单晶硅生产工艺Word文档下载推荐.docx
《单晶硅生产工艺Word文档下载推荐.docx》由会员分享,可在线阅读,更多相关《单晶硅生产工艺Word文档下载推荐.docx(7页珍藏版)》请在冰豆网上搜索。
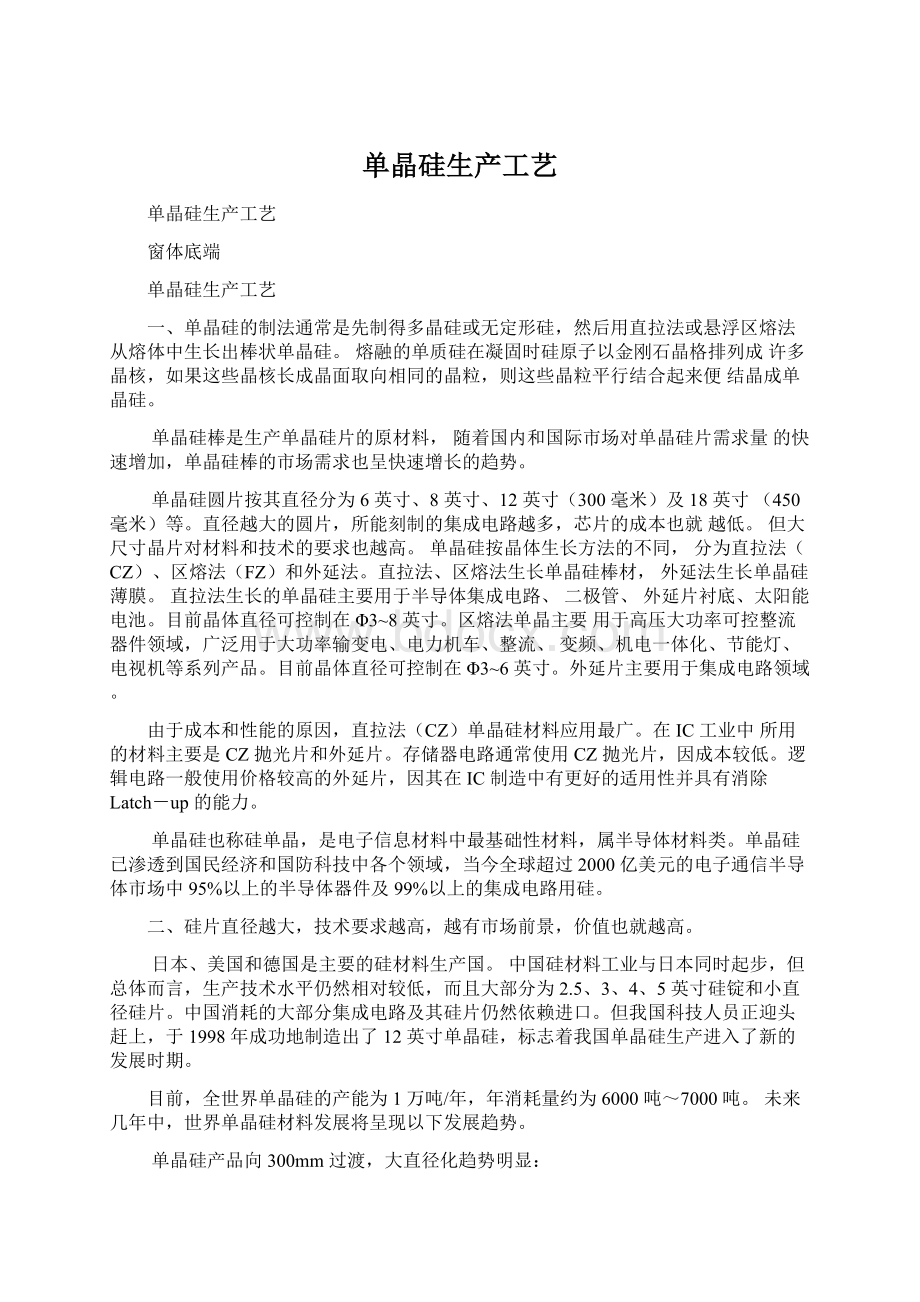
单晶硅也称硅单晶,是电子信息材料中最基础性材料,属半导体材料类。
单晶硅已渗透到国民经济和国防科技中各个领域,当今全球超过2000亿美元的电子通信半导体市场中95%以上的半导体器件及99%以上的集成电路用硅。
二、硅片直径越大,技术要求越高,越有市场前景,价值也就越高。
日本、美国和德国是主要的硅材料生产国。
中国硅材料工业与日本同时起步,但总体而言,生产技术水平仍然相对较低,而且大部分为2.5、3、4、5英寸硅锭和小直径硅片。
中国消耗的大部分集成电路及其硅片仍然依赖进口。
但我国科技人员正迎头赶上,于1998年成功地制造出了12英寸单晶硅,标志着我国单晶硅生产进入了新的发展时期。
目前,全世界单晶硅的产能为1万吨/年,年消耗量约为6000吨~7000吨。
未来几年中,世界单晶硅材料发展将呈现以下发展趋势。
单晶硅产品向300mm过渡,大直径化趋势明显:
随着半导体材料技术的发展,对硅片的规格和质量也提出更高的要求,适合微细加工的大直径硅片在市场中的需求比例将日益加大。
目前,硅片主流产品是200mm,逐渐向300mm过渡,研制水平达到400mm~450mm。
据统计,200mm硅片的全球用量占60%左右,150mm占20%左右,其余占20%左右。
根据最新的《国际半导体技术指南(ITRS)》,300mm硅片之后下一代产品的直径为450mm;
450mm硅片是未来22纳米线宽64G集成电路的衬底材料,将直接影响计算机的速度、成本,并决定计算机中央处理单元的集成度。
Gartner发布的对硅片需求的5年预测表明,全球300mm硅片将从2000年的1.3%增加到2006年的21.1%。
日、美、韩等国家都已经在1999年开始逐步扩大300mm硅片产量。
据不完全统计,全球目前已建、在建和计划建的300mm硅器件生产线约有40余条,主要分布在美国和我国台湾等,仅我国台湾就有20多条生产线,其次是日、韩、新及欧洲。
世界半导体设备及材料协会(SEMI)的调查显示,2004年和2005年,在所有的硅片生产设备中,投资在300mm生产线上的比例将分别为55%和62%,投资额也分别达到130.3亿美元和184.1亿美元,发展十分迅猛。
而在1996年时,这一比重还仅仅是零
2、硅材料工业发展日趋国际化,集团化,生产高度集中:
研发及建厂成本的日渐增高,加上现有行销与品牌的优势,使得硅材料产业形成“大者恒大”的局面,少数集约化的大型集团公司垄断材料市场。
上世纪90年代末,日本、德国和韩国(主要是日、德两国)资本控制的8大硅片公司的销量占世界硅片销量的90%以上。
根据SEMI提供的2002年世界硅材料生产商的市场份额显示,Shinetsu、SUMCO、Wacker、MEMC、Komatsu等5家公司占市场总额的比重达到89%,垄断地位已经形成。
3、硅基材料成为硅材料工业发展的重要方向:
随着光电子和通信产业的发展,硅基材料成为硅材料工业发展的重要方向。
