点,设计合适的热处理工艺方案;
(5)对热处理后的T10钢进行性能测试及显微组织分析,研究不同的热处理对T1钢的影响。
探寻最佳的热处理工艺。
(6)分析T10钢热处理后的各项性能,得出结论。
(7)撰写毕业设计说明书,完成全部研究工作和毕业论文。
1、查阅资料,翻译英文资料
查找设计所需的资料,资料的内容要有深度,要具有参考意义。
2、熟练掌握设计所需的内容
复习以前所学设计有关的专业知识,并熟练的运用到设计中去。
还要学习一些设计
中所用到的其它方面的知识。
3、合理安排实验设计内容
(1)围绕本课题的研究内容确定实验研究的技术路线;
(2)分析T10钢的落料凹模工作条件、主要失效形式及性能要求;
(3)根据T10钢落料凹模的特点,设计合适的热处理工艺;
(4)确定热处理工艺,;
(5)对热处理后的试件进行性能测试及显微组织分析,研究不同的热处理工艺对试件组织和性能的影响,分析实验结果,探寻最佳的热处理工艺。
(6)分析数据,确定最终的热处理工艺及其主要参数。
4、具体设计步骤
(1)
(2)
(3)
(4)
(5)
(6)
(7)
(8)
毕业设计(论文)开题报告
指导教师意见:
1.对“文献综述”的评语:
2.对本课题的深度、广度及工作量的意见和对设计(论文)结果的预测:
指导老师:
年月日
所在专业审查意见:
负责人:
年月日