防护盖多工位级进模设计毕业设计论文 材料成型专业.docx
《防护盖多工位级进模设计毕业设计论文 材料成型专业.docx》由会员分享,可在线阅读,更多相关《防护盖多工位级进模设计毕业设计论文 材料成型专业.docx(43页珍藏版)》请在冰豆网上搜索。
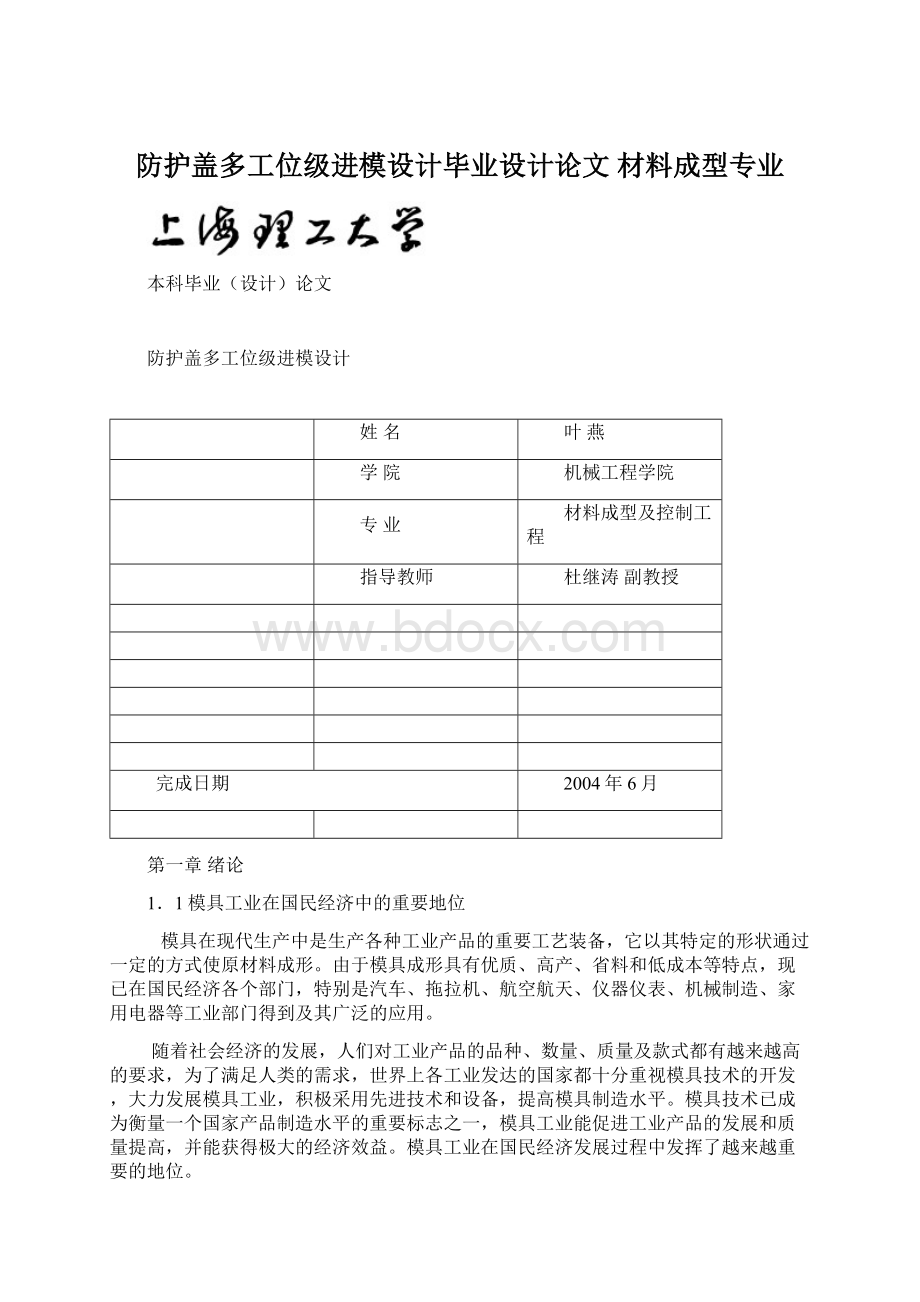
防护盖多工位级进模设计毕业设计论文材料成型专业
本科毕业(设计)论文
防护盖多工位级进模设计
姓名
叶燕
学院
机械工程学院
专业
材料成型及控制工程
指导教师
杜继涛副教授
完成日期
2004年6月
第一章绪论
1.1模具工业在国民经济中的重要地位
模具在现代生产中是生产各种工业产品的重要工艺装备,它以其特定的形状通过一定的方式使原材料成形。
由于模具成形具有优质、高产、省料和低成本等特点,现已在国民经济各个部门,特别是汽车、拖拉机、航空航天、仪器仪表、机械制造、家用电器等工业部门得到及其广泛的应用。
随着社会经济的发展,人们对工业产品的品种、数量、质量及款式都有越来越高的要求,为了满足人类的需求,世界上各工业发达的国家都十分重视模具技术的开发,大力发展模具工业,积极采用先进技术和设备,提高模具制造水平。
模具技术已成为衡量一个国家产品制造水平的重要标志之一,模具工业能促进工业产品的发展和质量提高,并能获得极大的经济效益。
模具工业在国民经济发展过程中发挥了越来越重要的地位。
1.2我国模具技术的现状
80年代以来,中国模具工业发展十分迅速。
国民经济的高速发展对模具工业提出了越来越高的要求,也为其发展提供了巨大的动力。
这些年来,中国模具工业一直以15%左右的增长速度快速发展。
当前,我国工业生产的特点是产品品种多、更新快和市场竞争激烈。
在这种情况下,用户对模具制造的要求是交货期短、精度高、质理好、价格低。
因此,模具工业的发展的趋势是非常明显的。
模具的制造周期逐步缩短,现代模具制造技术进一步得到推广应用,标准化程度逐步提高,使高精度多工位级进模的制造周期逐步缩短。
大型的制造周期4个月,中型的3个月,小型的2个月。
制造周期已达到国外同类模具的水准。
在工业生产中,冲压的应用十分广泛,其中多工位级进模是我国重点发展的精密、高效模具品种。
级进模是在压力机一次行程中完成多个工序的模具,其生产率高,成本低,可实现冲压自动化,且模具寿命长。
目前,国内已能生产精度达2微米的精密多工位级进模,工位数最多已达160个,寿命1~2亿次。
我国制造的多功能级进模达到国际上同类模具水平,模具导向精度高,能保证大批量生产中模具高速运行的稳定性。
模具主要零件制造精度达2μm,步距精度2~3μm,回转精度1',刃口及主要零件的表面粗糙度达Ra0.4~0.10μm,总寿命可达1亿次以上。
凸、凹模强度高,耐磨损、耐腐蚀,提高了使用寿命和产品质量。