硅基材料是在常规硅材料上制作的,是常规硅材料的发展和延续,其器件工艺与硅工艺相容。
主要的硅基材料包括SOI(绝缘体上硅)、GeSi和应力硅。
目前SOI技术已开始在世界上被广泛使用,SOI材料约占整个半导体材料市场的30%左右,预计到2010年将占到50%左右的市场。
Soitec公司(世界最大的SOI生产商)的2000年~2010年SOI市场预测以及2005年各尺寸SOI硅片比重预测了产业的发展前景。
4、硅片制造技术进一步升级:
目前世界普遍采用先进的切、磨、抛和洁净封装工艺,使制片技术取得明显进展。
在日本,Φ200mm硅片已有50%采用线切割机进行切片,不但能提高硅片质量,而且可使切割损失减少10%。
日本大型半导体厂家已经向300mm硅片转型,并向0.13μm以下的微细化发展。
另外,最新尖端技术的导入,SOI等高功能晶片的试制开发也进入批量生产阶段。
对此,硅片生产厂家也增加了对300mm硅片的设备投资,针对设计规则的进一步微细化,还开发了高平坦度硅片和无缺陷硅片等,并对设备进行了改进。
三、硅是地壳中赋存最高的固态元素,其含量为地壳的四分之一,但在自然界不存在单体硅,多呈氧化物或硅酸盐状态。
硅的原子价主要为4价,其次为2价;
在常温下它的化学性质稳定,不溶于单一的强酸,易溶于碱;
在高温下化学性质活泼,能与许多元素化合。
由于硅的禁带宽度和电子迁移率适中,硅器件的最高工作温度能达250℃,其制作的微波功率器件的工作频率可以达到C波段(5GHZ)。
在硅的表面能形成牢固致密的SiO2膜,此膜能充当电容的电介质、扩散的隔离层、器件表面的保护层,随着平面工艺与光刻技术的问世而促进了硅的超大规模集成电路的发展。
硅材料资源丰富,又是无毒的单质半导体材料,较易制作大直径无位错低微缺陷单晶。
晶体力学性能优越,易于实现产业化,从而导致半导体硅材料成为电子材料中的第一大主体功能材料,并在今后较长时间内仍将成为半导体的主体材料。
多晶硅材料是以工业硅为原料经一系列的物理化学反应提纯后达到一定纯度的电子材料,是硅产品产业链中的一个极为重要的中间产品,是制造硅抛光片、太阳能电池及高纯硅制品的主要原料,是信息产业和新能源产业最基础的原材料。
多晶硅产品分类:
多晶硅按纯度分类可以分为冶金级(工业硅)、太阳能级、电子级。
1、冶金级硅(MG):
是硅的氧化物在电弧炉中被碳还原而成。
一般含Si为90-95%以上,高达99.8%以上。
2、太阳级硅(SG):
纯度介于冶金级硅与电子级硅之间,至今未有明确界定。
一般认为含Si在99.99%–99.9999%(4~6个9)。
3、电子级硅(EG)一般要求含Si>
99.9999%以上,:
超高纯达到99.%~99.%(9~11个9)。
其导电性介于10-4–1010欧厘米。
多晶硅应用领域:
多晶硅是半导体工业、电子信息产业、太阳能光伏电池产业的最主要、最基础的功能性材料。
主要用做半导体的原料,是制做单晶硅的主要原料,可作各种晶体管、整流二极管、可控硅、太阳能电池、集成电路、电子计算机芯片以及红外探测器等。
多晶硅是制备单晶硅的唯一原料和生产太阳能电池的原料。
随着近几年我国单晶硅产量以年均26%的速度增长,多晶硅的需求量与日俱增,目前供应日趋紧张。
