水泥粉磨生产线培训课件Word下载.docx
《水泥粉磨生产线培训课件Word下载.docx》由会员分享,可在线阅读,更多相关《水泥粉磨生产线培训课件Word下载.docx(38页珍藏版)》请在冰豆网上搜索。
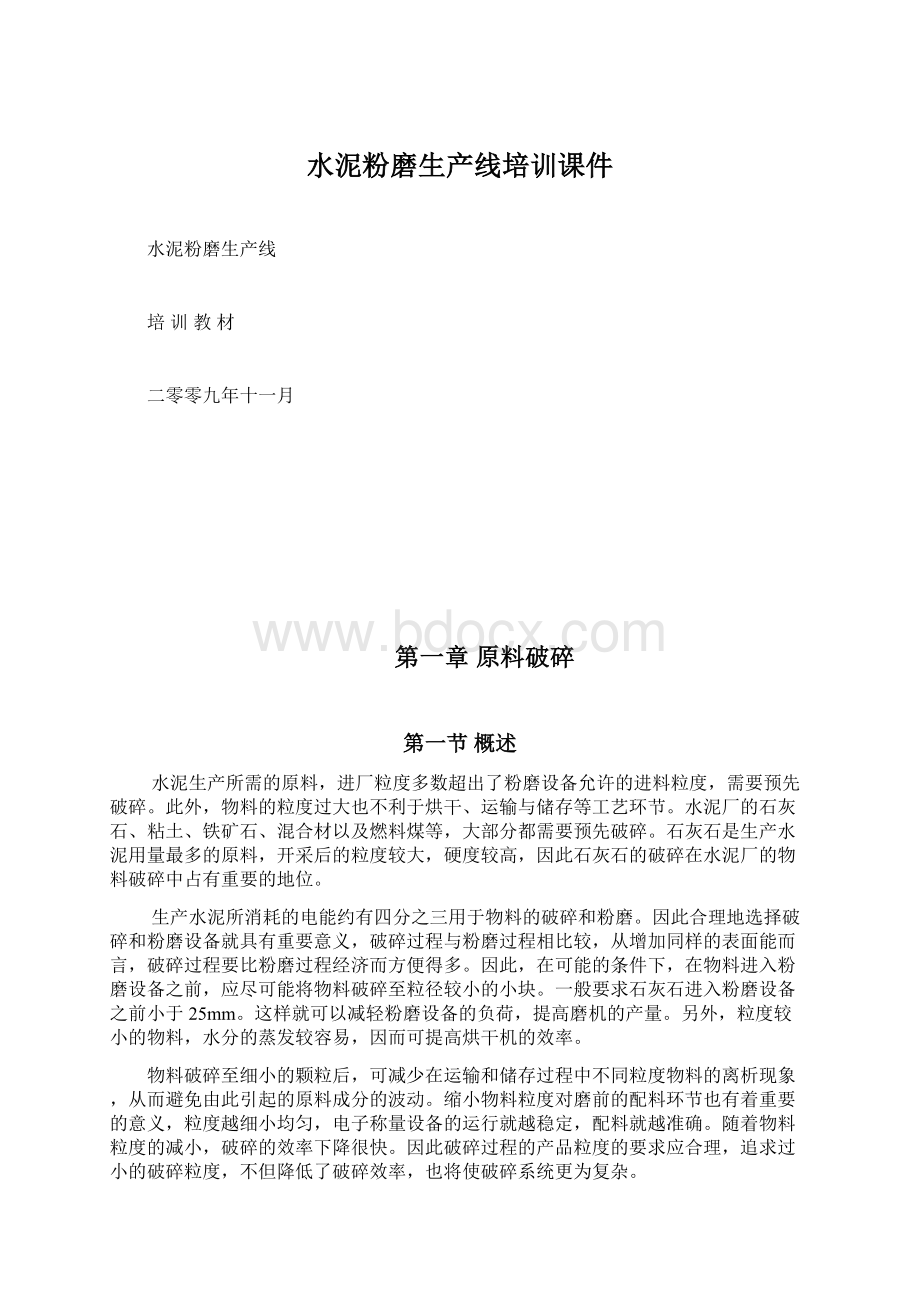
反击式破碎机
3-10
4-8
4-12
10-50
物料的物理机械性质是选择破碎机类型重要因素,诸如强度、硬度、密度,是脆性或是韧性,是块状或片状,含水量、含泥量及粘塑性、磨蚀性等。
因此,不同的物料在抗压能力、抗剪能力、抗冲击能力、抗研磨刮削能力等表现是不一样的。
水泥厂需要破碎的物料因其物理机械特质不同而需要选择不同类型的破碎机。
下面主要介绍缅甸郊塞水泥厂使用的几种类型的破碎机。
第二节破碎设备的类型
一、颚式破碎机
颚式破碎机在水泥工厂中被广泛采用,主要用来破碎石灰石、铁矿石、石膏和大块熟料等。
其结构如图3-1所示。
活动颚板在偏心轴带动下,有规律地作往复运动,物料在固定颚板和活动颚板之间被挤压破碎。
大块物料由进料口喂入,破碎后的小块物料由出料口排出。
颚式破碎机有粗碎和细碎之分,其规格都按其进料口的长宽尺寸来表示,如150×
750mm,250×
400mm,250×
500mm,250×
1000mm,400×
600mm,600×
900mm,900×
1200mm,1200×
1500mm和1500×
2100mm等。
为了使物料能顺利的进入破碎机,最大入料粒度通常为其进料口宽度的0.85,如进料口宽度250mm的最大进料粒度为210mm。
颚式破碎机的优点是:
构造简单、制造维护容易,机体坚固,能破碎高强度的矿石,进料口容许有物料堆积,因而对于喂料稳定性要求不高。
适用范围广,对耐磨和韧性强的物料有较好的适应性。
其缺点是:
破碎比较小,粗碎式颚式破碎机出料粒度往往不能满足入磨要求;
片状岩石由于容易发生漏料,不宜用颚式破碎机进行破碎;
其动颚运动时呈往复运动,空行程不起破碎作用,工作效率较低;
当破碎湿的和可塑性的物料时,出料口容易堵塞。
二、锤式破碎机
水泥工业中广泛地采用锤式破碎机,用来破碎石灰石、泥灰岩、熟料和煤块等。
锤式破碎机可分为单转子和双转子两种类型。
单转子锤式破碎机构造和工作原理如图3-2所示。
工作时,主轴被皮带轮上皮带拖动转动,离心力作用将自由悬挂的锤头沿着十字头旋转的方向抛出,进到弧形篦条上的料块,受到被锤头的猛烈冲击而破碎后从弧形篦条间落下,在降落过程中再被高速旋转的锤头破碎,落到三角形篦条上。
小于篦条空隙的碎粒将被排出机体,大于篦条空隙的大颗粒将继续破碎过程,料块除受到锤头旋转的冲击力外,在篦条上还受到锤头挤压和研磨作用。
出料粒度则借助于三角形篦条间的空隙宽度及篦条工作面和锤头端面间的距离来调节。
双转子锤式破碎机的工作原理与单转子锤式破碎机的工作原理相似。
锤式破碎机的优点是:
生产能力大,破碎比高,最大可达70;
构造简单,机体小,产品粒度较小,由于采用冲击式破碎方式,产品将产生大量细粉,有利于粉磨系统产量的提高。
零件易检修、拆换。
缺点是:
锤头、篦条、衬板磨损快;
工作时产生粉尘大;