多功能复合模具是在多工位级进模基础上开发出来的,一套多功能模具除了冲压成形零件外,还可担负转位、叠压、攻丝、铆接、锁紧等组装任务。
通过这种多劝能模具生产出来的不再是单个零件,而是成批的组件。
如触头与支座的组件,各种小型电机、电器及仪表的铁芯组件等。
我国的模具工业会朝着现代化的方向
第二章产品的工艺性分析
2.1零件的资料分析
跟据对零件的测绘,从而进一步明确了零件的形状特点、尺寸大小及所用材料,工件图如图所示。
该零件属于薄板冲裁弯曲件,除了φ5mm的孔有配合或有定位要求,其尺寸精度可按IT11级选取外,其余尺寸精度均按IT14级来取。
该零件材料为1Cr18Ni9Ti,材料的力学性能参见《冷冲压模具设计指导》上表8-1黑色金属材料的力学性能,可以查得不锈钢的材料状态是经热处理的,抗剪强度为451~511τ/MPa,抗拉强度为569~628σb/MPa,屈服点为196σs/MPa,伸长率35δ10/%,弹性模量为196E/103Mpa。
产品的生产批量为大批量生产,年产量/件>100万,冲压件的精度等级为IT14,因而根据“模具的精度与冲压件的精度关系”表,模具的精度等级取普通精度模具(PT)。
2.2零件的结构工艺性
2.2.1最小圆角半径
冲裁件的各直线或曲线的连接处,宜有适当的圆角,如果冲裁件有尖角,不仅给冲裁模的制造带来困难,而且模具也容易损坏。
如果是采用少、无废料排样冲裁,或是镶拼模具时可不要求冲裁件有圆角。
冲裁件的最小圆角半径参照《冷冲压模具设计指导》表2-1所示。
落料的最小圆角半径为0.35t,材料厚度为0.5mm,则为0.175mm。
冲孔的最小圆角半径为0.90t,则为0.45mm。
综上所述落料的最小圆角半径取0.5mm,冲孔的最小圆角半径为1mm
表2-1冲裁件最小圆角半径
工序
连接角度
黄铜、纯铜、铝
软钢
合金钢
落料
≥90°
0.18t
0.25t
0.35t
﹤90°
0.35t
0.50t
0.70t
冲孔
≥90°
0.20t
0.30t
0.45t
﹤90°
0.40t
0.60t
0.90t
2.2.2冲裁件的孔的最小尺寸
冲裁件上孔的尺寸受到凸模强度的限制,不能太小。
冲孔的最小尺寸见《冷冲压模具设计指导》表2-2所示。
由表可知采用精密导向凸模冲孔圆形为0.5t即为0.25mm,矩形为0.4t即为0.2mm。
而产品工件上最小冲裁孔为φ5mm,满足冲裁件最小孔尺寸要求。
表2-2冲孔的最小尺寸
材料
自由凸模冲孔
精密导向凸模冲孔
圆形
矩形
圆形
矩形
硬钢
1.3t
1.0t
0.5t
0.4t
软钢及黄铜
1.0t
0.7t
0.35t
0.3t
铝
0.8t
0.5t
0.3t
0.28t
酚醛层压布板
0.4t
0.35t
0.3t
0.25t
第三章工艺方案的确定
