毕业设计论文理工类解小宝DOC文档格式.docx
《毕业设计论文理工类解小宝DOC文档格式.docx》由会员分享,可在线阅读,更多相关《毕业设计论文理工类解小宝DOC文档格式.docx(21页珍藏版)》请在冰豆网上搜索。
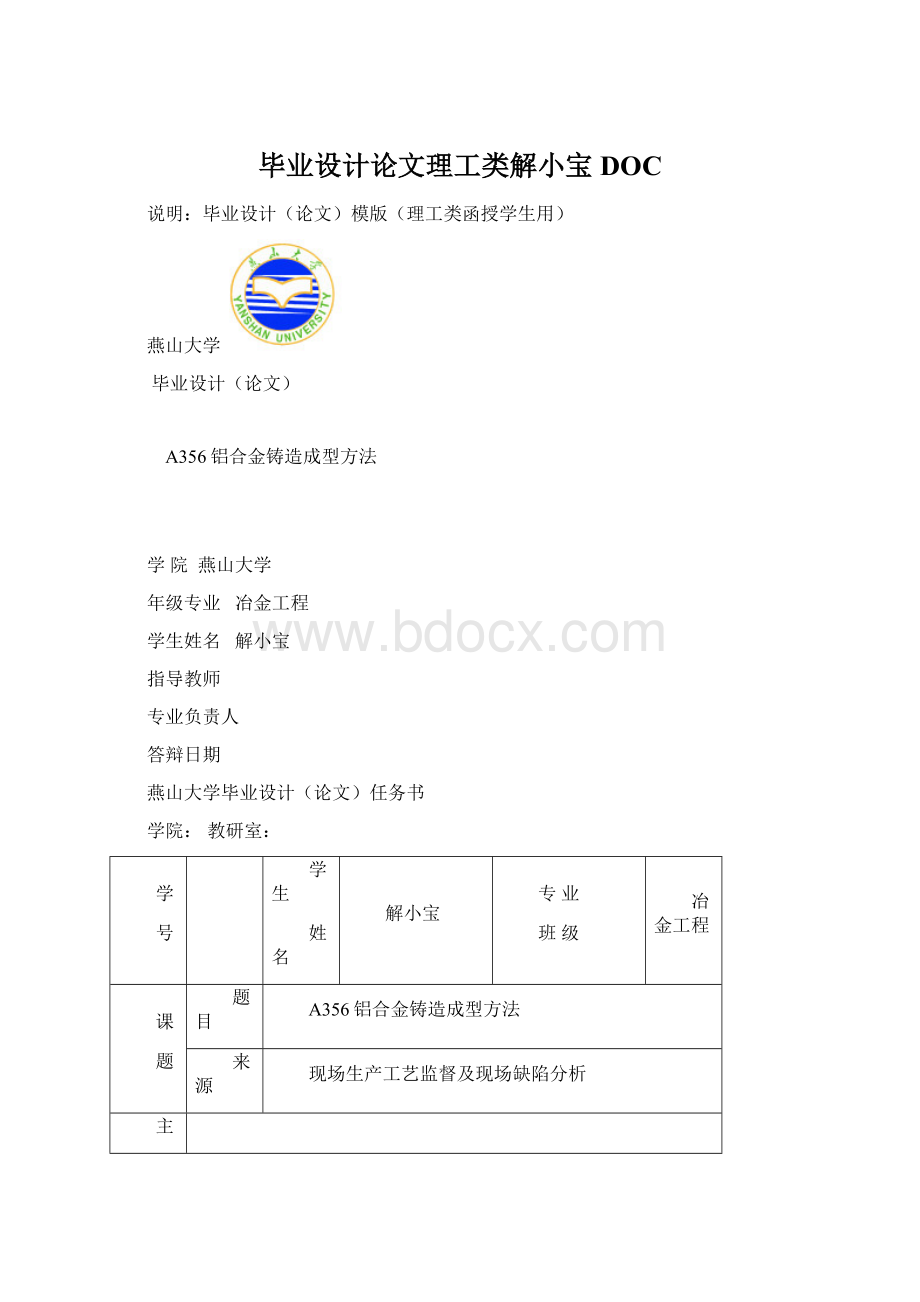
内
容
A356铝合金冶炼各工艺的描述;
铸造成型中常见的缺陷现象描述,常见铸造缺陷发生的原因,以及避免这些缺陷发生的防治措施。
基
本
求
熟悉A356铝合金冶炼各工艺的具体加工步骤,并结合铝合金晶粒的结晶过程对成品铸造生成的缺陷进行分析,防护。
参
考
资
料
1、潭新强等.新一代铝合金晶粒细化剂Al-Ti-C.铸造.2000.7
2、马宏声.金属及合金的熔炼与铸锭.东北工学院.1983年
3、彭学任、吴欣风.轻合金加工技术.1986年第9期.p10
4洪伟.有色金属连续铸造设备.冶金工业出版社.1987年.p6-p167
周次
1—4周
5—8周
9—12周
13—16周
17—18周
应
完
成
的
搜集关于铝合金冶炼及铸造的资料,并整理。
对A356铝合金现场生产工艺进行追踪,并记录数据。
对现场记录的数据进行整理。
结合现场数据整理分析A356铝合金所产生的缺陷进行分析,并得出结论
结合数据分析结果以及结论编写论文正文。
指导教师:
教研室审批:
如计算机输入,表题黑体小三号字,内容五号字。
本任务书一式三份,教务科、教师、学生各执一份。
摘要
在铸造合金中,铸造铝合金的应用最为广泛,是其他合金所无法比拟的. 由于铝合金各组元不同,从而表现出合金的物理、化学性能均有所不同,结晶过程也不尽相同
通过在工厂的具体实习研究了A356铝合金的工艺流程及其成型工艺,浇铸设备,以及其在生产中出现的缺陷和缺陷的防止办法.
A356铝合金的工艺流程:
配料→预热→装炉→熔炼(合金化)→搅拌取样→转炉→喷粉除渣→加入其他合金元素(合金化)→调整温度→除气精炼→炉前取样分析→浇铸→炉后检测→包装入库
关键词 铝合金浇铸成型工艺铸造方法
第一章绪论
1.1课题背景
近年来,汽车工业大量应用铝合金作为其产品的结构材料,以满足自身发展的需要。
20世纪80年代以来,在国际上,汽车结构变化的主要方向是提高使用经济性,而降低燃油消耗、实现轻量化是现代汽车最显著的特征。
因为汽车轻量化的结果会缓和能源需求的紧张状况,减轻环境污染,降低生产综合费用。
作为轻金属,将逐渐增大在汽车工业方面的开发应用,完全符合汽车工业自身当前的发展趋势。
1.1.1汽车铝合金铸件的应用
国际上,用铝合金代替铸铁制造汽车零件的历史可以追溯到20世纪40年代。
欧洲的汽车生产厂家,例如意大利菲亚特汽车公司研究出用铝代替铸铁制造进气歧管和气缸盖后,因其具有很多优点而开始少量生产。
同时,金属型铸造工艺用于汽车工业产品生产的优点也逐步表现出来。
50年代,澳大利亚引进了英国Alumasc公司的低压铸造技术,用于汽车铝铸件生产。