我国2000年产单晶硅459吨,2003年增加到1191吨,预计2005年产量将达1700吨,消耗多晶硅2720吨。
从单晶硅产品结构看,太阳电池用单晶硅产量增长最快,2000年产量207吨,2003年为696吨。
预计2005年将达到1000吨,约需多晶硅1590吨,而国内2004年仅生产多晶硅57.7吨,绝大部分需要进口。
我国主要的太阳能电池厂有5~6家,最大的无锡尚德太阳能电力有限公司2004年产量约为50MW,2005年计划生产100MW,如果完成计划,则约需多晶硅1300吨以上。
仅此一家企业,就要2家千吨级多晶硅厂为其供货,才能满足生产需要。
从国际市场看,国际市场多晶硅需求量在以每年10-12%的速度增长,按此增长速度预测,2005年全球多晶硅需求量将达27000吨,2010年将达60000吨,缺口很大。
亚太地区特别是日本、台湾、新加坡、韩国等地,都是多晶硅的主要需求地。
多晶硅生产技术:
多晶硅生产技术主要有:
改良西门子法、硅烷法和流化床法。
正在研发的还有冶金法、气液沉积法、重掺硅废料法等制造低成本多晶硅的新工艺。
世界上85%的多晶硅是采用改良西门子法生产的,其余方法生产的多晶硅仅占15%。
以下仅介绍改良西门子法生产工艺。
西门子法(三氯氢硅还原法)是以HCl(或Cl2、H2)和冶金级工业硅为原料,将粗硅(工业硅)粉与HCl在高温下合成为SiHCl3,然后对SiHCl3进行化学精制提纯,接着对SiHCL3进行多级精馏,使其纯度达到9个9以上,其中金属杂质总含量应降到0.1ppba以下,最后在还原炉中在1050℃的硅芯上用超高纯的氢气对SiHCL3进行还原而长成高纯多晶硅棒。
多晶硅副产品:
多晶硅生产过程中将有大量的废水、废液排出,如:
生产1000吨多晶硅将有三氯氢硅3500吨、四氯化硅4500吨废液产生,未经处理回收的三氯氢硅和四氯化硅是一种有毒有害液体。
对多晶硅副产物三氯氢硅、四氯化硅经过多级精馏提纯等化学处理,可生成白炭黑、氯化钙以及用于光纤预制棒的高纯(6N)四氯化硅。
四、硅锭的拉制,目前主要有以下几种方法:
*直拉法
即切克老斯基法(Czochralski:
Cz),直拉法是用的最多的一种晶体生长技术。
直拉法基本原理和基本过程如下:
1.引晶:
通过电阻加热,将装在石英坩埚中的多晶硅熔化,并保持略高于硅熔点的温度,将籽晶浸入熔体,然后以一定速度向上提拉籽晶并同时旋转引出晶体;
2.缩颈:
生长一定长度的缩小的细长颈的晶体,以防止籽晶中的位错延伸到晶体中;
放肩:
将晶体控制到所需直径;
3.等径生长:
根据熔体和单晶炉情况,控制晶体等径生长到所需长度;
4.收尾:
直径逐渐缩小,离开熔体;
5.降温:
降级温度,取出晶体,待后续加工
6.最大生长速度:
晶体生长最大速度与晶体中的纵向温度梯度、晶体的热导率、晶体密度等有关。
提高晶体中的温度梯度,可以提高晶体生长速度;
但温度梯度太大,将在晶体中产生较大的热应力,会导致位错等晶体缺陷的形成,甚至会使晶体产生裂纹。
为了降低位错密度,晶体实际生长速度往往低于最大生长速度。
7.熔体中的对流:
相互相反旋转的晶体(顺时针)和坩埚所产生的强制对流是由离心力和向心力、最终由熔体表面张力梯度所驱动的。
所生长的晶体的直径越大(坩锅越大),对流就越强烈,会造成熔体中温度波动和晶体局部回熔,从而导致晶体中的杂质分布不均匀等。