不适合硬度较高,潮湿及粘性物料的破碎,当破碎水分大或粘性物料时,产量会大大下降,易堵塞出料口,同时易损件的磨损大大加速。
三、环锤式破碎机
以往过去水泥厂的设计中,煤的破碎多采用锤式破碎机,或反击式破碎机,其结果是能耗大,过破碎现象严重,造成大量扬尘。
为了克服这些不足,目前设计中除采用颚式破碎机外,多数是采用环锤式破碎机。
环锤式破碎机用于各种脆性物料,物料的抗压强度不超过100MPa,表面水分不大于15%。
除用于煤的破碎外,也可用于焦炭和页岩等物料的破碎。
环锤式破碎机是利用高速旋转的转子带动环锤对物料进行冲击破碎,使被冲击后的物料又在环锤、破碎板和筛板之间受到压缩、剪切、碾磨作用,进而达到所需粒度的高效率破碎机械。
四、粘土冲击式破碎机
粘土质原料是水泥生产中的主要原料,约占水泥原料的10-20%。
由于粘土含水分高,又有较强的塑性,很容易粘结,故粘土破碎需专用设备。
目前采用较多的是粘土冲击式破碎机,见图3-4。
该破碎机的破碎系统由三个活动辊筒组成的反击板锤的转子体等部件所组成,主要借高速旋转的转子体上的板锤冲击湿粘土块,使其沿薄弱部分进行选择性破碎,被冲击的料块获的很大的动能,再经反击板和湿土块相互间的冲击后,又被进一步破碎。
为了防止破碎腔的粘结,本机采用辊筒,在其背后装有刮刀,湿料一旦粘结到筒上即被刮下。
机壳四周吊挂链条,随着破碎料的打击,不停地抖动,湿料无法粘上,高速旋转转子将诱导大量的空气进入破碎腔,随着转子的旋转,空气受到离心力的作用,使其机壳内的含湿气体沿着出料口的方向逸出,在此形成一个水蒸气分压差,可对破碎细料起到微小的烘干作用。
五、反击式破碎机
反击式破碎机在水泥工业中被广泛采用。
它适用于破碎石灰石等脆性物料,是一种高效率的破碎设备。
反击式破碎机如图3-5所示,它的破碎过程是:
物料经装料口处的导板(或称筛板)落在转子上,受到高速旋转着的转子上的打击板的高速冲打,被抛至上部悬挂着的反击板上,从反击板上掉下来的物料与转子陆续抛上来的物料相互冲击。
这样,物料在转子、导板、反击板及链幕之间的破碎空腔内受到反复剧烈的碰撞和冲击而得到破碎。
破碎后的成品由出料口排出。
出料粒度的大小,靠上下调节反击板尾部的螺栓来控制。
反击式破碎机具有结构简单,生产效率高,破碎比大,单位能耗低,产品粒度较细,磨损较少等优点。
不设下篦条的反击式破碎机产品中有少量大块;
用于单段破碎时,必须严格控制最大进料粒度,以免损坏转子。
第二章水泥制成
第一节水泥熟料的贮存
出窑熟料经冷却机冷却后,不能直接送到粉磨车间粉磨,而必须经过贮存。
熟料贮存的目的是:
1.降低熟料温度,以保证磨机的正常操作。
一般从冷却机出来的熟料温度达100℃以上,大块熟料的内部温度更高。
过热的熟料入磨会降低磨机产量,使磨机筒体因热膨胀而伸长,对轴承产生轴向压力;
影响磨机轴肩的润滑,对磨机的安全运转不利;
磨内温度过高,使石膏脱水过多,引起水泥凝结时间不正常;
过高的熟料温度,使磨内结团和包球的趋势增大,粉磨效率降低。
2.改善熟料质量,提高易磨性。
出窑熟料中含有一定数量的f-CaO,贮存时能吸收空气中部分水汽,使部分f-CaO消解为氢氧化钙,在熟料内部产生膨胀应力,因而提高了熟料的易磨性,改善水泥的安定性。