联邦德国KartlSchrmiolt公司对低压铸造技术作了进一步改进,用于生产结构复杂的零件,包括戴姆勒-本茨汽车公司的镶嵌铸铁衬套的铝制动鼓。
美国通用汽车公司在Massena铸造厂大量生产CorvairCertainly轿车铝铸件如气缸盖、曲轴箱、发动机后盖及滤清器接头。
60年代以后,以汽车工业为产业支柱的工业国家,将电子、机械制造技术与汽车制造溶为一体,追求高效率的生产方式,因此压铸技术获得了较大发展,压铸工艺成为汽车工业扩大轻金属应用的主要生产手段之一。
同时,也确立了现代汽车(其中主要是轿车)广泛应用铝铸件来减轻自身质量的基础。
总的说来,国际上铝合金逐步应用于汽车工业产品的发展历程主要分为两个阶段:
第一阶段应用的产品是气缸盖、进气管、活塞、离合器壳、变速器壳,以及镶嵌铁缸套的铝气缸体;
第二阶段开发应用的零件与车辆的安全性能有关,如盘式制动器座、悬臂架、制动鼓、万向节叉以及汽车轮毂。
在国内,汽车用铝铸件始于20世纪30~40年代,主要是制造汽车备件,供当时为数不多的汽车使用,生产量小,生产条件以及工艺技术很差。
在新中国成立以后,20世纪50年代我国建立了民族汽车工业(第一汽车制造厂);
70~80年代汽车工业飞跃发展,生产制造汽车品种从载货车、客车,并逐步发展到轻型汽车和轿车的制造,以生产轿车配套产品为主体,汽车用铝铸件的开发应用迅速发展起来。
汽车制造业为了减轻车辆自身质量,对铝铸件的需求不断增长。
在整个铝铸件总产量中,大约有60%-70%的铝铸件用于汽车制造,其主要用于以下两个产品。
纵观国内外,在汽车轮毂铝合金材料使用方面,国外如美国以及西欧,均采用356合金(或A356合金),而国内在引进国外的汽车轮毂铸造技术以后,经过国产化,形成现今使用的ZL101A合金。
在铸造方法上,主要采用金属型铸造,以及金属型低压铸造法,并且近年以来逐步开发生产带泥芯的铸造方法,即将轮毂幅条挖空,进一步减轻轮毅的质量。
在当前国内外汽车产品应用铝合金材料方面,按使用量计算,轮毂产品用铝合金数量位居首位。
由此可见,铝合金轮毂在汽车产品应用铝合金方面的重要意义。
1.1.2国内外铝合金熔铸技术的现状及发展趋势
(1)熔铸设备
近年来熔铸设备的发展一直追求大型、节能、高效和自动化。
在国外,大型顶开圆形炉和倾动式静置炉得到广泛应用,容量一般达30—50吨,多的达100吨以上,熔铝炉装料完全实现机械化。
铸造机通常使用液压铸造机,大型液压铸造机可铸100吨/次以上,最大铸锭重量达30吨。
为了使熔化炉内铝熔体的化学成分更均匀,减少劳动强度等原因,发达国家通常都在炉底安装电磁搅拌器。
国内在“七五”期间才研制成了“炉底平板式”电磁搅拌装置,现在该技术在国内应用不太多,只八五”期间才开始推广次新技术项目。
(2)晶粒细化
众所周知,在铝液中加入晶粒细化剂,可以明显改善铸锭的组织,晶粒细化的方法有多种,使用最广泛的是二元合金,Al-Ti和三元合金Al-Ti-B,国内产品主要有Al-4Ti、Al-5Ti-1B块状细化剂,在调整好铝熔体成分后加入。