实际生产中,晶体的转动速度一般比坩锅快1-3倍,晶体和坩锅彼此的相互反向运动导致熔体中心区与外围区发生相对运动,有利于在固液界面下方形成一个相对稳定的区域,有利于晶体稳定生长。
8.生长界面形状(固液界面):
固液界面形状对单晶均匀性、完整性有重要影响,正常情况下,固液界面的宏观形状应该与热场所确定的熔体等温面相吻合。
在引晶、放肩阶段,固液界面凸向熔体,单晶等径生长后,界面先变平后再凹向熔体。
通过调整拉晶速度,晶体转动和坩埚转动速度就可以调整固液界面形状。
9.连续生长技术:
为了提高生产率,节约石英坩埚(在晶体生产成本中占相当比例),发展了连续直拉生长技术,主要是重新装料和连续加料两中技术:
-重新加料直拉生长技术:
可节约大量时间(生长完毕后的降温、开炉、装炉等),一个坩埚可用多次。
-连续加料直拉生长技术:
除了具有重新装料的优点外,还可保持整个生长过程中熔体的体积恒定,提高基本稳定的生长条件,因而可得到电阻率纵向分布均匀的单晶。
连续加料直拉生长技术有两种加料法:
连续固体送料和连续液体送料法。
10.液体覆盖直拉技术:
是对直拉法的一个重大改进,用此法可以制备多种含有挥发性组元的化合物半导体单晶。
主要原理:
用一种惰性液体(覆盖剂)覆盖被拉制材料的熔体,在晶体生长室内充入惰性气体,使其压力大于熔体的分解压力,以抑制熔体中挥发性组元的蒸发损失,这样就可按通常的直拉技术进行单晶生长。
*悬浮区熔法:
主要用于提纯和生长硅单晶;
其基本原理是:
依靠熔体的表面张力,使熔区悬浮于多晶硅棒与下方生长出的单晶之间,通过熔区向上移动而进行提纯和生长单晶。
具有如下特点:
1.不使用坩埚,单晶生长过程不会被坩埚材料污染
2.由于杂质分凝和蒸发效应,可以生长出高电阻率硅单晶
*多晶硅浇注法
用于制备多晶硅太阳电池所用的硅原片,它是一种定向凝固法,晶体呈现片状生长过程和结构。
四、直拉法:
直拉法即切克老斯基法(Czochralski:
Cz),直拉法是半导体单晶生长用的最多的一种晶体生长技术。
五、直拉法单晶硅工艺过程
六、-引晶:
通过电阻加热,将装在石英坩埚中的多晶硅熔化,并保持略高于硅熔点的温度,将籽晶浸入熔体,然后以一定速度向上提拉籽晶并同时旋转引出晶体;
-缩颈:
生长一定长度的缩小的细长颈的晶体,以防止籽晶中的位错延伸到晶体中;
-放肩:
-等径生长:
-
收尾:
-降温:
降底温度,取出晶体,待后续加工
直拉法-几个基本问题
最大生长速度
晶体生长最大速度与晶体中的纵向温度梯度、晶体的热导率、晶体密度等有关。
但温度梯度太大,将在晶体中产生较大的热应力,会导致位错等晶体缺陷的形成,甚至会使晶体产生裂纹。
为了降低位错密度,晶体实际生长速度往往低于最大生长速度。
熔体中的对流
相互相反旋转的晶体(顺时针)和坩埚所产生的强制对流是由离心力和向心力、最终由熔体表面张力梯度所驱动的。
所生长的晶体的直径越大(坩锅越大),对流就越强烈,会造成熔体中温度波动和晶体局部回熔,从而导致晶体中的杂质分布不均匀等。
实际生产中,晶体的转动速度一般比坩锅快1-3倍,晶体和坩锅彼此的相互反向运动导致熔体中心区与外围区发生相对运动,有利于在固液界面下方形成一个相对稳定的区域,有利于晶体稳定生长。
生长界面形状(固液界面)