3.熟料的储存作为缓冲环节,有利于窑磨生产的平衡和控制调配入磨熟料的质量。
出窑的熟料可根据质量的好坏分库存放,以便搭配使用,保持水泥质量的稳定有控。
4.熟料的均化熟料储存中,可以在一定程度上实现熟料的均化。
熟料的煅烧过程中,由于生料系统不可避免出现的生料成分的波动和煅烧系统不可避免的热工制度的波动,将造成熟料质量的波动。
熟料储存过程中,利用进出物料不同的时间分布,将可一定程度上实现质量波动不太大的熟料的均化。
对于现代化水泥厂而言,熟料储存目前常用的有圆形储库或圆形帐篷库。
前者是由钢筋混凝土浇注而成。
这种圆库是密闭的,库顶一般设一至两个下料口,采用拉链机进料。
库底设置一个或多个锥型漏斗卸料口,以提高卸空率,锥形漏斗下部设置钢棒阀和计量设备。
这种熟料库大小不一,小则可容几百吨,大则可容上万吨。
库的高径比一般为1.8~2.5。
由于这种类型的熟料库出料口较少,也可直接在库底设置计量及控制设施,水泥磨的配料在库底完成后,直接送入水泥磨。
圆形储库密闭性较好,有利于收尘。
但作为水泥熟料的储存,散热较慢。
帐篷库的结构如图9-1所示。
这种结构在高度上与圆柱形库比降低很多,大约只有圆柱形库的1/3左右,因此对于建设场地的地耐力可降低要求。
与圆形储库相比,相同储量的帐篷库占地面积较大。
这种库的平面直径可由40~90m,熟料储存量可由7000吨到80000吨。
从几何形体上看实际上是一个短圆柱形与一个圆锥形的结合。
直段部分可由混凝土制成,锥盖通常由钢结构拼装。
物料由顶端进入位于帐篷库中心的混凝土圆柱体形小库,小库自下而上整个圆柱面上遍布卸料孔。
熟料进入小库后,由卸料孔自然流出,形成一个底角为熟料自然休止角的圆锥形料堆,采用这种进料方式有利于收尘。
帐篷库对于地耐力的要求较低,熟料暴露面积大,易于散热。
但是帐篷库的库底面积较大,设的下料口数量较多,因而不宜采用库底配料的方式,需要增加一轮转运;
帐篷库下可采用链式取料机取料,也可采用多点出料。
前者投资较大,设备维修费用也较高。
后者投资较低,设备也较可靠,但帐篷库卸空率比较低。
第二节石膏的作用
水泥工业中应用的石膏通常有天然石膏和工业副产品石膏两类。
天然石膏呈多种形态产出,其中二水石膏为含有两个结晶水的天然石膏,其主要形态为:
质纯无色的透明晶体,称为透石膏(selenite);
雪白色细粒块状、半透明者为雪花石膏和细晶石膏(alabaster);
呈纤维状具有丝绢光泽或半丝绢光泽者为纤维石膏(fibrousgypsum)。
还有含杂质较多的土石膏、泥质石膏(claygypsum)等。
二水石膏的分子式为CaSO4·
2H2O。
二水石膏中的结晶水,在65~70℃时开始缓慢脱水,而在120~150℃则开始加速脱水,失去一部分结晶水后成为半水石膏(CaSO4·
H2O);
当温度170~180℃时,结晶水全部脱离而成为无水石膏(CaSO4)。
自然界中有少量的无水石膏存在,因其质地较硬,所以又称硬石膏。
水泥生产中使用石膏主要是利用石膏与硅酸盐矿物生成的中间矿物,降低水泥的水化速度,延缓水泥的凝结时间,增进水泥强度以及改善水泥某些施工性能,如干缩性和抗冻性能等。