3.1模具结构的选择
冲裁模的结构形式多种多样,按工序的组合分类的话,单工序模、复合模、级进模是冲模结构的主要形式,并有着各自不同的优缺点及适用范围,如《冷冲压模具设计指导》书上表2-6所示。
表2-6单工序模、复合模和连续模的比较
比较项目
单工序模
复合模
连续模
冲压精度
较低
较高
一般
冲压生产率
低,压力机一次行程内只能完成一个工序
较高,压力机一次行程内可完成两个以上的工序
高,压力机一次行程内只能完成多个工序
实现操作机械化、自动化的可能性
较易,尤其适合于在多工位压力机上实现自动化
难,制件和废料排除较复杂,可以实现部分机械化
容易,尤其适应于单机上实现自动化
生产通用性
通用性好,适用于中小批量生产
通用性较差,仅适合大批量生产
通用性较差,仅是适合于中小型零件的大批量生产
冲模制造的复杂性和价格
结构简单,制造周期短,价格低
复杂性和价格较高
低于复合模
(1)从提高冲压件生产率来考虑,产品零件采用大批量生产>100万,选用复合模和级进模结构要比选则单工序冲裁模好得多。
因为单工序冲模在压力机一次行程下只能完成一个工序。
而复合模和级进模在一次行程内,可以同时完成多道工序的冲压工作,但级进模的生产效率相对复合模要高得多。
(2)从冲压精度的高低来看,用单工序模冲出的工件尺寸精度较低,而级进模最高可达到IT12~13级左右,复合模最高可达到IT9级以上,因此,当工件尺寸要求较高时,以采用复合模结构为宜,然而本设计零件最高精度为IT11级,故采用级进模。
(3)从生产的安全性来考虑,单工序冲模和复合模在工作时一般用手伸入冲模工作区内取、送料,工作起来及不安全。
而级进模工作时手不用伸入工作区内,或采用自动送料,工作时安全性较高。
(4)从冲模制造的复杂性和价格来看,虽然单工序模的结构简单,制造周期短,价格低,但是该零件的弯曲和冲裁较多,须做多个模具才可冲出,这样成本就很高了,且其占地面积很大;复合模的价格较高,所以采用级进模。
第四章零件的排样
4.1搭边a和a1的选取
搭边值参照《冷冲压模具设计指导》20页上表2-18来选取,材料厚度为0.5mm在0.5~0.8之间,工件间a1=1.8mm,沿边a=2.0mm,如果工件间的a1取得过小,会造成凸模强度不够,容易断裂,故取a1=5.0mm;考虑到搭边料的强度和导正销的摆放位置,所以取a=4.0mm。
表2-18搭边a和a1的数值(低碳钢)(mm)
圆件及圆角r>2t
矩形件边长l≤50
矩形件边长l﹥50或圆角r≤2t
材料厚度
t
工件间a1
沿边a
工件间a1
沿边a
工件间a1
沿边a
0.25以下
1.8
2.0
2.2
2.5
2.8
3.0
0.25~0.50
1.2
1.5
1.8
2.0
2.2
2.5
0.5~0.8
1.0
1.2
1.5
1.8
1.8
2.0