而国外多将细化剂做成棒状,在铸造流槽中加入,细化效果显著提高,产品有Al-5Ti-1B、Al-5Ti-0.2B、Al-3Ti-1B、Al-6Ti等,国内很多厂家在生产高质量产品时,都使用进口的棒状细化剂。
①
近年来,细化剂的研究集中在降低使用成本和减少添加细化剂对熔体质量的影响上,针对不同合金应采用不同的细化剂。
另外,1996年美铝研制出新的细化剂Al-Ti-C,先后应用在很多种系合金中,显示了其优点,而我国对Al-Ti-C的研究才刚刚起步。
(3)熔体净化
多年来,铝合金制品对铸锭的内部质量尤其是清洁度的要求不断提高,而熔体净化可分为炉内处理和在先线净化两种方式。
炉内熔体处理主要有气体精炼、溶剂精炼和喷粉精炼等方式。
炉内处理技术的发展较慢,国内只有90年代中期出现的喷粉精炼相对较新,其除气除渣效果较气体精炼和溶剂精炼好,但因精炼杆靠人工移动,精炼效果波动较大。
国外先进的炉内净化处理采用了自动控制,较有代表性的有两种,一种是从炉顶或炉墙向炉内熔体中插入多根喷枪进行喷粉或气体精炼,,但由于该技术存在喷枪易碎和密封困难的缺点未广泛应用。
另一种是在炉底均匀安装多个可更换的透气塞,由计算机控制精炼气流和精炼时间,该方法是比较有效的炉内处理方法。
炉内处理对铝合金熔体的净化效果是有限的,要进一步提高熔体纯洁度,尤其是进一步降低氢含量和去除非金属夹渣物,必须采用高效的除气和过滤在线净化技术。
(4)铸造技术
半连续铸造是世界上应用最普遍,历史最悠久的铝合金铸造技术,50年代初我们从苏联引进了此技术。
对于铝合金铸造,除了到铸锭成型的基本目的之外,各铝加工企业和研究机构,一直致力于提高铸锭表面质量,即使铸锭表面尽可能平整光滑,减少或消除粗晶层偏析瘤等表面缺陷,减少铸锭厚差及底部翘曲和肿胀等,使铸锭在热轧前尽可能少铣或不铣面,提高成材率。
铸造技术的新进展及有前景的技术有:
脉冲水、加气铸造、电磁铸造、气滑铸造、可调结晶器、低液位铸造(LHC)、ASM新式扁顶结晶起等。
多年来,我国铝熔铸工程技术人员不断努力和创新,使铝熔铸技术取得了很大的进步和发展,对我国各种铝材质量的提高起了非常重要的作用。
21世纪是知识经济时代,随着我国加入WTO,铝加工业同其他产业一样,面临更加激烈的全球竞争。
为了生存和发展,铝熔铸技术必须广泛吸收国外先进技术,紧跟世界先进水平,开展科技攻关和技术创新,不断提高熔铸技术水平,为我们铝加工业的发展作出应有的贡献。
第二章原材料及炉料的配比
2.1原材料纯铝
铝电解槽中生产出的原铝,在质量上相差较大。
另外,还含有一些金属杂质,气体和非金属固态夹杂物。
铝锭铸造的任务是提高低品位铝液的利用率,并尽可能除去其中的杂质。
原铝中的杂质可分为以下三类:
第一类是金属元素,如铁、硅、铜、钙、镁、钛、钒、硼、镍、锌、镓、锡、铅、磷等,其中主要元素是铁和硅;