但过多的石膏会引起水泥的体积安定性和其他的部分性能的恶化。
因此水泥中的石膏掺加量必须有所限制。
石膏的掺加量通常采用水泥产品中的SO3含量进行控制。
各国水泥标准对于水泥中的SO3的含量控制基本一致,约为2.5~3.0%。
第三节水泥的粉磨
水泥熟料通过粉磨后,表面积增加得越多,水化作用越快;
施工过程中只有小于一定粒度的水泥熟料颗粒才能进行水化反应,因而只有磨到一定细度的水泥才能具有一定的强度。
单纯从强度观点出发,最好把熟料磨细一些,但是在实际生产中粉磨过细会使磨机产量显著下降,电耗急剧增加。
各国水泥标准均对水泥细度提出要求,水泥细度大多控制在88μm筛余4~6%,或勃氏比表面积300m2/kg。
这些标准对细度要求一般要求并不高,但是作为强制执行的国家标准,实际反映了国家对于水泥产品的市场准入要求。
但考虑市场竞争,各个水泥生产企业通常提高水泥细度,以缩短水泥凝结时间,提高水泥早期强度,提高市场竞争力。
因此市场出售的水泥水泥细度趋于较大幅度高出国家水泥标准。
一、球磨系统
开流磨系统的主要优点是流程简单,生产可靠,设备和土建费用低。
它的缺点是粉磨高标号水泥时,即比表面积超过3000cm2/g时,电耗增加较大,为了控制开流磨的产品细度,水泥磨机的通风将大大受限,水泥生产过程中产品过高的温度,将很难降下来。
另外,产品细度也不易调节。
因此对于大型水泥磨系统,几乎完全是采用闭路系统。
60年代后期,继单仓和多仓管磨一级闭路的基础上发展了一种双仓中长磨闭路系统。
它弥补了单仓短磨由于粉磨线路太短,在粉磨比表面积较高情况下,循环负荷过大以及产量要求高时直径太大的缺点。
另外它又克服了多仓长磨粉磨线路太长,效率低的缺点。
所以这种双仓中长磨一级闭路系统对粉磨不同细度的水泥来说,适应性较强,尤其对比表面积高的水泥粉磨效率高,循环负荷适宜。
至今,采用双仓闭路系统,是世界水泥工业发展中的主要形式。
图9-2为闭路水泥磨系统工艺流程图。
二.高效选粉机
新型高效选粉机有日本小野田水泥公司的O—SEPA选粉机,史密斯公司的SEPAX选粉机以及美国斯图特公司的SD侧进风型选粉机等,均在物料的分散、气流流向、物料运动和分级性能方面有很大改进。
O—SEPA选粉机已引进消化,在国内组织生产。
根据这些高效选粉机的工作原理,我国的建材机械企业,也开发了一些类似的高效选粉机。
使我国水泥预分解生产线在进行建设筹划时,利用市场竞争,更好的满足建设需求,有了更多的选择。
O—SEPA选粉机在结构和工作原理上均有其独到之处。
物料从顶部喂入转子上的撒料盘,被离心力甩到挡料环上,把团粒打散;
同时改变方向,在强涡流空气的剪切作用下,进行第二次分散。
导向叶片与转子之间的分级区形成均匀的料幕。
磨机排气和粉磨系统内附属设备的含尘气体,分别作为一次和二次风沿切向进入蜗壳形机体内,借助导向叶片和回转转子,产生流速与压力稳定的水平涡流,分散的物料在此通过分级界限分明的选粉区,竖直高度上运动距离大,停留时间长,表现出较高的分选效率。
分选出来的细粉随气体送至收尘器收集。
而粗颗粒则被清洁的二三次风进行再次分选后排出。