0.8~1.2
0.8
1.0
1.2
1.5
1.5
1.8
1.2~1.6
1.0
1.2
1.5
1.8
1.8
2.0
1.6~2.0
1.2
1.5
1.8
2.5
2.0
2.2
2.0~2.5
1.5
1.8
2.0
2.2
2.2
2.5
2.5~3.0
1.8
2.2
2.2
2.5
2.5
2.8
3.0~3.5
2.2
2.5
2.5
2.8
2.8
3.2
3.5~4.0
2.5
2.8
2.5
3.2
3.2
3.5
4.0~5.0
3.0
3.5
3.5
4.0
4.0
4.5
5.0~12
0.6t
0.7t
0.7t
0.8t
0.8t
0.9t
4.2材料的利用率
衡量材料经济利用的指标是材料的利用率。
一个进距内的材料利用率η为
η=nA/Bh*100%
式中A——冲裁件面积(包括冲出小孔在内);
n—一个进距内的冲件数目;
B——条料宽度(mm);
h——进距(mm)
则材料的利用率由计算机直接得出η=31.19%
4.3排样图的确定
通过对整个零件的分析,初步决定的排样图如图所示。
冲压时先冲出工艺孔再逐步导正,考虑到工件上¢5mm的孔比较小,不宜做导正销孔,故把前面五步的导正销孔按重心对称分布在废料上,并且为了节约材料,减小搭边,故将导正孔位置放在图示上的倒角处。
预期的排样图总共有六个工序,第一步冲孔、工艺孔和冲长条。
工艺孔做为导正销孔起导
正之用。
第二步冲其它异形孔,并用导正销导正,第三步继续冲异形孔,也用导正销导正,既而产品的外廓形状就此完成。
冲异形孔时要考虑到凸模的易于制造,及零件上的直角要求,采用搭接的方式。
第四步弯一部分的小弯曲,并用导正销导正。
第五步完成其余的小弯曲,还是用导正销导正。
第六步完成大弯曲和落料,要注意的是最后一个工序必须是先弯曲后落料,并且是用零件上的孔作为导正孔来导正,因为在落料时会把原来的导正销孔和废料一并切掉。
初步的排样图经仔细考虑后发现两个问题:
第一是弯曲部分凸模出现了干涉现象,为了解决此弊端,在第四和第五步工序之间插入一个空位,然而在级进模中,冲件精度要求较高的部分应尽量安排在邻近工步内实现,为减小送进误差,尽量少用空位。
之后又发现该零件四边上的小弯曲不是全部是向上或向下弯曲,按照其弯曲的方向和所在的位置,在排样时将向上弯曲和向下弯曲分为两个工序,这样既避免了凸模间的相互干涉现象,又合理地安排了模具的空间布局,使其零件的平面度和其他精度达到一定的要求。
第二是最后一步工序落料时把搭边料也切下了,这个涉及到废料的清除问题,这两条搭边料比较长,很难清除,如果采用废料刀切断的话,刀口离折弯镶块很近,会影响凹模强度。
因而考虑落料时不切断废料,将这两条搭边料用卷料机卷起,以解决上述问题。
最终排样图如下图所示:
第五章计算和压力机的选用
5.1冲裁力的计算
在冲模设计