第二类是非金屑固态夹杂物,Al2O3,AlN和Al4C3;
第三类是气体,H2,CO2,CO,CH4,N2,其中主要的是H2。
在660C下,100g铝液中大约溶解0.2cm3的氢气。
气体在铝液中的溶解度随温度升高而增加。
从电解槽吸出的铝液,都要经过净化处理,清除掉一部分杂质,然后铸成商品铝锭(99.85%A1)。
含99.996%Al纯铝(铝丝φ2mm,硬拔者),电阻率为2.668×
10-8Ω·
m。
纯铝中如有杂质元素,则电阻率增大。
.影响最大者为铬、钒、锰、锂、钛。
影响较小者为铟、铅、锌、镉、锡、铍、铁。
用拜耳法从铝土矿生产出的工业氧化铝中,杂质的含量相对于原料铝土矿来说大为减少。
除了从碱液中带来的碱以外,杂质元素的分析值总量通常少于l%。
其中主要杂质是SiO2和Fe2O3。
除了氧化铝给电解槽带来杂质外,炭阳极和熔剂冰晶石也带来不少杂质。
炭阳极带来的杂质主要是铁和硅,冰晶石也是这样。
如果原料的杂质元素全部析出在原铝里,则所得铝的品位只有99.7%Al。
然而,实际生产出来的铝却具有较高的品位99.8%Al。
这种差别主要是由于杂质元素的蒸发造成的。
铁、钛、磷、锌和镓从氧化铝来的占多数,而硅和钒则从炭阳极来的占多数。
从熔剂来的杂质元素,以磷为多,约占磷总量的20%,其余硅、铁,钛和钒都很少。
平衡表的支出,硅和铁都超过了从原料带来的数量,其中硅超过60%左右,铁超过37%左右。
电解槽的内衬材料,例如高灰分的槽底炭块和炭糊以及耐火材料,是这些杂质元素的另一个重要来源。
此外,由于操作工具和阴极钢棒遭受侵蚀,使铁也进入了平衡。
其余几种元素,收支接近平衡。
支出分配在原铝和废气中的杂质元素量是不一样的。
蒸发量最大的是磷,占收入总量的72%,钒占64.4%,铁占62.4%,钛占57.7%,镓占49.6%,锌占19.7%。
最小的是硅,仅占收入总量的13.3%。
之所以如此,原因是:
①硅和锌在电解质里以比较难蒸发甚至不蒸发的化合物形态存在,倒如SiO2,ZnO或ZnF2。
硅和锌明显地积累在铝液里。
铝液被硅和锌污染的程度,主要是由物料平衡中供入的硅化合物和锌化合物总量来决定的。
在这种情形下,槽罩的收集效率无关紧要。
②铁、镓、钛和镍至少部分地以挥发性化合物的形态存在于体系中。
这些化合物大概是在进入电解质之后才生成的。
可能的化合物是Fe(CO)5,Ni(CO)4,TiF3,TiF4和GaF3等。
如果槽罩的收集效率提高,则会在一定程度上影响铝的质量。
③钒和磷只以挥发性化合物形态存在。
可能的化合物,首先是氟化物(VF3和PF3)和五氧化二磷(P2O5)。
由于电解质中磷含量升高会影响电流效率,而铝中钒量增多则会减小铝的导电性能,所以可以预料到提高槽罩的收集效率会对原铝质量以及最佳生产效果方面带来损害。
2.2炉料的分类及配比原则
2.2.1炉料的分类
配料的铝合金的炉料分三大类:
纯金属称为新金属;
回炉的废料或复化料;
中间合金.