固液界面形状对单晶均匀性、完整性有重要影响,正常情况下,固液界面的宏观形状应该与热场所确定的熔体等温面相吻合。
在引晶、放肩阶段,固液界面凸向熔体,单晶等径生长后,界面先变平后再凹向熔体。
生长过程中各阶段生长条件的差异
直拉法的引晶阶段的熔体高度最高,裸露坩埚壁的高度最小,在晶体生长过程直到收尾阶段,裸露坩埚壁的高度不断增大,这样造成生长条件不断变化(熔体的对流、热传输、固液界面形状等)即整个晶锭从头到尾经历不同的热历史:
头部受热时间最长,尾部最短,这样会造成晶体轴向、径向杂质分布不均匀。
直拉法-技术改进:
一,磁控直拉技术
1,在直拉法中,氧含量及其分布是非常重要而又难于控制的参数,主要是熔体中的热对流加剧了熔融硅与石英坩锅的作用,即坩锅中的O2,、B、Al等杂质易于进入熔体和晶体。
热对流还会引起熔体中的温度波动,导致晶体中形成杂质条纹和旋涡缺陷。
2,半导体熔体都是良导体,对熔体施加磁场,熔体会受到与其运动方向相反的洛伦兹力作用,可以阻碍熔体中的对流,这相当于增大了熔体中的粘滞性。
在生产中通常采用水平磁场、垂直磁场等技术。
3,磁控直拉技术与直拉法相比所具有的优点在于:
减少了熔体中的温度波度。
一般直拉法中固液界面附近熔体中的温度波动达10C以上,而施加0.2T的磁场,其温度波动小于1℃。
这样可明显提高晶体中杂质分布的均匀性,晶体的径向电阻分布均匀性也可以得到提高;
降低了单晶中的缺陷密度;
减少了杂质的进入,提高了晶体的纯度。
这是由于在磁场作用下,熔融硅与坩锅的作用减弱,使坩锅中的杂质较少进入熔体和晶体。
将磁场强度与晶体转动、坩锅转动等工艺参数结合起来,可有效控制晶体中氧浓度的变化;
由于磁粘滞性,使扩散层厚度增大,可提高杂质纵向分布均匀性;
有利于提高生产率。
采用磁控直拉技术,如用水平磁场,当生长速度为一般直拉法两倍时,仍可得到质量较高的晶体。
4,磁控直拉技术主要用于制造电荷耦合(CCD)器件和一些功率器件的硅单晶。
也可用于GaAs、GaSb等化合物半导体单晶的生长。
连续生长技术
为了提高生产率,节约石英坩埚(在晶体生产成本中占相当比例),发展了连续直拉生长技术,主要是重新装料和连续加料两中技术:
1,重新加料直拉生长技术:
可节约大量时间(生长完毕后的降温、开炉、装炉等),一个坩埚可用多次。
2,连续加料直拉生长技术:
除了具有重新装料的优点外,还可保持整个生长过程中熔体的体积恒定,提高基本稳定的生长条件,因而可得到电阻率纵向分布均匀的单晶。
液体覆盖直拉技术:
主要原理:
对惰性液体(覆盖剂)的要求:
-密度小于所拉制的材料,既能浮在熔体表面之上;
对熔体和坩埚在化学上必须是惰性的,也不能与熔体混合,但要能浸云晶体和坩埚;
熔点要低于被拉制的材料且蒸气压很低;
-有较高的纯度,熔融状态下透明。
广泛使用的覆盖剂为B2O3:
密度1.8g/cm3,软化温度450C,在1300C时蒸气压仅为13Pa,透明性好,粘滞性也好。
此种技术可用于生长GaAs、InP、GaP、GaSb和InAs等单晶。
悬浮区熔法:
基本原理:
依靠熔体的表面张力,使熔区悬浮于多晶硅棒与下方生长出的单晶之间,通过熔区向上移动而进行提纯和生长单晶。
不使用坩埚,单晶生长过程不会被坩埚材料污染,由于杂质分凝和蒸发效应,可以生长出高电阻率硅单晶。