由于这几种选粉机均在防止磨损上有很稳妥的技术措施(采用具有高耐磨性能的高合金铸钢,粘贴抗磨性良好的陶瓷马赛克等)可以在较高风速条件下,实现选粉作业的高效率。
磨内气体全部经过选粉机后排出,水泥及回粉冷却好。
实际使用中,其磨机系统的生产能力与普通离心式选粉机相比,约提高15%,节电约10—15%。
尤其在产品粉磨细度要求较高时,与普通选粉机相比,有更高的效率。
三.辊压机
辊压机是两个相对运转的料辊,在很高的压力下,对物料进行挤压,实现破碎和粉磨过程的粉磨机械。
辊压机的成功应用,得力于高压料层粉碎理论的发展。
该理论认为固体物料受外界压力时产生压缩变形和应力集中,当应力达到颗粒某一最弱的轴向破坏应力极限时,颗粒就会在最弱处发生碎裂。
固体物料受压而粉碎的难易程度,可用脆性值Br衡量:
式中:
Nc—为抗压强度Nt—为抗拉强度
脆性值越大,物料越易被压碎。
脆性值大而坚硬的物料,其粉碎功的利用率高。
水泥工业中熟料的物性是非常适应这种设备进行粉磨的。
应用这一原理,开发出的辊压机由固定辊和滑动辊组成的,其相向的转动的磨辊依靠摩擦,将需粉碎的物料带入挤压区,滑动辊在液压缸的驱动下,使辊间的挤压破碎区,在与物料接触的区域内,产生500—1000MPa的压力,使物料破裂。
其辊筒的表面多用堆焊,表面硬度可达到HRC55—58,硬化层厚度可达6—7mm。
辊压机设置了液压系统以及相应的监测和控制系统,使系统能够以稳定的压力和辊间隙正常运转。
对于一定的物料,有一个相应的被压碎至理想状态的临界压力。
当辊压力稍大于临界压力时,料层中的细粉已达到相当数量,继续增大压力只能使少量大颗粒处于细粉包围之中,对于继续粉碎产生不良影响。
因此一般控制在出辊压机的产品为用手轻松搓碎的扁平料饼。
辊压机能量利用率高于其它的粉磨设备。
由于慢速挤压,其研磨部件的磨损较小。
自1985年问世,我国部分建材机械企业先后引进德国洪堡公司设备生产技术,一些水泥研究设计院也先后研制小型辊压机。
取得节电14—30%的效果。
并根据不同条件,开发出开路,闭路,半闭路、生料终粉磨系统及相应配套的打散机等设备。
但是部分未完全解决的技术问题,也一直困扰着辊压机的使用。
物料与磨辊之间由于主要表现为静摩擦,其磨损速度及磨辊的维修周期,尚能为用户接受,但物料与辊压机侧板的磨擦,主要表现为动摩擦,磨损速度快,维修周期短。
一旦侧板出现较大的间隙,辊压机出料的粒度分布将恶化,通过辊压机边部的物料将得不到良好的挤压,但之后的管磨机的研磨介质的球径级配,又不可能随着入磨物料粒度变化而及时调整,因而不可避免的造成系统粉磨效率的大幅下降。
采用打散机实现闭路预粉磨,虽然能够解决这一问题,但又因系统过于复杂,系统运转率低。
轴承、液压系统、辊子在高压负荷下运转,使用寿命不理想。
凡此种种均造成辊压机运转率低下,维修费用较高。
由于以上原因,辊压机在我国水泥行业中的应用,一度曾陷入困境。
但近年设备和工艺系统的一系列改进,同时也因水泥生产线规模的扩大,也没有更好的设备及系统解决单机高产的水泥粉磨问题。
辊压机用于水泥预粉磨系统,又有了一定程度的发展,并取得了较好的效益。
这主要是:
降低推动动磨辊向静磨辊运行的液压缸液压系统的压力,从而提高液压系统工作的可靠性。
由于动静磨辊间的压力有所降低,使辊压机的挤压效果有所降低。
采用适当降低辊压机技术指标的方法,提高辊压机的运转率。
用极为简单的分料阀闭路预粉磨系统,取代繁杂的打散机预粉磨系统。
用少量牺牲系统分选指标的方法,提高预粉磨系统的运转率。
从辊压机的诞生到现在,已经有二十余年的使用历史。
在其使用初期,给予了其过高的期望值,选定了一些过于勉强、脱离实际的技术参数,导致了辊压机预粉磨系统运转率的下降。
在拥有一定的使用经验后,人们适当降低部分工艺参数,提高打散机和预粉磨系统的运转率,使辊压机预粉磨系统,真正进入了实用阶段。
四.水泥粉磨的CKP系统
辊式磨由于粉磨过程中的高效率,采用辊式磨研磨水泥,一直是水泥界梦想的工艺。
但辊式磨粉磨产品,存在产品粒径分布较窄,小于30微米的细颗粒数量较少,将因此引起水泥水化速度慢,强度尤其是早期强度不足的问题。
因而辊式磨用于水泥成品的终粉磨,一直是一个难于逾越的障碍。
在这种条件下,采用辊式磨作为预粉磨CKP系统就应运而生了。
早在上个世纪八十年代,中国建筑材料科学研究院水泥所总工程师左万信提出了用辊式磨进行预粉磨,而以填充白色石球的管磨机为终粉磨,对高水分,要求产品高细度的白水泥熟料进行粉磨。
从而提高白水呢粉磨电耗的设想,这是将高效率的辊式磨用于水泥预粉磨的早期设想。
上世纪末,日本国川崎公司率先在大型水泥粉磨系统采用辊式磨作为水泥预粉磨,创造了水泥粉磨的所谓“CKP”系统。
采用该系统大大降低了水泥粉磨电耗,使水泥粉磨电耗降低到不足30度的高水平。
由于大量的粉磨过程在冷却效果极好的辊式磨中完成,对于降低水泥温度,防止石膏脱水,也具有良好的技术优势。
在目前,由于CKP系统对于辊式磨的特殊要求,大型辊式磨的水泥预粉磨系统的设备制造技术我国还没有完全掌握。
全套设备进口费用的高昂,使国内推广CKP系统,在投资上还存有一定的障碍。
对于采用辊式磨直接完成水泥的终粉磨,在国际水泥界已经有成功的报道。
莱歇公司的终粉磨系统通过辊式磨的选粉机的改造,实现了水泥产品的宽粒度分布,小于30微米的水泥小颗粒比例大幅度提高,水泥熟料颗粒的微观形态,也实现了园形的优化。
因此采用辊式磨作为水泥的终粉磨,使水泥的物化性能,与管磨机相比,毫不逊色。
我国安徽朱家桥水泥有限公司通过技术和装备引进,于2000年开始了辊式磨完成水泥熟料终粉磨的工业试验。
虽然辊式磨完成水泥熟料终粉磨的成功报道不绝于耳,但国际水泥界对于熟料颗粒的微观形态是否理想,一直心存疑虑。
第三章水泥的储存与包装
第一节水泥储存
出磨水泥进入水泥储库。
水泥储存有以下作用:
1.严格控制水泥质量。
大中型水泥厂,水泥熟料质量稳定,用快速测定法几小时即可获得强度检验结果,但一般应看到三天强度检验结果,确认28天抗压强度有富余2.5MPa以上的把握方可出库。
确保出厂水泥全部合格。
2.改善水泥的质量,在存放过程中水泥吸收空气中的水分使水泥所含的游离氧化钙消解,同时水泥存放过程中,也使储存水泥的温度有所下降,以利水泥的输送与包装。