1纯金属—新料铝合金主要使用的纯金属主要是:
纯铝以及纯金属的形式入炉的合金中的金属元素
纯铝装炉有固体料和液体料两种.多数铝加工厂用原铝锭装炉,冶炼厂的铸造车间电解槽铝水,一些大型的工厂采用大型炉集中熔化铝.然后一液体料供应给各合金熔炼炉
本厂是用电解铝作为纯金属的
铝合金添加元素直接装炉的纯金属有铜,镁等.他们在装炉之前多剪成碎快,以便于配料和加速其在铝中的溶解
2废料:
⑴本厂废料来源于熔铸的工艺废品及几何废料.此类废料可根据本厂的实际情况分级分类使用,质量好的大块废料可直接回炉配制成品合金;
对质量较差的碎屑需经复化处理后才准限量的配制成品合金⑵厂外废料,厂外废料来源于用料工厂,长粉较混杂质量较差,不宜直接使用,需经复化处理并确定其成分后才使用
3中间合金:
一些熔点高的或在铝中溶解速度慢的合金元素,多数预先制成中间合金加入,如,铜,钛,锰,硅等中间合金应成分均匀,易于破碎,杂质少熔点应接近铝的熔炼温度。
2.2.2炉料的装炉的要求
1炉料入炉前化学成分及杂质含量应清楚
2炉料应清洁,干燥,无灰尘,油污,腐化物及水分
3装炉方便;
有利于机械化作业,减少装炉时间从而减少金属损失及提高熔化效率
2.2.3炉料的配比原则
1在保证产品质量和性能要求的前提下,选择适当品位的纯金属.品位用高了提高成本,浪费了金属材料;
品位用低了达不到质量要求
2在保证产品质量的前提下,根据制品用途和工艺要求,应充分利用废料,降低新料用量;
但要注意废料循环使用所造成的杂质含量的升高,因此废料用量应有适当比例
3尽量避免,完全使用新料或完全使用废料,用电解铝液最好掺入部分废料及冷却料
4在保证产品质量前提下,根据工艺要求,应调整好炉料杂质含量的比例。
第三章A356.2铸造工艺
3.1A356.2铸造工艺流程
3.2工艺各流程控制点及操作说明
一、配料
在配料时要看清下达的任务书,按照技术要求的各元素种类将现有的原材料按所需含量混合起来,在高温 炉和合金炉里熔化。
在配料过程中要遵循原材料检验合格报告,原材料按工艺准确配比,原材料准确称量。
二、二预热
了除掉原材料中的残余预热主要是为水分
铝和水气的反应
低于250时,铝和空气中的水蒸汽接触发生下列反应
2AL+6H2O=2AL(OH)3+3H2
氢氧化铝是一种白色的粉末,没有防氧作用,且易吸潮
在高于400的熔炼温度下,铝与水气发生下列反应
2AL+3H2O=AL2O3+6[H]
生成的游离态[H]极易溶于铝液中,此反应为铝液吸氢的主要途径
高温下氢氧化铝在炉内发生分解反应
2AL(OH)3=AL2O3+3H2O
此反产生的H2O又可以与铝反应生成[H]进入铝液.所以铝锭长期露天啊存放是造成熔炼含气量多的主要原因
三装炉熔铝
固体金属在炉内加热熔化所需的能量要由熔炼炉的热源所提供,由于采用能源的不同,其加热的方式也不一样.目前基本炉型仍是火焰炉.金属熔化所需的理论总热量比实际所消耗的的能量小的多
铝的熔点虽然低(660)但由于熔化潜热(393056KJ/kg)和比热大(故态1.138KJ/(kg.0C)液态1.046)熔化1KG所需要的热量要比铜大的多,而铝的黑度(=0.2)仅是铜铁的0.25因此铝和铝合金的火焰熔炼炉很难实现理想的热效率
四加硅熔硅
在高温炉中将纯铝和工业硅完全熔化。
熔炼时间为熔铝为45~75min,熔硅为45~75min;
熔炼温度为780~880℃,再此温度范围内铝和工业硅可以完全的熔化;
原料融化程度要保证原材料全部融化。
硅与铝的原子结构相同.同为面心立方体.熔化潜热大,加入到铝合金中提高合金的流动性.降低合金的收缩量,减少疏松,提高气密性.同时加入镁可以提高合金的强度.Si是A356合金的主要元素,微量Si的加入使w(Mg)=0.3%铝合金的流动性急剧下降,当w(Si)=0.3%,w(Mg)=0.3%时,其流动性为200mm;
当w(Si)=1.5%时为66.5mm,降幅为66.75%.但随着Si含量的继续增加,合金流动性开始缓慢上升,当w(Si)=11%,试验中由于Si加入使流动性降低的现象明显改善,流动性恢复到w(Si)=0%时,即试验开始时第一数据点的流动性水平。
分析认为,微量Si的加入使Al—0.3Mg合金流动性急剧下降的原因在于,微量Si与Mg结合生成Mg2Si,由于后者含量甚微,大多以固溶形式存在于α—Al基体中[2-3]。
固溶物与基体存在晶体结构和热物理性能差异,Al的导热系数为2.23J/(cm·
s·
℃),Mg2Si的导热系数为2.92J/(cm·
℃)~7.69×
10-3J/(cm·
℃),相差3个数量级,导致局部区域温度场不均匀,使α-Al晶体生长过程中原子堆垛发生异常,形成高能量畸变点[4-6],改变了初生相晶体生长的热扩散和原子扩散环境,使合金凝固区间扩大,从而使流动性急剧下降。
五搅拌取样
搅拌取样的目的为测钙,钙为铸造过程中的杂质元素,在铸造过程中影响合金液的流动性,搅拌时间为5min,这样以保证高温炉内的各部分元素均匀;
取样部位在炉中间部位,液面以下15~25cm[26],这样所取部位能够代表炉内各部分的钙含量的大小。
用光谱分析测钙,钙含量符合产品要求为<
0.05%。
实际生产注意事项
1搅拌时间
2取样部位
3钙含量符合产品要求
六转炉
控制点:
1、转炉时间:
15—30分钟
2、转炉温度:
780—880摄氏度
将高温炉内已经完全熔化的铝硅合金转移到合金炉内,以便于按照技术要求的各元素含量进行元素的配比。
转炉时间为15~30min,这样可以保证在从高温炉内的铝硅合金液温度符合,转炉温度为780~880℃。
七喷粉除渣
1、铝液温度:
710—720摄氏度
2、清渣剂用量:
铝液总重量的1/1000----1.3/1000
3、氩气的压力:
0.25---0.3MPa
4、喷粉时间:
3----5分钟
在氩气的作用下将精炼粉吹入合金液中,将杂质元素转变成固态的渣子浮到合金液表面,再用工具将渣子扒出,以达到减少杂质的目的。
在喷粉除渣中须注意1.铝液温度:
710~720℃,此温度是精炼剂和合金液中的杂质反应的最佳温度;
2.清渣剂用量为铝液总重量的1/1000~1.3/1000,此用量完全可以将合金液中的杂质元素清除干净;
3.氩气的压力为0.25~0.3MPa;
4.喷粉时间为3~5min,在此时间范围内可以将精炼剂全部吹入合金液中,并使渣子浮到合金液表面
八合金化处理
1、添加数量和要求
2、铝液温度:
660—690摄氏度
3、添加方式和顺序:
锶中间合金镁锭
加入中间合金后迅速搅拌使之熔化。
加入镁锭后迅速搅起铝液,将镁锭覆盖,然后反复将镁锭压入合金液,尽量不使镁锭泛起镁光,直至镁锭完全溶解,搅拌5---8分钟
4、搅拌时间:
>
=5分钟
按照技术要求加入Mg和Ti等元素,以达到技术要求中元素的含量。
在添加其他元素过程中要注意1.添加数量和要求,完全按照技术要求和配料作业指导书进行投料;
2.铝液温度为660~690℃,此时可以保证加入的合金元素不被大量的氧化或烧损,以节省原料,减小成本,提高利润;
3.添加方式和顺序:
锶中间合金、镁锭。
因为Mg比锶的熔点低,为减小镁的消耗,先加锶后加入镁.加入锶中间合金后迅速搅拌使之熔化。