3.水泥库可以起调节缓冲作用,以适应水泥粉磨车间的连续作业和水泥市场的季节性变化,有利于水泥包装及时出厂。
现代化的水泥工厂所采用的水泥库主要是圆柱形混凝土库,但出料方式、库底结构已经一改传统的锥斗结构的出料方式。
取而代之的是设有充气装置的约15°
的斜底库,并以罗茨风机进行充气助卸,以提高储库的卸空率,使水泥库的储存效率有所提高。
库底设置气动卸料阀和输送装置,将水泥快速卸出后,由输送系统转送至水泥包装和散装系统。
第二节水泥的包装和散装
为了便于运输和使用,出厂水泥根据市场需求,采用袋装和散装两种形式。
袋装通常采用纸袋、编织袋或编织物和包装纸结合的复合袋,每袋水泥净重50kg。
散装水泥则采用专用的散装车将出库水泥直接送至水泥使用点。
一、包装机
包装机主要分两种类型,即回转式包装机和固定式包装机。
1.回转式包装机
回转式包装机向包装袋灌注水泥基本有两种形式,一种采用压缩空气使水泥流态化,气力助卸。
另一种是依靠叶轮强迫灌装式。
通过灌装嘴灌入水泥袋内。
这种包装机可用自动插袋机和码包机实现包装作业的全部自动化。
由于这种自动化系统投资较高,对于水泥包装袋的质量及标准化程度要求较高,因此应用并不普遍。
目前我国企业多数采用人工插袋(将空包装袋插在包装机的灌装嘴上)作业,和人工辅助卸袋作业,以降低投资。
其余工序如灌装、秤量、卸装等按程序自动进行。
回转式包装机单机生产能力较大,回转式六嘴包装机能力为90—110t/h左右。
但这是指采用全套机械化插袋和卸袋条件下,所能达到的技术指标。
通常条件下,仅能达到60—70t/h,这是我们通常在进行生产技术平衡时,所能采用的可靠参数。
图10-1是中国引进德国哈佛公司技术生产的六嘴包装机结构图,由回转水泥仓、回转电动机、料位控制器、灌装工作机构、计量机构、搅拌器、主传动装置、空气管路等部分组成。
这种包装机采用叶轮强迫灌装式,进入包装袋的空气量较少,收尘风量较小。
包装袋破损也较少。
包装机的整个回转部分通过主轴悬吊在楼面的机座上,主轴的上端与主传动装置相连,可调速的主电动机运转时,通过主传动箱带动主轴和固定在主轴下端的水泥回转仓,作回转运动(由顶部俯视)。
灌装机构同灌装咀均匀分布在回转水泥仓的外壁上,随回转仓一起回转。
每个灌装嘴在回转一周的过程中,连序完成灌装水泥的各种作业。
包装机的每一个叶轮和灌装嘴及计量控制系统构成一个单元,可以在发生故障时整体拆下另换一个备品,一个单元的故障不影响其它单元的工作,因此运转率较高。
易损件中通用件较多,便于维修。
由于回转式包装机的单机效率较高,工人劳动强度较轻,工作点比较集中,收尘负荷较小。
因而对于50t/h以上的产量需求时,原则上应选用回转包装机。
2.固定式包装机
固定式包装机有螺旋式包装机、单嘴叶轮自卸式包装机和多嘴叶轮式包装机。
它具有重量轻、体积小、便于安装维护等优点。
图10-2为固定四嘴包装机,其单体与六嘴包装机是一样的,也就是说,四嘴包装机是以固定料仓作为支撑,而六嘴包装机以回转的料仓作为支撑平台。
该机灌装与计量同时进行,并能自动定量进行机械化作业。
水泥由进料装置中的给料器喂入包装机的四个室,卸料室中个有高速转动的“十”字形叶轴。
水泥受回转叶片的作用,从