加入镁锭后迅速搅起铝液,将镁锭覆盖,然后反复将镁锭压入合金液,尽量不使镁锭泛起镁光,直至镁锭完全溶解,搅拌5~8min。
九温度调整
当Ti含量低于0.15%时,将铝液温度调整到660~690℃;
当Ti含量在0.15—0.2%时,将铝液温度调整到690~720℃,当含Ti量高于0.2%或生产喊锑合金时,将铝液温度调到720~750℃。
十除气精练
710---720摄氏度
2、氩气压力:
3、除气时间:
针孔度<
=2级时,除气的时间应大于20分钟
针孔度<
=3级时,除气的时间应大于15分钟
在技术标准控制的温度下,向合金液内同入高纯氩气,将合金液内附着的气体尤其是氢气吹出,减小因气体的存在对铸件造成的缺陷的产生。
铝液温度控制为710~720℃,经研究表明,此温度下,氩气作用于合金液中氢气等气体容易冲破合金液的包裹,而被排除合金液减小铸造中的缺陷。
氩气压力需要0.25~0.3MPa;
当针孔度<
=2级时,除气的时间应大于20min,针孔度<
=3级时,除气的时间应大于15min。
十一炉前取样分析
680---700摄氏度
2、取样部位:
炉中间部位,液面以下15—25cm
3、取样时机
4、检测项目:
成分检测
5、产品标准要求
用小勺在炉内中间取出合金液注入专用模型中检验合金液的成分是否符合技术要求的标准。
铝液温度为680~700℃;
取样部为炉中间部位,液面以下15~25cm,取样时机,在除气精炼过程即将结束时进行取样分析,检测合金液的成分以保证产品的成分合格。
十二浇铸
1、浇铸温度:
640----660摄氏度
2、浇铸速度:
0.25----0.5块/秒
在成分和温度都符合要求的状态下,在半连续浇注机中将合金液注入专用的金属模具中,完成从液态到产品的过程。
浇铸温度为640~660℃;
速度为0.25~0.5块/秒[33],在此速度范围内,可以保证成品的质量、重量等复合产品的技术要求,做出合格的产品;
在浇注过程中用专用工具将浇铸的产品在凝固前将浮在表面的因浇铸时产生的氧化渣刮走,保证产品符合技术要求。
十三炉后检验
将最终的成品随机抽取按照规定的技术要求,取固定的部位检查其宏观组织和微观组织是否符合技术标准。
在浇铸中随机抽取第一、三、六车中的一个铸件打上A、C、F标志,分别代表本炉次的前、中、后部分的产品质量;
最后用金相显微镜观察金相组织,针孔和晶粒大小。
十四包装
规定将铝锭码放整齐并用钢带或高塑带打包,对有的客户特殊要求的进行套袋处理,然后登记入库。
第四章铸造工艺
由于在工厂的实习工种的不同,就在浇铸过程中的具体情况将铸造工艺在这里具体说明一下
现在铝锭铸造工艺一般采用浇铸工艺,就是把铝液直接浇到模子里,待其冷却后取出.产品质量的好坏主要在这一步骤,而且整个铸造工艺,也是以这一过程为主。
铸造过程是一个由液态铝冷却、结晶成为固体铝锭的物理过程。
4.1铝合金铸模的分类
块式铁模(水冷模)铸锭是目前我国小型铝加工厂和铝制品厂铸锭的主要生产方式,占半铸锭的三分之二,其特点是:
生产方便灵活,设备费少,利用余热加工,各向异性小,深冲性能好;
劳动条件差
铝合金常用的铸铁模有两种:
一种是对开的厚壁铁模;
一种是对开的水冷模,以水冷模多
一对金属模的要求
有一定的吸热能力,保证凝固所需的冷却速度操作简便灵活,膜模方便热稳定性好,不易变形有足够的强度
二铸模的冷却能力
铸锭的凝固是由于铸型的吸热而进行,所以任何铸件的凝固速度都受铸型吸热能力支配铸型吸热能力用蓄热系数b来衡量,铸型的蓄热系数越大,对铸锭的激冷能力越强
较为理想的铸模材料是紫铜,但是由于紫铜的价格贵,目前采用铸铁模.为减少铸模重量增加激冷能力